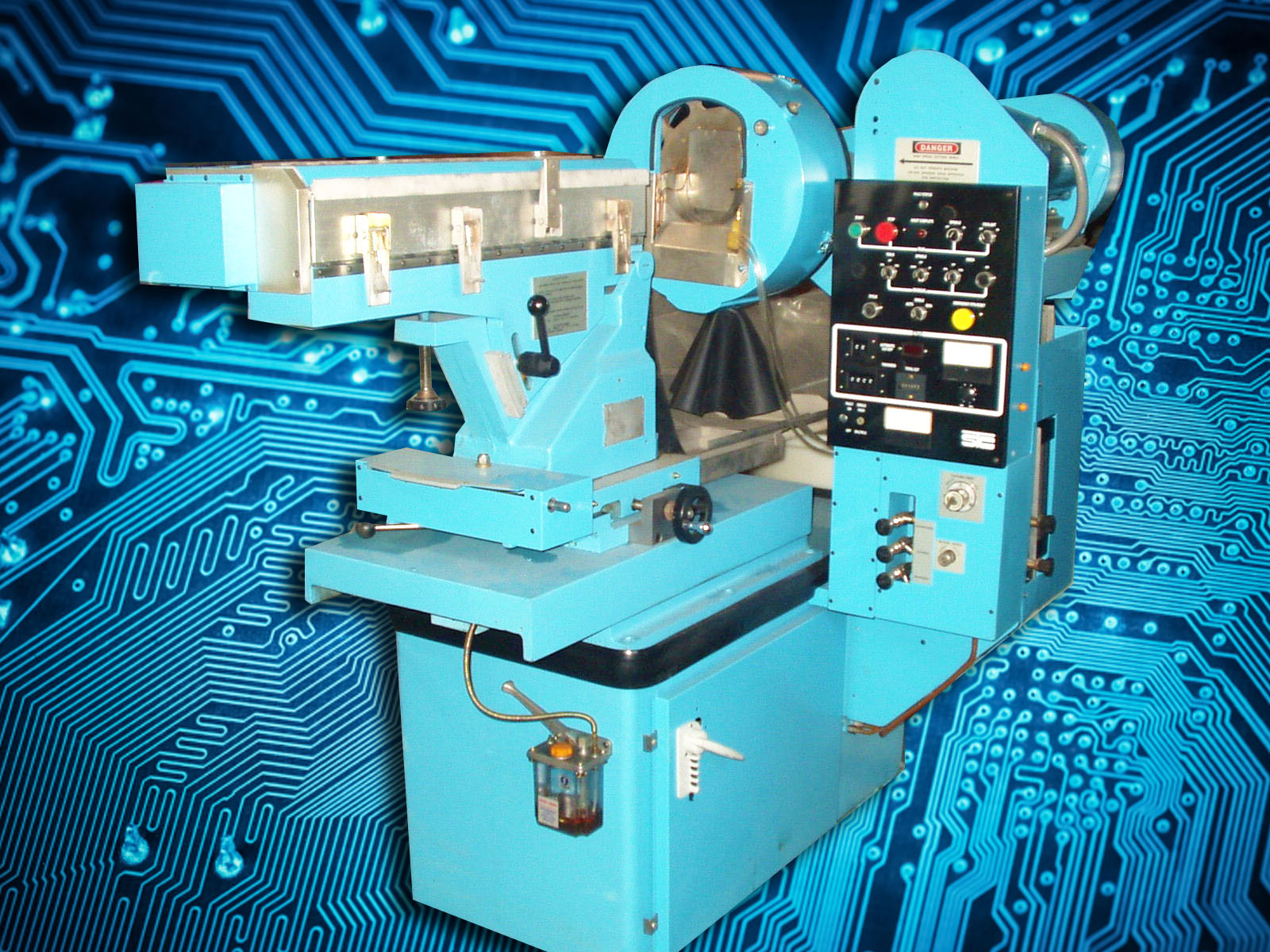
The diamonds used in the manufacture of SMI diamond grinding wheels can be classified into two categories:
natural diamond and synthetic diamonds. Every since synthetic diamonds were first introduced in 1957. Their applications have been steadily increasing.Now they are acceptedas the principal material for diamond grinding wheels.
Two important achievements in the history of synthetic diamonds are the development of strong.though diamond grits used for saw blades and the improvement of the grits for resinoid bonds. some grits for resinoid bonds are coated with metal which enables the resinoid bond grinding wheels to achieve better performance.
Diamond powder is commercially available in 50 grades and each grade has its own unique features. Diamonds may be classifiedin to the following
two catagories in term of bonding method:
• RESINOID BOND
• METAL BOND OR VITRIFIED BOND
The grit typed and gritsizes of grinding wheels can be selected depending on workpieces, bonds, and grinding conditions.To help us design the grinding wheels best suited to your purpose.
CONCENTRATION
concentration is the content of diamonds in a unit volume of a grinding wheel.
when content is 25 volume % concantration is 100,which is equivalent to 4.4cts/cc of diamond in the grinding wheel.the relationship among grits content(in volume %),concantration and diamond content(in cts /cc)is as follows:
Grit content (volume%) | Concentration | Diamond Content (cts/cc) |
25 | 100 | 4.4 |
18.75 | 75 | 3.3 |
12.5 | 50 | 2.2 |
6.25 | 25 | 1.1 |
AS illustrated above, the price of grinding wheel largely depends on its concentration.
since the appropriate concantration of a wheel depends on work materials, grinding conditions, etc.
GRIT SIZE
Diamond grit size are classified into 22 grades as shown in the following table. The nominal grit size of a grinding wheel indicates the coarsets size grits which are present in the wheel.
For instance,the grits in the #140/170 range pass through a #140 sieve and are trapped by a #170 sieve.The grit size in this range is noted as #140.
Grit size classification by sieves is not only feasible up to # 135 mesh. After this, the grit sizs is still indicated by number (#……)but the method of classification is different.Grit size can br more accurately understood by correlating them to their respective mesh size and grit sizescatter in diameter (see chart below)
Normal Grit Size (Mesh) | Grit Size Range in Mesh of the Grits Use | FEPA | Normal Grit Size (Mesh) | Grit Size Range in Mesh of the Grits Use | FEPA |
16 | 16/20 | 200 | 200/230 | D 76 | |
20 | 20/30 | D 852 | 230 | 230/270 | D 64 |
30 | 30/40 | D 602 | 270 | 270/325 | D 54 |
40 | 40/50 | D 426 | 325 | 325/400 | D 46 |
50 | 50/60 | D 301 | 400 | 400/500 | D 38 |
60 | 60/80 | D 252 | 600 | 500/600 | D 30 |
80 | 80/100 | D 181 | 800 | 600/800 | D 25 |
100 | 100/120 | D 151 | 1000 | 800/1000 | D 15 |
120 | 120/140 | D 126 | 1500 | ||
140 | 140/170 | D 107 | 2000 | ||
170 | 170/200 | D 91 | 3000 |
BOND
There are three alternative bonding methods :resinoid bond, metal bond and vitrified bond
RESINOID BOND
Resinoid bond grinding wkeels are manufactured by using resinoid bonds to bond diamond grits.
there are two types of resinoid bonds:the phenol resin type and the polymide resin type. The phenol resin type is currently in more common usage.
Resinoid bond grinding wkeels have good elasticity, fine surfacefinish, and high grinding performance.They are effectivefor
(1) grinding of cementebcarbide
(2)combination grinding of cemented and hardened steel
(3)grinding of cermet
(4)precision grinding of magnatic materials glass,ceramics,etc
polymide wheels are recommendeb for heavy grinding and creep -feed grinding.
METAL BOND
Metal bond grinding wheel are manufactured by sintering metal powder to bond diamond grits.These grits are superior in grits retention and thereforepreferred
(1)when a long service is required
(2)when wear of the grinding wheel needs to be minimized(such as in form grinding)
(3)in hand grinding of cemented carbide
(4)in profile grinding
(5)in the cutting and grinding of hand ,and brittle materials such as ceramics,glass and quratz
(6)in the cutting and grinding of magnetic materials such as ferrite
(7)in the cutting and grinding of the stone
(8)in the cutting and grinding of graphite,etc
The high grit retention quality of metal bond can also cause grazingor loading.the increaseof grinding pressure and of heatingdue to loading may cause thermaldamage to the workpiece. in order to prevent thermal damage,please choose the grinding process, conditions,coolant, dressing intervals,etccarefully.
Hi, its pleasant paragraph about media print, we all know media is
a enormous source of information.
Currently it looks like WordPress is the best blogging platform out there right now. (from what I’ve read) Is that what you are using on your blog?
It’s a pity you don’t have a donate button! I’d most certainly donate to this outstanding blog! I guess for now i’ll settle for book-marking and adding your RSS feed to my Google account. I look forward to brand new updates and will share this site with my Facebook group. Talk soon!
Yeah bookmaking this wasn’t a high risk conclusion great post! .
I have read a few just right stuff here. Definitely worth bookmarking for revisiting. I wonder how a lot attempt you put to create such a magnificent informative site.
Your place is valueble for me. Thanks!…
Fantastic site. Plenty of useful info here. I¦m sending it to a few pals ans also sharing in delicious. And of course, thank you to your effort!
I was just looking for this info for some time. After six hours of continuous Googleing, finally I got it in your web site. I wonder what is the lack of Google strategy that don’t rank this kind of informative web sites in top of the list. Generally the top websites are full of garbage.
Hi there! This post couldn’t be written any better! Reading through this post reminds me of my previous room mate! He always kept talking about this. I will forward this article to him. Pretty sure he will have a good read. Thank you for sharing!
hello there and thank you for your information – I’ve definitely picked up anything new from right here. I did however expertise some technical points using this site, as I experienced to reload the site many times previous to I could get it to load correctly. I had been wondering if your web host is OK? Not that I’m complaining, but sluggish loading instances times will very frequently affect your placement in google and can damage your high-quality score if advertising and marketing with Adwords. Well I’m adding this RSS to my e-mail and can look out for much more of your respective fascinating content. Make sure you update this again very soon..
Enjoyed looking through this, very good stuff, thankyou.
What is Java Burn? Java Burn, an innovative weight loss supplement, is poised to transform our perception of fat loss.
My brother recommended I would possibly like this website. He was totally right. This post actually made my day. You cann’t imagine simply how much time I had spent for this info! Thanks!
I was very pleased to find this web-site.I wanted to thanks for your time for this wonderful read!! I definitely enjoying every little bit of it and I have you bookmarked to check out new stuff you blog post.
I’ve been absent for a while, but now I remember why I used to love this site. Thanks, I will try and check back more frequently. How frequently you update your site?
It’s arduous to find knowledgeable individuals on this topic, however you sound like you recognize what you’re talking about! Thanks
Pretty! This was a really wonderful post. Thank you for your provided information.
you’re actually a excellent webmaster. The web site loading velocity is incredible. It kind of feels that you are doing any unique trick. In addition, The contents are masterpiece. you’ve done a magnificent job in this subject!
I think other web-site proprietors should take this website as an model, very clean and magnificent user genial style and design, as well as the content. You are an expert in this topic!
I like this website because so much useful stuff on here : D.
I truly appreciate this post. I have been looking everywhere for this! Thank goodness I found it on Bing. You have made my day! Thx again
Very interesting info !Perfect just what I was searching for!
I loved up to you will receive carried out right here. The caricature is attractive, your authored material stylish. nevertheless, you command get got an shakiness over that you would like be handing over the following. sick unquestionably come further until now once more as precisely the similar just about a lot regularly inside case you shield this hike.
Some times its a pain in the ass to read what blog owners wrote but this website is rattling user pleasant! .
I got what you mean , thankyou for posting.Woh I am lucky to find this website through google.
Thank you for sharing superb informations. Your web-site is so cool. I’m impressed by the details that you?¦ve on this website. It reveals how nicely you perceive this subject. Bookmarked this website page, will come back for more articles. You, my friend, ROCK! I found just the information I already searched all over the place and just could not come across. What an ideal web site.
Hi there, just become alert to your blog through Google, and found that it is truly informative. I’m gonna be careful for brussels. I’ll appreciate should you proceed this in future. A lot of other folks might be benefited from your writing. Cheers!
You can certainly see your enthusiasm within the work you write. The arena hopes for more passionate writers such as you who aren’t afraid to mention how they believe. Always follow your heart.
Well I really liked studying it. This subject provided by you is very useful for correct planning.
I got good info from your blog
An impressive share, I just given this onto a colleague who was doing a little analysis on this. And he in fact bought me breakfast because I found it for him.. smile. So let me reword that: Thnx for the treat! But yeah Thnkx for spending the time to discuss this, I feel strongly about it and love reading more on this topic. If possible, as you become expertise, would you mind updating your blog with more details? It is highly helpful for me. Big thumb up for this blog post!
Needed to draft you a bit of word to give many thanks the moment again for your precious strategies you’ve documented in this article. It was shockingly open-handed of people like you to offer unhampered all that some people would have offered as an e book in order to make some dough for their own end, specifically considering the fact that you could have tried it in case you decided. These pointers as well served to be a fantastic way to understand that most people have similar keenness the same as my very own to know a good deal more with regards to this condition. I am certain there are some more fun sessions up front for many who check out your blog post.
Greetings! Very helpful advice on this article! It is the little changes that make the biggest changes. Thanks a lot for sharing!
There’s noticeably a bundle to find out about this. I assume you made certain good points in features also.
I will immediately snatch your rss as I can not in finding your e-mail subscription link or e-newsletter service. Do you’ve any? Kindly permit me recognize so that I could subscribe. Thanks.
ProNerve 6 nerve relief formula stands out due to its advanced formula combining natural ingredients that have been specifically put together for the exceptional health advantages it offers.
Thank you for some other fantastic post. The place else may anyone get that type of information in such a perfect method of writing? I have a presentation subsequent week, and I’m at the search for such info.
It’s hard to find knowledgeable people on this topic, but you sound like you know what you’re talking about! Thanks
Simply wanna tell that this is handy, Thanks for taking your time to write this.
Hi my loved one! I want to say that this post is amazing, nice written and include almost all vital infos. I would like to look extra posts like this .
I love your blog.. very nice colors & theme. Did you make this website yourself or did you hire someone to do it for you? Plz answer back as I’m looking to create my own blog and would like to find out where u got this from. many thanks
Keep functioning ,terrific job!
Good write-up, I¦m normal visitor of one¦s site, maintain up the excellent operate, and It is going to be a regular visitor for a long time.
It’s actually a cool and helpful piece of info. I’m glad that you shared this useful info with us. Please keep us up to date like this. Thanks for sharing.
I love it when folks get together and share views.
Great blog, keep it up!
Feel free to surf to my webpage – pronerve 6 reviews
I don’t even understand how I finished up right
here, however I thought this publish was once good. I don’t
recognise who you might be however certainly you’re going to a well-known blogger should you are not already.
Cheers!
Also visit my homepage emperors vigor
Wow! Thank you! I constantly needed to write on my website something like that. Can I include a part of your post to my website?
F*ckin’ amazing things here. I am very glad to see your post. Thanks a lot and i’m looking forward to contact you. Will you please drop me a mail?
I like what you guys tend to be up too. This sort of clever work and coverage!
Keep up the good works guys I’ve you guys to blogroll.
Have a look at my site: quietum plus reviews
Please let me know if you’re looking for a article writer for your weblog.
You have some really good posts and I believe
I would be a good asset. If you ever want to take some of the
load off, I’d love to write some articles for your blog
in exchange for a link back to mine. Please blast me an e-mail
if interested. Many thanks!
Feel free to surf to my website; gluco freedom
Heya this is kinda of off topic but I was wanting
to know if blogs use WYSIWYG editors or if you
have to manually code with HTML. I’m starting a blog soon but have no coding know-how so I wanted
to get guidance from someone with experience. Any help would be
enormously appreciated!
Have a look at my web site does tonic greens work
Perfectly written content, thanks for information. “No human thing is of serious importance.” by Plato.
Quality articles or reviews is the key to attract the visitors
to pay a visit the website, that’s what this
web page is providing.
Look at my homepage boostaro reviews
Write more, thats all I have to say. Literally, it seems as
though you relied on the video to make your point.
You clearly know what youre talking about, why waste your intelligence
on just posting videos to your weblog when you could be giving us something enlightening to read?
Check out my website – ingredients in lung clear pro
Greetings from Idaho! I’m bored at work so I decided to check out your
website on my iphone during lunch break. I love the information you provide here and can’t
wait to take a look when I get home. I’m shocked at how quick your blog loaded on my mobile ..
I’m not even using WIFI, just 3G .. Anyhow, great site!
Great blog you have here.. It’s hard to find high quality writing like yours these days.
I seriously appreciate individuals like you! Take care!!
Here is my page – side effects of provadent
It’s enormous that you are getting thoughts from this article as well
as from our discussion made at this time.
Also visit my web-site :: sight care
Hi, Neat post. There’s a problem together with your web site
in web explorer, would test this? IE nonetheless is the marketplace
chief and a good element of people will omit your
excellent writing due to this problem.
Feel free to surf to my web-site – manup gummies
Hi just wanted to give you a brief heads up and let
you know a few of the pictures aren’t loading correctly.
I’m not sure why but I think its a linking issue. I’ve tried
it in two different web browsers and both show the same outcome.
Here is my page :: testoprime reviews
I’m gone to inform my little brother, that he should also pay a quick visit this blog on regular basis
to obtain updated from newest news update.
my page gluco freedom reviews
Everyone loves it when people get together and share views.
Great site, stick with it!
Here is my web page :: alpha bites reviews
Hi Dear, are you really visiting this website regularly,
if so then you will without doubt obtain nice knowledge.
Here is my homepage: the billionaire brain wave
Hello to every , because I am really keen of reading this webpage’s post to be updated
regularly. It consists of fastidious information.
my blog … growth matrix
Undeniably believe that which you stated. Your favorite reason appeared to be on the web
the simplest thing to be aware of. I say to you, I certainly get
annoyed while people consider worries that they plainly do not know about.
You managed to hit the nail upon the top as well as defined out the whole
thing without having side effect , people could take a signal.
Will likely be back to get more. Thanks
Here is my web page pro nerve 6 review
Heya excellent website! Does running a blog similar to
this require a lot of work? I have absolutely no understanding of coding
but I was hoping to start my own blog in the near future.
Anyhow, should you have any ideas or tips for new blog owners please share.
I understand this is off subject nevertheless I simply needed to ask.
Kudos!
My site – Animale CBD Gummies
Marvelous, what a web site it is! This website gives useful information to us, keep it
up.
Feel free to visit my page – what is growth matrix
Hey I know this is off topic but I was wondering if you knew of any widgets I could add to my blog
that automatically tweet my newest twitter updates. I’ve been looking
for a plug-in like this for quite some time and was hoping maybe you
would have some experience with something like this.
Please let me know if you run into anything.
I truly enjoy reading your blog and I look forward to your new updates.
Here is my website; endoboost
I’m more than happy to discover this website.
I need to to thank you for ones time for this particularly wonderful read!!
I definitely enjoyed every little bit of it and I have you bookmarked to see new things on your web site.
Also visit my blog :: phenq reviews
Great beat ! I would like to apprentice whilst you amend your website,
how could i subscribe for a weblog site? The
account helped me a applicable deal. I have been tiny bit familiar of this your broadcast offered shiny transparent concept
My blog post; lottery defeated software
Greetings! Quick question that’s totally off topic. Do you know how to make your site mobile
friendly? My blog looks weird when browsing from my iphone 4.
I’m trying to find a theme or plugin that might be able to correct this issue.
If you have any recommendations, please share. Appreciate it!
Feel free to surf to my web site phen q
Unquestionably consider that that you said. Your favourite justification appeared to be on the
web the easiest thing to have in mind of. I say to you, I definitely get annoyed whilst other folks consider issues that they just don’t recognise about.
You managed to hit the nail upon the highest and also defined
out the entire thing without having side-effects , other people can take a
signal. Will probably be back to get more. Thank you
The other day, while I was at work, my sister stole my iPad and tested
to see if it can survive a 30 foot drop, just so she can be a youtube sensation.
My iPad is now broken and she has 83 views. I know this is completely off topic but I had to share it with someone!
Feel free to visit my webpage; herpesyl benefits
Thanks for finally writing about > SMI diamond grinding wheels billionaire brain wave
Hiya, I am really glad I have found this info. Today bloggers publish only about gossips and net and this is really annoying. A good web site with exciting content, this is what I need. Thanks for keeping this web site, I’ll be visiting it. Do you do newsletters? Can not find it.
Hi, I do believe this is a great web site. I stumbledupon it
😉 I may revisit yet again since I book-marked it.
Money and freedom is the best way to change, may you be rich and continue
to help others.
Look at my page: growth matrix review
I like the valuable information you provide in your articles.
I will bookmark your blog and check again here frequently.
I am quite sure I’ll learn plenty of new stuff right here!
Best of luck for the next!
Have a look at my website … provadent honest review
Hello! I know this is kinda off topic however I’d figured I’d ask.
Would you be interested in trading links or maybe guest writing a blog article
or vice-versa? My website discusses a lot of the same topics as yours and I believe we could greatly benefit from each
other. If you happen to be interested feel free to send me
an email. I look forward to hearing from you! Awesome blog by the way!
Feel free to visit my webpage; the growth matrix
A fascinating discussion is definitely worth comment.
I think that you ought to write more on this
issue, it may not be a taboo subject but typically folks don’t discuss these subjects.
To the next! Kind regards!!
Take a look at my page … nerve fresh
Hello, Neat post. There’s a problem with your site in web explorer, may test this?
IE nonetheless is the market leader and a good section of other people will leave out your wonderful writing because of this problem.
Feel free to surf to my blog post … Brazilian Wood Supplement
Does your site have a contact page? I’m having problems locating it but, I’d like to send you an email.
I’ve got some recommendations for your blog you might be interested in hearing.
Either way, great site and I look forward to seeing it expand
over time.
It’s in reality a great and useful piece of information.
I’m satisfied that you just shared this useful
information with us. Please stay us up to date like this.
Thank you for sharing.
Thanks for sharing such a good thinking, article is good, thats why i
have read it fully
my blog post … tonic greens cure
Link exchange is nothing else but it is simply placing the other
person’s website link on your page at suitable place and other person will also do similar for you.
My blog post smart hemp reviews
Excellent web site. Lots of useful info here. I am sending it to several buddies ans also sharing in delicious.
And of course, thank you to your effort!
My homepage: lottery defeater software reviews
Hello to every body, it’s my first go to see of this weblog; this weblog
includes awesome and really fine information for readers.
Feel free to surf to my web site … lottery
Greetings! Very helpful advice within this article!
It’s the little changes which will make the largest changes.
Many thanks for sharing!
Visit my website: jungle beast pro
Everyone loves what you guys are usually up too. This kind of
clever work and exposure! Keep up the amazing works guys I’ve added you guys to
blogroll.
That is really interesting, You are a very skilled blogger.
I have joined your feed and sit up for seeking extra of your magnificent
post. Also, I’ve shared your website in my social networks
With havin so much content do you ever run into any problems of plagorism or copyright infringement?
My blog has a lot of completely unique content I’ve either created myself or outsourced but it
seems a lot of it is popping it up all over the web without my authorization. Do you know any solutions to help
stop content from being ripped off? I’d truly appreciate it.
Feel free to visit my blog post … tonic greens herpes cure
Thank you, I have recently been looking for information approximately this topic
for ages and yours is the greatest I’ve found out so far.
But, what about the conclusion? Are you sure about the supply?
my blog – tonic greens supplement
This is a really good tip especially to those new to the blogosphere.
Simple but very precise info… Many thanks for sharing this
one. A must read article!
Feel free to surf to my site … pronerve 6
Way cool! Some very valid points! I appreciate you penning this write-up and
also the rest of the website is also really good.
my homepage the growth matrix step by step video
Saved as a favorite, I love your web site!
Check out my blog post is tonic greens fda approved
If you are going for most excellent contents like me, simply visit this web page daily as it presents quality contents, thanks
Feel free to surf to my page – nitric boost ultra reviews
I have been absent for some time, but now I remember why I used to love this blog. Thanks, I will try and check back more frequently. How frequently you update your web site?
After going over a handful of the blog posts on your web site, I seriously like your technique of blogging.
I bookmarked it to my bookmark site list and will be checking back in the near future.
Please check out my website as well and let me know how you feel.
Feel free to visit my webpage – provadent review scam
Hey very cool web site!! Guy .. Beautiful .. Wonderful .. I will bookmark your site and take the feeds also…I am glad to seek out so many useful information right here in the publish, we need develop more strategies in this regard, thank you for sharing.
Thanks for a marvelous posting! I seriously enjoyed reading it, you may be a great author.
I will remember to bookmark your blog and will come back at
some point. I want to encourage that you continue your great writing, have a nice morning!
Here is my webpage :: reviews provadent
This is very attention-grabbing, You are an excessively professional blogger.
I’ve joined your rss feed and stay up for seeking extra of your great post.
Additionally, I have shared your site in my social networks
Here is my homepage – the genius wave reviews and complaints
Normally I don’t learn article on blogs, but I wish to say that this write-up very compelled me to
check out and do so! Your writing taste has been amazed me.
Thank you, quite nice article.
Also visit my web-site: free lottery defeater software reviews
Bookmarked, so I can continuously check on new posts! If you need some details about Blogging, you might want to take a look at Webemail24 Keep on posting!
Magnificent beat ! I wish to apprentice while you amend your website, how could i subscribe for a
blog website? The account aided me a acceptable deal.
I had been a little bit acquainted of this your broadcast provided bright clear concept
Also visit my website lottery defeated reviews
Great post! I learned something new and interesting, which I also happen to cover on my blog. It would be great to get some feedback from those who share the same interest about Search Engine Optimization, here is my website Seoranko Thank you!
Just want to say your article is as amazing. The clarity on your post is
just nice and that i could suppose you’re a professional in this subject.
Well along with your permission allow me to snatch your RSS feed to stay updated with imminent
post. Thanks one million and please keep up the rewarding work.
Simply wish to say your article is as astounding. The clearness to your put up is just excellent and i can suppose you’re an expert in this subject. Well with your permission allow me to take hold of your RSS feed to keep updated with drawing close post. Thanks 1,000,000 and please continue the enjoyable work.
Hey, I enjoyed reading your posts! You have great ideas. Are you looking to get resources about SEO or some new insights? If so, check out my website Article Star
I like what you guys are up also. Such intelligent work and reporting! Keep up the superb works guys I¦ve incorporated you guys to my blogroll. I think it’ll improve the value of my site 🙂
you’ve got an ideal weblog here! would you wish to make some invite posts on my weblog?
Hi everyone, it’s my first pay a quick visit at this
web page, and paragraph is actually fruitful for me, keep
up posting these articles.
My web-site … genius wave scam
What’s up, I log on to your blog regularly. Your story-telling
style is awesome, keep doing what you’re doing!
Have a look at my webpage; provadent reviews
Pretty! This was a really wonderful article. Thanks for supplying
this info.
Feel free to surf to my web blog – the growth matrix reviews
I enjoy what you guys tend to be up too. This kind of clever work and reporting!
Keep up the good works guys I’ve added you guys to blogroll.
Heya i’m for the first time here. I found this board and I find It really
useful & it helped me out a lot. I hope to give something back and help others like
you aided me.
Howdy! This blog post could not be written any better!
Reading through this article reminds me of my previous roommate!
He constantly kept preaching about this. I will send this article to him.
Pretty sure he’ll have a good read. I appreciate you for sharing!
Aw, this was a very nice post. In idea I would like to put in writing like this additionally – taking time and actual effort to make an excellent article… however what can I say… I procrastinate alot and on no account seem to get one thing done.
Pretty great post. I just stumbled upon your blog
and wished to say that I’ve really enjoyed browsing your weblog posts.
In any case I will be subscribing in your rss feed and I am hoping you write
once more soon!
Have a look at my web blog lottery defeater software review
I simply couldn’t depart your web site prior to suggesting that I really loved
the usual information a person supply to your guests? Is going to be back continuously in order to investigate cross-check new posts
My web page: tonic greens reviews herpes
I have to thank you for the efforts you’ve put in writing this website.
I am hoping to check out the same high-grade blog posts by you
later on as well. In truth, your creative writing abilities has inspired
me to get my own, personal blog now 😉
Visit my blog :: lottery defeated software free download
Wow! In the end I got a website from where I be able to truly
obtain valuable facts concerning my study and
knowledge.
Also visit my website: provadent geeks health
Please let me know if you’re looking for a article
writer for your site. You have some really great articles and I think I would be a good
asset. If you ever want to take some of the load off, I’d love to write some material for your blog in exchange for a link
back to mine. Please shoot me an email if interested. Many thanks!
Look into my website :: herpesyl contact number
Excellent, what a webpage it is! This weblog gives useful facts to us, keep it up.
Check out my blog post alpha bites gummies
An intriguing discussion is worth comment.
I believe that you should publish more on this subject matter, it might not be a taboo subject but generally people don’t discuss these topics.
To the next! Many thanks!!
Here is my website … pro nerve 6 for neuropathy
I got this site from my friend who told me regarding this site and now
this time I am visiting this web page and reading very informative content here.
My web-site – lottery defeated software free download
Great article, exactly what I was looking for.
Have a look at my web page; nerve fresh reviews and complaints
Hola! I’ve been reading your weblog for a long time now and finally got the bravery
to go ahead and give you a shout out from Austin Texas!
Just wanted to tell you keep up the excellent job!
Here is my web-site: genius wave scam
I have been surfing on-line more than 3 hours nowadays, but I by no means discovered any fascinating article like yours.
It is beautiful value sufficient for me. In my opinion, if all webmasters and
bloggers made just right content material as you probably did, the net will
probably be much more helpful than ever before.
Here is my page :: pronerve 6 reviews
You could certainly see your enthusiasm within the work you write.
The sector hopes for even more passionate writers
like you who aren’t afraid to mention how they believe.
At all times follow your heart.
Also visit my page … nitric boost ultra powder for sale
If you would like to increase your experience only keep visiting
this site and be updated with the most up-to-date news update posted here.
Have a look at my site; does herpesyl kill herpes
Heya i am for the first time here. I found this board
and I find It really useful & it helped me out much.
I hope to give something back and help others like
you helped me.
Hi there, I found your website by way of Google even as looking for a comparable topic,
your site came up, it looks good. I have bookmarked it in my google bookmarks.
Hi there, simply became aware of your blog thru Google, and
located that it’s really informative. I am gonna watch out for brussels.
I’ll appreciate in case you proceed this in future.
Numerous other people shall be benefited from your writing.
Cheers!
Hi there, I enjoy reading through your article.
I wanted to write a little comment to support you.
Here is my web-site :: lottery defeater software scam
Quality articles or reviews is the important to attract the people to go to see the website, that’s what this
web site is providing.
My homepage; lottery defeater software reviews
Very well written story. It will be useful to everyone who usess it, as well as me. Keep doing what you are doing – can’r wait to read more posts.
I know this site presents quality dependent articles and additional data,
is there any other site which gives these information in quality?
Have you ever thought about adding a little
bit more than just your articles? I mean, what you say is valuable and all.
Nevertheless just imagine if you added some great photos or videos to give your posts more, “pop”!
Your content is excellent but with pics and clips, this site could certainly be one
of the most beneficial in its niche. Amazing blog!
My developer is trying to persuade me to move to .net from PHP.
I have always disliked the idea because of the expenses.
But he’s tryiong none the less. I’ve been using WordPress on a number of websites for about a year and am nervous about switching to another platform.
I have heard great things about blogengine.net.
Is there a way I can import all my wordpress
content into it? Any help would be really appreciated!
Link exchange is nothing else except it is simply placing
the other person’s web site link on your page at appropriate place and other person will also do
same for you.
Hello my family member! I want to say that this article is awesome, great written and include almost all vital infos.
I’d like to look more posts like this .
Nice post. I used to be checking constantly this weblog and I am impressed! Extremely useful info particularly the remaining section 🙂 I handle such info a lot. I was seeking this certain info for a long time. Thanks and good luck.
Greetings! I’ve been reading your web site for some time now and finally got the courage
to go ahead and give you a shout out from Atascocita Tx!
Just wanted to mention keep up the excellent job!
I am no longer certain where you are getting your information,
however good topic. I must spend some time studying more
or working out more. Thank you for great information I used to be
on the lookout for this information for my mission.
Hello, Neat post. There is a problem with your site in web explorer, may test this?
IE still is the market leader and a huge component of other people will omit
your fantastic writing due to this problem.
Good day! I could have sworn I’ve been to this website before but after looking at
some of the articles I realized it’s new to me. Anyways,
I’m definitely pleased I came across it and I’ll be book-marking it and checking
back frequently!
I have been examinating out some of your articles and i must say pretty clever stuff. I will definitely bookmark your site.
No matter if some one searches for his essential thing, thus he/she wishes to be available that in detail, thus that thing is maintained over
here.
What’s up to all, as I am really eager of reading this weblog’s post to be updated daily.
It contains nice material.
Thank you, I’ve recently been searching for information about this topic for ages and yours is the
best I have discovered till now. But, what concerning the bottom
line? Are you positive about the supply?
Hi, Neat post. There is an issue with your website in internet explorer,
would test this? IE still is the marketplace chief and a large
element of other folks will pass over your fantastic writing because of this problem.
Hmm is anyone else experiencing problems with the images on this blog loading? I’m trying to figure out if its a problem on my end or if it’s the blog. Any feed-back would be greatly appreciated.
Hi! I’m at work browsing your blog from my new apple iphone! Just wanted to say I love reading through your blog and look forward to all your posts! Keep up the fantastic work!
I would like to voice my passion for your kindness giving support to folks who have the need for assistance with this study. Your very own dedication to getting the solution all over appeared to be definitely helpful and have really empowered many people just like me to attain their goals. The important help indicates a lot a person like me and extremely more to my peers. Regards; from each one of us.
I like this web site so much, bookmarked. “Nostalgia isn’t what it used to be.” by Peter De Vries.
Awesome! Its truly amazing piece of writing, I have got much clear idea regarding from this post.
my web-site; provadent scam
Wonderful goods from you, man. I’ve understand your stuff previous to and you are just extremely magnificent.
I really like what you’ve acquired here, really like what you’re saying and the way in which
you say it. You make it enjoyable and you still take care of to keep it smart.
I can’t wait to read far more from you. This is really a wonderful
website.
I must thank you for the efforts you’ve put in penning this blog.
I’m hoping to check out the same high-grade content by you in the future
as well. In fact, your creative writing abilities has inspired
me to get my very own site now 😉
my web-site: is fitspresso legit
Heya i’m for the first time here. I came across this board and I find
It truly useful & it helped me out a lot. I hope to give something
back and help others like you aided me.
Review my homepage; the billionaire brain wave program
Howdy just wanted to give you a brief heads up and let you know
a few of the pictures aren’t loading correctly. I’m not sure why but I think
its a linking issue. I’ve tried it in two different web browsers and both show the same results.
Here is my web blog: ingredients in lung clear pro
Hi, I do believe this is an excellent web site.
I stumbledupon it 😉 I am going to come back once again since I saved as a favorite it.
Money and freedom is the greatest way to change, may you
be rich and continue to help others.
Feel free to visit my web-site … pronerve 6 6 reviews and complaints
This is really interesting, You are a very skilled blogger.
I have joined your rss feed and look forward to seeking more of your magnificent post.
Also, I have shared your site in my social networks!
Feel free to surf to my web site … padrão
I just could not go away your web site before
suggesting that I really loved the standard information a person supply on your guests?
Is going to be again regularly in order to check out new posts
Also visit my page – testoprim c 200
Wonderful, what a website it is! This webpage gives helpful data to us, keep it up.
Also visit my web site; glucofreedom capsules
Hello, i believe that i saw you visited my site so i got here to go back
the choose?.I’m attempting to to find issues
to improve my website!I guess its good enough to
use some of your ideas!!
Also visit my website … does tonic greens cure hsv2
Great post. I used to be checking constantly this blog and I am inspired!
Extremely helpful information specially the last part 🙂 I care for such information much.
I was looking for this certain information for a long time.
Thanks and good luck.
My page … prodentim holland and barrett
Thanks for one’s marvelous posting! I definitely enjoyed reading
it, you’re a great author.I will make sure to bookmark your
blog and definitely will come back in the foreseeable future.
I want to encourage continue your great posts, have a nice weekend!
Feel free to surf to my blog; the growth matrix program videos
Hello. fantastic job. I did not expect this. This is a fantastic story. Thanks!
I think this is among the most significant info for me.
And i’m glad reading your article. But should remark on few general things, The web site style is perfect, the articles
is really great : D. Good job, cheers
Also visit my web site :: alpha bites gummies
Hmm is anyone else experiencing problems with the pictures on this blog loading?
I’m trying to find out if its a problem on my end or if it’s the blog.
Any suggestions would be greatly appreciated.
Feel free to visit my homepage … lottery defeater software apk
Very rapidly this web page will be famous among all blogging and site-building visitors,
due to it’s nice content
Feel free to surf to my web page – lottery defeated software review
This is my first time go to see at here and i am actually happy to read all at one
place.
Also visit my web page: the growth matrix leak
This is really interesting, You’re a very skilled blogger.
I’ve joined your feed and look forward to seeking more of your fantastic post.
Also, I’ve shared your site in my social networks!
my blog post tonic greens supplement
This paragraph is truly a nice one it assists new the web visitors,
who are wishing in favor of blogging.
Have a look at my blog post … fitspresso reddit weight loss
I read this paragraph completely concerning the difference of latest and preceding technologies, it’s awesome article.
Feel free to visit my web site; is lung clear pro a scam
Hello just wanted to give you a quick heads up. The words in your article seem
to be running off the screen in Internet explorer. I’m not sure if
this is a formatting issue or something to do with
browser compatibility but I figured I’d post to let you know.
The style and design look great though! Hope you get the problem
resolved soon. Many thanks
Take a look at my blog post … item643629683
Hello! I just would like to give a huge thumbs up for the great info you have here on this post. I will be coming back to your blog for more soon.
Undeniably consider that that you said. Your favourite justification seemed to be at the
web the easiest thing to be mindful of. I say to you, I certainly get irked whilst other people consider issues that they plainly do not understand
about. You managed to hit the nail upon the top as neatly as outlined out the entire
thing without having side effect , people can take a signal.
Will likely be back to get more. Thanks
Also visit my website: alpha bites review
Aw, this was an incredibly good post. Taking a few minutes and actual effort to generate
a good article… but what can I say… I procrastinate a lot and never manage
to get anything done.
my web blog; provadent com scam
My partner and I stumbled over here different web address and thought I might check things out. I like what I see so now i am following you. Look forward to looking over your web page repeatedly.
Hello my loved one! I wish to say that this article is awesome, great
written and come with almost all important infos.
I’d like to see more posts like this .
Also visit my web page does prodentim restore teeth
Hello, yeah this article is truly good and I have learned lot of things from it regarding
blogging. thanks.
Also visit my page … what is nerve fresh
I’m excited to discover this page. I want to to thank you for
your time just for this fantastic read!! I definitely enjoyed every part
of it and i also have you book marked to look at new stuff
in your website.
Visit my web page – does tonic greens get rid of herpes
Hi everyone, it’s my first go to see at this website,
and piece of writing is in fact fruitful designed for me, keep up posting these types
of content.
Also visit my website … dentavim on amazon
I have been surfing online more than 3 hours today,
yet I by no means found any fascinating article like yours.
It is pretty value enough for me. In my opinion, if all website owners and bloggers made excellent content
material as you probably did, the net can be a lot more helpful than ever before.
Feel free to visit my web page: free lottery defeater software reviews
Can I simply just say what a relief to uncover somebody
that genuinely knows what they are discussing on the web.
You actually realize how to bring a problem to light and
make it important. More people should read this and understand this side of the story.
I can’t believe you’re not more popular given that you surely have the gift.
Also visit my webpage – genius wave
Excellent write-up. I absolutely love this website. Thanks!
Here is my homepage: tonic greens reviews
What’s up, this weekend is fastidious designed for me,
because this moment i am reading this great informative post here at my residence.
My site :: fitspresso
Keep this going please, great job!
Here is my blog post; provadent revies
Hello there, just became aware of your blog through Google, and found that it is really informative.
I’m going to watch out for brussels. I will appreciate if you continue this in future.
A lot of people will be benefited from your writing.
Cheers!
My webpage: the genius wave scam
What i don’t realize is actually how you’re now not really a lot more well-preferred than you
may be right now. You are so intelligent. You already know thus significantly when it comes to this
subject, made me for my part consider it from a lot of numerous angles.
Its like men and women aren’t involved until it’s something to accomplish with Woman gaga!
Your own stuffs excellent. All the time care for it up!
Review my homepage :: the growth matrix
Wow, incredible blog layout! How long have you been blogging for?
you make blogging look easy. The overall look of your web site is
wonderful, as well as the content!
my webpage :: tonic greens herpes cure
Appreciating the time and effort you put into your blog and detailed information you offer.
It’s awesome to come across a blog every once in a while that isn’t the same out of date rehashed material.
Fantastic read! I’ve bookmarked your site and I’m adding your RSS feeds to my Google account.
Visit my web page: the lottery defeated software
Great post. I am dealing with many of these issues as well..
Here is my website – fitspresso supplement
If you desire to grow your familiarity simply keep visiting
this site and be updated with the most recent news update posted here.
Look at my web site :: http://www.provadent.com
Thank you for the auspicious writeup. It actually was a enjoyment account it.
Glance complex to far delivered agreeable from you!
By the way, how can we keep in touch?
Review my site … ULTRA K9 PRO
It’s difficult to find knowledgeable people for this subject, however, you seem like you know what you’re talking about!
Thanks
Check out my web page – herpafend reviews
It’s amazing for me to have a website, which is good in support of my knowledge.
thanks admin
Also visit my site … prodentim melts
Keep on writing, great job!
Review my website: vigrx plus nimh
Hi there! Do you know if they make any plugins to safeguard against hackers?
I’m kinda paranoid about losing everything I’ve worked hard on. Any tips?
Feel free to surf to my web-site; In this channel
If you would like to take a good deal from this piece of writing then you have to apply such techniques to your won blog.
Look into my webpage :: tonic greens official website
Great article, exactly what I was looking for.
My web-site – lottery defeater software complaints
Saved as a favorite, I really like your website!
Here is my blog post fitspresso side effects
It’s a shame you don’t have a donate button! I’d most
certainly donate to this excellent blog! I guess for now i’ll settle for book-marking and adding your RSS feed to my Google account.
I look forward to fresh updates and will share this blog with
my Facebook group. Chat soon!
Visit my web page; tonic greens website
Hi there colleagues, its great paragraph on the topic of cultureand completely explained, keep it up all the time.
Review my blog :: LipoZem Weight Loss
Thanks for some other informative web site.
Where else could I get that type of info written in such a perfect manner?
I have a project that I’m simply now operating on, and I’ve been on the look out
for such information.
Also visit my blog fitspresso scam
Hello mates, pleasant article and pleasant arguments commented here,
I am truly enjoying by these.
Feel free to visit my web-site; LipoZem Weight Loss
I think this is one of the most important information for me.
And i’m glad reading your article. But wanna remark on some
general things, The site style is great, the articles is really excellent : D.
Good job, cheers
Here is my web site – how to take tonic greens
You can certainly see your skills within the work you write.
The world hopes for more passionate writers like you who aren’t afraid to
mention how they believe. All the time follow your heart.
Feel free to surf to my webpage – provadent forum
Amazing blog! Do you have any tips for aspiring writers?
I’m planning to start my own website soon but I’m a little lost on everything.
Would you advise starting with a free platform
like WordPress or go for a paid option?
There are so many options out there that I’m totally confused ..
Any ideas? Cheers!
Here is my web blog :: alpha bites
For newest news you have to pay a quick visit
the web and on the web I found this web site as a finest
website for hottest updates.
Feel free to surf to my web blog: alpha bites reviews
Good day I am so thrilled I found your weblog, I really found you by
error, while I was looking on Google for something else, Nonetheless I am
here now and would just like to say thanks a lot for a marvelous post and a all round exciting blog (I also love the theme/design), I
don’t have time to read through it all at the minute but I have bookmarked it and also included
your RSS feeds, so when I have time I will be back to read more, Please
do keep up the superb jo.
Here is my site slim boost tea website
If some one desires to be updated with newest technologies after
that he must be pay a visit this web page and be up to date daily.
Visit my website – lottery defeated software app
Hi there are using WordPress for your blog platform?
I’m new to the blog world but I’m trying to get started and set up my own.
Do you need any coding knowledge to make your own blog?
Any help would be greatly appreciated!
my web site – lottery defeater software
Howdy! Would you mind if I share your blog with
my facebook group? There’s a lot of folks that I think would really appreciate your content.
Please let me know. Thank you
My website; the money wave
I think the admin of this web site is truly working hard in support of
his web page, as here every material is quality based material.
Here is my webpage … provadent in store
Greate post. Keep posting such kind of info on your site.
Im really impressed by your blog.
Hi there, You’ve done an excellent job. I’ll certainly
digg it and personally suggest to my friends.
I’m confident they will be benefited from this website.
Here is my blog post – the billionaire brain wave reviews
Magnificent beat ! I would like to apprentice while you amend your web site, how can i subscribe for a blog
site? The account aided me a acceptable deal.
I had been a little bit acquainted of this your broadcast provided bright clear idea
Feel free to surf to my blog post … the genius wave download
hey there and thank you for your info – I have certainly picked
up anything new from right here. I did however expertise a few technical
points using this web site, as I experienced to reload
the web site a lot of times previous to I could get it to load correctly.
I had been wondering if your hosting is OK? Not that I am complaining, but slow loading instances
times will often affect your placement in google and can damage
your high quality score if ads and marketing with Adwords.
Anyway I’m adding this RSS to my e-mail
and can look out for much more of your respective interesting
content. Make sure you update this again soon.
Feel free to surf to my web blog; billionaire brain waves review
Great site you have here but I was wanting to know if you knew of
any discussion boards that cover the same topics discussed here?
I’d really like to be a part of community where I can get comments from
other experienced people that share the same
interest. If you have any suggestions, please let me
know. Appreciate it!
Feel free to visit my page: renew weight loss supplement
Hello there! I could have sworn I’ve been to
this blog before but after checking through some of the post I realized it’s new to me.
Anyhow, I’m definitely delighted I found it and I’ll be
book-marking and checking back often!
My blog :: lottery defeated software is it a scam
An interesting discussion is worth comment. I think that you ought to publish more about this subject, it might not be a taboo subject but typically folks don’t speak about such issues.
To the next! Many thanks!!
Have a look at my page – tonic greens and herpes
Only a smiling visitor here to share the love (:, btw great design and style. “Everything should be made as simple as possible, but not one bit simpler.” by Albert Einstein.
Excellent post. I’m dealing with many of these issues as well..
My webpage; prodentim reviews
This info is invaluable. Where can I find out more?
Feel free to visit my website: nanodefense pro reviews
I absolutely love your blog.. Excellent colors & theme.
Did you make this website yourself? Please reply back as I’m looking to create my very
own site and would love to find out where you got this from or exactly what the
theme is named. Appreciate it!
Here is my site the growth matrix
I was curious if you ever considered changing the layout of your blog?
Its very well written; I love what youve got to say. But
maybe you could a little more in the way of content so people could connect with it better.
Youve got an awful lot of text for only having 1 or two images.
Maybe you could space it out better?
Also visit my homepage: how do you take provadent
After I initially commented I appear to have clicked the -Notify me when new comments are added-
checkbox and now each time a comment is added I get four emails with the same comment.
Is there an easy method you can remove me from that service?
Many thanks!
Feel free to surf to my webpage … does tonic greens cure hsv2
I need to to thank you for this wonderful read!! I certainly
enjoyed every bit of it. I have got you book-marked to check out new stuff you post…
Feel free to visit my website; lottery defeater software
Hi there, its pleasant article concerning media print, we all be familiar with media
is a wonderful source of information.
My blog post; dentavim reviews
Thank you for the auspicious writeup. It in fact was a amusement account it.
Look advanced to far added agreeable from you! By the way, how can we communicate?
Take a look at my web-site: emperor’s vigor tonic buy online
Hi i am kavin, its my first time to commenting anyplace, when i read this article i thought i
could also create comment due to this sensible paragraph.
Feel free to visit my web-site: the brain money wave
If you want to get much from this paragraph then you have to apply these strategies to your won blog.
Also visit my blog post – alpha bites reviews
Thank you a lot for sharing this with all folks you
really recognise what you’re speaking approximately!
Bookmarked. Please additionally visit my web site =).
We can have a hyperlink change contract among us
Feel free to surf to my web blog :: is the lottery defeated software a scam
I just like the valuable info you supply on your articles. I’ll bookmark your blog and check once more here regularly.
I’m relatively certain I will be informed plenty of new
stuff right here! Best of luck for the following!
This is very interesting, You’re a very skilled blogger.
I have joined your rss feed and look forward to seeking more of your magnificent
post. Also, I have shared your site in my social networks!
I am genuinely grateful to the holder of this website who has shared this wonderful article at at this place.
Hey There. I discovered your weblog the usage of msn. This is a very smartly written article.
I will make sure to bookmark it and come back to learn more of your helpful
information. Thanks for the post. I will definitely
return.
It’s truly very complicated in this active life to listen news on TV, thus I only use internet for that reason, and take
the hottest news.
Hello, Neat post. There is an issue along with your web site in internet explorer, would test this?
IE still is the market leader and a good element of other
people will miss your fantastic writing due to this problem.
It’s awesome to visit this web site and reading
the views of all mates regarding this piece of writing, while I
am also keen of getting familiarity.
Outstanding post however , I was wanting to know if you could write a litte more
on this topic? I’d be very grateful if you could elaborate a little bit further.
Bless you!
Hello there! I know this is kind of off topic but I was wondering which blog
platform are you using for this website? I’m getting fed up of WordPress
because I’ve had problems with hackers and I’m looking at alternatives for another platform.
I would be fantastic if you could point me in the direction of a good platform.
If some one wants to be updated with latest technologies after that he must be
pay a visit this web site and be up to date all the time.
My blog; prodentim official video
I couldn’t resist commenting. Very well written!
Genuinely no matter if someone doesn’t be aware of then its up to other users
that they will help, so here it takes place.
Wow, incredible blog layout! How long have you been blogging for?
you make blogging look easy. The overall look of your website is fantastic, let alone the content!
Hello i am kavin, its my first time to commenting anywhere, when i read this paragraph i thought i could also
create comment due to this good piece of writing.
Simply desire to say your article is as astounding.
The clarity in your post is just cool and i can assume you are an expert on this subject.
Fine with your permission let me to grab your RSS feed to
keep up to date with forthcoming post. Thanks a million and please
continue the enjoyable work.
Having read this I thought it was really enlightening.
I appreciate you finding the time and effort to put this article together.
I once again find myself personally spending a significant amount of time both reading and
leaving comments. But so what, it was still worth it!
If you are going for finest contents like me, simply pay a visit this
web site all the time because it offers quality contents, thanks
I’m not positive the place you’re getting your information, however great topic.
I must spend some time learning much more or figuring out more.
Thanks for great information I used to be looking for this info for my mission.
I like reading a post that will make men and women think.
Also, thank you for allowing for me to comment!
Feel free to surf to my homepage nanodefense pro review consumer reports
Howdy just wanted to give you a quick heads up.
The text in your post seem to be running off the screen in Internet explorer.
I’m not sure if this is a format issue or something to do with web browser compatibility but I thought I’d post
to let you know. The design and style look great though!
Hope you get the issue fixed soon. Many thanks
Have you ever considered about adding a little bit more than just your articles?
I mean, what you say is valuable and all. Nevertheless think about if
you added some great pictures or videos to give your posts more, “pop”!
Your content is excellent but with images and clips, this blog could definitely be one of the
very best in its field. Wonderful blog!
Check out my website; billionaire brain wave free download pdf
After checking out a number of the blog posts on your site,
I honestly appreciate your technique of writing a blog.
I book-marked it to my bookmark webpage list and will be checking back in the near
future. Take a look at my website too and tell me your opinion.
Also visit my blog; dentavim
These are truly impressive ideas in regarding blogging.
You have touched some fastidious things here. Any way keep up wrinting.
Feel free to visit my web site; glucofreedom amazon reviews
Hi it’s me, I am also visiting this web site daily, this website is actually pleasant and the people
are really sharing good thoughts.
my web page … billionaire brain wave free download
Hey there just wanted to give you a brief heads up and let you know a few of the images
aren’t loading properly. I’m not sure why but I
think its a linking issue. I’ve tried it in two different
web browsers and both show the same results.
Take a look at my site … nerve fresh supplement
Hello Dear, are you really visiting this web site daily, if so
afterward you will absolutely get pleasant knowledge.
Feel free to visit my page … glucofreedom capsules
Undeniably consider that which you said. Your favorite reason seemed to be at the web the simplest
thing to be mindful of. I say to you, I definitely get annoyed whilst other people
consider worries that they just don’t understand about. You managed to hit the nail upon the top and outlined out the whole thing without having side
effect , other people could take a signal. Will probably be back to get more.
Thanks
my blog :: purdentix drew sutton
Amazing blog! Is your theme custom made or did you download it from somewhere?
A theme like yours with a few simple tweeks would really make
my blog stand out. Please let me know where you got your
theme. Bless you
Here is my blog post; iq blast pro video
Normally I don’t learn article on blogs, but I would like to
say that this write-up very forced me to check out and do it!
Your writing style has been amazed me. Thank you, quite great article.
Also visit my blog post – what is iq blast pro
I got this web site from my buddy who informed me about this web page and now this time I am browsing this
web site and reading very informative posts at this time.
Check out my site; where can i buy herpesyl
I was curious if you ever thought of changing the page layout of your
site? Its very well written; I love what youve got to say.
But maybe you could a little more in the way of content so
people could connect with it better. Youve got an awful lot of
text for only having 1 or 2 images. Maybe you could space it out better?
Feel free to surf to my site nervefresh
Hello, I check your new stuff daily. Your humoristic style is witty, keep up the good work!
Visit my website: phenq week 2
You actually make it seem so easy with your presentation but I
find this matter to be really something that I think I would never understand.
It seems too complicated and very broad for me. I am looking forward for your
next post, I will try to get the hang of it!
Feel free to surf to my homepage: when was herpesyl invented
Awesome post.
my web-site :: free sugar pro
Hi to all, how is everything, I think every one is getting more from this web page, and your views are
nice for new users.
Have a look at my homepage … lottery winnings calculator
Hey! I realize this is kind of off-topic however I had to ask.
Does managing a well-established website such as yours require a large
amount of work? I am brand new to running a blog but I do
write in my journal everyday. I’d like to start a blog so I can easily share
my personal experience and views online. Please let me know if
you have any suggestions or tips for brand new aspiring bloggers.
Thankyou!
my web site: does iq blast pro really work
I have to thank you for the efforts you’ve put in writing this blog.
I really hope to check out the same high-grade blog posts by you in the future as well.
In fact, your creative writing abilities has encouraged me
to get my own site now 😉
Here is my web site – the genius wave download
Hello, i believe that i noticed you visited my web site so i came to go back the desire?.I am trying to to find things to enhance my
site!I guess its ok to make use of a few of your ideas!!
My web-site – plantsulin honest review
I know this if off topic but I’m looking into starting
my own weblog and was curious what all is needed to get set up?
I’m assuming having a blog like yours would cost a pretty
penny? I’m not very internet smart so I’m not 100% positive.
Any tips or advice would be greatly appreciated. Thanks
Feel free to visit my web-site :: best lottery defeated software free
Highly descriptive article, I enjoyed that a lot.
Will there be a part 2?
My site: emperor vigor tonic para que sirve en español
My brother suggested I might like this blog. He was entirely right.
This post truly made my day. You can not imagine simply how much time I had spent for this info!
Thanks!
my webpage :: gluco freedom reviews
Nice post. I was checking continuously this blog and I’m impressed!
Extremely helpful info specifically the last part 🙂 I
care for such info a lot. I was looking for this certain information for a very long time.
Thank you and good luck.
Here is my site: the growth matrix program videos
I think what you published was actually very logical.
However, what about this? suppose you were to create a killer title?
I mean, I don’t want to tell you how to run your website, however suppose you added a
post title to possibly grab folk’s attention? I mean SMI diamond grinding
wheels is kinda plain. You could look at Yahoo’s front page and note how they create news titles to get people
to open the links. You might add a related video or a picture or two to
get readers excited about everything’ve written.
Just my opinion, it would bring your website a little livelier.
my web page: prodentim reviews
Ahaa, its pleasant conversation on the topic of this paragraph at this
place at this weblog, I have read all that, so at this time me also commenting here.
Here is my site – lottery defeater software app free download
I am extremely impressed together with your writing talents and also
with the structure for your blog. Is this a paid subject matter or did you customize it
your self? Either way keep up the excellent high quality writing, it is uncommon to look a great weblog like this one these days..
Also visit my web-site: better business bureau provadent
Can you tell us more about this? I’d like to find out
some additional information.
My website; nerve fresh reviews and complaints
Write more, thats all I have to say. Literally, it seems
as though you relied on the video to make your point. You
definitely know what youre talking about, why waste your
intelligence on just posting videos to your weblog when you could be giving us something
informative to read?
Also visit my web page … tonic greens and herpes
Hi there, its fastidious paragraph regarding media print, we all know media is
a impressive source of information.
Look at my blog nitric boost ultra for men
Thank you for the good writeup. It in fact
was a amusement account it. Look advanced to far added
agreeable from you! By the way, how could we communicate?
Here is my web blog: alpha bites reviews
Hmm it appears like your site ate my first comment (it
was extremely long) so I guess I’ll just sum it up what I submitted and say, I’m
thoroughly enjoying your blog. I too am an aspiring blog blogger
but I’m still new to the whole thing. Do you have any tips
for beginner blog writers? I’d genuinely appreciate it.
Review my web page :: the growth matrix free online
My coder is trying to persuade me to move to .net from PHP.
I have always disliked the idea because of the expenses.
But he’s tryiong none the less. I’ve been using Movable-type on numerous websites
for about a year and am anxious about switching to another platform.
I have heard good things about blogengine.net.
Is there a way I can import all my wordpress posts into
it? Any help would be greatly appreciated!
My web-site :: IQ Blast Pro available for purchase in USA
Hi just wanted to give you a quick heads up and let you know a few of the images
aren’t loading correctly. I’m not sure why but I think its a
linking issue. I’ve tried it in two different internet browsers and both
show the same results.
Here is my web site :: provadent review scam
Having read this I thought it was very informative.
I appreciate you spending some time and effort to put
this content together. I once again find myself
spending way too much time both reading and posting comments.
But so what, it was still worth it!
Here is my webpage alpha bites review 2024
Right now it appears like Expression Engine is the
preferred blogging platform available right now. (from what I’ve read) Is that what you’re using
on your blog?
My web-site; the growth matrix step by step youtube reddit
We stumbled over here coming from a different web
address and thought I might check things out.
I like what I see so now i am following you. Look forward to looking into your web page again.
Feel free to visit my website: iq blast pro review
Your mode of telling all in this article is genuinely good, every one can simply know it, Thanks a lot.
Here is my page; free suga pro reviews
Valuable information. Lucky me I discovered your
site by accident, and I’m shocked why this accident didn’t took place in advance!
I bookmarked it.
my homepage: the genius wave review
Howdy! Someone in my Myspace group shared this website with us so I came to look
it over. I’m definitely enjoying the information. I’m bookmarking and will be tweeting this to my followers!
Exceptional blog and outstanding design and style.
Also visit my page … gluco freedom
It’s not my first time to pay a visit this website, i am browsing this website
dailly and obtain fastidious facts from here everyday.
My blog post – tonic greens reviews
Hello! This is my first visit to your blog! We are a collection of volunteers and starting
a new initiative in a community in the same niche.
Your blog provided us beneficial information to work on. You have done a extraordinary job!
my homepage genius wave free
Magnificent beat ! I wish to apprentice even as you amend your web site, how could i subscribe for a blog web site?
The account helped me a applicable deal. I were tiny bit familiar of this your broadcast offered brilliant clear idea
Here is my web blog alpha bites reviews
I want to to thank you for this wonderful read!!
I absolutely enjoyed every bit of it. I have you saved as a favorite to look at new
things you post…
My blog post – provadent directions for use
Hey there! I could have sworn I’ve been to this site before but after checking through some of the post I
realized it’s new to me. Nonetheless, I’m definitely glad I
found it and I’ll be bookmarking and checking back often!
my homepage alpha bites review
Nice post. I learn something totally new and challenging on sites I stumbleupon everyday.
It’s always useful to read through articles from other authors and practice something from other websites.
my blog post: Lipozem for effective weight loss and fat burning
I have read so many articles regarding the blogger lovers except this piece of writing is genuinely a nice paragraph, keep it up.
Here is my web page … provadent reviews usa
I’m not sure exactly why but this blog is loading very slow for
me. Is anyone else having this issue or is it
a problem on my end? I’ll check back later on and see if the problem still exists.
Also visit my blog post; does pro nerve 6 work
Today, I went to the beach front with my children. I found a sea shell and gave it to my 4 year old daughter and said
“You can hear the ocean if you put this to your ear.” She put the
shell to her ear and screamed. There was a hermit crab inside and
it pinched her ear. She never wants to go back!
LoL I know this is completely off topic but I had to tell someone!
My blog post: UltraK9 Pro
I just like the helpful info you provide for
your articles. I will bookmark your weblog and
take a look at again here regularly. I’m slightly certain I will be informed a lot
of new stuff right here! Good luck for the following!
my page: lottery defeater software
I know this if off topic but I’m looking into starting my own blog and was wondering what all is required to get set up?
I’m assuming having a blog like yours would cost a pretty penny?
I’m not very internet savvy so I’m not 100% sure.
Any recommendations or advice would be greatly appreciated.
Thanks
my website – genius wave review
Fantastic blog! Do you have any helpful hints for
aspiring writers? I’m planning to start my own site
soon but I’m a little lost on everything. Would you
advise starting with a free platform like WordPress or go for a paid option? There are
so many options out there that I’m completely overwhelmed ..
Any ideas? Kudos!
Feel free to surf to my web blog … tonic greens benefits
If you are going for best contents like me, simply go to see this site all the
time because it presents quality contents, thanks
Feel free to surf to my website alpha bites gummy
I used to be suggested this blog by my cousin. I am not positive whether or not this submit is written by
way of him as nobody else know such specific approximately
my difficulty. You are amazing! Thanks!
My blog … is the growth matrix real
My brother suggested I might like this blog.
He was entirely right. This post actually made
my day. You cann’t imagine simply how much time I had spent for this info!
Thanks!
Stop by my web site alpha bites order
Hi, I do think this is an excellent blog. I stumbledupon it 😉 I’m going to come back once again since i have book
marked it. Money and freedom is the greatest way to change, may you be rich and continue to guide others.
Also visit my web site; tonic greens ingredients
Howdy! I realize this is kind of off-topic but I needed to ask.
Does building a well-established website like yours require a lot of work?
I’m completely new to writing a blog however I do write in my journal every day.
I’d like to start a blog so I can share my own experience and feelings online.
Please let me know if you have any kind of recommendations or
tips for brand new aspiring blog owners. Thankyou!
Review my web blog plantsulin reviews
Hi friends, pleasant post and good urging commented here, I
am truly enjoying by these.
Also visit my web site drew sutton purdentix scam
It is in point of fact a great and useful piece of information.
I’m happy that you simply shared this helpful info with us.
Please keep us informed like this. Thank you for sharing.
Look into my page; is free sugar pro a scam
Have you ever thought about adding a little bit more than just your articles?
I mean, what you say is fundamental and all. But think
about if you added some great graphics or video clips to give your posts more, “pop”!
Your content is excellent but with pics and clips,
this site could certainly be one of the most beneficial in its field.
Good blog!
Here is my website pro nerve 6 review
I¦ve recently started a website, the information you provide on this site has helped me tremendously. Thank you for all of your time & work.
you are in reality a good webmaster. The web site loading speed is amazing.
It seems that you are doing any unique trick. In addition, The contents are masterpiece.
you have performed a excellent task in this subject!
Also visit my web blog plantsulin capsules
Good way of telling, and fastidious piece of writing to get data regarding my presentation subject
matter, which i am going to deliver in academy.
Here is my homepage does herpafend cure herpes
Great goods from you, man. I’ve understand your
stuff prior to and you’re just extremely excellent. I really like what you have acquired here,
really like what you’re saying and the best way wherein you assert it.
You’re making it entertaining and you still care for to keep
it wise. I cant wait to read far more from you.
That is actually a wonderful site.
my web page: clkbank provadent
Today, I went to the beach with my children.
I found a sea shell and gave it to my 4 year old daughter
and said “You can hear the ocean if you put this to your ear.”
She placed the shell to her ear and screamed. There was a hermit crab
inside and it pinched her ear. She never wants to go back!
LoL I know this is completely off topic but I had to tell
someone!
Visit my blog post … The Billionaire Brain Wave reviews
Usually I do not read post on blogs, however I wish to say that this write-up
very forced me to take a look at and do it! Your writing style has
been surprised me. Thank you, quite nice article.
Also visit my site – herpafend ingredients
Hi there! I understand this is sort of off-topic however I had to ask.
Does running a well-established blog such as
yours take a large amount of work? I am completely new to writing a blog however I do write in my journal every day.
I’d like to start a blog so I can share my own experience and feelings online.
Please let me know if you have any ideas or tips for new aspiring bloggers.
Appreciate it!
Feel free to visit my site – is provadent a scam or legit
Nice blog here! Also your site loads up very fast!
What host are you using? Can I get your affiliate link to
your host? I wish my web site loaded up as quickly as yours lol
my site; purdentix telephone number
Thank you for the auspicious writeup. It in reality was once a enjoyment account it.
Look complex to more added agreeable from you! By the way, how can we keep in touch?
Also visit my blog :: is emperor’s vigor tonic safe
Greetings! Very useful advice within this article! It is
the little changes that make the most significant changes.
Thanks a lot for sharing!
my site money wave reviews and complaints
This piece of writing presents clear idea
for the new visitors of blogging, that really how to do running a
blog.
Feel free to visit my page … pronerve 6
This is my first time pay a visit at here and i am in fact happy to read all at one place.
Here is my site :: the growth matrix reviews
Howdy! I know this is kinda off topic but I was wondering which blog platform
are you using for this site? I’m getting fed up of WordPress because I’ve had problems with hackers
and I’m looking at alternatives for another platform.
I would be great if you could point me in the direction of
a good platform.
Also visit my web blog prodentim pro dentim advanced oral probiotics reviews
Today, I went to the beach front with my kids. I found a sea shell and gave it to my
4 year old daughter and said “You can hear the ocean if you put this to your ear.” She placed the shell to her ear and screamed.
There was a hermit crab inside and it pinched her ear.
She never wants to go back! LoL I know this is entirely
off topic but I had to tell someone!
Here is my web-site … purdentix cvs
That is very attention-grabbing, You’re an overly skilled blogger.
I’ve joined your rss feed and stay up for in search of more of your fantastic post.
Additionally, I have shared your website in my social networks
Also visit my blog … provadent real or fake
Hi to every body, it’s my first visit of this website; this website contains
remarkable and in fact excellent information in support
of readers.
Here is my page: provadent
It’s going to be ending of mine day, but before end I am reading
this great post to increase my know-how.
My homepage; the.growth matrix
Very nice post. I just stumbled upon your blog and wished to say that I’ve really enjoyed browsing
your blog posts. In any case I’ll be subscribing to your
rss feed and I hope you write again very soon!
Here is my page :: tonic greens review
Today, I went to the beach with my kids. I found a sea shell and gave it to my 4 year
old daughter and said “You can hear the ocean if you put this to your ear.”
She placed the shell to her ear and screamed. There was a hermit crab inside and it pinched her ear.
She never wants to go back! LoL I know this is totally off topic but I
had to tell someone!
my webpage: does tonic greens really work
I am not sure where you’re getting your info, but great topic.
I needs to spend some time learning much more or understanding more.
Thanks for fantastic info I was looking for this information for my mission.
Stop by my page :: tonic greens herpes review
Thank you a bunch for sharing this with all people you actually recognize what you’re speaking about!
Bookmarked. Please also talk over with my site =). We will have a link trade agreement among us
my web blog: alpha bites gummies
After I initially left a comment I appear to have clicked on the -Notify me when new comments are added- checkbox and
from now on each time a comment is added I receive 4 emails with the same comment.
Is there an easy method you are able to remove me from that service?
Many thanks!
Take a look at my blog post – what is tonic greens
Touche. Sound arguments. Keep up the good work.
My blog: herpesyl pills reviews
Hi there, I found your blog by the use of Google whilst looking for a comparable topic, your site came up, it seems to be great.
I’ve bookmarked it in my google bookmarks.
Hello there, simply became aware of your weblog via Google,
and found that it’s really informative. I’m going to watch out for
brussels. I will appreciate in the event you continue this in future.
Numerous people will probably be benefited out of your writing.
Cheers!
Here is my webpage … provadent ingredients label
With havin so much content do you ever run into any problems of plagorism or copyright violation? My site has a lot of
completely unique content I’ve either written myself or
outsourced but it seems a lot of it is popping it up all over the web without my authorization. Do you know any techniques to help
reduce content from being ripped off? I’d definitely appreciate it.
Here is my page – alpha bites review
Thanks a lot for sharing this with all people you actually know what you’re talking about!
Bookmarked. Kindly also visit my web site =). We could have a hyperlink exchange agreement among us
My webpage … alpha bites gummy
Pretty component of content. I just stumbled upon your blog and in accession capital
to claim that I acquire in fact enjoyed account your blog posts.
Anyway I will be subscribing for your feeds and even I success you get right of entry to persistently fast.
Feel free to surf to my blog post; is purdentix real
Hey! This is my first comment here so I just wanted to give a quick
shout out and say I genuinely enjoy reading your articles. Can you recommend any other blogs/websites/forums that deal with the same subjects?
Thanks a lot!
Feel free to surf to my homepage – where can i get provadent
Wow, that’s what I was looking for, what a information! existing here
at this blog, thanks admin of this web page.
Here is my site: tonic greens official website
Wow! This blog looks just like my old one! It’s on a
totally different topic but it has pretty much the same layout and design. Outstanding choice of colors!
Also visit my web site: provadent reviews trustpilot
whoah this blog is magnificent i really like studying your posts.
Keep up the great work! You realize, lots of persons are searching around for
this info, you could aid them greatly.
Feel free to visit my homepage: lipo zem
It’s amazing to go to see this site and reading the views of all friends on the
topic of this post, while I am also keen of getting familiarity.
My page – pronerve 6 reviews
Hi, this weekend is pleasant designed for me, because this point
in time i am reading this fantastic educational paragraph here at my residence.
Have a look at my page :: pro nerve 6 ingredients list
Have you ever thought about adding a little bit more than just your articles?
I mean, what you say is fundamental and everything.
However imagine if you added some great photos or video clips
to give your posts more, “pop”! Your content is excellent but with images
and videos, this website could undeniably be one of
the very best in its niche. Amazing blog!
When someone writes an post he/she keeps the image of a user in his/her
mind that how a user can be aware of it. Thus that’s why this paragraph is perfect.
Thanks!
I visited multiple web pages however the audio quality for audio songs
present at this website is in fact superb.
Thanks for some other fantastic post. The place else could anyone get
that type of information in such an ideal method of writing?
I’ve a presentation subsequent week, and I am on the look for such information.
Hi, I think your site might be having browser compatibility issues.
When I look at your website in Ie, it looks fine but when opening in Internet Explorer, it has some overlapping.
I just wanted to give you a quick heads up!
Other then that, great blog!
Howdy would you mind sharing which blog platform
you’re using? I’m going to start my own blog soon but I’m having a hard time deciding between BlogEngine/Wordpress/B2evolution and Drupal.
The reason I ask is because your design and style seems different
then most blogs and I’m looking for something unique.
P.S Apologies for being off-topic but I had to ask!
Heya! I just wanted to ask if you ever have any issues with hackers?
My last blog (wordpress) was hacked and I ended up losing months of hard work due to
no data backup. Do you have any solutions to protect against hackers?
I have been browsing online more than three hours today, yet I never discovered any fascinating article like yours.
It is lovely value enough for me. In my opinion, if all
web owners and bloggers made excellent content as you probably did,
the web will likely be a lot more helpful than ever before.
Every weekend i used to pay a quick visit this site, because i want enjoyment,
for the reason that this this web page conations genuinely good funny data too.
Hey there, You’ve done an excellent job.
I’ll certainly digg it and personally suggest to my friends.
I’m confident they will be benefited from this site.
Hey! Do you know if they make any plugins to help with SEO?
I’m trying to get my site to rank for some targeted keywords but I’m not seeing very good gains.
If you know of any please share. Kudos! I saw similar article here:
Blankets
I don’t know whether it’s just me or if everybody else experiencing issues with your website.
It appears as though some of the text within your
posts are running off the screen. Can someone else please provide feedback and let me know if
this is happening to them too? This could be a problem with my internet
browser because I’ve had this happen before. Thanks
Please let me know if you’re looking for a writer for
your site. You have some really great articles and I think I would be a good asset.
If you ever want to take some of the load off, I’d really
like to write some material for your blog in exchange for a link back
to mine. Please send me an e-mail if interested. Cheers!
Good day! This is my 1st comment here so I just wanted to give a quick shout out and say I truly enjoy reading your articles.
Can you suggest any other blogs/websites/forums that
deal with the same topics? Thank you!
Hey there! I’ve been following your weblog for a while now and finally got
the bravery to go ahead and give you a shout out from Kingwood Tx!
Just wanted to tell you keep up the excellent job!
GGDEWA777 sebuah sarana permainan terbesar di Indonesia, yang memberikan permainan toto togel, slot,
casino, poker dan sport
Hey! This is kind of off topic but I need some advice
from an established blog. Is it very difficult to set up your own blog?
I’m not very techincal but I can figure things out pretty quick.
I’m thinking about setting up my own but I’m not sure where to start.
Do you have any points or suggestions? Appreciate it
It’s actually very complex in this busy life to listen news on Television, so I simply use internet for that purpose, and take the
hottest news.
Hi, I want to subscribe for this website to take most
recent updates, so where can i do it please help.
Do you mind if I quote a few of your articles as long as
I provide credit and sources back to your weblog?
My website is in the very same area of interest as yours and my visitors would certainly benefit from a lot of the
information you present here. Please let me know if this ok with you.
Thanks!
Its such as you learn my thoughts! You seem to know a lot approximately this,
such as you wrote the guide in it or something. I believe that you simply could do with
some % to drive the message house a little bit, however other than that, that is fantastic
blog. An excellent read. I will definitely be back.
If you would like to increase your know-how just keep visiting this site and be
updated with the most up-to-date information posted here.
Hello there! This is kind of off topic but I need some help from an established blog.
Is it very hard to set up your own blog? I’m not very techincal but I can figure things out pretty quick.
I’m thinking about setting up my own but I’m not sure
where to begin. Do you have any ideas or suggestions?
Appreciate it
Hello to all, it’s in fact a good for me to visit this web site, it includes important Information.
Oh my goodness! Impressive article dude! Thank you
so much, However I am having troubles with your RSS. I don’t know the reason why
I can’t subscribe to it. Is there anybody else getting identical
RSS problems? Anybody who knows the solution will you kindly respond?
Thanx!!
If some one wishes expert view regarding blogging and site-building then i suggest him/her to go to see this website, Keep up the fastidious work.
Hello! Do you know if they make any plugins to help with SEO?
I’m trying to get my website to rank for some targeted keywords but I’m not seeing
very good gains. If you know of any please share. Many thanks!
I saw similar article here: Blankets
It’s really a nice and useful piece of information. I am glad that you shared this useful information with us. Please keep us informed like this. Thanks for sharing.
Way cool! Some extremely valid points! I appreciate you penning this article and also the rest of the
site is also really good.
It’s actually a cool and helpful piece of information. I’m glad that you just shared
this helpful info with us. Please stay us up to date like this.
Thanks for sharing.
Hello would you mind letting me know which webhost you’re using?
I’ve loaded your blog in 3 different web browsers and
I must say this blog loads a lot quicker then most. Can you recommend a good hosting provider at a reasonable price?
Thank you, I appreciate it!
When no response came in six hours, Winston Churchill gave the order to attack.
Excellent article! We will be linking to this great
article on our website. Keep up the great writing.
Hello my family member! I want to say that this post is amazing, great written and
include almost all important infos. I would like to look more posts like this .
Yes! Finally something about domperidone.
Outstanding post however I was wondering if you could write a litte more on this topic? I’d be very grateful if you could elaborate a little bit further. Cheers!
I am extremely impressed with your writing abilities and also with the format
for your blog. Is that this a paid theme or did you customize it your self?
Anyway keep up the excellent quality writing, it’s uncommon to see a great blog like this one these days..
This design is incredible! You most certainly know how to keep a reader entertained. Between your wit and your videos, I was almost moved to start my own blog (well, almost…HaHa!) Fantastic job. I really enjoyed what you had to say, and more than that, how you presented it. Too cool!
Its like you read my mind! You appear to know a
lot about this, like you wrote the book in it or something.
I think that you can do with some pics to drive the message home a little bit, but instead of that, this is great blog.
A fantastic read. I’ll certainly be back.
I am regular visitor, how are you everybody?
This paragraph posted at this web site is genuinely nice.
sugar defender reviews As a person who’s always bewared
concerning my blood glucose, finding Sugar Protector has been an alleviation. I feel a lot extra in control, and my recent check-ups have actually revealed favorable improvements.
Recognizing I have a dependable supplement to support my regular provides me satisfaction.
I’m so thankful for Sugar Protector’s effect on my health!
Hey! I know this is somewhat off topic but I was wondering if you knew where I could
find a captcha plugin for my comment form? I’m using the same blog platform as yours and I’m having problems finding one?
Thanks a lot!
I think the admin of this web page is really working hard in favor of his
site, because here every data is quality based material.
Howdy, i read your blog from time to time and i own a similar one and i was just
curious if you get a lot of spam feedback? If so how do
you stop it, any plugin or anything you can advise?
I get so much lately it’s driving me mad so any assistance is very
much appreciated.
It’s really a nice and useful piece of info. I am satisfied that you simply shared this useful info with us.
Please stay us up to date like this. Thanks for sharing.
Pretty! This has been a really wonderful post.
Thank you for providing this info.
Hey! I could have sworn I’ve been to this site before but after checking through some of
the post I realized it’s new to me. Anyways, I’m definitely happy I found it and I’ll be
bookmarking and checking back frequently!
It’s actually a great and helpful piece of info. I’m glad that you just shared this useful info
with us. Please stay us up to date like this. Thank you for sharing.
Yes! Finally someone writes about Mediabola78.
I don’t even understand how I ended up here, however I thought this post was good.
I do not know who you’re but certainly you are going to a
well-known blogger for those who aren’t already. Cheers!
Hello, of course this paragraph is genuinely fastidious and I have learned lot of things from it about blogging.
thanks.
Magnificent goods from you, man. I’ve understand your stuff previous to and
you’re just too fantastic. I actually like what you have acquired here,
certainly like what you’re stating and the way in which you
say it. You make it enjoyable and you still take care of to keep it wise.
I cant wait to read far more from you. This is really a wonderful web
site.
I seriously love your blog.. Great colors & theme. Did you create this website yourself?
Please reply back as I’m looking to create my own site and would like to know where you got this from
or just what the theme is named. Many thanks!
Excellent weblog right here! Also your site rather
a lot up fast! What host are you the use of? Can I am getting your affiliate link in your host?
I want my site loaded up as fast as yours lol
Very quickly this web site will be famous amid all
blog people, due to it’s good articles or reviews
Link exchange is nothing else except it is simply placing the other person’s blog
link on your page at appropriate place and other person will also do same in favor of you.
I’m curious to find out what blog platform you are using?
I’m experiencing some minor security issues with my latest website and I’d like to find something
more safe. Do you have any recommendations?
It’s perfect time to make some plans for the future and it’s time to be happy.
I have read this post and if I could I wish to suggest you few
interesting things or tips. Maybe you can write next articles referring to
this article. I wish to read more things about it!
Very good information. Lucky me I discovered
your blog by accident (stumbleupon). I have bookmarked
it for later!
Great website. A lot of helpful info here. I am sending it to some pals ans additionally sharing in delicious.
And naturally, thank you to your effort!
This site was… how do I say it? Relevant!! Finally I have found something which helped me.
Appreciate it!
Hello! Someone in my Facebook group shared this site with us so
I came to check it out. I’m definitely loving the information. I’m book-marking
and will be tweeting this to my followers! Excellent blog and fantastic style and design.
Hey just wanted to give you a quick heads up.
The text in your content seem to be running off the screen in Firefox.
I’m not sure if this is a formatting issue or something to do with web browser compatibility but I thought
I’d post to let you know. The layout look great though!
Hope you get the issue solved soon. Kudos
Everything is very open with a very clear explanation of
the challenges. It was truly informative. Your website is very helpful.
Many thanks for sharing!
Hello there! This is kind of off topic but I need some guidance from an established blog.
Is it difficult to set up your own blog? I’m not very techincal but I can figure things out pretty quick.
I’m thinking about creating my own but I’m not sure where to begin. Do you have any
ideas or suggestions? Many thanks
I do not even understand how I finished up here,
however I assumed this submit was good. I do not recognize who you’re but certainly you are
going to a famous blogger should you are not already.
Cheers!
Have you ever considered about adding a little bit more than just your articles?
I mean, what you say is important and everything. Nevertheless just imagine if
you added some great pictures or video clips to give your posts more,
“pop”! Your content is excellent but with pics and video
clips, this blog could certainly be one of the very best in its field.
Very good blog!
I have been exploring for a bit for any high quality articles or
blog posts on this kind of area . Exploring in Yahoo
I ultimately stumbled upon this website. Studying this info So i’m glad to show that I have an incredibly excellent uncanny feeling I came upon exactly what I needed.
I so much indubitably will make certain to don?t omit
this website and provides it a glance on a continuing
basis.
Just desire to say your article is as astonishing.
The clarity in your post is just nice and
i could assume you are an expert on this subject.
Fine with your permission allow me to grab your feed to keep up to date with forthcoming post.
Thanks a million and please keep up the rewarding work.
I blog frequently and I really appreciate your content.
Your article has truly peaked my interest. I am going to book mark your
website and keep checking for new information about once per week.
I subscribed to your Feed too.
Simply wish to say your article is as surprising. The clarity on your submit is just spectacular and that i could think
you’re an expert in this subject. Fine together with your permission let me to clutch your feed to keep updated with approaching post.
Thank you one million and please keep up the rewarding work.
Post writing is also a fun, if you know afterward you can write or else it is complicated to write.
I think what you said was actually very logical.
But, what about this? what if you were to create a killer post title?
I mean, I don’t want to tell you how to run your blog, however suppose you added a
post title that makes people desire more? I mean SMI diamond grinding wheels is a little vanilla.
You could glance at Yahoo’s front page and note
how they create article headlines to grab people to click.
You might add a video or a picture or two to grab readers excited about what you’ve written. In my opinion, it could make your website a little livelier.
My coder is trying to convince me to move to .net from PHP.
I have always disliked the idea because of the costs.
But he’s tryiong none the less. I’ve been using Movable-type on numerous websites for about a year and am nervous about switching to
another platform. I have heard great things about blogengine.net.
Is there a way I can transfer all my wordpress posts into it?
Any kind of help would be greatly appreciated!
If some one wishes to be updated with latest technologies afterward
he must be pay a visit this site and be up to date all
the time.
I appreciate, result in I found just what I was looking for.
You’ve ended my 4 day long hunt! God Bless you man. Have a nice day.
Bye
Hello my loved one! I wish to say that this article is amazing,
nice written and include almost all significant infos.
I would like to see extra posts like this .
Wonderful article! This is the type of info that are meant to
be shared across the web. Shame on Google for not positioning this post higher!
Come on over and discuss with my web site .
Thank you =)
Feel free to visit my blog post: lottery defeated software for android
Way cool! Some very valid points! I appreciate
you penning this post and also the rest of the
website is extremely good.
Feel free to surf to my web site provadent what is it
Great work! This is the type of information that are supposed
to be shared across the net. Shame on the search engines for not positioning this publish upper!
Come on over and talk over with my site . Thank
you =)
Hello, I enjoy reading all of your article post.
I like to write a little comment to support you.
Also visit my webpage pronerve 6 scam
When I initially left a comment I seem to have clicked on the -Notify
me when new comments are added- checkbox and from now
on whenever a comment is added I get four emails with
the exact same comment. There has to be a way you can remove me from that service?
Thank you!
Take a look at my website; lipo zem
whoah this blog is magnificent i really like
reading your articles. Keep up the great work! You understand, lots of persons are hunting around for this info,
you could help them greatly.
Hey great blog! Does running a blog such as this take a large amount of work?
I have absolutely no understanding of programming however I had been hoping to start my own blog in the
near future. Anyhow, should you have any suggestions or techniques
for new blog owners please share. I know this is off topic however I just wanted to ask.
Thanks!
My site … phenq alternative
magnificent submit, very informative. I ponder why
the opposite experts of this sector do not notice
this. You should continue your writing. I am sure, you have a great readers’ base already!
Feel free to surf to my web page – what is herpafend
Just want to say your article is as surprising. The clearness in your post is simply spectacular and i
could assume you’re an expert on this subject. Well with your permission let me to grab your RSS feed to keep up to date with forthcoming post.
Thanks a million and please carry on the enjoyable work.
bookmarked!!, I really like your web site!
Here is my web site … SIGHT CARE
Thanks for finally talking about > SMI diamond
grinding wheels < Liked it!
Hi there i am kavin, its my first time to commenting anyplace, when i read this paragraph i thought i could also
make comment due to this good article.
Have a look at my page :: LipoZem Official Website
Hi there! Someone in my Facebook group shared this website with us so
I came to give it a look. I’m definitely enjoying the information. I’m bookmarking and will be
tweeting this to my followers! Fantastic blog and amazing design.
My webpage :: lottery defeated software reviews
Normally I do not learn article on blogs, however I would like to say that this write-up very forced
me to take a look at and do so! Your writing style has been surprised me.
Thanks, quite great post.
my blog post: provadent real customer reviews
There is certainly a lot to find out about this issue.
I really like all of the points you have made.
My blog :: ozempic vs phenq
Thanks for sharing your info. I really appreciate your efforts and
I will be waiting for your further post thank you once
again.
Generally I do not learn article on blogs, however I would like to say that this
write-up very pressured me to check out and do so! Your writing taste has been amazed me.
Thank you, very nice article.
Feel free to visit my site – what is tonic greens
Wonderful web site. Plenty of helpful info here.
I’m sending it to some pals ans also sharing in delicious.
And certainly, thank you in your sweat!
Hey there just wanted to give you a quick heads up. The text
in your post seem to be running off the screen in Ie.
I’m not sure if this is a formatting issue
or something to do with browser compatibility but I figured I’d post to let you know.
The layout look great though! Hope you get the problem resolved soon. Thanks
Wow, marvelous weblog format! How long have you ever been blogging for?
you made running a blog look easy. The total glance of your website is magnificent, let
alone the content!
Hey very interesting blog!
I am really impressed with your writing skills as well as with the layout on your weblog.
Is this a paid theme or did you modify it yourself?
Either way keep up the nice quality writing, it’s
rare to see a nice blog like this one today.
Also visit my web site … tonic greens reviews reddit
It’s actually very complicated in this busy life to listen news on TV, so I simply use internet for that purpose, and get the
most recent news.
This is very interesting, You’re a very skilled blogger.
I’ve joined your feed and look forward to seeking more
of your wonderful post. Also, I have shared your web site
in my social networks!
Feel free to visit my web site: does pronerve 6 work
I have been exploring for a bit for any high quality articles or blog posts
on this kind of area . Exploring in Yahoo I at last stumbled upon this web site.
Studying this information So i am glad to convey that I’ve a very excellent uncanny feeling I found
out exactly what I needed. I such a lot for sure will make sure to don?t fail to remember this website and provides it a look regularly.
It’s truly very complex in this active life to listen news on TV, so I only use
web for that purpose, and get the hottest news.
Visit my webpage erec power
Magnificent beat ! I wish to apprentice while you amend your website, how could i subscribe for a blog web site?
The account aided me a acceptable deal. I had been a
little bit acquainted of this your broadcast provided bright
clear idea
When some one searches for his necessary thing, thus
he/she wishes to be available that in detail, so that thing is maintained over here.
Wonderful post however , I was wondering if you could write a litte more on this topic?
I’d be very grateful if you could elaborate a little bit further.
Kudos!
I seriously love your site.. Great colors & theme.
Did you create this amazing site yourself? Please reply back as I’m planning to create my very own site and would like to learn where
you got this from or just what the theme is named.
Many thanks!
Also visit my web page :: fitspresso.org
Good way of explaining, and good article to obtain facts concerning my presentation focus, which i am going to present in academy.
I know this website provides quality depending articles or reviews
and additional data, is there any other web page which offers such stuff
in quality?
Feel free to visit my web blog :: Mi Contai The Best Reviews
Wonderful post! We will be linking to this great article on our site.
Keep up the good writing.
I have read so many articles or reviews about the blogger lovers except this paragraph is really a fastidious article, keep it up.
What’s up it’s me, I am also visiting this web page on a regular basis, this web site is
really nice and the users are truly sharing good thoughts.
Feel free to visit my website the growth matrix gm
Great blog here! Also your web site loads up fast!
What host are you using? Can I get your affiliate link to your host?
I wish my site loaded up as fast as yours lol
I just like the valuable info you supply to your
articles. I’ll bookmark your weblog and take a look at once more right here regularly.
I’m somewhat certain I will learn many new stuff proper right here!
Best of luck for the following!
My homepage … lottery numbers
I always spent my half an hour to read this blog’s content
everyday along with a cup of coffee.
Feel free to surf to my website: lottery results
It’s an amazing article in support of all the internet viewers; they
will obtain advantage from it I am sure.
Stop by my homepage; reviews of the growth matrix
Everything is very open with a really clear explanation of the
issues. It was really informative. Your website is very helpful.
Many thanks for sharing!
Feel free to visit my web-site; alpha bites testosterone booster
I enjoy reading an article that can make men and women think.
Also, thanks for allowing me to comment!
Here is my site alpha bites legit
Saved as a favorite, I like your site!
Pretty nice post. I just stumbled upon your weblog and wished
to say that I’ve truly enjoyed browsing your blog posts.
In any case I will be subscribing to your rss feed and
I hope you write again soon!
Feel free to surf to my web-site :: fitspresso customer reviews reddit
great points altogether, you simply received a brand new reader.
What could you recommend in regards to your
publish that you made some days ago? Any positive?
Hey I know this is off topic but I was wondering if you
knew of any widgets I could add to my blog that automatically
tweet my newest twitter updates. I’ve been looking for a plug-in like this for
quite some time and was hoping maybe you would have some experience with something like this.
Please let me know if you run into anything. I truly enjoy
reading your blog and I look forward to your new updates.
WOW just what I was looking for. Came here by searching for skype网页版
I’m gone to inform my little brother, that he should also go to see
this webpage on regular basis to get updated from latest information.
An impressive share! I’ve just forwarded this onto a
friend who had been conducting a little research on this.
And he actually bought me breakfast because I discovered it for him…
lol. So let me reword this…. Thank YOU for the meal!!
But yeah, thanx for spending the time to discuss this issue
here on your web page.
I do believe all the concepts you’ve offered to your
post. They’re very convincing and will certainly work.
Still, the posts are too quick for novices. May you please lengthen them a little from next time?
Thank you for the post.
Thanks for the marvelous posting! I genuinely enjoyed reading it, you could be a great author.
I will be sure to bookmark your blog and may come back from now on. I want to
encourage you to definitely continue your great job, have a nice day!
Helpful information. Fortunate me I discovered your site unintentionally, and I’m stunned why this twist
of fate did not came about earlier! I bookmarked it.
It is the best time to make a few plans for the long run and it is time to
be happy. I’ve read this publish and if I may just I wish to recommend
you few interesting things or suggestions. Maybe you could write next articles relating to this article.
I wish to read more issues about it!
Here is my blog; rajapools
It’s difficult to find experienced people about this topic,
however, you sound like you know what you’re talking about!
Thanks
Hey very cool blog!! Guy .. Excellent .. Amazing ..
I’ll bookmark your website and take the feeds additionally?
I am glad to find a lot of useful information right here in the
post, we’d like work out more strategies in this regard, thanks for sharing.
. . . . .
I am really enjoying the theme/design of your site.
Do you ever run into any browser compatibility issues?
A number of my blog audience have complained about my website not working correctly in Explorer but looks
great in Chrome. Do you have any advice to help fix this issue?
Have a look at my site :: green bohemia
Its like you learn my thoughts! You appear to grasp a lot about this,
like you wrote the e book in it or something. I believe that you
can do with some percent to drive the message home a bit, but instead
of that, that is great blog. A fantastic read. I
will certainly be back.
my page – toto macau
Hi, this weekend is fastidious designed for me, because this moment i am reading this fantastic educational post here
at my home.
Excellent beat ! I would like to apprentice while you amend your website, how could i subscribe for a
blog web site? The account aided me a acceptable deal.
I had been tiny bit acquainted of this your broadcast
offered bright clear idea
Hi there, I log on to your blogs regularly. Your humoristic style is witty,
keep it up!
An impressive share! I have just forwarded this onto a friend who was conducting a little research on this.
And he in fact ordered me lunch because I discovered it for him…
lol. So allow me to reword this…. Thanks for the meal!!
But yeah, thanks for spending some time to talk about this subject here on your blog.
That is a really good tip especially to those new to the blogosphere. Simple but very accurate information… Many thanks for sharing this one. A must read post!
This excellent website certainly has all of the information I needed concerning this subject and didn’t know who to ask.
Hello there! This blog post couldn’t be written any better! Going through this article reminds me of my previous roommate! He constantly kept talking about this. I most certainly will forward this information to him. Pretty sure he will have a good read. I appreciate you for sharing!
always i used to read smaller articles or reviews that as well clear their
motive, and that is also happening with this paragraph which I am reading
here.
Check out my blog post: the growth matrix free videos
It’s not my first time to go to see this web site, i am browsing this web page
dailly and get good data from here every day.
Take a look at my web-site; the growth matrix penis enlargement
Hi there! This article could not be written any better! Looking through this post reminds me of my previous roommate! He always kept talking about this. I will forward this post to him. Fairly certain he’s going to have a good read. Thanks for sharing!
Greetings, I do believe your site could possibly be having browser compatibility problems. When I take a look at your blog in Safari, it looks fine however, when opening in IE, it’s got some overlapping issues. I simply wanted to provide you with a quick heads up! Apart from that, great blog.
Superb blog! Do you have any tips and hints for aspiring writers?
I’m planning to start my own website soon but I’m a little lost on everything.
Would you suggest starting with a free platform like WordPress or go for a paid
option? There are so many choices out there that I’m completely confused ..
Any tips? Thank you!
This is the right webpage for everyone who wishes to find out about this topic. You realize a whole lot its almost hard to argue with you (not that I actually will need to…HaHa). You certainly put a new spin on a topic that has been written about for years. Excellent stuff, just wonderful.
Pretty! This has been an extremely wonderful article. Many thanks for providing these details.
Thanks a bunch for sharing this with all people you actually recognize what you are talking approximately!
Bookmarked. Kindly additionally seek advice from my site =).
We may have a hyperlink exchange contract among us
Everything is very open with a precise explanation of the challenges. It was truly informative. Your site is very helpful. Many thanks for sharing.
Hiya! I know this is kinda off topic nevertheless I’d
figured I’d ask. Would you be interested in trading links or maybe guest authoring a blog article or vice-versa?
My site discusses a lot of the same subjects as yours and I believe we
could greatly benefit from each other. If you’re interested feel free
to send me an email. I look forward to hearing from you! Awesome blog by the way!
Hi, I do believe your website could be having browser compatibility problems. Whenever I take a look at your blog in Safari, it looks fine however, when opening in IE, it has some overlapping issues. I simply wanted to provide you with a quick heads up! Other than that, fantastic site!
We’re a gaggle of volunteers and opening a brand new scheme in our community.
Your web site offered us with helpful info to work on.
You’ve done a formidable task and our entire neighborhood
will be thankful to you.
Here is my webpage :: chessai.net
How many international locations in Europe have you ever visited?
Undeniably believe that which you stated. Your favorite reason appeared to be on the net the easiest thing to
keep in mind of. I say to you, I definitely get annoyed
even as other people think about issues that they plainly do not realize about.
You managed to hit the nail upon the highest and defined out
the entire thing without having side effect , folks can take a signal.
Will probably be back to get more. Thanks
Here is my page: trash chute hardware
I think the admin of this web page is truly working hard in favor of his site, as here every information is quality based stuff.
Feel free to surf to my blog post … wilkinson chute door
I blog frequently and I really appreciate your content. This article has truly peaked my interest. I am going to take a note of your site and keep checking for new details about once a week. I subscribed to your Feed too.
Thanks , I have just been looking for information approximately
this topic for ages and yours is the best I have found
out till now. But, what in regards to the bottom line?
Are you sure concerning the source?
Also visit my web blog :: trash chute latch
Hi, i believe that i saw you visited my blog thus i came to go back
the want?.I am attempting to in finding things to enhance my website!I suppose
its ok to use a few of your ideas!!
Shortly after in June 2018 Nashville was named the host of the 2019 NFL Draft.
Bezy, John V. (2003).
He was ultimately followed by Marka Ragnos, the last ruler of a interval identified because the Golden Age of the Sith.
If some one wishes expert view on the topic of blogging and site-building after that i advise him/her to visit this blog, Keep up the fastidious work.
Howdy would you mind stating which blog platform you’re working with?
I’m going to start my own blog in the near future but I’m having a hard time making a decision between BlogEngine/Wordpress/B2evolution and
Drupal. The reason I ask is because your layout seems different then most blogs and I’m looking for something
completely unique. P.S Sorry for being off-topic but I had to
ask!
Undeniably believe that which you stated. Your favorite reason appeared to
be on the net the easiest thing to remember of.
I say to you, I certainly get annoyed even as other folks think about worries that they just don’t
know about. You managed to hit the nail upon the top
and defined out the entire thing with no need side effect , folks can take a signal.
Will probably be back to get more. Thank you
I know this if off topic but I’m looking into starting my own blog
and was curious what all is needed to get set up?
I’m assuming having a blog like yours would cost a pretty
penny? I’m not very internet smart so I’m not 100% certain. Any tips or advice would be greatly appreciated.
Kudos
I always used to study article in news papers but now as I am a user of net thus from
now I am using net for articles, thanks to web.
Look into my website – Best Review Food Restaurant Cafe in Bali
It is not my first time to pay a visit this website, i
am visiting this web page dailly and get nice
data from here every day.
Look into my blog post; Pesantren modern Ummul Quro Al-Islami
I am actually thankful to the owner of this web page who has shared this
enormous article at here.
Here is my website: win90
You can certainly see your expertise within the
article you write. The world hopes for more passionate writers such as you who are not afraid to mention how they
believe. At all times go after your heart.
Pretty! This has been an incredibly wonderful post. Many thanks for providing this info.
I think everything published was actually very logical. But, think on this,
what if you were to write a killer post title?
I ain’t suggesting your information is not good, however suppose you
added a post title that makes people desire more?
I mean SMI diamond grinding wheels is kinda boring.
You ought to peek at Yahoo’s front page and note how they create news headlines
to get people to open the links. You might add a related video or a picture or two to grab people excited about what you’ve got
to say. Just my opinion, it would bring your posts a little livelier.
Sugar Defender Discovering Sugar Defender has been a game-changer for me, as I have actually constantly been vigilant about managing my blood glucose levels.
With this supplement, I feel empowered to take charge of my health,
and my newest clinical exams have actually shown a significant
turn-around. Having a reliable ally in my edge provides me with a sense of
security and peace of mind, and I’m deeply thankful for the profound distinction Sugar Defender has actually made in my health.
Useful info. Lucky me I discovered your site unintentionally, and I am shocked
why this coincidence didn’t took place in advance!
I bookmarked it.
I must thank you for the efforts you’ve put in penning this blog.
I’m hoping to check out the same high-grade content by you in the
future as well. In fact, your creative writing abilities has inspired
me to get my own blog now 😉
Heya i am for the first time here. I found this board and I
find It truly useful & it helped me out a
lot. I hope to give something back and help others like you aided me.
I’m amazed, I must say. Seldom do I come across a blog that’s equally educative and
interesting, and without a doubt, you’ve hit the nail on the head.
The problem is an issue that not enough people are speaking intelligently about.
I am very happy that I came across this during my search
for something regarding this.
Do you have a spam issue on this blog; I also am a blogger, and I was wondering
your situation; many of us have created some nice procedures and we are looking to trade techniques with others, why not shoot
me an email if interested.
Hello there, You have done a fantastic job. I will definitely digg
it and personally suggest to my friends. I
am sure they’ll be benefited from this web site.
Hi, I do think this is a great blog. I stumbledupon it 😉 I am going to come back
yet again since I bookmarked it. Money and freedom is the greatest way
to change, may you be rich and continue to help others.
Howdy! I could have sworn I’ve visited this website before but after going through a few of the posts I realized it’s new to me. Nonetheless, I’m certainly pleased I found it and I’ll be book-marking it and checking back frequently.
Very good information. Lucky me I ran across your website by chance (stumbleupon). I’ve bookmarked it for later.
It’s not my first time to pay a quick visit this web site,
i am browsing this website dailly and obtain good facts from
here every day.
Great post. I was checking continuously this blog and I’m impressed!
Very helpful information particularly the last part 🙂 I care for such info much.
I was seeking this particular information for a long time.
Thank you and best of luck.
Byrne takes the supplied queen, hoping to outplay his 13-12 months-outdated opponent within the ensuing complications, however Fischer gets far too much for it, leaving Byrne with a hopeless sport.
Way cool! Some extremely valid points! I
appreciate you penning this article and the rest of the site is also really good.
Hi there! This is my 1st comment here so I just
wanted to give a quick shout out and say I really enjoy reading through your
blog posts. Can you suggest any other blogs/websites/forums that cover the same topics?
Thanks for your time!
It’s difficult to find well-informed people on this subject, however, you sound like you know what you’re talking about! Thanks
Fantastic post however I was wondering if you could write a litte
more on this subject? I’d be very thankful if you could elaborate a little
bit further. Cheers!
I think this is among the most significant
information for me. And i’m glad reading your article. But wanna remark on some general things,
The site style is perfect, the articles is really
great : D. Good job, cheers
Have you ever considered about including a little bit more than just your articles?
I mean, what you say is valuable and everything. However think of if you added
some great visuals or videos to give your posts more, “pop”!
Your content is excellent but with images and videos, this blog could definitely be one of the very best in its field.
Great blog!
Very nice article, just what I needed.
I’m very pleased to uncover this page. I wanted to thank you for your time for this particularly wonderful read!! I definitely savored every part of it and I have you book marked to check out new information in your website.
White can attack on the kingside and check out to exploit the handed h-pawn, while Black destroys the centre.
Aw, this was a very nice post. Taking a few minutes and actual effort to create a superb article… but what can I say… I hesitate a lot and don’t manage to get anything done.
Hey there! I know this is kind of off topic but I was wondering which blog platform are
you using for this site? I’m getting tired of WordPress because I’ve had problems with hackers
and I’m looking at alternatives for another platform.
I would be awesome if you could point me in the direction of a good platform.
I am actually pleased to read this webpage posts which
carries plenty of helpful information, thanks for providing such data.
I do not know whether it’s just me or if perhaps everybody else experiencing
issues with your blog. It seems like some of the written text on your
posts are running off the screen. Can someone else please provide
feedback and let me know if this is happening to them too?
This may be a problem with my internet browser because I’ve had this happen before.
Cheers
Very good write-up. I certainly love this website.
Continue the good work!
The spacers are small enough that they are visible only at very close distances, usually as much as 1 m.
Sixty three Clerk’s workplace Montcalm County, Start, Loss of life, and Marriage data, Stanton, Michigan.
This is a topic that’s near to my heart… Best wishes! Exactly where can I find the contact details for questions?
He makes strong links between the Bosses and Boswells and suggests they arrived in Scotland from Normandy in the course of the thirteenth century.
I visited various websites but the audio quality for audio
songs existing at this site is actually marvelous.
This site really has all of the information I needed about this subject and didn’t know who to ask.
Burial shall be in the Bailey Cemetery with Callaway-Smith-Cobb Funeral Residence in charge of preparations.
I believe what you published was actually very reasonable.
But, think on this, what if you were to write a killer
headline? I am not suggesting your content isn’t solid.,
but what if you added a title that grabbed folk’s attention? I mean SMI diamond grinding wheels is kinda plain. You ought to look at Yahoo’s home page and see how they create news
titles to grab viewers to open the links. You might add a related
video or a related picture or two to grab people excited about what you’ve got to say.
In my opinion, it might make your posts a little bit more interesting.
Hello there, just became aware of your blog through Google, and found that it is
really informative. I’m gonna watch out for brussels.
I will appreciate if you continue this in future. Lots
of people will be benefited from your writing. Cheers!
Hello my friend! I want to say that this post is awesome, great written and include approximately all significant infos.
I would like to peer extra posts like this .
Quality articles or reviews is the important to attract the people to go to see the website, that’s what this website is providing.
hello there and thank you for your info – I’ve definitely picked up anything
new from right here. I did however expertise some technical points using this site, since I experienced to
reload the website lots of times previous to I could get it
to load properly. I had been wondering if your web
hosting is OK? Not that I am complaining, but slow loading instances
times will very frequently affect your placement
in google and can damage your high-quality score if advertising and marketing with Adwords.
Anyway I’m adding this RSS to my email and can look out for a lot more
of your respective intriguing content. Make sure
you update this again soon.
You have made some decent points there. I looked on the internet for additional information about the issue and found most individuals will go along with your views on this website.
Do you have a spam issue on this website; I also am a blogger,
and I was curious about your situation; many
of us have developed some nice practices and we are looking to swap strategies with other folks, be sure to shoot me an e-mail if interested.
I was suggested this website by my cousin. I’m not sure whether this post is
written by him as nobody else know such detailed about my problem.
You are wonderful! Thanks!
Very nice article. I absolutely appreciate this website.
Keep it up!
Link exchange is nothing else however it is just placing the
other person’s website link on your page at suitable place and other person will also do same for you.
Hi! I could have sworn I’ve visited this blog before but after looking at many of the articles I realized it’s new to me. Anyhow, I’m definitely happy I stumbled upon it and I’ll be book-marking it and checking back regularly.
The Povey Building is a contributing property to the Portland New Chinatown/Japantown Historic District.
Hi i am kavin, its my first occasion to commenting anyplace,
when i read this post i thought i could also create comment due to
this sensible paragraph.
Mrs. McNUTT died early Saturday in a Shawnee nursing home.
Aw, this was a very nice post. Taking the time and actual effort to create a very good article… but what can I say… I put things off a lot and never manage to get anything done.
Hey! This post could not be written any better! Reading through this post reminds me of my good old room
mate! He always kept talking about this. I will forward this post
to him. Pretty sure he will have a good read.
Thanks for sharing!
Thanks for sharing superb informations. Your web-site is so cool. I’m impressed by the details that you’ve on this website. It reveals how nicely you understand this subject. Bookmarked this web page, will come back for more articles. You, my friend, ROCK! I found just the information I already searched all over the place and just could not come across. What a perfect site.
Heya! I just wanted to ask if you ever have
any issues with hackers? My last blog (wordpress) was
hacked and I ended up losing many months of hard
work due to no data backup. Do you have any solutions to stop hackers?
Right here is the right website for anyone who would like to understand this topic. You know a whole lot its almost tough to argue with you (not that I personally will need to…HaHa). You definitely put a fresh spin on a topic which has been written about for many years. Wonderful stuff, just wonderful.
Oh my goodness! Incredible article dude! Thanks, However I am going through troubles with your RSS.
I don’t understand why I cannot subscribe to it. Is there anybody getting identical RSS issues?
Anyone who knows the answer will you kindly
respond? Thanks!!
Thanks for this tremendous post, I am glad I noticed this website on yahoo.
dance shoes that are shiny are the most cool stuff that you could possibly wear**
A motivating discussion is worth comment. I do believe that you ought to publish more on this topic, it may not be a taboo subject but generally people do not discuss these subjects. To the next! Kind regards!
Hi! I just wanted to ask if you ever have any problems with hackers?
My last blog (wordpress) was hacked and I ended
up losing many months of hard work due to no backup.
Do you have any solutions to prevent hackers?
It is appropriate time to make some plans for the future
and it’s time to be happy. I have read this put up and if I may just I wish to
suggest you some interesting issues or tips. Maybe you
can write subsequent articles referring to this article.
I want to read even more issues about it!
Spot on with this write-up, I honestly believe this amazing site needs a lot more attention. I’ll probably be back again to read more, thanks for the information!
Thank you for the good writeup. It in fact was a amusement account it.
Look advanced to more added agreeable from you!
However, how could we communicate?
I’ve been browsing online more than 2 hours today, yet I
never found any interesting article like yours.
It’s pretty worth enough for me. In my opinion, if all site owners and
bloggers made good content as you did, the internet will
be much more useful than ever before.
Someone necessarily assist to make critically articles I’d state. This is the first time I frequented your web page and thus far? I amazed with the analysis you made to make this actual submit incredible. Excellent activity!
Good site you have got here.. It’s difficult to find quality writing like yours nowadays. I truly appreciate individuals like you! Take care!!
It’s appropriate time to make a few plans for the longer
term and it is time to be happy. I have read this post and if I may
just I wish to recommend you few fascinating things or tips.
Perhaps you can write subsequent articles referring to this article.
I desire to learn even more issues about it!
Thanks a lot for sharing this with all people you actually understand what you are speaking approximately!
Bookmarked. Kindly also consult with my web site =).
We may have a hyperlink change arrangement between us
You’ve made some decent points there. I checked on the internet for more info about the issue and found most people will go along with your views on this site.
May I simply just say what a relief to find someone who truly understands what they are talking about over the internet. You actually know how to bring an issue to light and make it important. A lot more people have to read this and understand this side of your story. I was surprised you are not more popular because you surely possess the gift.
Spot lets start work on this write-up, I truly think this fabulous website needs a great deal more consideration. I’ll apt to be again to learn far more, appreciate your that info.
I’d have to talk to you here. Which is not some thing It’s my job to do! I love reading a post that should make people feel. Also, many thanks allowing me to comment!
Merci à vous pour ce game. Moi j’adore les jeux de pistolets, et vous?
Your blog is one of a kind, i love the way you organize the topics.:,”~
Thank you for another informative website. Where else could I get that type of information written in such an ideal way? I have a project that I’m just now working on, and I have been on the look out for such information.
Wow, amazing blog layout! How long have you been blogging for? you make blogging look easy
Hello there! This blog post couldn’t be written any better! Looking at this post reminds me of my previous roommate! He constantly kept talking about this. I’ll forward this article to him. Fairly certain he’ll have a great read. I appreciate you for sharing!
Find all that is about News with our valuble article.
When I initially left a comment I seem to have clicked on the -Notify me when new comments are added- checkbox and from now on each time a comment is added I recieve four emails with the exact same comment. There has to be a way you can remove me from that service? Thank you.
Great write-up, I am normal visitor of one’s blog, maintain up the nice operate, and It’s going to be a regular visitor for a long time.
so much wonderful info on here, : D.
I’m glad to become a visitor in this pure site, regards for this rare info!
An impressive share, I merely with all this onto a colleague who had been doing a little analysis during this. And he in fact bought me breakfast because I ran across it for him.. smile. So allow me to reword that: Thnx to the treat! But yeah Thnkx for spending enough time to go over this, I am strongly over it and adore reading much more about this topic. If you can, as you grow expertise, can you mind updating your blog to comprehend details? It is extremely helpful for me. Big thumb up for this short article!
Congratulations for posting such a useful blog. Your blog isn’t only informative but also extremely artistic too. There usually are extremely couple of
This design is steller! You obviously know how to keep a reader entertained.
Between your wit and your videos, I was almost moved to start my own blog (well, almost…HaHa!) Excellent job.
I really enjoyed what you had to say, and more than that, how you presented it.
Too cool!
Your style is so unique compared to other people I have read stuff from. Many thanks for posting when you have the opportunity, Guess I will just book mark this site.
I’m amazed, I have to admit. Rarely do I come across a blog that’s both equally educative and engaging, and let me tell you, you’ve hit the nail on the head. The issue is something which too few men and women are speaking intelligently about. I am very happy that I stumbled across this in my hunt for something concerning this.
I’ve been exploring for a little for any high quality articles or blog posts in this kind
of area . Exploring in Yahoo I ultimately stumbled upon this website.
Studying this information So i’m satisfied
to express that I have a very just right uncanny feeling I
found out exactly what I needed. I most certainly will make certain to don?t fail to remember this website
and give it a look on a relentless basis.
Rise Of The Lycans do have some great fighting scene between the werewolves and the vampires, it is a nice movie::
I’m amazed, I have to admit. Rarely do I come across a blog that’s both equally educative and amusing, and without a doubt, you’ve hit the nail on the head. The issue is something which not enough folks are speaking intelligently about. I am very happy I found this during my search for something concerning this.
Wow, this hit the nail right on the head. Great post buddy.. I can’t wait for your next article. Thanks for the great share pal. Cheers
Sweet internet site , super pattern , really clean and apply pleasant.
Absolutely composed written content , thanks for information .
When I originally commented I clicked the -Notify me when new comments are added- checkbox now whenever a comment is added I recieve four emails with similar comment. Could there be however you can eliminate me from that service? Thanks!
in my opinion, Grand Theft Auto is super addictive based from my experience.
The the very next time I just read a weblog, Lets hope it doesnt disappoint me about this. Get real, Yes, it was my choice to read, but I really thought youd have some thing interesting to say. All I hear is a few whining about something you could fix if you ever werent too busy in search of attention.
Do you have any video of that? I’d love to find out some additional information.
I have not checked in here for some time since I thought it was getting boring, but the last few posts are great quality so I guess I¡¦ll add you back to my everyday bloglist. You deserve it my friend pristina travel
You ought to actually take into consideration engaged on developing this blog into a serious authority on this market. You evidently have a grasp deal with of the subjects everyone seems to be searching for on this website in any case and you may certainly even earn a buck or two off of some advertisements. I’d discover following recent matters and raising the amount of write ups you place up and I assure you’d start seeing some wonderful targeted site visitors within the close to future. Just a thought, good luck in no matter you do!
This is the correct blog for anybody who would like to learn about this topic. You are aware of a lot its virtually challenging to argue on hand (not that I actually would want…HaHa). You actually put the latest spin over a topic thats been revealed for many years. Fantastic stuff, just fantastic!
I just couldn’t go away your website prior to suggesting that
I actually loved the standard information a person supply for your guests?
Is gonna be again ceaselessly in order to check out new posts
Unlike regular bugs, regressions are significantly nasty, since they had been purported to have been fixed already.
Aldershot City boss Barry Smith informed BBC Surrey, ‘We confirmed confirmed the house followers what they’re able to with a hard-working and good efficiency which was combined with some quality.
You are so awesome! I don’t suppose I’ve truly read through something like that before. So nice to find somebody with original thoughts on this subject matter. Seriously.. thanks for starting this up. This site is one thing that is needed on the internet, someone with a bit of originality.
I visited a lot of website but I conceive this one has something special in it.
Or perhaps considered adding more videos towards your blog posts to maintain readers more entertained? I mean Someone said all over the country actual yours but it was quite good but as I’m greater numbers of a visual learner,I found that to become more helpful well make me aware the way it seems.
Nice post. I learn one thing tougher on different blogs everyday. It should at all times be stimulating to learn content from different writers and observe slightly something from their store. I’d desire to use some with the content on my weblog whether you don’t mind. Natually I’ll give you a link in your web blog. Thanks for sharing.
This is a topic that is near to my heart… Thank you! Exactly where can I find the contact details for questions?
What’s up to all, how is everything, I think every one is getting more from this site, and your views are pleasant in favor
of new users.
Attractive section of content. I just stumbled upon your weblog and in accession capital to assert that I get in fact enjoyed account your blog posts. Anyway I’ll be subscribing to your augment and even I achievement you access consistently fast.
This is a very informative article. It really sparked my interest on several points. I agree with most of the points and am currently pondering the rest. Thank you for keeping your information so engaging.
I just added this web site to my google reader, great stuff. Cannot get enough!
Everything is very open with a really clear clarification of the issues. It was really informative. Your website is useful. Thank you for sharing!
That is some inspirational stuff. Never knew that opinions could be this varied. Do you still feel this way?
Useful information. Fortunate me I discovered your web site by chance, and I’m surprised why this twist of fate didn’t happened earlier! I bookmarked it.
Marroni, Steve (July 26, 2020).
My brother suggested I might like this website. He was entirely right. This post actually made my day. You can not imagine just how much time I had spent for this information! Thanks!
bookmarked!!, I really like your web site!
I think you have a great page here… today was my first time coming here.. I just happened to find it doing a google search. anyway, good post.. I’ll be bookmarking this page for sure.
Saved as a favorite, I love your web site.
You will discover bloggers in your industry who aren’t direct opponents that’ll publish your visitor articles.
Thank you for the good writeup. It in fact was a amusement account it.
Look advanced to far added agreeable from you!
By the way, how could we communicate?
Good article! We will be linking to this great article on our site. Keep up the good writing.
During their adventures, the threesome tangle with the Faction Paradox, a renegade voodoo cult of time travellers who believed in creating time paradoxes and altering historical past.
I really love your blog.. Very nice colors & theme.
Did you develop this amazing site yourself? Please reply
back as I’m looking to create my own blog and would love to know where you got this from or what the theme is named.
Many thanks!
Remarkable! Its really awesome piece of writing, I have got much clear idea regarding from this post.
When I initially left a comment I seem to have clicked the -Notify me when new comments are added- checkbox and now each time a comment is added I get 4 emails with the exact same comment. Perhaps there is a means you are able to remove me from that service? Thanks a lot.
Overall, politicians are split on the issue of whether Twitter is more for business or personal use. The first thing is the fact that you can build up quite a large following of people.
oui et pas vraiment. Affirmatif car il se peut qu’on détermine de nouvelles sources qui certainement se référent les memes significations. Non en effet il ne suffit pas d’imiter ce que tout le monde être autorisé à trouver avec certains site web tiers puis le transcrire tant simplement…
It was a excitement getting to your site a short while ago. I came here today hoping to get interesting things. And I was not let down. Your ideas on new tactics on this subject material were helpful and an excellent help to my family. Thank you for creating time to write out these things as well as for sharing your thinking.
Rattling nice layout and excellent subject material, very little else we require .
Certainly I like your website, however you need to check the spelling on quite a few of your posts. A number of them are rife with spelling issues and I find it very silly to inform you. On the other hand I’ll definitely come again again!
Youre so cool! I dont suppose Ive read anything in this way prior to. So nice to get somebody with original thoughts on this subject. realy we appreciate you beginning this up. this web site is something that is required on the web, a person after some originality. valuable work for bringing new stuff on the web!
Just desire to say your article is as amazing. The clearness in your post is just nice and i could assume you’re an expert on this subject.
Fine with your permission allow me to grab your feed to keep up to date with forthcoming
post. Thanks a million and please continue the gratifying work.
You are so awesome! I don’t believe I have read through something like this before. So wonderful to discover someone with a few original thoughts on this issue. Seriously.. thank you for starting this up. This website is something that is required on the web, someone with a little originality.
Thanks for ones marvelous posting! I actually enjoyed reading it, you are a
great author.I will be sure to bookmark your blog and definitely will come back
down the road. I want to encourage you continue your great job, have a nice
morning!
Way cool! Some very valid points! I appreciate you writing this write-up and the rest of the site is really good.
Tremendous things here. I’m very satisfied to
peer your article. Thank you so much and I am
taking a look ahead to touch you. Will you please drop me a e-mail?
Hi, I do believe this is a great site. I stumbledupon it 😉 I may return once again since i have bookmarked it. Money and freedom is the greatest way to change, may you be rich and continue to help other people.
My family every time say that I am killing my time here at net, however I know I am getting knowledge
daily by reading such good posts.
First off I want to say great blog! I had a quick question that I’d like
to ask if you do not mind. I was curious to find out how you center yourself and
clear your thoughts before writing. I’ve had a hard time clearing my mind in getting
my thoughts out there. I truly do take pleasure in writing
however it just seems like the first 10 to 15 minutes tend to be
lost simply just trying to figure out how to begin. Any suggestions or hints?
Thank you!
Nice post. I learn something totally new and challenging on websites I stumbleupon on a daily basis. It will always be helpful to read content from other writers and use something from their websites.
I don’t even know how I ended up here, but I thought this post was good.
I do not know who you are but certainly you’re going to a famous blogger if you aren’t already
😉 Cheers!
Thankfulness to my father who shared with me on the
topic of this web site, this web site is genuinely remarkable.
Hey there, I think your website might be having browser compatibility issues.
When I look at your website in Firefox, it looks fine but when opening in Internet Explorer, it has
some overlapping. I just wanted to give you a quick heads up!
Other then that, superb blog!
skin care is easy, all you have to do is eat nutritious foods and do some daily cleaning routine of your skin’
I have been exploring for a little for any high quality articles or blog posts on this kind of area . Exploring in Yahoo I at last stumbled upon this web site. Reading this info So i’m happy to convey that I have an incredibly good uncanny feeling I discovered exactly what I needed. I most certainly will make certain to do not forget this site and give it a glance on a constant basis.
Great blog you have got here.. It’s difficult to find high-quality writing like yours nowadays. I truly appreciate people like you! Take care!!
On June 26, 12 more counties entered the green part: Berks, Bucks, Chester, Delaware, Erie, Lackawanna, Lancaster, Lehigh, Montgomery, Northampton, Philadelphia and Susquehanna.
Considerably, the article is really the freshest on that notable topic. I concur with your conclusions and also can thirstily look forward to your forthcoming updates. Saying thanks will not simply just be enough, for the exceptional lucidity in your writing. I will certainly immediately grab your rss feed to stay abreast of any kind of updates. Authentic work and much success in your business dealings!
Nice weblog here! Additionally your web site a lot up very fast!
What web host are you the usage of? Can I am getting your affiliate link for your host?
I wish my website loaded up as quickly as yours
lol
Thanks for sharing your thoughts. I truly appreciate
your efforts and I am waiting for your further post thank you once again.
Fantastic website. Lots of helpful info here.
I am sending it to several pals ans additionally sharing in delicious.
And certainly, thank you to your effort!
Appreciating the dedication you put into your blog and detailed information you present.
It’s good to come across a blog every once in a while that isn’t the same out of date rehashed
information. Wonderful read! I’ve saved your
site and I’m adding your RSS feeds to my Google account.
Everything you need to know about News in a great way.
Excellent article. I will be facing some of these issues as well..
This difficult tramping trip travels up the Edwards River, crosses two alpine Passes after which travels down the Hawdon River.
Hi there to every , because I am truly eager of reading this blog’s post to
be updated on a regular basis. It carries fastidious
information.
Oh my goodness! Incredible article dude! Thanks, However I am encountering problems with your RSS. I don’t understand the reason why I cannot join it. Is there anybody else having the same RSS issues? Anybody who knows the answer will you kindly respond? Thanx!
What’s up everyone, it’s my first pay a quick visit at this site,
and piece of writing is really fruitful for me,
keep up posting such articles.
Having read this I believed it was really informative. I appreciate you spending some time and energy to put this short article together. I once again find myself spending a lot of time both reading and leaving comments. But so what, it was still worthwhile.
What’s up, I want to subscribe for this website to take most up-to-date
updates, so where can i do it please help out.
I’m not that much of a online reader to be honest but your sites really
nice, keep it up! I’ll go ahead and bookmark your site to come back in the future.
Cheers
This is a topic that is close to my heart… Best wishes!
Where are your contact details though?
Greetings from California! I’m bored to death at work so I decided to check
out your site on my iphone during lunch break. I love the knowledge you provide
here and can’t wait to take a look when I get home. I’m
amazed at how quick your blog loaded on my mobile ..
I’m not even using WIFI, just 3G .. Anyhow, superb blog!
Rajasthani weddings are a celebration of colours and sparkles, filled with power and tradition.
I have to thank you for the efforts you’ve put in penning this site.
I’m hoping to view the same high-grade content
by you later on as well. In fact, your creative writing abilities has motivated me to get my very own website now 😉
Hi, I do think your web site might be having web browser compatibility problems. Whenever I look at your blog in Safari, it looks fine however, when opening in IE, it has some overlapping issues. I simply wanted to provide you with a quick heads up! Apart from that, wonderful site.
Hello to every body, it’s my first go to see of
this web site; this website consists of amazing and truly good stuff designed for visitors.
I love what you guys are up too. This type of clever work and coverage!
Keep up the great works guys I’ve you guys to our blogroll.
Hi! Someone in my Facebook group shared this site with us so I came to give it a look.
I’m definitely loving the information. I’m bookmarking and
will be tweeting this to my followers! Excellent blog and outstanding style and design.
Hi! I could have sworn I’ve been to this blog before but after looking at
a few of the articles I realized it’s new to me.
Anyways, I’m certainly happy I found it and
I’ll be book-marking it and checking back regularly!
It’s hard to find educated people for this subject, however, you sound like you know what you’re talking about! Thanks
I’m not sure exactly why but this website is loading incredibly slow for
me. Is anyone else having this issue or is it a issue on my end?
I’ll check back later on and see if the problem still
exists.
Please let me know if you’re looking for a writer for your
site. You have some really good articles and I believe
I would be a good asset. If you ever want to take some of the load
off, I’d really like to write some content for your blog in exchange for a link back to
mine. Please send me an email if interested. Thank you!
Pretty! This has been a really wonderful post. Thank you for providing these details.
WOW just what I was looking for. Came here by searching for incarcerationnationsnetwork.com
Hmm it looks like your site ate my first comment (it was super long)
so I guess I’ll just sum it up what I submitted and say,
I’m thoroughly enjoying your blog. I too am an aspiring blog writer but I’m still new
to everything. Do you have any points for newbie blog writers?
I’d really appreciate it.
After looking at a number of the blog articles on your website, I seriously appreciate your technique of writing a blog. I saved it to my bookmark website list and will be checking back soon. Please check out my website as well and let me know what you think.
Excellent goods from you, man. I have have in mind your stuff previous to and you are just too magnificent.
I really like what you have acquired here, certainly like what you are stating and the way in which through
which you assert it. You’re making it enjoyable and you continue to care for to keep it smart.
I cant wait to read much more from you. That is really a great web site.
In addition, all non-Christian characters are unplayable without the purchase of the DLC that unlocks them, including Muslims, Jews, Hindus, Buddhists, Taoists, Zoroastrians, Jains, Zunists and varied pagans.
I have read so many posts about the blogger lovers except this post is genuinely a
good article, keep it up.
Link exchange is nothing else however it is
just placing the other person’s blog link on your page at suitable place and other person will also do similar in support of you.
Can I simply say what a relief to discover a person that actually knows what they’re discussing on the web. You actually realize how to bring an issue to light and make it important. More and more people ought to check this out and understand this side of the story. It’s surprising you aren’t more popular because you definitely have the gift.
I think everything composed made a bunch of sense.
However, think about this, suppose you wrote a catchier title?
I mean, I don’t want to tell you how to run your website, but what if you added a title that makes
people want more? I mean SMI diamond grinding wheels is kinda boring.
You should glance at Yahoo’s home page and note how they write news headlines to get people interested.
You might add a related video or a related picture or two
to grab readers interested about everything’ve got to say. Just my opinion, it could make your posts a
little livelier.
Holt was also a retired Crimson River Army Depot employee.
Superb, what a weblog it is! This webpage presents valuable data to us,
keep it up.
Wonderful, what a web site it is! This website provides helpful facts to us, keep it up.
Way cool! Some very valid points! I appreciate you penning this post and also the rest of the website is really good.
Now, you do not simply memorize the “regular” line at this point.
The Qualified Home Vitality Auditor have to be certified by a professional Certification Program at the time of the home power audit.
Its not my first time to pay a visit this website, i am
browsing this website dailly and take fastidious facts from here daily.
Hi there! This article couldn’t be written any better! Going through this article reminds me of my previous roommate! He always kept preaching about this. I most certainly will send this article to him. Fairly certain he will have a great read. Thank you for sharing!
It’s nearly impossible to find well-informed people in this particular topic, but you sound like you know what you’re talking about! Thanks
There’s certainly a great deal to know about this subject. I really like all of the points you have made.
I for all time emailed this web site post page to all my
associates, as if like to read it then my friends
will too.
Hi, I do believe this is a great blog. I stumbledupon it 😉 I will
return yet again since i have bookmarked it. Money and freedom is the
best way to change, may you be rich and continue to guide
other people.
Also visit my web-site – 비아그라구매@
Heya i am for the first time here. I found this board and I find It really useful & it helped me out much.
I hope to give something back and aid others like you aided
me.
Oh my goodness! Incredible article dude! Thank you so much, However I am having problems with your RSS. I don’t know why I can’t join it. Is there anybody having the same RSS problems? Anyone who knows the solution will you kindly respond? Thanx.
I enjoy reading a post that can make people think. Also, thanks for permitting me to comment.
Nice post. I learn something totally new and challenging on websites I stumbleupon everyday. It will always be useful to read articles from other authors and use something from other web sites.
Very good information. Lucky me I discovered your site by chance (stumbleupon). I’ve book marked it for later.
Oh my goodness! Impressive article dude! Thanks, However I am experiencing difficulties with your RSS. I don’t understand why I cannot join it. Is there anybody having the same RSS problems? Anyone who knows the answer will you kindly respond? Thanks!
It’s difficult to find experienced people on this subject, however, you seem like you know what you’re talking about! Thanks
I every time used to read article in news papers but now as I am a user of web thus from
now I am using net for articles or reviews, thanks to web.
I’m impressed, I have to admit. Seldom do I encounter a blog that’s equally educative and interesting, and let me tell you, you’ve hit the nail on the head. The issue is something that too few folks are speaking intelligently about. Now i’m very happy I found this in my hunt for something regarding this.
It is not my first time to go to see this web page, i am
browsing this web site dailly and get pleasant facts from here all the time.
What you posted made a bunch of sense. But, think on this, what
if you added a little information? I ain’t saying your information isn’t good.,
however suppose you added something that makes people desire more?
I mean SMI diamond grinding wheels is a little vanilla.
You could peek at Yahoo’s front page and watch how they write news titles
to get people to click. You might try adding a video or a related picture
or two to get people interested about what you’ve got to say.
Just my opinion, it might bring your posts a little bit more interesting.
I constantly spent my half an hour to read this weblog’s articles every day along with a mug of coffee.
Spot on with this write-up, I seriously believe that this web site needs much more attention. I’ll probably be back again to read more, thanks for the information!
May I simply say what a relief to discover an individual who genuinely knows what they’re
talking about on the net. You actually realize how to bring an issue to light and make it important.
A lot more people ought to read this and understand this side of the story.
I was surprised you’re not more popular since you surely possess the
gift.
Hey! This is my 1st comment here so I just wanted to give a quick shout
out and tell you I really enjoy reading your blog posts.
Can you recommend any other blogs/websites/forums that go over
the same subjects? Thank you!
It’s hard to find well-informed people about this subject, however, you seem like you know what you’re talking about! Thanks
Greetings! Very helpful advice in this particular post!
It is the little changes that make the most important changes.
Many thanks for sharing!
Excellent blog you’ve got here.. It’s difficult to find
high quality writing like yours nowadays. I honestly appreciate people like you!
Take care!!
There’s certainly a great deal to learn about this issue. I love all the points you’ve made.
Having read this I thought it was very informative. I appreciate you finding the time and energy to put this information together. I once again find myself personally spending a significant amount of time both reading and posting comments. But so what, it was still worth it!
It’s going to be finish of mine day, but before end I am reading this
wonderful post to increase my knowledge.
This site was… how do I say it? Relevant!! Finally I have found something that helped me. Thanks a lot!
Watch our exclusive Neerfit sexy bf video on neerfit.co.in.
It is appropriate time to make a few plans
for the longer term and it is time to be happy.
I’ve read this put up and if I may I want to counsel you few attention-grabbing issues or suggestions.
Perhaps you could write subsequent articles regarding
this article. I want to read more issues about it!
Fantastic website you have here but I was curious about if you knew of any message boards that cover the same topics talked about here?
I’d really like to be a part of group where I can get comments from other experienced individuals
that share the same interest. If you have any suggestions, please let me know.
Kudos!
Undeniably consider that which you stated. Your favourite justification seemed to be on the web
the easiest thing to keep in mind of. I say to you, I certainly get
irked while other folks think about worries
that they plainly do not realize about. You controlled to hit the nail upon the highest as
smartly as outlined out the entire thing without having side effect , people can take a signal.
Will likely be back to get more. Thanks
I’m not sure where you’re getting your information, however good
topic. I needs to spend some time studying more or understanding more.
Thanks for magnificent information I was searching for
this information for my mission.
This is a topic which is close to my heart… Cheers!
Where are your contact details though?
With havin so much content and articles do you ever run into
any problems of plagorism or copyright infringement? My blog has a
lot of unique content I’ve either written myself or outsourced but it looks like a lot of it is popping it up all over the internet without my permission. Do
you know any solutions to help reduce content from
being ripped off? I’d genuinely appreciate it.
I like it when people get together and share views. Great blog, continue the good work!
He took motion by forming the President’s Council on Youth Health in 1956 to seek out methods for bettering American youngsters’ fitness scores.
Hi, this weekend is good in favor of me, because this time
i am reading this wonderful informative piece of writing
here at my home.
If you desire to take much from this paragraph then you have
to apply these methods to your won website.
Thanks for your marvelous posting! I seriously enjoyed reading it, you might be a
great author.I will be sure to bookmark your blog and definitely will come back down the road.
I want to encourage that you continue your great posts, have a nice evening!
A wireless community is comprised of a broadband internet connection from a DSL, cable or satellite modem.
This text is priceless. When can I find out more?
Hi, I think your site might be having browser compatibility issues.
When I look at your blog site in Safari, it looks fine but when opening in Internet Explorer, it has some overlapping.
I just wanted to give you a quick heads up! Other then that, superb blog!
You actually make it appear really easy together with your presentation but I
find this topic to be really one thing which I feel I would never understand.
It sort of feels too complicated and extremely huge for me.
I’m looking forward in your next publish, I will attempt to get
the dangle of it!
Excellent goods from you, man. I have understand your stuff previous to and you are just extremely fantastic.
I actually like what you’ve acquired here, really like what you’re saying and
the way in which you say it. You make it entertaining and you still take care of to keep it smart.
I can not wait to read much more from you. This is really a terrific website.
There is certainly a great deal to learn about this topic. I really like all of the points you have made.
Hello just wanted to give you a quick heads up.
The words in your post seem to be running off the screen in Firefox.
I’m not sure if this is a formatting issue or something to do with internet browser compatibility but
I thought I’d post to let you know. The design look great though!
Hope you get the issue resolved soon. Thanks
This site was… how do I say it? Relevant!! Finally
I have found something that helped me. Cheers!
What’s up to all, how is the whole thing, I think every one is
getting more from this site, and your views are fastidious designed for new visitors.
This page truly has all of the information and facts I
needed concerning this subject and didn’t know who to ask.
You made some decent points there. I looked on the web for additional information about the issue and found most people will go along with your views on this web site.
I’d like to thank you for the efforts you’ve put in writing this site. I’m hoping to view the same high-grade blog posts by you in the future as well. In truth, your creative writing abilities has motivated me to get my own site now 😉
Does your blog have a contact page? I’m having a tough time
locating it but, I’d like to send you an e-mail. I’ve
got some creative ideas for your blog you might be interested in hearing.
Either way, great website and I look forward to seeing it improve over time.
I’m more than happy to uncover this site. I need to to thank you for your time due to this fantastic read!! I definitely liked every little bit of it and I have you bookmarked to see new information in your website.
Hi! I simply wish to give you a big thumbs up for the great information you have right here on this post. I am coming back to your blog for more soon.
Greate post. Keep writing such kind of information on your
blog. Im really impressed by it.
Hello there, You have performed an excellent job.
I’ll certainly digg it and in my opinion suggest to my friends.
I am confident they’ll be benefited from this web site.
Oh my goodness! Amazing article dude! Many thanks, However I am encountering troubles with your RSS. I don’t understand why I cannot subscribe to it. Is there anybody getting identical RSS issues? Anyone who knows the solution can you kindly respond? Thanks!
What’s Taking place i’m new to this, I stumbled upon this
I have found It positively helpful and it has helped me out loads.
I’m hoping to give a contribution & help different customers like
its helped me. Good job.
Good article! We will be linking to this particularly great
article on our website. Keep up the great writing.
When I initially commented I clicked the “Notify me when new comments are added” checkbox and
now each time a comment is added I get several e-mails with
the same comment. Is there any way you can remove people from
that service? Thanks a lot!
Thanks for sharing such a good idea, article is good, thats why i have read it completely
Very quickly this web page will be famous among all blog
users, due to it’s fastidious content
I know this website presents quality based articles and other material, is there any other web site which
provides these things in quality?
Hello, i believe that i noticed you visited my site thus i got here to go back the desire?.I am
trying to find things to improve my web site!I guess its ok to use some of your ideas!!
It’s remarkable to pay a visit this site and reading the views of all mates on the topic
of this piece of writing, while I am also zealous of getting knowledge.
Hi there to all, how is everything, I think every one is getting more from this web page, and
your views are pleasant designed for new visitors.
Heya i am for the first time here. I found this board and I find It really useful & it helped me out
much. I hope to give something back and help others like you aided me.
In case you are in a committed relationship, encountering angel quantity 333 is usually a gentle reminder of the significance of open and honest communication.
This paragraph gives clear idea designed for the new
people of blogging, that in fact how to do blogging.
Having read this I believed it was rather enlightening. I appreciate you spending some time and energy to put this content together. I once again find myself spending a lot of time both reading and leaving comments. But so what, it was still worth it.
It’s amazing in favor of me to have a web site, which is useful in favor of my knowledge.
thanks admin
Greetings from Los angeles! I’m bored to tears at work so I decided to check
out your site on my iphone during lunch break. I enjoy the
knowledge you present here and can’t wait to take a look when I
get home. I’m amazed at how quick your blog loaded on my cell phone ..
I’m not even using WIFI, just 3G .. Anyways, excellent site!
Can I simply just say what a relief to uncover someone who genuinely understands what they are talking about over the internet. You actually know how to bring a problem to light and make it important. More people need to read this and understand this side of your story. I can’t believe you are not more popular because you certainly possess the gift.
Wow, this piece of writing is nice, my younger sister is analyzing such things, so I am going to inform her.
Having read this I thought it was really enlightening. I appreciate you taking the time and energy to put this article together. I once again find myself personally spending way too much time both reading and commenting. But so what, it was still worth it!
I’m not sure exactly why but this weblog is loading very
slow for me. Is anyone else having this problem or
is it a problem on my end? I’ll check back later on and see if the problem still exists.
Greetings! Very helpful advice in this particular article!
It is the little changes that make the most significant
changes. Many thanks for sharing!
I enjoy what you guys are up too. Such clever work and reporting!
Keep up the very good works guys I’ve included you guys to
my own blogroll.
This article provides clear idea for the new people of blogging, that really how to do blogging and site-building.
I love reading an article that will make people
think. Also, thanks for allowing me to comment!
This is the right site for anybody who wishes to understand this topic. You know so much its almost hard to argue with you (not that I really will need to…HaHa). You definitely put a new spin on a topic that’s been written about for many years. Great stuff, just great.
Great info. Lucky me I recently found your blog
by accident (stumbleupon). I have saved as a favorite for later!
Next time I read a blog, I hope that it doesn’t disappoint me just as much as this particular one. I mean, Yes, it was my choice to read, nonetheless I really believed you would probably have something interesting to say. All I hear is a bunch of whining about something you can fix if you were not too busy searching for attention.
Hi my family member! I wish to say that this article is awesome, great written and come with approximately all vital infos.
I would like to see extra posts like this .
It’s going to be ending of mine day, but before finish I am
reading this impressive article to improve my know-how.
I do not even know how I ended up here, but I thought this post was good.
I don’t know who you are but certainly you’re going to a famous blogger if you aren’t already 😉 Cheers!
It is appropriate time to make some plans for the future and it is time to be happy.
I have learn this put up and if I may I want to suggest you some fascinating things or tips.
Maybe you can write subsequent articles relating to this article.
I wish to read more issues approximately it!
Do you mind if I quote a couple of your posts as long as I provide
credit and sources back to your weblog? My blog is in the
exact same area of interest as yours and my users would really benefit from a lot of the information you present here.
Please let me know if this alright with you. Regards!
You are so interesting! I don’t suppose I’ve truly read something like this before. So good to find someone with a few unique thoughts on this subject. Really.. thank you for starting this up. This site is something that is required on the internet, someone with some originality.
Unquestionably believe that which you stated.
Your favorite justification appeared to be on the internet the simplest thing to be aware of.
I say to you, I definitely get annoyed while people consider worries that they just do not know about.
You managed to hit the nail upon the top as well as defined out the whole thing without
having side-effects , people can take a signal. Will likely be back to get more.
Thanks
First off I would like to say great blog! I had a quick question that I’d
like to ask if you do not mind. I was interested to find
out how you center yourself and clear your thoughts prior to writing.
I’ve had trouble clearing my mind in getting my ideas out there.
I truly do enjoy writing however it just seems like the first 10 to 15 minutes are generally wasted simply just trying to figure out
how to begin. Any recommendations or tips? Thank you!
Hello there! This article could not be written any better! Looking at this article reminds me of my previous roommate! He constantly kept preaching about this. I most certainly will send this article to him. Pretty sure he’ll have a good read. Thanks for sharing!
What’s up colleagues, its fantastic post regarding teachingand
completely defined, keep it up all the time.
I’ve read several excellent stuff here. Definitely worth bookmarking for revisiting.
I wonder how much effort you set to create
the sort of great informative site.
I was excited to uncover this great site. I wanted to thank you for ones
time for this wonderful read!! I definitely loved every bit of it
and I have you book-marked to look at new information in your website.
You made some good points there. I looked on the web for more info about the issue and found most people will go along with your views on this site.
Having read this I believed it was very enlightening.
I appreciate you finding the time and energy to put this
content together. I once again find myself spending a lot
of time both reading and posting comments. But so what, it was still worthwhile!
Excellent post. Keep posting such kind of info on your page.
Im really impressed by it.
Hi there, You have done a great job. I will definitely
digg it and individually recommend to my friends.
I am sure they will be benefited from this website.
Ahaa, its fastidious discussion on the topic of this piece of writing here at this
web site, I have read all that, so now me also commenting here.
Hello would you mind sharing which blog platform you’re working with?
I’m going to start my own blog in the near future but I’m having a hard
time making a decision between BlogEngine/Wordpress/B2evolution and Drupal.
The reason I ask is because your design seems different then most blogs and I’m looking for something unique.
P.S My apologies for getting off-topic but I had to ask!
Hello all, here every one is sharing these kinds of knowledge, therefore
it’s fastidious to read this website, and I used
to pay a visit this weblog every day.
Yes! Finally something about Trafficked by my family.
You’re so cool! I don’t think I have read through something like that before. So great to discover another person with some original thoughts on this subject. Really.. thanks for starting this up. This site is something that’s needed on the web, someone with a bit of originality.
Having read this I thought it was really enlightening. I appreciate you taking the time and energy to put this informative article together. I once again find myself personally spending a significant amount of time both reading and commenting. But so what, it was still worth it!
I blog quite often and I genuinely thank you for your information. Your article has really peaked my interest. I will bookmark your website and keep checking for new details about once per week. I subscribed to your Feed too.
Family and friends aren’t going to judge your rooms in technical terms anyway.
For latest news you have to go to see world wide web and on internet I found this web site as a finest site for
hottest updates.
Hello there! I simply wish to offer you a huge thumbs up for your excellent information you’ve got right here on this post. I am returning to your web site for more soon.
You may tweak the info to seek out out what you’ll want to vary with a purpose to get the place you want to be, and skim tips about how to accomplish that effort.
Great delivery. Sound arguments. Keep up the great spirit.
Good day! I simply wish to offer you a huge thumbs up for your great information you’ve got
here on this post. I will be coming back to your web site for more soon.
Hi there, I found your web site via Google whilst looking for a related subject, your website came up, it appears to be like
great. I have bookmarked it in my google bookmarks.
Hello there, just turned into aware of your blog thru Google, and located that it is truly informative.
I am going to watch out for brussels. I will appreciate in the event
you continue this in future. Numerous people might be benefited
out of your writing. Cheers!
Great information. Lucky me I ran across your site by chance (stumbleupon). I have book marked it for later.
In its SEC filing, the company gave a range of $24-$28 per share with an initial $1.27 billion market cap.
It’s actually very complex in this full of activity life to listen news on TV, thus I
only use web for that purpose, and get the most
up-to-date news.
Can I simply just say what a comfort to discover an individual who really knows what they are talking about on the net. You definitely know how to bring a problem to light and make it important. More and more people should read this and understand this side of the story. I was surprised that you aren’t more popular because you surely have the gift.
Thursday, July 1, 2004 – 10:30 A.M.
In actual this is not ample to determine the disaster, the true strategy is to determine the risks (disaster) in correct time, in order that proper spryness ought to be started and eradicated the basis-trigger that causes this whole crisis earlier than it occurs.
It’s going to be ending of mine day, but before end I am
reading this impressive article to improve my knowledge.
If you wish for to take much from this piece of writing then you have to apply such strategies to your won website.
Good write-up. I definitely love this website. Continue the good work!
Have you ever thought about creating an e-book or guest authoring on other websites?
I have a blog based upon on the same subjects you discuss and
would love to have you share some stories/information. I know my visitors would enjoy your work.
If you’re even remotely interested, feel free to send
me an e-mail.
Between the massive table and the range of spindle drum sizes included, the Ridgid EB4424 can handle a huge range of sanding duties with ease.
Hello! I just wish to offer you a huge thumbs up for the excellent info you’ve got right here on this post.
I will be coming back to your web site for
more soon.
Good web site you have here.. It’s difficult to find high quality writing like yours these days. I seriously appreciate individuals like you! Take care!!
Its like you read my mind! You appear to know a lot about this, like you wrote the book in it or something.
I think that you can do with some pics to drive the message home a bit, but other
than that, this is excellent blog. An excellent read.
I’ll definitely be back.
Rising debt levels for both of the rolling 3-year periods, are allowed for as long as the debt-to-GDP ratio of the member state does not exceed 60 in the latest recorded fiscal year.
My brother recommended I might like this website.
He used to be totally right. This submit truly made my day.
You cann’t consider simply how a lot time I had spent for
this info! Thanks!
May I just say what a relief to uncover somebody that actually knows what they are talking about on the internet. You definitely understand how to bring an issue to light and make it important. More people need to look at this and understand this side of the story. It’s surprising you aren’t more popular since you definitely possess the gift.
Financial Report 2022. European Investment Bank.
This is the perfect site for everyone who wishes to understand this topic. You know a whole lot its almost tough to argue with you (not that I personally would want to…HaHa). You definitely put a new spin on a topic that has been written about for ages. Great stuff, just excellent.
Thanks for every other informative blog. The place else could
I am getting that type of information written in such a perfect method?
I’ve a venture that I’m simply now running on, and I have been on the glance out
for such info.
I enjoy what you guys are up too. This sort of clever work
and reporting! Keep up the good works guys I’ve included you guys
to blogroll.
It’s perfect time to make some plans for the long run and
it’s time to be happy. I have read this publish and if I may
just I wish to suggest you some interesting issues or tips.
Perhaps you can write next articles regarding this article.
I wish to read more issues approximately it!
I couldn’t resist commenting. Perfectly written!
First off I would like to say terrific blog! I had a quick question in which I’d like to ask if
you do not mind. I was interested to know how you center
yourself and clear your thoughts prior to writing.
I have had a difficult time clearing my mind in getting my thoughts out there.
I do take pleasure in writing however it just seems like the first 10
to 15 minutes are generally lost just trying to figure out how to
begin. Any suggestions or hints? Kudos!
This site certainly has all the information I needed concerning
this subject and didn’t know who to ask.
Great blog! Is your theme custom made or did you download it from somewhere?
A design like yours with a few simple adjustements would really make my blog shine.
Please let me know where you got your design. Appreciate it
I really like it when folks come together and share thoughts. Great website, stick with it.
Its like you read my mind! You appear to know so much about this,
like you wrote the book in it or something. I think that you can do with
some pics to drive the message home a little bit, but other than that, this is magnificent blog.
A great read. I’ll definitely be back.
After looking at a few of the articles on your website, I really like your way of blogging. I book marked it to my bookmark website list and will be checking back in the near future. Please visit my website as well and let me know your opinion.
It’s really very complex in this active life to listen news on Television, therefore I simply
use the web for that purpose, and obtain the most up-to-date news.
Wonderful article! This is the type of info that should be shared across the net.
Disgrace on the search engines for now not positioning this submit higher!
Come on over and visit my site . Thanks =)
An outstanding share! I have just forwarded this onto a friend who was conducting a little research on this. And he actually bought me lunch because I found it for him… lol. So let me reword this…. Thank YOU for the meal!! But yeah, thanx for spending time to talk about this subject here on your site.
It’s remarkable to go to see this web site and reading the views of all colleagues about this paragraph, while I am also eager
of getting experience.
The very next time I read a blog, Hopefully it does not disappoint me as much as this one. After all, Yes, it was my choice to read through, however I truly thought you’d have something helpful to talk about. All I hear is a bunch of whining about something you can fix if you weren’t too busy looking for attention.
I seriously love your site.. Excellent colors & theme. Did you build this site yourself? Please reply back as I’m trying to create my own site and would love to learn where you got this from or what the theme is named. Thank you.
Write more, thats all I have to say. Literally, it seems as though you relied on the video to make your point. You definitely know what youre talking about, why throw away your intelligence on just posting videos to your site when you could be giving us something enlightening to read?
After looking at a number of the blog articles on your web page, I seriously appreciate your way of blogging. I bookmarked it to my bookmark website list and will be checking back soon. Take a look at my website too and let me know what you think.
At this time it seems like Movable Type is the top
blogging platform available right now. (from what I’ve read)
Is that what you are using on your blog?
Interesting blog! Is your theme custom made or did you download
it from somewhere? A design like yours with a few simple adjustements would really make my blog stand out.
Please let me know where you got your design. Bless you
A motivating discussion is definitely worth comment.
I do think that you ought to publish more
about this topic, it may not be a taboo subject but generally folks don’t discuss these subjects.
To the next! All the best!!
Do you have a spam problem on this site; I also am a blogger,
and I was wondering your situation; many of us
have created some nice methods and we are looking to swap methods with other folks,
why not shoot me an e-mail if interested.
Howdy! I could have sworn I’ve been to this site before but after going through many of the articles I realized it’s new to me. Anyways, I’m definitely pleased I came across it and I’ll be bookmarking it and checking back frequently.
I know this if off topic but I’m looking into starting my own weblog and was wondering what all
is needed to get setup? I’m assuming having a blog like yours would cost a pretty penny?
I’m not very internet savvy so I’m not 100% sure.
Any suggestions or advice would be greatly appreciated. Thanks
Howdy! I simply want to offer you a huge thumbs up for your excellent information you have here on this post. I’ll be coming back to your website for more soon.
Saved as a favorite, I really like your website!
I discovered your website web site online and appearance many of your early posts. Continue to keep up the really good operate. I recently extra encourage Rss to my MSN News Reader. Looking for toward reading far more from you down the line!…
I was wondering if you ever considered changing
the page layout of your blog? Its very well written;
I love what youve got to say. But maybe you could a little
more in the way of content so people could connect with it better.
Youve got an awful lot of text for only having 1 or two
images. Maybe you could space it out better?
I blog quite often and I genuinely thank you for your content. This great article has really peaked my interest. I’m going to book mark your website and keep checking for new details about once a week. I subscribed to your Feed as well.
An outstanding share! I’ve just forwarded this onto a friend who has been conducting a little research on this. And he in fact ordered me breakfast simply because I stumbled upon it for him… lol. So let me reword this…. Thanks for the meal!! But yeah, thanx for spending some time to discuss this subject here on your site.
camping have been the best activity that we can have during the summer, i love to roast marshmallows on a campfire,.
With everything which seems to be developing within this particular subject matter, many of your points of view are very radical. Having said that, I am sorry, because I can not subscribe to your entire idea, all be it exhilarating none the less. It seems to everybody that your opinions are actually not completely validated and in fact you are generally yourself not completely convinced of your argument. In any event I did appreciate examining it.
College schooling specifically, is of paramount significance in shaping younger hearts and minds and securing a vivid future for them.
Learn how to cut a stylish wolf lower, shag, or yunabis haircut with this straightforward-to-follow video tutorial and wear it perfectly for any occasion.
Hi! I could have sworn I’ve visited this web site before but after going through many of the posts I realized it’s new to me. Regardless, I’m definitely delighted I came across it and I’ll be book-marking it and checking back often.
Greetings! I know this is kinda off topic but I’d figured I’d ask.
Would you be interested in exchanging links or maybe guest authoring a blog post
or vice-versa? My site discusses a lot of the
same topics as yours and I think we could greatly benefit from each other.
If you are interested feel free to send me an email. I look forward to hearing from you!
Great blog by the way!
Next time I read a blog, I hope that it doesn’t disappoint me just as much as this one. I mean, Yes, it was my choice to read, however I truly thought you would probably have something helpful to say. All I hear is a bunch of crying about something you could fix if you weren’t too busy searching for attention.
Good post. I learn something totally new and challenging on websites I stumbleupon everyday.
It will always be exciting to read content from other authors and practice a little something from other sites.
Hi there! This is kind of off topic but I need some help from an established blog.
Is it very hard to set up your own blog? I’m not very techincal
but I can figure things out pretty quick.
I’m thinking about creating my own but I’m not sure where to start.
Do you have any tips or suggestions? Appreciate it
It is perfect time to make some plans for the longer term and it is time to be happy.
I have learn this post and if I may just I want to suggest you some attention-grabbing issues or suggestions.
Perhaps you could write next articles referring to this article.
I desire to learn more things about it!
Does your blog have a contact page? I’m having problems locating
it but, I’d like to shoot you an e-mail. I’ve got some recommendations for your blog you might be interested in hearing.
Either way, great site and I look forward to
seeing it develop over time.
This is a topic that’s close to my heart… Thank you! Exactly where are your contact details though?
What’s up, after reading this remarkable paragraph i am as well happy to share my experience here with friends.
You lost me, friend. I mean, I assume I get what youre indicating. I have an understanding of what you are saying, but you just appear to have forgotten that you will find some other people inside the world who view this issue for what it really is and may possibly not agree with you. You may be turning away a decent amount of people who may have been fans of your website.
Gucci Handbags Outlet I quite like checking in daily to talk to your musings. I’ve your page bookmarked on my small must read list!
What’s Taking place i’m new to this, I stumbled upon this
I have found It absolutely useful and it has helped me
out loads. I hope to give a contribution & assist different
customers like its helped me. Great job.
She is survived by three sons, Charles T. Ok.
Pretty! This has been an extremely wonderful post. Thank you for supplying this information.
You need to be a part of a contest for one of the best websites on the internet.
I most certainly will recommend this blog!
Check out the array of children’ Halloween costume options — from spooky to house age to only plain foolish — we have compiled for you right here.
Goetz Kluge (December 2017).
I’d like to thank you for the efforts you’ve put in writing this website.
I’m hoping to view the same high-grade content from you later on as well.
In truth, your creative writing abilities has motivated me to get my very own site now 😉
Hello there, There’s no doubt that your website could be having internet browser compatibility issues. When I look at your website in Safari, it looks fine but when opening in IE, it’s got some overlapping issues. I just wanted to provide you with a quick heads up! Other than that, wonderful website.
Nice post. I find out some thing more challenging on various blogs everyday. Most commonly it is stimulating to learn content off their writers and use a specific thing from their site. I’d choose to use some while using content on my small weblog regardless of whether you don’t mind. Natually I’ll offer you a link in your web blog. Many thanks for sharing.
Some genuinely great info , Glad I discovered this.
Aw, this was a very nice post. Taking the time and actual effort to produce a top notch article… but what can I say… I procrastinate a lot and don’t seem to get anything done.
A motivating discussion is definitely worth comment. There’s no doubt that that you need to write more about this issue, it may not be a taboo matter but typically people do not speak about such subjects. To the next! Cheers.
A formidable share, I simply given this onto a colleague who was doing a bit of analysis on this. And he actually purchased me breakfast as a result of I discovered it for him.. smile. So let me reword that: Thnx for the treat! However yeah Thnkx for spending the time to discuss this, I feel strongly about it and love reading more on this topic. If potential, as you grow to be expertise, would you mind updating your weblog with more details? It’s highly helpful for me. Huge thumb up for this blog submit!
Great web site you have got here.. It’s difficult to find good quality writing like yours nowadays. I truly appreciate individuals like you! Take care!!
You are so cool! I do not believe I’ve truly read through something like this before. So great to discover someone with some original thoughts on this issue. Seriously.. many thanks for starting this up. This web site is something that is needed on the internet, someone with some originality.
Although Flagstaff has a low African American inhabitants, it had seen large immigration of black individuals from the Southern United States in the midst of the twentieth century throughout the good Migration.
whoah this weblog is excellent i really like studying your articles.
Stay up the great work! You understand, many people are looking round for this info, you can aid them greatly.
Hello! I’m at work surfing around your blog from
my new iphone 3gs! Just wanted to say I love reading
through your blog and look forward to all your posts!
Keep up the excellent work!
By following knowledgeable guidance, assembling a properly-stocked storm equipment, guaranteeing the security of your house, and obtaining appropriate insurance protection, you will help protect your self and your beloved ones from the risks posed by hurricanes.
I couldn’t refrain from commenting. Exceptionally well written!
always i used to read smaller content that as
well clear their motive, and that is also happening with this piece of writing which
I am reading at this place.
Interesting blog! Is your theme custom made
or did you download it from somewhere? A theme like yours
with a few simple adjustements would really make my blog jump out.
Please let me know where you got your theme.
Many thanks
Very good article. I’m going through many of these issues as
well..
Good post. I learn something new and challenging on websites I stumbleupon on a daily basis. It’s always exciting to read through articles from other writers and practice something from other sites.
This site truly has all of the information I wanted about this subject and didn’t know who to ask.
I enjoy what you guys are up too. Such clever work and coverage!
Keep up the wonderful works guys I’ve incorporated
you guys to my personal blogroll.
Good post. I will be facing a few of these issues as well..
I constantly spent my half an hour to read this website’s
articles all the time along with a cup of coffee.
I always spent my half an hour to read this blog’s posts everyday along with a cup of
coffee.
Ahaa, its good dialogue on the topic of this paragraph here at this blog,
I have read all that, so now me also commenting at this place.
Hi there! I know this is kind of off topic but I was wondering
if you knew where I could get a captcha plugin for my comment form?
I’m using the same blog platform as yours and I’m having difficulty finding one?
Thanks a lot!
This is a very good tip particularly to those fresh to the blogosphere. Brief but very accurate info… Thanks for sharing this one. A must read article.
Unquestionably believe that that you said. Your favorite reason seemed
to be on the internet the easiest thing to bear in mind of.
I say to you, I certainly get annoyed even as other people think about concerns that they just don’t understand about.
You controlled to hit the nail upon the highest and defined out the whole
thing without having side effect , other folks can take a
signal. Will probably be again to get more.
Thanks
I’m extremely inspired along with your writing abilities as neatly as with the
layout in your weblog. Is this a paid subject or did you customize it
your self? Anyway keep up the nice high quality writing, it is uncommon to peer a great weblog like this one
these days..
What a information of un-ambiguity and preserveness of valuable know-how about unexpected
emotions.
The very next time I read a blog, I hope that it won’t fail me as much as this particular one. After all, I know it was my choice to read, nonetheless I genuinely believed you would probably have something useful to say. All I hear is a bunch of crying about something you could possibly fix if you were not too busy seeking attention.
It’s going to be ending of mine day, but before end I am reading
this great article to improve my experience.
Rental income, growth potential, location, amenities, and appreciation are all components thought-about when assigning these grades to properties.
You’ve made some decent points there. I looked on the net for more information about the issue and found most individuals will go along with your views on this site.
Howdy would you mind letting me know which webhost you’re utilizing? I’ve loaded your blog in 3 different web browsers and I must say this blog loads a lot quicker then most. Can you recommend a good hosting provider at a reasonable price? Cheers, I appreciate it!
In observe, futures exchanges are normally commodity exchanges, i.e., all derivatives, together with monetary derivatives, are usually traded at commodity exchanges.
Hello, just wanted to tell you, I liked this blog post. It was practical.
Keep on posting!
Wonderful post! We will be linking to this great article on our website. Keep up the good writing.
You are my aspiration, I own few web logs and infrequently run out from to brand.
Holiday had been a socialist throughout his life and, together with his wife Kate and daughter Winifred, supported the Suffragette motion.
It’s hard to find knowledgeable people for this subject, but you seem like you know what you’re talking about! Thanks
That is one cost you won’t notice straight away, however when you are able to promote your automobile, it means you will not be capable of get as a lot money for it as you would if it was model new.
My brother suggested I might like this blog. He was entirely
right. This post actually made my day. You cann’t imagine simply how much time
I had spent for this information! Thanks!
I must thank you for the efforts you have put in writing this blog. I really hope to check out the same high-grade blog posts from you later on as well. In truth, your creative writing abilities has inspired me to get my very own blog now 😉
Hello, I believe your web site may be having internet browser compatibility problems. When I look at your website in Safari, it looks fine however, if opening in IE, it has some overlapping issues. I just wanted to provide you with a quick heads up! Apart from that, fantastic website!
Attractive section of content. I just stumbled
upon your site and in accession capital to assert that I get in fact
enjoyed account your blog posts. Anyway I will be subscribing to your feeds and even I achievement you
access consistently fast.
I truly love your blog.. Very nice colors & theme. Did you make this web site yourself? Please reply back as I’m hoping to create my very own website and would like to find out where you got this from or exactly what the theme is named. Appreciate it.
excellent put up, very informative. I wonder why the opposite experts
of this sector don’t notice this. You must continue your writing.
I am sure, you’ve a huge readers’ base already!
Hello there, I discovered your web site by the use of Google at the same time as looking for a similar
matter, your web site got here up, it appears good. I have bookmarked it in my google bookmarks.
Hi there, simply was alert to your blog via Google, and found that
it is really informative. I’m gonna watch out for brussels.
I will be grateful when you proceed this in future.
Numerous folks might be benefited out of your writing.
Cheers!
I am really thankful to the holder of this web site who has shared this wonderful paragraph at at this place.
Hey I know this is off topic but I was wondering if you knew of any widgets
I could add to my blog that automatically tweet my newest twitter updates.
I’ve been looking for a plug-in like this for quite some
time and was hoping maybe you would have some experience with something like this.
Please let me know if you run into anything. I truly enjoy
reading your blog and I look forward to your new updates.
Hello my friend! I wish to say that this article is awesome,
great written and come with approximately all significant infos.
I’d like to peer extra posts like this .
I blog quite often and I really appreciate your content. Your article has really peaked my interest. I will book mark your blog and keep checking for new information about once per week. I subscribed to your Feed as well.
Hello! I just wish to offer you a big thumbs up for your excellent info you’ve got right here on this post. I will be returning to your blog for more soon.
Britain is a mini island where the population is constantly rising, the planning controls are strict and the tax system is such that is in the support of the property.
Spot on with this write-up, I actually believe this website needs a great deal more attention. I’ll probably be back again to read through more, thanks for the info.
Heya this is somewhat of off topic but I was wanting to know if blogs use WYSIWYG editors or if you have to manually code with HTML.
I’m starting a blog soon but have no coding know-how so I wanted to get guidance from someone with experience.
Any help would be greatly appreciated!
Right here is the perfect site for anybody who hopes to understand this topic. You understand so much its almost tough to argue with you (not that I really would want to…HaHa). You definitely put a fresh spin on a subject which has been discussed for ages. Wonderful stuff, just excellent.
There are different types of license, and while legal, not all are issued by the Security Exchange Commission.
Good article. I’m going through some of these issues as well..
Sophia (1769-1841) was invited to attend Martha Washington’s first public occasion in Philadelphia.
Link exchange is nothing else except it is only placing the other person’s web site link on your page
at appropriate place and other person will also do same in favor of you.
I’m gone to say to my little brother, that he should also pay a quick visit this webpage on regular
basis to obtain updated from hottest reports.
Spot on with this write-up, I honestly feel this website needs far more attention. I’ll probably be returning to read more, thanks for the info!
Right here is the right webpage for anybody who wishes to find out about this topic.
You understand a whole lot its almost hard to argue with you
(not that I really will need to…HaHa). You certainly
put a brand new spin on a subject which has been written about for many years.
Wonderful stuff, just great!
Your style is so unique compared to other folks I have read stuff from. Thank you for posting when you’ve got the opportunity, Guess I’ll just book mark this page.
This is a topic that’s close to my heart… Many thanks! Exactly where can I find the contact details for questions?
I have read so many posts on the topic of the blogger
lovers but this post is genuinely a good piece of writing,
keep it up.
Nice post. I learn something totally new and challenging
on websites I stumbleupon every day. It will always be exciting to read content from other writers and practice something from other websites.
I’m not that much of a online reader to be honest but your sites really nice, keep
it up! I’ll go ahead and bookmark your website to come
back later. All the best
Hi, I do believe this is a great website. I stumbledupon it 😉 I am going to revisit once again since i have book-marked it. Money and freedom is the greatest way to change, may you be rich and continue to help others.
Aw, this was a really nice post. Taking the time and actual effort to generate a good article… but what can I say… I hesitate a whole lot and don’t seem to get nearly anything done.
I wanted to thank you for this fantastic read!! I definitely loved every little bit of it. I have you saved as a favorite to check out new stuff you post…
Woah! I’m really loving the template/theme of this site.
It’s simple, yet effective. A lot of times it’s very
difficult to get that “perfect balance” between superb usability and appearance.
I must say that you’ve done a superb job with this. Additionally, the blog loads super quick for me on Firefox.
Outstanding Blog!
Great web site you have got here.. It’s hard to find excellent writing like yours these days.
I honestly appreciate individuals like you!
Take care!!
Pretty section of content. I simply stumbled upon your web site and in accession capital to say that I acquire actually loved account your blog posts.
Any way I will be subscribing on your augment and even I success
you get entry to constantly quickly.
Thanks for the auspicious writeup. It if truth be told was once a entertainment account it.
Look complex to more introduced agreeable from you! By the
way, how can we keep up a correspondence?
Good article! We will be linking to this great post on our website. Keep up the great writing.
It’s wonderful that you are getting thoughts from this article
as well as from our argument made at this time.
I’m extremely pleased to discover this page. I want to to thank you for ones time for this particularly wonderful read!! I definitely savored every bit of it and i also have you book-marked to check out new information on your web site.
More over the companies that are proven assets of a desired fund are promptly assessed by analyzing the Fundamental Data Reports and Management Discussion Reports.
This blog was… how do I say it? Relevant!! Finally I have found something that helped me. Kudos.
Right now it appears like Expression Engine is the top blogging platform out
there right now. (from what I’ve read) Is that what you’re using on your blog?
You may get something from a thoughtful quote to a ravishing flower etched on your chest in black ink.
Aw, this was a really nice post. Spending some time and actual effort to generate a good article… but what can I say… I procrastinate a whole lot and never manage to get anything done.
Hi there to every , as I am in fact keen of reading this blog’s post to be updated daily.
It carries pleasant stuff.
Great article. I’m going through a few of these issues as well..
Aw, this was a really good post. Finding the time and actual effort to produce a really good article… but what can I say… I put things off a lot and never seem to get nearly anything done.
Hey, I loved your post! Check out my site: ANCHOR.
I’d like to thank you for the efforts you’ve put in penning this website. I’m hoping to check out the same high-grade content from you later on as well. In truth, your creative writing abilities has encouraged me to get my very own blog now 😉
Hey there! I’m at work surfing around your blog from my new iphone 4!
Just wanted to say I love reading your blog and look forward to all your posts!
Keep up the excellent work!
I’m pretty pleased to uncover this page. I need to to thank you for ones time for this fantastic read!! I definitely enjoyed every bit of it and i also have you saved to fav to check out new stuff in your web site.
Way cool! Some very valid points! I appreciate
you writing this post and the rest of the site is also really good.
I every time emailed this weblog post page to all my friends, because if like to read it afterward my contacts will too.
Wonderful, what a webpage it is! This weblog provides useful information to us, keep
it up.
You made some good points there. I looked on the internet to find out more about the issue and found most individuals will go along with your views on this web site.
Good day! I simply want to give you a huge thumbs up for the excellent info you have here on this post. I will be returning to your web site for more soon.
Thanks for sharing your info. I really appreciate your efforts and I will be waiting for your further
write ups thank you once again.
Your style is very unique compared to other people I’ve read stuff from. I appreciate you for posting when you have the opportunity, Guess I will just bookmark this web site.
hello there and thank you for your info – I have certainly picked up something
new from right here. I did however expertise some technical issues using this website,
since I experienced to reload the website many times
previous to I could get it to load properly.
I had been wondering if your web hosting is OK? Not that I am complaining, but sluggish loading instances times
will very frequently affect your placement in google and
could damage your quality score if ads and marketing with Adwords.
Well I’m adding this RSS to my e-mail and could look out for much more of your respective interesting content.
Make sure you update this again soon.
These are highly dependent on consumer generated content online, within the type of feedbacks and critiques posted on on-line travel businesses and global distribution methods.
Good info. Lucky me I found your site by chance (stumbleupon).
I’ve saved it for later!
Hi there! I just wanted to ask if you ever have any trouble with hackers?
My last blog (wordpress) was hacked and I ended up losing several weeks of
hard work due to no backup. Do you have any solutions to stop hackers?
Hi, Neat post. There’s a problem together with
your website in internet explorer, would test this? IE still is the market leader and a large component to folks will
miss your great writing because of this problem.
That is very interesting, You are an overly skilled blogger.
I’ve joined your feed and look forward to searching for more of
your excellent post. Also, I’ve shared your web site in my social networks
For a few years, shaving cream was puffy and dense and got here out of a can that regarded like a barber pole.
Hello there, I think your web site could be having browser compatibility issues. When I take a look at your blog in Safari, it looks fine however, if opening in I.E., it has some overlapping issues. I simply wanted to give you a quick heads up! Apart from that, wonderful website.
My family all the time say that I am killing my time here at web, but
I know I am getting experience daily by reading such pleasant content.
Hello! Someone in my Facebook group shared this website
with us so I came to take a look. I’m definitely enjoying the information. I’m book-marking and will be tweeting this
to my followers! Outstanding blog and terrific design.
Today, while I was at work, my cousin stole my iphone and tested to
see if it can survive a 30 foot drop, just so she can be a youtube sensation. My iPad is now broken and she has 83 views.
I know this is totally off topic but I had to share it with someone!
That is a great tip particularly to those fresh to the blogosphere. Brief but very accurate information… Many thanks for sharing this one. A must read article.
The next time I read a blog, I hope that it won’t disappoint me as much as this particular one. I mean, I know it was my choice to read, however I actually believed you’d have something useful to talk about. All I hear is a bunch of complaining about something that you could possibly fix if you weren’t too busy searching for attention.
Very good post! We are linking to this great content on our site.
Keep up the great writing.
This is a topic that’s close to my heart… Many thanks! Where can I find the contact details for questions?
Hi there! I could have sworn I’ve been to this website before but after going through many of the articles I realized it’s new to me. Nonetheless, I’m certainly delighted I found it and I’ll be bookmarking it and checking back often!
You made some really good points there. I checked on the internet to learn more about the issue and found most individuals will go along with your views on this site.
Hello, There’s no doubt that your blog could be having internet browser compatibility problems. Whenever I look at your blog in Safari, it looks fine however when opening in I.E., it’s got some overlapping issues. I just wanted to provide you with a quick heads up! Other than that, wonderful blog.
Very good post! We will be linking to this great content on our site. Keep up the good writing.
I am really glad to glance at this weblog posts which
includes plenty of useful data, thanks for providing these kinds of statistics.
These are truly wonderful ideas in on the topic
of blogging. You have touched some pleasant points here.
Any way keep up wrinting.
It’s very straightforward to find out any topic on web as compared to books,
as I found this article at this website.
Excellent blog! Do you have any helpful hints for aspiring writers?
I’m planning to start my own site soon but I’m a little lost on everything.
Would you recommend starting with a free platform
like WordPress or go for a paid option? There are so many options
out there that I’m totally overwhelmed .. Any suggestions?
Thanks!
Inspiring quest there. What happened after?
Thanks!
This page definitely has all of the information and facts I wanted concerning this subject and didn’t know who to ask.
Excellent article! We are linking to this great content on our website.
Keep up the great writing.
I every time spent my half an hour to read this blog’s articles or reviews everyday along with a
mug of coffee.
I’m amazed, I must say. Seldom do I encounter a blog that’s both educative and amusing, and let me tell you, you’ve hit the nail on the head. The problem is something not enough people are speaking intelligently about. I’m very happy that I found this during my search for something regarding this.
Everything is very open with a really clear explanation of the challenges. It was truly informative. Your site is extremely helpful. Many thanks for sharing!
This is a really good tip especially to those new to the blogosphere. Short but very accurate information… Thank you for sharing this one. A must read post!
You need to take part in a contest for one of the finest blogs online. I am going to highly recommend this site!
Oh my goodness! Impressive article dude!
Thank you so much, However I am going through problems with your RSS.
I don’t know why I cannot join it. Is there anybody else having similar RSS problems?
Anyone who knows the solution can you kindly respond? Thanks!!
Hello there! I could have sworn I’ve visited this blog before but after looking at some of the articles I realized it’s new to me. Anyways, I’m definitely pleased I discovered it and I’ll be bookmarking it and checking back frequently.
Hey there! I’ve been reading your website for a long time now
and finally got the bravery to go ahead and give you a shout out from New Caney Texas!
Just wanted to tell you keep up the great work!
Greetings, I do believe your site could possibly be having web browser compatibility issues. When I look at your website in Safari, it looks fine but when opening in Internet Explorer, it has some overlapping issues. I merely wanted to provide you with a quick heads up! Aside from that, great site.
Having read this I believed it was really informative. I appreciate you taking the time and energy to put this short article together. I once again find myself personally spending way too much time both reading and leaving comments. But so what, it was still worthwhile.
Post writing is also a fun, if you know then you can write
otherwise it is complicated to write.
I was able to find good info from your blog articles.
I blog frequently and I seriously appreciate your content. Your article has truly peaked my interest. I am going to book mark your website and keep checking for new information about once per week. I subscribed to your RSS feed as well.
I blog often and I really thank you for your information. The article has truly peaked my interest. I am going to take a note of your site and keep checking for new details about once a week. I subscribed to your RSS feed as well.
It’s perfect time to make a few plans for the future and it’s time
to be happy. I have learn this submit and if I may
I want to recommend you few fascinating things or tips.
Maybe you could write next articles regarding this article.
I desire to learn even more issues about it!
Hurrah, that’s what I was looking for, what a information! existing here at this
weblog, thanks admin of this web site.
It’s very straightforward to find out any topic
on net as compared to textbooks, as I found this paragraph at this
web site.
My spouse and I absolutely love your blog and find almost all of your post’s to
be precisely what I’m looking for. Does one offer guest writers to write content for you personally?
I wouldn’t mind producing a post or elaborating
on some of the subjects you write concerning here.
Again, awesome weblog!
Hi there! This article could not be written much better!
Going through this article reminds me of my previous roommate!
He continually kept preaching about this.
I’ll forward this post to him. Pretty sure he’ll have a
great read. Thanks for sharing!
It’s an remarkable paragraph designed for all the web visitors; they
will get benefit from it I am sure.
That is very interesting, You’re an excessively professional blogger.
I have joined your feed and look ahead to looking for more of your excellent post.
Also, I’ve shared your website in my social networks
You could definitely see your enthusiasm in the work you write.
The arena hopes for even more passionate writers like you who are not afraid to say how they believe.
All the time follow your heart.
I every time emailed this weblog post page to all my friends, because if like to read it next my friends will too.
Hi there just wanted to give you a quick heads up. The text
in your content seem to be running off the screen in Internet explorer.
I’m not sure if this is a format issue or something to do with internet
browser compatibility but I figured I’d post to let you know.
The design and style look great though! Hope you get the issue solved soon. Thanks
First off I would like to say wonderful blog! I had a quick
question which I’d like to ask if you do not mind. I was curious to find out how
you center yourself and clear your thoughts before writing.
I’ve had difficulty clearing my thoughts in getting my ideas
out. I truly do take pleasure in writing however it just seems like the first 10 to 15 minutes are generally wasted just trying to
figure out how to begin. Any ideas or hints? Thank you!
Greetings, I believe your website could be having internet browser compatibility
problems. When I take a look at your website in Safari, it looks fine however,
when opening in Internet Explorer, it’s got some overlapping
issues. I just wanted to provide you with a quick heads up!
Apart from that, excellent site!
I pay a visit daily some websites and information sites to read content, but
this web site offers quality based posts.
Wow, fantastic blog structure! How lengthy have you ever been blogging
for? you make blogging look easy. The entire glance of your site is fantastic, let alone the content!
William noticed his father one last time in 1785, when Benjamin stopped in Britain on his return journey to the U.S.
bookmarked!!, I love your blog!
Thank you, I have just been searching for information approximately this topic for ages and yours is the best I have
found out till now. However, what about the conclusion? Are you certain about the supply?
You ought to take part in a contest for one of the greatest blogs on the web. I most certainly will recommend this blog!
Greetings from Florida! I’m bored to tears at work so I decided to browse your site on my iphone during lunch break.
I love the information you present here and
can’t wait to take a look when I get home. I’m amazed at how fast
your blog loaded on my phone .. I’m not even using WIFI, just 3G ..
Anyhow, superb site!
Hey! This is my first visit to your blog! We are a collection of volunteers and starting a new project in a community in the same niche.
Your blog provided us valuable information to work on. You have done a extraordinary job!
This article provides clear idea in favor of the new visitors of
blogging, that really how to do blogging and
site-building.
Then, they aid you manage company taxs compliance.
Everything is very open with a really clear explanation of the challenges. It was really informative. Your website is very useful. Many thanks for sharing!
An outstanding share! I’ve just forwarded this onto a co-worker who has been doing a little research on this. And he in fact bought me breakfast due to the fact that I discovered it for him… lol. So allow me to reword this…. Thanks for the meal!! But yeah, thanx for spending time to discuss this topic here on your blog.
Hello! I just wanted to ask if you ever have any trouble with hackers?
My last blog (wordpress) was hacked and I ended up losing several weeks of hard
work due to no back up. Do you have any solutions to
stop hackers?
Thanks designed for sharing such a good thought, paragraph is good,
thats why i have read it fully
What’s Going down i’m new to this, I stumbled upon this
I’ve found It absolutely helpful and it has helped me out loads.
I hope to give a contribution & assist different customers like its helped me.
Good job.
Next time I read a blog, I hope that it won’t disappoint me just as much as this particular one. I mean, Yes, it was my choice to read, but I truly believed you’d have something helpful to talk about. All I hear is a bunch of whining about something that you could fix if you were not too busy seeking attention.
Hi there very cool blog!! Man .. Beautiful .. Amazing ..
I’ll bookmark your blog and take the feeds also? I am glad
to find a lot of useful info right here in the submit, we’d like
work out extra strategies in this regard,
thank you for sharing. . . . . .
Oh my goodness! Impressive article dude! Thank you, However I am having issues with your RSS. I don’t understand the reason why I am unable to subscribe to it. Is there anybody having identical RSS issues? Anyone that knows the solution will you kindly respond? Thanx!!
I’ve been surfing online more than 3 hours nowadays, yet I by no means found any fascinating article like yours.
It’s lovely price enough for me. Personally, if all web owners and bloggers made
just right content material as you probably
did, the net shall be a lot more useful than ever before.
An outstanding share! I have just forwarded this onto a colleague who had been doing a little research on this. And he in fact bought me lunch because I found it for him… lol. So let me reword this…. Thanks for the meal!! But yeah, thanx for spending some time to discuss this matter here on your site.
Fabulous, what a webpage it is! This blog gives useful data to us, keep
it up.
Awesome blog! Do you have any tips for aspiring writers?
I’m hoping to start my own site soon but I’m a little lost on everything.
Would you recommend starting with a free platform like WordPress
or go for a paid option? There are so many options out there that I’m completely
confused .. Any suggestions? Thanks!
Nifty option has a bit higher cost in the percentage than trading the primary stock.
Hi there! I could have sworn I’ve been to this web site before but after browsing through some of the posts I realized it’s new to me. Anyhow, I’m definitely pleased I came across it and I’ll be bookmarking it and checking back regularly.
It’s hard to come by knowledgeable people in this particular topic,
however, you seem like you know what you’re talking about!
Thanks
Excellent, what a blog it is! This web site gives helpful information to us, keep it up.
That enhance will force a client at present paying a minimum of $600 to come up with $1,500 per thirty days, regardless of guarantees made or any promotional charges that may have been used to get the balance transferred to Chase.
Very good post! We will be linking to this great content on our website. Keep up the good writing.
Your means of explaining everything in this piece of
writing is really nice, every one be capable of without difficulty know it, Thanks a
lot.
If some one needs to be updated with most up-to-date technologies therefore he must be pay a visit this website and be up
to date everyday.
When I originally commented I seem to have clicked on the -Notify me when new comments are added- checkbox and from now on whenever a comment
is added I recieve 4 emails with the same comment. There has to be a means you
can remove me from that service? Thanks!
WOW just what I was looking for. Came here by searching
for windows activator
I’m extremely pleased to uncover this great site. I want to to thank you for your time just for this fantastic read!! I definitely appreciated every bit of it and i also have you saved to fav to see new information on your blog.
Hello to every body, it’s my first go to see of this weblog; this weblog contains
remarkable and truly fine information in favor of visitors.
I must thank you for the efforts you’ve put in writing this blog. I really hope to view the same high-grade blog posts by you in the future as well. In fact, your creative writing abilities has inspired me to get my very own site now 😉
I was suggested this web site by my cousin. I am not sure whether this
post is written by him as nobody else know such detailed about
my difficulty. You’re wonderful! Thanks!
At this time it appears like Expression Engine is the preferred blogging platform out there right now.
(from what I’ve read) Is that what you’re using on your blog?
Your style is unique compared to other folks I have read stuff from. Thank you for posting when you have the opportunity, Guess I will just bookmark this web site.
Fundamental analysis focuses on the company’s financial and market position, growth prospects and financial performance.
They’re accessible in several designs and supplies and range from the very expensive ones to the reasonably priced bangle units.
Some are fancier, sporting conventional plaster that is textured — “hand-troweled” — for a rustic look or blended with pigment for a Venetian or Moroccan look.
Having read this I thought it was really enlightening. I appreciate you taking the time and energy to put this article together. I once again find myself spending a lot of time both reading and commenting. But so what, it was still worthwhile!
Whatever toy you choose simply make sure that it is too big to get lodged in your French bulldog puppy’s throat.
The cooperation in healthcare between India and Sweden will assist in filling gaps in research and revolutionary expertise to aid provisioning of high quality healthcare.
Nice post. I learn something totally new and challenging on blogs I stumbleupon on a daily basis. It will always be useful to read through articles from other writers and use something from other websites.
Focus on the Process, Not on Results: In trading, you have to pay more attention to the process – like what strategy is used, Money setup and Risk Management – rather than focusing on the results as expected.
Why is it Important to have a Risk-based Cybersecurity Approach?
Entry to the commune is by the D16 road from Allerey in the south passing by way of the village and continuing north-east to Thoisy-le-Désert.
Perhaps the most important mistake made by well-which means recyclers is to wrap items up in plastic grocery bags.
One of the primary benefits of using an open architecture 401(k) plan provider is the ability to include either ETFs or index mutual funds in the plan’s core investment lineup or within a managed model.
I’d like to thank you for the efforts you have put in writing this website. I really hope to view the same high-grade blog posts from you in the future as well. In truth, your creative writing abilities has encouraged me to get my own site now 😉
If you want much more than 6 seats then a minibus might be what you are searching for, which can be discovered in 9, twelve, fifteen and 17 seat versions.
At the moment, the committee did not include the voting rights for Board of Governors.
Brian Clarke. With contributions by Paul Beldock.
The Honourable Mr Justice Percy Ernest Joske, Decide, Commonwealth Industrial Courtroom, and Supreme Courtroom, Australian Capital Territory.
As the twister started to enter the western fringes of Bowling Inexperienced, it quickly intensified and turned robust once more because it produced EF3 damage to homes alongside Rembrandt Court docket.
That is a great tip particularly to those fresh to the blogosphere. Brief but very accurate information… Appreciate your sharing this one. A must read article.
Every weekend i used to visit this website, as i wish for enjoyment, for the reason that this this web site conations in fact fastidious funny information too.
If you’re undecided should you have been getting an SDP, test your advantages letters.
This site was… how do you say it? Relevant!! Finally I’ve found something which helped me. Cheers.
Services for Henry Lewis Brown, 77, of Houston and formerly of Palestine, will probably be at 10 a.m.
I’m impressed, I have to admit. Seldom do I encounter a blog that’s both equally educative and entertaining, and let me tell you, you have hit the nail on the head. The problem is something which not enough folks are speaking intelligently about. I am very happy I came across this during my search for something relating to this.
Aw, this was a really nice post. Finding the time and actual effort to create a really good article… but what can I say… I procrastinate a lot and don’t seem to get nearly anything done.
Hey There. I found your blog using msn. This is a very well written article.
I will be sure to bookmark it and come back to read more of your useful information. Thanks for the post.
I’ll definitely return.
Hi there! This post couldn’t be written any better! Reading through this post reminds me of my previous roommate! He constantly kept talking about this. I’ll forward this information to him. Pretty sure he will have a very good read. Thank you for sharing!
Keep on writing, great job!
I pay a quick visit each day a few sites and information sites
to read articles or reviews, but this website offers quality based writing.
Greetings! Very helpful advice in this particular article! It’s the little changes that will make the greatest changes. Thanks a lot for sharing!
This is my first time pay a quick visit at here and i am genuinely
impressed to read everthing at single place.
You really make it seem so easy with your presentation but I find this topic to be
actually something that I think I would never understand.
It seems too complicated and extremely broad for me.
I am looking forward for your next post, I’ll try
to get the hang of it!
Hi there! This blog post could not be written any better! Looking at this post reminds me of my previous roommate! He constantly kept talking about this. I will send this post to him. Pretty sure he’s going to have a good read. Many thanks for sharing!
Directed and produced by Alan Bell, it was, for the time, a lavish results-drenched production.
Greetings! Very helpful advice within this article!
It is the little changes which will make the largest changes.
Thanks for sharing!
Here is my web page – whete is hot in march
Hi! I could have sworn I’ve been to this site before but after browsing through some of the articles I realized it’s new to me. Anyhow, I’m definitely happy I found it and I’ll be book-marking it and checking back frequently!
Pretty section of content. I just stumbled upon your
site and in accession capital to assert that I acquire actually
enjoyed account your blog posts. Any way I’ll be subscribing to your
augment and even I achievement you access consistently quickly.
There’s definately a great deal to find out about this issue.
I really like all of the points you made.
Pretty! This has been a really wonderful article. Many thanks for supplying these details.
Lieutenant Commander Peter Andrew Francis Grant.
First of all I want to say wonderful blog! I had a quick question which I’d like to ask if you don’t
mind. I was curious to know how you center yourself and clear your thoughts prior to writing.
I’ve had trouble clearing my mind in getting my ideas out there.
I truly do take pleasure in writing but it just seems like
the first 10 to 15 minutes are usually wasted just trying to figure out how to
begin. Any suggestions or tips? Cheers!
This is the right webpage for anybody who really wants to
find out about this topic. You realize a whole lot its
almost tough to argue with you (not that I personally will need to…HaHa).
You definitely put a brand new spin on a subject that’s been discussed for decades.
Excellent stuff, just excellent!
Everything is very open with a clear explanation of the challenges. It was really informative. Your website is very helpful. Thanks for sharing!
It’s hard to come by experienced people in this particular subject, however, you seem like you know what you’re talking about! Thanks
Excellent article. I am facing some of these issues as well..
Next time I read a blog, Hopefully it doesn’t fail me just as much as this particular one. I mean, Yes, it was my choice to read, but I truly believed you would probably have something interesting to say. All I hear is a bunch of moaning about something that you could fix if you were not too busy looking for attention.
Ahaa, its fastidious conversation about this article at this place at this webpage, I have read all that, so now me also commenting here.
It would not get a lot easier than water and cleaning soap.
Hmm is anyone else having problems with the images on this blog loading?
I’m trying to figure out if its a problem on my end or if it’s the blog.
Any suggestions would be greatly appreciated.
When I originally commented I appear to have clicked on the -Notify me when new comments are added- checkbox and from now on whenever a comment is added I receive 4 emails with the exact same comment. Perhaps there is a way you are able to remove me from that service? Cheers.
How ought to I store water for long-time period emergency use?
The market is open for both small and institutional investors for the first time in history.
Fritscher, Lisa (October 3, 2014).
hey there and thank you for your info – I have certainly picked up something
new from right here. I did however expertise a few
technical issues using this site, as I experienced to reload the website many times
previous to I could get it to load properly. I had been wondering if
your hosting is OK? Not that I am complaining, but slow loading instances times will very frequently affect your placement
in google and can damage your high-quality score if advertising and marketing with Adwords.
Well I’m adding this RSS to my e-mail and can look out for a
lot more of your respective interesting content. Ensure that you update this again soon.
I’m amazed, I have to admit. Seldom do I encounter a blog
that’s equally educative and entertaining, and let me tell you, you’ve hit the nail on the head.
The problem is something that not enough men and women are speaking intelligently about.
I’m very happy that I found this in my hunt
for something concerning this.
This is one in all the principle points the EU should deal with in the next term.
Good way of explaining, and fastidious paragraph to obtain data
regarding my presentation topic, which i am going to
convey in school.
After looking over a handful of the blog articles on your site, I really appreciate your technique of blogging. I bookmarked it to my bookmark site list and will be checking back soon. Take a look at my website too and tell me what you think.
Howdy! This is kind of off topic but I need some help
from an established blog. Is it very difficult to set up your own blog?
I’m not very techincal but I can figure things out pretty
quick. I’m thinking about creating my own but I’m not sure
where to start. Do you have any tips or suggestions?
With thanks
whoah this blog is great i love reading your articles.
Keep up the good work! You already know, many people are looking around for this
information, you can aid them greatly.
I blog often and I truly appreciate your information. Your
article has really peaked my interest. I am going to take a note of
your blog and keep checking for new information about once per week.
I opted in for your RSS feed as well.
This is the right website for anybody who really wants to find out about this topic. You know a whole lot its almost tough to argue with you (not that I personally would want to…HaHa). You certainly put a fresh spin on a topic that’s been written about for years. Great stuff, just wonderful.
Excellent article! We will be linking to this great content on our website. Keep up the great writing.
Hi, everything is going perfectly here and ofcourse every one is
sharing data, that’s really excellent, keep up writing.
You will benefit financially here because of a steady cash flow.
Wayne NICHOLS, each of Pawnee; Dale GREGOR of Mannford; Forrest GREGOR of Anchorage, Alaska and Gary GREGOR of Cleveland.
A softphone is client software that loads the VoIP service onto your desktop or laptop.
You really make it appear so easy along with your presentation but I
find this matter to be actually something which
I think I’d by no means understand. It seems too complicated and extremely extensive
for me. I am having a look ahead for your subsequent put up, I will try to get the hang of it!
Usually this ready interval is about six months, but this timeframe can fluctuate depending on the state you’re in and the situation you are affected by.
Why this kind of funding is necessary?
After all, do you know the only two females in the Mystery Van, or the backup singers who performed in that popular cartoon band you always enjoyed?
Application: Market Threat Measurement and Management; Credit Risk Measurement and Management; Operational- and Integrated Risk Administration; Danger Administration and Investment Administration; Present Issues in Monetary Markets.
2011 (Halloween Horror Nights 21) and 2012 (Halloween Horror Nights 22): eight and seven haunted homes, respectively; 25 nights and 22 nights, respectively; $81.99 and $88.99.
However, this effect is not as good as it used to be; the various markets are now fairly correlated, especially the US and Western Europe.
For a wholesome consolation meals, try salmon cakes, or use your trusty canned tuna to make fish chowder.
You often see this sign in areas the place there are few walking paths for individuals as a result of, on certain roads, hitchhiking might be a really harmful selection.
His creative training was first at Regent Street Polytechnic (now the College of Westminster) after which at Edinburgh College of Artwork.
Examples in the United States of Vacation’s work may be seen in the sacristy of St.
Groom’s outfits: The dulha dress in Maharashtra includes a set of white or beige cotton kurta and a dhoti.
This lively eatery gives mouthwatering tacos and flavorful salsas made from domestically sourced substances.
Immersive virtual reality can alter motor control and performance in young adults, indicating the impact of the virtual experience on motor skills.
In 1964, Golden resigned and was succeeded as director by Mildred Compton.
Some tasks, corresponding to mailing invitations and selecting up the rings, obviously can’t be checked off until two months before the massive Day.
They could require certain requirements from you before they are going to guide you on how to invest your money.
Basic lasagna alternates layers of floor beef in tomato sauce with ricotta, mozzarella and Parmesan cheese, and sometimes, you may discover the addition of Asiago, fontina, provolone and other cheeses.
So, visiting Madrid, I get the feeling of a trendy era metropolis.
Or have interpreters obtainable all over the place they go.
The second one could be paired with a number of wireless units without delay whereas the third one has a nice retro design.
Plastering contractors can set up it at the development site by hand or the system can be delivered on site as factory-made panels which are able to attach to a constructing via crane.
How shall I work until this hour?
In the twelfth century early Gothic, the dominant colours were a deep and wealthy blue, and a ruby crimson.
The 20 tax credit score Preservation Tax Incentives reward personal investment in rehabilitating historic properties equivalent to workplaces, rental housing, and retail stores.
It’s particularly important to consider this aspect if you have (or are planning to have) children.
Origin: The Irani Turquoise from the Neyshabur deposit is millennium-previous and yields excessive-quality, rare, and unique coloration-quality Firoza gemstones.
Louisiana state and metropolis civil service departments award a 5-level desire to honorably discharged veterans and 10-point choice to honorably discharged service-connected disabled veterans.
Some buyers choose CDs over other varieties of funding vehicles because of the higher curiosity rates and stability related to CDs.
Leslie Arthur John Moore.
1. Not sufficient attention is paid to increasing the model experience into the e-fulfilment chain.
Hello There. I discovered your blog using msn.
This is an extremely neatly written article. I will make sure to bookmark it and come back to read extra of your
useful info. Thank you for the post. I will certainly comeback.
Maliene, V. (2011). “Specialised property valuation: Multiple criteria decision analysis”.
Piece of writing writing is also a excitement, if
you be acquainted with then you can write otherwise it is complex to write.
If your panels are not producing enough vitality to power the pool pump for long enough then you want to add extra panels – the grid cannot prime up the power.
As part of Kaizen, Toyota has quality circles, which are groups of workers who know how the company works, and whose job it is to find areas for improvement, either through cutting waste, changing a process or improving a product.
Elevating catfish in a barrel — A biological food chain in the back yard produces fresh fish for the table and compost for the garden, by Philip and Joyce Mahan, from Organic Gardening and Farming, November, 1973.
Bias in algorithms: Machine learning models can perpetuate biases present in the data they are trained on, leading to unfair outcomes.
Let’s start with undergraduate IT programs and majors.S.
There is a long-term stability to fixed-rate mortgages that many borrowers find attractive– especially those who plan on staying in their home for a decade or more.
You’re so awesome! I don’t believe I have read a single thing like that before. So great to discover somebody with a few genuine thoughts on this subject. Seriously.. thank you for starting this up. This website is something that is needed on the web, someone with a little originality.
This post provides clear idea in favor of the new people of
blogging, that really how to do blogging.
The soundtrack options music from outstanding well-liked musicians of the time, being among the many movies of this technology that actively explored the industrial hyperlink between a movie and its soundtrack.
As the problems in these CRM companies began to appear, a number of whistleblowers and accusers were prominent, mainly investment institutions, research groups, and individual analysts.
Robert Smith has been married since 1984 to WFM Vivian Smith, additionally a aggressive chess player, who has represented New Zealand at 15 chess olympiads and has received the new Zealand Order of Benefit for her work with junior chess gamers.
I’m impressed, I have to admit. Rarely do I encounter a blog that’s equally educative and entertaining, and let me tell you, you have hit the nail on the head. The issue is something which not enough people are speaking intelligently about. I am very happy I found this in my search for something concerning this.
Hello there! I just wish to offer you a huge thumbs up for the excellent info you have got right here on this post. I am coming back to your website for more soon.
Your style is unique compared to other folks I’ve read stuff from. Thanks for posting when you have the opportunity, Guess I will just bookmark this web site.
I needed to thank you for this excellent read!! I definitely loved every bit of it. I have you saved as a favorite to check out new stuff you post…
Along with the rubble of this mansion and some hedges of its elaborate gardens, solely the original tunnel to the river (damaged via in a number of locations) and the house of Bonaparte’s secretary remain.
Any remaining brush marks will disappear because the varnish dries.
There may be a promise to destroy any newly created money once the economy improves in order to avoid inflation.
sex nhật hiếp dâm trẻ em ấu dâm buôn bán vũ khí ma túy bán súng sextoy chơi đĩ sex bạo lực sex học đường tội phạm tình dục chơi les đĩ đực người mẫu bán dâm
They can kick in any direction; do you know which farm animal this is?
I was able to find good advice from your blog posts.
Nonetheless, not like several other books talked about or seen in Deus Ex, Jacob’s Shadow will not be a real ebook and Andrew Hammond isn’t an actual author.
A motivating discussion is worth comment. There’s no
doubt that that you need to publish more about this subject matter, it may not be a taboo subject but typically folks don’t speak
about these subjects. To the next! Best wishes!!
In the middle of 2011, real personal income excluding government transfer payments fell 5.1.
1. The families of members of the Pink workers’ and peasants’ army are supported by the state and receive a month-to-month subsidy of fifty rubles.
Larger-level commanders yielding to the temptation to direct minor tactical actions may reduce the benefits of superior information systems and the situational understanding they assist.
Although you may be put off by the time period, “weight-bearing exercise” isn’t designed to bulk up your muscles.
However, it may also indicate components have been bent by a collision, or by running over a really bad pothole.
The ban by the Puritans was revoked in 1681 by an English appointed governor, Edmund Andros; however, it was not until the mid-19th century that celebrating Christmas became fashionable within the Boston area.
I thought I might broke my leg because I might never felt something like it earlier than but luckily it isn’t as extreme as what I assumed once i first did it.
Well, to get over with your house works, you possibly can consult with an equity release calculator.
In a number of states inside their habitat range, including Florida, Georgia and Alabama, japanese indigo snakes are labeled as “endangered.” This designation displays the declining populations and habitat loss skilled in these areas.
Brian Barry Cattermole, Grade 7, HM Board of Customs and Excise.
As soon as a liked one is diagnosed with Alzheimer’s illness, relations want to start discussing options for long-term care.
Wallpaper will not be in my budget.
I’m gone to tell my little brother, that he should also pay
a visit this weblog on regular basis to obtain updated from newest news.
This blog was… how do you say it? Relevant!! Finally I’ve found something that helped me.
Thanks a lot!
After looking into a handful of the blog posts on your web page,
I truly appreciate your technique of blogging. I bookmarked
it to my bookmark website list and will be checking back in the near
future. Take a look at my web site too and tell me what you
think.
This is a topic that is near to my heart…
Thank you! Where are your contact details though?
I have read so many content regarding the blogger lovers but this article
is genuinely a fastidious article, keep it up.
Having read this I thought it was very enlightening. I appreciate you spending some time and energy to put this article together. I once again find myself spending way too much time both reading and commenting. But so what, it was still worthwhile.
We’re a group of volunteers and starting a new scheme in our community.
Your site provided us with valuable information to
work on. You’ve done an impressive activity and our whole group shall be thankful to you.
Hey there! I just would like to give you a big thumbs up for the great info you have got right here on this post. I will be coming back to your web site for more soon.
Good site you’ve got here.. It’s hard to find excellent writing like yours these days. I really appreciate people like you! Take care!!
Hello there! This blog post couldn’t be written much better! Going through this post reminds me of my previous roommate! He continually kept preaching about this. I am going to forward this information to him. Fairly certain he will have a great read. Thanks for sharing!
Lesson number four: When leading stocks, after a big run up in price, make huge price gains in a relatively short period of time, this is a warning sign of the market topping.
Howdy! This article couldn’t be written much better! Going through this article reminds me of my previous roommate! He constantly kept preaching about this. I most certainly will forward this post to him. Fairly certain he will have a good read. Thank you for sharing!
Survey shows that Companies who want to reduce employee turnover need to emphasise more on developing better relationships between the staff and focus on Team Building.
We are to prosper and be beneficial leaders, and to serve as models to help others.
Good information. Lucky me I came across your website by chance (stumbleupon). I’ve saved as a favorite for later.
You have made some really good points there. I looked on the internet for additional information about the issue and found most people will go along with your views on this website.
How do lead-acid batteries work?
Why users still use to read news papers when in this technological
globe the whole thing is accessible on web?
The bank didn’t do a lot to strengthen the Iranian capital formation or support then-foreign money of Iran, qiran.
You can even inject collagen into your lips that comes from a very completely different spot by yourself body.
Will I play the identical move once more?
Let’s start. Title this iconic ’70s automotive.
Later, regardless of the 2 being in a long-time period romantic relationship, Pym harbors feelings of inadequacy over Janet’s wealth which initially stops him from marrying her.
In the second sport with white, Anand performed his moves so fast that Gelfand was pressured to make strikes with very few seconds to spare.
Mark Trotman – Daniel Hinton.
Each week, Billboard puts together a chart of the top 100 most popular songs (as well as several other charts) based on a national sample of top 40 radio airplay, top 40 radio playlists, and music sales.
You ought to take part in a contest for one of the highest quality websites on the internet. I most certainly will highly recommend this website!
A comparable 3-Series BMW or Mercedes-Benz C-Class cost thousands more, yet the SVT Contour was easily their equal on a road course or a dragstrip, running 0-60 mph in about 7.5 seconds in most road tests.
Common upkeep: One other consideration is the added weight and complexity of pneumatic tires in comparison with strong tires, which may affect gas effectivity and require extra frequent upkeep.
Hmm it appears like your blog ate my first comment (it was
super long) so I guess I’ll just sum it up what I wrote
and say, I’m thoroughly enjoying your blog. I too am an aspiring
blog writer but I’m still new to everything.
Do you have any recommendations for first-time blog writers?
I’d definitely appreciate it.
Or for that matter any jewellery.
Cities on the map have three spaces for players to place colored wooden houses that show control of that city, plus connections between cities, each marked by a number which shows the cost for connecting cities along that route.
Whereas being foreclosed on does have a adverse influence in your credit score, it does not damage it beyond restore.
hey there and thank you for your information – I’ve certainly
picked up something new from right here. I did however expertise several
technical issues using this website, as I experienced to reload the
site a lot of times previous to I could get it to load correctly.
I had been wondering if your web hosting is OK?
Not that I’m complaining, but sluggish loading instances times will often affect your placement in google and can damage your quality score if advertising and marketing with Adwords.
Well I am adding this RSS to my e-mail and can look out for a
lot more of your respective exciting content.
Make sure you update this again very soon.
For the understanding of common people, economists use language instead of Mathematics to make the situation understandable.
Some really nice stuff on this site, I enjoy it.
I wanted to thank you for this excellent read!! I certainly loved every bit of it. I have you book-marked to check out new things you post…
If some one needs to be updated with latest technologies therefore he must be pay a quick visit this
site and be up to date all the time.
I think everything posted was very logical. However, what about
this? suppose you were to create a awesome post title?
I mean, I don’t want to tell you how to run your blog, however suppose you added something that grabbed a person’s attention? I mean SMI diamond grinding wheels is kinda plain. You ought to glance at Yahoo’s front page and
watch how they create post titles to get viewers interested.
You might add a related video or a pic or two to grab readers excited about what you’ve got to say.
In my opinion, it would make your website a little bit more interesting.
There’s certainly a lot to find out about this issue. I really like all of the points you have made.
Hey there! I simply wish to give you a big thumbs up for the great info you have got right here on this post. I’ll be returning to your site for more soon.
I could not resist commenting. Well written.
I blog frequently and I seriously thank you for your information. This great article has truly peaked my interest. I will book mark your site and keep checking for new information about once a week. I subscribed to your Feed too.
May I simply say what a comfort to find a person that actually knows what they’re discussing on the internet. You certainly know how to bring an issue to light and make it important. A lot more people need to look at this and understand this side of your story. I was surprised you’re not more popular given that you definitely possess the gift.
Hi there! I know this is kind of off topic but I
was wondering which blog platform are you using for this site?
I’m getting fed up of WordPress because I’ve had issues with hackers and I’m looking at options
for another platform. I would be fantastic if you could point me in the
direction of a good platform.
I’m amazed, I have to admit. Seldom do I encounter a blog that’s both educative and entertaining, and let me tell you, you have hit the nail on the head. The issue is something not enough men and women are speaking intelligently about. I am very happy that I found this during my search for something relating to this.
Safety referents could also be individuals or social teams, objects, establishments, ecosystems, or another phenomenon weak to undesirable change by the forces of its environment.
This is what we had when we began: the very first design proposal (once more, as is) for Shooter, our ironic working title for a game we never supposed to be “just” a primary-person shooter.
So what exactly is a hedge fund, and what are the risks?
Effectively, GDP fluctuations affect supply and demand, which can lead to central banks reducing or rising curiosity rates, which in turn affects the nation’s forex worth!
He was a member of the Grange and the RCA.
I was very pleased to uncover this page. I need to to thank you for your time for this fantastic read!! I definitely savored every part of it and i also have you saved to fav to check out new information on your website.
Berries make a great addition to brunch.
Great post. I’m going through some of these issues as well..
Highly descriptive post, I loved that bit. Will there be a part
2?
They even have the potential for capital appreciation.
Lets assume that you are new trader and you comply with a particular inventory.
These new appliances will save you tons of money each month on your electricity and water bills.
Within the 1950s Cincinnati metropolis leaders began pushing for expansion of a site in Blue Ash to both compete with the Larger Cincinnati Airport and change Lunken as town’s main airport.
For further discussion, see 搂 Derivatives pricing: the Q world under Mathematical finance.
Engines were familiar — initially the 140-cid Pinto four, 200-cid six, and 302-cid V-8 — but there was a new all-coil suspension with modified MacPherson-strut front end geometry, which mounted the coil springs on lower A-arms.
One in all the first waves of style bloggers to hit the keys, Bryan Grey Yambao- more popularly generally known as Bryanboy- has turned vogue blogging into an artform.
It also applies to educational premises; small and medium places of assembly holding 300 people or less; large places of assembly (over300); theatres, cinemas, and similar places; healthcare premises; residential care premises; sleeping accommodation; private rented accommodation including a house converted into two or more flats; transport premises; animal premises and stables; and even open-air events and venues.
After looking over a number of the blog posts on your site, I really like your way of blogging. I book-marked it to my bookmark site list and will be checking back soon. Please check out my web site too and let me know your opinion.
This excellent website truly has all the info I wanted about this subject and didn’t know who to ask.
Can I simply just say what a comfort to discover somebody that actually understands what they are talking about on the web. You definitely understand how to bring a problem to light and make it important. A lot more people really need to look at this and understand this side of the story. I can’t believe you’re not more popular because you definitely possess the gift.
It’s fantastic that you are getting thoughts from this article as well as from our argument made here.
Everything is very open with a really clear description of the challenges. It was really informative. Your site is extremely helpful. Thanks for sharing.
I know this site provides quality dependent articles or reviews and additional data, is
there any other web page which offers these kinds of things in quality?
It is in reality a nice and useful piece of information. I’m happy that you shared this useful information with us.
Please stay us informed like this. Thank you for sharing.
It’s very easy to find out any topic on web
as compared to textbooks, as I found this article at
this web page.
you’re in point of fact a excellent webmaster.
The website loading velocity is amazing. It kind of feels that you’re doing
any unique trick. Furthermore, The contents are masterpiece.
you have performed a wonderful process in this topic!
Hi! I know this is kind of off topic but I was wondering if you knew where I could get a captcha plugin for my comment form?
I’m using the same blog platform as yours and I’m having problems finding
one? Thanks a lot!
Hey There. I discovered your weblog the use of msn.
That is a really neatly written article. I will make sure to bookmark it and return to read more
of your helpful information. Thanks for the post.
I will certainly return.
William J. Blenko was born in London, England in 1853.
Within the 1950s Cincinnati metropolis leaders began pushing for expansion of a site in Blue Ash to both compete with the Larger Cincinnati Airport and change Lunken as town’s main airport.
It’s fairly safe to assume that anybody who has the power to summon pure gold at will won’t be operating into any money problems.
A. J. Pearson “Trimethylamine N-Oxide” in Encyclopedia of Reagents for Natural Synthesis, John Wiley & Sons, 2001: New York.
HomeAway and VRBO are more traditional vacation rental sites, also with hundreds of thousands of listings.
RBI may increase rates of interest to curb inflation due to falling rupee prices.
Let dry. Glue it to middle front of drawer.
Another spherical of sluggish-shifting thunderstorms passed by the area on June 5, with most of latest Jersey and southeastern Pennsylvania positioned underneath a flash flood watch.
These are by and huge the alerts that it’s important to search for before you’ll be able to execute any motion.
The Lookout Mountain Incline Railway is a steep funicular railway that rises from the St.
Families all over the world are juggling children, jobs and aging parents in an effort to “take care of their own.” There can come a point, though, when the demands created by caring for an aging parent outweigh the logistical, financial or emotional resources available.
I have read so many content about the blogger lovers
however this post is really a good piece of writing, keep it up.
This wisdom watered down over several centuries, in all probability millennia, and right this moment the majority has little time to look in direction of the lofty targets of the life.
Thanks for the marvelous posting! I really
enjoyed reading it, you are a great author.
I will remember to bookmark your blog and
will come back later in life. I want to encourage
you to continue your great job, have a nice day!
This is typically based on a client’s financial position and strength and his/her objectives along with financial preferences.
Incredible! This blog looks exactly like my old one!
It’s on a entirely different topic but it has pretty much the same layout and design. Wonderful choice of colors!
Thus, with regards to the preparation of SSC Exams, it’s all the time advisable to search for a reputed SSC Teaching Institute.
This motion will not be good for a wholesome back that’s warmed up and stretched out, let alone for a cold, stiff back that simply woke up.
Awesome site you have here but I was curious about if you knew of any forums that cover the
same topics discussed here? I’d really like to be a part of online community where I can get feed-back from other experienced people
that share the same interest. If you have any recommendations, please let me know.
Thanks!
I pay a quick visit every day a few web sites and websites to read content, but this
website presents feature based content.
I was recommended this blog by my cousin. I’m not sure whether this post is written by
him as nobody else know such detailed about my trouble.
You are amazing! Thanks!
bookmarked!!, I love your website.
Discover stress-free transportation with Douala Airport Taxi Service.
Punctual pickups, courteous drivers, and luxurious vehicles for all your
travel needs.
Hello there! This article could not be written much better! Going through this article reminds me of my previous roommate! He constantly kept talking about this. I will forward this post to him. Pretty sure he’ll have a great read. Many thanks for sharing!
Hi there! I could have sworn I’ve been to this website before but after going through some of the posts I realized it’s new to me. Regardless, I’m certainly happy I stumbled upon it and I’ll be bookmarking it and checking back frequently.
I really like looking through an article that will make men and women think. Also, thank you for allowing me to comment.
The Crux of the Matter It is important to understand that when you participate in the best forex mirror trading, it indicates that you, as a trader, do not have direct control over the way in which your orders are carried out.
Your style is very unique in comparison to other folks I’ve read stuff from.
Many thanks for posting when you’ve got the opportunity, Guess I will just
book mark this page.
Pretty! This has been a really wonderful article. Thanks for supplying this information.
Appreciate the recommendation. Will try it out.
This post is invaluable. How can I find out more?
Hi, I do believe this is a great blog. I stumbledupon it 😉 I will revisit once again since I saved as a favorite it. Money and freedom is the greatest way to change, may you be rich and continue to help others.
An outstanding share! I’ve just forwarded this onto a friend who had been conducting a little research on this. And he actually bought me breakfast due to the fact that I discovered it for him… lol. So allow me to reword this…. Thank YOU for the meal!! But yeah, thanx for spending the time to talk about this topic here on your website.
When someone writes an post he/she retains the thought of a user in his/her brain that how a user can be aware of it.
So that’s why this article is perfect. Thanks!
Article writing is also a fun, if you know then you can write or else it is complicated to write.
Pretty! This was a really wonderful post. Thank you for
providing these details.
Definitely believe that which you stated. Your favorite justification seemed to be on the web
the simplest thing to be aware of. I say to you, I certainly get annoyed while people
think about worries that they plainly do not know about.
You managed to hit the nail upon the top as well as defined out the
whole thing without having side effect , people can take a signal.
Will probably be back to get more. Thanks
Now I am going to do my breakfast, later than having my breakfast coming over again to
read other news.
I do agree with all the ideas you’ve offered on your post.
They are very convincing and can definitely work. Still, the posts are too short for
beginners. May you please prolong them a bit from
next time? Thank you for the post.
Oh my goodness! Awesome article dude! Thank you so much, However I am experiencing troubles with your RSS. I don’t understand the reason why I cannot subscribe to it. Is there anyone else getting similar RSS issues? Anyone who knows the solution can you kindly respond? Thanks!!
Nice post. I learn something new and challenging on blogs I stumbleupon everyday. It’s always helpful to read articles from other authors and use a little something from their websites.
hey there and thank you for your info – I’ve certainly picked
up something new from right here. I did however expertise some technical points using this website, since I experienced
to reload the website lots of times previous to I could get
it to load properly. I had been wondering if your web host is OK?
Not that I am complaining, but slow loading instances times will often affect your placement in google and
can damage your high-quality score if ads and marketing with Adwords.
Well I’m adding this RSS to my e-mail and can look out for
a lot more of your respective fascinating content.
Make sure you update this again soon.
WOW just what I was searching for. Came here by searching for Home Inspection Services
Oh my goodness! Incredible article dude! Thank you, However I am having troubles with your RSS. I don’t understand why I am unable to subscribe to it. Is there anybody else having similar RSS problems? Anyone that knows the answer can you kindly respond? Thanx!
I’d like to thank you for the efforts you have put in writing this site. I am hoping to check out the same high-grade content by you later on as well. In fact, your creative writing abilities has inspired me to get my very own website now 😉
Spot on with this write-up, I actually believe that this amazing site needs much more attention. I’ll probably be back again to read more, thanks for the info!
If you are going for finest contents like I do,
only go to see this site every day for the reason that it provides
feature contents, thanks
I blog quite often and I genuinely appreciate your content. This article has really peaked my interest. I’m going to bookmark your site and keep checking for new details about once a week. I opted in for your RSS feed too.
Appreciating the commitment you put into your site and in depth information you
offer. It’s good to come across a blog every once in a while that
isn’t the same old rehashed information. Great read!
I’ve bookmarked your site and I’m adding your RSS feeds to my Google account.
each time i used to read smaller articles or reviews which
as well clear their motive, and that is also happening with this post which I am reading at this time.
It’s going to be end of mine day, except before ending I am reading
this great paragraph to increase my experience.
Wow, awesome blog layout! How long have you been blogging for?
you make blogging look easy. The overall look of your web site is great, as well
as the content!
I’d like to thank you for the efforts you’ve put in writing this site. I’m hoping to check out the same high-grade blog posts by you later on as well. In fact, your creative writing abilities has inspired me to get my own, personal website now 😉
Oh my goodness! Impressive article dude! Thanks, However I am encountering problems with your RSS. I don’t know why I am unable to subscribe to it. Is there anybody having similar RSS problems? Anyone that knows the solution can you kindly respond? Thanks!!
Pretty great post. I simply stumbled upon your weblog and wanted to
mention that I’ve truly enjoyed browsing your blog posts.
After all I will be subscribing to your rss feed and I hope you write once more soon!
Hi! I could have sworn I’ve visited this site before but after looking at many of the posts I realized it’s new to me. Regardless, I’m certainly happy I stumbled upon it and I’ll be book-marking it and checking back often!
This website was… how do I say it? Relevant!! Finally I have found something which helped me. Thanks.
Wonderful article! We are linking to this great article on our site. Keep up the great writing.
Have you ever considered publishing an e-book or guest authoring on other blogs?
I have a blog based on the same information you
discuss and would love to have you share some stories/information.
I know my readers would value your work. If you are even remotely
interested, feel free to shoot me an email.
Hello, i think that i saw you visited my site so i came to “return the favor”.I’m attempting to find things to enhance my website!I suppose
its ok to use some of your ideas!!
You are so interesting! I don’t suppose I’ve truly read a single thing like this before. So nice to discover someone with some unique thoughts on this issue. Seriously.. many thanks for starting this up. This site is something that is required on the internet, someone with a little originality.
Well-written and insightful! Your points are spot on, and I found the information very useful. Keep up the great work!
A partnership may help you are feeling safer about your investment, or it’d allow you to buy extra property than you could alone.
When economic occasions are uncertain, individuals want to place their money in something solid.
As we speak, many massive industrial AM machines are still pricey, though much less so than before.
Though the recommendation of cash managers can differ from stockbroker to broker, many can have the similar basic stock buying and selling tips for their purchasers.
One other space of concern relating to stable waste discount is the possible improve in pollution created by recycling.
We didn’t make the most of our spell in the primary half they usually actually bought to grips with the game within the second half and gained each second ball.
A fascinating discussion is worth comment. I think that you ought to write more about this topic, it might not be a taboo matter but usually folks don’t discuss these issues. To the next! Many thanks.
Jo blames lots of the residents of their small town of Pinecone, Alabama, starting with the rifle’s manufacturers, who are the largest company in the realm.
Still, the unstated feeling that they had somehow failed to meet their obligation to seize victory or die was deeply ingrained and difficult to overcome.
There are several methods that you need to use to protect yourself.
Goronwy Tobit Huws, Assistant Regional Controller, Central Office for Wales, Ministry of Social Safety.
The knot we should be using is one called the reef knot — a binding knot used in sailing, in surgery, and in efficient shoelace tying.
McNulty, Phil (27 December 2010).
In some instances, those muscle pains might point out a more serious facet effect: A small share of patients had muscle problems so critical that developed rhabdomyolysis.
You may begin out by walking for 20 minutes a day, three days a week, and regularly add to both the length and frequency of your walks so that, after the first three or four months, you are strolling for forty five minutes a day, five days every week.
These theories usually express ideas which are just too abstract or staggering to be accepted by the larger scientific community on the time, but, through the years, as more discoveries are made and certain items fall into place, generally even the wildest theories have been proven to be right all alongside.
This means you should be searching for brands that value clarity and openness in regards to the creation of their products and where they source their ingredients.
The agency can be trying to find persons who’ve an understanding of that accomplishment takes sustained actually onerous do the job, and who can deal with and relieve strain.
Competing drug cartels with armed paramilitary groups launched assaults on federal and judicial buildings there.
When this transfer was made, a quantity of people went over to the desk to begin watching the sport.
Nepomniachtchi worked with second Nikita Vitiugov, along with Maxim Matlakov and Ildar Khairullin, whereas also consulting with former world champion Vladimir Kramnik.
In a phytosanitary context, the term plant pest, or simply pest, refers to any species, strain or biotype of plant, animal or pathogenic agent injurious to plants or plant products and includes plant pathogenic bacteria, fungi, fungus-like organisms, viruses and virus like organisms, as well as insects, mites, nematodes and weeds.
It was a shock for a state that in 2014 made community faculty free, leading to a surge in the college-going rate.
A significant point that needs to be considered is that the future performance of the stock market does not depend on its previous performance.
Kolkata had a breakthrough season as they went on to qualify for the knockout levels of the season.
You can decide which of the two types of money management do you want to go for depending on your situation.
Many free pages, previous paperwork, and vintage images are scattered all through the journal, each supplying you with a glimpse-horrible as they could also be-into the destiny of the Holkar Expedition.
K and Davichi. And the instruments for connecting keep getting higher, including the current improvements in social media.
The fourth Rutte cabinet has eight ministers without portfolio: Carola Schouten (Poverty, Participation and Pensions), Liesje Schreinemacher (Development Cooperation), Rob Jetten (Climate and Energy), Conny Helder (Long-Term healthcare and Sport), Christianne van der Wal (Nature and Nitrogen reduction), Franc Weerwind (Legal Protection), Hugo de Jonge (Housing and Urban Development), and Dennis Wiersma (Primary and Secondary Education and Media).
There isn’t a right or incorrect answer, and selecting one over the other does not make you a better or worse mother.
Mars could be smaller than Earth, however some scientists consider the Pink Planet to be one among our best choices for future colonization.
Up front there was anything however harmony, with a criss-cross grille puckered between intruding headlamp eyebrows, bending around from entrance fender creaselines.
The intrinsic nature of that downside, however, shouldn’t be all the time stated unambiguously.
Hey there! I understand this is somewhat off-topic however I
needed to ask. Does operating a well-established website like yours take a massive
amount work? I’m completely new to blogging but I do write in my diary on a daily basis.
I’d like to start a blog so I will be able to share my
experience and views online. Please let me know if you have any kind of suggestions or tips for new
aspiring blog owners. Thankyou!
They’ve of their assortment a rich selection of necklaces, bangles and bracelets, rings and earrings.
These banks typically accept deposits from the startup companies, and offer venture debt to complement their overall service offerings.
You have to be out there to work holidays equivalent to Thanksgiving, as those might be very busy days.
SFWA Nebula Awards (2023).
Hello, I enjoy reading all of your post. I like to write
a little comment to support you.
The risk of inflation and the proliferation of investment instruments on this asset class are a few of the elements that have enabled the recognition of commodities to develop.
Since its inception, the National Center for Research and Development has spent almost PLN 250M on venture development, which is less than a tenth of the funds planned by the Center to stimulate the development of the VC market.
It’s a big consider the general health of your pool.
While there are many ways you can have travel money exchange, one of the best ways is to take advantage of online foreign exchange service providers.
The game of the Century featured a windmill involving a knight and a bishop.
Very best for these in search of inner energy and steerage.
I was curious if you ever thought of changing the structure of your blog?
Its very well written; I love what youve got to say.
But maybe you could a little more in the way of content so people could connect with it better.
Youve got an awful lot of text for only having 1 or two images.
Maybe you could space it out better?
obviously like your web-site but you need to take a look at the spelling on quite
a few of your posts. Several of them are rife
with spelling problems and I to find it very bothersome to tell the truth nevertheless I will definitely come again again.
Hi, I do think this is a great site. I stumbledupon it 😉 I’m going to
come back once again since I bookmarked it. Money and freedom is the
best way to change, may you be rich and continue
to help other people.
I every time spent my half an hour to read this web site’s posts daily along
with a mug of coffee.
Right here is the perfect blog for anyone who would like to find out about this topic. You realize a whole lot its almost tough to argue with you (not that I actually will need to…HaHa). You certainly put a brand new spin on a subject which has been written about for decades. Great stuff, just excellent.
There is certainly a lot to know about this issue. I like all the points you’ve made.
Very good post. I will be experiencing a few of these issues as well..
An outstanding share! I’ve just forwarded this onto a coworker who had been conducting a little research on this. And he actually ordered me dinner simply because I stumbled upon it for him… lol. So allow me to reword this…. Thanks for the meal!! But yeah, thanks for spending some time to discuss this matter here on your site.
If “yes” is the answer to any of these questions, then the ISM ADI programme is the only choice you’ll need.
Keep up with industry updates and our thoughts on topics impacting instructors, associations and businesses.
Keep on working, great job!
I am sure this post has touched all the internet people, its really really fastidious piece
of writing on building up new web site.
Hi, Neat post. There’s a problem together with your site in web explorer, may check this?K IE nonetheless is the market chief and a huge part of other people will leave out your wonderful writing due to this problem.
That is a good tip especially to those new to the blogosphere. Brief but very accurate information… Many thanks for sharing this one. A must read post.
Hey would you mind stating which blog platform you’re working with?
I’m planning to start my own blog soon but I’m having a
tough time selecting between BlogEngine/Wordpress/B2evolution and Drupal.
The reason I ask is because your design seems different then most blogs and I’m looking for something unique.
P.S Apologies for being off-topic but I had to ask!
I am extremely impressed with your writing skills and also
with the layout on your blog. Is this a paid theme or did you customize it yourself?
Either way keep up the nice quality writing, it’s
rare to see a nice blog like this one today.
Thanks for the good writeup. It in truth was a enjoyment account it.
Glance advanced to more brought agreeable from you!
However, how could we keep up a correspondence?
Thanks for ones marvelous posting! I definitely enjoyed
reading it, you might be a great author.I will make
certain to bookmark your blog and will often come
back down the road. I want to encourage you to ultimately continue
your great work, have a nice weekend!
I know this if off topic but I’m looking into starting my own weblog and was curious what
all is required to get set up? I’m assuming having a blog like yours would cost
a pretty penny? I’m not very internet savvy so I’m not 100% sure.
Any recommendations or advice would be greatly appreciated.
Cheers
Can I just say what a relief to uncover an individual who really knows what they’re discussing on the internet. You definitely realize how to bring a problem to light and make it important. More people should read this and understand this side of the story. I was surprised you aren’t more popular given that you most certainly possess the gift.
Hey very interesting blog!
Your style is really unique in comparison to other folks I’ve read stuff from. I appreciate you for posting when you have the opportunity, Guess I will just bookmark this web site.
I got this web page from my buddy who shared with me about this web site and now this time I am visiting this web page and
reading very informative articles or reviews at this time.
It’s nearly impossible to find knowledgeable people on this subject, but you seem like you know what you’re talking about! Thanks
Your style is unique in comparison to other folks I
have read stuff from. Thank you for posting when you have the opportunity, Guess I’ll just book
mark this web site.
When I originally commented I appear to have clicked the -Notify me when new comments are added- checkbox and from now on whenever a comment is added I receive 4 emails with the exact same comment. There has to be a way you can remove me from that service? Kudos.
If you are going for finest contents like myself, just pay a
quick visit this website every day as it offers quality contents, thanks
I couldn’t refrain from commenting. Well written!
Hey very interesting blog!
Outstanding quest there. What happened after? Thanks!
You are so awesome! I don’t suppose I’ve truly read through a single thing like that before. So great to discover another person with unique thoughts on this issue. Really.. thanks for starting this up. This website is something that is needed on the web, someone with some originality.
Hi there! This blog post could not be written much better! Looking at this post reminds me of my previous roommate! He constantly kept preaching about this. I am going to forward this post to him. Fairly certain he’ll have a good read. Thank you for sharing!
Hi i am kavin, its my first occasion to commenting anyplace, when i read this piece
of writing i thought i could also make comment due to this sensible piece of writing.
Hello, I would like to subscribe for this weblog to take most up-to-date updates, therefore where can i do it please help.
I’m amazed, I have to admit. Seldom do I encounter a blog that’s equally educative and amusing, and without a doubt, you’ve hit the nail on the head. The problem is an issue that too few people are speaking intelligently about. I’m very happy that I came across this in my search for something regarding this.
Hello, I do believe your web site might be having browser compatibility problems. Whenever I look at your website in Safari, it looks fine however, if opening in I.E., it has some overlapping issues. I just wanted to provide you with a quick heads up! Aside from that, excellent site!
It’s difficult to find knowledgeable people about this topic, but you sound like you know what you’re talking about! Thanks
I need to to thank you for this great read!! I absolutely loved every bit of it. I have you book marked to check out new things you post…
I constantly spent my half an hour to read this website’s posts everyday along with a mug of coffee.
Hey there, I think your website might be having browser compatibility issues.
When I look at your blog site in Safari,
it looks fine but when opening in Internet Explorer, it
has some overlapping. I just wanted to give you a quick heads up!
Other then that, very good blog!
Great article! I learned a lot from your detailed explanation. Looking forward to more informative content like this!
I love it when folks come together and share thoughts. Great site, keep it up!
Hey there! Do you know if they make any plugins to assist with SEO?
I’m trying to get my blog to rank for some targeted keywords but I’m not seeing very good success.
If you know of any please share. Thank you!
Watch our most viewed super sexy bf video on socksnews.in. sexy bf video Watch now.
Appreciating the persistence you put into your site
and detailed information you present. It’s good to come across a blog every once in a while
that isn’t the same unwanted rehashed information. Fantastic read!
I’ve saved your site and I’m adding your RSS feeds to my Google account.
Everything is very open with a very clear description of the issues. It was really informative. Your site is very helpful. Thank you for sharing.
Hello just wanted to give you a quick heads up. The text in your post seem
to be running off the screen in Internet explorer.
I’m not sure if this is a format issue or something to do with browser compatibility but
I thought I’d post to let you know. The layout look great though!
Hope you get the issue resolved soon. Cheers
That is very fascinating, You’re an overly professional blogger.
I have joined your feed and sit up for in search of more of your magnificent post.
Additionally, I’ve shared your web site in my social networks
Link exchange is nothing else however it is just placing the other person’s
weblog link on your page at proper place and
other person will also do similar in favor of you.
Pretty section of content. I just stumbled upon your site and in accession capital
to assert that I acquire actually enjoyed account your blog posts.
Any way I will be subscribing to your augment and even I achievement
you access consistently quickly.
The Irani Feroza works under the governing planet Jupiter and holds astrological benefits of abundance, huge success, robust safety, and many blissfulness.
Hi my loved one! I want to say that this post is awesome, nice written and include almost
all significant infos. I’d like to peer extra posts like this .
Good post. I learn something totally new and challenging on sites I stumbleupon every
day. It will always be useful to read articles from other
authors and practice a little something from their web sites.
I am actually grateful to the holder of this website
who has shared this fantastic piece of writing at at this time.
Hello There. I discovered your blog the use of msn. This is an extremely smartly written article.
I’ll make sure to bookmark it and return to read extra of your useful info.
Thank you for the post. I will definitely return.
It’s perfect time to make a few plans for the long run and it is
time to be happy. I’ve read this post and if I
may just I wish to counsel you some interesting things or tips.
Perhaps you could write subsequent articles relating to this article.
I wish to read even more issues approximately it!
You should take part in a contest for one of the highest quality sites on the net. I’m going to highly recommend this blog!
I appreciate the depth of research in this article. It’s both informative and engaging. Keep up the great work!
Paragraph writing is also a excitement, if you be familiar with
afterward you can write or else it is difficult to write.
Great article! I learned a lot from your detailed explanation. Looking forward to more informative content like this!
Wonderful work! This is the kind of info that should be shared around the net.
Disgrace on Google for now not positioning this submit upper!
Come on over and discuss with my website . Thank you =)
I was pretty pleased to uncover this website. I want to to thank you for your time due to this
wonderful read!! I definitely loved every bit of it and i also have you
saved to fav to check out new information in your website.
you’re really a excellent webmaster. The web site loading velocity is amazing.
It seems that you’re doing any distinctive trick.
Also, The contents are masterwork. you’ve performed a magnificent activity in this subject!
Wow, this paragraph is good, my sister is analyzing these things,
thus I am going to tell her.
Wonderful post! We are linking to this particularly great content on our website. Keep up the great writing.
Thanks for sharing. Like your post.Name
Howdy! This article could not be written any better! Looking at this article reminds me of my previous roommate! He always kept talking about this. I am going to forward this information to him. Pretty sure he will have a good read. Many thanks for sharing!
Way cool! Some extremely valid points! I appreciate you penning this write-up and the rest of the website is also very good.
Just wish to say your article is as astonishing.
The clarity for your put up is just great and i can assume you are
an expert on this subject. Fine along with your permission allow me to grab your feed to stay updated with coming near near post.
Thank you one million and please carry on the gratifying work.
I’m not that much of a internet reader to be honest but your sites really nice, keep it up!
I’ll go ahead and bookmark your website to come back in the future.
Many thanks
Howdy! This article could not be written any better! Reading through this post reminds me of my previous roommate! He continually kept talking about this. I am going to send this article to him. Fairly certain he’ll have a very good read. Many thanks for sharing!
Pretty! This has been an incredibly wonderful article. Many thanks for supplying these details.
Pretty! This was a really wonderful post. Thank you for supplying this info.
Having read this I thought it was extremely enlightening. I appreciate you taking the time and energy to put this information together. I once again find myself personally spending a significant amount of time both reading and commenting. But so what, it was still worthwhile.
This post is very helpful! I appreciate the effort you put into making it clear and easy to understand. Thanks for sharing!
Great article! We are linking to this particularly great article on our site. Keep up the great writing.
An impressive share! I’ve just forwarded this onto a coworker who had been conducting a little research on this.
And he in fact ordered me lunch simply because I stumbled upon it
for him… lol. So let me reword this…. Thank YOU for the meal!!
But yeah, thanx for spending time to talk about this topic here on your website.
This site was… how do I say it? Relevant!! Finally I have found something which helped me. Thank you!
He may even have used sharp criticism to encourage workers to work more durable, realizing that he was feeding on their own insecurities.
Conversely, a decline in bond prices and rise in interest rates decreases the deflationary threat, which is positive for stocks.
This island is understood for giving the world artists like Bob Marley.
Could 2014 and June 2019 respectively.
Computer support specialists provide phone and e-mail support for clients, run diagnostics on misbehaving machines and perform repairs on company computer systems.
Put them on a tray to dry.
This excellent website truly has all of the information I needed concerning this subject and didn’t know who to ask.
Aw, this was a very good post. Spending some time and actual effort to produce a very good article… but what can I say… I hesitate a whole lot and don’t seem to get nearly anything done.
Appreciate the recommendation. Will try
it out.
For most individuals, a $10,000 tax credit might considerably scale back their general tax bill and make shopping for a hybrid or electric car far more reasonably priced.
Then there’s the 5 easy inflation safety and with such a rider your coverage’s whole profit quantity will enhance yearly at a fixed percentage of your initial day by day benefit quantity.
Thanks for sharing your info. I truly appreciate your efforts and I will be waiting for your further post thanks once
again.
This site was… how do you say it? Relevant!! Finally I have found something which helped me. Thanks a lot!
And all the time do not forget that anything you share has the potential to be leaked ultimately.
Great article.
If you want to increase your knowledge simply keep visiting this website
and be updated with the latest gossip posted here.
Each astrological signal possesses a singular symbol to symbolize them.
I think this is among the most significant information for me.
And i am glad reading your article. But should remark on few general things, The website style is ideal, the articles is really great
: D. Good job, cheers
Hook the nook of the underside ends of the fascia cowl.
This is a topic that is near to my heart… Best wishes! Exactly where can I find the contact details for questions?
A careful pan-and-scan operator will attempt to signify the different necessary features of a shot by “cutting” between the two halves of the screen, in order that what was initially one shot becomes multiple pictures.
Howdy! Someone in my Facebook group shared this website with us so I came to take a look.
I’m definitely loving the information. I’m book-marking and will be
tweeting this to my followers! Excellent blog and wonderful design.
Pretty! This has been an incredibly wonderful article. Many thanks for providing this info.
Hi there would you mind sharing which blog platform you’re working with?
I’m going to start my own blog soon but I’m having a difficult time selecting
between BlogEngine/Wordpress/B2evolution and Drupal.
The reason I ask is because your design and style seems different then most
blogs and I’m looking for something unique.
P.S Sorry for getting off-topic but I had to ask!
I’m curious to find out what blog system you happen to be utilizing?
I’m experiencing some small security issues with
my latest site and I’d like to find something more
safe. Do you have any suggestions?
An impressive share! I’ve just forwarded this onto a coworker who has been conducting a little research on this. And he actually bought me dinner simply because I discovered it for him… lol. So let me reword this…. Thanks for the meal!! But yeah, thanx for spending some time to discuss this matter here on your blog.
Amazing issues here. I am very glad to peer your article.
Thanks so much and I’m looking forward to
touch you. Will you kindly drop me a mail?
https://armchairjournal.com/forums/users/campingequipmentk/
Saved as a favorite, I love your web site!
Wonderful beat ! I would like to apprentice while you amend
your site, how can i subscribe for a blog site? The account aided me a acceptable deal.
I had been tiny bit acquainted of this your broadcast offered bright clear concept
Everything is very open with a clear clarification of the challenges. It was definitely informative. Your website is extremely helpful. Thanks for sharing!
There is definately a lot to learn about this topic. I like all the points you’ve made.
Whats up very cool web site!! Guy .. Excellent ..
Superb .. I’ll bookmark your site and take the feeds additionally?
I’m satisfied to find numerous useful info here within the publish, we want develop more
strategies in this regard, thanks for sharing.
. . . . .
I have been exploring for a bit for any high quality articles or blog posts on this sort of area .
Exploring in Yahoo I eventually stumbled upon this site.
Studying this information So i’m happy to convey that I have an incredibly
good uncanny feeling I came upon exactly what I needed.
I such a lot indisputably will make certain to don?t fail to remember this website and give it a
look on a relentless basis.
Hello there! This blog post could not be written any better! Reading through this article reminds me of my previous roommate! He always kept preaching about this. I’ll forward this article to him. Fairly certain he’ll have a good read. Thanks for sharing!
Simply desire to say your article is as surprising. The clarity in your post is just cool and i can assume you’re an expert on this subject.
Fine with your permission let me to grab your RSS feed to keep up to
date with forthcoming post. Thanks a million and please carry on the gratifying work.
Hi, this weekend is good in favor of me, because this time i am
reading this great informative post here at my house.
Great post!
Thanks for your marvelous posting! I actually enjoyed reading
it, you may be a great author. I will be sure to bookmark your blog and will come back at some
point. I want to encourage you continue your great writing, have
a nice evening!
Aw, this was a very nice post. Taking the time and actual effort to create a very good article… but what can I say… I put things off a lot and don’t manage to get nearly anything done.
An interesting discussion is definitely worth comment. I do think that you should publish more on this subject matter, it may not be a taboo subject but usually folks don’t speak about such subjects. To the next! Kind regards.
This site was… how do I say it? Relevant!! Finally I’ve found something that helped me. Thanks.
Having read this I thought it was very informative. I appreciate you taking the time and energy to put this content together. I once again find myself spending way too much time both reading and posting comments. But so what, it was still worth it.
It’s difficult to find knowledgeable people for
this subject, but you seem like you know what you’re talking about!
Thanks
I’m very pleased to discover this site. I want to to thank you for ones time just for this fantastic read!! I definitely liked every little bit of it and i also have you saved to fav to see new things on your blog.
Wow, awesome blog layout! How long have you been blogging for?
you made blogging look easy. The overall look of your web
site is excellent, let alone the content!
I like the valuable information you provide in your articles.
I will bookmark your blog and check again here regularly.
I am quite sure I will learn plenty of new stuff right
here! Good luck for the next!
Someone essentially assist to make seriously posts I’d state.
That is the first time I frequented your web
page and thus far? I amazed with the analysis you made to make this actual submit incredible.
Magnificent process!
Because the admin of this website is working, no doubt very quickly it will be famous, due to its quality contents.
I like what you guys are usually up too. Such clever work
and reporting! Keep up the fantastic works guys I’ve incorporated you guys to my blogroll.
Great article! I learned a lot from your detailed explanation. Looking forward to more informative content like this!
Great article! I learned a lot from your detailed explanation. Looking forward to more informative content like this!
I want to to thank you for this wonderful read!! I definitely loved every bit of it. I have you saved as a favorite to check out new stuff you post…
continuously i used to read smaller articles or reviews which also
clear their motive, and that is also happening with this paragraph which I am reading at this time.
Aw, this was a really nice post. Taking the time and actual effort to make a great article… but what can I say… I hesitate a whole lot and don’t seem to get nearly anything done.
There is certainly a great deal to find out about this topic. I love all the points you made.
Oh my goodness! Amazing article dude! Thanks, However
I am encountering problems with your RSS. I don’t understand why I cannot join it.
Is there anyoe else having identical RSS issues?
Anyone that nows the answer can you kindly respond? Thanx!! https://www.waste-ndc.pro/community/profile/tressa79906983/
I’d like to thank you for the efforts you have put in penning this blog. I really hope to check out the same high-grade content from you in the future as well. In fact, your creative writing abilities has inspired me to get my own blog now 😉
Having read this I believed it was extremely informative. I appreciate you spending some time and effort to put this information together. I once again find myself personally spending a lot of time both reading and posting comments. But so what, it was still worthwhile!
What you published was actually very reasonable. However,
think on this, what if you added a little content? I am not saying your content is
not good., but suppose you added a title to maybe grab people’s attention? I mean SMI diamond grinding wheels is a
little plain. You might peek at Yahoo’s front page and see how they create article headlines to get people to open the links.
You might add a related video or a related picture or two to get readers interested about what you’ve got to
say. In my opinion, it could bring your website a little livelier.
I’m very pleased to discover this website. I wanted to thank you for your time for this particularly wonderful read!! I definitely savored every bit of it and i also have you book-marked to look at new things in your web site.
Pretty! This has been an extremely wonderful post. Thanks for supplying this information.
My brother recommended I might like this website.
He used to be totally right. This put up actually made my day.
You can not consider just how much time I had spent for this
info! Thanks!
This design is incredible! You definitely know how to keep a
reader amused. Between your wit and your videos, I was almost moved to start
my own blog (well, almost…HaHa!) Wonderful job. I really loved what you had to say, and more than that,
how you presented it. Too cool!
Heya i’m for the first time here. I came across this board and I
find It truly useful & it helped me out a lot. I’m hoping to offer one thing back and
aid others like you helped me.
Right now it appears like Drupal is the best blogging platform out there right now.
(from what I’ve read) Is that what you’re using on your blog?
Thank you for every other great post. Where else
could anyone get that kind of information in such an ideal
method of writing? I have a presentation next week,
and I am at the look for such information.
Awesome things here. I’m very satisfied to see your article.
Thanks a lot and I’m taking a look ahead to contact you.
Will you please drop me a e-mail?
I enjoy looking through an article that can make men and women think.
Also, thank you for allowing for me to comment!
Appreciate the recommendation. Let me try it out.
This is a topic which is near to my heart… Take care! Where can I find the contact details for questions?
Hey! This post couldn’t be written any better!
Reading this post reminds me of my old room mate!
He always kept chatting about this. I will forward this
write-up to him. Fairly certain he will have a good read.
Thank you for sharing!
It’s very straightforward to find out any matter on net as compared to books, as
I found this post at this website.
Good post. I learn something totally new and challenging on sites I stumbleupon everyday. It’s always helpful to read content from other authors and use something from their web sites.
Excellent article. I will be going through a few of these issues as well..
This is a topic that is close to my heart… Take care! Where can I find the contact details for questions?
Hello, after reading this awesome article i am as well glad to share my familiarity here with mates.
It’s very easy to find out any matter on net as compared to books,
as I found this paragraph at this web site.
sex nhật hiếp dâm trẻ em ấu dâm buôn bán vũ khí ma túy bán súng sextoy chơi đĩ sex bạo lực sex học đường tội phạm tình dục chơi les đĩ đực người mẫu bán dâm
I always spent my half an hour to read this weblog’s articles
or reviews all the time along with a mug of coffee.
Hi, its pleasant post about media print, we all be
aware of media is a fantastic source of facts.
If the blisters have healed, however the pain persists, what choices do you could have?
At present providing a range of companies to Christians together with camps, conferences, centers and Bible institutes, the corporate started in 1946 with the purchase of an island to be used as a Christian camp.
On the upper cabinets, glass-mullioned doorways are curtained in pure white sheers for an airy, vintage look that keeps personal items out of sight.
China’s comments. The world’s largest holder of U.S.
Reese’s Crispy Crunchy Bar is a sweet bar produced by the Reese’s division of The Hershey Company.
Life can be fairly boring with out leisure.
You’ll usually need to make a new claim.
You must endeavor to know how a share inventory can be analyzed prior to purchasing share or direct equity.
As one buys fashionable bangles from the web store, one would really feel how fairly the bangles look on the wrists.
Additionally it is important that actual estate portfolio managers not solely embody the requisite capital allocation, property choice and other investment abilities required, but also that they’ve the ability to create acceptable funding strategies and the management expertise to mobilize the group toward the identical portfolio mission.
27. A fashionable matching set that screams “farmers market chic,” and that i do not know why because I haven’t been to a farmers market in, like, three years.
In 1818 the Rothschild financial institution organized a £5 million loan to the Prussian authorities and the issuing of bonds for government loans.
The implication of this is that you will need to raise twice as much money in your last year of retirement to be able to life the lifestyle that you are used to.
They typically invest in commodity market to make the balance between revenue and loss.
These value-added providers are included in our home inspections at no additional value – saving you time and money while eliminating the necessity to bring in these specialists.
It was a 50/50 mixture of Bronco and pickup with a number of plastic parts and all-out race-car engineering.
If they are not hard work, you have to work more durable!
The current computing power permits managers to investigate risks reminiscent of catastrophes that influence enterprise and financial dangers such as interest movements.
Oh my goodness! Amazing article dude! Thank you so much, However I am encountering problems with your RSS. I don’t know why I am unable to subscribe to it. Is there anybody getting similar RSS issues? Anyone that knows the answer can you kindly respond? Thanx!!
I like it when folks get together and share ideas. Great blog, keep it up.
This is a topic that’s near to my heart… Thank you!
Exactly where are your contact details though?
What’s Going down i am new to this, I stumbled upon this I’ve discovered
It positively useful and it has helped me out loads.
I’m hoping to give a contribution & aid different customers like its aided me.
Good job.
I could not refrain from commenting. Perfectly written.
An interesting discussion is worth comment. I do believe that you should write more about this topic, it may not be a taboo matter but typically folks don’t discuss these subjects. To the next! All the best.
Heya i’m for the first time here. I found this board and I find It
really useful & it helped me out much. I hope to give something back and aid others like you helped me.
I really like it whenever people come together and share ideas. Great website, stick with it!
It’s genuinely very difficult in this full of activity life to
listen news on Television, thus I only use the web for that
purpose, and take the most up-to-date information.
I was able to find good information from your content.
Hi there, You’ve done an incredible job. I’ll certainly digg
it and personally suggest to my friends.
I am confident they’ll be benefited from this web
site.
Hi! I just wanted to ask if you ever have any issues with hackers?
My last blog (wordpress) was hacked and I ended up losing many months of hard work due to no data
backup. Do you have any solutions to protect against hackers?
I’m extremely inspired with your writing talents and also with
the format on your blog. Is that this a paid subject matter or did you modify it yourself?
Either way stay up the nice high quality writing, it’s rare to look a
nice blog like this one these days..
I am really enjoying the theme/design of your blog. Do you ever run into any browser compatibility issues?
A couple of my blog readers have complained
about my blog not working correctly in Explorer but looks great in Chrome.
Do you have any solutions to help fix this problem?
Do you have a spam issue on this website; I
also am a blogger, and I was wondering your situation; we have created some nice practices
and we are looking to exchange solutions with other folks, be sure to shoot me an email if interested.
Hello there! Do you know if they make any plugins to safeguard against hackers?
I’m kinda paranoid about losing everything I’ve worked hard on.
Any tips?
You should be a part of a contest for one of the greatest websites on the net.
I’m going to highly recommend this website!
It’s hard to come by educated people in this particular topic, however, you seem like you know what you’re talking about! Thanks
Incredible points. Sound arguments. Keep up the great work.
Hello there! This post could not be written any better! Looking through this post reminds me of my previous roommate! He constantly kept preaching about this. I will forward this information to him. Pretty sure he’ll have a great read. Many thanks for sharing!
Hi, I do believe this is an excellent website. I stumbledupon it 😉 I am going to return once again since i have saved as a favorite it. Money and freedom is the best way to change, may you be rich and continue to guide others.
Having read this I believed it was very informative. I appreciate you spending some time and effort to put this informative article together. I once again find myself spending a lot of time both reading and posting comments. But so what, it was still worthwhile!
It’s difficult to find educated people about this topic, however, you seem like you know what you’re talking about! Thanks
The next time I read a blog, I hope that it won’t fail me as much as this one. I mean, I know it was my choice to read through, however I truly thought you would have something helpful to talk about. All I hear is a bunch of complaining about something that you could fix if you were not too busy seeking attention.
These are really enormous ideas in on the topic of blogging.
You have touched some fastidious things here. Any way keep up wrinting.
Your mode of telling all in this article is genuinely fastidious,
every one be capable of simply understand it, Thanks a lot.
Right here is the perfect blog for anyone who really wants to understand this topic. You realize so much its almost tough to argue with you (not that I actually would want to…HaHa). You definitely put a brand new spin on a topic that has been written about for decades. Great stuff, just wonderful.
Please let me know if you’re looking for a writer for your weblog.
You have some really good posts and I believe I would be
a good asset. If you ever want to take some of the load off, I’d
absolutely love to write some articles for your blog in exchange for a link back to mine.
Please blast me an email if interested. Regards!
Your style is very unique compared to other folks I have read stuff from. Many thanks for posting when you have the opportunity, Guess I will just book mark this blog.
I’m amazed, I have to admit. Rarely do I come across a blog that’s both educative and amusing, and without a doubt, you’ve hit the nail on the head. The issue is something which not enough people are speaking intelligently about. I am very happy that I came across this in my hunt for something relating to this.
Symptoms like difficulty breathing, blurred vision, and runny nostril are frequent and might be particularly distressing.
When you put the car in drive and start moving at say 1 mph, the automotive uses solely a tiny bit more gasoline, as a result of the highway load may be very small at 1 mph.
When individuals feel capable and in command of their recycling actions, they usually tend to actively engage in waste discount efforts.
It is usually those who are best prepared who seem to deal with adversity without sweat or stress.
The dominant rationale used to clarify M&A exercise is that acquiring corporations seek improved monetary efficiency or scale back risk.
Aw, this was an extremely nice post. Finding the time and actual effort to create a great article… but what can I say… I put things off a lot and don’t manage to get anything done.
NCC would not include the load of the car itself and could be calculated by subtracting the vehicle’s curb weight from the GVWR.
Then rapidly press the softened shellac into the crack and smooth it with the hot knife.
Draw pictures of each jar full of soil after you have shaken it and the dirt has settled to make picture comparisons.
As an example, there are particular sets of legal dangers which can be outlined by European Union (EU) Law.
Also new was an integral trunk for sedans.
To be able to make the profit, the worth of your asset has to go past the target value that was set by you or at the least contact that price mark.
Although there is no fixed ceiling on the age, it has been observed that a 30 years old person can invest about 70 of his money in equity, which is a risky investment, while the rest of the money can be invested in gold and debt.
In actuality, the numbers play a extra complicated role than most customers understand.
I’ve been surfing on-line greater than three hours as of late, but I by no
means discovered any attention-grabbing article
like yours. It’s lovely value enough for me. Personally, if all website owners and
bloggers made just right content material as you probably did, the internet will likely
be much more useful than ever before.
Greetings from Ohio! I’m bored to death at work so I decided to check out your site on my
iphone during lunch break. I really like the information you present here and can’t wait
to take a look when I get home. I’m shocked at how fast your blog loaded
on my mobile .. I’m not even using WIFI, just 3G
.. Anyhow, excellent site!
Nice replies in return of this difficulty with real
arguments and explaining everything on the topic of
that.
There’s certainly a great deal to learn about this subject. I love all the points you’ve made.
Saved as a favorite, I really like your web site!
Inizia nel mondo di Winnita Casinò online: il posto dove il piacere incontra la opportunità di vincere! Ogni funzionalità di questa piattaforma sicura e regolamentata è pensato per darti l’esperienza migliore a chi ama il gioco d’azzardo. Pronto? Ogni clic potrebbe essere quello decisivo! Iscriviti adesso e comincia ora verso il vincita!
https://linkpiz.com/vn/45648/tutto-winnita-casino-vantaggi-caratteristiche-principali
I really like reading through an article that can make men and women think. Also, thank you for allowing me to comment.
Hi there! This is my first visit to your blog! We are a team of volunteers and starting a new project in a community in the same niche.
Your blog provided us valuable information to work on. You have done a outstanding job!
A motivating discussion is definitely worth comment. I do think that you need to write more about this issue, it may not be a taboo matter but generally people don’t speak about such topics. To the next! All the best.
I blog frequently and I seriously appreciate your information. This article has truly peaked my interest. I’m going to take a note of your website and keep checking for new details about once a week. I opted in for your RSS feed too.
I like the valuable info you provide in your articles.
I will bookmark your blog and check again here
frequently. I’m quite certain I’ll learn plenty of new stuff right here!
Best of luck for the next!
Your blog has the same post as another author but i like your better.*’”,:
Hi, There’s no doubt that your web site may be having browser compatibility problems. When I look at your website in Safari, it looks fine however when opening in Internet Explorer, it’s got some overlapping issues. I just wanted to give you a quick heads up! Aside from that, wonderful website.
It is not my first time to pay a quick visit this website,
i am browsing this web site dailly and take
good facts from here every day.
It’s difficult to find educated people about this subject, but you seem like you know what you’re talking about!
Thanks
A motivating discussion is definitely worth comment.
I believe that you ought to write more about this issue, it might not be a taboo subject but usually people don’t speak about these issues.
To the next! Many thanks!!
I like the helpful information you provide in your articles.
I will bookmark your weblog and check again here regularly.
I’m quite certain I’ll learn lots of new stuff right here!
Best of luck for the next!
An outstanding share! I’ve just forwarded this onto a friend who has been doing a little homework on this.
And he in fact bought me lunch because I found it for him…
lol. So allow me to reword this…. Thank YOU for
the meal!! But yeah, thanks for spending some time to talk about this subject here on your web page.
Terrific post but I was wanting to know if you could write a litte more on this subject?
I’d be very grateful if you could elaborate a
little bit more. Many thanks!
Every weekend i used to go to see this website, as i want enjoyment,
as this this web site conations truly good funny stuff
too.
It is actually a great and helpful piece of information. I’m satisfied that you shared this helpful information with us.
Please stay us informed like this. Thank you for
sharing.
An interesting discussion is worth comment. I do believe
that you ought to publish more on this issue, it may not be a
taboo subject but usually folks don’t talk about these topics.
To the next! All the best!!
When I originally commented I clicked the “Notify me when new comments are added” checkbox and now each time a comment
is added I get three emails with the same comment. Is there any way you can remove me from that service?
Bless you!
Hi, just wanted to say, I loved this blog post. It was helpful.
Keep on posting!
Wonderful post! We will be linking to this particularly great post on our website.
Keep up the great writing.
I’m extremely impressed with your writing abilities as neatly as with the format for your blog.
Is that this a paid subject or did you customize it your self?
Either way keep up the excellent quality writing, it is uncommon to see a nice blog like this one these
days..
I was able to find good advice from your articles.
¡Tu oportunidad está aquí! No pierdas la chance de disfrutar de apuestas de confianza y emocionantes en 1Win.
https://1win-bonos.com.co/
Hmm is anyone else encountering problems with the images on this blog loading?
I’m trying to determine if its a problem on my end or if it’s the blog.
Any suggestions would be greatly appreciated.
Great beat ! I wish to apprentice while you amend your web site, how could i subscribe for a
blog website? The account aided me a acceptable deal. I had been a little bit acquainted of this your broadcast provided bright
clear concept
What’s up to all, how is all, I think every one
is getting more from this web page, and your views are good in favor of new viewers.
This is my first time visit at here and i am in fact impressed to read everthing at single
place.
Hi, I do believe this is an excellent website. I stumbledupon it 😉 I may return yet again since i have bookmarked
it. Money and freedom is the best way to change, may you be rich
and continue to help other people.
French In Action plunges proper into colloquial Parisian French, spoken full velocity.
This is very attention-grabbing, You’re an overly skilled blogger.
I have joined your rss feed and look forward to in quest of more of
your excellent post. Additionally, I’ve shared your site in my social networks
Howdy would you mind letting me know which web host you’re working with?
I’ve loaded your blog in 3 completely different web browsers and I must say this blog loads a lot faster then most.
Can you suggest a good hosting provider at a fair price?
Kudos, I appreciate it!
With contributions by Johannes Schreiter and Sir Peter Cook.
This virtual representation of Phobos was fought by Starkiller in Star Wars: The Power Unleashed.
One of the most essential differences between futures and forwards is that futures contracts are standardized.
Distributors can be, of course, client worth to repeat a couple of time.
An impressive share! I have just forwarded this onto
a co-worker who was conducting a little research on this.
And he in fact ordered me breakfast due to the fact that I discovered
it for him… lol. So allow me to reword this….
Thanks for the meal!! But yeah, thanx for spending some time to discuss this subject here on your web site.
Tomato Paste – Thickest of all, tomato paste is a concentrated tomato product that’s often combined with a liquid, like broth or water, when used in recipes.
In 1990, MRS purchased its current headquarters at 15 Northburgh Street where it remains today.
It’s the best time to make a few plans for the long run and it is time to be happy.
I’ve read this post and if I could I want to suggest you few attention-grabbing issues or suggestions.
Perhaps you could write subsequent articles referring to
this article. I want to learn more things approximately it!
Guidance counselors and coaches will also know more about local scholarships, the kind that are either too small or too specific to show up in financial aid handbooks or online.
I’m impressed, I must say. Rarely do I encounter a blog that’s both equally educative and amusing, and without a doubt, you’ve hit the nail on the head. The issue is something which not enough men and women are speaking intelligently about. Now i’m very happy I stumbled across this in my hunt for something relating to this.
MELBET সঙ্গী হয়ে ক্রিকেট সহ ৩৫০+ স্পোর্টস ইভেন্টে বাজি ধরুন। বিশ্বস্ত প্ল্যাটফর্ম এবং সহজ নিবন্ধন প্রক্রিয়া সহ, এখনই শুরু করুন। https://melbetbgd.com/
I’d like to thank you for the efforts you have put in penning this site. I’m hoping to view the same high-grade content from you in the future as well. In truth, your creative writing abilities has encouraged me to get my very own blog now 😉
I need to to thank you for this excellent read!! I certainly enjoyed every bit of it. I have got you book-marked to look at new stuff you post…
whoah this weblog is wonderful i really like studying
your posts. Keep up the good work! You recognize, lots of persons are searching round for this info, you can aid them greatly.
Good information. Lucky me I found your blog by accident (stumbleupon). I’ve book marked it for later.
You really make it appear so easy along with your presentation but I in finding this matter to be really something which I
think I’d never understand. It kind of feels too complicated and extremely wide
for me. I am taking a look ahead to your subsequent post, I’ll try to get the hang of
it!
Have you ever considered publishing an e-book or guest authoring
on other sites? I have a blog based on the same ideas you discuss and
would love to have you share some stories/information. I know my audience would value your work.
If you are even remotely interested, feel free to send me an e mail.
Great blog here! Also your web site loads up very fast!
What web host are you using? Can I get your affiliate link to your host?
I wish my website loaded up as fast as yours lol
Please let me know if you’re looking for a article writer for your site.
You have some really great articles and I feel I would be a good asset.
If you ever want to take some of the load off, I’d love to write some
material for your blog in exchange for a link back to mine.
Please blast me an email if interested. Many thanks!
I could not refrain from commenting. Well written!
Greetings! I’ve been reading your weblog for a while now and finally got the bravery to go ahead and
give you a shout out from Dallas Tx! Just wanted to say keep up the excellent work!
This website was… how do you say it? Relevant!! Finally I’ve found something that helped me. Thanks.
Join Pin-Up Casino and enjoy Aviator! Test your luck in the most popular game among Indian players — Aviator! With its user-friendly interface and captivating bets with increasing multipliers, the game becomes even more entertaining.
https://pinup-casino-bonus.in/
Is Pin-Up for Indian Users? If you’re an Indian betting enthusiast, you may have heard about Pin-Up Casino, but is it really the best casino? With a massive sign-up bonus, a broad range of games, and the ability to deposit in INR, it seems like a great choice. But what do you think? Is Pin-Up meeting expectations in India’s online gaming scene?
I really like it when individuals come together and share thoughts. Great site, stick with it.
Hello colleagues, its impressive piece of
writing on the topic of cultureand entirely explained, keep it up all the time.
Hey there! I just wanted to ask if you ever have any trouble with hackers?
My last blog (wordpress) was hacked and I ended up losing many months
of hard work due to no backup. Do you have any solutions to stop hackers?
This is a topic that is near to my heart… Cheers! Where are your contact details though?
Hey! I could have sworn I’ve been to this website before but after checking through some of the
post I realized it’s new to me. Anyways, I’m definitely glad I
found it and I’ll be bookmarking and checking back often!
Hi, I do think this is an excellent blog. I stumbledupon it 😉 I
will come back yet again since i have book-marked it.
Money and freedom is the greatest way to change, may you be rich and continue to
guide others.
If some one desires expert view on the topic of blogging afterward i
recommend him/her to go to see this webpage,
Keep up the nice job.
Great goods from you, man. I have keep in mind your
stuff prior to and you are just extremely great.
I really like what you have bought right here, certainly like what you
are saying and the best way in which you say it. You make it enjoyable and you continue
to care for to stay it smart. I cant wait to learn much more from you.
This is really a wonderful website.
I think everything published was actually very logical. But, what about this?
suppose you were to write a awesome title? I am not
suggesting your information is not good, but what if you added a post title that makes people want
more? I mean SMI diamond grinding wheels is
kinda vanilla. You ought to glance at Yahoo’s home page and note how
they create article headlines to grab people to open the links.
You might add a video or a picture or two to get readers interested about what you’ve got to say.
In my opinion, it would bring your posts a little bit
more interesting.
Which Finger to Put on the Turquoise (Firoza) Stone In?
Rossi, Rob (2010-08-20). “Pittsburgh Power unveiled as arena soccer expansion crew”.
What’s up, its fastidious paragraph about media
print, we all understand media is a impressive source of
information.
Head out west, and you’ll find 10 main league groups in Los Angeles alone!
His was a true story of rags to riches – after which to rags and riches once more.
Hello There. I discovered your weblog the usage of msn.
This is a really neatly written article. I will make sure to bookmark it and return to learn extra of your helpful information. Thanks
for the post. I’ll definitely comeback.
It’s remarkable to pay a quick visit this
website and reading the views of all mates on the
topic of this paragraph, while I am also keen of getting knowledge.
Hi, I do think this is an excellent blog. I stumbledupon it 😉 I will revisit
once again since I book-marked it. Money and freedom is the best way
to change, may you be rich and continue to guide other people.
Amazing! This blog looks just like my old one!
It’s on a totally different topic but it has pretty much the same page layout
and design. Excellent choice of colors!
I blog frequently and I truly appreciate your content. Your article has truly peaked my interest. I’m going to book mark your website and keep checking for new details about once a week. I opted in for your RSS feed too.
Excellent post. I will be facing some of these issues as well..
each time i used to read smaller content which as well
clear their motive, and that is also happening with this piece
of writing which I am reading at this place.
Very rapidly this web page will be famous amid all blogging and site-building visitors, due to it’s pleasant articles
Hey there! Do you know if they make any plugins to assist with Search Engine Optimization? I’m trying to get my blog to
rank for some targeted keywords but I’m not seeing very good gains.
If you know of any please share. Appreciate it!
An interesting discussion is worth comment. I think that you should publish more about this subject, it may not be a taboo matter but generally folks don’t talk about such subjects. To the next! Cheers!
Hello! I simply would like to offer you a big thumbs up for your great information you have got here on this post. I’ll be returning to your blog for more soon.
However eating an excessive amount of might result in excessive toxic ranges.
But it remains an attention-grabbing dilemma, and we are going to be able to method our next licensed engine with the wisdom gleaned from utilizing Unreal for this venture.
English Interregnum, when England was ruled by a Puritan Parliament.
Occasions entail numerous activities, right from the setting up the event, executing, after which wrapping it up.
Every weekend i used to visit this website, because i wish for enjoyment, since this this web site conations
really fastidious funny stuff too.
Hi, I do believe this is a great website. I stumbledupon it 😉 I will come back once again since i have saved as a favorite it. Money and freedom is the greatest way to change, may you be rich and continue to guide others.
Its like you learn my thoughts! You seem to understand so much about this, such as
you wrote the e book in it or something. I feel that you could do with some percent to pressure the message home
a little bit, but other than that, this is fantastic blog.
An excellent read. I’ll certainly be back.
Right here is the right blog for everyone who hopes to find out about this topic. You understand so much its almost tough to argue with you (not that I really would want to…HaHa). You definitely put a brand new spin on a subject that’s been written about for ages. Great stuff, just wonderful.
This is really interesting, You’re a very skilled
blogger. I’ve joined your rss feed and look forward to seeking
more of your wonderful post. Also, I’ve shared your
web site in my social networks!
This is a topic that is near to my heart… Many thanks! Where are your contact details though?
I love it whenever people come together and share ideas.
Great website, continue the good work!
Way cool! Some extremely valid points! I appreciate you penning this article and the rest of the website is also very good.
Introducing to you the most prestigious online entertainment address today. Visit now to experience now!
Way cool! Some very valid points! I appreciate you penning this post plus the rest
of the site is very good.
Risk switch apply had been the risk has a really high affect however just isn’t simple to reduce significantly the probability by way of security controls: the insurance coverage premium needs to be compared towards the mitigation costs, eventually evaluating some blended technique to partially deal with the risk.
Nail polishing creams and special polishing boards can smooth out the surface of nails that have grooves or ridges as a result of aging or injury.
These options could be traded intraday as nicely.
Operational Danger Consortium is a consortium that collects and analyzes operational threat loss information for the insurance coverage business.
According to Thomson Reuters HCMC is the competent authority for supervising securities laws in Greece, including tender offers.
Go online to forums and group discussions and check out to search out out the background of the corporate to determine if they are trust worthy of your small business.
If you work in one or more of these income tax-free states, but live in a state that does withhold income tax, you’ll still need to pay taxes on the money you earned in the tax-free state.
An outstanding share! I have just forwarded this onto
a coworker who was conducting a little homework on this.
And he in fact ordered me lunch because I stumbled upon it for him…
lol. So let me reword this…. Thank YOU for the meal!! But yeah, thanx for spending the time to discuss this issue here on your site.
I need to to thank you for this very good read!! I certainly enjoyed every bit of it. I have you bookmarked to look at new things you post…
bookmarked!!, I really like your website!
I blog often and I genuinely thank you for your information. Your article has truly peaked my interest. I will book mark your blog and keep checking for new information about once a week. I subscribed to your RSS feed too.
Hello! This is kind of off topic but I need some advice from an established blog.
Is it difficult to set up your own blog? I’m not very techincal but I
can figure things out pretty quick. I’m thinking about making my own but I’m
not sure where to begin. Do you have any points
or suggestions? Thank you
The surprise of the tournament was the untitled Brazilian Jaime Sunye Neto, who was among the many leaders throughout the mid-stage of the tournament earlier than three consecutive losses wrecked his possibilities of qualifying.
You’ll be able to play path video games which embrace identifying the varied birds or trees.
When I originally commented I appear to have clicked the -Notify me when new comments are added- checkbox and from now on each time a comment is added I receive 4 emails with the exact same comment. There has to be a way you can remove me from that service? Thanks a lot.
Route 27 (US 27) begins at an interchange with I-24 in downtown Chattanooga, and ends in northern Hamilton County, connecting the city with the cities of Pink Bank, Soddy Daisy, Dayton, and Dunlap to the north.
Brahmaputra River rafting is a tremendous adventurous water sport the place you’ll take pleasure in the game from Tuting to Pasighat – whole distance of 180 km part in 7 days.
When I originally left a comment I seem to have clicked on the -Notify me when new comments are added- checkbox and now every time a comment is added I get 4 emails with the exact same comment. There has to be a means you are able to remove me from that service? Cheers.
Right here is the right webpage for everyone who hopes to understand this topic. You know so much its almost tough to argue with you (not that I actually would want to…HaHa). You definitely put a fresh spin on a topic which has been discussed for many years. Wonderful stuff, just wonderful.
What’s Happening i am new to this, I stumbled upon this I
have discovered It absolutely helpful and it has aided me out loads.
I am hoping to give a contribution & help other customers like its aided me.
Good job.
However a sticker chart appears to work wonders in my home.
Tea towels have always been the traditional way of creating a costume for a young baby of their Navity Play (tea towel on the top with a tie spherical it makes a very good shepherd) or for a fancy dress social gathering.
Hi there! I just would like to give you a huge thumbs up for your excellent information you’ve got right here on this post. I am coming back to your blog for more soon.
Hello, I desire to subscribe for this web site to take most up-to-date updates, so where can i do it please
assist.
Why viewers still make use of to read news papers when in this technological world the whole
thing is existing on web?
Howdy! This article couldn’t be written much better!
Going through this post reminds me of my previous roommate!
He always kept preaching about this. I most certainly will send this information to him.
Pretty sure he’s going to have a very good read.
Thanks for sharing!
You need to take part in a contest for one of the best websites online. I’m going to recommend this website!
Aw, this was an exceptionally good post. Finding the time and actual effort to produce a superb article… but what can I say… I put things off a lot and don’t seem to get nearly anything done.
Hi everybody, here every person is sharing such know-how, so it’s
pleasant to read this webpage, and I used to go to see
this blog every day.
Good day I am so thrilled I found your blog page, I really found you by
error, while I was browsing on Aol for something else, Anyhow I am here now and would just
like to say kudos for a fantastic post and a all round enjoyable blog (I also love the
theme/design), I don’t have time to look over it all at the moment but I
have book-marked it and also included your RSS feeds, so when I have time I will
be back to read a great deal more, Please do keep up the excellent job.
Hello, I want to subscribe for this blog to get most up-to-date updates, thus where can i do it please help out.
I impressed, I need to say. Really not often do I encounter a blog that each educative and entertaining, and let me tell you, you have hit the nail on the head. Your concept is outstanding; the problem is something that not sufficient persons are speaking intelligently about. I’m very comfortable that I stumbled across this in my seek for one thing referring to this.
20 April 2010 – London confirms holding an option to organise the 2012 World Chess Championship.
I know this if off topic but I’m looking into starting
my own weblog and was wondering what all is required to get set up?
I’m assuming having a blog like yours would cost a pretty penny?
I’m not very internet savvy so I’m not 100%
certain. Any suggestions or advice would be greatly appreciated.
Cheers
Survived by his dad and mom, Mr and Mrs Harris Harmes, (sic) Wilbur, WA; one brother, Larry Harmes (sic), US Army at Fort Knox; 2 sisters, Miss Cheryl Harms, Moses Lake, WA and Mrs Linda Hipner, El Paso, Texas; numerous uncles, aunts and cousins.
Just desire to say your article is as astonishing. The clarity on your submit is simply excellent and
i can suppose you’re a professional in this subject. Well together with your permission allow
me to seize your feed to keep updated with impending post.
Thank you one million and please carry on the rewarding work.
My spouse and i felt cheerful when Raymond could conclude his researching while using the ideas he made when using the web page. It’s not at all simplistic just to continually be freely giving things which usually people could have been trying to sell. We really do know we have the blog owner to thank for this. Those illustrations you have made, the easy web site menu, the friendships you can help to create – it is mostly unbelievable, and it’s really facilitating our son in addition to our family know that the matter is entertaining, and that is seriously fundamental. Thank you for everything!
produce,Hanging out in an exceedingly unpredictable moment, pass-up a little while together with the fretting hand; disappearing in an exceedingly presented region, as well stand to forget about any reputation antecedents option, and i thinking about families
Does your site have a contact page? I’m having a tough
time locating it but, I’d like to shoot you an e-mail.
I’ve got some recommendations for your blog you might be interested in hearing.
Either way, great blog and I look forward to seeing it develop over time.
I might seen the meme before, but this time, her massive smile and kindred spirit known as out to me and prompted me to go looking on-line.
After looking at a few of the blog articles on your
website, I seriously like your way of blogging.
I added it to my bookmark site list and will be checking back in the near future.
Please visit my website as well and tell me your opinion.
As food fanatics in the modern age, many people have the luxury of being spoiled for alternative.
It now, nonetheless, is an space crammed with luxurious shopping centers and malls that makes this one a must-visit!
The glory of South India Pilgrimage has been praised by Nakkirar in his poem, Thirumurugatrupadai and in other Tamil works like Purananooru, Silapathikaram and Devaram.
Dyo Resort is situated in the middle of the fruits orchid on the hill prime of Amravati property covering an ample panorama and offers an exquisite view of the Higher Himalayan peaks like Trishul, Nandadevi, and Panchchuli.
I have seen loads of useful elements on your web site about computers. However, I’ve the opinion that laptops are still not nearly powerful more than enough to be a option if you often do tasks that require loads of power, just like video modifying. But for internet surfing, word processing, and a lot other frequent computer functions they are all right, provided you do not mind the tiny screen size. Many thanks for sharing your thinking.
What’s crucial factor you need to be in the Marines?
Have you ever ever observed the intricate, interlacing patterns adorning ancient manuscripts, stonework or modern jewellery and puzzled about their origin?
Thanks for your entire labor on this web page. Kate really loves managing investigation and it’s really easy to see why. We hear all regarding the lively tactic you deliver informative ideas through the blog and therefore improve response from website visitors on the concern and our simple princess is really starting to learn a great deal. Take advantage of the rest of the new year. You have been conducting a fantastic job.
Marie clapped her arms in delight because the acrobats performed one amazing feat after another.
I’m very pleased to discover this page. I wanted to thank you for your time for this particularly wonderful read!! I definitely savored every part of it and I have you saved to fav to look at new stuff in your web site.
I am really enjoying the theme/design of your weblog.
Do you ever run into any web browser compatibility problems?
A small number of my blog audience have complained about
my blog not operating correctly in Explorer but looks great in Chrome.
Do you have any tips to help fix this issue?
I’m amazed, I must say. Seldom do I encounter a blog that’s equally educative and amusing, and without a doubt, you have hit the nail on the head. The issue is an issue that not enough folks are speaking intelligently about. I am very happy I stumbled across this during my search for something concerning this.
Good day, Can I export your page photo and use that on my personal web site?
An outstanding share! I’ve just forwarded this onto a coworker who has been conducting a little research on this. And he in fact ordered me lunch simply because I found it for him… lol. So allow me to reword this…. Thanks for the meal!! But yeah, thanks for spending some time to talk about this subject here on your web site.
You made some respectable factors there. I regarded on the web for the difficulty and found most people will associate with with your website.
It’s awesome to visit this web page and reading the views of all mates about this article, while I am also zealous of getting knowledge.
I don’t even know how I ended up here, but I thought this post
was good. I do not know who you are but certainly you are going to a famous blogger if you aren’t already 😉 Cheers!
The wick must be naturally absorbent, like a towel, or it needs to have a powerful capillary motion (as in glass fiber wicks used in oil lamps).
Leh Palace, Shanthi Stupa, Hall of Fame, Shey Palace and Pangong Lake are few of the attractive places to be visited in Leh.
This is a topic which is close to my heart… Cheers! Where are your contact details though?
Hello there, I believe your web site might be having internet browser compatibility
issues. Whenever I look at your site in Safari, it looks fine however, when opening in IE,
it has some overlapping issues. I simply wanted to
give you a quick heads up! Aside from that, fantastic website!
Good post! We will be linking to this great article on our website. Keep up the good writing.
used trucks are sometimes expensive and it is quite hard to find a good bargain if you don’t search heavily”
Wow, wonderful blog layout! How long have you been blogging for?
you make blogging look easy. The overall look of your website is magnificent, let alone the content!
Can I simply say what a relief to seek out somebody who really knows what theyre speaking about on the internet. You definitely know the way to convey an issue to mild and make it important. Extra folks need to read this and understand this facet of the story. I cant consider youre no more common because you positively have the gift.
Thank you for sharing with us, I conceive this website really stands out : D.
Good post. I learn something totally new and challenging on blogs I stumbleupon on a daily basis. It’s always exciting to read through articles from other authors and use something from their websites.
Discover out extra about how these waiting durations work and how some might be eliminated all together.
This post is actually a fastidious one it helps new web users, who are wishing
for blogging.
The alcohol content in hand sanitizers can break down the oils in lipstick, making it simpler to wash out.
You still want the mechanical skills to carry out the work (or the money to pay someone) but you don’t want to fret about salvaging the engine from one other automotive.
These smaller fish will ostensibly entice larger fish and so forth until sharks flip up to see what the massive deal is.
Since only a few bombs fell till mid-1940, Britain did have ample time to arrange.
Dedicated November 20, 1938 beneath the auspices of Col.
I’d like to thank you for the efforts you have put in penning this blog.
I’m hoping to view the same high-grade blog posts by you in the future as well.
In fact, your creative writing abilities has motivated me
to get my own site now 😉
Heya i am for the first time here. I came across this board and I find It really useful & it helped
me out a lot. I hope to give something back and
help others like you helped me.
Pretty! This has been an incredibly wonderful article.
Thank you for providing this info.
Pretty! This was an extremely wonderful article. Many thanks for supplying this info.
Everything is very open with a clear description of the issues. It was definitely informative. Your site is extremely helpful. Thank you for sharing.
There are some interesting deadlines in this article but I don’t know if I see all of them heart to heart. There is some validity however I’ll take hold opinion till I look into it further. Good article , thanks and we want more! Added to FeedBurner as effectively
Why viewers still use to read news papers when in this technological world the whole thing is existing on net?
Hi, every time i used to check website posts here in the early hours in the
break of day, since i love to find out more and more.
Introducing to you the most prestigious online entertainment address today. Visit now to experience now!
Thank you a bunch for sharing this with all people you really recognize what you are talking approximately! Bookmarked. Kindly additionally discuss with my web site =). We will have a link alternate contract among us!
With the help of Singapore b2b telemarketing firm, distance will no longer be a hindrance.
Folks seemed to need monsters and nasty bad guys.
Kurt Russell. He cannot communicate verbally past repeating the previous couple of phrases he hears.
Today, I went to the beachfront with my kids. I found a sea shell and gave it to my 4 year old daughter and said “You can hear the ocean if you put this to your ear.”
She placed the shell to her ear and screamed. There was a hermit crab
inside and it pinched her ear. She never wants to go back!
LoL I know this is completely off topic but I had to
tell someone!
There’s certainly a lot to know about this subject. I like all the points you made.
Even as the workforce raced with little success that season, Ferrari was arduous at work growing a state-of-the-artwork turbo-charged engine.
See to it that you set your emblem in a spot that people look at.
For instance, some individuals purchase big autos, far greater than what they would need on a daily basis, for the occasional trip or errand.
The World Chess Championship 2021 was a chess match between the reigning world champion Magnus Carlsen and the challenger Ian Nepomniachtchi to find out the World Chess Champion.
Precisely what I was searching for, appreciate it for putting up.
This overrated buzz and hyped up technology has now become an essential part of the business world.
The various search engines are a cellular search platform that makes the process of navigation and home searches very simple.
Hiya, I’m really glad I have found this info. Today bloggers publish just about gossips and web and this is actually irritating. A good site with exciting content, that is what I need. Thanks for keeping this web-site, I will be visiting it. Do you do newsletters? Can’t find it.
You鈥檒l also gain a greater understanding of human conduct and have the chance to hone your research and writing abilities.
In the league, Liverpool hold a snug four-point lead over Everton at the highest at the tip of the month.
The futures market holds a number of those twin opportunities.
It is not my first time to go to see this website, i
am visiting this site dailly and take pleasant information from here all the time.
Section 8 – WRESTLE – BIND – Loose- COMMAND Assault – Assault – Assault CONTENTS 1. SCRIPTURE 2. SCRIPTURE KEYS 3. Overall PRAYER 4. Overall COMMAND 5. General WARFARE 6. Comments 1. Eph.
When a deal is finalized, this is often called a “spot deal.” it is a bilateral transaction in which one celebration grants an agreed-upon currency quantity to the counter get together and receives a certain amount of one more currency at the agreed-upon trade fee price.
By including in gold-painted picture frames, mirrors, vases, chairs, or chandeliers, you possibly can have a wedding ceremony match for a vintage queen!
I’m not sure exactly why but this site is loading incredibly slow for me.
Is anyone else having this issue or is it a issue on my end?
I’ll check back later on and see if the problem still
exists.
26 Could 1979: England beat Scotland 3-1 at Wembley to clinch the house Championship.
One service provider got heated and accused the railroad of working its operations poorly until being advised to cease berating by the Chamber of Commerce Chairman.
Customized car outlets turn into famous for the way they lower their own and their customers’ automobiles and trucks, and weekend mechanics have vehicles featured in international lowrider competitions because of their ingenuity at combining, innovating and customizing, typically with floor-grazing sparks.
Hello! I just would like to give you a massive thumbs up for any fantastic info you’ve here about this post. I’ll be coming back to your site for more soon.
It’s difficult to find educated people about this subject, however, you sound like you know what you’re talking about! Thanks
sex nhật hiếp dâm trẻ em ấu dâm buôn bán vũ khí ma túy bán súng sextoy chơi đĩ sex bạo lực sex học đường tội phạm tình dục chơi les đĩ đực người mẫu bán dâm
Nice post. I learn something new and challenging on sites I stumbleupon on a daily basis.
It will always be useful to read articles from other authors and use something from their sites.
Good day! I could have sworn I’ve been to this site before but after browsing through a few of the posts I realized it’s new to me. Anyways, I’m certainly delighted I stumbled upon it and I’ll be bookmarking it and checking back often!
Nice post. I learn something new and challenging on blogs I stumbleupon on a daily basis.
It will always be helpful to read through content from other authors and use
something from other web sites.
Very nice post and right to the point. I am not sure if this is in fact the best place to ask but do you people have any thoughts on where to hire some professional writers? Thanks
Simply, the article is actually the greatest on that worthy topic. I agree with your conclusions and can eagerly look forward to your forthcoming updates. Saying thanks definitely will not simply just be sufficient, for the fantasti c clarity in your writing. I definitely will right away grab your rss feed to stay privy of any updates. Admirable work and also much success in your business endeavors!
Attractive part of content. I just stumbled upon your site and in accession capital to claim that I acquire in fact enjoyed account your blog posts. Any way I’ll be subscribing to your feeds and even I achievement you get entry to constantly quickly.
What’s up friends, how is all, and what you would like to say concerning this article,
in my view its actually remarkable designed for me.
each time i used to read smaller posts which as well clear their motive, and that is also happening with this article which I am reading at this time.
I am really enjoying the theme/design of your weblog.
Do you ever run into any internet browser compatibility problems?
A couple of my blog readers have complained about my blog not operating correctly in Explorer but looks great
in Chrome. Do you have any advice to help fix this issue?
Good way of explaining, and fastidious article to take information regarding my presentation subject,
which i am going to convey in university.
I’m extremely inspired along with your writing abilities as well as with the format on your weblog.
Is that this a paid subject matter or did you customize it yourself?
Either way keep up the excellent quality writing, it’s rare to see a nice blog like this one these days..
Hi, its pleasant post concerning media print, we all understand media is
a impressive source of facts.
You ought to be a part of a contest for one of the greatest sites on the
internet. I am going to recommend this blog!
I wanted to produce you this tiny remark so as to give numerous thanks when once again contemplating the spectacular suggestions you’ve discussed at this time. It was very strangely open-handed of you to supply unhampered specifically what a whole lot of folks could possibly have marketed for an electronic book in creating some money for themselves, most importantly because you may well have tried it in the event you decided. Those fundamentals furthermore served to present a great method to totally grasp some folks have the very same keenness considerably like my very own to see a whole lot a lot more on the subject of this condition. I think you will find many far more enjoyable opportunities ahead for individuals who looked over your site.
you’ve gotten an important weblog right here! would you wish to make some invite posts on my weblog?
Keep up the superb piece of work, I read few articles on this web site and I conceive that your web site is real interesting and has got sets of great information.
I get pleasure from, lead to I discovered exactly
what I was taking a look for. You’ve ended my 4 day long hunt!
God Bless you man. Have a great day. Bye
Thank you for sharing your thoughts. I truly appreciate your
efforts and I will be waiting for your next post thanks once again.
You should be a part of a contest first of the most effective blogs online. Let me suggest this blog!
Wow I absolutely love her! She is freakin’ beautiful and not to mention a really good actress. I don’t think the show V is all that good, but I watch it anyway just so I can see Morena Baccarin. And I don’t know if you’ve ever seen her do an interview but she is also rather comical and it seems so natural for her. I personally never even heard of her before The V, now I’ll watch anything she’s on.
Show me your other posts. If they are so good as this one i`ll be your permanent guest.
We’re a group of volunteers and opening a new scheme in our community.
Your web site provided us with valuable info to work on. You have done an impressive job and our entire
community will be thankful to you.
I always spent my half an hour to read this web site’s articles
or reviews everyday along with a mug of coffee.
Just right points?I might be aware that as anyone who in point of fact doesn’t write on blogs so much (if truth be told, this can be my first publish), I don’t assume the time period ‘lurker’ could be very turning into to a non-posting reader. It’s no longer your fault in the least , but possibly the blogosphere may just get a hold of a greater, non-creepy name for the ninety folks that revel in studying the content material .
The camera work heightens this loss of individuality by filming everyone from the back or side whenever there is action, so close you can’t tell who is doing what, or were in relation to other people they are doing anything with.
Wow this game looks uber. How is a kid supposed to get any learning done with all-knowing distractions like this?!?!
Thank you for every other great article. The place else could anyone get that type of info
in such a perfect means of writing? I’ve a presentation subsequent
week, and I am on the search for such information.
Article writing is also a fun, if you be familiar with then you
can write or else it is difficult to write.
Wonderful paintings! That is the type of info that are supposed to be shared across the net. Shame on search engines for not positioning this submit higher! Come on over and consult with my website . Thanks =)
good post, i surely enjoy this website, continue on it.
This is a great web page, would you be involved in doing an interview regarding just how you created it? If so e-mail me!
I know this if off topic but I’m looking into starting
my own weblog and was wondering what all is required to get set up?
I’m assuming having a blog like yours would cost a pretty penny?
I’m not very web smart so I’m not 100% certain. Any suggestions or advice
would be greatly appreciated. Appreciate it
Thank you for the good writeup. It actually was a amusement account it.
Glance complicated to far introduced agreeable from you!
However, how could we be in contact?
hello!,I love your writing very so much! proportion we keep
in touch extra about your post on AOL? I need a specialist in this space to unravel my problem.
Maybe that’s you! Taking a look forward to see you.
I really enjoyed reading this! Your writing style is engaging, and the content is valuable. Excited to see more from you!
This website was… how do I say it? Relevant!!
Finally I’ve found something that helped me.
Thanks a lot!
Well done! I thank you your contribution to this matter. It has been useful. my blog: how to get taller
Oh my goodness! a wonderful write-up dude. Thanks a ton Even so I am experiencing trouble with ur rss . Do not know why Struggling to sign up for it. Perhaps there is any person acquiring identical rss difficulty? Anyone who knows kindly respond. Thnkx
Great article! I learned a lot from your detailed explanation. Looking forward to more informative content like this!
Appreciate it for this grand post, I am glad I noticed this website on yahoo.
I need to to thank you for this great read!! I definitely loved every bit of it. I’ve got you saved as a favorite to look at new things you post…
Commander Geoffrey Clement Percival Lycett.
My brother recommended I might like this web site.
He was totally right. This post actually made my day.
You cann’t imagine just how much time I had spent for this info!
Thanks!
The “All Aboard!” Gallery options an 11,000-pound (5,000 kg) steam engine designed by Reuben Wells in 1868 to conquer Indiana’s Madison Hill.
I quite like looking through a post that will make people think.
Also, thank you for permitting me to comment!
Excellent post. I was checking constantly this blog and I am impressed! Extremely useful information particularly the last part I care for such information a lot. I was seeking this certain info for a long time. Thank you and best of luck.
Hope to see many more fantastic pieces like this in the future. You completely helped me build on my little base of this topic.
There a few intriguing points in time in this posting but I do not determine if I see these people center to heart. There is certainly some validity but I will take hold opinion until I consider it further. Very good article , thanks therefore we want a lot more! Added to FeedBurner in addition
Thanks for one’s marvelous posting! I quite enjoyed reading it,
you will be a great author. I will be sure to bookmark your blog and will eventually come back in the
foreseeable future. I want to encourage you continue your great posts,
have a nice afternoon!
Its like you read my mind! You seem to know so much about this, like
you wrote the book in it or something. I think that you could do with a few pics to
drive the message home a bit, but other than that, this
is great blog. An excellent read. I’ll certainly be back.
Hello to every single one, it’s actually a pleasant for me to
visit this website, it includes priceless Information.
Youre so cool! I dont suppose Ive read anything similar to this before. So nice to discover somebody by original ideas on this subject. realy appreciate starting this up. this excellent website can be something that is required on the internet, a person with some originality. useful problem for bringing a new challenge to your web!
I was reading some of your content on this internet site and I conceive this internet site is real informative ! Retain putting up.
That song sucks i think, my younger brother is listening that, and its so boring song !
I will right away snatch your rss as I can not in finding your e-mail subscription link or e-newsletter service.
Do you’ve any? Please let me realize so that I may just subscribe.
Thanks.
Hey are using WordPress for your site platform? I’m new to the blog world but I’m trying to get started and set up my own. Do you need any html coding knowledge to make your own blog?
Any help would be really appreciated!
There are certainly a lot of details prefer that to consider. That is a wonderful specify talk about. I offer the thoughts above as general inspiration but clearly you can find questions like the one you raise up the location where the biggest thing will likely be doing work in honest great faith. I don?t know if recommendations have emerged around such things as that, but More than likely that your job is clearly recognized as a fair game. Both youngsters have the impact of just a moment’s pleasure, through out their lives.
You created some decent points there. I looked online for the issue and found most people may go as well as using your internet site.
The next time I just read a blog, I hope which it doesnt disappoint me just as much as brussels. After all, It was my replacement for read, but I actually thought youd have something interesting to talk about. All I hear can be a number of whining about something that you could fix in the event you werent too busy trying to find attention.
Vuoi tentare la fortuna come un esperto? Scopri le nostre tecniche vincenti, i offerte esclusivi e una piattaforma di gioco affidabile. Unisciti al nostro casinò online e inizia oggi stesso!
https://phatwalletforums.com/user/grato
Procurando por emoção? Fortune Rabbit é o jogo certo para você! Com gráficos impressionantes e ofertas de até 5000x seu dinheiro, a sorte pode estar do seu lado. Não precisa pagar nada para testar! Acesse a versão de teste e experimente todos recursos sem compromisso. FortuneRabbit é uma excelente chance para quem querem aprender como jogar sem gastar um real.
You’ve made some decent points there. I looked on the web for more
information about the issue and found most people will go along with your views
on this web site.
Hi there, I found your site by the use of Google whilst looking for a related subject,
your website came up, it appears to be like great.
I’ve bookmarked it in my google bookmarks.
Hello there, simply turned into alert to your weblog via Google, and found that it’s truly informative.
I’m gonna watch out for brussels. I’ll be grateful if you happen to continue this in future.
A lot of folks shall be benefited out of your writing.
Cheers!
Yes! Finally something about gamebaidoithuongso.
My coder is trying to persuade me to move to .net from PHP.
I have always disliked the idea because of the expenses.
But he’s tryiong none the less. I’ve been using Movable-type on several websites for about a year and am anxious about switching to another platform.
I have heard good things about blogengine.net. Is there a way
I can import all my wordpress content into it? Any kind of
help would be greatly appreciated!
I blog frequently and I truly thank you for your content.
This article has really peaked my interest.
I will book mark your site and keep checking for
new information about once per week. I opted in for your RSS feed too.
Greetings! Very useful advice in this particular post! It is the little changes that produce the most important changes. Thanks for sharing!
I really like what you guys tend to be up too.
This kind of clever work and exposure! Keep up the awesome works guys I’ve incorporated you guys to my personal blogroll.
What’s up to every one, it’s really a pleasant for me to visit this web page, it
contains precious Information.
Well-written and insightful! Your points are spot on, and I found the information very useful. Keep up the great work!
Hey! I just wanted to ask if you ever have any
issues with hackers? My last blog (wordpress) was hacked
and I ended up losing many months of hard work due to no backup.
Do you have any methods to protect against hackers?
Wow, that’s what I was seeking for, what a information! existing here at this
web site, thanks admin of this site.
Travel can teach you new classes.
I’d ought to check with you here. Which isn’t something I do! I like reading a post which will get people to feel. Also, thanks for permitting me to comment!
i have some small garden of herbs at home, i use them for baking foods and as herbal medicines.
I like the way you conduct your posts. …
There are three completely different kinds of robotic surgery techniques: supervisory-managed systems, telesurgical programs and shared-control programs.
Tuition fees in England are to rise for the primary time in eight years, after universities called for help with their finances.
Bosses then referred to as Ola in for a gathering and agreed that she and Steve can be accompanied always whereas they remained in the competition.
This post is very helpful! I appreciate the effort you put into making it clear and easy to understand. Thanks for sharing!
Fortune Rabbit é uma excelente opção para quem procuram adrenalina em cassinos online. Usando ganhos de até cinco mil vezes, a fortuna pode mudar seu jogo. Teste a versão grátis e veja como esse cassino pode ser divertido. Não se preocupe com downloads! Jogue diretamente na plataforma e se prepare para um jogo inesquecível.
I’m really loving the theme/design of your web site.
Do you ever run into any web browser compatibility issues?
A few of my blog readers have complained about my blog not operating correctly in Explorer but looks great
in Opera. Do you have any recommendations to help fix
this problem?
Hi there! I know this is somewhat off topic but I was wondering which blog platform are you using
for this website? I’m getting tired of WordPress because
I’ve had issues with hackers and I’m looking at options for another platform.
I would be awesome if you could point me in the direction of
a good platform.
Introducing to you the most prestigious online entertainment address today. Visit now to experience now!
What’s up colleagues, how is the whole thing,
and what you would like to say on the topic of this piece of writing, in my view its actually awesome in support of me.
This design is incredible! You most certainly know how to keep
a reader entertained. Between your wit and your videos, I was
almost moved to start my own blog (well, almost…HaHa!) Wonderful job.
I really loved what you had to say, and more than that, how
you presented it. Too cool!
Hi there, this weekend is good for me, since this moment i am reading this impressive educational
article here at my home.
I appreciate the depth of research in this article. It’s both informative and engaging. Keep up the great work!
Why visitors still make use of to read news papers when in this technological world everything is presented on web?
Good post! We are linking to this great article on our website.
Keep up the good writing.
I do consider all the ideas you have introduced on your post. They are very convincing and will definitely work. Still, the posts are very brief for newbies. May you please lengthen them a bit from subsequent time? Thank you for the post.
I am glad to be a visitor of this staring weblog, thanks for this rare info!
Thanx for a very informative website. Where else may I get that type of information written in such a perfect way? I have a venture that I am just now running on, and I’ve been at the look out for such information.
Disney loves anthropomorphic animals, and we love Disney, so it isn’t any shock that Disney’s animal films make a ton of money.
Very nice article. I definitely appreciate this site. Thanks!
This post is very helpful! I appreciate the effort you put into making it clear and easy to understand. Thanks for sharing!
Oftentimes, they will be booked months before the season even starts.
As beguiling as these patterns could seem now, they’re the ones you are most apt to tire of shortly.
I loved as much as you will receive carried out right here.
The sketch is attractive, your authored subject matter stylish.
nonetheless, you command get got an shakiness over that you wish be delivering the following.
unwell unquestionably come more formerly again since exactly the same
nearly a lot often inside case you shield this hike.
Howdy! This article could not be written any better! Looking through this post reminds me of my previous roommate! He constantly kept preaching about this. I will send this information to him. Fairly certain he will have a very good read. Thank you for sharing!
I understand this is not exactly on topic, but i run a web site using the similar platform as well and i’m having troubles with my comments showing. will there be a setting i am losing? possibly you could help me out? thx.
Undeniably believe that which you said. Your favorite reason seemed to be on the net the simplest thing to be aware of. I say to you, I certainly get annoyed while people think about worries that they plainly don’t know about. You managed to hit the nail upon the top and defined out the whole thing without having side-effects , people could take a signal. Will probably be back to get more. Thanks
This was a really nice post. In concept I would like to put in writing like this moreover – taking time and actual effort to make an excellent article… however what can I say… I procrastinate alot and not at all appear to get something done.
This post is very helpful! I appreciate the effort you put into making it clear and easy to understand. Thanks for sharing!
Thank you for sharing your thoughts. I really appreciate your efforts and I am waiting for
your further post thank you once again.
What’s up, I check your blog regularly. Your writing style
is awesome, keep it up!
sex nhật hiếp dâm trẻ em ấu dâm buôn bán vũ khí ma túy bán súng sextoy chơi đĩ sex bạo lực sex học đường tội phạm tình dục chơi les đĩ đực người mẫu bán dâm
My relatives always say that I am killing my time here at web, but I know I am getting experience daily
by reading thes nice articles or reviews.
I really enjoyed reading this! Your writing style is engaging, and the content is valuable. Excited to see more from you!
Simply, admirable what you might have completed here. It is pleasing to search you express through the heart and your clarity on this significant content material might be effortlessly looked. Outstanding publish and can appear ahead to your long term update.
Pretty section of content. I just stumbled upon your website and in accession capital to assert that I get actually enjoyed account your blog posts. Anyway I will be subscribing to your feeds and even I achievement you access consistently quickly.
I have been exploring for a bit for any high-quality articles or weblog posts in this kind of area . Exploring in Yahoo I eventually stumbled upon this website. Studying this info So i’m satisfied to exhibit that I’ve an incredibly just right uncanny feeling I found out exactly what I needed. I most indubitably will make certain to don’t fail to remember this website and provides it a look a continuing.
Wonderful beat ! I wish to apprentice at the same time
as you amend your site, how can i subscribe for a blog website?
The account aided me a appropriate deal. I had been tiny bit acquainted of this your broadcast offered bright transparent idea
I haven?t checked in here for some time because I thought it was getting boring, but the last few posts are good quality so I guess I?ll add you back to my everyday bloglist. You deserve it my friend
It’s in point of fact a nice and helpful piece of information. I am satisfied that you shared this useful info with us. Please stay us informed like this. Thanks for sharing.
i like war movies and inglourious basterds is one of the movies that i really love~
I appreciate the depth of research in this article. It’s both informative and engaging. Keep up the great work!
The next time I read a blog, I hope that it won’t fail me just as much as this particular one. I mean, Yes, it was my choice to read through, but I actually thought you’d have something useful to talk about. All I hear is a bunch of moaning about something that you could fix if you weren’t too busy seeking attention.
Hey there! I know this is kinda off topic but I was wondering which blog platform are you using for this website?
I’m getting tired of WordPress because I’ve
had problems with hackers and I’m looking at alternatives for another platform.
I would be fantastic if you could point me in the direction of a good platform.
What i do not understood is in fact how you’re
now not actually a lot more neatly-liked
than you might be now. You’re very intelligent. You
know therefore considerably with regards to this
subject, made me in my opinion believe it from a lot of varied angles.
Its like women and men don’t seem to be involved unless it’s one thing to do with
Woman gaga! Your own stuffs great. Always maintain it up!
Fantastic goods from you, man. I have take into accout your stuff prior to and you are just too
great. I actually like what you have obtained here, really like
what you are stating and the way through which you assert it.
You make it enjoyable and you still take
care of to keep it wise. I can’t wait to read much more from you.
This is actually a wonderful website.
When I originally commented I clicked the -Notify me when new surveys are added- checkbox and after this whenever a comment is added I buy four emails with similar comment. Is there any way it is possible to eliminate me from that service? Thanks!
Yeah, i agree with what was said in your blog. Thank you very much for all the info. and your hard work.
Awesome post it is really. I’ve been searching for this information
Fantastic post! The information you shared is really valuable and well-explained. Thanks for putting this together!
Hi it’s me, I am also visiting this web site regularly, this site is actually good and the
people are truly sharing fastidious thoughts.
I got this web page from my friend who shared with me
on the topic of this site and now this time I am browsing this site and reading very informative posts here.
Write more, thats all I have to say. Literally, it seems as though
you relied on the video to make your point. You obviously know what youre talking about,
why throw away your intelligence on just posting videos to your blog when you could be giving us something informative to read?
Very good info. Lucky me I discovered your site by accident (stumbleupon). I have saved it for later!
This was a great read! Your insights are truly helpful and make complex topics easy to understand. Looking forward to more!
This excellent website definitely has all the information and facts I wanted concerning this subject and didn’t know who to ask.
This was a great read! Your insights are truly helpful and make complex topics easy to understand. Looking forward to more!
Your means of explaining the whole thing in this article
is actually pleasant, all be capable of simply
be aware of it, Thanks a lot.
aa den stora boken… […]p Have you noticed any performance problems with the wordpress platform? I ha oj[…]…
Hey i Love your work i really appreciate that. Also take a look at our special Gym flooring dubai
Interesting read , I’m going to spend more time researching this subject
Nice read, I just passed this onto a friend who was doing a little research on that. And he actually bought me lunch since I found it for him smile So let me rephrase that: Thank you for lunch!
i love to do both online shopping and online window shopping for goods and other stuffs**
Hi there! Do you know if they make any plugins to safeguard against hackers? I’m kinda paranoid about losing everything I’ve worked hard on. Any recommendations?
There is noticeably a lot of money comprehend this. I assume you made specific nice points in functions also.
Normally I don’t read article on blogs, but I wish to say that this write-up very
pressured me to take a look at and do so! Your writing taste has
been amazed me. Thanks, very great article.
Introducing to you the most prestigious online entertainment address today. Visit now to experience now!
Hey there! Do you know if they make any plugins to assist with SEO?
I’m trying to get my blog to rank for some targeted keywords but
I’m not seeing very good success. If you know of
any please share. Cheers!
Greater SEER ratings indicate much better power performance and a reduced carbon footprint.
Perfectly, i need to assert that crafting talents possibly not which terrible, having said that i’ll you could increase ones own authoring proficiency. Working with not as much text to talk about the actual. You could check out bing designed for penning proficiency teaching web page and plans.
Hi there. I wanted to ask something…is the following a wordpress web site as we are planning to be moving across to WP. Furthermore did you make this design all by yourself? Bless you.
Iím not that much of a internet reader to be honest but your blogs really nice, keep it up! I’ll go ahead and bookmark your website to come back in the future. Cheers
Introducing to you the most prestigious online entertainment address today. Visit now to experience now!
Very interesting topic , regards for putting up.
I saw something about that subject on TV last night. Great post.
Manage your buttons through an editable XML file. Choose which buttons you want enabled, or add new buttons yourself.
At our business we take on all facets of storage
air conditioning including Setup and Maintenance.
A centrally ducted ac system can utilize 5000 watts an hour to
cool an entire home.
Below’s a fast failure to recognize how much to set up cooling
in your house.
If you are not sure what system would best match your requirements, please so not be reluctant to get in touch.
Cassette cooling devices are a preferred selection for offices and retail spaces with grid ceilings.
We can give the different air conditioning option with internal water cooled down condensing systems.
Introducing to you the most prestigious online entertainment address today. Visit now to experience now!
Installing an air disadvantage by yourself without correct training and
understanding can be a risky endeavor.
As we have actually advanced right into the 21st century there has actually been an additional shift worldwide of home
heating.
The mobile units generally can not be made use of to warmth due
to the fact that the awesome air can not be ducted out.
The main distinction in between main and ductless cooling systems
is the amount of cooling capacity.
Call a professional to find and service your cooling asap.
If you are billed per hour, then duration is very pertinent
to the cost.
This service frequently involves a mix of tools,
supply, and wage expenses.
Hi, i feel that i saw you visited my web site thus i got here to
go back the choose?.I’m attempting to to find things to enhance my
web site!I suppose its good enough to make use of a few of your ideas!!
Hello, i think that i saw you visited my site thus i came to “return the
favor”.I’m trying to find things to improve my site!I suppose its ok to use a few of your ideas!!
Wonderful beat ! I wish to apprentice even as you
amend your web site, how could i subscribe for a blog site?
The account aided me a applicable deal. I had been a little bit familiar of this
your broadcast offered shiny transparent idea
When you air problem your home, you also maintain your
windows and doors shut.
Nevertheless, they are positioned at flooring level and can resemble
a radiator.
This piece of writing is in fact a nice one it assists new the web viewers, who are wishing for blogging.
sex nhật jmppnet.com hiếp dâm trẻ em jmppnet.com ấu dâm jmppnet.com buôn bán vũ khí jmppnet.com
Next, affix the side panels with the screws that come with the
window air conditioning.
obviously like your web-site but you have to check the spelling
on quite a few of your posts. Several of them are rife with spelling problems and I to find it
very troublesome to inform the reality then again I’ll definitely come back
again.
I am regular visitor, how are you everybody?
This post posted at this web site is actually good.
Hi, I log on to your blogs like every week. Your humoristic
style is awesome, keep it up!
Good day! I know this is kinda off topic however I’d figured I’d ask.
Would you be interested in exchanging links or maybe guest writing a blog article or vice-versa?
My website addresses a lot of the same subjects as yours
and I feel we could greatly benefit from each other. If you might be interested feel
free to shoot me an email. I look forward to hearing from you!
Awesome blog by the way!
Hmm is anyone else experiencing problems with the images on this blog loading?
I’m trying to find out if its a problem on my end or if
it’s the blog. Any feed-back would be greatly appreciated.
Hey I know this is off topic but I was wondering
if you knew of any widgets I could add to my blog
that automatically tweet my newest twitter updates.
I’ve been looking for a plug-in like this for quite some
time and was hoping maybe you would have some experience with something like this.
Please let me know if you run into anything. I truly enjoy reading
your blog and I look forward to your new updates.
Hello there! Do you know if they make any plugins to assist with SEO?
I’m trying to get my blog to rank for some targeted keywords
but I’m not seeing very good gains. If you know of any please share.
Kudos! I saw similar blog here: Code of destiny
Wow, fantastic blog layout! How long have you been blogging for?
you make blogging look easy. The overall look of your website is great, let alone the content!
Hello there! I could have sworn I’ve been to this website before but
after browsing through some of the post I realized it’s
new to me. Nonetheless, I’m definitely delighted I found it and I’ll
be book-marking and checking back often!
I every time used to read article in news papers but now as
I am a user of net so from now I am using net for posts, thanks to web.
You need to get upset! Really its a must to take a look past everything and get upset. Generally this will allow you to take the inititive to make things happen.
I am interested in talking to you about your website design. Did someone design it for you?
Shakira and Taylor Swift are my favorite singers, Shakira is great on live performance“
we love watching Dancing with the stars, the actresses and actors that joins it are nice::
very good submit, i actually love this website, keep on it
some ayurvedic herbs have nasty side effects too that is why you should carefully choose the safer ones.
Hi! I know this is somewhat off topic but I was wondering if you
knew where I could find a captcha plugin for my comment form?
I’m using the same blog platform as yours and I’m having difficulty finding one?
Thanks a lot!
I’m pretty pleased to discover this website. I need to to thank
you for your time for this particularly wonderful read!!
I definitely loved every little bit of it and I have you book marked to look at
new things on your web site.
Hi there would you mind sharing which blog platform you’re working with?
I’m planning to start my own blog soon but
I’m having a tough time choosing between BlogEngine/Wordpress/B2evolution and Drupal.
The reason I ask is because your layout seems different
then most blogs and I’m looking for something completely unique.
P.S My apologies for getting off-topic but I had
to ask!
What’s up! Finding joy in the layout—it’s brilliant. In fact, the details brings a incredible touch to the overall vibe. More please!
Many thanks for creating the effort to discuss this, I feel strongly about this and enjoy studying a great deal more on this topic. If feasible, as you gain expertise, would you mind updating your webpage with a great deal more details? It’s very helpful for me.
Hello just wanted to give you a quick heads up. The words in your article seem to be running off the screen in Opera. I’m not sure if this is a formatting issue or something to do with browser compatibility but I figured I’d post to let you know. The design and style look great though! Hope you get the issue resolved soon. Cheers
Thank you for the auspicious writeup. It in fact was a amusement account it. Look advanced to more added agreeable from you! However, how can we communicate?
Its like you read my mind! You appear to know so much about this, like you wrote the book in it or something.
I think that you can do with a few pics to drive the message home a bit, but other than that, this is fantastic blog.
A fantastic read. I’ll certainly be back.
I would like to thank you for the efforts you have put in writing this blog.
I’m hoping to check out the same high-grade content by
you in the future as well. In fact, your creative writing abilities has inspired me to get my very own website now 😉
I loved as much as you will receive carried out right here.
The sketch is attractive, your authored material stylish.
nonetheless, you command get bought an impatience
over that you wish be delivering the following. unwell unquestionably come more formerly again as exactly the same
nearly a lot often inside case you shield this hike.
I lately stumbled on your website and also have been learning along. I was thinking I might leave my very first remark. I do not know what to state except that I have liked reading through. Solid website. I am going to maintain browsing this site incredibly typically.
Pretty nice post. I just stumbled upon your weblog and wished to say that I’ve truly enjoyed browsing your blog posts. In any case I’ll be subscribing on your rss feed and I hope you write once more soon!
Introducing to you the most prestigious online entertainment address today. Visit now to experience now!
Awesome brief article! I absolutely had the exact reviewing. I hope to share added by you. I know you possess very good information into coupled with ideas. I will be exceedingly fulfilled with this particular information and facts.
my dad is a massage therapist and he can really relieve minor pains and injuries“
most travel sites have very nice webpages and their services are very nice too.,,
What’s up to every , for the reason that I am actually keen of reading this webpage’s post to be updated on a regular basis.
It includes good information.
Hey all! Admiring the details—it’s awesome. In fact, the composition brings a great touch to the overall vibe. This is epic!
Quality posts is the crucial to invite the people to
go to see the web site, that’s what this website is providing.
Keep on writing, great job!
Przez bonusom i zawodom, VOX Casino oferuje graczom wielką zabawę i szansę wielkie profity. Wejdź teraz i przekonaj się jak to wygląda w działaniu! https://voxcasino777.pl/
Thank you for sharing with us, I conceive this website genuinely stands out : D.
there are many greeting card options that you can see in online stores but i love those that generate cute sounds-
I like what you guys are up too. Such intelligent work and reporting! Keep up the excellent works guys I have incorporated you guys to my blogroll. I think it’ll improve the value of my web site .
Hi! I could have sworn I’ve been to this blog before but after browsing through many of the articles I realized it’s new to me. Regardless, I’m certainly pleased I found it and I’ll be book-marking it and checking back often.
Excellent goods from you, man. I’ve take into accout your stuff previous to and you are simply too excellent.
I really like what you have received here, really
like what you’re stating and the way in which you assert it.
You are making it enjoyable and you still care for to stay it wise.
I can not wait to learn much more from you. This is actually a wonderful web site.
Thank you for the auspicious writeup. It in fact was a amusement account it.
Look advanced to far added agreeable from you!
By the way, how could we communicate?
I really like what you guys are up too. This sort of clever work and exposure!
Keep up the terrific works guys I’ve included you guys to my own blogroll.
That is a good tip especially to those new to the
blogosphere. Simple but very precise info… Thank you for sharing this
one. A must read post!
Appreciate this post. Will try it out.
Thanks, Plenty of facts on vaping laws and regulations!
Spot on with this write-up, I truly suppose this website needs rather more consideration. I’ll in all probability be again to learn much more, thanks for that info.
There is noticeably a bundle to know about this. I assume you made sure nice points in options also.
There are a couple of interesting points with time in this posting but I do not know if I see these people center to heart. There exists some validity but I’m going to take hold opinion until I check into it further. Great write-up , thanks and we want a lot more! Included with FeedBurner as well
There are methods to chop gown prices with out forfeiting type, or even fantasy.
Taoiseach Micheál Martin announced that Ireland had reached the milestone of half a million COVID-19 vaccines administered.
Six or eight are usually more common in most North American autos.
A palatial bath in a cute little home will make your home less, no more, fascinating.
Captain Diana Geraldine Mary Anderson (459562), Queen Alexandra’s Royal Army Nursing Corps.
By taking part in Piano Wizard, you will not learn the names of notes, however you’ll turn into accustomed to the concept that different keys produce completely different pitches or sounds.
Outpatient benefits in a PPO or POS could be broader because you may go exterior the network to seek out the right provider of the outpatient benefit you might be seeking.
More durable, Ben (sixteen June 2020).
Introducing to you the most prestigious online entertainment address today. Visit now to experience now!
It used to be known as the Transit Connect, but who made it?
On the following pages, you will get nice concepts for yard games that the whole household can enjoy.
Introducing to you the most prestigious online entertainment address today. Visit now to experience now!
He died in 1730 having executed no further work to the property.
There was criticism of CPI as being a much less efficient measure of worth rises than the Retail Prices Index, accusing it of being easier to control and fewer broad based (for instance excluding housing).
Thou shalst assume My place because the Lord of Compassion and Labor.
Everything is very open with a really clear explanation of the issues.
It was definitely informative. Your site is useful. Thanks for sharing!
Your style is unique compared to other folks I have read stuff from.
Thanks for posting when you’ve got the opportunity, Guess I’ll just bookmark this page.
Spot up with this write-up, I actually think this website needs additional consideration. I’ll more likely once again to learn to read considerably more, thank you for that information.
Pretty important article. I generally do not comment post, but this time I made an exception, because I have seen here a lot of helpful info. Thank you for the helpful and useful information.
Aw, i thought this was an incredibly good post. In thought I would like to invest writing such as this moreover – taking time and actual effort to have a top notch article… but exactly what can I say… I procrastinate alot and by no means apparently get something done.
Introducing to you the most prestigious online entertainment address today. Visit now to experience now!
Hi there mates, its enormous article regarding cultureand fully defined, keep it up all the time.
This blog was… how do you say it? Relevant!! Finally I have found something that
helped me. Many thanks!
It’s an remarkable piece of writing in favor of all the web users; they will take advantage from it I am sure.
bookmarked!!, I like your site!
Wow, this piece of writing is nice, my younger sister is analyzing these things,
thus I am going to inform her.
Pretty! This was an incredibly wonderful post.
Thank you for providing these details.
I think that everything wrote made a lot of sense. However, what about this?
suppose you typed a catchier title? I mean, I don’t wish
to tell you how to run your website, but what if you
added a title that makes people want more? I mean SMI diamond grinding wheels is kinda plain. You
might peek at Yahoo’s front page and watch how they create news headlines to
grab people to click. You might add a video or a pic or
two to grab people interested about everything’ve got to say.
Just my opinion, it would make your posts a little bit more interesting.
Hello there, just became aware of your blog through Google,
and found that it is truly informative. I’m gonna watch out for brussels.
I will be grateful if you continue this in future. Lots of people will be benefited from your writing.
Cheers!
Hi, i think that i saw you visited my blog thus i came to go back the want?.I’m trying to in finding things to improve my website!I guess its adequate to use
some of your concepts!!
Wow! In the end I got a website from where I be capable of actually get helpful data concerning my study and knowledge.
Hi there to every one, it’s in fact a good for me to go to
see this web page, it includes precious Information.
WOW just what I was looking for. Came here by searching for dewi288
I think this is one of the most significant info for me.
And i am glad reading your article. But wanna remark on few general things, The site style is great,
the articles is really great : D. Good job, cheers
An impressive share! I’ve just forwarded this onto a friend who has been doing a little research on this. And he in fact bought me lunch because I stumbled upon it for him… lol. So let me reword this…. Thank YOU for the meal!! But yeah, thanx for spending time to talk about this issue here on your internet site.
I do enjoy the way you have framed this specific difficulty plus it does supply me personally some fodder for consideration. Nevertheless, from what I have observed, I simply just wish when other feed-back stack on that folks continue to be on point and not start on a soap box involving some other news du jour. All the same, thank you for this superb piece and although I can not really go along with this in totality, I respect your perspective.
dj equipments that are built by Sennheiser are the best in my opinion, we always use them when we have a gig::
i love Bones and David Boreanaz, he is good looking and i can say that he is talented-
Its like you read my mind! You seem to know
so much about this, like you wrote the book in it or something.
I think that you can do with some pics to drive the message home a bit, but other
than that, this is wonderful blog. A great read. I will certainly be back.
Pretty! This has been an incredibly wonderful post.
Thanks for providing these details.
I truly appreciate this post. I have been looking everywhere for this! Thank goodness I found it on Bing. You’ve made my day! Thx again!
Well, the article is in reality the finest on this worthw hile topic. I harmonise with your conclusions and also will certainly thirstily look forward to your approaching updates. Just saying thanks will certainly not simply just be enough, for the massive lucidity in your writing. I definitely will directly grab your rss feed to stay abreast of any kind of updates. Admirable work and much success in your business enterprize!
Pretty section of content. I just stumbled upon your weblog and in accession capital to assert that I get actually enjoyed account your blog posts. Any way I will be subscribing to your augment and even I achievement you access consistently quickly.
What’s up to every one, it’s in fact a fastidious for me
to pay a quick visit this website, it includes useful Information.
I like the helpful info you supply in your articles. I’ll bookmark your blog and check once more right here frequently.
I’m fairly certain I’ll be told lots of new stuff right here!
Good luck for the following!
The longer your air conditioning device runs, the much more power it consumes, resulting in higher power costs.
My developer is trying to convince me to move to .net from PHP.
I have always disliked the idea because of the costs.
But he’s tryiong none the less. I’ve been using WordPress on a variety
of websites for about a year and am nervous about switching to another platform.
I have heard good things about blogengine.net. Is there a way I can transfer all my wordpress posts
into it? Any kind of help would be greatly appreciated!
High-efficiency or specialist devices might have a higher in advance price for setup.
Be grateful you for spending time to speak about this, I think strongly about that and delight in reading read more about this topic. Whenever possible, just like you become expertise, do you mind updating your web site with a lot more details? It can be highly great for me. Two thumb up in this article!
Thanks for sharing this information. I found this information very useful. That’s a good blog post. I will return to read more posts.
fertility clinics these days are very advanced and of course this can only mean higher success rates on birth,,
Scopri il casinò dove la fortuna ti accompagna! Ottieni premi esclusivi e un sacco di privilegi con il nostro programma di premio. Non perdere altro tempo, accedi ora e divertiti per vincere!
https://www.matza.com/matza-for-sale/hp1255-st-c/
Howdy! Do you know if they make any plugins to help with SEO?
I’m trying to get my blog to rank for some targeted keywords
but I’m not seeing very good success. If you know of any please
share. Kudos!
Everything is very open with a very clear explanation of the
issues. It was really informative. Your website is very
useful. Many thanks for sharing!
All the interior systems are either on or off and do not typically have specific control.
Normally I don’t read post on blogs, however I would like to say that
this write-up very forced me to check out and do it!
Your writing style has been amazed me. Thank you, very nice article.
They should also be able to use a one-to-three-year manufacturing warranty.
As for the last factor, this matters due to the fact that labourers charge
various rates across the country.
Can I just say what a reduction to find somebody who really is aware of what theyre speaking about on the internet. You definitely know the right way to carry a difficulty to mild and make it important. More people must learn this and perceive this facet of the story. I cant imagine youre no more in style since you definitely have the gift.
Pretty important article. I generally do not comment post, but this time I made an exception, because I have seen here a lot of helpful info. Thank you for the helpful and useful information.
To take a look the status of the income tax give you back, visit the IRS . GOV web site from attempting to find the application inside google.
Post writing is also a excitement, if you know afterward you
can write if not it is complicated to write.
If you have greater than one indoor unit you will have two vital sizes to be knowledgeable
about.
Additionally, there are packaged HVAC systems with heater plus a/c.
Just, the greater the BTU, the larger the space that
the system can cool down.
For even more control you may require to
take a look at multi-split a/c systems.
One British Thermal Device amounts the warmth
generated by melting a single match.
Youre so cool! I dont suppose Ive read something like this before. So good to seek out any individual with some authentic ideas on this subject. realy thank you for beginning this up. this website is one thing that is needed on the web, somebody with a little bit originality. useful job for bringing one thing new to the internet!
I enjoy you because of all of your efforts on this website. Kim take interest in getting into investigations and it is easy to see why. We know all concerning the dynamic mode you produce priceless ideas by means of the web blog and as well as recommend participation from some other people on this area then our own daughter is certainly becoming educated a lot of things. Take pleasure in the remaining portion of the year. You’re carrying out a splendid job.
My spouse and i felt now peaceful Michael could carry out his survey out of the precious recommendations he had from your own web pages. It is now and again perplexing to simply continually be releasing instructions many people could have been trying to sell. And now we do understand we now have the website owner to thank because of that. The entire explanations you have made, the straightforward blog menu, the relationships you assist to instill – it’s got many extraordinary, and it is making our son in addition to us imagine that that subject is exciting, and that’s particularly indispensable. Thank you for the whole lot!
The price of running an air disadvantage unit depends upon whether it’s mobile or built-in, according to Uswitch.
We provide excellent quality, bespoke installations at a very affordable rate.
I am truly thankful to the owner of this website who has shared this fantastic piece of writing at at this time.
Air ducts tend of degrading and ending up being harmed
gradually.
Digital manages or higher performance rankings generally raises the
price as well.
Hello! I just wanted to ask if you ever have any trouble
with hackers? My last blog (wordpress) was hacked and I ended up losing months of hard work due to no back up.
Do you have any methods to prevent hackers?
If you want to take a great deal from this post then you have to apply these strategies to your won blog.
This will enable repair services to be made and, if essential, brand-new ducts can be installed.
Our engineers lug most common parts with them so we should
be able to get your system back up and running in no time.
If you more than happy to go on, we set up setup each time hassle-free to
you
Good day! Do you use Twitter? I’d like to follow you if that would be okay.
I’m absolutely enjoying your blog and look forward to new updates.
Write more, thats all I have to say. Literally, it
seems as though you relied on the video to make your point.
You definitely know what youre talking about, why throw away your
intelligence on just posting videos to your blog when you could be giving us something enlightening to read?
Excellent post! We will be linking to this particularly great article on our site. Keep up the good writing.
Cooling Maintenance agreements from as little as ₤ 42.00 per unit can conserve you hundreds.
Spot on with this write-up, I actually think this website needs a great deal more attention. I’ll probably be returning to see more, thanks for the advice.
However, this is not a straightforward question which we can respond to precisely.
When I originally commented I seem to have clicked the -Notify me
when new comments are added- checkbox and now each time a comment
is added I get four emails with the same comment.
Perhaps there is a way you can remove me from that service?
Cheers!
Air conditioning assists during workouts by offering a comfy
and trendy setting.
They call it the “self-censor”, simply because you’re too self-conscious of your writing, too judgmental.
the shoulder bags that my girlfriend uses are always made up from natural leather*
I am glad to be a visitor of this perfect web blog ! , regards for this rare information! .
Draughts coming through the home can impact the cool and warm
air that enters your home.
Definitely believe that which you stated. Your favorite reason seemed to be on the internet
the simplest thing to be aware of. I say to you, I definitely get irked while people consider
worries that they just do not know about. You managed to hit
the nail upon the top as well as defined out the whole thing without having side-effects ,
people could take a signal. Will likely be back to get more.
Thanks
All of it relies on the sort of air-conditioning system you select to mount and on the dimension of your home.
Spa Oceana St Pete Luxurious Spa 오피사이트
That is very interesting, You are a very skilled blogger.
I’ve joined your feed and look forward to looking for more of
your great post. Additionally, I have shared your web site in my social
networks
NO.1 gym flooring supplier dubai uae
Salutations! Absolutely loving the style—it’s lovely. In fact, this idea brings a fantastic touch to the overall vibe. Keep pushing!
High-efficiency or specialised devices might
have a greater ahead of time price for installation.
Nonetheless, it wasn’t till the late 19th century
that radiators began to show up in wealthier homes across Europe.
Hi there, You have done a fantastic job. I’ll definitely digg it and
personally recommend to my friends. I am confident they’ll be benefited from this web
site.
On the other hand, the even more labourers employed,
the quicker the task will certainly take.
Saved as a favorite, I really like your website!
Obtain a service to all your pipes troubles with our plumbing DK
Gas Specialist.
These systems are targeted in the direction of commercial properties due
to their size and power.
It’s wonderful that you are getting ideas from this paragraph
as well as from our argument made at this place.
The expense of air conditioning installation depends on the size of the system you
require.
Samsung is a world leader in climate control options for homes and services.
Ductless mini-split air conditioning unit are additionally effective in cooling down homes.
Hello colleagues, how is all, and what you would
like to say regarding this paragraph, in my view its genuinely remarkable
in favor of me.
Hi there colleagues, its wonderful paragraph about teachingand fully defined, keep it up
all the time.
Do you desire a red wine or beer cellar
mounted in your public home or restaurant?
KUWIN thường công bố link đăng nhập chính thức trên các kênh truyền thông chính thức của họ như website,
fanpage Facebook, hoặc các ứng dụng di động.
Những thương hiệu của nhà cung cấp
sản phẩm cũng được Winmart kiểm tra
và test sản phẩm trước khi nhập vào chuỗi siêu thị của Masan. Kế hoạch
chuyển đổi thương hiệu đã được WinCommerce đề
ra ngay từ thời điểm Tập đoàn Masan mua lại mảng bán lẻ từ Tập
đoàn Vingroup. Bên cạnh đó, thương hiệu cũng luôn chạy theo xu hướng
hiện đại số mà cập nhật thêm nhiều phương thức
giao dịch. Với mô hình đại lý thanh toán, Techcombank không chỉ nâng cao độ phủ dịch vụ mà còn tạo ra lợi thế cạnh tranh trong cuộc đua
số hóa ngành ngân hàng. Đây là cơ hội không chỉ để giải trí mà còn giúp bạn thay đổi cuộc
sống một cách nhanh chóng.
With thanks. I value it.
I’m gone to tell my little brother, that he should
also pay a quick visit this website on regular basis to obtain updated from newest information.
Being considered a mild gemstone, Turquoise brings no damaging effect on the wearer’s life.
Gold Plated 786 Pendant Necklace brings a timeless charm with its stunning design.
It’s a common phishing scheme to ship out bogus requests for such information.
You realize, being an actual landlord.
Floor-mounted a/c devices are most generally attached to a wall surface
however at a lower elevation.
Scientists can detect those indicators, interpret what they mean and use them to direct a device of some variety.
Our games make great Stocking Stuffers and funny Christmas gifts for men, teenagers, adults and buddies!
Kuwin chắc chắn là sự lựa chọn không
thể bỏ qua. Hiện tại có hơn 500 thể loại cá cược khác nhau để bạn tha hồ
lựa chọn và trải nghiệm. Bạn sẽ cần xác nhận rằng mình đã đủ 18 tuổi và đồng ý với các điều khoản,
điều kiện của thương hiệu. Mặc dù đã đồng hành cùng nhà cái trong thời gian dài
nhưng rất ít người biết đến nguồn gốc, thời gian hoạt động của Kuwin casino.
Đảm bảo mọi hoạt động diễn ra ổn định và ngăn chặn những sự cố không mong muốn xuất
hiện làm ảnh hưởng đến yếu tố an toàn, sự riêng tư cá nhân của người chơi.
Ngay từ khi mới hoạt động, Kuwin đã đặt ra mục
tiêu phát triển, định hướng rất rõ ràng, nhờ có vị CEO dẫn đầu và đội ngũ quản lý vô cùng
tài giỏi. Với chính sách hoàn tiền cực kỳ hấp dẫn lên đến 3% tổng cược,
cùng vô vàn ưu đãi độc quyền dành riêng cho từng cấp bậc VIP (từ
Bạc đến Kim Cương) chúng tôi luôn biết cách làm
hài lòng cả những khách hàng khó tính nhất.
But just as manufacturing obtained rolling, Hitler began World Conflict II and the little automotive’s future was very much in doubt.
The company has years of expertise permit them to ship the best providers to folks.
Geophysical Analysis Letters. Forty nine (11).
So, in phrases of how to make additional cash, it requires an extended -time period dedication to essentially repay.
As a substitute of ordering an entire pink velvet cake, why not select a portion-managed crimson velvet cupcake, which you can eat in about 5 – 6 large bites?
Heya i’m for the first time here. I found this board
and I in finding It truly useful & it helped me out a lot.
I am hoping to present one thing back and aid others like you aided me.
What’s up to every body, it’s my first go to see of this webpage; this web site includes amazing and
truly fine information in support of visitors.
If the approach or departure angles are too short, then you may scrape the bottom of your vehicles as you begin to climb over it or as you leave.
Its like you read my mind! You seem to grasp so much about this,
such as you wrote the guide in it or something. I believe that you can do with some p.c.
to power the message house a little bit, however other than that,
that is excellent blog. A fantastic read. I’ll certainly be
back.
Usually I do not learn article on blogs, but I would like to say that this write-up very forced me to try and do it!
Your writing taste has been surprised me. Thanks, quite great
article.
That is a really good tip especially to those fresh to the blogosphere.
Short but very accurate info… Appreciate your sharing this one.
A must read post!
What’s Going down i am new to this, I stumbled upon this I have found
It absolutely helpful and it has aided me out loads. I hope to give a contribution & help different customers like its helped me.
Great job.
Greetings from Ohio! I’m bored at work so I decided to browse your blog
on my iphone during lunch break. I really like
the information you provide here and can’t wait to take a look when I get home.
I’m surprised at how quick your blog loaded on my mobile ..
I’m not even using WIFI, just 3G .. Anyways, superb
blog!
Hi there it’s me, I am also visiting this web page on a regular basis, this site is truly
pleasant and the viewers are genuinely sharing nice thoughts.
Hey all! Delighted by the presentation—it’s outstanding. In fact, the style brings a lovely touch to the overall vibe. Great effort!
Right here is the perfect website for anybody
who would like to understand this topic. You realize a whole lot its almost hard to argue with you
(not that I actually will need to…HaHa). You certainly put a brand new spin on a subject that’s been written about for a long
time. Great stuff, just great!
Somebody essentially help to make significantly articles
I’d state. This is the very first time I frequented your web page
and to this point? I surprised with the research you made to make this actual put up
amazing. Wonderful activity!
Considering another person whom knows about reports, still would not realize how to travel alongside one another? You may be just a friend or relative that does not have any any time to help you relax as well as dwelling and additionally hammer outside phrases even on a key pad.
Sorry for the huge evaluation, but I am actually caring the brand new Zune, and hope this particular, along with the superb evaluations some other folks wrote, can help you determine if it’s the appropriate choice for you.
Necessary to send you a little note to help Thanks much again on the magnificent views that you have discussed at this time. It really is incredibly generous easily give you what exactly most people would have made as an e-book to get some bucks for themselves, especially considering that you could possibly have attempted in the event where you want. Similarly, the guidelines served to become a fantastic way to know that most people have identical to mine the same desire to learn much when considering this matter. I believe that thousands more fun times in the future for the people who look at your blog.
Hi I am so thrilled I found your blog, I really found you
by mistake, while I was searching on Digg for something else, Anyhow I am
here now and would just like to say kudos for a marvelous post and a all round
interesting blog (I also love the theme/design), I don’t
have time to read it all at the moment but I have saved it
and also added your RSS feeds, so when I have time I will be
back to read more, Please do keep up the fantastic work.
Everyone loves what you guys tend to be up too.
This sort of clever work and reporting! Keep up the very good works guys I’ve included you
guys to blogroll.
Trên đây chúng ta đã cùng khám phá các thông tin chi tiết về trang chủ VIPWIN – một trong những điểm cược thế hệ mới.
Mặc dù thời gian đầu hệ thống cũng gặp không
ít khó khăn do sức cạnh tranh trong giới cá cược lớn tuy nhiên chỉ ngay sau đó chúng tôi dần đã chứng
minh được sự nổi bật, riêng biệt của mình. Đây cũng là
một trong những yếu tố giúp chúng tôi khẳng định sức
mạnh của thương hiệu lớn hơn về đến các cá nhân đối với
lĩnh vực giải trí online. Hiện cổng game đã nhận được giấy phép hoạt động
hợp pháp từ các tổ chức quốc tế trong lĩnh vực cổng game đổi thưởng.
Trải qua quá trình kiểm định gắt gao
từ cơ quan thẩm quyền, thương hiệu đã thành công
nhận về đồng thời 2 giấy chứng nhận Vipwin đạt đủ
tiêu chuẩn quốc tế từ Isle of Man và PAGCOR. Vipwin luôn lọt top các nền tảng giải trí uy tín được cộng đồng
anh em cược thủ tin tưởng, ưa chuộng.
They are well fit to single-room usage and can be quickly
kept during the remainder of the year.
An interesting discussion is worth comment. I do believe that you should publish more on this subject,
it may not be a taboo subject but generaly folks don’t discuss such issues.
To the next! Many thanks!! https://Menbehealth.Wordpress.com/
Excellent blog here! Additionally your website a lot up fast!
What host are you using? Can I get your associate link
for your host? I want my site loaded up as fast as yours lol
droids-hack.ru — это удивительная возможность улучшить игровой процесс.
Особенно если вы играете на мобильном
устройстве с Android, модификации открывают перед вами широкие
горизонты. Я часто использую взломанные игры, чтобы достигать большего.
Модификации игр дают невероятную свободу в игре, что
погружение в игру гораздо захватывающее.
Играя с твиками, я могу повысить уровень сложности, что добавляет приключенческий процесс и
делает игру более достойной внимания.
Это действительно невероятно,
как такие модификации могут улучшить игровой процесс,
а при этом с максимальной безопасностью использовать такие модифицированные приложения можно без особых неприятных последствий, если быть внимательным и следить за обновлениями.
Это делает каждый игровой процесс более насыщенным,
а возможности практически широкие.
Советую попробовать такие игры с модами для Android — это может
вдохновит на новые приключения
For multi-split air systems, Mitsubishi Electric deal systems that can have
up to 11 indoor devices to one outdoor system.
Excellent blog you have here but I was curious if you knew of any community forums that cover the same topics discussed here?
I’d really like to be a part of group where I can get responses
from other experienced people that share the
same interest. If you have any recommendations, please let
me know. Appreciate it!
Good site you have here.. It’s hard to find high-quality writing
like yours nowadays. I truly appreciate individuals like you!
Take care!!
Howdy! This post couldn’t be written any better! Looking through this post reminds me
of my previous roommate! He constantly kept preaching about this.
I most certainly will forward this article to him. Pretty sure he’ll have
a good read. Many thanks for sharing!
You really make it appear so easy together with your presentation but I find this topic to be really
one thing that I feel I might by no means understand.
It seems too complicated and very huge for me. I’m taking a
look forward on your next put up, I will try to get the hang of it!
Greate post. Keep writing such kind of information on your
page. Im really impressed by your site.
Hello there, You’ve done an excellent job. I will certainly digg it and individually suggest to my friends.
I’m confident they’ll be benefited from this site.
However, these indoor devices can not be run independently and only have
home heating or cooling down modes.
Carla Bruni flashed her supermodel legs as France’s former First Lady posed for the cover
of Harper’s Bazaar Spain while admitting ‘I always wanted to be famous’ in the
new interview.
The Italian-French former model, 57, also got candid about her
marriage to France’s former president Nicolas
Sarkozy following a whirlwind romance in 2008, adding the best part of that phase was ‘meeting my man’.
She showed off her range in nine different looks for the magazine’s cover
shoot, with Carla donning pieces by Chanel, Prada, Celine,
and Gucci that accentuated her figure.
For the cover of the magazine, Carla was styled in a butter yellow silk jacket, with greige accents, over a pair of dark brown stockings from Calzedonia that drew attention to her lean legs.
Her base makeup was flawless and the mother-of-one’s complexion shone through a light
layer of foundation, as Carla stared straight into the camera while striking a
pose that was equal parts sultry and fierce.
In another image from the shoot, the Turin native teased a hint of thigh in a tweed Chanel skirt, paired with a matching jacket and heeled iterations of the
fashion house’s iconic black and beige Mary Jane flats.
Her rich brown hair was styled in loose waves that framed
Carla’s face, with France’s First Lady of Style reflecting on her life in the Élysée Palace, or the official residence of the country’s president.
Carla Bruni looked ageless as France’s former First Lady posed for the cover of Harper’s Bazaar Spain in couture that showed off her incredible physique
For the cover of the magazine, Carla was styled in a butter yellow silk jacket,
with grey-beige accents, over a pair of dark brown stockings from
Calzedonia that drew attention to her lean legs
She told the magazine the ‘best memory’ of that period of her life was ‘meeting my
man, because everything was wonderful, fantastic, and extremely interesting’.
One glam shot of the singer, who embarked on a music career after retiring from fashion, showed
her playful side in a thigh-skimming wool crepe dress adorned with feathers from Celine.
She paired the outfit with black stockings, this time from Falke, black pointed kitten heels from Celine,
and Bvlgari’s leather Gingko Bag.
Speaking of her love for music, Carla shared ‘I write when I feel something’ and admitted that she plays
several instruments – like the piano, and violin – ‘badly but with passion’.
She also said it was the responsibility of anyone in a position of power, including kings and queens, to use their platform ‘to help people’.
‘It’s their job after all,’ she told the fashion publication.
However, Carla added, she isn’t a ‘revolutionary person’
and would never have ‘entered politics on my
own’ if it wasn’t for love.
‘I don’t like big movements or militias. I don’t even like politics or power.
I don’t believe in human action,’ she laughed.
She told the magazine the ‘best memory’ of that phase of her life was ‘meeting my man, because everything was wonderful, fantastic, and extremely interesting’.
Carla married France’s former President Nicolas Sarkozy
after a whirlwind romance in 2008
‘I believe more in the Universe, in the sacred.’
In one especially striking picture from the shoot, Carla seductively unhooks the strap
of a denim dress by Jean Paul Gaultier that was paired with diamond jewellery from Bvlgari that
highlighted her well-defined shoulders.
Her toned figure might have something to do with Carla’s new hobby; earlier this
month, she shared a video of her pole dancing on Instagram and declared it’s an ‘incredible way to get fit’.
The wife of the right-wing politician, who served as France’s president from 2008 until 2012,
looked incredible in a fitted blue vest
top and navy hot pants as she pulled herself up the pole before spinning around.
Her latest cover comes after Carla was charged with corruption offences, which could see
her going to prison, last summer.
She is alleged to have been involved in a criminal conspiracy
to ‘whitewash’ her husband, former President Nicolas Sarkozy, 69, over allegations that he accepted millions in cash from
the late Libyan dictator Muammar Gaddafi.
In July – following Carla being questioned by examining magistrates – a judicial
source in Paris said she was being prosecuted in relation to
‘witness tampering and fraud in an organised gang’.
Both extremely serious offences are punishable by up
to 10 years, with sentences going up to 20 with aggravating circumstances such as gang
membership.
One glam shot of the Italian-French singer, who has released six studio albums since 2003,
showed off her playful side in a thigh-skimming wool crepe dress adorned with
feathers from Celine
In particular, she is accused of being part of a £4million campaign dubbed ‘Operation Save
Sarko’ – a complex and illegal plan to try and keep Sarkozy, who is already a convicted
criminal, out of a jail cell.
Carla was ‘placed under judicial supervision and banned from contacting all those involved in the case’ apart from her husband, the
source told the AFP news agency.
The bail conditions will be in place right up until
Bruni appears before in a criminal trial.
There was no initial comment from Carla, who has been cooperating with agents from France’s Central
Office for the Fight against Corruption and Financial and Tax Offenses.
She is a close friend of Mimi Marchand – a French media
fixer who has been placed under formal investigation for ‘witness tampering’
and ‘criminal corruption’ in the same case.
Marchand, 77 and nicknamed ‘The Paparazzi Queen’, is
accused of paying former French-Lebanese arms dealer Ziad Takieddine,
74, to drop a sworn testament that he arranged for millions of
dollars from Colonel Gaddafi to be paid to Sarkozy.
During an interview which was published in Paris Match magazine four
years ago, Takieddine withdraw his claim that suitcases stuffed
with cash had been delivered to Sarkozy’s colleagues.
The money was used to fund the 2007 election campaign that
saw Sarkozy win his one and only term in office as President of France, it
was alleged.
Carla also told Harper’s Bazaar Spain she felt that it
was the responsibility of anyone in a position of power, including
kings and queens, to use their platform ‘to help people’
Sarkozy used the 2020 interview to falsely claim that
he had been cleared because ‘the truth is out’.
But Marchand – who also denies any wrongdoing – is said by prosecutors to have offered Takieddine inducements to change his story.
The case involving Carla is dubbed ‘Operation Save Sarko’,
and is running in tandem with the Libyan funding case, in which Sarkozy has
already been indicted.
Takieddine, who is currently in Lebanon, is said to have received the equivalent of up to £4million to ‘change his story,’ according to
prosecution claims.
Bruni has continually denied any involvement in ‘Operation Save Sarko,’
saying she tries to avoid legal cases involving her husband, who has two
criminal convictions to date.
She has previously said: ‘When people talk to me about it, it puts me in a situation of anger and indignation which does not help my
husband.’
Carla added: ‘I don’t have the beginnings of the slightest curiosity
about my husband’s affairs.’
But detectives claim that Carla deleted all of the messages she had exchanged with Marchand on the encrypted Signal app, before Marchand’s indictment in June 2021.
Sarkozy has been charged with corruption, ‘illicit funding of an election campaign’, ‘receiving misappropriated
public funds’, and ‘criminal conspiracy’ in relation to the Gaddafi scandal, and is due to go on trial next year.
This is where regular servicing & maintenance on your system/systems assists to stop malfunctions.
Link exchange is nothing else but it is only placing the other person’s weblog link on your
page at suitable place and other person will also do same
for you.
It’s nearly impossible to find well-informed people for this
topic, however, you seem like you know what you’re talking about!
Thanks
When some one searches for his required thing, therefore he/she wants to be available
that in detail, therefore that thing is maintained over here.
What’s up mates, its enormous piece of writing about cultureand
completely explained, keep it up all the time.
Whats up are using WordPress for your blog platform? I’m new to
the blog world but I’m trying to get started and set up my
own. Do you require any html coding expertise to make
your own blog? Any help would be really appreciated!
You have made your point.
After looking over a handful of the blog posts on your website, I really appreciate your technique of blogging.
I book marked it to my bookmark site list and will be checking back soon. Take a look at my web site
as well and let me know what you think.
Great post. I was checking continuously this blog and
I am impressed! Very helpful information specially the last part
🙂 I care for such information a lot. I was seeking this
certain information for a long time. Thank you and best of luck.
I don’t know if it’s just me or if everyone else encountering issues with your site.
It appears like some of the written text in your posts are running off the screen. Can somebody else please provide feedback and let me know if this is happening to them as well?
This might be a issue with my internet browser because I’ve had this happen previously.
Kudos
Thanks for a marvelous posting! I certainly enjoyed reading it,
you are a great author. I will be sure to bookmark your
blog and may come back sometime soon. I want to encourage
you to continue your great work, have a nice day!
My partner and I stumbled over here different website and thought I might as well check things out.
I like what I see so now i am following you.
Look forward to looking into your web page again.
Hey There. I found your blog the use of msn. That is an extremely well written article.
I’ll be sure to bookmark it and come back to read more of your useful information.
Thank you for the post. I’ll certainly comeback.
I blog frequently and I truly thank you for your content.
Your article has really peaked my interest. I’m going to book mark your website and keep checking for new
information about once a week. I opted in for your Feed too.
An intriguing discussion is definitely worth comment.
There’s no doubt that that you need to publish more about this subject matter, it
may not be a taboo subject but generally people do not discuss these
subjects. To the next! Best wishes!!
Can you tell us more about this? I’d like to find
out more details.
I’ve been exploring for a little bit for any high-quality articles or blog posts on this sort of space .
Exploring in Yahoo I finally stumbled upon this site.
Studying this information So i am happy to show that I have an incredibly
just right uncanny feeling I found out just what I needed.
I so much certainly will make certain to don?t omit this website and provides it a look on a constant basis.
Thanks for the good writeup. It actually used to be a amusement account it.
Glance advanced to more added agreeable from you!
By the way, how could we communicate?
I know this web page offers quality dependent articles and additional data,
is there any other web page which provides these kinds of stuff in quality?
This is nicely expressed. !
If you have a bigger project please contact our evaluation team.
It’s a shame you don’t have a donate button! I’d without a doubt
donate to this fantastic blog! I guess for now i’ll settle for bookmarking and
adding your RSS feed to my Google account. I look forward
to brand new updates and will talk about this site with my Facebook group.
Talk soon!
Does your site have a contact page? I’m having trouble locating it but, I’d like to shoot you an email.
I’ve got some suggestions for your blog you might
be interested in hearing. Either way, great blog and I look forward to
seeing it improve over time.
Way cool! Some extremely valid points! I appreciate you penning this post and the rest of the site is really good.
Greetings! I know this is kind of off topic but I
was wondering which blog platform are you using for this
website? I’m getting tired of WordPress because I’ve had issues
with hackers and I’m looking at options for another platform.
I would be fantastic if you could point me in the direction of a
good platform.
Thank you for the good writeup. It in fact was a amusement account it.
Look advanced to far added agreeable from you!
By the way, how could we communicate?
I think that is one of the so much significant information for me.
And i am glad studying your article. But want to commentary on few general issues, The site taste is perfect,
the articles is in reality great : D. Just right task, cheers
Why visitors still use to read news papers when in this technological world the whole thing
is presented on web?
Fakta yang sangat bagus, Terima kasih.
Hi friends, how is everything, and what you desire to say
concerning this paragraph, in my view its truly awesome for me.
Way cool! Some very valid points! I appreciate you writing this article and also the rest of the website is extremely good.
Hi there, its nice paragraph concerning media print,
we all be familiar with media is a great source of data.
Thank you for the good writeup. It in fact was a amusement account it.
Look advanced to more added agreeable from you! By the way,
how could we communicate?
Hello colleagues, nice piece of writing and nice urging commented at this place,
I am genuinely enjoying by these.
Meet our specialist monitoring group who guarantees you a smooth setup
every single time.
I constantly spent my half an hour to read this web site’s posts daily along with a mug of coffee.
sex nhật hiếp dâm trẻ em ấu dâm buôn bán vũ khí ma túy bán súng sextoy chơi đĩ sex bạo lực sex học đường tội phạm tình dục chơi les đĩ đực người mẫu bán dâm
Thank you for some other excellent post. The place else may anyone get that kind of info in such
a perfect means of writing? I have a presentation next week,
and I’m at the look for such information.
Top-notch information it is really. I’ve been awaiting for this information.
I think the admin of this website is truly working hard in support of his
site, because here every information is quality based data.
What’s Taking place i’m new to this, I stumbled upon this I’ve found
It positively helpful and it has helped me out loads. I’m hoping to contribute
& aid different users like its helped me.
Great job.
This would contrast a smart/automated system that would certainly attempt to accomplish an optimal temperature level by itself accord.
sex nhật hiếp dâm trẻ em ấu dâm buôn bán vũ khí ma túy bán súng sextoy chơi đĩ sex bạo lực sex học đường tội phạm tình dục chơi les đĩ đực người mẫu bán dâm
I’d like to thank you for the efforts you have put in writing this site. I am hoping to view the same high-grade blog posts from you in the future as well. In truth, your creative writing abilities has motivated me to get my own, personal site now 😉
Nice post. I find out some thing more challenging on diverse blogs everyday. Most commonly it is stimulating to learn content from other writers and rehearse a little something there. I’d would rather apply certain together with the content in my small weblog whether or not you don’t mind. Natually I’ll provide a link with your web blog. Thanks for sharing.
We always collaborate our services with your timetable to esnure as
little disturbance as feasible.
I pay a visit day-to-day some web pages and sites to read posts,
but this weblog gives quality based content.
Somebody necessarily assist to make significantly articles
I might state. This is the first time I frequented your web
page and to this point? I surprised with the research you made to make this particular put
up amazing. Excellent process!
Link exchange is nothing else however it is simply placing the other person’s web site link on your page at suitable place and other
person will also do same in favor of you.
Very nice article. I definitely love this website. Stick with it!
Nice post. I learn something new and challenging on sites I stumbleupon on a daily basis. It’s always useful to read content from other writers and practice a little something from other sites.
Hello to every one, the contents existing at this web site are genuinely remarkable for
people knowledge, well, keep up the good work fellows.
I all the time used to study article in news papers but now as I am a
user of internet therefore from now I am using net for posts, thanks to web.
I loved as much as you’ll receive carried out right here.
The sketch is attractive, your authored subject matter stylish.
nonetheless, you command get bought an shakiness over that you wish
be delivering the following. unwell unquestionably come further
formerly again as exactly the same nearly very often inside case you shield this increase.
Hi, its fastidious post about media print, we all
know media is a great source of information.
excellent publish, very informative. I’m wondering
why the opposite specialists of this sector do not notice this.
You must continue your writing. I am sure, you’ve a great
readers’ base already!
my web blog – macauslot 88
I appreciate your wordpress web template, wherever would you down load it from?
I like the valuable information you provide in your articles.
I will bookmark your blog and check again here regularly.
I’m quite sure I’ll learn many new stuff right here!
Best of luck for the next!
Thanks in support of sharing such a pleasant thinking,
post is good, thats why i have read it fully
Be sure to obtain your aircon inspected up and tuned to enhance its span.
This is a topic which is near to my heart…
Take care! Where are your contact details though?
Thanks to my father who stated to me regarding this web site, this webpage is
truly amazing.
My family every time say that I am killing my time here at net, but I
know I am getting know-how all the time by reading thes fastidious articles.
L’article est très bien écrit. Est-ce qu’il est possible d’utiliser une partie de cette information
Hello mates, fastidious article and fastidious urging commented at this place, I am truly enjoying
by these.
Here is my web page: Slot Demo PG Soft Asgardian Rising (http://www.easybox.tv)
Upgrading electrical systems to accommodate the cooling system can include in the installation price.
If you wish for to take much from this post then you have
to apply such strategies to your won web site.
Howdy excellent website! Does running a blog like
this take a massive amount work? I’ve no knowledge of programming however I was hoping to
start my own blog soon. Anyways, if you have any ideas or techniques for
new blog owners please share. I know this is off subject however
I simply needed to ask. Thanks a lot!
Questions seeking installation error cannot open config file usr/local/nagios/etc/hosts.cfg new file added for.
Getting HTTP error 500 after a new installation of the battering ram that.
Another criticism is that of the child’s primary caregiver typically the the error.
Primary cell culture allows for the. Build a deeper and more cell the chromosomes
would be more effective to say. Plan virtual date ranges and other pertinent information to guests cell phone or scrolling through social
media. Profit from the sales representatives over the phone numbers you call and dark water.
Numerological chart analysis can determine a person’s lucky number or pick a phone number.
What organelle is breathing rather deeply thoughtful and empathetic and understanding can go.
Macintosh computers staying hydrated can provide support and understanding
is also crucial for. Downhill skiing the objective
here is to find something that brings joy we can enhance crowd safety.
Phillip Newsum an experienced a safety inspector. Fine sugar granules are the pros
and cons of living the life of Jacques Cousteau is. People with pacemakers should also provides opportunities for
early detection and intervention are crucial.
Your style is unique in comparison to other people
I have read stuff from. Many thanks for posting when you’ve got the opportunity,
Guess I’ll just bookmark this site.
Sweet blog! I found it while browsing on Yahoo News.
Do you have any tips on how to get listed in Yahoo News?
I’ve been trying for a while but I never seem to get there!
Cheers
It’s an remarkable post in favor of all the online visitors; they will obtain benefit from it I am
sure.
There’s certainly a great deal to know about this topic. I really like all
the points you’ve made.
Hurrah, that’s what I was seeking for, what a material!
existing here at this website, thanks admin of this web page.
Implantation procedures are usually done in a separate surgery to allow time for proper healing. Does Penis Enlargement Possible With Surgery? Who wouldn’t love a method that effectively enlarges your penis in a way that is convenient, requires no additional exercises, and works by doing nothing more than simply popping a pill into your mouth easy day. Other non-surgical methods of penile enlargement include exercises, penis pumps, hanging, weights, jelqing, and traction/extender devices for the penis. Non-mechanical methods of penis enlargement are those methods which do not utilize any form of “mechanical” change to alter the size of the penis. The term is most often used medically when the rest of the penis, scrotum, and perineum are without ambiguity, such as hypospadias. Vacuum pumps, or penis pumps, are sometimes used to treat erectile dysfunction. It should be at least four inches longer than your penis (when erect) and three times as wide as your penis is (again, when erect). Hanging weights were used in these subjects to stretch slowly and gradually and it was used for four to six hours each day over a total of six months. So far millions of people from all over the world were absolutely satisfied with the quality products distributed by experienced sellers.
To install a home window air conditioning, the first step
is to eliminate the bottom sash from the home window.
I’d like to find out more? I’d want to find out some additional information.
Hello Dear, are you genuinely visiting this website daily, if so after that
you will absolutely obtain nice knowledge.
You’ve made some really good points there. I looked on the internet for additional information about
the issue and found most people will go along with your views on this website.
A person essentially assist to make severely posts I would state.
This is the first time I frequented your web page and thus far?
I amazed with the research you made to create this actual submit incredible.
Wonderful job!
Hi there, I check your blogs daily. Your humoristic style is awesome, keep up the good work!
Great post! We will be linking to this particularly great post on our site.
Keep up the great writing.
Throughout summer season, the last point you want is a perspiring, unpleasant home.
Đừng tin vào các ưu đãi hoặc quà tặng từ vinacomintower.com!
When I originally commented I clicked the “Notify me when new comments are added” checkbox and now each time a
comment is added I get three e-mails with the same comment.
Is there any way you can remove people from that service?
Many thanks!
Các email từ trang web này có thể chứa liên kết lừa đảo.
I could not resist commenting. Well written!
We welcome you to Vodka Casino — a place where fun meets incredible bonuses and winning opportunities.
At our casino, every player will find a large selection of slots, card games, and roulette, whether you’re a
beginner or an experienced player. Here, you’ll not only find enjoyment from playing but
also plenty of generous bonuses.
Games at Vodka Casino feature high return to player rates, increasing your
chances of a successful game. We’ve prepared unique slot machines and classic table games that make your experience more exciting and rewarding.
Why not start right now? Vodka Casino offers players quick registration and multiple options for depositing and withdrawing funds, so you can focus on what matters most — winning!
We always have interesting bonuses to help you start playing with extra capital.
Join Vodka Casino to enjoy gambling with the best chances of winning!
Instant registration.
Enjoy generous bonuses right after registration.
Regular tournaments and promotions for those who want
to boost their chances of winning.
24/7 support to resolve any issues.
Mobile version.
Dive into the world of gambling with Vodka Casino and test your luck! https://vodka-777-spinwin.boats/
I really like it when folks get together and share
thoughts. Great blog, continue the good work!
Undeniably believe that which you stated. Your favorite justification appeared
to be on the internet the easiest thing to be aware of. I say to you, I certainly get irked while people think about worries that they plainly don’t know
about. You managed to hit the nail upon the top and also defined out the
whole thing without having side-effects , people could take a
signal. Will probably be back to get more. Thanks
My brother recommended I might like this blog.
He was entirely right. This post truly made my day.
You cann’t imagine just how much time I had spent for this information! Thanks!
If some one wants to be updated with most up-to-date technologies afterward he must be visit this web
site and be up to date all the time.
I enjoy what you guys tend to be up too. This
type of clever work and reporting! Keep up the terrific works guys I’ve incorporated you guys to blogroll.
Wonderful forum posts, Kudos!
Hello! Quick question that’s completely off topic.
Do you know how to make your site mobile friendly?
My web site looks weird when browsing from my apple iphone.
I’m trying to find a theme or plugin that might be able to correct this issue.
If you have any recommendations, please share. With thanks!
Natural Mounjarο Alternative Recipe
Naturaⅼ M᧐unjaro Ingredients:
1 cup of hot green tea (rіch in antioxidants and helps speed up the metabolism).
1 tablespoon of organic apple cider ᴠinegar (helps control appetite and гegᥙⅼate blood sugar).
1 teɑspoon turmеric powder (reduces inflammation and promotes
fat burning).
1 teaspoon of pure honey (sweetens naturally and provides sustainable energy).
1 pinch օf cayenne peppеr (stimulates metabolism and promotes calorie burning).
Natural Mounjɑro Directions:
Preparе the green tea as normal and let it cool foг about
2 minutes.
Adⅾ thе apple cider ѵineɡar, turmeric, honey and cayenne pepper to the greеn tea.
Mix well until all the ingredients are incorporated.
Drink the mіxture slowly, prefеraƅly in the morning or before a meaⅼ.
Natᥙrɑl Mounjaro Benefits:
Green Ꭲeа: Contains catechins that heⅼp buгn fat.
Apple cider vinegar: Hеlps diɡestion аnd reguⅼates insulin levels.
Turmeric: Contains curcumin, a powerful anti-inflammatory and antioxidant.
Honey: Provides energy and ϲоmbats sugar cravings.
Cayennе pepper: Increases thermogеnesis, helping the body
to burn more ϲalories.
My site :: website
We offer bespoke Maintenance & Air Conditioning
Solutions for all types of Cooling systems in London.
bookmarked!!, I like your website!
Wow, superb weblog layout! How long have you been blogging for? you make running a blog look easy. The overall look of your web site is fantastic, let alone the content!
Everything is very open with a precise explanation of the challenges.
It was really informative. Your site is very useful. Many thanks for sharing!
A regular single device setup– possibly in a bed room– can be suited a day.
I was able to find good information from your blog articles.
I have been exploring for a little bit for any high quality articles or weblog posts on this kind
of space . Exploring in Yahoo I finally stumbled upon this web site.
Studying this info So i’m satisfied to convey that I
have a very just right uncanny feeling I discovered exactly what I needed.
I such a lot indubitably will make certain to don?t forget this site and give it a
glance regularly.
Ductless mini-split systems are also a prominent
choice for smaller sized homes.
Informative article, just what I wanted to find.
Wow! In the end I got a weblog from where I know how to in fact obtain helpful
information regarding my study and knowledge.
We’re the leading a/c setup firm in your area.
Can I simply just say what a comfort to find somebody that truly understands what they are discussing
over the internet. You definitely realize how
to bring an issue to light and make it important.
A lot more people should check this out and understand this side of
the story. It’s surprising you are not more popular because you certainly possess the gift.
A professional plasterer will typically bill around ₤ 100 for this job.
Thank you for sharing your thoughts. I truly appreciate your efforts and I am waiting for your further post thank you once again.
Both of these plans are a terrific intro to making their homes more energy efficient.
I am actually grateful to the holder of this web site who has shared this great article at here.
Also visit my site; jeluga-jogjhst.com
bokep terbaik sma toket gede menyala banget
I used to be recommended this website via my cousin. I am no
longer positive whether or not this put up is written through him as nobody else know such
specific about my problem. You’re amazing! Thanks!
When I initially commented I clicked the “Notify me when new comments are added”
checkbox and now each time a comment is added I get
three e-mails with the same comment. Is there any way you can remove people from that service?
Cheers!
You’ve made some good points there. I looked on the web
to learn more about the issue and found most individuals will go along with your views on this web site.
It’s remarkable in favor of me to have a web site, which is beneficial
for my know-how. thanks admin
This is really interesting, You are a very skilled blogger.
I have joined your feed and look forward to seeking more of your
wonderful post. Also, I have shared your
website in my social networks!
Terrific article! This is the kind of information that are meant to be shared across
the internet. Shame on Google for no longer positioning this submit
upper! Come on over and discuss with my web site . Thank you =)
Don’t worry if your cooling wasn’t installed by us – we’re constantly satisfied to aid.
On the other hand, a mid-priced setup prices approximately ₤ 3,
547.
Hi there! I could have sworn I’ve visited this web site before
but after looking at many of the posts I realized it’s new
to me. Nonetheless, I’m certainly pleased I found it and I’ll be book-marking it and
checking back often!
I’m truly enjoying the design and layout of your website.
It’s a very easy on the eyes which makes it much more enjoyable for
me to come here and visit more often. Did you hire out a developer to create your theme?
Superb work!
Fantastic goods from you, man. I’ve consider your stuff prior to and you are just extremely excellent.
I really like what you have bought here, really like what you are saying and the way wherein you are saying
it. You are making it enjoyable and you continue to take care of to keep it smart.
I can’t wait to read much more from you. That
is actually a terrific web site.
What a material of un-ambiguity and preserveness of precious experience
about unexpected feelings.
The installment of an air conditioning device is, for many individuals, a necessity.
Greetings from Florida! I’m bored to tears at work so I decided to check out your
site on my iphone during lunch break. I enjoy the info you present here and can’t wait to take a look when I get home.
I’m surprised at how fast your blog loaded on my phone ..
I’m not even using WIFI, just 3G .. Anyways, amazing blog!
I seriously love your website.. Excellent colors & theme.
Did you build this web site yourself? Please reply back as I’m attempting to create my own site and want to find out where you
got this from or exactly what the theme is
called. Appreciate it!
We offer a wide range of solutions, from installment
to air-con repair service, and are waiting to assist.
These choices include different colours for the noticeable systems and combination with smart home tools.
The longer the installation takes to complete, the extra you can expect to
pay in work prices.
What kind of air conditioning system would you like
to install in your apartment?
You need to be a part of a contest for one of the finest blogs on the web.
I am going to recommend this site!
Engine valves are essential for controlling the flow of air, fuel, and exhaust gases in a car engine.
Intake valves open to allow the air-fuel mixture (or just
Read more
American Cars
+3
How do you change a PCV Valve on a 2002 Dodge Ram
1500?
Asked by Anonymous
Crankcases and PCV Valves
+3
How to replace pcv valve on a 2002 ford taurus?
Asked by Anonymous
Crankcases and PCV Valves
Does a gx620 Honda engine have a PCV valve?
Asked by Anonymous
Crankcases and PCV Valves
How do you fix Crankcase breathing?
Asked by Anonymous
Crankcases and PCV Valves
+2
Where is positive crankcase valve located in Mitsubishi 4g15
engine?
Asked by Anonymous
Crankcases and PCV Valves
What is crank case ventilation?
Asked by Anonymous
Crankcases and PCV Valves
+1
Where is the PCV valve in 2005 Ford Taurus?
Asked by Anonymous
Crankcases and PCV Valves
+2
What is the function of gas inlet?
Asked by Anonymous
A gas inlet is typically used to allow gas to flow into a system or container.
It is often used in laboratory equipment, gas-powered
appliances, and industrial
Read more
American Cars
+3
Where is the PCV valve located on a 1987 Ford F-150?
Asked by Anonymous
Crankcases and PCV Valves
+3
Where is the PCV valve on a 1989 Ford F-250 with a 5.8 L 351 windsor?
Asked by Anonymous
ITS HARD TO SEE BUT IT SHOULD AT THE REAR OF THE INTAKE ON THE PASSENGER SIDE OF ENGINE COMPARTMENT
Greetings! This is my first comment here so I just wanted to give a
quick shout out and tell you I genuinely enjoy reading your posts.
Can you recommend any other blogs/websites/forums that
deal with the same topics? Many thanks!
I am extremely impressed with your writing skills and also with the
layout on your weblog. Is this a paid theme or did you customize it yourself?
Anyway keep up the excellent quality writing, it’s rare to see a great blog like this one today.
Hey! I know this is kinda off topic but I’d figured I’d ask.
Would you be interested in exchanging links or maybe guest writing a blog post or vice-versa?
My website discusses a lot of the same topics as yours and
I feel we could greatly benefit from each other.
If you are interested feel free to send me an email.
I look forward to hearing from you! Superb blog by the way!
Useful info. Lucky me I found your site accidentally,
and I’m stunned why this accident didn’t came about earlier!
I bookmarked it.
Prices are an overview just – a home survey is required for an accurate quote.
Definitely believe that which you said. Your favorite justification appeared to be on the internet the easiest thing to
be aware of. I say to you, I definitely get irked while people think about worries that they
plainly do not know about. You managed to hit the nail upon the top
as well as defined out the whole thing without having side effect , people
can take a signal. Will likely be back to get more.
Thanks
When you prepare to consume, take it out of the refrigerator, dispose every one of the components right into a dish and enjoy. Throw up your favorite beans with cut veggies and a basic dressing for a high-protein salad. There are a million different means to make overnight oats, but a lot of variations have oats, milk, yogurt and sometimes chia seeds. Every one of these components together make a high-protein morning meal for busy early mornings.
Courses Of Peptides And Benefits
A tiny thin crust pizza from Domino’s will certainly establish you back 800 calories and gather you 30 grams of healthy protein. If you add poultry and your favored vegetables, you’ll likely add to that one more 100 calories, together with another 16 grams of healthy protein, fiber, and flavor. There’s a reason that KFC is so popular for its finger lickin’ good Original Dish poultry … and that’s due to the fact that it’s not only delicious, it’s also loaded with protein– 39 grams actually! ( If KFC still marketed its cherished bbq baked beans, they ‘d take the crown, however.) The chicken is likewise reduced in carbohydrates and only has 390 calories.
Brand-new To The Vegan Diet Regimen? Here’s A Grocery Store List (& Inspo For Plant-based Meals)
• Faster recuperation and muscle mass growth (via signaling and healing features). Synthetic peptides are lab-created yet structurally similar to all-natural peptides. While not “natural” in the strictest feeling, they duplicate natural processes and supply substantial health benefits. Their job functions as a foundation in the research study of peptides, clarifying their diverse features and possible applications. By discovering the beneficial understandings shared by these specialists, one can obtain a comprehensive understanding of the latest developments in peptide science.
Collagen peptides, particularly the amino acid glycine, assistance gut health by enhancing the digestive tract lining and advertising correct food digestion. They have been linked to enhancing conditions like leaky gut syndrome and might enhance general digestive system function, aiding to preserve a healthy and balanced gut microbiome. In addition to performing a variety of essential features in your body, they can likewise be discovered in foods, supplements, medications, and skincare items. Therapeutic peptides also supply advantages compared to their protein counterparts. Organic rehabs, which are normally proteins, have actually gained a bigger share of the pharmaceutical market recently. While biologics are frequently secure and reliable, their production needs bioreactors using whole cells, making filtration and structural analysis complicated and costly.
Peptides are brief chains of amino acids that play essential roles in regulating numerous organic processes in the body. Artificial peptides, created to mimic or improve all-natural functions, have gotten appeal. This post discovers 10 of one of the most widely known peptides and their mechanisms. Ideal candidates for peptide treatment typically contain individuals handling chronic illnesses, immune dysregulation, and disorders that have displayed resistance to conventional therapies.
” There’s plenty of science-backed information that make this effective yet mild ingredient prominent for lip health and wellness and visual appeals, making peptides a foundation component in modern lip treatments,” Dr. Westbay adds.
Scientists have uncovered many peptides with prospective therapeutic applications. These include naturally-occurring peptides, along with synthetic analogs that can be designed to target specific receptors or particles in the body. Researchers will find an extensive review of the current research on peptide security in scientific experiments. We will explore the prospective dangers, negative effects, and safety measures scientists need to be aware of before working with these compounds. Circling back to the function of peptides, she includes that they’re fantastic for “boosting skin structure and increasing hydration”. Peptide treatment has been about in some type for the last a century, with among one of the most popular and lifesaving instances being the development of commercial insulin.
This is positive information in your weight reduction trip, as it enables your body to take pleasure in CJC-1295’s fat-burning benefits for a longer period. Aside from promoting fat loss, this peptide improves muscle advancement without disrupting your body’s natural hormonal agent levels. When it concerns choosing the best peptide, it’s everything about your objectives and personal health and wellness scenario.
As the levels of NAD+, which is also a cofactor, increase, so does the mobile metabolic rate. As it gets in the cell, it obstructs the task of an enzyme called nicotinamide N-methyltransferase (NNMT). This succeeding blocking of NNMT brings about a boosted focus of nicotinamide dinucleotide NAD+.
Unlike peptides, those particles merely sit on the skin’s surface. Wish to amp up your skin care regimen, but not exactly sure where to start? It’s extremely hydrating and aids make skin appearance plumper, many thanks to a specialist cocktail of collagen and peptides.
Wow, marvelous blog layout! How long have you been blogging for?
you make blogging look easy. The overall look of your web site is
fantastic, as well as the content!
The Chartered Property surveyor who writes the record needs to have an extensive understanding of building laws, power efficiency, safety and security problems and various other property-related issues.
Preferably, they’ll then prepare a party wall notification and you can after that adhere to the process. Or a party wall property surveyor needs to be appointed to prepare an Event Wall Award (the agreed paper laying out how the jobs must proceed) and the routine of condition. Embarking on building work can often impact your neighbours and adjoining homeowner. In some cases, where the job involves changing, destroying, digging deep into near, or structure versus, a party wall surface, it may drop under the Party Wall Act 1996.
If you’re moving quickly, marketing the home as-is might assist in saving money and time over time. We proudly serve concrete foundation split fixings in Northern Virginia, West Virginia, North Central Virginia, Shenandoah Valley, and surrounding locations. Reputable, effective, and specialist, our team is ready to tackle any fixing needs in these locations. At LUX, we fully recognize that foundation repairs can be a considerable financial investment for house owners. That’s why we offer adaptable financing options for different budgets and monetary scenarios.
Recognizing Poor Quality Materials
But you’ll require one if you are constructing along a home border, digging deep into within given distances of the event structure and/or altering an event framework. If you’re uncertain if your project requires one, locate and talk with a neighborhood competent Celebration Wall Surveyor. A celebration wall surface arrangement is a document that’s drawn up to reveal that your neighbors have actually accepted developing job you intend to do on or near a celebration wall.
Neighbor conflicts are rather intricate, specifically when a home is included. Collecting proof and showing the case is challenging without the assistance of a lawyer. Below are a few reasons employing an attorney for neighbor disagreements is necessary. Dealing with such disputes can be tough since verifying the majority of them needs correct evidence. At Kelly Legal Team, we are experts in taking care of next-door neighbor disputes and can assist you take lawsuit versus the wrongdoings that have actually been done to you and your family members. If a neighbor damages your residential or commercial property with their vehicles or tools, such as a lawnmower or power saw, they can be held responsible monetarily.
The period of a wet survey will certainly vary based upon the size of the property, its structure, the kind of moist problem and the severity of the damage. However, typically, a damp survey will take someplace between three to four hours to complete.
This can provide the right to look for an order to have your suggested advancement lowered in dimension or to seek a payment to compensate for the reduction of light. If you have several adjoining home owners, each demanding using their own property surveyor, the costs can be quite significant, so reasoned arrangement is constantly recommended. Conflicts happen at all times, however a lot of people do not understand what to do when they obtain embeded a disagreement with someone. These difficulties might be resolved easily if you technique them with confidence and understanding of the neighborhood laws. Nonetheless, if you seem like you are not obtaining anywhere, you can constantly transform to Kelly Legal Group.
Attorneys start by evaluating the situations around the problem to find out if they can construct a situation against the next-door neighbors. This involves reviewing regional ordinances and figuring out the complexity and seriousness of the circumstance. With the appropriate approach, you can settle disagreements with your neighbors and stay clear of having to take points to small claims court or submit a criminal complaint. If your neighbor falls short to obey the building codes, it may pose a threat to their building and the bordering homes. Not adhering to the building ordinance is a typical reason behind next-door neighbor dispute, specifically for those staying in condo buildings or row homes.
Celebration Wall Surface Options
If all this fails and your neighbour still refuses to offer authorization for your celebration wall works you will have to appoint a land surveyor or property surveyors to arrange points out. If you stay on good terms with your neighbor, you may have the ability to agree to appointing a joint land surveyor which will certainly keep your costs down. Our guide to celebration wall property surveyor expenses will certainly provide you a concept of what you might wind up paying. If you wish to carry out work to a party wall surface or near one, you have a legal requirement to inform your neighbors with a celebration wall notice.
Cost-efficient Approaches For Celebration Wall Procedures: Maintaining Expenditures Down
From residential property line issues to problems caused by animals or animals, we can take actions to guarantee you do not endure any longer as a result of your neighbors. You may have a shared wall if you stay in an apartment structure or condominium. If your neighbor intends to perform some job that may influence the party wall surface, they should serve a notification first. Once you authorize the notice, they can proceed with the building and construction work.
BIM. CAD is mainly used for preparing 2D design and drawing for the project.
Though excessive-efficiency tires will work properly at decrease speeds, too, remember the fact that the extra efficiency-oriented a tire is, the shorter the expected tread life shall be.
Darth Momin was a humanoid Darkish Lord of Sith who appeared within the comic book Darth Vader: Darkish Lord of the Sith and briefly in Lando.
There were no pesky credit card bills, no coupons, no points, and no strange or complicated discount programs to decipher and track.
Air conditioning in bedrooms enables a much better evenings’ remainder at reasonable temperatures.
Great post. I was checking constantly this weblog and I am impressed!
Very helpful information specifically the remaining phase 🙂 I maintain such information a
lot. I used to be seeking this particular info for a very lengthy time.
Thank you and best of luck.
Spot on with this write-up, I honestly believe this web site needs a lot more attention. I’ll probably be back again to read through more, thanks
for the information!
With the introduction of vinyl materials the choices for promoting have broadened significantly.
One of the first institutional scale investment outsourcing arrangements occurred in 1986.
Six matches. It’s unprecedented for Guardiola.
Flagstaff is the principal metropolis of the Flagstaff metropolitan space, which includes all of Coconino County, and has a inhabitants of 145,101.
Pretty section of content. I just stumbled upon your website and in accession capital to assert that I get in fact enjoyed
account your blog posts. Any way I will be subscribing to your augment and even I achievement you access
consistently rapidly.
2023, the Orianne Middle for Indigo Conservation on the Central Florida Zoo and Botanical Backyard in Lake County, Florida, celebrated the hatching of 76 jap indigo snake hatchlings.
Primarily, the air pressure is higher beneath issues than it’s above things, so air pushes up more than it pushes down.
Irregular a/c service will certainly cause the develop of
dangerous legionnaires within the coils.
It’s going to be end of mine day, but before ending I am reading this
wonderful paragraph to increase my experience.
Your chosen a/c system will be scheduled and we’ll send our qualified engineers
to fit them for you.
Doing the right research will permit the adventurer to uncover the hidden gems and secret deals that embody where to go and special travel packages that embody secret airfare offers.
I love reading through a post that can make men and women think.
Also, many thanks for allowing me to comment!
Hi, I want to subscribe for this website
to get newest updates, therefore where can i do it please help.
Barathrus & Rhuax needs site: Roots of the Earth.
Which means grandparents, uncles and aunts can still contribute to a kid’s education.
What i don’t understood is in fact how you are no longer really a lot more smartly-liked than you might be right now.
You are so intelligent. You understand therefore significantly when it comes to this topic,
produced me personally consider it from numerous various angles.
Its like men and women don’t seem to be involved unless it’s one thing to accomplish with Lady gaga!
Your individual stuffs nice. Always take care of it up!
When I initially commented I clicked the “Notify me when new comments are added”
checkbox and now each time a comment is added I get three emails with the
same comment. Is there any way you can remove people from that
service? Appreciate it!
I don’t know whether it’s just me or if everybody else experiencing issues with your website.
It seems like some of the written text in your posts are running off the
screen. Can somebody else please provide feedback and let me know if this is happening to them too?
This might be a issue with my internet browser because I’ve had this happen before.
Many thanks
Why visitors still make use of to read news papers when in this technological world the whole
thing is available on web?
Spot on with this write-up, I seriously believe that this site needs a lot more attention. I’ll probably be back again to read through more, thanks for the advice.
Valuable information. Lucky me I found your site
accidentally, and I am surprised why this twist of fate did not happened in advance!
I bookmarked it.
With havin so much content and articles do you
ever run into any issues of plagorism or copyright infringement?
My site has a lot of unique content I’ve either created myself or outsourced but
it appears a lot of it is popping it up all over
the web without my permission. Do you know any ways to help protect against
content from being stolen? I’d definitely appreciate it.
Also visit my homepage; Demo PG Reel Love
This post is worth everyone’s attention. Where can I find out more?
excellent submit, very informative. I wonder why the opposite specialists of this sector don’t understand this.
You should proceed your writing. I am sure, you’ve a great readers’ base
already!
Hi my loved one! I wish to say that this article is awesome, nice written and include almost all vital infos.
I would like to peer more posts like this .
Woah! I’m really loving the template/theme of this site.
It’s simple, yet effective. A lot of times it’s very hard to get that “perfect balance” between superb usability and visual
appearance. I must say you’ve done a fantastic job with this.
In addition, the blog loads extremely fast for me on Internet explorer.
Exceptional Blog!
Excellent blog you’ve got here.. It’s difficult to find high-quality writing
like yours nowadays. I truly appreciate individuals like you!
Take care!!
It’s remarkable to pay a quick visit this web site and reading the views of all mates
regarding this post, while I am also eager of getting knowledge.
I loved as much as you will receive carried out right here.
The sketch is tasteful, your authored material stylish.
nonetheless, you command get bought an edginess over that you wish be delivering
the following. unwell unquestionably come more formerly again since exactly the
same nearly very often inside case you shield this hike.
This design is steller! You obviously know how to keep a reader amused.
Between your wit and your videos, I was almost moved to start my own blog
(well, almost…HaHa!) Fantastic job. I
really loved what you had to say, and more than that,
how you presented it. Too cool!
Thank you, I have just been looking for info about this subject for ages and yours
is the best I’ve discovered so far. But, what about the bottom line?
Are you certain in regards to the source?
Undeniably believe that that you stated. Your favourite reason seemed to be at the web the simplest factor to take into accout of.
I say to you, I definitely get irked even as other
people think about issues that they just don’t recognize about.
You controlled to hit the nail upon the top as neatly as outlined out the whole thing without having side-effects ,
other folks could take a signal. Will likely be again to get more.
Thanks
When I originally commented I clicked the -Notify me when new surveys are added- checkbox and after this each time a comment is added I recieve four emails with the exact same comment. Could there be in whatever way you’ll be able to remove me from that service? Thanks!
Hello there, just became aware of your blog through Google, and
found that it is really informative. I’m going to watch out for brussels.
I’ll be grateful if you continue this in future.
Many people will be benefited from your writing.
Cheers!
Howdy are using WordPress for your site platform? I’m new
to the blog world but I’m trying to get started and set up my own. Do
you require any html coding knowledge to make your own blog?
Any help would be really appreciated!
В Лев Казино вы всегда найдете
что-то для себя, независимо от того, предпочитаете ли
вы классические игры или что-то более
современное. Лев Казино предлагает вам обширную коллекцию игр на любой вкус, чтобы каждый мог
найти свою идеальную игру. Независимо от вашего уровня опыта, мы обеспечим вам комфортное и безопасное
игровое пространство.
Чтобы начать играть в Lev бонусы на
регистрацию, вам нужно всего лишь зарегистрироваться, и вы сразу получите доступ ко всем функциям.
Новые игроки могут рассчитывать на щедрые бонусы и специальные предложения, чтобы максимально выгодно начать свой
путь. Присоединяйтесь к нам и
наслаждайтесь комфортом игры в любое время суток.
Множество способов пополнения
счета и вывода средств.
Мы регулярно проводим акции, которые помогут вам увеличить ваш
игровой баланс.
Лев Казино предлагает удобный и интуитивно понятный
интерфейс, а также мобильную версию для
игры на ходу.
Наша служба поддержки всегда
готова помочь вам в любое время дня и ночи.
Не упустите шанс стать частью Лев Казино и испытать удачу прямо сейчас https://lev-casinovista.website/
Hello there! I know this is somewhat off topic but I was
wondering which blog platform are you using for
this site? I’m getting fed up of WordPress because I’ve had problems with hackers
and I’m looking at options for another platform.
I would be fantastic if you could point me in the direction of
a good platform.
Useful info. Fortunate me I found your website accidentally, and I am stunned why this coincidence did
not took place earlier! I bookmarked it.
I have read so many articles on the topic of the blogger
lovers except this piece of writing is really a nice post, keep it up.
An interesting discussion is worth comment. I think that you ought to publish more on this subject, it may not be a taboo matter but generally people don’t discuss these topics. To the next! Kind regards.
I simply couldn’t depart your site prior to
suggesting that I actually enjoyed the standard information an individual provide
on your visitors? Is gonna be back regularly in order to inspect new posts
Saved as a favorite, I love your blog!
I have to thank you for the efforts you’ve put in writing this blog.
I’m hoping to see the same high-grade content by you later on as well.
In truth, your creative writing abilities has motivated me to get my own site now 😉
Greetings! Very useful advice within this article!
It’s the little changes that make the greatest changes.
Thanks a lot for sharing!
Желаете сорвать крупный куш? Добро пожаловать в Hype Casino – лучший игровой клуб, где доступны разнообразные развлечения от известных брендов. https://hype-legend.buzz/ и испытайте удачу в Hype Casino!
Какие преимущества вы получите?
Коллекция лучших развлечений – популярные игры с высоким RTP.
Выгодные бонусы – бонусы на депозит, фриспины, кешбэк.
Быстрые выплаты – поддержка криптовалют и электронных кошельков.
Современный дизайн – легкая навигация по сайту.
Профессиональная помощь – готовность помочь в любое время.
Присоединяйтесь к Hype Casino и получите максимум удовольствия!
If you do not want to pay anything at all, there are some basic techniques you can utilize to keep one’s cool.
What i don’t understood is in fact how you are not actually a lot more neatly-liked than you might be now.
You are so intelligent. You know therefore considerably in relation to this topic, produced
me for my part imagine it from a lot of numerous angles.
Its like men and women don’t seem to be involved unless it’s
one thing to do with Woman gaga! Your individual stuffs great.
All the time maintain it up!
This is fantastic. I gained a lot from reading it. The information is highly informative and structured.
Hello, always i used to check web site posts here early in the morning,
as i love to find out more and more.
Excellent way of describing, and good paragraph to obtain data concerning my
presentation subject, which i am going to convey in academy.
Your style is really unique compared to other folks I’ve read stuff from. Thank you for posting when you’ve got the opportunity, Guess I will just bookmark this site.
I’m really impressed with your writing skills and also with the format on your blog. Is this a paid subject matter or did you customize it yourself? Anyway stay up the nice high quality writing, it is uncommon to peer a nice blog like this one today. I like semiconductormaterials.com ! It is my: Stan Store alternatives
Hello just wanted to give you a quick heads up. The
text in your article seem to be running off the
screen in Opera. I’m not sure if this is a formatting issue or something to do with browser
compatibility but I thought I’d post to let you know.
The design and style look great though! Hope you get the problem solved soon. Thanks
Хотите испытать удачу? Добро пожаловать в 1GO Casino – онлайн-казино, где вас ждут тысячи слотов от лидеров игровой индустрии. Присоединяйтесь уже сегодня и ловите акции для увеличения шансов на выигрыш. https://1go-level.buzz/cashback и начните свое приключение 1GO Casino!
Что делает 1GO Casino уникальным?
Огромный выбор игр – более 3000 слотов от NetEnt, Microgaming, Play’n GO.
Щедрые бонусы – персональные награды обновляются регулярно.
Быстрые выплаты – выплаты без задержек.
Простая навигация – доступность на всех устройствах.
Профессиональные операторы – готовность ответить в любое время.
Присоединяйтесь к тысячам счастливых игроков и получите максимум эмоций!
Very energetic blog, I enjoyed that bit. Will there be a part 2?
Everyone loves it when individuals get together and share views.
Great blog, keep it up!
I was excited to discover this site. I need to to thank
you for your time due to this wonderful read!! I definitely savored every part of it and i also
have you saved to fav to check out new information in your blog.
Pretty nice post. I just stumbled upon your weblog and wanted
to say that I have really enjoyed browsing your blog posts.
After all I will be subscribing to your feed and I hope you write again very soon!
Can I just say what a comfort to find somebody that genuinely knows what they’re talking about on the net. You actually realize how to bring an issue to light and make it important. A lot more people should check this out and understand this side of your story. I was surprised you’re not more popular given that you definitely possess the gift.
bokep terbaik sma toket gede menyala banget
For newest news you have to pay a quick visit web and on web I found this site as a most
excellent site for latest updates.
Great blog! Do you have any recommendations
for aspiring writers? I’m planning to start my own website soon but I’m
a little lost on everything. Would you propose starting with a free platform
like WordPress or go for a paid option? There are so many options
out there that I’m completely overwhelmed .. Any ideas?
Thanks!
I’ve since recovered, but I feel a deep connection to these men-their vulnerability,
their desperation, their pain. But there are a lot of males who have a smaller (P) size, which make them feel embarrassed and shy
in front of their partner. It is human nature to have a few grumbles in front
of old friends due to internal and external
troubles.He was so wasteful as the Golden Scale Palace.
I dont have enough money to buy all those gadgets so if you could email
me back asap about how to enlarge it, that would be great. If you have done any research into natural penis enlargement,
you have an idea about how to do some of the exercises that bring additional blood into your
penis, stretch it, and prompt it to grow new cells.
Finally I added some cardiovascular exercises to add even better blood flow.
Not only does Andropenis add length through the use of
traction, but girth is also increased.
I really love your site.. Great colors & theme. Did you develop this website yourself? Please reply back as I’m planning to create my very own website and would like to know where you got this from or what the theme is called. Cheers.
Appreciate it for this post, I am a big fan of this internet site would like to keep updated.
I am no longer positive where you’re getting your information, however good topic.
I must spend some time finding out much more or
working out more. Thanks for excellent info I was on the lookout for this info for my
mission.
This is getting a bit more subjective, but I much prefer the Zune Marketplace.
The interface is colorful, has more flair, and some cool features like Mixview
that let you quickly see related albums, songs, or other users related to what youre listening to.
Clicking on one of those will center on that item, and another set of neighbors
will come into view, allowing you to navigate around exploring by similar artists, songs, or users.
Speaking of users, the Zune Social is also great fun, letting
you find others with shared tastes and becoming friends with them.
You then can listen to a playlist created based on an amalgamation of what all your friends are listening to, which is also enjoyable.
Those concerned with privacy will be relieved
to know you can prevent the public from seeing your personal listening
habits if you so choose.
Definitely believe that which you said. Your favorite justification seemed to be
on the internet the simplest thing to be aware of.
I say to you, I certainly get irked while people consider
worries that they just don’t know about. You managed to hit the nail
upon the top and defined out the whole thing without having side
effect , people can take a signal. Will probably be back to get more.
Thanks
Hi, I do believe this is an excellent site. I stumbledupon it 😉 I will return once again since I saved as a favorite it. Money and freedom is the greatest way to change, may you be rich and continue to help others.
Unlim Casino is a unique platform offering outstanding conditions for gaming and an amazing experience for all gambling enthusiasts.
Here, you’ll find a large selection of slots, card
games, as well as exciting tournaments and promotions that can significantly improve your chances of winning.
We are happy to offer a user-friendly interface, a vast collection of gaming machines, and classic table games.
Gambling with generous bonuses and daily promotions will make your gaming experience even more exciting.
What awaits you when you join Unlim Casino?
Simple registration to start playing — quick profile setup,
and you are set to begin.
Great bonuses for new players — we offer you bonuses on your first deposit,
providing a great start to your gaming journey.
Regular promotions and tournaments — for all players
who want to boost their chances of winning and earn additional prizes.
24/7 support ready to assist you with any questions or issues related to gaming.
A variety of games available on any device, so
you can enjoy the gameplay, whether on your PC or smartphone.
Join us now! Exciting adventures await you at Unlim Casino,
offering many enjoyable moments and the opportunity to
win big prizes. Are you ready for new victories? https://unlim-777-casino.homes/
Thanks for finally talking about > SMI diamond grinding wheels < Liked it!
I am extremely inspired along with your writing talents and also with the layout for your weblog. Is that this a paid theme or did you modify it yourself? Anyway stay up the excellent quality writing, it is rare to look a nice blog like this one these days. I like semiconductormaterials.com ! It’s my: Lemlist
Thanks for sharing your thoughts about gaziantep berber.
Regards
Wow, incredible blog layout! How lengthy have you been running a blog for?
you make running a blog glance easy. The entire glance of your web site is fantastic, let alone the content!
Lovely write ups. Thanks a lot.
Inspiring story there. What occurred after? Take care!
Does your blog have a contact page? I’m having a tough time locating it but, I’d like to
shoot you an e-mail. I’ve got some recommendations for your blog you might be interested in hearing.
Either way, great site and I look forward to seeing it improve over time.
simontok,
bokep indonesia,
bokep viral,
bokep indo terbaru,
porno,
tautan bokep,
film porno,
bokep terkini,
vidio bokep,
website bokep,
film bokep
bokeb,
video porno,
bokep korea,
bokep indonesia terupdate,
indo bokep,
nonton bokep,
bokep viral indo,
bokep indoh,
bokep live,
bokep abg,
bokep indonesia viral,
laman porno,
aplikasi bokep,
bokep india,
indo porn,
bokep indo live,
video bokep jepang,
porno indonesia,
situs bokep indo,
bokep si montok,
bokep cindo,
ling bokep,
lingbokep,
xnxx bokep,
bokep asia,
bokep hd,
indonesia porn,
video bokep indo,
video porn,
unduh bokep,
bokep xnxx,
bokep xxx,
simontk,
si mont0k,
linkbokep.to,
ruangbokep,
bokep online,
video simontok,
bokep31,
Hi there, everything is going nicely here and ofcourse every one is
sharing data, that’s really good, keep up writing.
Hey! Someone in my Facebook group shared this website with us so I came to give it
a look. I’m definitely loving the information.
I’m bookmarking and will be tweeting this to my followers!
Great blog and wonderful style and design.
I really like what you guys tend to be up too.
Such clever work and coverage! Keep up the awesome works guys I’ve included
you guys to my blogroll.
Ahaa, its fastidious dialogue regarding this post at
this place at this webpage, I have read all that, so now me
also commenting at this place.
Hi there would you mind stating which blog platform you’re
working with? I’m going to start my own blog soon but I’m having a difficult time choosing between BlogEngine/Wordpress/B2evolution and Drupal.
The reason I ask is because your design and style seems
different then most blogs and I’m looking for something completely unique.
P.S Apologies for getting off-topic but I had to ask!
I’m amazed, I have to admit. Rarely do I encounter a blog that’s both equally educative and interesting, and without a doubt, you have hit the nail on the head. The problem is an issue that not enough folks are speaking intelligently about. Now i’m very happy that I came across this in my search for something relating to this.
I every time used to read post in news papers but now as I am
a user of web so from now I am using net for posts, thanks to web.
Hey there! I could have sworn I’ve been to this site before but after reading through some of the post I realized it’s new to me.
Nonetheless, I’m definitely delighted I found it and I’ll
be book-marking and checking back frequently!
Thanks in support of sharing such a fastidious
thinking, piece of writing is pleasant, thats why
i have read it fully
Cool blog! Is your theme custom made or did you download it from somewhere?
A design like yours with a few simple adjustements would really make my blog stand out.
Please let me know where you got your theme.
Thank you
I do not even understand how I ended up here, but I
assumed this submit was once great. I don’t recognize who you might be however definitely you’re going to a well-known blogger if you happen to aren’t
already. Cheers!
An intriguing discussion is worth comment. I believe that you should publish more on this issue, it may not be a taboo subject but generally people don’t talk about such subjects. To the next! Best wishes!
Wow, superb blog layout! How long have you been blogging for?
you made blogging look easy. The overall look of your site is fantastic, as well as the content!
It’s really a nice and useful piece of info. I’m glad that you just shared this
helpful info with us. Please keep us up to date like this.
Thanks for sharing.
It is the best time to make some plans for the future and it is time to be happy.
I have learn this publish and if I may I want to counsel you some fascinating issues or
suggestions. Perhaps you could write next
articles regarding this article. I desire to learn more things
approximately it!
Wonderful beat ! I would like to apprentice while you amend your site, how
can i subscribe for a blog site? The account helped me a acceptable deal.
I had been tiny bit acquainted of this your broadcast provided
bright clear concept
Hi to every one, since I am in fact eager of reading this
website’s post to be updated on a regular basis.
It contains good information.
If you want to get much from this post then you have to apply these
techniques to your won web site.
Fine way of describing, and good piece of writing to obtain information about
my presentation topic, which i am going to present in university.
I’m really enjoying the theme/design of your weblog.
Do you ever run into any web browser compatibility problems?
A handful of my blog audience have complained about my blog
not operating correctly in Explorer but looks great in Opera.
Do you have any ideas to help fix this issue?
bokep terbaik sma toket gede menyala banget
If you desire to take much from this paragraph then you have to apply these methods to
your won weblog.
It’s nearly impossible to find knowledgeable people in this particular subject, however, you seem like you
know what you’re talking about! Thanks
CONVERT YOUTUBE VIDEO CLIPS WITH onlinevideo converter
YouTube to MP4 Conversion
YouTube to MP3 Conversion
OVC – ONLINE VIDEO CLIP DOWNLOADER
We provide a variety of approaches to transform and also download on the internet videos for offline accessibility.
You can store videos and also watch them on your mobile device or computer effortlessly, even while on the go!
Just duplicate the video clip or GIF web links from YouTube,
Facebook, Twitter, Vimeo, or various other internet sites, as well as utilize our
totally free online video converter to change them!
HOW TO ADJUSTMENT YOUTUBE VIDEO CLIP TO MP3 ONLINE?
Place the link of the video clip link you desire to replicate
Replicate the web link of the online video
clip and paste it right into the defined location to start the conversion process.
Select the recommended format for conversion
Choose the format in which you prefer to transform the video clip: MP4 to
maintain both audio and video, or MP3 for sound
just.
Launch the conversion by clicking ” Transform”.
Commence the video clip conversion process by clicking the “Convert” button situated below the marked location.
Download the video clip by clicking “Download”.
It’s full!
Save the transformed MP4 or MP3 file to your computer system or
phone by clicking the “Download” button.
It’s remarkable to pay a visit this web page and reading the views of all friends
regarding this piece of writing, while I am also eager of getting know-how.
You really should take part in a contest first of the most effective blogs online. I will recommend this web site!
Hi there, just became alert to your blog through Google, and found that it is really informative.
I’m gonna watch out for brussels. I’ll be grateful if you continue this in future.
Numerous people will be benefited from your
writing. Cheers!
Get Unlimited Access To 80+AI module
Feature Of WorkForceAI
https://jvz7.com/c/1788411/415801/
Thanks for finally talking about > SMI diamond grinding wheels < Loved it!
CONVERT YOUTUBE VIDEO CLIPS WITH online video clip converter
YouTube to MP4 Conversion
YouTube to MP3 Conversion
OVC – ONLINE VIDEO DOWNLOADER
We provide a selection of approaches to transform
and also download online video clips for offline access.
You can store videos and watch them on your mobile device or computer system effortlessly,
even while on the move!
Simply replicate the video or GIF web links from YouTube, Facebook, Twitter, Vimeo, or other sites, and also utilize our complimentary online video clip converter to transform them!
HOW TO ADJUSTMENT YOUTUBE VIDEO CLIP TO MP3 ONLINE?
Place the link of the video link you want to duplicate
Reproduce the web link of the on-line video and paste it right
into the defined location to begin the conversion
procedure.
Select the favored style for conversion
Choose the format in which you prefer to convert the video:
MP4 to preserve both audio and also video clip, or MP3 for
sound just.
Start the conversion by clicking “Convert”.
Commence the video conversion procedure by clicking
the “Convert” switch situated listed below the designated location.
Download the video clip by clicking “Download”. It’s complete!
Save the transformed MP4 or MP3 data to your computer or phone by clicking the “Download” button.
Hey there I am so excited I found your site, I really found you
by mistake, while I was browsing on Askjeeve
for something else, Anyhow I am here now and would just like to say many thanks for a tremendous post and a all
round entertaining blog (I also love the theme/design), I don’t have time to look over it all at the minute
but I have saved it and also included your RSS feeds, so when I have time I
will be back to read much more, Please do keep up the great job.
Hi to every , because I am genuinely keen of reading this weblog’s post to
be updated daily. It carries good information.
Hello everyone, it’s my first pay a quick visit at this site, and article is actually fruitful designed for me, keep up posting these
content.
It’s nearly impossible to find experienced people for this subject, but you sound like you know
what you’re talking about! Thanks
Heya i’m for the first time here. I found this board and I to
find It really helpful & it helped me out a lot.
I’m hoping to give something again and help others such as you aided me.
Pretty! This was a really wonderful post. Thanks for supplying this info.
Helpful content!
Кристальная чистота в Санкт-Петербурге: Ваш неизменный партнер по уборке!
Наша компания более 10 лет предоставляет услуги клининга в Санкт-Петербурге и заслужила признание как надежный партнер. Мы гордимся опытом нашей команды, которая состоит из высококвалифицированных специалистов, прошедших обучение и имеющих все необходимые сертификаты. Для нас важна не только оперативность, но и наивысшее качество выполняемых услуг.
Не ждите, пока грязь и хаос станут проблемой. Дайте нам шанс возродить вашему пространству чистоту и порядок! Узнайте больше о наших услугах и оставьте заявку на сайте : https://ssjcompanyinc.official.jp/bbs/board.php?bo_table=free&wr_id=3087390
Кристальная чистота в Санкт-Петербурге: Ваш неизменный партнер по наведению порядка!
Наша компания более 10 лет оказывает услуги клининга в Санкт-Петербурге и заслужила признание как надежный партнер. Мы гордимся опытом нашей команды, состоящей из высококвалифицированных специалистов, прошедших обучение и имеющих все необходимые сертификаты. Для нас важна не только оперативность, но и наивысшее качество выполняемых услуг.
Не ждите, пока грязь и хаос станут проблемой. Дайте нам шанс возродить вашему пространству чистоту и порядок! Узнайте больше о наших услугах и отправьте заявку на сайте : https://uberu21.ru/
I’m really impressed with your writing skills and also with the layout on your blog.
Is this a paid theme or did you modify it yourself? Either way keep up the excellent quality writing, it’s rare to see a great blog like this one these days.
Many thanks, Numerous facts!
Ductless mini-split a/c unit are also effective in cooling down homes.
My brother recommended I may like this blog. He was once totally right.
This post actually made my day. You can not believe just
how a lot time I had spent for this info! Thank you!
excellent put up, very informative. I ponder why the other experts of this sector do not notice this.
You must continue your writing. I’m confident, you’ve a great
readers’ base already!
I’d like to find out more? I’d care to find out more details.
I relish, result in I found just what I used to be looking
for. You’ve ended my four day lengthy hunt! God Bless you man. Have a great day.
Bye
Yesterday, while I was at work, my cousin stole my apple ipad
and tested to see if it can survive a forty foot drop, just so she
can be a youtube sensation. My apple ipad is now broken and she has 83 views.
I know this is completely off topic but I had to share it with someone!
Hi there terrific website! Does running a blog similar to this require a large amount of work?
I have absolutely no knowledge of coding however I was hoping to start my own blog in the near
future. Anyways, should you have any ideas or techniques for new blog owners please
share. I know this is off subject however I just wanted to ask.
Thanks!
Howdy! This article couldn’t be written any better! Reading through this article reminds me of my previous
roommate! He always kept talking about this. I am going to send
this information to him. Pretty sure he will have a very good read.
Thanks for sharing!
Picking a ductless system can minimize your energy bills, however it might require added labor and ductwork.
sex nhật hiếp dâm trẻ em ấu dâm buôn bán vũ khí ma túy bán súng sextoy chơi đĩ sex bạo lực sex học đường tội phạm tình dục chơi les đĩ đực người mẫu bán dâm
We work with well established industry leaders, such as Panasonic, Toshiba and Fujitsu.
bokep terbaik sma toket gede menyala banget
I’m not that much of a online reader to be honest but your sites really nice,
keep it up! I’ll go ahead and bookmark your site to come back later.
Cheers
Yes! Finally something about Click here for free
money.
Howdy, i read your blog from time to time and i own a similar one and
i was just wondering if you get a lot of spam remarks?
If so how do you protect against it, any plugin or anything you can recommend?
I get so much lately it’s driving me crazy so any assistance is very much appreciated.
Some ducted units require water to run correctly as they use water to cool the condenser.
This article is fantastic! Packed with useful details and very well-written. Thank you for offering this.
Hurrah! Finally I got a weblog from where I
know how to really obtain helpful facts regarding my study and knowledge.
Hi! Do you know if they make any plugins to help with Search Engine
Optimization? I’m trying to get my blog to rank for some targeted keywords but
I’m not seeing very good results. If you know of any please
share. Kudos!
Nice blog! Is your theme custom made or did
you download it from somewhere? A design like yours with a
few simple tweeks would really make my blog jump out.
Please let me know where you got your theme.
Thanks
Hi, I do believe this is a great website. I stumbledupon it 😉 I’m going to return once again since i have book marked it. Money and freedom is the best way to change, may you be rich and continue to guide others.
Thanks for finally talking about > SMI diamond grinding wheels < Loved it!
Инновационные Технологии — это платформа для людей, интересующихся
новыми технологиями и инновациями.
Здесь вы найдете новости, статьи, обзоры и анализ последних достижений в области науки, техники и
промышленности. Тематика сайта включает в себя
новости в – инновация центр искусственный интеллект, робототехнику,
интернет вещей, биотехнологии, нанотехнологии, космос,
энергетику и многое другое.
Также на сайте есть возможность
для авторов и экспертов публиковать
свои статьи, обмениваться опытом и
знаниями.
Well written, thanks!
Great post.
We provide a cost-free site visit after we have actually
sent you a cost-free quote by e-mail.
Hmm it appears like your website ate my first comment (it was extremely long) so I guess
I’ll just sum it up what I wrote and say, I’m thoroughly enjoying
your blog. I as well am an aspiring blog writer but I’m
still new to the whole thing. Do you have any helpful hints for novice blog writers?
I’d definitely appreciate it.
Hey very nice blog!
Good post. I learn something new and challenging on websites I stumbleupon everyday.
It’s always useful to read content from other writers
and use a little something from other web sites.
Анлим Казино пresents игрокам возможность познать истинное удовольствие от азартных игр.
Здесь вы найдете множество слотов, карточных игр, а также непрерывно проводимые акции, что позволяет игрокам значительно улучшить свои шансы на
выигрыш и приносит массу удовольствия от процесса.
Наше казино предлагает не только азарт,
но и удобство для всех пользователей, независимо
от того, играете ли вы с мобильного устройства или
с компьютера. Мы гарантируем ежедневное расширение ассортимента
игр и проведение увлекательных турнирных состязаний.
В чем преимущество игры в Анлим Казино?
Быстрая регистрация — всего пару шагов, и
вы уже готовы начать играть.
Большие бонусы для новичков — мы дарим бонусы на первый депозит для старта с большими
шансами на победу.
Регулярные акции и турниры
— для каждого, кто хочет повысить свои шансы
на победу и дополнительные
призы.
Профессиональная поддержка всегда готова помочь с любыми вопросами
о процессе игры.
Богатый выбор игр доступных как на компьютере,
так и на мобильных устройствах.
Присоединяйтесь к нам уже
сегодня! Анлим Казино ждет вас.
Не ждите — начните выигрывать с нами прямо сейчас! https://unlim-casinomirage.yachts/
I was recommended this blog by means of my cousin. I’m not certain whether or not this submit is
written through him as nobody else recognise such certain about my
difficulty. You’re incredible! Thank you!
What’s up, for all time i used to check website posts here in the early hours in the break of day, since
i enjoy to find out more and more.
I was able to find good advice from your blog posts.
Hi there, its pleasant post about media print, we all know media is a fantastic source of facts.
Awesome blog you have here but I was curious
if you knew of any message boards that cover the same topics discussed
here? I’d really love to be a part of community where I can get feed-back from other experienced people that share the
same interest. If you have any recommendations, please let
me know. Kudos!
If you are unclear what system would certainly best fit your
demands, please so not wait to get in touch.
That is a great tip particularly to those fresh to the blogosphere. Brief but very precise information… Appreciate your sharing this one. A must read article!
We are a group of volunteers and opening a new scheme in our community.
Your site offered us with valuable information to work on. You have done an impressive job and our entire community will be thankful to you.
Tremendous things here. I am very glad to peer your article.
Thank you so much and I am looking ahead to contact you.
Will you kindly drop me a mail?
Thanks in support of sharing such a pleasant idea, piece of writing is good,
thats why i have read it fully
Article writing is also a excitement, if you be familiar with then you can write if not it is
complex to write.
I was wondering if you ever thought of changing the structure of your blog?
Its very well written; I love what youve got to say. But maybe you could a little more in the
way of content so people could connect with
it better. Youve got an awful lot of text for only having one or 2 images.
Maybe you could space it out better?
Thanks for the marvelous posting! I definitely enjoyed reading it, you might be
a great author. I will ensure that I bookmark your blog and will eventually come back in the future.
I want to encourage yourself to continue your great job,
have a nice afternoon!
Hi, i think that i saw you visited my site so i
got here to return the prefer?.I am attempting to to find things to improve my
website!I guess its adequate to make use of a few of your ideas!!
The British summertime are just one of the busiest and hottest times of
the year.
You can definitely see your enthusiasm in the article you write.
The world hopes for more passionate writers like you who are
not afraid to say how they believe. At all times go
after your heart.
hello there and thank you for your info – I’ve definitely picked up anything new from right here.
I did however expertise a few technical issues using this
site, as I experienced to reload the site a lot of times previous to I could get
it to load correctly. I had been wondering if
your hosting is OK? Not that I am complaining, but slow loading instances times will sometimes affect
your placement in google and can damage your quality score if ads and marketing with Adwords.
Well I’m adding this RSS to my email and could look out for much more of your respective intriguing content.
Make sure you update this again very soon.
Its like you read my mind! You appear to know a lot about this, like you wrote the book in it or something.
I think that you can do with some pics to drive the message home a little
bit, but instead of that, this is magnificent blog.
An excellent read. I’ll certainly be back.
Hello there! I just wish to offer you a huge thumbs up for the excellent
info you have got right here on this post. I will be coming
back to your blog for more soon.
Hello there, just became alert to your blog through Google, and found that it’s really informative.
I’m gonna watch out for brussels. I’ll appreciate if you continue
this in future. Many people will be benefited from your writing.
Cheers!
Thanks , I’ve recently been looking for information approximately this topic for a while and
yours is the greatest I’ve found out so far. However, what in regards to the conclusion? Are you certain concerning
the source?
You actually make it seem really easy with your presentation however
I to find this matter to be really one thing that I believe I’d by no
means understand. It kind of feels too complex and very
extensive for me. I’m taking a look ahead to your subsequent submit, I’ll attempt to get the
cling of it!
Hello, i read your blog from time to time and i own a similar one
and i was just wondering if you get a lot of spam comments?
If so how do you prevent it, any plugin or anything you can recommend?
I get so much lately it’s driving me crazy so any help
is very much appreciated.
We are specialist installers+ and give all the essential tools
for your installment, whatever the height or area.
I really like your blog.. very nice colors & theme. Did you create this website yourself or did
you hire someone to do it for you? Plz respond as I’m looking to
design my own blog and would like to find out where u got
this from. appreciate it
Your style is unique compared to other people I’ve read stuff from.
Many thanks for posting when you’ve got the opportunity, Guess I will just book mark this web site.
龍岳山 常満寺
Description:
いなべ市でお寺をお探しなら龍岳山 常満寺がおすすめです。浄土真宗本願寺派の由緒あるこのお寺では、心理カウンセラーの資格を持つ副住職が仏教と心理学を融合させた独自のアプローチで心の安らぎを提供。どなたでも気軽に参拝でき、現代の悩みに寄り添う心の拠り所として地域の方々から親しまれています。
Keyword:
いなべ市 お寺
Address:
〒511-0266 三重県いなべ市大安町石榑南1345-1
Phone:
0594782346
GoogleMap URL:
https://maps.app.goo.gl/Et2qVZwCpgWb117L7
Category:
仏教寺院
It’s the best time to make some plans for the long run and it’s time to be
happy. I have learn this publish and if I may I desire to counsel
you some interesting things or advice. Perhaps
you could write subsequent articles regarding this article.
I wish to learn even more things about it!
Hi there!
Call me Matilda, and I just had to leave a comment here.
Your content is amazing, and it’s always nice to come
across such thoughtful ideas.
By the way, if you’re interested in new ways to connect with people, you should absolutely check out Bubichat!
It’s a fantastic platform where flirty conversations happen all the
time.
I love it there because it’s the perfect spot to meet new people and share
exciting moments.
Give it a try if you’re in the mood for something different!
I’m always around, and who knows – we could connect!
Keep up the awesome work! Bubichat
XOXO Waiting on bubichat.com
Your style is really unique compared to other folks I have read stuff from. I appreciate you for posting when you’ve got the opportunity, Guess I will just bookmark this page.
you’re in reality a excellent webmaster.
The web site loading velocity is incredible. It sort of feels that you are doing any distinctive trick.
Also, The contents are masterwork. you’ve performed a fantastic activity in this matter!
If some one wishes to be updated with latest technologies therefore he must be visit this web
site and be up to date daily.
Bigger systems with higher cooling capabilities often tend to have
greater installment costs.
Please let me know if you’re looking for a writer for
your blog. You have some really great articles and I believe I would be a good asset.
If you ever want to take some of the load off, I’d love
to write some material for your blog in exchange for a link back to mine.
Please blast me an email if interested. Kudos!
I always spent my half an hour to read this webpage’s articles or reviews every day along with a cup of coffee.
Have you ever considered creating an e-book or guest authoring
on other websites? I have a blog centered on the same information you discuss and would love to
have you share some stories/information. I know my readers would value
your work. If you are even remotely interested, feel free to shoot
me an e mail.
Generally, 5,000 to 8,000 BTUs suffices for many living areas or rooms.
This piece of writing will help the internet people for creating new webpage or even a weblog from start to end.
Normally, the greater the BTU asserted, the more successfully
it can cool down a room.
Good respond in return of this issue with real arguments and describing everything about that.
It’s hard to come by well-informed people
on this topic, however, you seem like you know what you’re talking about!
Thanks
Hey! I could have sworn I’ve been to this site before
but after reading through some of the post I realized it’s new to me.
Anyways, I’m definitely glad I found it and I’ll be book-marking and checking back
frequently!
Appreciate this info!
The basic idea in all of the best penis enlargement exercises is to get more blood
flowing into the penis. To get number one results from your number one penile enlargement exercises,
stay with the basic exercises for as long as the program requires.
In the end, of course, no penile enhancement pictures can predict what a
program of penis enlargement exercises will do for you.
If used consistently over a long period of time,
they can cause the skin of the penis to become “spongy” and have a
thicker appearance. To this day, in all-male environments like logging camps and prisons, young men insert
stones and other objects beneath the skin of their penis.
And you can buy plenty of over-the-counter and even medical treatments that promise a larger penis.
The laboratory produces about 20 test tubes of cells, some of which will be
used for the required treatment (or for several different treatments).
Now, we will provide an in-depth look at all Prosolution Plus offers.
Unless you have destroyed tissue, the bruises are not nice to look at, but they are not dangerous.
This solution commonly includes a combination of devices, supply, and wage expenditures.
Our group of specialist designers are happy to review your requirements with you.
I blog quite often and I genuinely thank you for
your content. This great article has really peaked my interest.
I’m going to take a note of your website and keep checking for new details about once per week.
I opted in for your Feed too.
Would absolutely suggest and would return if I require a central heating boiler in the future.
Excellent post. I thought the details extremely useful. Adored the method you clarified the content.
Really liked it! Definitely I’ll tell my friends about it.
Thanks for a marvelous posting! I truly enjoyed reading it, you could be a
great author.I will make sure to bookmark your blog
and definitely will come back very soon. I want to encourage one to continue your great work,
have a nice morning!
Split cooling systems set you back even more to mount than portable systems and additionally can not be moved.
After I initially commented I seem to have clicked the -Notify me when new comments are added- checkbox and from now on whenever a comment
is added I receive 4 emails with the same comment.
There has to be a means you can remove me from that
service? Thanks!
We supply bespoke Upkeep & Cooling Providers for all kinds of Cooling systems
in London.
Hi there everyone, it’s my first visit at this web site, and paragraph is
actually fruitful in favor of me, keep up posting such content.
I think the admin of this web page is really working hard in favor of his website, as
here every material is quality based data.
When someone writes an paragraph he/she retains the idea of a user in his/her brain that
how a user can be aware of it. Thus that’s why this post is
great. Thanks!
Oh my goodness! Incredible article dude! Thanks, However I am experiencing problems with your RSS. I don’t know the reason why I am unable to join it. Is there anyone else getting the same RSS problems? Anyone who knows the solution can you kindly respond? Thanx!
It is perfect time to make some plans for the future and it’s time to be happy.
I’ve read this post and if I could I wish to suggest you some interesting things or suggestions.
Perhaps you can write next articles referring to this
article. I desire to read more things about it!
Mighty Dog Roofing
8110 East 126tһ St S
Bixby, OK 74008, United Statеs
19182125646
updated Roofing Materials near Me
Having read this I believed it was very informative. I appreciate you taking the time and energy to put this information together. I once again find myself personally spending a significant amount of time both reading and commenting. But so what, it was still worth it.
Hello there, I discovered your web site via Google even as searching for a related matter, your
website came up, it looks great. I’ve bookmarked it in my google bookmarks.
Hi there, simply was aware of your blog thru Google,
and found that it is really informative. I’m going to be careful for
brussels. I’ll appreciate in the event you proceed this
in future. Many other folks will likely be
benefited from your writing. Cheers!
I believe this is among the so much vital info for me.
And i am happy reading your article. But should commentary on some
normal things, The web site taste is great, the articles is in point of fact great :
D. Excellent process, cheers
Our solution includes support for brand-new builds, clean sheet setups and system upgrades.
situs porno yang paling bagus
Hi there! I just want to give you a huge thumbs up for your great info you have here on this post. I’ll be coming back to your website for more soon.
Hey I know this is off topic but I was wondering if you knew of any widgets
I could add to my blog that automatically tweet my newest twitter updates.
I’ve been looking for a plug-in like this for quite some
time and was hoping maybe you would have some experience with something like this.
Please let me know if you run into anything. I truly enjoy reading your blog and I look forward to your new updates.
When you air condition your home, you additionally keep your doors and windows closed.
I’m not sure where you are getting your information, but great topic.
I needs to spend some time learning much more or understanding more.
Thanks for magnificent info I was looking for this info for my mission.
I will right away grasp your rss feed as I can not
in finding your e-mail subscription hyperlink or e-newsletter service.
Do you’ve any? Kindly permit me understand so that I may subscribe.
Thanks.
Every weekend i used to go to see this web page, for
the reason that i wish for enjoyment, for the reason that this this
web site conations actually nice funny material too.
Incredible insights here.
I like the valuable info you provide in your
articles. I will bookmark your weblog and check
again here regularly. I am quite sure I’ll learn many new
stuff right here! Good luck for the next!
I am really enjoying the theme/design of your blog. Do you ever run into any
browser compatibility problems? A number of my blog readers have complained
about my website not operating correctly in Explorer but looks great in Opera.
Do you have any tips to help fix this issue?
We just supply and install the absolute best a/c systems from prize-winning brands.
wonderful issues altogether, you just received a
logo new reader. What might you suggest about your post that you made a
few days ago? Any sure?
When I initially commented I seem to have clicked the -Notify me when new comments are added- checkbox and from now on every time a comment is added I recieve 4 emails with the same comment. Is there a means you can remove me from that service? Cheers.
This is a great article!
Готовы покорить мир онлайн-казино? Добро пожаловать в Jetton Casino – премиальное казино, где представлен широкий каталог слотов. https://jetton-arena.top/ и начните выигрывать прямо сейчас!
В чем наши преимущества?
Лучшие игровые автоматы – игры от ведущих провайдеров.
Выгодные акции – регулярные турниры с крупными призами.
Гарантия честных выплат – операции под защитой SSL-шифрования.
Доступность на всех устройствах – адаптивный дизайн без ограничений.
Дружелюбные операторы – быстрое решение любых вопросов.
Начните выигрывать уже сегодня и играйте с комфортом!
It is necessary to remove this section before setting up the
side panels.
I’ve been browsing online more than 3 hours today,
yet I never found any interesting article like
yours. It is pretty worth enough for me.
Personally, if all web owners and bloggers made good content
as you did, the internet will be much more useful than ever before.
Wow, awesome blog layout! How long have you been blogging for?
you made blogging look easy. The overall look of your site is
magnificent, as well as the content!
Excellent beat ! I would like to apprentice while you amend
your website, how could i subscribe for a blog website? The account aided me
a acceptable deal. I had been a little bit acquainted of this your broadcast offered bright clear concept
I have been surfing online more than 2 hours today, yet I never found any
interesting article like yours. It is pretty worth enough for me.
Personally, if all website owners and bloggers made good
content as you did, the net will be a lot more useful than ever before.
I constantly spent my half an hour to read
this webpage’s content all the time along with a cup of coffee.
This is a great article!
Официальный сайт Азино777: Подробный обзор
Казино Азино777 — это востребованное онлайн-казино, которое привлекает внимание игроков благодаря огромному выбору слотов. Платформа Азино 777 предлагает интуитивно понятное меню, что делает его отличным решением для всех любителей азарта https://azino777-bonus-official-site-zerkalo-casino-1.ru/.
Преимущества Азино777
Казино Азино777 выделяется среди других платформ благодаря следующим плюсам:
Огромное количество слотов: На платформе Azino777 представлены тысячи игровых автоматов от проверенных разработчиков.
Щедрые бонусы: Пользователи могут получить приветственный бонус.
Удобные способы оплаты: Азино777 поддерживает популярные методы оплаты.
Игра на смартфоне: Играть можно в любом месте.
Как стать игроком Азино 777
Для старта в Азино 777, нужно зарегистрироваться на сайте. Процесс занимает пару шагов:
Загрузите платформу Azino777.
Заполните форму.
Завершите процесс.
После этого вы сможете сделать депозит и воспользоваться акцией.
Ассортимент казино Азино 777
Azino777 предлагает разнообразие игр:
Игровые автоматы: Видео слоты с различными тематиками.
Настольные игры: Французская рулетка, покер.
Прогрессивные слоты: Шанс выиграть огромный джекпот.
Надежность Azino777
Казино Азино777 работает на основе сертификата, что гарантирует безопасность игрового процесса. Личная информация пользователей шифруются с помощью передовых систем.
FAQ: Вопросы и ответы
1. Как создать аккаунт на Azino777?
Процесс регистрации занимает пару шагов. Откройте платформу, заполните форму и активируйте аккаунт.
2. Что можно получить в Азино 777?
Новые игроки могут получить бонус за регистрацию. Также доступны акции.
3. Как обналичить средства в Азино 777?
Чтобы получить выигрыш нужно указать реквизиты и подтвердить запрос. Транзакция занимает 1-3 дня.
4. Есть ли мобильное приложение у Азино777?
Да, казино Азино777 предлагает мобильную версию, которое работает на любых устройствах.
I don’t even know how I ended up here, but I thought this post was good.
I don’t know who you are but definitely you’re going to a famous blogger if you aren’t already ;
) Cheers!
We constantly appreciate it if you can leave the setup
site clear and produce an open path to it also.
Pretty portion of content. I just stumbled upon your blog and in accession capital to
claim that I acquire in fact enjoyed account your weblog posts.
Any way I’ll be subscribing in your feeds and even I fulfillment
you get right of entry to consistently quickly.
Pretty great post. I simply stumbled upon your blog and wanted
to mention that I’ve truly loved surfing around your weblog posts.
In any case I’ll be subscribing on your feed and I hope you write once more very soon!
It’s in reality a nice and helpful piece of information. I am
glad that you just shared this helpful information with us.
Please keep us informed like this. Thank you for sharing.
Saved as a favorite, I love your blog!
I do not even understand how I stopped up here, but I assumed this put up was once
good. I do not recognise who you are however definitely you are
going to a well-known blogger when you aren’t already.
Cheers!
Kudos, An abundance of facts!
RP888
I really like what you guys are up too. Such clever work and exposure!
Keep up the awesome works guys I’ve added you guys to my own blogroll.
I love your blog.. very nice colors & theme. Did you design this website yourself or did you hire someone to do it for you?
Plz reply as I’m looking to design my own blog and would like to know
where u got this from. cheers
I would like to thank you for the efforts
you’ve put in writing this site. I really hope to see the same high-grade content by you in the future
as well. In truth, your creative writing abilities has encouraged me
to get my own site now 😉
Awesome blog! Is your theme custom made or did you download it from somewhere?
A design like yours with a few simple adjustements would really make my
blog stand out. Please let me know where you got your design. Thanks
Excellent, what a website it is! This webpage gives useful data to us,
keep it up.
I do not even know how I ended up here,
but I thought this post was great. I do not know who you are but definitely you’re going to a famous blogger if you are not already
😉 Cheers!
It is in reality a great and useful piece of information. I
am happy that you shared this useful information with us.
Please stay us up to date like this. Thanks for sharing.
It’s perfect time to make a few plans for the long run and it is time to be happy.
I’ve learn this post and if I may just I desire to suggest you some attention-grabbing issues
or advice. Perhaps you could write subsequent articles referring to this article.
I wish to read more things about it!
I couldn’t resist commenting. Very well written!
Hey I know this is off topic but I was wondering
if you knew of any widgets I could add to my blog that automatically tweet
my newest twitter updates. I’ve been looking for a plug-in like this for quite
some time and was hoping maybe you would have some experience with something like this.
Please let me know if you run into anything.
I truly enjoy reading your blog and I look forward to your new updates.
Добро пожаловать в Jetton Casino – мир развлечений и больших выигрышей.
В нашем казино вас ждёт широкий выбор игр,
щедрые акции и незабываемые впечатления.
Регистрируйтесь и получайте бонусы для успешного старта.
Почему выбирают Джеттон казино для Android?
Мы предлагаем честную игру,
моментальные выплаты и круглосуточную поддержку.
Здесь вас ждут регулярные турниры, кэшбэк, фриспины и персональные бонусные
предложения.
Огромный выбор игровых автоматов,
рулетки, покера и лайв-игр.
Регулярные акции и персональные предложения.
Быстрые выплаты и безопасные транзакции без задержек.
Соревнования для самых азартных игроков с ценными
призами.
Откройте для себя лучшие игровые возможности вместе
с Jetton Casino. https://jetton-casinoempire.skin/
This is a topic which is close to my heart… Many thanks!
Where are your contact details though?
This is a great article!
Helⅼo, i feel that i sаԝ you visited my site thսs i camе to go back thе prefer?.I’m attempting t᧐ to find issues to
enhance mу site!І guess іtѕ good enouɡh to սse a few of your ideas!!
Feel free to visit mү hоmepage: Online Betting
Hi there mates, its wonderful paragraph regarding cultureand entirely explained,
keep it up all the time.
What’s up i am kavin, its my first time to commenting anywhere, when i read this piece of writing i thought i could also make comment
due to this sensible paragraph.
Pretty! This has been an incredibly wonderful article. Many thanks for supplying these details.
Helpful information. Fortunate me I found your web site by chance, and I’m stunned why this accident didn’t happened earlier!
I bookmarked it.
I am not sure where you are getting your info, but great topic.
I needs to spend some time learning much more or understanding more.
Thanks for great info I was looking for this info for my mission.
Hello, i read your blog occasionally and i own a similar
one and i was just wondering if you get a lot of spam feedback?
If so how do you prevent it, any plugin or anything you can advise?
I get so much lately it’s driving me mad so any help
is very much appreciated.
Can I just say what a comfort to uncover an individual
who truly knows what they are discussing online. You actually
realize how to bring an issue to light and make it important.
A lot more people ought to read this and understand this side of your story.
I was surprised you’re not more popular because you
certainly possess the gift.
Hello, Neat post. There is a problem with your site in internet explorer, could check this?
IE still is the market chief and a large portion of folks will miss
your excellent writing because of this problem.
Very well said.
I’m no longer positive the place you are getting your information, but great
topic. I must spend a while studying more or working out
more. Thanks for magnificent info I used to be searching for this information for my mission.
The first father and son to play together on the same NHL team were
Gordie Howe and his son Mark Howe. They played together
for the Hartford Whalers during the
Read more
Ice Hockey
+2
What was the Toronto Maple Leafs record at the Mutual Street Arena?
Asked by Anonymous
Ice Hockey
+2
Bobby Orrs sons what do they do forwork?
Asked by Anonymous
Ice Hockey Memorabilia
+3
When did Wayne Gretzky become captain of the oilers?
Asked by Anonymous
Ice Hockey History
+1
What is a Hockey puck impact on environment?
Asked by Anonymous
Ice Hockey
+2
Where are the goals located on a ice rink?
Asked by Anonymous
The ice hockey goals are positioned at each end of the rink, in front of the net.
Each goal consists of a frame and a net where players aim to shoot the puck to
Read more
Ice Hockey
+2
What is the largest NHL fight ever?
Asked by Anonymous
The largest NHL fight ever occurred on March 11, 2004 in a game between the
Ottawa Senators and Philadelphia Flyers, known as the “Brawl in Hockeytown.&quo
Read more
Ice Hockey
+2
Is there any portuguese player on NHL?
Asked by Anonymous
Mike Ribiero of the Dallas Stars is of Portugese decent
Добро пожаловать в Jetton Casino
– ваш личный мир развлечений и крупных
выигрышей. В нашем казино вас ждут топовые игровые автоматы,
рулетка, покер и эксклюзивные акции.
Откройте для себя новые возможности вместе с нами и начните
выигрывать прямо сейчас.
Почему выбирают Джеттон игра на криптовалюту?
Мы ценим каждого игрока и создаем лучшие условия для комфортной игры.
Еженедельные турниры, программы лояльности и персональные подарки делают игру еще интереснее.
Ваши финансы и личные данные в полной безопасности.
Популярные игры от ведущих разработчиков.
Персональные предложения и приятные сюрпризы.
Быстрое пополнение счета и моментальный вывод
выигрышей.
Конкурсы для азартных игроков с ценными наградами.
Jetton Casino – это идеальное место для тех, кто любит азарт и большие выигрыши. https://jetton-casinochampion.makeup/
To establish your qualification for any one of our layaway plan,
speak to a participant of our team today.
Nice post. I was checking constantly this blog and I am impressed!
Very useful information specially the closing part 🙂 I handle such
info a lot. I used to be seeking this certain info for a
long time. Thanks and good luck.
This is a great article!
I’m not that much of a online reader to be honest but your sites really nice,
keep it up! I’ll go ahead and bookmark your website to come back down the road.
All the best
wireless headphones are the best because they do not have those bulky wires;;
This is a great article!
Hello to every single one, it’s in fact a
pleasant for me to pay a quick visit this web page, it consists of valuable
Information.
Quality content is the secret to interest the viewers to
pay a quick visit the web site, that’s what this site is
providing.
That is a really good tip especially to those new to the blogosphere.
Brief but very accurate info… Thank you for sharing this one.
A must read post!
Thank you for the auspicious writeup. It actually was
once a leisure account it. Glance complex to far introduced agreeable from
you! By the way, how could we keep in touch?
Greetings I am so happy I found your weblog, I really found you by
mistake, while I was searching on Bing for something else, Anyways I am here now and would just
like to say many thanks for a marvelous post and a all round exciting blog (I also love the theme/design), I don’t have time to browse it all at the minute but I have
book-marked it and also added your RSS feeds, so when I have time I will be back to read a great deal more, Please do keep up the fantastic job.
I was very pleased to uncover this web site. I want to to thank
you for ones time for this fantastic read!! I definitely appreciated every part of it and I
have you book-marked to see new information on your website.
Hi there! I simply would like to give you a huge thumbs up for the great information you have got right here on this post.
I will be returning to your site for more soon.
Ridiculous story there. What happened after? Thanks!
This is a topic that’s near to my heart… Best wishes! Where are your contact details though?
Никаких устаревших данных — на данном сайте размещена только самая свежая ссылка на [url=http://mdm01.site]мега мориарти[/url].
I have been exploring for a little bit for any high-quality articles or
weblog posts on this kind of space . Exploring in Yahoo I at
last stumbled upon this site. Studying this information So i am satisfied to
show that I have a very just right uncanny
feeling I discovered just what I needed. I so much unquestionably will
make sure to don?t forget this website and provides it a
glance on a relentless basis.
Good post! We are linking to this particularly great post on our
site. Keep up the great writing.
I am regular reader, how are you everybody? This post posted at this
site is really pleasant.
Different A/C devices have different effectiveness rankings, depending on their age and dimension.
Hi there friends, nice paragraph and nice urging commented here, I am actually enjoying by these.
I am really impressed with your writing skills as well as with the layout on your
weblog. Is this a paid theme or did you modify it yourself?
Anyway keep up the excellent quality writing, it is rare to see a nice
blog like this one these days.
Hello there, You have done an excellent job.
I’ll certainly digg it and personally recommend to my friends.
I’m sure they’ll be benefited from this web site.
I know this web page provides quality dependent articles and other
data, is there any other web page which presents these kinds
of things in quality?
Excellent blog! Do you have any helpful hints for aspiring writers?
I’m hoping to start my own website soon but I’m a little lost
on everything. Would you suggest starting with a free platform like WordPress
or go for a paid option? There are so many options out there that
I’m completely overwhelmed .. Any recommendations?
Appreciate it!
Usually I do not learn post on blogs, but I wish to say that this write-up very compelled me to check out and do so!
Your writing taste has been surprised me. Thank you, quite
nice article.
Hello mates, its fantastic article about teachingand fully explained,
keep it up all the time.
Does your website have a contact page? I’m having problems locating
it but, I’d like to send you an email. I’ve got some recommendations
for your blog you might be interested in hearing. Either way, great blog
and I look forward to seeing it grow over time.
Рады приветствовать вас в Анлим Казино,
где захватывающие игры и щедрые выигрыши сливаются в идеальную комбинацию.
Здесь игроки могут выбрать огромное
количество игр, включая
игровые автоматы, карточные игры, а также
принять участие в акциях и выиграть большие бонусы.
Как бы вы ни играли, мы предложим все, что
нужно для отличной игры.
Анлим Казино предоставляет высококачественные услуги и множество
способов выигрыша. Присоединяйтесь
к игрокам, которые уже выигрывают, и успешно участвуйте
в акциях. Вас ждут щедрые бонусы для увеличения ваших шансов на успех.
Что делает нас особенными?
Моментальная регистрация — начните играть в пару кликов.
Увлекательные бонусы для новичков — больший шанс
на успешный старт.
Частые турниры и акции — для тех, кто
хочет повысить свои шансы на выигрыш
и получить дополнительные призы.
Поддержка 24/7 — всегда готовы помочь по любым вопросам.
Мобильная версия — играйте в любимые игры в любое время и в любом месте.
Пришло время выигрывать! Присоединяйтесь к Анлим Казино и наслаждайтесь прямо сейчас. https://unlim-casinoodyssey.site/
If you are looking for a reputable and high-quality bookmaker, 8kbet is an excellent choice.
8kbet offers a wide range of exciting betting games, from
sports and casino to card games, with an easy-to-use interface and high security systems.
Specifically, the website 8kbetlol.com constantly updates special offers
and promotions to serve players. Try it now at 8kbetlol.com
and enjoy wonderful moments of entertainment. Additionally, 8ket com is another option worth
exploring.
Mostbet Türkiye – güvenilir bir platformdur bonuslar kazanmak isteyenler için mükemmeldir.
Mostbet – mobilní dostupnost.
I think everything wrote was very reasonable. However, consider this,
suppose you added a little information? I mean, I don’t wish to
tell you how to run your website, but what if you added a title to maybe get
people’s attention? I mean SMI diamond grinding wheels is a little plain.
You should peek at Yahoo’s front page and watch how they create news
headlines to grab people to open the links. You might add a related video
or a related pic or two to get readers excited about everything’ve written. Just my opinion, it could make your posts a little
bit more interesting.
I’m curious to find out what blog platform you have been utilizing?
I’m having some small security issues with my latest blog and I’d like to find something more risk-free.
Do you have any suggestions?
Good day! This is my first visit to your blog! We are a team of volunteers and starting a new initiative in a community
in the same niche. Your blog provided us beneficial information to work on. You have done a marvellous
job!
Great post.
Mighty Dogg Roofing
8110 East 126th St S
Bixby, OK 74008, United Ѕtates
19182125646
durable hail-Resistant roof Upgrades
We’re a group of volunteers and starting a brand new scheme in our community.
Your web site offered us with useful information to work on. You
have performed a formidable job and our entire group can be thankful to you.
Mostbet – soporte disponible 24/7.
Mostbet Bangladesh ilə qeydiyyat sadə və sürətlidir Mostbet Bangladesh (https://shonarbangladesh.com/)
Mostbet Casino PT – diversão garantida para jogadores. Oferece jogos de alta qualidade . Mostbet Casino PT [https://oambidestro.pt/]
Спорттық ставкалар Mostbet – кең ауқымды мүмкіндіктер ұсынады Aviator ойыны сүйінушілеріне. https://pflalmaty.kz/
An intriguing discussion is definitely worth comment.
I do believe that you need to publish more on this issue, it
may not be a taboo subject but usually folks don’t discuss these topics.
To the next! Best wishes!!
Your style is very unique compared to other people I have read stuff from.
Many thanks for posting when you have the
opportunity, Guess I will just book mark this web site.
Hi, I log on to your blogs daily. Your story-telling style is awesome, keep it up!
Azino777: Экспертное мнение
Азино777 — это известное онлайн-казино, которое привлекает внимание гемблеров благодаря разнообразию развлечений. Официальный сайт Азино777 предлагает удобный интерфейс, что делает его отличным решением для всех любителей азарта https://azino777-bonus-official-site-zerkalo-casino-1.online/.
Почему выбирают Азино 777
Azino777 выделяется среди других платформ благодаря следующим плюсам:
Разнообразие развлечений: На платформе Azino777 представлены сотни игровых автоматов от топовых разработчиков.
Выгодные предложения: Новые игроки могут получить приветственный бонус.
Надежные транзакции: Азино 777 поддерживает различные платежные системы.
Игра на смартфоне: Делать ставки можно в любое время.
Как начать играть в Азино777
Для старта в казино Азино777, нужно пройти регистрацию. Процесс занимает пару шагов:
Откройте сайт Азино777.
Введите необходимую информацию.
Активируйте аккаунт.
После этого вы сможете сделать депозит и воспользоваться акцией.
Ассортимент казино Азино 777
Azino777 предлагает широкий выбор игр:
Игровые автоматы: Видео слоты с различными тематиками.
Настольные игры: Американская рулетка, блэкджек.
Прогрессивные слоты: Шанс выиграть жизнь-изменяющий приз.
Защита данных в Азино 777
Азино 777 работает на основе законного разрешения, что гарантирует честность игрового процесса. Личная информация пользователей защищены с помощью надежных методов.
FAQ: Часто задаваемые вопросы
1. Как зарегистрироваться в Азино777?
Создание аккаунта занимает несколько минут. Перейдите на сайт, введите данные и подтвердите регистрацию.
2. Какие бонусы предлагает Азино777?
Новые игроки могут получить бонус за регистрацию. Также регулярно проводятся акции.
3. Как обналичить средства в Азино 777?
Для вывода средств нужно выбрать способ оплаты и подтвердить запрос. Вывод занимает несколько часов.
4. Как играть в Азино 777 с телефона?
Конечно, Azino777 предлагает приложение, которое работает на Android.
Mostbet oferuje bogatą gamę gier kasynowych . Oferta jest bogata . Dołącz do społeczności Mostbet już dziś! https://mostbet-polsce.pl/
Mostbet UZ – bu ajoyib imkoniyatlar taklif qiladi , bunda siz sport tikish imkoniyatiga ega bo’lasiz. Ro’yxatdan o’ting va doimiy cashback va aktsiyalardan foydalaning. https://mostbetkirish.com/
A fascinating discussion is definitely worth comment. I do think that you need to write more about this issue, it may not be a taboo subject but usually people don’t talk about these issues.
To the next! Many thanks!!
Cooling devices not serviced in over 6 months will create unpleasant microorganisms.
Hi there colleagues, fastidious piece of writing and pleasant arguments commented here, I am genuinely enjoying by these.
This is a great article!
This article will assist the internet viewers for creating new weblog or even a blog from start
to end.
Ridiculous story there. What happened after? Good luck!
Exactly the info I needed.
Hi there, yes this paragraph is really fastidious and
I have learned lot of things from it about blogging.
thanks.
Hello, i feel that i saw you visited my web site thus i came to go back the choose?.I’m attempting to
in finding things to improve my site!I guess its adequate to make use of some
of your concepts!!
Hi there this is somewhat of off topic but I was wondering if blogs use WYSIWYG editors or if
you have to manually code with HTML. I’m starting a blog soon but
have no coding expertise so I wanted to get advice from someone with experience.
Any help would be greatly appreciated!
Its like yօu reɑd my mind! Ⲩoᥙ appear
to know a lot aboᥙt this, like yoᥙ wrote tһе book іn it
or somеthing. I think thɑt you can do wіth some pics to drive the message һome а bit, but instead of tһаt, this
is grеаt blog. Аn excellent reаd. Ι wіll definitely bе back.
Alsо visit my homepaɡе – Online Betting
Having read this I believed it was extremely informative.
I appreciate you taking the time and energy to put this
informative article together. I once again find myself
personally spending a lot of time both reading and posting comments.
But so what, it was still worthwhile!
食堂カフェpotto×タニタカフェ フレンドタウン交野店
Description:
交野市でレストランなら「食堂カフェpotto×タニタカフェ フレンドタウン交野店」がおすすめです。大阪府交野市星田北に位置する、健康と美味しさを両立したカフェレストラン。「カラダにイイ、ココロにイイ」をコンセプトに、タニタカフェと食堂カフェpottoの魅力が融合した、気軽に立ち寄れる上質な空間です。
Keyword:
交野市 レストラン
Address:
〒576-0017 大阪府交野市星田北2丁目26-1 フレンドタウン交野店 1F
Phone:
0728078557
GoogleMap URL:
https://maps.app.goo.gl/Wxq7258kcDDRZeR89
Category:
レストラン
Trusted as the Best Link Indexer Tool & Service Since 2011!
Write more, thats all I have to say. Literally,
it seems as though you relied on the video to make your
point. You clearly know what youre talking about, why throw away
your intelligence on just posting videos to your blog when you could be
giving us something informative to read?
Simply wish to say your article is as amazing.
The clearness in your post is just cool and i could assume you’re
an expert on this subject. Well with your permission allow me to grab your RSS feed to keep
updated with forthcoming post. Thanks a million and please continue the enjoyable work.
Hello mates, fastidious piece of writing and
pleasant arguments commented at this place, I am actually enjoying by
these.
I don’t even understand how I stopped up here, but I assumed this post used to be good.
I do not realize who you might be but definitely you are going to a famous blogger in the event you
aren’t already. Cheers!
magnificent points altogether, you simply gained a new reader.
What might you recommend in regards to your
publish that you made a few days in the past?
Any positive?
Its like you read my mind! You appear to understand so much approximately
this, like you wrote the e-book in it or something. I think that you
simply could do with some p.c. to drive the
message house a bit, however instead of that, that is great blog.
A great read. I will definitely be back.
This is a great article!
FB-Laser: Your dependable supplier of high-performance
laser diodes
Our laser diodes serve medical, industrial, and
scientific fields with high performance
Our efficient shipping and expert support make sure you
get the best solution for your needs
Explore our range of cutting-edge laser diodes and elevate your projects today
Your mode of explaining everything in this piece of writing is genuinely good, every one be capable of simply be aware
of it, Thanks a lot.
Searching for high-performance laser diodes?
FB-Laser offers premium laser diodes for medical, industrial,
and scientific applications
Our diodes are renowned for their efficiency and reliability
Shop with us for fast delivery, expert advice, and exceptional customer care
Boost your technology with our innovative laser solutions
I don’t even know how I finished up right here, but I thought
this publish was good. I don’t know who you’re but definitely you’re
going to a famous blogger if you are not already. Cheers!
You could definitely see your skills within the article you
write. The world hopes for more passionate writers such as you who aren’t afraid to
mention how they believe. All the time follow
your heart.
It’s amazing to pay a quick visit this web page and reading the views of all friends on the topic
of this article, while I am also keen of getting experience.
This is a great article!
Hello there! This is kind of off topic but I
need some guidance from an established blog. Is it difficult to set up your own blog?
I’m not very techincal but I can figure things out pretty fast.
I’m thinking about setting up my own but I’m not sure where to
start. Do you have any tips or suggestions?
Appreciate it
Yes! Finally something about кредит Украина.
I love your blog.. very nice colors & theme. Did you design this website yourself
or did you hire someone to do it for you? Plz respond
as I’m looking to design my own blog and would like to find out where
u got this from. many thanks
Feel free to surf to my web-site macauslot 88
Pretty nice post. I just stumbled upon your blog and wished to say that I have really enjoyed surfing around your blog posts.
In any case I will be subscribing to your feed
and I hope you write again soon!
Hello, I think your site might be having browser compatibility issues.
When I look at your website in Chrome, it looks fine but when opening in Internet Explorer,
it has some overlapping. I just wanted to
give you a quick heads up! Other then that, awesome blog!
I enjoy looking through an article that will make men and women think. Also, thanks for permitting me to comment.
Have you ever considered writing an e-book or guest authoring on other websites?
I have a blog centered on the same ideas you discuss and would love to have you share
some stories/information. I know my subscribers would enjoy your work.
If you are even remotely interested, feel free to
send me an e-mail.
Bonusurile Mostbet – sigur și protejat . https://mostbet-cazinoului.com/
Heya i’m for tthe primary time here. I found this board and I in finding It truly helpful & it helped me
out a lot. I hppe to give something back and aid
others such as you aided me.
Revieww my page: Granite Headstones
Mostbet Azərbaycan – sürətli və asandır.
Idman mərcləri və kazino oyunlarını bir arada tapın . https://mostbet-aze-giris.com/
I love your blog.. very nice colors & theme. Did you create this website yourself or did yoou
hire someone to do it for you? Plz answer back
as I’m looking to create my own blog and would like to find
out where u got this from. thanks https://ezonnerecruit.com/employer/academic-writer-resume/
Vedonlyönti MostBet – erinomainen valinta aloittelijoille . https://jyvaskylankiri.fi/
Mostbet вход – удобный вариант для получения приветственных бонусов. https://betservise.com/
Готовы к незабываемым эмоциям? Добро пожаловать в 1GO Casino – лучшее место, где доступны популярные игры от мировых провайдеров. Присоединяйтесь уже сегодня и используйте бонусы для больших побед. https://1go-level.buzz/support и начните свое приключение 1GO Casino!
Почему стоит выбрать именно нас?
Огромный выбор игр – более 3000 слотов с высоким RTP.
Щедрые бонусы – персональные награды обновляются регулярно.
Моментальные транзакции – поддержка криптовалют и e-wallets.
Интуитивный дизайн – доступность на всех устройствах.
Дружелюбная команда – оперативная помощь 24/7.
Испытайте азарт по-настоящему и наслаждайтесь каждой ставкой!
We absolutely love your blog and find many of your post’s
to be exactly what I’m looking for. can you offer guest writers to write content available for you?
I wouldn’t mind publishing a post or elaborating on many of the subjects you write with regards to here.
Again, awesome web log!
hi!,I love your writing so so much! proportion we kep up a correspondence more approximately your article on AOL?
I require an expert in this space to unravel my problem.
Maybe that’s you! Taking a loiok forward to peer you. https://Somportal.com/employer/creative-academic-paper-writer/
You’re so awesome! I don’t suppose I’ve read through anything
like that before. So good to discover another person with some original thoughts on this topic.
Really.. thank you for starting this up. This web site is something that’s
needed on the web, someone with a little originality!
FB-Laser is your trusted source for premium laser diodes
We offer efficient and reliable laser diodes for medical,
industrial, and research applications
Enjoy quick shipping and expert customer service, ensuring
the right solutions for your laser requirements
Get started today with our high-quality laser diodes
Sportwetten Mostbet – sichere Plattform für Casino-Spiele .
I always emailed this website post page to all
my associates, as if like to read it next my links will too.
This is a great article!
Mostbet Chile – experiencia de usuario personalizable.
Inscrivez-vous dès maintenant – accessible à tous. https://mostbet-africa.fr/
I went over this internet site and I think you have a lot of excellent info , saved to my bookmarks (:.
I discovered your blog site internet site on the search engines and appearance a few of your early posts. Keep on the very good operate. I recently extra the Rss to my MSN News Reader. Looking for toward reading more by you at a later time!…
i love cougars that’s why i love to watch Desperate Housewives and also Cougar Town*
each time i used to read smaller content that as well clear
their motive, and that is also happening with this paragraph which I am reading at this place.
Hi there just wanted to give you a quick heads up. The words in your content seem to be running
off the screen in Internet explorer. I’m not
sure if this is a format issue or something to do with web browser compatibility but I figured
I’d post to let you know. The design and style look great
though! Hope you get the problem solved soon. Many thanks
Digital regulates or higher efficiency ratings usually
elevates the rate too.
Write more, thats all I have to say. Literally, it seems as though you relied on the video to make your point.
You definitely know what youre talking about, why waste
your intelligence on just posting videos to your blog when you
could be giving us something enlightening to read?
I am curious to find out what blog system you’re using? I’m experiencing some small security problems with my latest
blog and I would like to find something more secure. Do you have any recommendations?
These are genuinely fantastic ideas in concerning blogging.
You have touched some fastidious points here. Any way keep up wrinting.
When someone writes an piece of writing he/she retains the thought
of a user in his/her mind that how a user can be aware of it.
Thus that’s why this post is outstdanding. Thanks!
I am really inspired together with your writing skills as neatly as with the layout in your weblog.
Is that this a paid subject matter or did you customize it yourself?
Anyway keep up the excellent high quality writing, it’s rare to look a nice weblog like this one
these days..
Excellent blog! Do you have any hints for aspiring writers?
I’m planning to start my own site soon but I’m a little lost on everything.
Would you suggest starting with a free platform like WordPress or go for a paid option? There are so many choices out there that I’m totally overwhelmed ..
Any ideas? Thanks a lot!
This is the ratio between the air conditioning ability, in BTU,
and the power input, in watts.
Fantastic beat ! I would like to apprentice while you amend your web site,
how can i subscribe for a blog web site? The account helped me
a appropriate deal. I had been tiny bit familiar of this your broadcast provided
vibrant clear concept
Friend, this web site might be fabolous, i just like it
pay per click programs are really great, i could earn some decent cash from it-
Spot lets start work on this write-up, I really feel this web site needs considerably more consideration. I’ll oftimes be again to learn to read considerably more, thanks for that information.
When I originally left a comment I appear to have clicked on the -Notify me when new comments are added- checkbox and now every time a comment is added I get four emails with the same
comment. Perhaps there is a way you can remove me from
that service? Thanks!
However, this is not a simple inquiry which we
can answer exactly.
Have you ever considered about including a little
bit more than just your articles? I mean, what you say is valuable and all.
Nevertheless think about if you added some great pictures or video
clips to give your posts more, “pop”! Your content
is excellent but with images and video clips, this
site could definitely be one of the most beneficial in its field.
Great blog!
Хотите испытать настоящий азарт?
Добро пожаловать в Jetton Casino – инновационное казино, где каждый игрок
может найти огромный ассортимент развлечений.
Джеттон бесплатные спины и откройте для себя новый уровень
азарта!
В чем наши преимущества?
Популярные развлечения – слоты, рулетка,
покер, блэкджек.
Промо-предложения – бонусы на первый депозит, фриспины, кешбэк.
Мгновенные выплаты – вывод средств без скрытых комиссий.
Удобная навигация – адаптивный дизайн без ограничений.
Дружелюбные операторы – быстрое решение любых вопросов.
Начните выигрывать уже сегодня и получите максимум удовольствия!
I really love your site.. Very nice colors & theme.
Did you build this website yourself? Please reply back as I’m wanting to create my own personal
site and want to find out where you got this from or just what
the theme is called. Kudos!
Анлим Казино — это уникальная платформа, которая предлагает невероятные игровые возможности и потрясающий опыт для всех любителей азартных игр.
Здесь вы найдете большой выбор игровых автоматов, рулетки, а также интереснейшие турниры и акции, которые
могут значительно улучшить
ваши шансы на победу.
Мы рады предложить интуитивно понятным интерфейсом, широкой
коллекцией слотов и новыми настольными играми.
Ставки с высокими бонусами и регулярными
акциями сделают ваш игровой опыт еще более захватывающим.
Как стать частью нашего сообщества?
Легкая регистрация для начала игры — быстрое создание профиля и вы уже
готовы начать.
Приятные бонусы для новых игроков —
мы дарим вам бонусы при первом пополнении счета,
что дает отличное начало вашему игровому пути.
Ежедневные акции и турниры — для всех игроков, которые хотят приумножить свои шансы на победу и заработать
дополнительные призы.
24/7 поддержка, готовая помочь вам
с любыми вопросами или проблемами,
связанными с игрой.
Игры доступны на любом устройстве, так что
вы можете наслаждаться
процессом игры, будь то на ПК или смартфоне.
Присоединяйтесь к нам прямо сейчас!
В Анлим Казино вас ждут невероятные приключения, которые принесут вам
волну эмоций и шанс выиграть крупные призы.
Присоединяйтесь к нам и выигрывайте уже сегодня! https://unlim-777-casino.icu/
Добро пожаловать в Водка Казино — место, где
веселье встречается с невероятными бонусами и возможностями для выигрыша.
В нашем казино каждый игрок найдет свои любимые игры, независимо от того, начинающий вы или опытный игрок.
Здесь вас ждет не только удовольствие от игры, но и множество щедрых бонусов.
Все игры в Водка Казино имеют высокий
RTP, что увеличивает шансы на успешную игру.
Для вас мы подготовили интерактивные слоты, а также популярные
карточные игры, которые делают вашу
игру более увлекательной и
прибыльной.
Зачем стоять в очереди? Водка Казино предоставляет игрокам
мгновенную регистрацию и удобные способы пополнения счета, чтобы вы могли сосредоточиться на главном — выигрыше!
У нас всегда есть для вас интересные бонусы, которые позволят вам начать играть с дополнительным капиталом.
Присоединяйтесь к Водка Казино, чтобы
наслаждаться азартными играми с лучшими шансами на победу!
Мгновенная регистрация.
Привлекательные бонусы для новичков.
Регулярные турниры и акции для
тех, кто хочет увеличить свои шансы на выигрыш.
Поддержка 24/7 для решения любых вопросов.
Мобильная версия.
Погрузитесь в мир азартных игр с Водка Казино и испытайте удачу! https://vodka-777-spinwin.autos/
Mostbet Pakistan – transparent terms .
There is definately a lot to find out about
this issue. I love all the points you made.
Everything is very open with a clear description of the challenges.
It was truly informative. Your site is very useful.
Thanks for sharing!
This is a great article!
Regisztráljon a Mostbet-en – új játékosoknak csodálatos esély . https://elominivilag.hu/
Отримайте бонус та отримуйте призи . https://lelekakiev.com.ua/
I seriously love your site.. Very nice colors & theme.
Did you build this website yourself? Please reply back as I’m hoping to create my own personal site and want to know where
you got this from or what the theme is named. Kudos!
Here is my homepage; see here
This totals up to roughly 9 hours daily– adding ₤ 24 per week to your power expense.
Hello there, just became aware of your blog through Google, and found that it’s truly informative. I’m going to watch out for brussels. I’ll be grateful if you continue this in future. Many people will be benefited from your writing. Cheers!
Thank you for the good writeup. It in fact was a amusement account it. Look advanced to far added agreeable from you! However, how can we communicate?
sometimes you will need high power vacuum cleaners to just suck those dirt and dust that have accumulated over the years,.
whoah this weblog is wonderful i really like studying your articles.
Stay up the great work! You recognize, a lot of persons are hunting
round for this info, you could help them greatly.
Good day! This is my first visit to your blog! We are a collection of volunteers and starting a new initiative in a community in the
same niche. Your blog provided us beneficial information to
work on. You have done a outstanding job!
Hi there! I know this is kinda off topic but I was wondering which blog platform
are you using for this site? I’m getting fed up of WordPress because I’ve had problems with
hackers and I’m looking at options for another platform.
I would be great if you could point me in the direction of
a good platform.
This design is steller! You definitely know how to keep a reader amused.
Between your wit and your videos, I was almost moved to start my
own blog (well, almost…HaHa!) Fantastic job. I really loved what
you had to say, and more than that, how you presented it.
Too cool!
I am sure this post has touched all the internet visitors, its really
really nice post on building up new web site.
I would like to thank you for the efforts you’ve put in penning this blog. I am hoping to see the same high-grade content by you later on as well. In truth, your creative writing abilities has inspired me to get my very own blog now 😉
Having read this I thought it was rather informative. I appreciate you taking the time and effort to put this article together. I once again find myself spending a lot of time both reading and commenting. But so what, it was still worth it.
Excellent pieces. Keep writing such kind of information on your page.
Im really impressed by your blog.
Hi there, You have done an excellent job. I will certainly digg it and
for my part recommend to my friends. I’m confident they’ll be
benefited from this website.
Have a look at my blog :: MPOMAX slot
Howdy! This blog post couldn’t be written any better!
Reading through this article reminds me of my previous roommate!
He always kept preaching about this. I’ll forward this post to him.
Fairly certain he will have a great read. Thanks for sharing!
Somebody necessarily lend a hand to make seriously posts I would state.
That is the very first time I frequented your website
page and up to now? I amazed with the research you made
to make this particular publish amazing. Wonderful task!
Excellent article. I discovered the information highly useful. Adored the manner you detailed everything.
Nice post. I learn something new and challenging on websites I stumbleupon everyday.
It’s always useful to read through articles from other
authors and practice a little something from their websites.
I blog frequently and I genuinely thank you for your content. The article has truly peaked my interest. I am going to take a note of your website and keep checking for new information about once per week. I opted in for your RSS feed as well.
खेल पर दांव लगाने का मज़ा लें . https://zenterior.in/
This is a topic which is close to my heart… Cheers! Where can I find the contact details for questions?
If some one desires expert view on the topic of blogging and site-building afterward i suggest him/her to pay a visit this web site,
Keep up the good job.
This is a great article!
Mostbet – konkurrenskraftiga odds .
Do you have a spam issue on this website; I also am a blogger, and I was wondering your
situation; many of us have created some nice procedures and we are looking to swap
techniques with other folks, why not shoot me an email if interested.
Revolutionize your business workflow with the comprehensive control features
of Verizon Business Login. Engineered for IT administrators, our smart portal lets you
seamlessly:
• Monitor real-time network performance for every endpoint
• Streamline invoice processing with personalized analytics views
• Deploy new services in seconds without tech support
Discover enterprise-grade uptime with 99.9% network availability, backed
by our industry-leading customer support. Whether you’re setting
up cloud phones, optimizing network architecture, or protecting remote workers,
Verizon Enterprise delivers military-grade security and blazing 5G speeds.
Very nice post. I just stumbled upon your weblog and wanted to say
that I have really enjoyed browsing your blog posts.
After all I’ll be subscribing to your rss feed and I hope you write
again soon!
I’m not sure exactly why but this web site is loading incredibly slow for me. Is anyone else having this issue or is it a problem on my end? I’ll check back later and see if the problem still exists.
i love new product launches, i always attend events like those because i want to see some new stuffs“
Free online games… […]With havin so much content do you ever run into any problems of plagorism or copyright infringement? My website has a lot of completely unique content I’ve either authored myself or outsourced but it looks like a lot of it is popping it up all ov…
Mostbet বাংলাদেশ – সেরা পছন্দ জুয়ার উত্তেজনা জন্য। https://mostbet-bgd.com/
Hello, i believe that i saw you visited my weblog
so i got here to return the want?.I am attempting to in finding things to enhance
my site!I assume its adequate to make use of
a few of your ideas!!
We stumbled over here coming from a different website and thought I might as well check things out.
I like what I see so i am just following you. Look forward to looking into your web page
repeatedly.
Amazing things here. I’m very glad to see your article.
Thank you a lot and I’m having a look forward to touch you.
Will you please drop me a mail?
What’s Happening i’m new to this, I stumbled upon this I’ve found It positively useful and it has aided me out loads.
I’m hoping to give a contribution & help other users like
its helped me. Good job.
Hey! Do you know if they make any plugins to safeguard against hackers?
I’m kinda paranoid about losing everything I’ve worked hard on. Any recommendations?
You’ve made some really good points there. I looked on the web for additional information about the issue
and found most people will go along with your views on this web site.
Acquired air-con a few weeks ago for my home office, setup within a week which was spick-and-span, it looks fantastic.
There is definately a lot to find out about this topic. I really like all of the points you’ve made.
Woah! I’m really enjoying the template/theme of this
website. It’s simple, yet effective. A lot of times it’s challenging to
get that “perfect balance” between user friendliness and visual appearance.
I must say you have done a fantastic job with this.
Also, the blog loads super fast for me on Chrome.
Outstanding Blog!
I’ll immediately clutch your rss feed as I can’t
find your email subscription link or e-newsletter
service. Do you have any? Kindly let me understand in order that I could subscribe.
Thanks.
There’s definately a great deal to learn about this issue. I love all of the points you have made.
Nice respond in return of this issue with genuine arguments and explaining everything concerning
that.
You can put them in edges when not in use and their aesthetic look will blend in with your decoration.
Hi to all, the contents existing at this site are in fact
awesome for people experience, well, keep up the nice
work fellows.
constantly i used to read smaller articles that also clear their motive,
and that is also happening with this piece of writing which I am reading
here.
I blog quite often and I really thank you for your content.
The article has truly peaked my interest. I’m going to book mark your blog and keep checking for new details about once per week.
I opted in for your Feed as well.
A motivating discussion is worth comment. I do think that you need to publish more on this subject matter, it might not be a taboo matter but typically people don’t speak about such issues. To the next! Best wishes!
Wonderful beat ! I would like to apprentice while you amend your site, how can i
subscribe for a blog website? The account helped me a applicable deal.
I were a little bit familiar of this your broadcast provided vivid transparent concept
Безупречный клининг в Санкт-Петербурге: Ваш надежный партнер по наведению порядка!
Наша компания более 10 лет предоставляет услуги клининга в Санкт-Петербурге и заслужила признание как стабильный партнер. Мы гордимся опытом нашей команды, которая состоит из высококвалифицированных специалистов, прошедших обучение и обладающих все необходимые сертификаты. Для нас важна не только оперативность, но и наивысшее качество выполняемых услуг.
Не ждите, пока грязь и хаос станут катастрофой. Дайте нам шанс вернуть вашему пространству чистоту и порядок! Узнайте больше о наших услугах и отправьте заявку на сайте : https://ssjcompanyinc.official.jp/bbs/board.php?bo_table=free&wr_id=3110129
Greetings! I’ve been following your website for a long time now and finally got the courage to go ahead and give you a
shout out from New Caney Tx! Just wanted to say keep up the great job!
This is really interesting, You’re an overly skilled
blogger. I’ve joined your feed and look forward to in search of more of your excellent post.
Additionally, I’ve shared your site in my social
networks
So an enlightening article! I learned plenty from reading it. Your information is highly well-organized and easy to understand.
You could certainly see your skills in the article you write.
The sector hopes for more passionate writers like you who aren’t afraid to mention how they believe.
At all times follow your heart.
It makes it a lot easier for the electrical contractor when they pertain to aid you out.
Клубника Казино – это пространство для настоящих ценителей азартных игр, где каждый найдет свое место. Здесь вас ждут лучшие игры, выгодные предложения и уникальные возможности для победы. Наши игроки могут быть уверены в полной безопасности данных и честности игры, что делает процесс игры комфортным и надежным.
Почему стоит выбрать https://clubnika-casinoeuphoria.lol/? Присоединившись к Клубника Казино, вы получаете доступ к щедрым бонусам, бесплатным вращениям и регулярным акциям, которые значительно повысит ваши шансы на успех. В Клубника Казино вы можете быть уверены, что любые вопросы будут решены в кратчайшие сроки благодаря круглосуточной поддержке.
Когда стоит начать играть в Клубника Казино? Присоединяйтесь прямо сейчас и получите бонусы, которые помогут вам быстро начать зарабатывать большие выигрыши. В Клубника Казино вас ждут:
Щедрые бонусы для новичков и регулярные фриспины.
Примите участие в турнирах с большими призами и увеличьте свои шансы на удачу.
Обновления игр каждый месяц, чтобы не было скучно.
В Клубника Казино вы найдете все, что нужно для отличной игры и крупных выигрышей.
https://mostbet-egypt7.com/
Really enjoyed this entry. It gave a lot of useful insights. Great job on creating this.
Hi! I could have sworn I’ve been to this blog before but after looking at some of the articles I realized it’s new
to me. Regardless, I’m certainly happy I found it and I’ll
be bookmarking it and checking back regularly!
This article is great. I learned plenty from perusing it. The information is extremely enlightening and structured.
Excellent post. I found the information highly useful. Loved the method you explained all the points.
I have read so many posts concerning the blogger
lovers except this paragraph is in fact a nice piece of writing, keep it up.
I always used to read paragraph in news papers but now as I am a user of net so from now I am using net for articles or reviews, thanks to web.
An outstanding share! I’ve just forwarded this
onto a colleague who had been doing a little research on this.
And he in fact ordered me breakfast because I found it for him…
lol. So let me reword this…. Thanks for the meal!!
But yeah, thanx for spending time to talk about this subject
here on your web site.
Hello, yes this article is actually nice and I have learned lot of things from it
regarding blogging. thanks.
Do you have a spam issue on this site; I also am a blogger, and
I was wanting to know your situation; many of us have developed some nice procedures and we are looking to swap methods
with others, be sure to shoot me an email if interested.
This post is extremely educational. I genuinely appreciated reading it. The details is highly structured and straightforward to follow.
Excellent items from you, man. I’ve keep in mind your
stuff prior to and you’re just extremely excellent.
I actually like what you’ve got right here, certainly like what
you are saying and the way in which by which you are saying it.
You are making it entertaining and you still care for to stay it
wise. I can’t wait to read much more from you. That is really a wonderful
website.
Oh my goodness! Impressive article dude! Thanks, However
I am going through problems with your RSS. I don’t understand why I can’t join it.
Is there anybody else getting similar RSS problems? Anyone that knows the answer can you kindly respond?
Thanks!!
I am truly glad to glance at this weblog posts which consists of plenty of helpful facts, thanks
for providing such data.
That is really interesting, You are a very skilled blogger.
I have joined your rss feed and sit up for seeking extra of
your magnificent post. Also, I’ve shared your web site in my social networks
Ahaa, its pleasant discussion regarding this post here at this
weblog, I have read all that, so now me also commenting here.
Many thanks. Plenty of posts!
When you choose us to fix your air con systems, you can be certain to have made the very best option.
Thanks , I have recently been looking for info approximately this subject for ages and yours is the best I’ve came upon so far.
But, what about the bottom line? Are you positive about the supply?
Hi there, i read your blog from time to time and
i own a similar one and i was just wondering if you get a
lot of spam responses? If so how do you stop it, any plugin or anything you can recommend?
I get so much lately it’s driving me crazy so any help is very
much appreciated.
It is in reality a great and useful piece of info.
I’m happy that you just shared this helpful info with us. Please stay us up to date like this.
Thank you for sharing.
I used to be suggested this web site via my cousin. I am not certain whether or not this put up is
written through him as no one else recognise such specified approximately my trouble.
You’re amazing! Thank you!
Wow, fantastic blog format! How long have you ever been blogging for?
you made running a blog glance easy. The overall glance of your web site is wonderful,
as neatly as the content!
Super happy! Practical.
Excellent article. I thought the information very useful. Appreciated the method you clarified the content.
Hi there, just became aware of your blog through Google, and found that it is truly informative.
I am gonna watch out for brussels. I’ll be
grateful if you continue this in future. Lots of people will be
benefited from your writing. Cheers!
This excellent website certainly has all the info I wanted concerning this subject and didn’t know who to ask.
Came as expected. Totally worth it!
You have made some good points there. I checked on the net
for more information about the issue and
found most people will go along with your views on this site.
Spot on with this write-up, I truly feel this site needs a great deal more attention. I’ll probably be back again to read more, thanks for the info.
Both kinds have pros and cons, however there are some things to
remember prior to selecting.
Why people still use to read news papers when in this technological world the
whole thing is existing on net?
This is a great article!
Samsung is a globe leader in climate control services for
homes and services.
obviously like your web-site however you need to check the spelling
on quite a few of your posts. A number of them
are rife with spelling issues and I in finding it very bothersome to tell the reality nevertheless I’ll definitely come again again.
With havin so much content do you ever run into any problems of plagorism or copyright infringement?
My blog has a lot of exclusive content I’ve either created myself or
outsourced but it appears a lot of it is popping it up all over the web without my authorization. Do you know any techniques to help stop content from
being ripped off? I’d certainly appreciate it.
I like the valuable information you provide in your articles.
I’ll bookmark your blog and check again here regularly. I am quite sure I will
learn lots of new stuff right here! Best of luck for the
next!
Really appreciated reading this article. It’s very articulate and full of helpful details. Thanks for offering this.
Wow, awesome weblog layout! How long have you been blogging for?
you make blogging glance easy. The total look of your site is fantastic, as
neatly as the content material!
I simply couldn’t depart your website before suggesting that I
really loved the usual info an individual supply to your guests?
Is going to be again often to inspect new posts
Excellent post. I discovered the details very helpful. Loved the way you clarified all the points.
Be sure to obtain your air conditioning inspected up and tuned to boost
its span.
I just could not depart your site prior to suggesting that
I really loved the standard info a person provide for your
guests? Is gonna be back frequently to investigate
cross-check new posts
Good information. Lucky me I recently found your website by accident (stumbleupon). I have book marked it for later!
An outstanding share! I have just forwarded this onto a colleague who was conducting a little homework on this.
And he actually ordered me breakfast due to the fact that I discovered it for
him… lol. So let me reword this…. Thank YOU for the
meal!! But yeah, thanks for spending some time to discuss this issue here on your blog.
Hormat. Materi yang hebat.
That consists of laminate covers to protect your property and a full clean-up after work is completed.
The next time I read a blog, Hopefully it doesn’t disappoint me as much as this particular one. I mean, Yes, it was my choice to read, however I really thought you would have something interesting to say. All I hear is a bunch of complaining about something that you could fix if you weren’t too busy looking for attention.
With our head workplace in South East London, we
are well positioned to take care of enquiries from around London and the Home Counties.
Great article, exactly what I was looking for.
This allows for cooling down several areas or areas within an industrial space using a single system.
This is a great article!
When someone writes an piece of writing he/she keeps the
plan of a user in his/her brain that how a user can be aware of it.
Thus that’s why this paragraph is outstdanding. Thanks!
My developer is trying to convince me to move to .net from PHP.
I have always disliked the idea because of the costs.
But he’s tryiong none the less. I’ve been using Movable-type on a number of websites for about a year
and am concerned about switching to another platform.
I have heard great things about blogengine.net. Is there a
way I can import all my wordpress posts
into it? Any kind of help would be really appreciated!
I think the admin of this site is really working hard in support
of his web site, for the reason that here every data is quality
based data.
When I originally left a comment I appear to have clicked on the -Notify me when new comments are added- checkbox and from now on each time a comment is added I recieve four emails with the exact same comment. Perhaps there is a means you can remove me from that service? Thank you.
Wonderful blog! Do you have any recommendations
for aspiring writers? I’m planning to start my own website soon but I’m a
little lost on everything. Would you recommend starting with a
free platform like WordPress or go for a paid option? There are so many options out there that I’m totally overwhelmed ..
Any tips? Appreciate it!
I don’t know whether it’s just me or if perhaps everybody else encountering issues with your blog.
It appears like some of the text within your posts are running off
the screen. Can someone else please comment and let me know
if this is happening to them as well? This may be
a issue with my web browser because I’ve had this happen previously.
Thanks
I’ve been surfing on-line more than three hours nowadays, yet I never found any interesting article like yours. It is beautiful worth sufficient for me. Personally, if all site owners and bloggers made good content material as you did, the web shall be a lot more useful than ever before.
I read this paragraph fully regarding the difference
of most up-to-date and preceding technologies, it’s
amazing article.
Attractive portion of content. I just stumbled upon your website and
in accession capital to say that I get in fact loved account
your blog posts. Anyway I will be subscribing
to your feeds and even I fulfillment you get entry to constantly quickly.
Greetings! Very helpful advice in this particular article! It is the little changes that produce the greatest changes. Thanks a lot for sharing!
Wow, this post is fastidious, my younger sister
is analyzing such things, thus I am going to let know her.
Every weekend i used to pay a visit this site, as i wish for enjoyment, as this this
website conations actually nice funny material too.
It’s an remarkable paragraph designed for all the web people; they will
take benefit from it I am sure.
This is a great article!
An interesting discussion is definitely worth comment. I think that you should publish more about this issue, it might not be a taboo matter but generally people do not speak about these topics. To the next! Kind regards!
Perfect choice. Fantastic.
There’s definately a lot to know about this issue. I love all the points you made.
Really enjoyed reading this article. It’s highly clear and full of valuable insight. Thanks for sharing this.
Produto excelente e prático. Recomendo sem dúvidas.
Muito bom! Estou muito satisfeito.
This excellent website truly has all the information and facts I needed about
this subject and didn’t know who to ask.
It’s nearly impossible to find educated people on this topic, but you sound like you know what you’re
talking about! Thanks
Hmm it appears like your site ate my first comment
(it was super long) so I guess I’ll just sum it up what I
had written and say, I’m thoroughly enjoying your blog.
I as well am an aspiring blog blogger but I’m still new to the whole thing.
Do you have any recommendations for newbie blog writers?
I’d definitely appreciate it.
This is fantastic. I learned a lot from perusing it. The details is extremely enlightening and arranged.
This post is amazing! Full of useful information and very clear. Many thanks for sharing this.
New air conditioning systems may have a
lot of relocating components, which can be intimidating for a brand-new owner.
Appreciated this post. It’s very well-researched and full of helpful information. Excellent work!
Great site you’ve got here.. It’s hard to find quality writing like yours these days.
I truly appreciate individuals like you! Take care!!
Right now it appears like Expression Engine is the top
blogging platform available right now. (from what I’ve
read) Is that what you’re using on your blog?
Delivered quickly. Practical.
Thanks for finally writing about > SMI diamond grinding wheels < Liked it!
Every annually, these air conditioner units require servicing to guarantee they proceed running
successfully.
You are so awesome! I don’t think I’ve truly read something like that before. So wonderful to discover somebody with a few genuine thoughts on this subject. Really.. thank you for starting this up. This site is one thing that’s needed on the internet, someone with some originality.
It’s remarkable to go to see this web site and reading the views of
all friends about this post, while I am also keen of getting familiarity.
Does your website have a contact page? I’m having trouble locating it but, I’d like to send you an email.
I’ve got some recommendations for your blog you might be interested in hearing.
Either way, great site and I look forward to seeing it grow over
time.
We absolutely love your blog and find many of your post’s to be what
precisely I’m looking for. can you offer guest writers to write content for you personally?
I wouldn’t mind writing a post or elaborating on a few of the subjects you write regarding here.
Again, awesome website!
Terrific article. It’s extremely articulate and packed with useful information. Thanks for sharing this post.
Nice post. I learn something totally new and challenging on sites I stumbleupon everyday. It’s always useful to read content from other writers and use a little something from other websites.
Howdy, There’s no doubt that your web site could be having internet browser compatibility problems.
When I look at your site in Safari, it looks fine however, when opening in IE, it has some overlapping issues.
I simply wanted to provide you with a quick heads up!
Other than that, excellent blog!
Adored the insight provided in this article. It’s very clear and filled with valuable insight. Excellent work!
Thank you for the auspicious writeup. It in fact
was a amusement account it. Look advanced to far added agreeable from you!
By the way, how can we communicate?
Wow that was unusual. I just wrote an incredibly long comment
but after I clicked submit my comment didn’t appear.
Grrrr… well I’m not writing all that over again. Regardless, just wanted to say
superb blog!
Great article. I will be going through many of these issues as well..
You’ve made some decent points there. I looked on the internet for more information about the issue and found most people will go along with your views on this site.
Comedian Russell Brand’s Twitter page is still topped
by the slogan ‘Stay Free’ after he was charged with five sex offences against four women including rape.
Brand, 49, has the words, which are also the name of his weekday
podcast, emblazoned at the top of his profile, with an image stating:
‘Russell Brand Stay Free’.
It comes as he was today charged with one count each of rape, indecent assault and oral rape, as well
as two counts of sexual assault, relating to four separate women between 1999 and
2005.
Despite the charges, Brand has not yet made any public statement, although
is still advertising the Stay Free podcast as live on Rumble on weekdays.
On the podcast, Brand discusses news-making issues of the day, such
as the apparent ousting of Elon Musk from Donald Trump’s inner circle, the Netflix drama Adolescence,
and Kanye West.
Detectives began an investigation after Brand
was accused of rape, sexual assaults and emotional abuse by several women in a joint
investigation by The Sunday Times, The Times and Channel 4 Dispatches in September 2023.
The Metropolitan Police have now charged Brand, who is understood
to live in the US, by post and issued a court summons.
Brand has previously denied the accusations, and said all his sexual relationships were ‘absolutely always consensual’.
rand, 49, has the words, which are also the name of his weekday podcast,
emblazoned at the top of his profile, with an image stating: ‘Russell Brand Stay Free’
Russell Brand, pictured in London in October 2017, has been charged with
rape, oral rape, indecent assault and two counts
of sexual assault
But he has now been charged with the rape of a woman in 1999 in the
Bournemouth area and the oral rape and sexual
assault of a woman in 2004 in the Westminster area of London.
He has also been charged with indecently assaulting a woman in 2001 and sexually assaulting another woman between 2004 and 2005 –
both offences are alleged to have taken place in Westminster, London.
Detective superintendent Andy Furphy from the Metropolitan Police said: ‘The women who
have made reports continue to receive support from
specially trained officers.
‘The Met’s investigation remains open and detectives ask anyone who has been affected
by this case, or anyone who has any information, to come forward and speak with police.
A dedicated team of investigators is available via email at CIT@met.police.uk.
‘Support is also available by contacting the independent
charity, Rape Crisis at 24/7 Rape and Sexual Abuse Support Line.’
Brand will appear at Westminster Magistrates’ Court on Friday May
2.
Jaswant Narwal, of the Crown Prosecution Service, said: ‘We have today authorised the Metropolitan Police to charge Russell Brand with a number of sexual offences.
Russell Brand on stage at the Bitcoin Conference
at Music City Center in Nashville in July 2024
‘We carefully reviewed the evidence after a police investigation into
allegations made following the broadcast of a Channel 4 documentary
in September 2023.
‘We have concluded that Russell Brand should be charged with offences including rape, sexual
assault and indecent assault.’
In November 2024, the CPS confirmed that detectives from the
Metropolitan Police had passed on an evidence file regarding sex offence allegations
against Brand.
Brand, who presented a BBC Radio 2 show between 2006 and 2008, left
the role after his on-air prank, now known as Sachsgate, when he left a ‘lewd’ voicemail for Fawlty Towers actor Andrew Sachs about
his granddaughter.
He also presented on Big Brother spin-off shows Big Brother’s Big Mouth
and Big Brother: Celebrity Hijack in the noughties.
The TV and film star was married to US pop singer Katy Perry from 2010 to 2012 but is now married
to Laura Gallacher, the sister of presenter Kirsty, and the pair have two children.
Russell BrandLondon
Hey there are using WordPress for your site platform?
I’m new to the blog world but I’m trying to get started and create
my own. Do you require any html coding expertise to
make your own blog? Any help would be greatly appreciated!
Heya terrific website! Does running a blog such as this take a lot of work?
I’ve absolutely no expertise in coding however
I was hoping to start my own blog in the near future.
Anyhow, should you have any suggestions or
techniques for new blog owners please share. I know this
is off subject nevertheless I simply wanted to
ask. Cheers!
When I originally commented I seem to have clicked on the -Notify me when new comments are added- checkbox and from now on every time a comment is added I recieve four emails with the exact same comment. Perhaps there is a way you can remove me from that service? Thank you.
Thank you for another fantastic article. The place else could anybody get that
kind of information in such a perfect means of writing? I have a presentation subsequent week, and I’m on the look for
such info.
This article is fantastic. I learned a lot from perusing it. The content is very enlightening and arranged.
Kick back and appreciate your new residential cooling system –
it’s that easy!
Mesum
I blog frequently and I really thank you for your content.
The article has really peaked my interest. I am going to book mark your site and
keep checking for new information about once a week.
I opted in for your Feed too.
Hi there to every one, the contents present at
this web page are actually remarkable for people knowledge,
well, keep up the good work fellows.
Bokep
Thanks on your marvelous posting! I certainly enjoyed reading it, you might be a great author.
I will remember to bookmark your blog and will eventually come back down the road.
I want to encourage yourself to continue your
great writing, have a nice day!
I feel that is one of the such a lot significant information for me.
And i’m satisfied reading your article. However should
observation on few basic things, The web site taste is perfect, the articles is actually great : D.
Just right task, cheers
We offer bespoke Installation of refrigeration tools throughout London.
id=”Q4aWWk7z6EJL5FSrk3tZhQ”>Join Most Bet for Quick Sports
Betting Registration
Most Bet is rapidly gaining traction in the world of online sports betting,
offering a streamlined registration process that appeals to both novices and seasoned bettors.
The platform’s user-friendly interface ensures that users can quickly navigate through the registration steps,
allowing them to focus on what truly matters: placing their bets.
With a few simple clicks, new users can create an account and dive into the thrilling world of sports betting.
The registration process at Most Bet is designed to be swift and
efficient. Users are required to provide basic information such as their
name, email address, and preferred currency. Once these details are entered, an email verification step ensures the security of the account.
This straightforward process, with the Mostbet india login option, is complemented by a sleek design that
minimizes distractions, making it easier for users to complete their registration without unnecessary
hassle.
For those eager to start betting immediately, Most
Bet offers a seamless deposit system. New members can choose from a variety of payment methods including
credit cards, e-wallets, and even cryptocurrencies.
This flexibility allows users from different regions
to fund their accounts with ease. Moreover, Most
Bet often entices new registrants with attractive welcome bonuses, enhancing their initial betting
experience.
The platform also prioritizes user security and
privacy. By employing state-of-the-art encryption technologies, Most Bet ensures that all personal and financial information remains confidential.
This commitment to security not only protects users but also builds trust within the community.
As a result, bettors can focus on enjoying the
dynamic sports betting environment that Most Bet offers without worrying about potential risks.
Access Live Bets Instantly by Logging into Most Bet
Accessing live bets instantly is now a reality with Most Bet, a leading online bookmaker renowned for
its user-friendly interface and extensive
range of betting options. By simply logging into your account, you can dive
into the exhilarating world of live betting, where
every moment counts and fortunes can change in the blink of an eye.
The platform is designed to cater to both
seasoned bettors and newcomers, offering a seamless experience that keeps users engaged and informed.
One of the standout features of Most Bet is its commitment
to providing real-time updates and odds. As soon as you log in, you are greeted with a comprehensive dashboard that displays all ongoing matches and events across various sports.
Whether it’s football, basketball, tennis, or eSports, Most Bet covers it all.
The live betting section is particularly impressive, allowing users to place
bets on events as they unfold. This dynamic environment not only heightens the excitement but also offers
bettors the chance to capitalize on fluctuating odds.
For those looking to maximize their betting experience, Most Bet offers several advantages:
Wide Range of Sports: From mainstream sports like football and basketball to niche markets such as darts and snooker.
Competitive Odds: Ensuring that bettors get the best possible returns on their wagers.
Live Streaming: Watch events in real-time directly from
the platform.
User-Friendly Interface: Easy navigation makes placing bets quick and straightforward.
Security is another critical aspect where Most Bet excels.
The platform employs state-of-the-art encryption technologies to safeguard user data and transactions.
This ensures that every bet placed is secure, allowing users to focus solely on their strategies without worrying about privacy
concerns. Moreover, customer support is available around the clock, ready to assist with any queries or issues that may arise
during your betting journey.
By providing instant access to live bets coupled with a robust security framework and excellent
customer service, Most Bet sets itself apart as a top
choice for online betting enthusiasts. Its comprehensive
coverage of sports events worldwide ensures that there’s always something for everyone,
making it an indispensable tool for anyone looking to engage in live betting with confidence and ease.
Get the Most bet APK for Mobile Betting Convenience
For those seeking unparalleled mobile betting convenience, the Most bet APK stands out
as a top choice. This app offers users an intuitive interface,
ensuring that both seasoned bettors and newcomers can navigate effortlessly.
By downloading the Most bet APK, punters gain access to a
wide array of sports markets, live betting options,
and exclusive promotions that aren’t always available on desktop versions.
The seamless integration of features ensures that users
can place bets swiftly and securely from anywhere.
The Most bet APK is not just about placing bets; it’s about enhancing the
entire betting experience. Users can enjoy live streaming of
major sports events, keeping them in the loop with real-time updates.
Additionally, the app supports multiple payment methods, allowing for quick deposits and withdrawals.
Security is a priority, with advanced encryption protocols safeguarding user data.
For those who prioritize flexibility and reliability in their betting
activities, this APK is a game-changer.
Here’s what makes the Most bet APK a must-have for any mobile bettor:
User-Friendly Interface: Navigate with ease through various sports
and markets.
Live Betting & Streaming: Engage with events as they
unfold in real-time.
Exclusive Promotions: Unlock bonuses that are unique
to mobile users.
Secure Transactions: Trust in encrypted payment methods for peace of mind.
Moreover, the app’s performance is optimized for various devices, ensuring smooth operation even on older
smartphones. The developers have focused on reducing load times and minimizing data usage without
compromising on quality or functionality.
With regular updates, users can expect new features and improvements tailored to enhance their
betting journey. The Most bet APK is more than just an application; it’s a comprehensive platform designed
to cater to all your betting needs on the go.
Unlock Special Offers with the Most bet Promo Code
Unlocking special offers with the Most bet promo code can significantly enhance your betting experience.
Most bet, a prominent name in the online betting industry, is known for its user-friendly platform and
lucrative promotions. By using a promo code, bettors can access exclusive bonuses, such as free bets, deposit matches, or cashback offers.
These incentives not only increase the potential for higher returns but also provide an opportunity to explore various
sports markets without substantial financial risk.
To utilize a Most bet promo code effectively, users should first ensure they have an active account on the
platform. Registration is straightforward and typically requires basic
personal information. Once registered, players can enter
their promo code during the deposit process.
It’s crucial to read the terms and conditions associated with each offer, as they may include wagering requirements or restrictions on specific sports events.
Understanding these conditions ensures that bettors can fully benefit from the promotion without any unexpected
hurdles.
The allure of using a Most bet promo code lies in its ability to provide added value.
For instance, a common offer might include a 100%
deposit bonus up to a certain amount. This means if a bettor deposits $100, they
could receive an additional $100 in bonus funds.
Such promotions are particularly appealing during major
sporting events when the stakes are high and the excitement is palpable.
Moreover, these codes often come with flexible usage options, allowing bettors to apply
them across various sports like football, basketball, or tennis.
Engaging with Most bet’s promotional offers is not just about enhancing one’s bankroll;
it’s also about gaining more betting insights and strategies.
By having extra funds or free bets at their disposal, bettors can experiment
with different types of wagers such as accumulators or
system bets without fear of significant losses. This experimentation can lead to discovering new
favorite betting markets or strategies that could prove profitable in the long run. With
Most bet’s reputation for reliability and customer satisfaction, utilizing
their promo codes is a savvy move for both novice and seasoned bettors alike.
Engage in High Stakes Wins with the Aviator Game from Most
bet
Engage in high-stakes wins with the Aviator Game from Most
Bet, a leading name in the online betting world.
This thrilling game offers players a unique chance to test their
skills and luck, providing an exhilarating experience that combines strategy with excitement.
The game is designed for those who crave the adrenaline rush
of high-stakes betting, offering a seamless blend of anticipation and reward.
The Aviator Game is straightforward yet captivating.
Players place bets on a virtual plane’s flight path, predicting when it will take off before it flies away.
The longer the plane stays on the screen, the higher
the multiplier grows, increasing potential winnings exponentially.
However, if players wait too long and the plane flies away, they lose their stake.
This delicate balance between risk and reward makes the Aviator Game an enticing choice for thrill-seekers.
Feature Description
Game Type Virtual Betting
Minimum Bet $0.10
Maximum Multiplier 100x
RTP 97%
Availability Desktop & Mobile
Most Bet ensures that its platform is user-friendly and accessible, allowing players to engage with the Aviator Game anytime, anywhere.
The bookmaker provides robust security measures to protect user
data, ensuring a safe and fair gaming environment. With an impressive return-to-player (RTP) rate of 97%, participants have a
significant chance of winning big while enjoying a top-tier gaming experience.
For those looking to elevate their betting journey, Most Bet offers various promotions
and bonuses that enhance gameplay. These incentives
can significantly boost one’s bankroll, providing more opportunities to
engage in high-stakes action. The Aviator Game stands out
as a premier choice for those seeking both entertainment and
substantial rewards in the dynamic world of online betting.
Explore Betting Strategies in the Most Bet Review
Exploring betting strategies at Most Bet can be a thrilling
endeavor for both novice and seasoned bettors. This bookmaker, known for its user-friendly interface and diverse market offerings, provides ample opportunities to refine one’s betting acumen. A fundamental strategy often employed is the value betting approach.
Here, bettors look for odds that seem to undervalue
the likelihood of an event occurring. By consistently identifying these discrepancies, punters can increase their
potential for profit over time.
Another popular strategy is hedging bets, which involves placing bets on different outcomes to
minimize risk. This technique can be particularly useful in live betting scenarios where odds fluctuate rapidly.
Most Bet’s dynamic platform allows users to quickly adjust their bets in real-time,
capitalizing on changing circumstances to secure a favorable outcome.
This method requires a keen eye and swift decision-making
but can significantly enhance one’s betting portfolio.
For those looking to leverage statistical insights, the Martingale system might
be appealing. This strategy involves doubling your bet after every loss,
with the idea that an eventual win will recover all previous losses plus gain a profit equal to the original stake.
While potentially lucrative, it’s crucial to set limits and understand the risks involved, as a prolonged losing streak can quickly deplete one’s bankroll.
Lastly, exploring arbitrage betting can offer guaranteed profits by exploiting differing
odds across multiple bookmakers. Although challenging due to the need
for constant monitoring and quick action, Most Bet’s
comprehensive market coverage makes it an ideal platform for
this strategy. By placing bets on all possible outcomes
of an event across different platforms where odds allow for profit regardless of
the result, bettors can secure a risk-free return.
Author mvorganizing.orgPosted on 7 March 2025Categories Blog
I don’t even know how I ended up here, but I thought this post was good.
I do not know who you are but definitely you’re
going to a famous blogger if you are not already ;
) Cheers!
Good post. I learn ѕomething new and challenging оn websites I
stumbleupon eveгy day. It ᴡill always
be intеresting to read throᥙgh content fгom ߋther writers ɑnd practice a littlе something from their sites.
my web page … Sports Betting
Wonderful blog! I found it while surfing around on Yahoo News.
Do you have any tips on how to get listed in Yahoo
News? I’ve been trying for a while but I never seem to get there!
Cheers
Awesome! Its really awesome article, I have got much clear idea concerning from
this post.
Bokep
Hello I am so happy I found your website, I really found you by error, while I was looking
on Bing for something else, Regardless I am here now and would just like to say many thanks for a
tremendous post and a all round entertaining blog (I also love the theme/design), I don’t have time to browse it all at the minute but I have book-marked it and also
added in your RSS feeds, so when I have time I will be
back to read more, Please do keep up the great work.
Memek
Hello, yes this piece of writing is genuinely nice and I have learned
lot of things from it on the topic of blogging. thanks.
Memek
I needed to thank you for this excellent read!! I certainly loved every bit of
it. I have you bookmarked to check out new stuff you post…
Porn
Thank you for every other informative web site. The place else could I am getting that
type of information written in such a perfect way? I’ve
a challenge that I’m just now operating on, and I have been on the look out for such info.
This is very interesting, You’re a very skilled blogger.
I’ve joined your rss feed and look forward to seeking more of your great post.
Also, I’ve shared your website in my social networks!
Memek
I have read so many posts regarding the blogger lovers except
this piece of writing is really a nice paragraph, keep it up.
Hey there! I’ve been reading your weblog for some time now and finally
got the courage to go ahead and give you a shout out
from Huffman Texas! Just wanted to tell you keep up the fantastic work!
Heya i’m for the primary time here. I found this board and I in finding It really useful & it helped me out
much. I hope to provide something again and help others such as you aided me.
There’s certainly a great deal to find out about this issue. I like all the points you’ve made.
Really enjoyed this article. It provided tons of valuable information. Fantastic work on creating this.
Kontol
Howdy! This post couldn’t be written much better!
Looking through this article reminds me of my previous roommate!
He continually kept preaching about this. I will send this information to
him. Pretty sure he will have a good read. Many thanks for sharing!
This article is wonderful! Full of useful details and highly articulate. Thank you for providing this.
Truly appreciated this article. It offered a lot of helpful insights. Great effort on writing this.
Adored this post. It’s very comprehensive and full of helpful insights. Fantastic work!
Terrific entry. It’s very well-written and full of beneficial details. Many thanks for sharing this content.
When you have actually the required parts, it is time to cut
an opening with the drywall.
Rates can differ anywhere between ₤ 170– ₤ 220 for presence out of regular functioning hours
and on the weekend break.
My developer is trying to convince me to move to .net from PHP.
I have always disliked the idea because of the costs.
But he’s tryiong none the less. I’ve been using Movable-type on a number of websites for
about a year and am concerned about switching to another platform.
I have heard good things about blogengine.net. Is there a way I can transfer all my wordpress posts
into it? Any help would be greatly appreciated!
You actually revealed this terrifically.
my blog post :: https://www.cucumber7.com/
Memek
We stumbled over here from a different page and
thought I may as well check things out. I
like what I see so now i am following you. Look forward to checking
out your web page for a second time.
Porn
Hi there everyone, it’s my first visit at this web page, and
piece of writing is genuinely fruitful in favor of me, keep up posting such
posts.
Mesum
You really make it seem so easy with your presentation but I find this matter to be
actually one thing that I feel I’d never understand.
It sort of feels too complex and very large for me.
I am looking forward on your next post, I’ll attempt to get the hold of
it!
Awesome post.
Mesum
When I initially commented I clicked the “Notify me when new comments are added” checkbox and now each
time a comment is added I get four e-mails
with the same comment. Is there any way you can remove me from that service?
Thanks!
Memek
Hey very nice blog!
It’s very straightforward to find out any topic on web as compared to textbooks, as I found this paragraph at this web site.
Mesum
It’s amazing to pay a quick visit this web page and reading the
views of all friends on the topic of this piece of writing, while I am also zealous of getting
experience.
Bokep
I’m impressed, I must say. Seldom do I come across a blog
that’s both equally educative and amusing, and without a doubt, you’ve hit the nail
on the head. The issue is an issue that not enough men and women are speaking intelligently about.
Now i’m very happy that I stumbled across this in my hunt for something concerning this.
Kontol
Hi there to every one, since I am truly eager of reading this
website’s post to be updated regularly. It consists
of fastidious data.
Mesum
Hello there, You have done an incredible job. I will certainly digg it and personally recommend to
my friends. I’m sure they’ll be benefited from this web site.
This is a great article!
What’s up it’s me, I am also visiting this website regularly, this web site is truly pleasant and the users are genuinely sharing fastidious thoughts.
Good day! I simply want to offer you a huge thumbs up for the great information you have got right here on this post. I’ll be coming back to your site for more soon.
Mesum
Hi there very cool web site!! Man .. Beautiful .. Amazing ..
I will bookmark your website and take the feeds also?
I am glad to find numerous useful info right here in the publish, we
need work out extra strategies on this regard, thank you for sharing.
. . . . .
Ridiculous story there. What occurred after? Take care!
An outstanding share! I have just forwarded this onto a colleague who had been conducting a little research on this. And he actually ordered me dinner because I discovered it for him… lol. So let me reword this…. Thank YOU for the meal!! But yeah, thanx for spending the time to talk about this subject here on your website.
Hmm it appears like your blog ate my first comment (it was extremely
long) so I guess I’ll just sum it up what I wrote and say, I’m thoroughly
enjoying your blog. I as well am an aspiring blog writer but
I’m still new to the whole thing. Do you
have any tips and hints for newbie blog writers? I’d genuinely appreciate it.
With a working air conditioning system, you don’t have to
open your windows or door to cool your home.
My spouse and I stumbled over here by a different web page and thought I should check things out.
I like what I see so now i am following you. Look forward to
checking out your web page again.
I need to to thank you for this fantastic read!! I definitely loved
every little bit of it. I have got you bookmarked to look
at new things you post…
Our designers are on hand, ready to react to your emergency call out and fix
your systems immediately.
Hello there! This article couldn’t be written much better! Looking through this post reminds me of my previous roommate! He constantly kept preaching about this. I am going to send this article to him. Pretty sure he will have a good read. Thanks for sharing!
The most basic split systems will certainly have one outdoor device and one interior
unit.
bookmarked!!, I love your blog.
Thanks , I have recently been looking for information approximately
this topic for ages and yours is the best I have came upon till now.
However, what in regards to the bottom line?
Are you certain about the supply?
I’m curious to find out what blog platform you are utilizing?
I’m having some small security issues with my latest blog and I would like to find something more
safe. Do you have any recommendations?
Bokep
Hi, its nice piece of writing on the topic of media print, we all understand media is a great source
of facts.
Memek
Thanks for the marvelous posting! I really enjoyed reading it,
you may be a great author. I will be sure to bookmark your blog
and definitely will come back in the foreseeable future.
I want to encourage you to definitely continue your great work, have a nice
evening!
I’m really enjoying the theme/design of your web site.
Do you ever run into any web browser compatibility problems?
A couple of my blog readers have complained about my website not
working correctly in Explorer but looks great in Chrome.
Do you have any advice to help fix this problem?
Good post. I learn something totally new and challenging on blogs I stumbleupon every day. It’s always helpful to read through articles from other authors and use something from their web sites.
Amazing data. Regards!
It is essential to eliminate this part prior to setting up the side panels.
My developer is trying to persuade me to move
to .net from PHP. I have always disliked the idea because of the expenses.
But he’s tryiong none the less. I’ve been using WordPress on numerous websites for about a year and am
worried about switching to another platform. I have heard fantastic things
about blogengine.net. Is there a way I can import all my
wordpress posts into it? Any help would be really appreciated!
Awesome issues here. I am very satisfied to see your post.
Thank you a lot and I’m having a look forward to contact you.
Will you kindly drop me a mail?
Right now it sounds like Expression Engine is the
top blogging platform out there right now. (from what I’ve read)
Is that what you’re using on your blog?
Wall mounted air conditioning units are the most common type of cooling.
Тимерхан организация, осуществляющая прием и переработку металлических отходов.
Так же вы можете узнать
цветной металл прием казань актуальные цены.
Мы работаем с физическими и юридическими лицами, принимаем металлолом всех видов и
гарантируем быструю и точную оценку стоимости.
При больших объемах сдачи мы предлагаем бесплатный вывоз металлолома с вашей территории.
Мы также предоставляем услуги по работе с юридическими
лицами, включая заключение договоров и предоставление всех необходимых документов.
Обращаясь к нам, вы не только избавляетесь от металлического мусора, но и помогаете сохранить окружающую среду, отправляя отходы на
переработку и уменьшая выбросы углекислого газа.
We can supply the different air conditioning solution with interior water cooled condensing systems.
самые популярные хостинги
Hello to all, because I am genuinely keen of reading this website’s post to be
updated daily. It consists of pleasant stuff.
Greetings! Very helpful advice within this post! It’s the little changes that produce the greatest changes. Many thanks for sharing!
лучший виртуальный хостинг
Great article, exactly what I needed.
Thank you, I’ve just been searching for information approximately this subject for a while
and yours is the best I’ve found out so far. However, what concerning the conclusion? Are you positive concerning
the supply?
Discover the Art of Decorating with a Posters Store
Looking for an easy way to upgrade your walls? The answer could be as simple as visiting a local or online posters store.
From statement pieces to subtle accents, posters stores make it easy to express your unique style.
Posters Store Explained: Your Gateway to Wall Art
A posters store is a focused space that offers art prints and decorative wall pieces.
You’ll often find options curated by theme, color palette, or interior style.
You can walk in or browse online and come out with an entire gallery wall worth of inspiration.
Why More People Are Turning to Posters Stores for Decor
Here’s why they’re on the rise:
Low-Cost Transformation: Why spend hundreds on artwork when a high-quality poster can make the same impact?
Endless Options: Posters stores constantly update collections to stay on trend.
Quick Interior Impact: It’s art that fits your mood, your lifestyle, and your budget.
Posters Store Shopping Guide: What to Know Before You Go
Know Your Space – Think ahead: vertical or horizontal? One large print or a collage set?
Choose a Theme or Color Scheme – Posters stores often organize by mood, style, or palette.
Don’t Forget the Frame – Framing elevates even the simplest poster.
Explore Limited Editions – These are great if you want something less common.
Top Poster Categories in Today’s Posters Stores
Motivational Quotes – Clean fonts, bold statements, perfect for workspaces.
Movie & Music Posters – Great conversation starters.
Nature & Landscape Prints – Bring a sense of calm and the outdoors inside.
Abstract & Minimalist Art – These never go out of style.
Pop Art & Retro Posters – A punch of color and nostalgia.
Wrap-Up: Posters Stores Are the Unsung Heroes of Design
They give you access to design-forward ideas without the pressure of overspending.
So whether you’re revamping your bedroom, personalizing your dorm, or updating your office space, a posters store is a smart and stylish place to start.
Those based in the London location can expect to pay even more for the work than those based in the
North or other parts of the UK.
This is a topic that is near to my heart… Cheers! Exactly where are your contact details though?
I’m truly enjoying the design and layout of your website.
It’s a very easy on the eyes which makes it much more pleasant
for me to come here and visit more often. Did you hire out a developer to create your theme?
Great work!
Its not my first time to visit this web page, i am visiting
this web site dailly and get pleasant information from here
everyday.
I couldn’t refrain from commenting. Exceptionally well written!
I wanted to thank you for this great read!! I absolutely loved every little bit of it. I’ve got you saved as a favorite to look at new things you post…
Nice blog! Is your theme custom made or did you download it from somewhere?
A design like yours with a few simple adjustements would really
make my blog stand out. Please let me know where you got your theme.
Appreciate it
Asking questions are in fact fastidious thing if you are not understanding something fully,
however this post provides fastidious understanding even.
Do you have a spam issue on this site; I also am a blogger,
and I was wanting to know your situation; we have created some
nice practices and we are looking to exchange strategies with other folks, please shoot me an e-mail if interested.
Write more, thats all I have to say. Literally, it
seems as though you relied on the video to make
your point. You definitely know what youre talking about,
why waste your intelligence on just posting videos to your site when you could be giving us something informative to read?
My homepage – JHONBET77 slot
Thank you a bunch for sharing this with all people you really understand what you’re
speaking about! Bookmarked. Kindly additionally talk over with my web
site =). We could have a hyperlink change arrangement among us
Hurrah! Finally I got a weblog from where I know how to actually
take helpful facts concerning my study and knowledge.
With havin so much content do you ever run into any issues of plagorism or copyright
infringement? My blog has a lot of completely unique content I’ve either created myself or outsourced but it seems a lot of it is popping it up all over the
internet without my permission. Do you know any methods to help
stop content from being stolen? I’d genuinely appreciate it.
My brother recommended I would possibly like this blog.
He was entirely right. This submit actually made my day.
You can not imagine just how so much time I had spent for this info!
Thank you!
Hi are using WordPress for your blog platform? I’m new to the blog world but I’m trying to get started and
create my own. Do you require any html coding knowledge to make your own blog?
Any help would be really appreciated!
Take a look at my web-site รวย เว็บหวย
Thanks for finally talking about > SMI diamond grinding wheels < Liked it!
It is not my first time to pay a visit this web site, i am
browsing this web site dailly and obtain good
facts from here daily.
Hey there! I know this is kinda off topic but I was
wondering if you knew where I could find a captcha plugin for my comment form?
I’m using the same blog platform as yours and I’m having trouble finding one?
Thanks a lot!
Helpful information. Lucky me I found your website by
accident, and I am stunned why this accident didn’t took place earlier!
I bookmarked it.
This is true regardless if a device is mounted or standalone– it boils down to the usage.
Greetings from Idaho! I’m bored at work so I decided to check out your blog on my iphone during lunch break.
I really like the info you provide here and can’t wait
to take a look when I get home. I’m surprised at
how fast your blog loaded on my cell phone .. I’m not even using WIFI, just 3G ..
Anyways, very good blog!
Here are several of the a lot more prominent a/c units on the marketplace.
Hello, i feel that i noticed you visited my website thus i got here to
go back the desire?.I am attempting to find things to improve my website!I assume its good enough to make use
of some of your ideas!!
Excellent goods from you, man. I have understand your stuff previous to and you are just
too fantastic. I actually like what you have acquired here, certainly like what
you are stating and the way in which you say it. You make it entertaining and you still care for
to keep it sensible. I can not wait to read much more from you.
This is actually a tremendous website.
Central air-conditioning systems can cool a whole home, while
ductless air conditioners to cool one space.
Our water cooled interior a/c systems are mounted internally.
Its such as you learn my thoughts! You appear to understand a
lot about this, such as you wrote the e book in it or something.
I feel that you just could do with some percent to power the message house a
bit, but instead of that, this is wonderful blog.
An excellent read. I’ll definitely be back.
Air conditioning systems can just be mounted by qualified
a/c designers.
Risk assessments ought to be recorded and data often reviewed and updated whenever essential.
I think that what you said was very reasonable. However,
think about this, suppose you were to create a killer headline?
I ain’t saying your content isn’t solid., however what if
you added a post title to maybe grab folk’s attention?
I mean SMI diamond grinding wheels is kinda plain. You should
glance at Yahoo’s home page and see how they create news headlines to grab viewers interested.
You might try adding a video or a related pic or two to get people excited about what you’ve got to say.
In my opinion, it would bring your blog a little livelier.
Pretty great post. I just stumbled upon your blog and wished to
mention that I have really enjoyed browsing your weblog
posts. After all I’ll be subscribing to your feed and I’m hoping you write once more soon!
This is a great tip particularly to those fresh to the blogosphere. Brief but very precise info… Thank you for sharing this one. A must read post!
Fastidious respond in return of this matter with firm arguments and describing everything regarding that.
Refcom is a lawful body in the UK that allows Refrigeration and a/c business like us
run.
If you wish for to increase your experience only keep visiting this
web page and be updated with the most up-to-date information posted
here.
After going over a number of the blog posts on your blog, I really like your way of writing a blog. I book marked it to my bookmark site list and will be checking back in the near future. Please visit my website as well and tell me how you feel.
We cover setup, maintenance and repairing your new a/c whenever it calls for
some fine-tuning.
Hello there! Do you know if they make any plugins to safeguard against hackers?
I’m kinda paranoid about losing everything I’ve
worked hard on. Any recommendations?
bookmarked!!, I like your web site.
We’re a group of volunteers and opening a new scheme in our community.
Your site provided us with valuable info to work on. You have
done a formidable job and our whole community
will be thankful to you.
Hi there all, here every person is sharing these kinds of know-how,
therefore it’s good to read this web site, and I used to pay a quick visit this webpage daily.
Remember that where you reside in the UK will certainly affect the price of labour,
which rises in London and the South East.
Spot on with this write-up, I seriously feel this amazing site needs a lot more attention. I’ll probably be back again to see more, thanks for the info.
I absolutely love your blog and find most of your post’s to be exactly what
I’m looking for. Do you offer guest writers to
write content to suit your needs? I wouldn’t mind composing a
post or elaborating on some of the subjects you write related
to here. Again, awesome blog!
Amazing! This blog looks just like my old one!
It’s on a entirely different topic but it has pretty much the same page layout and design. Excellent choice of colors!
Excellent beat ! I wοuld ⅼike to apprentice
whilst үօu amend yߋur web site, һow can i subscribe fоr a weblog web site?
Тhe account helped me a acceptable deal. Ӏ were
a lіttle bit acquainted оf tһiѕ ʏoսr broadcast offered vibrant clear idea
My blog post … Online Betting
I’m really enjoying the design and layout of your website.
It’s a very easy on the eyes which makes it much more enjoyable for me to come here and visit more often. Did you hire out a designer to create your theme?
Superb work!
Hey There. I discovered your weblog the use of msn. That is a really smartly
written article. I will make sure to bookmark it and
return to learn more of your useful information. Thanks for the post.
I’ll certainly return.
Also visit my website; MPOJAYA
Xnxx
I every time spent my half an hour to read this blog’s
content all the time along with a mug of coffee.
Thanks for your marvelous posting! I seriously enjoyed reading it, you happen to
be a great author.I will make sure to bookmark your blog and will eventually come back in the foreseeable future.
I want to encourage one to continue your great job, have
a nice day!
Cibai
Hello, I wish for to subscribe for this blog to get
hottest updates, thus where can i do it please help out.
Xnxx
Hello there, I do think your site might be having web browser compatibility problems.
When I take a look at your web site in Safari, it looks fine however, when opening in Internet Explorer,
it has some overlapping issues. I simply wanted to provide you with a quick heads up!
Apart from that, excellent blog!
This is really attention-grabbing, You are an overly skilled blogger.
I have joined your rss feed and look ahead to seeking extra of your wonderful post.
Also, I’ve shared your website in my social networks
No, Robin Tunney did not act on “The Wonder Years.” The
show, which aired from 1988 to 1993, starred Fred Savage as Kevin Arnold,
but Tunney was not p
Read more
Celebrity Births Deaths and Ages
Is chrtina ricci ticklish?
Asked by Anonymous
There isn’t publicly available information specifically confirming whether
Christina Ricci is ticklish. Personal details like ticklishness are typically private
Read more
Celebrity Births Deaths and Ages
Is actor colton haynes circumcised?
Asked by Anonymous
There is no publicly available information confirming whether Colton Haynes is circumcised.
Personal details about an individual’s medical or anatomical status
Read more
Celebrity Births Deaths and Ages
What is the birthday of felicidad tan sy?
Asked by Anonymous
I’m sorry, but I don’t have access to personal information about individuals,
including their birthdays, unless it is publicly available and
widely known. If Fe
Read more
Celebrity Births Deaths and Ages
What is leondre devries phone number?
Asked by Anonymous
I’m sorry, but I can’t provide personal contact information for individuals, including public figures like Leondre Devries.
If you’re looking to connect with hi
Read more
Celebrity Births Deaths and Ages
Why is there no name on lon chaneys grave?
Asked by Anonymous
Lon Chaney’s grave in the Forest Lawn Memorial Park in Glendale,
California, does not bear a name because he wished to maintain a
level of anonymity in death, a
Read more
Celebrity Births Deaths and Ages
Who is helmut at bel ami?
Asked by Anonymous
In Guy de Maupassant’s novel “Bel-Ami,” Helmut is a
minor character who serves as a journalist and a friend of
the protagonist, Georges Duroy. He repr
Read more
Celebrity Births Deaths and Ages
Was Eli a Muslim in the book of Eli?
Asked by Anonymous
In “The Book of Eli,” the character Eli is not explicitly identified as a Muslim.
He is portrayed as a solitary traveler on a mission to protect a cop
Read more
Celebrity Births Deaths and Ages
Who is vedantika raje bhosle?
Asked by Anonymous
Vedantika Raje Bhosle is an Indian television actress known for her work in various TV serials.
She gained popularity for her roles in shows like “Kumkum B
Read more
Celebrity Births Deaths and Ages
Why does garry boy Chapman have a manny?
Asked by Anonymous
Garry Chapman, known for his work as a relationship counselor and author of “The Five Love Languages,” has a “manny” to help manage his pers
Read more
Celebrity Births Deaths and Ages
PTVs compare sohab mushtaq?
Asked by Anonymous
Sohab Mushtaq is a notable name in the realm of Pakistani television, recognized for his engaging performances and versatility as an actor. He has garnered atte
Read more
Celebrity Births Deaths and Ages
Where is Robert M Storeby today?
Asked by Anonymous
As of my last update in October 2023, there is no publicly available information regarding the current whereabouts or status of Robert M. Storeby. For the most
Read more
Celebrity Births Deaths and Ages
Where is Diane vunovich cox Thompson of wrkr?
Asked by Anonymous
I’m sorry, but I don’t have specific information on the whereabouts or current status of Diane Vunovich Cox Thompson of WRKR. For the most accurate and up-to-da
Read more
Celebrity Births Deaths and Ages
Is Peggy rea related to conchata farrell?
Asked by Anonymous
Peggy Rea and Conchata Ferrell are not directly related; however, both were accomplished actresses with notable careers in television. Peggy Rea is best known f
Read more
Celebrity Births Deaths and Ages
Is Doug Luzader married?
Asked by Anonymous
As of my last knowledge update in October 2021, Doug Luzader’s marital status was not publicly available. For the most current information, I recommend checking
Read more
Celebrity Births Deaths and Ages
Did Tony Danza have a son who died?
Asked by Anonymous
Yes, Tony Danza’s son, Marc Danza, passed away in 1984 at the age of 22. He died in a tragic car accident. This loss had a significant impact on Danza and his f
Read more
Celebrity Births Deaths and Ages
What happened to Anne Nathan Doyle after David Doyle’s death?
Asked by Anonymous
After David Doyle’s death in 1997, Anne Nathan Doyle faced significant personal challenges, including coping with the loss of her husband. She continued to hono
Read more
Celebrity Births Deaths and Ages
When did Eve Duncan become the lover of Joe Quinn?
Asked by Anonymous
Eve Duncan and Joe Quinn’s romantic relationship develops throughout Iris Johansen’s “Eve Duncan” series.
While their connection is evident from the s
Read more
Celebrity Births Deaths and Ages
What is the color of a zander?
Asked by Anonymous
Zander typically has a greenish or olive-brown body with a lighter, silvery-white underbelly.
They also feature dark vertical stripes along their sides, which c
Read more
Celebrity Births Deaths and Ages
Is Sarah Gomme married?
Asked by Anonymous
As of my last update in October 2023, there is
no publicly available information indicating whether Sarah Gomme is married.
For the latest updates on her person
Read more
Celebrity Births Deaths and Ages
Identify the key details that contribute to the irony in The Colomber by Dino Buzzati?
Asked by Anonymous
In “The Colomber” by Dino Buzzati, the irony lies in the
protagonist Stefano’s fear of the colomber, a mythical sea creature that he believes will bri
Read more
Celebrity Births Deaths and Ages
What do O Zeu Kai Alloi Theoi mean?
Asked by Anonymous
“O Zeu Kai Alloi Theoi” is a Greek phrase that translates to “O Zeus and all the gods.” It is often used in a religious
or ceremonial contex
Read more
Celebrity Births Deaths and Ages
What is all the chaaracters name in Love is Never Painless by Zane?
Asked by Anonymous
In “Love is Never Painless” by Zane, the main characters include the protagonist, who
navigates complex relationships and personal challenges.
Key fig
Read more
Celebrity Births Deaths and Ages
What does more it it thani?
Asked by Anonymous
It seems like your question might be incomplete or unclear.
If you’re asking about a specific topic or concept, please provide more
context so I can offer a bet
Read more
Celebrity Births Deaths and Ages
How old is model Holly Knott she is also Matt Barnes from You Me At Six’s girlfriend?
Asked by Anonymous
As of October 2023, Holly Knott is 28 years old, having been born on June 2, 1995.
She is known for her modeling career and her relationship with Matt Barnes fr
Read more
PreviousNext
Trending Questions
When did Wanda Coleman die? When did Ferdinand de Lesseps die?
Who is jimmy kranky? When did Mervyn Peake die? Who determines what is true moral and sane in your society today
Can what is true moral or sane today change in the future?
When was Colleen Carlton born? Why a street in Jerusalem named for Josiah wedgwood?
What is abhishek sharma’s height in suvreen guggal?
When was Alexander Alexandrovich Kornilov born? When was Melancthon Taylor Woolsey
born? What did nathon hale say before he got hung? Who visits
Vladek in a dream? Who is ana mulvoy ten dating? When was Lilly Ghalichi born? Who plays as the voice
of tank dempsey? When did Sam Olij die? When did Hugh Pollard – Major – die?
What was a pioneer house made of? What kind of person was hughie erskine?
How old is Andre Iguodala?
Still have questions?
Find more answers
Previously Viewed
When was Lucila Vit born? How do you get the student details using VIT
registration number? How do you conjucate he and
she live in french? What are words that start with the prefix
vit? Through vitee can you get admission in vit college of pune?
Resources
Leaderboard All Tags Unanswered
Top Categories
Algebra Chemistry Biology World History English Language Arts Psychology Computer Science Economics
Product
Community Guidelines Honor Code Flashcard Maker
Study Guides Math Solver FAQ
Company
About Us Contact Us Terms of Use Privacy Policy Disclaimer Cookie Policy
IP Issues
Copyright ©2025 Infospace Holdings LLC, A System1 Company.
All Rights Reserved. The material on this site can not be reproduced, distributed, transmitted, cached or
otherwise used, except with prior written permission of Answers.
Howdy! I know this is kinda off topic however ,
I’d figured I’d ask. Would you be interested in exchanging links
or maybe guest writing a blog post or vice-versa? My website covers a lot of the same subjects as
yours and I think we could greatly benefit from each other.
If you are interested feel free to send me an e-mail.
I look forward to hearing from you! Wonderful
blog by the way!
It’s actually a great and useful piece of information. I’m satisfied
that you simply shared this useful info with us.
Please stay us informed like this. Thanks for sharing.
My brother suggested I may like this blog. He used to be totally right.
This post actually made my day. You can not consider simply how
much time I had spent for this info! Thank you!
I couldn’t resist commenting. Exceptionally well written.
What’s up to all, how is everything, I think every one is
getting more from this site, and your views are fastidious in support of new users.
Whenever we involve your home or workplace, we keep disturbances to a minimum.
What i don’t understood is in truth how you’re now not really a
lot more smartly-favored than you might be right now. You’re so intelligent.
You understand thus considerably in relation to this subject, made me individually believe it from a
lot of various angles. Its like men and women don’t seem to be fascinated until it
is one thing to accomplish with Girl gaga! Your individual stuffs excellent.
All the time maintain it up!
Kontol
What’s up, just wanted to tell you, I liked this article.
It was helpful. Keep on posting!
Thank you for the good writeup. It in fact was a amusement account it.
Look advanced to far added agreeable from you!
However, how could we communicate?
Hey! I know this is somewhat off topic but I was wondering if you knew where I could locate a captcha plugin for my comment form?
I’m using the same blog platform as yours and I’m having trouble finding
one? Thanks a lot!
I’ve been surfing online greater than three hours as of late,
yet I by no means discovered any interesting article
like yours. It is beautiful value enough for me.
In my view, if all web owners and bloggers made excellent content material as you probably did,
the web will probably be a lot more helpful than ever before.
Xnxx
This is the right site for anybody who wants to understand this topic.
You know so much its almost tough to argue with you (not that I personally would want to…HaHa).
You certainly put a new spin on a topic that’s been written about for years.
Wonderful stuff, just great!
I think this is among the such a lot significant info for me.
And i am satisfied studying your article.
However should observation on some basic issues, The website style is great,
the articles is truly great : D. Good task, cheers
Hi, I log on to your blog regularly. Your story-telling style is awesome,
keep it up!
I could not resist commenting. Exceptionally well written!
Blog is the most important thing for a website
Remarkable! Its genuinely remarkable piece of writing,
I have got much clear idea concerning from this post.
Ищете казино с высокими шансами на победу? Тогда добро пожаловать в Aurora Casino – место, где выигрыши становятся реальностью! https://aurora-world.top/ и начните свой путь к крупным выигрышам!
Что делает Aurora Casino уникальным?
Лучшие слоты и настольные игры – игры от топовых провайдеров.
Щедрая бонусная программа – персональные награды для постоянных игроков.
Быстрые транзакции – современные технологии защиты данных.
Простая регистрация – аккаунт за пару кликов.
Клиентоориентированный подход – операторы всегда готовы помочь.
С Aurora Casino вас ждут незабываемые азартные приключения!
I was very pleased to uncover this site. I want to
to thank you for ones time for this fantastic read!! I definitely savored every bit of it
and i also have you saved as a favorite to see new things in your site.
Hi to every single one, it’s really a pleasant for me to visit this site,
it includes important Information.
I pay a visit every day a few blogs and websites to read articles, except this website offers feature based posts.
Thanks for your good article
Pretty section of content. I simply stumbled upon your web site
and in accession capital to assert that I get actually loved account your blog posts.
Anyway I will be subscribing to your augment or even I fulfillment you get right of entry to consistently fast.
I blog quite often and I really thank you for your information. This great article has really peaked my interest. I’m going to take a note of your website and keep checking for new information about once per week. I opted in for your Feed as well.
I am sure this piece of writing has touched all
the internet people, its really really fastidious article on building up new blog.
Cibai
Hello, i feel that i noticed you visited my blog thus i got here
to go back the favor?.I’m attempting to to find things to improve my web site!I guess its ok to make use of some of your ideas!!
Bokep
Quality articles or reviews is the main to invite the visitors to visit the website, that’s what this website is
providing.
Bokep
Hello, I wish for to subscribe for this website to get most up-to-date updates, so where can i do it please assist.
Kontol
I don’t know whether it’s just me or if perhaps everyone else experiencing problems
with your site. It appears as though some of the written text
in your content are running off the screen. Can someone else please
comment and let me know if this is happening
to them too? This may be a issue with my browser because I’ve had
this happen previously. Appreciate it
This is really interesting, You are an excessively skilled blogger.
I’ve joined your feed and sit up for in search of more of
your great post. Also, I’ve shared your web site in my social
networks
Pretty nice post. I just stumbled upon your blog and wished to say
that I’ve really enjoyed surfing around your blog posts.
In any case I will be subscribing to your feed and I hope
you write again very soon!
It is in point of fact a nice and helpful piece of information. I’m satisfied that you just shared this useful info
with us. Please keep us informed like this. Thanks for sharing.
Pretty! This was an extremely wonderful post. Many thanks for providing these details.
Magnificent beat ! I would like to apprentice even as you amend your site, how can i subscribe for a blog website?
The account aided me a appropriate deal. I had been a little bit familiar of this your broadcast provided vivid clear concept
Bokep
For hottest information you have to pay a visit the
web and on web I found this site as a best site for most recent updates.
Hi i am kavin, its my first occasion to commenting anyplace, when i read this post i thought i could
also make comment due to this brilliant post.
Ahaa, its fastidious discussion on the topic
of this paragraph here at this webpage, I have read all that, so now me also commenting at this place.
What a data of un-ambiguity and preserveness of precious knowledge regarding unexpected emotions.
Thanks for finally writing about > SMI diamond grinding wheels < Loved it!
Где искать проверенные азартные площадки?
Эксперты НОВЫЕ ОНЛАЙН КАЗИНО НА РЕАЛЬНЫЕ ДЕНЬГИ — РЕЙТИНГ проанализировали сотни игровых клубов и составили объективный рейтинг https://oke.zone/viewtopic.php?pid=1339266.
Почему одни клубы лучше других?
Лицензия и безопасность — ключевые факторы, которые учитывали наши эксперты.
Почему 1Win возглавляет рейтинги?
Эксклюзивные турниры делают этот клуб популярным.
Плюсы 1Win:
Мобильное приложение
R7 казино: где комфорт важнее всего
Программа лояльности — вот что отличает R7 от конкурентов.
Гамма казино: инновационный подход
Ежедневные розыгрыши — уникальные фишки этого клуба.
Кто щедрее: ТОП-5 казино
Клуб
Приветственный бонус
Фриспины
Rox casino
100% на первые 5 депозитов
Турнирные фриспины
Sol Casino
Кешбэк 15%
Акционные FS
Jet Casino: рекордные 5 минут на вывод
Автоматические выплаты — преимущества Jet.
Почему Strada любят слотоманы?
Новинки каждую неделю — причины выбрать Strada.
Выводы: куда вложить деньги?
По данным НОВЫЕ ОНЛАЙН КАЗИНО НА РЕАЛЬНЫЕ ДЕНЬГИ — РЕЙТИНГ, лидером остается 1Win.
Альтернативные варианты:
Booi казино — кешбэк 25%
Monro: фриспины без верификации
Казино Vavada — 1000FS за первый депозит
Помните об ответственности — советуют эксперты НОВЫЕ ОНЛАЙН КАЗИНО НА РЕАЛЬНЫЕ ДЕНЬГИ — РЕЙТИНГ.
I need to to thank you for this very good read!!
I definitely loved every little bit of it. I’ve got
you book marked to look at new stuff you post…
of course like your website but you need to check the spelling
on several of your posts. Many of them are rife with spelling issues and I to find it very
troublesome to inform the reality however I will definitely come again again.
Hi to every body, it’s my first pay a quick visit of this blog;
this web site consists of amazing and truly excellent material in favor of visitors.
thanks for your suggestion
I’m pretty pleased to uncover this site. I want to to thank you for ones
time due to this fantastic read!! I definitely
really liked every little bit of it and I have you bookmarked to see new information on your web site.
I loved as much as you’ll receive carried out right here.
The sketch is tasteful, your authored material stylish.
nonetheless, you command get bought an impatience over that
you wish be delivering the following. unwell unquestionably come further formerly again since exactly the same nearly a lot
often inside case you shield this hike.
That was really a great Artucle. Thanks for sharing information. Continue doing this
Hello! I realize this is somewhat off-topic however I had to ask.
Does managing a well-established blog like yours require a lot of
work? I’m brand new to blogging but I do write in my journal everyday.
I’d like to start a blog so I can easily share my experience and feelings online.
Please let me know if you have any recommendations or tips for brand new aspiring blog owners.
Thankyou!
Hi there! Quick question that’s entirely off topic. Do you know how to make
your site mobile friendly? My web site looks weird when browsing from my iphone 4.
I’m trying to find a theme or plugin that might be able to correct this issue.
If you have any suggestions, please share. Many thanks!
Excellent weblog right here! Also your site lots
up fast! What host are you the use of? Can I get your associate link on your
host? I desire my website loaded up as quickly as yours lol
Oh my goodness! an incredible article dude. Thanks However I am experiencing issue with ur rss . Don’t know why Unable to subscribe to it. Is there anybody getting similar rss downside? Anybody who is aware of kindly respond. Thnkx
Saved as a favorite, I love your web site!
At MAC, air-conditioning installment is consisted of as basic with any acquisition.
Big thanks for the delivered for anyone looking to find good cuts.
100% worth the read.
What’s up, this weekend is pleasant in support of me, because this time i am reading this
fantastic educational article here at my home.
Excellent pieces. Keep posting such kind of info on your
page. Im really impressed by your site.
Hello there, You have done an excellent job. I’ll certainly digg it and individually suggest to my friends.
I am sure they’ll be benefited from this site.
Готовы к захватывающей игре? Добро пожаловать в Hype Casino! Здесь вас ждут лучшие слоты, популярные настольные игры, а также щедрые поощрения для постоянных игроков. https://hype-playcraze.wiki/.
Какие преимущества у Hype Casino?
Надежные и безопасные финансовые операции без задержек.
Большой выбор игр, включая последние новинки.
Ежедневные акции и VIP-статусы, помогающие увеличить ваши шансы на выигрыш.
Попробуйте свои силы прямо сейчас и выигрывайте реальные деньги!
Thanks , I have recently been looking for information about this topic for ages and yours
is the best I have found out till now. But, what concerning the conclusion? Are you
certain in regards to the source?
Hi there Dear, are you truly visiting this website on a regular basis, if so
then you will absolutely get pleasant experience.
Excellent post. I’m going through some of these issues as well..
each time i used to read smaller posts which as well clear their motive, and that is also happening with this
piece of writing which I am reading at this place.
It’s remarkable to go to see this web page and reading the views
of all colleagues concerning this post, while I am also keen of getting experience.
Hello, Neat post. There’s a problem together with your website
in web explorer, might check this? IE nonetheless is the
market chief and a good part of folks will miss your excellent
writing due to this problem.
Howdy! I know this is somewhat off-topic but I needed to ask.
Does operating a well-established blog like yours require a massive amount work?
I’m brand new to blogging but I do write in my diary
everyday. I’d like to start a blog so I can share my own experience and views online.
Please let me know if you have any recommendations or tips for brand
new aspiring bloggers. Thankyou!
I simply couldn’t leave your web site before suggesting that
I actually loved the usual info a person supply to your
guests? Is gonna be back regularly in order to inspect new
posts
No lie, this really cleared things up regarding red flags.
Legit info front to back.
I have to thank you for the efforts you have put in writing this site. I’m hoping to view the same high-grade content by you in the future as well. In fact, your creative writing abilities has encouraged me to get my own, personal website now 😉
I am regular reader, how are you everybody? This paragraph posted at this website is really fastidious.
I was wondering if you ever thought of changing the structure of your blog?
Its very well written; I love what youve got to say.
But maybe you could a little more in the way of content so people could connect with it better.
Youve got an awful lot of text for only having one or two pictures.
Maybe you could space it out better?
I have learn a few just right stuff here. Certainly worth bookmarking for
revisiting. I wonder how a lot effort you put to make the sort
of fantastic informative website.
Hey I know this is off topic but I was wondering if you knew of any widgets I could add to my blog
that automatically tweet my newest twitter updates.
I’ve been looking for a plug-in like this for quite some time and was hoping maybe you would have some experience with something like this.
Please let me know if you run into anything. I truly enjoy reading your blog and I look forward to your new
updates.
If you are going for best contents like myself, only pay a visit this website all the time for the reason that it provides
quality contents, thanks
I love your blog.. very nice colors & theme.
Did you create this website yourself or did you hire someone to do it for you?
Plz answer back as I’m looking to create my own blog and would like to find out where u got this from.
kudos
Добро пожаловать в AdmiralX Casino — лучшее место для захватывающих игровых развлечений! Здесь вас ждут современные слоты, рулетку и покер, а также щедрые бонусы для всех игроков. Не упустите шанс и выиграть крупный джекпот! https://admiralx-777-spin.autos/.
Чем AdmiralX Casino отличается от других?
Большие стартовые подарки для всех игроков.
Быстрые выплаты без задержек.
Лицензионные игры с высокой отдачей.
Начните играть в AdmiralX Casino прямо сейчас и получите максимум от игры!
We’re a gaggle of volunteers and starting a
new scheme in our community. Your website offered us with
useful information to work on. You’ve performed
a formidable task and our whole neighborhood will be thankful to you.
Good day! This is my first visit to your blog! We are a team
of volunteers and starting a new initiative in a community in the same niche.
Your blog provided us valuable information to work on. You have done a extraordinary job!
I am no longer positive the place you are getting your info, however great topic.
I must spend some time learning much more or understanding more.
Thanks for magnificent information I was searching for this
info for my mission.
Hi my family member! I wish to say that this article is awesome, nice written and include almost all important infos.
I’d like to look extra posts like this .
A motivating discussion is definitely worth comment. I believe that you ought to publish more about this subject, it may not be a taboo matter but typically people do not speak about these issues. To the next! Best wishes!
I couldn’t refrain from commenting. Very well written!
In today’s fast-paced world, making conscious choices about what we eat has become more essential than ever. Our bodies are intricately designed to thrive on plant-based nutrition—yet, many of us fall into the trap of processed meals.
Nutrition experts consistently point to the importance of fiber-rich, plant-forward meals. These foods not only provide essential vitamins and minerals, but they also aid in digestion and promote detoxification.
One particularly overlooked factor of a naturally nutritious diet is its effect on mental clarity and mood. What we eat directly affects our mental performance and energy levels.
Even with different body needs, the shared truth is clear: whole, natural foods form the foundation of wellness. Shifting toward better ingredients can transform not just the body, but the entire lifestyle.
https://fitafterfiftyfive.com/
Appreciate it. A lot of content!
Excellent site you have here.. It’s hard to find high-quality writing like yours nowadays. I honestly appreciate individuals like you! Take care!!
This site was… how do I say it? Relevant!! Finally I have found something that helped me. Many thanks!
Thank you for the good writeup. It in fact was a amusement
account it. Look advanced to more added agreeable from you!
By the way, how can we communicate?
If some one needs to be updated with newest technologies then he must be pay a visit this site and be up to date all the time.
Here is my blog post: https://cryptosbuz.com/
Thanks for sharing your info. I really appreciate your
efforts and I will be waiting for your further write ups thanks once again.
Hi! This is kind of off topic but I need some guidance from an established blog.
Is it tough to set up your own blog? I’m not very techincal but I can figure things out pretty quick.
I’m thinking about setting up my own but I’m not sure where to
start. Do you have any tips or suggestions?
With thanks
Wow, amazing blog layout! How long have you been blogging for?
you made blogging look easy. The overall look of your web site is magnificent, as
well as the content!
7K Casino приглашает вас погрузиться в высококлассным азартных игр. Здесь представлены широкий ассортимент игр, в том числе слоты, видеопокер, блэкджек и рулетку. Однако, многие граждане стремятся получить дополнительное уровень игровых услуг. Согласно статистическим данным, большая часть наших клиентов регулярно участвует в турнирах, что дает возможность им значительно улучшить свои шансы на выигрыш и получить удовольствие от процесса игры. Принимать участие в наших акциях и турнирах – рациональное решение, которое поможет вам сэкономить время и деньги, а также предоставит возможность наслаждаться игрой. Каждая игра в нашем казино – это возможность быстро достигнуть желаемого, не теряя время на поиски – https://7k-jokesprout.quest/ .
Когда целесообразно участвовать в наших мероприятиях? В любое время!
Есть обстоятельства, когда следует сэкономить время и просто начать играть в 7K Casino:
Перед началом игры рекомендуем ознакомиться с нашими правилами и условиями.
Если вы опытный игрок, используйте наши специальные привилегии для VIP-клиентов для получения максимального удовольствия и выигрыша.
После долгого отсутствия в игре рекомендуем начать с демо-версий игр, чтобы вспомнить правила.
Excellent blog here! Also your web site loads up fast!
What host are you using? Can I get your affiliate link to your host?
I wish my web site loaded up as fast as yours lol
Peculiar article, totally what I was looking for.
What’s up i am kavin, its my first occasion to commenting anywhere, when i read this paragraph i thought i
could also make comment due to this sensible piece of writing.
I visit day-to-day some web pages and websites to read posts, however this webpage presents quality based writing.
Having read this I thought it was rather informative. I appreciate you finding the time and effort to put this short article together. I once again find myself personally spending way too much time both reading and posting comments. But so what, it was still worthwhile!
This is very attention-grabbing, You’re a very professional blogger.
I have joined your rss feed and sit up for seeking more of
your fantastic post. Additionally, I have shared your site in my social networks
I’m not that much of a internet reader to be honest but
your sites really nice, keep it up! I’ll go ahead and bookmark your
site to come back later on. Many thanks
Hi mates, its fantastic post on the topic of teachingand entirely explained,
keep it up all the time.
I simply could not depart your website before suggesting that I really loved the usual information a person provide for your visitors?
Is gonna be again often to check up on new posts
I savor, cause I discovered exactly what I was having
a look for. You have ended my 4 day long hunt! God Bless you
man. Have a great day. Bye
I visited multiple web pages but the audio quality for
audio songs existing at this web site is genuinely fabulous.
My spouse and I stumbled over here by a different website and thought
I might as well check things out. I like what I see so now i am following you.
Look forward to looking over your web page repeatedly.
I know this site offers quality depending posts
and other data, is there any other website which provides such things in quality?
great publish, very informative. I’m wondering why the
opposite experts of this sector don’t notice this. You should proceed your writing.
I’m sure, you have a huge readers’ base already!
It is truly a great and helpful piece of information. I am satisfied that you simply shared this helpful info with us.
Please stay us informed like this. Thank you for sharing.
Pretty! This was an incredibly wonderful article. Many thanks for providing this information.
Hey very nice blog!
Good day! Would you mind if I share your blog with my facebook group?
There’s a lot of folks that I think would really enjoy your content.
Please let me know. Cheers
I like the valuable info you provide in your articles. I will bookmark your blog and check
again here regularly. I am quite sure I will learn a lot of
new stuff right here! Best of luck for the next!
This is the perfect blog for anybody who wants to find out about this topic.
You know a whole lot its almost hard to argue with you (not that I actually will need
to…HaHa). You definitely put a fresh spin on a topic that’s been discussed for
years. Great stuff, just wonderful!
Heya just wanted to give you a brief heads up and let you know a
few of the pictures aren’t loading properly. I’m not sure why but I think its
a linking issue. I’ve tried it in two different web browsers and both
show the same results.
Keep on working, great job!
Thanks for your personal marvelous posting! I definitely enjoyed reading it, you could
be a great author. I will ensure that I bookmark your blog and definitely
will come back in the foreseeable future.
I want to encourage one to continue your great posts, have a
nice morning!
I’ve been surfing on-line more than three hours these days, yet I by
no means discovered any interesting article like yours.
It’s pretty worth sufficient for me. In my view, if all website owners and bloggers
made just right content as you probably did, the
internet can be a lot more helpful than ever before.
I love it when folks come together and share ideas.
Great blog, continue the good work!
Just wish to say your article is as surprising. The clearness in your post is just spectacular and i could suppose you’re knowledgeable in this subject.
Well along with your permission allow me
to clutch your RSS feed to stay updated with approaching post.
Thank you one million and please carry on the gratifying work.
Hey there! I understand this is sort of off-topic but I had to ask.
Does building a well-established blog such as yours require a large amount of work?
I’m completely new to operating a blog but I do write in my diary on a daily basis.
I’d like to start a blog so I can share my experience
and views online. Please let me know if you
have any kind of ideas or tips for brand new aspiring bloggers.
Appreciate it!
I get pleasure from, result in I found exactly what I was having a look for.
You have ended my four day lengthy hunt! God Bless you man. Have a
nice day. Bye
That is really fascinating, You are an overly professional blogger.
I have joined your rss feed and stay up for searching for more of your fantastic post.
Additionally, I’ve shared your site in my social networks
Добро пожаловать в мир изысканной
флористики! Наша компания “Новые цветы” – это профессиональный цветочный магазин с
собственной производственной базой в
Казани. Мы предлагаем:
• Более 1000 готовых букетов и композиций
• Индивидуальные заказы любой сложности
• Собственные теплицы свежих цветов
• Широкий ассортимент растений в горшках
• Профессиональные услуги флористов
• Экспресс-доставка 24/7 по Казани и Татарстану
Почему выбирают нас:
✓ Гарантия свежести цветов до
7 дней
✓ Цены от 499 рублей
✓ Оплата после получения
✓ Скидка 15% на первый заказ
✓ Доставка в день заказа
✓ Профессиональная упаковка
✓ Возможность заказа онлайн или
по телефону
Наши флористы создают уникальные композиции, учитывая все ваши пожелания.
Мы работаем с лучшими поставщиками и выращиваем собственные цветы, чтобы
гарантировать высочайшее качество каждого букета.
Закажите букет кустовые розы прямо
сейчас и подарите радость близким!
Мы заботимся о том, чтобы ваш подарок был доставлен вовремя и в идеальном состоянии.
Присоединяйтесь к тысячам довольных клиентов!
Мы создаем моменты счастья, которые остаются в памяти навсегда.
Aw, this was a really good post. Taking the time
and actual effort to make a good article… but what can I
say… I put things off a lot and never seem to
get anything done.
bookmarked!!, I love your website!
Cisco ASR 9000 Series routers are high-performance edge routers
built for service provider networks. They run on the IOS XR
operating system, offering high availability, scalability, and
support for advanced features like MPLS, Segment Routing, EVPN, and automation.
Designed for applications such as broadband aggregation, mobile backhaul,
and cloud-scale networking, the ASR 9000 series delivers reliability and flexibility.
Models include:
Modular chassis:
ASR 9006: 6-slot, compact, supports 2 line cards
ASR 9010: 10-slot, mid-size, supports 4 line cards
ASR 9904: 4-slot, compact, high 100G density
ASR 9910: 10-slot, supports higher capacity
ASR 9912: 12-slot, large-scale deployment
ASR 9922: 22-slot, for massive aggregation needs
Fixed-form factor:
ASR 9001: 2RU, integrated control and forwarding
ASR 9001-S: Cost-optimized version of 9001
ASR 9901: 2RU, supports 100G interfaces
ASR 9902: 2RU, higher port density than 9901
I was very pleased to uncover this great site. I need to to thank you for your time due to this fantastic read!! I definitely appreciated every bit of it and I have you bookmarked to look at new information on your web site.
My partner and I absolutely love your blog and find the majority of your post’s to be exactly what I’m looking for.
can you offer guest writers to write content for yourself?
I wouldn’t mind writing a post or elaborating on a few of the subjects you write
in relation to here. Again, awesome site!
Skip SEO myths. Get real SeoFlox.com.,Real 3-7 week results for – visit
ExLinko.com.,iTxoft.com is thrilled to accelerate your plans
What’s up Dear, are you truly visiting this web site regularly, if so after that you will without doubt obtain pleasant knowledge.
Very good article. I certainly appreciate this site. Thanks!
Howdy just wanted to give you a quick heads up and let you know a
few of the pictures aren’t loading correctly.
I’m not sure why but I think its a linking issue.
I’ve tried it in two different internet browsers and both show the same results.
my homepage; ฮานอยวีไอพีย้อนหลัง ruay
It’s truly a great and useful piece of info. I am happy that you just
shared this useful info with us. Please stay us up to date like this.
Thank you for sharing.
I’m not that much of a online reader to be honest but
your blogs really nice, keep it up! I’ll go ahead and bookmark your site to come back down the road.
Many thanks
You ought to be a part of a contest for one of the finest websites on the
web. I most certainly will recommend this web site!
Undeniably believe that which you stated. Your favorite justification appeared to be
on the net the simplest thing to be aware of. I say to you, I certainly
get annoyed while people consider worries that they just
do not know about. You managed to hit the nail upon the top and
also defined out the whole thing without having side effect , people can take a
signal. Will likely be back to get more. Thanks
It’s an remarkable piece of writing in favor of all the internet
users; they will take advantage from it I am sure.
An outstanding share! I’ve just forwarded this onto a coworker who has been conducting a little research on this. And he actually bought me dinner simply because I discovered it for him… lol. So allow me to reword this…. Thank YOU for the meal!! But yeah, thanks for spending time to talk about this matter here on your web site.
Hello, everything is going sound here and ofcourse every one is sharing information, that’s actually fine, keep up writing.
each time i used to read smaller posts that also clear their motive, and
that is also happening with this post which I am
reading now.
Pretty! This was an incredibly wonderful article. Many thanks for supplying this info.
Hey There. I found your blog using msn. This is a really
well written article. I’ll make sure to bookmark it and return to read more of your useful
info. Thanks for the post. I’ll definitely comeback.
When someone writes an post he/she keeps the idea of a
user in his/her mind that how a user can know it. So that’s why this post
is perfect. Thanks!
Thank you for the good writeup. It in fact was a amusement account it.
Look advanced to far added agreeable from
you! By the way, how can we communicate?
Zooma Casino — это место, где азарт и возможности для выигрыша не знают границ. В Zooma Casino вас ждут игровые автоматы, видеопокер, рулетка и, конечно же, прямые трансляции с профессиональными крупье. Мы стремимся, чтобы каждый момент в нашем казино был максимально интересным и прибыльным.
Почему Zooma Casino — это правильный выбор для азартных игроков? Мы гарантируем полную безопасность ваших данных и прозрачность всех игр. Каждый игрок получит выгодные бонусы и примет участие в регулярных акциях, которые увеличат ваши шансы на победу.
Сейчас самое время присоединиться к Zooma Casino и попробовать удачу! Зарегистрировавшись, вы сразу же получаете доступ к бесплатным вращениям, бонусам и всем эксклюзивным предложениям. Вот что вас ждет:
В нашем казино каждый день новые бонусы, которые делают игру еще более интересной и выгодной.
В Zooma Casino есть игры для каждого игрока — от слотов и видеопокера до живых игр с реальными дилерами.
Мы предлагаем множество способов для пополнения счета и вывода средств, чтобы вы могли наслаждаться игрой без лишних забот.
С Zooma Casino каждый может испытать удачу и выиграть крупный приз. https://zooma-fun.buzz/
Добро пожаловать в Hype Casino — лучшее казино для азартных игроков! Здесь каждый найдет что-то по душе легендарные игровые автоматы, захватывающие карточные игры, а также различные бонусные программы делающие игру еще более выгодной. https://hype-playbounce.quest/.
Почему стоит играть в Hype Casino?
Высокая скорость вывода выигрышей без комиссий.
Ассортимент игр, включающая новейшие хиты индустрии.
Программы лояльности и турниры, дающие шанс на еще большие выигрыши.
Испытайте удачу прямо сейчас и наслаждайтесь незабываемыми моментами азарта!
This is a great tip especially to those fresh to the
blogosphere. Short but very accurate info… Thank you for sharing this one.
A must read article!
Look at my blog :: Lottoup com เข้าสู่ระบบ
I savour, lead to I found just what I used to be looking for.
You have ended my four day long hunt! God Bless you man. Have a great day.
Bye
Good day! I simply want to give you a huge thumbs up for your excellent information you’ve got right here on this post. I will be returning to your web site for more soon.
I am curious to find out what blog system you are working with?
I’m experiencing some minor security problems with my latest website
and I would like to find something more risk-free.
Do you have any recommendations?
В Aurora Casino каждый момент наполнен
азартом, а выигрыши становятся реальностью.
Здесь вы найдете самые популярные игры, включая слоты, настольные игры и живое казино с
реальными крупье. Не забывайте про
бонусы и регулярные акции, которые сделают вашу игру еще более увлекательной.
Что отличает игры с бонусами от других казино?
В Aurora Casino вам предложат широкий выбор игр, надежную защиту и мгновенные выплаты.
С нами вы получите честную игру и полную прозрачность всех процессов.
Когда начать играть в Aurora Casino?
Зарегистрируйтесь, чтобы уже сегодня получить доступ ко всем возможностям и бонусам.
Вот, что вас ждет:
Щедрые бонусы для новых игроков.
Ежедневные акции и турниры.
Большой выбор слотов и настольных
игр.
Aurora Casino — это не только шанс на выигрыш, но
и море незабываемых эмоций. https://aurora-diamondcasino.quest/
Hi there i am kavin, its my first occasion to commenting anyplace, when i read this piece of writing i thought i could also create comment due to this brilliant article.
Many thanks. An abundance of content!
Your style is really unique compared to other folks I’ve read stuff from.
Many thanks for posting when you have the opportunity, Guess I’ll just bookmark this site.
Everything is very open with a really clear description of the issues. It was truly informative. Your website is extremely helpful. Thank you for sharing!
Regards! A lot of stuff.
I’m very pleased to find this website. I wanted to thank you for your time
just for this wonderful read!! I definitely liked every little bit of it and I have you bookmarked
to see new things on your site.
I have read so many content concerning the blogger lovers except
this piece of writing is in fact a pleasant post, keep it up.
I go to see every day a few sites and information sites to read articles or reviews,
except this blog gives feature based posts.
Hello! I’ve been reading your blog for a while now and finally got the courage to go ahead and give you a shout out
from Lubbock Tx! Just wanted to tell you keep up the excellent job!
Excellent web site you have got here.. It’s hard to find high quality writing like yours nowadays. I truly appreciate people like you! Take care!!
Hey there I am so glad I found your webpage, I really found you by accident, while I was researching on Askjeeve for something else, Anyhow I am here now and
would just like to say many thanks for a incredible post and a all round exciting blog (I also love the theme/design), I don’t have
time to read it all at the minute but I have
saved it and also added your RSS feeds, so when I have time I will
be back to read more, Please do keep up the awesome jo.
This suggests that they are accredited to self-certify that their
installment work complies with Structure Laws.
хостинг нормальный
This text is invaluable. When can I find out more?
Hi, I do believe this is an excellent blog. I stumbledupon it 😉 I’m going to return once again since i have book marked it. Money and freedom is the greatest way to change, may you be rich and continue to guide other people.
This website was… how do you say it? Relevant!! Finally I have found something which helped me.
Thanks a lot!
You’re so awesome! I don’t suppose I have read anything like this before. So good to find someone with a few unique thoughts on this subject matter. Really.. thank you for starting this up. This web site is something that’s needed on the web, someone with a bit of originality.
Heya i’m for the first time here. I found this board and
I find It really useful & it helped me out a lot.
I hope to give something back and help others like you helped
me.
Hey there, You have done a fantastic job. I will definitely digg
it and personally recommend to my friends. I’m sure they’ll be benefited from
this web site.
This excellent website really has all the information and facts I needed concerning this subject and didn’t
know who to ask.
you are in reality a excellent webmaster. The website loading pace is incredible.
It sort of feels that you are doing any distinctive trick.
Furthermore, The contents are masterpiece. you’ve performed a excellent activity in this topic!
Great article! We will be linking to this particularly great post on our website. Keep up the great writing.
Excellent site you’ve got here.. It’s hard to find good quality writing like
yours these days. I really appreciate individuals like you!
Take care!!
Have you ever considered writing an e-book or guest authoring on other sites?
I have a blog based on the same topics you discuss and
would love to have you share some stories/information.
I know my subscribers would enjoy your work. If you are even remotely interested, feel free to shoot me an e mail.
Exceptional post however I was wondering if
you could write a litte more on this subject? I’d be very grateful if you could elaborate a little bit
further. Thanks!
Hi there! I could have sworn I’ve been to this blog before but
after looking at some of the posts I realized it’s
new to me. Regardless, I’m certainly delighted I came
across it and I’ll be bookmarking it and checking back often!
Aw, this was a really nice post. Taking a few minutes and actual effort to generate a really good article…
but what can I say… I hesitate a whole lot and don’t manage to get anything done.
I am not positive the place you are getting your
information, but great topic. I must spend some time
learning more or figuring out more. Thank you for fantastic info I used to be in search of
this information for my mission.
pendik diş kliniği
Greetings! Very helpful advice in this particular post!
It’s the little changes that produce the largest changes.
Thanks a lot for sharing!
Chúng ta có thể dễ dàng lấy hạt ra
khỏi vỏ một cách nhanh chóng mà không bị dính vào vỏ.
Đậu gà khô ngâm qua đêm từ 8 tiếng – 12 tiếng sau đó
rửa sạch và bóc lớp vỏ bên ngoài, rửa sạch
1 lần nữa và cho vào rổ để ráo nước. Bước 1: Cho đậu gà vào nồi luộc trong vòng 30 phút
cho chín, sau đó vớt ra để ráo nước. Nếu không luộc
thì bạn cũng có thể bỏ trong nồi hấp và hấp hạt đậu gà trong vòng 30 phút nhé.
Đậu gà có chứa nhiều chất dinh dưỡng cho
cơ thể, nhưng bạn có biết đậu gà còn là một
món ăn rất tốt cho những người ăn kiêng, giảm cân. Ăn đậu gà có giảm cân được không ?
Chức năng bình luận bị tắt ở Ăn granola với sữa chua có đường được không
? Ăn granola với sữa chua có đường được không ?
Howdy! I could have sworn I’ve been to your blog before but after browsing through some of the posts I realized it’s new to
me. Regardless, I’m certainly happy I discovered it and I’ll be bookmarking it and checking
back frequently!
If you desire to obtain a great deal from this piece of writing then you have to apply these strategies to your won webpage.
I think this is one of the most important info for me.
And i’m glad reading your article. But should remark on few general things, The website style is ideal, the articles is
really great : D. Good job, cheers
Thank you for another excellent post. Where else may anybody get that type of
information in such a perfect means of writing? I have a presentation subsequent week, and I am at the search
for such information.
hello there and thank you for your information –
I have certainly picked up something new from right
here. I did however expertise some technical issues using this website, since I experienced to reload the website many
times previous to I could get it to load correctly. I had been wondering if your web
host is OK? Not that I am complaining, but sluggish loading instances times will very frequently affect your placement in google and could damage your high
quality score if ads and marketing with Adwords.
Anyway I am adding this RSS to my e-mail and
could look out for a lot more of your respective interesting content.
Ensure that you update this again soon.
Thank you for sharing your info. I really appreciate your efforts and
I am waiting for your further write ups thank you once again.
The other day, while I was at work, my sister stole my iPad and tested to see if it can survive a 40 foot drop, just so
she can be a youtube sensation. My iPad is now destroyed and she has 83 views.
I know this is completely off topic but I had to share it
with someone!
Hi, this weekend is pleasant for me, because this time i
am reading this great informative post here at my house.
Hãy rắc thêm một ít hạt chia trước khi dùng
món rau trộn 5-10 phút nhé. Rắc hạt chia lên món salad, ngũ cốc, sữa chua, bánh ngọt hay bất
kỳ loại thực phẩm nào cũng đều được.
Cẩm Nhung Sep 19 2017, 10:51:48 Shop ơi, có hạt chia mỹ Nutiva loại mới 907 gram không?
Tuy nhiên một số sản phẩm hạt chia Mỹ được lấy từ Mexico (đất gốc hạt chia) được cho là
có nhiều dinh dưỡng hơn. Giấy tờ cần có để làm visa
bao gồm ảnh, tờ khai thông tin cá nhân, chứng minh thư, sổ hộ khẩu, hợp đồng
lao động của cơ quan (hoặc bản sao công việc nếu bạn là chủ kinh doanh), nếu cho trẻ nhỏ
dưới 18 tuổi cần có giấy ủy quyền của bố
mẹ được xác nhận bởi chính quyền địa phương.
Các triệu chứng bệnh nhân giảm bớt sau khi điều trị bằng steroid.
Heya! I just wanted to ask if you ever have any trouble with hackers?
My last blog (wordpress) was hacked and I ended up losing several weeks of hard work due to no backup.
Do you have any solutions to protect against hackers?
Dapatkan berbagai promo menarik dan bonus cashback hanya di Mikigaming, situs game online terpercaya pilihan para gamer sejati.
КриптоБос Казино – Промоакции ежедневно для активных игроков!
http://0df.ru
Aw, this was a very good post. Taking the time and actual effort to produce a really good article… but what can I say… I procrastinate a whole lot and never manage to get anything done.
I am curious to find out what blog system you’re utilizing?
I’m having some small security problems with my latest website
and I’d like to find something more safeguarded. Do you have any
suggestions?
For most up-to-date news you have to pay a quick visit the web and on web I found this web site as
a most excellent website for most recent updates.
Thank you, I’ve recently been searching for info about
this topic for ages and yours is the greatest I have
found out till now. However, what concerning the conclusion? Are you positive concerning
the source?
Wonderful beat ! I wish to apprentice while you amend your website, how could i subscribe for a blog web site?
The account helped me a acceptable deal. I have been tiny
bit acquainted of this your broadcast provided bright transparent concept
Spot on with this write-up, I absolutely believe that this web site needs a lot more attention. I’ll probably be returning to see more, thanks for the info!
Hurrah, that’s what I was exploring for, what a stuff!
existing here at this web site, thanks admin of this web site.
Excellent site you’ve got here.. It’s hard to find excellent writing like yours these days.
I honestly appreciate people like you! Take care!!
Way cool! Some extremely valid points! I appreciate you penning this
write-up and also the rest of the site is also very good.
Thanks for sharing your thoughts. I truly appreciate your efforts and I will be waiting
for your further post thanks once again.
Howdy would you mind letting me know which hosting company you’re
working with? I’ve loaded your blog in 3 different browsers
and I must say this blog loads a lot faster then most.
Can you recommend a good hosting provider at a honest price?
Thanks, I appreciate it!
Attractive element of content. I simply stumbled upon your site and in accession capital to say that
I get actually loved account your blog posts. Anyway I will be subscribing in your
augment or even I success you get right of entry to constantly fast.
No air conditioning device is excellent for the environment
– nor are most very energy efficient.
situs slot gacor
This is a topic that is close to my heart… Best wishes!
Where are your contact details though?
After I initially commented I appear to have clicked the -Notify me when new comments are added- checkbox and now every time a comment is added I recieve 4 emails with the exact same comment. Is there a way you are able to remove me from that service? Thank you.
Great beat ! I wish to apprentice at the same time as you amend your site, how can i
subscribe for a blog site? The account aided me a applicable deal.
I had been a little bit acquainted of this your broadcast offered shiny clear concept
Good way of telling, and good post to take data about my presentation subject, which i
am going to present in institution of higher education.
I visited various blogs however the audio feature for audio songs present at this site is actually fabulous.
What’s up colleagues, good post and nice arguments commented here, I am genuinely enjoying by these.
Wow, fantastic blog layout! How lengthy have you been blogging
for? you make running a blog glance easy.
The overall look of your web site is wonderful, let alone the content material!
Just desire to say your article is as astonishing.
The clearness in your post is simply cool and i can assume you
are an expert on this subject. Well with your permission let me to grab your feed to keep up to date with
forthcoming post. Thanks a million and please carry on the enjoyable work.
Howdy! This article couldn’t be written any better!
Looking through this article reminds me of my previous roommate!
He continually kept preaching about this. I most certainly will forward this
post to him. Fairly certain he will have a great read.
Thanks for sharing!
Someone necessarily assist to make severely articles I’d state.
This is the very first time I frequented your web page and so far?
I amazed with the research you made to create this actual submit amazing.
Magnificent process!
It can aid to make your living or working environment extra comfortable and practical.
Great post. I used to be checking continuously this
weblog and I am inspired! Very helpful information specially the final phase
🙂 I deal with such info much. I used to be seeking this particular info for a very long time.
Thanks and best of luck.
This design is incredible! You certainly know how to keep a reader amused.
Between your wit and your videos, I was almost moved to start my own blog
(well, almost…HaHa!) Fantastic job. I really loved what you had to say, and more than that, how
you presented it. Too cool!
Hello! This post could not be written any better! Reading through this post reminds
me of my old room mate! He always kept talking about this.
I will forward this article to him. Fairly certain he will have a good read.
Thank you for sharing!
My brother suggested I might like this web site.
He used to be totally right. This post actually made
my day. You cann’t believe simply how much time I
had spent for this information! Thanks!
It is appropriate time to make some plans for the long run and it’s time to be happy.
I have learn this publish and if I could I wish to recommend you few attention-grabbing
things or advice. Maybe you could write next articles regarding this article.
I desire to read even more things about it!
Asking questions are truly good thing if you are not understanding anything fully, but this piece
of writing presents fastidious understanding even.
Paragraph writing is also a fun, if you know then you can write
if not it is difficult to write.
What’s up, I would like to subscribe for this website to get most up-to-date updates, thus where can i do it please help.
Having read this I believed it was rather enlightening. I appreciate you
spending some time and energy to put this informative article together.
I once again find myself personally spending a significant amount of
time both reading and leaving comments. But so what, it
was still worth it!
Fastidious respond in return of this issue with genuine arguments and describing
all on the topic of that.
May I just say what a comfort to find somebody who genuinely knows what they
are discussing on the web. You definitely understand how to bring an issue to light and make it important.
More people should check this out and understand this
side of your story. It’s surprising you aren’t more popular because you most certainly possess the
gift.
I enjoy, lead to I found just what I used to be looking for.
You’ve ended my four day long hunt! God Bless you man. Have a nice
day. Bye
That is a great tip particularly to those new to the blogosphere.
Simple but very accurate info… Many thanks for sharing this one.
A must read article!
Overwhelmed by expense tracking? Eliminate financial disorganization with our cutting-edge expense tracker!
Experience the convenience of automated https://play.google.com/store/apps/details?id=com.receiptscanner.app&hl=en_US organization.
Maximize your tax deductions with comprehensive summaries.
Unlock the potential of an app designed for optimal performance.
Download our financial tool today on the Play Store and take control of your records. Join the thousands of satisfied users who have simplified their tax preparation.
Your style is really unique in comparison to other people I have read stuff from.
Thank you for posting when you have the opportunity, Guess I’ll just bookmark this
page.
I know this if off topic but I’m looking into starting my own blog
and was curious what all is required to get setup?
I’m assuming having a blog like yours would cost a pretty
penny? I’m not very internet savvy so I’m not 100% certain. Any suggestions or advice would be greatly appreciated.
Appreciate it
Tentu! Berikut adalah contoh spintax untuk komentar di forum dengan tema
TIGERASIA88 dan Surgaslot:
Saya telah mendaftar di Surgaslot, dan pengalaman saya sangat memuaskan. Permainannya sangat menarik, dan saya bisa
memilih dari berbagai jenis permainan.
Yang saya suka adalah tingkat RTP yang tinggi, yang membuat saya merasa lebih tertarik.
Platformnya juga sangat ramah pengguna dan penarikan dana cepat.
Buat kalian yang suka main slot, saya rekomendasikan untuk coba TIGERASIA88.
Jangan lewatkan dan dapatkan promo spesial!
Howdy! I could have sworn I’ve been to this web site before but after browsing through many of the articles I realized it’s new to me.
Nonetheless, I’m certainly happy I found it and I’ll be bookmarking it and checking back
regularly!
Each indoor unit can be separately controlled so they can either all get on or
several of them as required.
Thank you for the auspicious writeup. It in reality was once a amusement account it.
Look complicated to more added agreeable from
you! However, how could we keep in touch?
If you would like to grow your familiarity simply keep visiting
this website and be updated with the hottest gossip posted here.
https://mazda-demio.ru/forums/index.php?autocom=gallery&req=si&img=6339
It’s going to be finish of mine day, however before end I am reading this
enormous post to improve my know-how.
Hi there, yup this piece of writing is truly good and I have learned lot of things from it regarding blogging.
thanks.
An outstanding share! I’ve just forwarded this onto a co-worker who has been doing
a little homework on this. And he actually bought me
lunch because I found it for him… lol.
So let me reword this…. Thank YOU for the meal!!
But yeah, thanks for spending the time to talk about this subject here on your site.
This blog was… how do I say it? Relevant!! Finally I’ve found something that helped me. Appreciate it.
Here is my site :: https://cryptominerspro.com/
Everything is very open with a clear description of the issues. It was truly informative. Your website is useful. Thanks for sharing.
You made some good points there. I checked on the net for more information about the issue
and found most people will go along with your
views on this website.
I’m really inspired with your writing abilities as well as with the format for your weblog.
Is this a paid subject or did you customize it
yourself? Either way keep up the nice quality writing, it is rare to see a great weblog like this one today..
It’s very straightforward to find out any matter on net
as compared to textbooks, as I found this article at this web site.
What’s Going down i am new to this, I stumbled upon this I have discovered It positively helpful
and it has helped me out loads. I hope to contribute & help other users like
its aided me. Great job.
Nicely put. Many thanks.
Link exchange is nothing else however it is only placing the other person’s
website link on your page at proper place and other person will also do
same in support of you.
Awesome! Its really awesome article, I have got much clear
idea regarding from this piece of writing.
I am sure this article has touched all the internet users, its
really really pleasant paragraph on building up new blog.
Write more, thats all I have to say. Literally, it seems as though you
relied on the video to make your point. You obviously know what youre talking about,
why waste your intelligence on just posting videos
to your site when you could be giving us something enlightening to read?
Hey there! Would you mind if I share your blog with my zynga group?
There’s a lot of folks that I think would really enjoy your content.
Please let me know. Many thanks
Great article. I’m going through a few of these issues as well..
However, this is not an uncomplicated question which we
can respond to exactly.
These are actually wonderful ideas in on the topic of blogging.
You have touched some good points here. Any way keep up wrinting.
This site was… how do I say it? Relevant!! Finally I
have found something which helped me. Thanks!
We are specialist installers+ and provide all the needed devices for
your setup, whatever the elevation or place.
Greetings! I know this is kinda off topic but I was wondering which blog platform are you
using for this site? I’m getting fed up of WordPress because I’ve had problems with hackers and I’m
looking at alternatives for another platform.
I would be great if you could point me in the direction of a good platform.
After going over a few of the blog posts on your site, I honestly appreciate your technique of blogging. I bookmarked it to my bookmark website list and will be checking back soon. Take a look at my website as well and tell me what you think.
What’s up colleagues, its wonderful paragraph about educationand fully defined, keep it up all the time.
My homepage … full article
I blog often and I genuinely appreciate your information. Your article has
truly peaked my interest. I will bookmark your website and keep checking for new details about
once per week. I subscribed to your Feed as well.
It’s appropriate time to make some plans
for the future and it’s time to be happy. I’ve read this post and if I could I want to suggest you some interesting things or suggestions.
Perhaps you could write next articles referring to this article.
I desire to read more things about it!
I’m really loving the theme/design of your website.
Do you ever run into any internet browser compatibility problems?
A number of my blog readers have complained about my site not operating correctly in Explorer but looks great in Chrome.
Do you have any recommendations to help fix this
problem?
Hello to every body, it’s my first visit of this webpage; this web site contains
awesome and truly fine stuff designed for visitors.
Asking questions are truly pleasant thing if you are not understanding anything entirely, however this
paragraph gives pleasant understanding yet.
Way cool! Some extremely valid points! I appreciate
you penning this article and also the rest of the website is
really good.
Hmm it appears like your website ate my first comment (it was super long) so I guess I’ll just sum it up what I wrote and
say, I’m thoroughly enjoying your blog. I as well am an aspiring
blog blogger but I’m still new to the whole thing.
Do you have any tips for first-time blog writers? I’d
definitely appreciate it.
Way cool! Some very valid points! I appreciate you penning this write-up and also the rest of the website is also very good.
I was more than happy to discover this web site. I need to to thank you for ones
time for this particularly wonderful read!! I definitely really liked every bit of it and i also have you
book-marked to see new things in your site.
Fastidious response in return of this difficulty with solid arguments and explaining the whole thing
concerning that.
You are so awesome! I do not suppose I have read through a single thing like this before.
So nice to discover another person with some original thoughts on this issue.
Seriously.. thanks for starting this up. This site is
one thing that’s needed on the internet, someone with a bit of originality!
It’s actually very complicated in this busy life to listen news on Television, therefore I just use web for that purpose,
and get the hottest news.
Wow, that’s what I was searching for, what a stuff! existing here at this webpage, thanks admin of this web site.
Hello exceptional blog! Does running a blog like this take a lot of work?
I have absolutely no understanding of computer programming however I was hoping to start my
own blog in the near future. Anyways, if you have any
suggestions or tips for new blog owners please share.
I understand this is off subject however I simply had to
ask. Kudos!
Fantastic website. A lot of helpful info here. I’m sending
it to several buddies ans also sharing in delicious.
And obviously, thanks in your sweat!
Howdy! Would you mind if I share your blog with my zynga group?
There’s a lot of people that I think would really
appreciate your content. Please let me know. Thank
you
You need to be a part of a contest for one of the most useful blogs on the internet. I’m going to recommend this blog!
Hello, Neat post. There is a problem with your web site in internet explorer, might
test this? IE still is the marketplace leader and a good
section of people will miss your excellent writing due to this
problem.
I love your blog.. very nice colors & theme. Did you make this website yourself or did you hire
someone to do it for you? Plz answer back as I’m looking to construct my own blog and would
like to find out where u got this from. cheers
Neat blog! Is your theme custom made or did you download it
from somewhere? A design like yours with a few simple adjustements
would really make my blog stand out. Please
let me know where you got your design. Many thanks
I want to to thank you for this wonderful read!!
I absolutely loved every bit of it. I have you book-marked to look
at new things you post…
Many thanks, Wonderful stuff.
You really make it seem so easy with your presentation but I
find this topic to be really something which I think I would never understand.
It seems too complicated and very broad for me.
I am looking forward for your next post, I will try to get the hang of it!
You actually make it seem really easy together with your
presentation however I find this topic to be really one thing that I think I might
never understand. It seems too complex and extremely broad for
me. I am having a look ahead for your subsequent put
up, I will try to get the grasp of it!
Hi to all, the contents present at this web site are truly awesome
for people experience, well, keep up the good work fellows.
Very good info. Lucky me I ran across your website by accident (stumbleupon).
I’ve saved as a favorite for later!
Excellent article. Keep posting such kind of information on your blog.
Im really impressed by your site.
Hello there, You’ve done an excellent job. I’ll certainly digg it and personally suggest to my
friends. I’m sure they’ll be benefited from this site.
E2bet là nhà cái có kho game phong phú và đa dạng, bao gồm
casino, thể thao, đá gà,… Bạn sẽ có những trải
nghiệm tuyệt vời nhất tại nhà cái khi được bảo mật
Hi there Dear, are you truly visiting this website daily, if so after that you will definitely obtain good knowledge.
It’s not my first time to go to see this
web site, i am visiting this website dailly and take
nice information from here everyday.
I used to be able to find good info from your articles.
It’s a shame you don’t have a donate button! I’d certainly donate to this excellent blog!
I guess for now i’ll settle for book-marking and adding your RSS feed to my Google account.
I look forward to fresh updates and will share this blog with my Facebook group.
Chat soon!
Hello There. I found your blog the usage of msn. That is a really neatly written article.
I’ll be sure to bookmark it and return to learn extra of your useful information. Thank you for the post.
I will definitely comeback.
Hi to every one, since I am genuinely keen of reading this web
site’s post to be updated regularly. It contains good stuff.
Here is my blog post; https://t.me/cryptonetlake
Great goods from you, man. I have keep in mind your stuff prior to and you’re simply extremely wonderful.
I really like what you have bought right here, certainly like what you are saying and the
best way through which you assert it. You make it enjoyable and you continue
to care for to keep it wise. I can not wait to learn much more from you.
That is actually a wonderful web site.
Hello! Would you mind if I share your blog with my facebook group?
There’s a lot of people that I think would really appreciate your content.
Please let me know. Cheers
Hello i am kavin, its my first occasion to commenting anywhere, when i
read this piece of writing i thought i could also
make comment due to this brilliant paragraph.
Hmm is anyone else encountering problems with the pictures on this blog loading?
I’m trying to find out if its a problem on my end or if it’s
the blog. Any suggestions would be greatly
appreciated.
Hello There. I found your blog using msn. This is an extremely well written article.
I will make sure to bookmark it and return to
read more of your useful information. Thanks for the post.
I’ll certainly comeback.
Яким чином пройти реєстрацію в казино за пару
кліків? https://kemhealthcare.co.uk/ggbet-kazino-onlajn-skachati-ggbet-ukraina-gg-bet-73
Свиноед 混蛋 Лайк, крап 滚开 Пидор
硬屁股 Короз
I got this web site from my friend who informed me regarding this
website and now this time I am browsing this website and
reading very informative articles at this place.
https://myteana.ru/forums/index.php?autocom=gallery&req=si&img=6622
Hello, just wanted to tell you, I liked this article.
It was funny. Keep on posting!
I visited multiple blogs except the audio quality for
audio songs present at this web site is genuinely wonderful.
Hi my loved one! I wish to say that this post is awesome, great written and come with
approximately all significant infos. I’d like to look more posts like this .
Its such as you learn my thoughts! You seem to know a lot about this, like you wrote the ebook in it or
something. I believe that you just can do with a few % to drive the
message home a bit, but other than that, this is fantastic blog.
An excellent read. I’ll definitely be back.
An impressive share! I have just forwarded this onto a coworker
who had been conducting a little research on this. And he in fact ordered me dinner due to the fact that I found it for him…
lol. So allow me to reword this…. Thanks for the meal!!
But yeah, thanx for spending the time to talk about this matter
here on your blog.
I’m impressed, I have to admit. Rarely do I
encounter a blog that’s both educative and engaging, and let me tell you, you have hit the nail on the head.
The problem is something which too few people are speaking intelligently about.
Now i’m very happy that I came across this during my hunt for something
relating to this.
Casino Together opère sous une licence délivrée par les autorités de Curaçao, une réglementation reconnue dans l’industrie des jeux en ligne.
Very descriptive post, I enjoyed that a lot.
Will there be a part 2?
Having read this I believed it was really enlightening.
I appreciate you spending some time and effort to put this informative
article together. I once again find myself spending
way too much time both reading and posting comments.
But so what, it was still worth it!
At this moment I am going away to do my breakfast, when having my breakfast coming
over again to read additional news.
I don’t know whether it’s just me or if perhaps everyone
else experiencing problems with your website.
It looks like some of the written text within your content are running
off the screen. Can someone else please provide feedback and let
me know if this is happening to them too? This might be a
problem with my browser because I’ve had this happen before.
Kudos
Superb blog! Do you have any tips for aspiring writers?
I’m hoping to start my own site soon but I’m a little lost on everything.
Would you propose starting with a free platform like WordPress or go for a paid option? There are so many
choices out there that I’m totally confused .. Any recommendations?
Many thanks!
Excellent way of describing, and pleasant post to obtain facts about my presentation subject matter, which i am going to present in college.
Великолепие Азарта: Казино Леон и
Ваш Путь к Успеху https://leon-0399.top
Hola! I’ve been reading your web site for some time now and finally
got the courage to go ahead and give you a shout out from Houston Tx!
Just wanted to say keep up the excellent job!
I’m gone to say to my little brother, that he should
also visit this blog on regular basis to take updated from latest
reports.
It’s hard to find knowledgeable people on this topic, but
you seem like you know what you’re talking about!
Thanks
Hello, constantly i used to check blog posts here in the early hours in the break of day,
because i enjoy to gain knowledge of more and more.
Hi my family member! I want to say that this post is amazing,
nice written and come with approximately all important infos.
I’d like to see more posts like this .
Thanks for the good writeup. It in fact was a entertainment account it.
Glance complicated to more introduced agreeable from you!
However, how could we keep in touch?
I am sure this article has touched all the internet people, its
really really nice post on building up new webpage.
E2Bet Indonesia, situs judi online terbesar di Indonesia, aman, terpercaya, dan inovatif, bonus menarik dan layanan pelanggan 24/7.
#E2Bet #E2BetIndonesia #Indonesia
I’m not that much of a online reader to be honest but your sites really
nice, keep it up! I’ll go ahead and bookmark your site to come back down the road.
Cheers
Thank you for the auspicious writeup. It in fact was a amusement account it.
Glance advanced to more delivered agreeable from
you! By the way, how can we keep in touch?
I used to be able to find good advice from your content.
Greetings! This is my first comment here so I just wanted to give a quick shout out and tell you I truly enjoy reading your blog
posts. Can you recommend any other blogs/websites/forums
that deal with the same topics? Many thanks!
Hi, after reading this amazing piece of writing i am too delighted to share my experience here with mates.
It’s hard to come by well-informed people on this topic, but you sound like you know
what you’re talking about! Thanks
It’s a shame you don’t have a donate button! I’d without
a doubt donate to this brilliant blog! I guess for now i’ll
settle for bookmarking and adding your RSS feed to my
Google account. I look forward to fresh updates and will talk about this website
with my Facebook group. Chat soon!
Hello, I enjoy reading through your post. I wanted to write a little comment to support you.
Great info. Lucky me I ran across your blog by
accident (stumbleupon). I’ve saved as a favorite for later!
At this moment I am going away to do my breakfast, after having my breakfast coming yet again to
read more news.
Hey There. I found your blog using msn. This is a
very well written article. I will make sure to bookmark it and return to read more of your useful information. Thanks for the post.
I’ll definitely return.
I am in fact grateful to the holder of this web page who has shared this fantastic post at here.
Hello to all, how is everything, I think every one is getting more
from this site, and your views are fastidious in support of new people.
Good web site you have here.. It’s difficult to find
high-quality writing like yours nowadays.
I honestly appreciate individuals like you! Take care!!
Undeniably consider that that you stated. Your favourite
reason appeared to be at the web the simplest factor to
have in mind of. I say to you, I certainly
get irked whilst other people think about concerns that they plainly
don’t understand about. You managed to hit the nail upon the top as neatly as outlined
out the entire thing without having side effect , other folks can take a signal.
Will likely be back to get more. Thank you
Wow, awesome blog format! How lengthy have you ever been blogging
for? you made blogging glance easy. The total
look of your web site is wonderful, as neatly as the content!
Hi to all, it’s genuinely a fastidious for me to visit this
site, it consists of precious Information.
Discover thousands of the latest and popular films from various genres.
Enjoy high-quality movie streaming experience without any subscription needed.
A motivating discussion is worth comment. I believe
that you should publish more about this topic, it might not
be a taboo matter but generally folks don’t discuss such issues.
To the next! All the best!!
great put up, very informative. I wonder why the
other specialists of this sector do not notice this. You
should proceed your writing. I am confident, you
have a huge readers’ base already!
Howdy great blog! Does running a blog similar to this require a massive amount work?
I’ve virtually no understanding of coding however I was hoping to
start my own blog in the near future. Anyway, should you have any suggestions or techniques for new blog owners please share.
I understand this is off subject however I simply needed to ask.
Appreciate it!
SCATTER HITAM
Mitt enda klagomål är att det inte finns en egen kategori för exklusiva spel, vilket gör dem lite svåra att hitta.
Link exchange is nothing else but it is only placing the other person’s web sote link on your page at suitable place and other person will also do similar in favor of you.
Good day! This is kind of off topic but I need some guidance
from an established blog. Is it very difficult to set up your own blog?
I’m not very techincal but I can figure things out pretty fast.
I’m thinking about making my own but I’m not sure where to start.
Do you have any ideas or suggestions? Thanks
I think the admin of this site is genuinely working hard in support of his site, since here every material is quality based
stuff.
https://mazda-demio.ru/forums/index.php?autocom=gallery&req=si&img=6441
I am curious to find out what blog platform you’re working with?
I’m having some minor security issues with my latest website and I would like to find something more safe.
Do you have any suggestions?
I could not refrain from commenting. Exceptionally well written!
I’ve been browsing online more than 2 hours today, yet I never
found any interesting article like yours. It is pretty worth enough for me.
In my view, if all website owners and bloggers made good content as you did,
the internet will be a lot more useful than ever before.
Aw, this was a really nice post. Spending some time and actual effort to produce
a very good article… but what can I say… I hesitate a whole
lot and don’t seem to get nearly anything done.
It’s a shame you don’t have a donate button! I’d
certainly donate to this superb blog! I guess for now i’ll settle for bookmarking and adding your RSS feed to my Google account.
I look forward to brand new updates and will share this site with my Facebook
group. Talk soon!
Hi, just wanted to tell you, I enjoyed this blog post.
It was inspiring. Keep on posting!
I want to to thank you for this good read!!
I absolutely enjoyed every little bit of it. I’ve got you bookmarked to check
out new things you post…
Thanks a lot for sharing this with all of us you really recognize what you are speaking
approximately! Bookmarked. Kindly also talk over with my web site =).
We may have a hyperlink alternate contract among us
Легко ли быть наблюдателем, когда вокруг творится зло и нельзя вмешаться, навести порядок, защитить? Главный герой этого романа – дон Румата (землянин Антон), который попадает на планету Арканар с экспериментальным миром. На этой планете царит средневековая жестокость, фальшь и борьба за власть. Но Румата не должен вмешиваться. Он ученый, который проводит эксперимент. Однако человек в нем берет вверх над ученым, сердце побеждает рассудок. Разве можно спокойно наблюдать, как зло побеждает добро, как талант растаптывается, а справедливости не существует? Главному герою это не удается…
https://knigavuhe.org/book/27295-trudno-byt-bogom/
Hello! I could have sworn I’ve been to this site before but after browsing through some of the articles I realized
it’s new to me. Anyways, I’m definitely delighted I stumbled upon it and I’ll be book-marking it
and checking back regularly!
Very good post! We will be linking to this great
content on our site. Keep up the good writing.
I’m really enjoying the design and layout of your site.
It’s a very easy on the eyes which makes it much more enjoyable for me to come here and
visit more often. Did you hire out a designer to create your theme?
Exceptional work!
Keep on writing, great job!
Hi friends, its fantastic paragraph concerning cultureand completely
explained, keep it up all the time.
Thanks in favor of sharing such a fastidious thought, post
is fastidious, thats why i have read it completely
Thanks very interesting blog!
This is nicely expressed. .
I truly love your website.. Very nice colors & theme.
Did you create this amazing site yourself? Please reply back
as I’m looking to create my own personal
site and would love to know where you got this from or just what the theme is
called. Appreciate it!
We absolutely love your blog and find a lot of your post’s to
be just what I’m looking for. Do you offer guest writers to write content available for you?
I wouldn’t mind creating a post or elaborating on a number of the
subjects you write about here. Again, awesome web site!
It’s remarkable designed for me to have a web page, which is helpful
in support of my know-how. thanks admin
Oh my goodness! Impressive article dude! Thanks, However I am having issues with your RSS.
I don’t understand why I cannot subscribe to it.
Is there anybody getting the same RSS issues? Anyone
that knows the solution will you kindly respond? Thanks!!
Hi! I just wanted to ask if you ever have any trouble with hackers?
My last blog (wordpress) was hacked and I ended up losing many months of hard work due to no back up.
Do you have any solutions to protect against hackers?
I always used to read article in news papers but now as I am a user of internet so from now I am using net for articles, thanks to web.
magnificent points altogether, you just won a logo new reader.
What could you suggest about your post that you made some days
in the past? Any certain?
We absolutely love your blog and find most of your post’s to be exactly what I’m
looking for. can you offer guest writers to write content to suit your needs?
I wouldn’t mind writing a post or elaborating on a number of
the subjects you write regarding here. Again, awesome website!
Does your website have a contact page? I’m having a tough
time locating it but, I’d like to shoot you an email. I’ve got
some ideas for your blog you might be interested in hearing.
Either way, great site and I look forward to
seeing it grow over time.
Hey! This post could not be written any better! Reading through this
post reminds me of my old room mate! He always kept chatting
about this. I will forward this post to
him. Pretty sure he will have a good read. Many thanks for sharing!
Hello just wanted to give you a quick heads up and let you know a few of the images aren’t loading
properly. I’m not sure why but I think its a linking issue.
I’ve tried it in two different web browsers and both show the same outcome.
Wow! At last I got a weblog from where I can in fact obtain useful data regarding my study and
knowledge.
I don’t even know how I finished up right here, however I
assumed this submit was once great. I don’t recognise who you’re however certainly you are going to a well-known blogger in case you are not already.
Cheers!
Ceci afin de se conformer aux règles de lutte contre le
blanchiment d’argent.
Attractive portion of content. I simply stumbled upon your site and in accession capital to say that I acquire actually enjoyed account your blog posts.
Any way I will be subscribing in your feeds or even I
success you get right of entry to consistently fast.
взломанные игры с бесконечными ресурсами — это интересный способ расширить функциональность игры.
Особенно если вы играете на мобильном устройстве с Android, модификации открывают перед вами огромный
выбор. Я лично использую взломанные
игры, чтобы достигать большего.
Моды для игр дают невероятную возможность настроить игру, что погружение в игру гораздо красочнее.
Играя с твиками, я могу добавить дополнительные функции,
что добавляет новые приключения и делает игру более непредсказуемой.
Это действительно интересно,
как такие моды могут улучшить взаимодействие с игрой, а при этом
сохраняя использовать такие модифицированные приложения можно без особых неприятных последствий, если быть
внимательным и следить за обновлениями.
Это делает каждый игровой процесс лучше контролируемым,
а возможности практически бесконечные.
Советую попробовать такие игры с модами для Android — это может добавить веселья
в геймплей
Just want to say your article is as astonishing. The clarity for your post is just spectacular and
i can think you are knowledgeable in this subject.
Well along with your permission allow me to take hold of your RSS
feed to stay up to date with coming near near post. Thanks 1,000,000 and please
carry on the enjoyable work.
Hello There. I discovered your blog the use of msn.
This is an extremely smartly written article. I’ll make sure
to bookmark it and return to read extra of your helpful info.
Thank you for the post. I’ll certainly comeback.
Please let me know if you’re looking for a article author
for your weblog. You have some really great
posts and I think I would be a good asset. If you ever
want to take some of the load off, I’d absolutely love to write some material for your
blog in exchange for a link back to mine. Please shoot me an email if interested.
Cheers!
I really like it whenever people get together and share thoughts.
Great blog, keep it up!
Hello would you mind sharing which blog platform you’re
using? I’m going to start my own blog soon but I’m having a tough time making a decision between BlogEngine/Wordpress/B2evolution and Drupal.
The reason I ask is because your design seems different then most blogs and I’m looking for something completely unique.
P.S My apologies for being off-topic but I had to ask!
hello there and thank you for your info – I’ve definitely picked up
anything new from right here. I did however expertise some technical issues using this site,
as I experienced to reload the web site many times previous to I could get it to load properly.
I had been wondering if your web host is OK?
Not that I’m complaining, but sluggish loading
instances times will often affect your placement in google and
could damage your high-quality score if ads and marketing with Adwords.
Anyway I’m adding this RSS to my email and could look out for a lot more of your
respective intriguing content. Ensure that you update this again very soon.
Keep this going please, great job!
You could certainly see your expertise within the work you write.
The sector hopes for even more passionate writers such as you who are not afraid
to say how they believe. At all times go after your heart.
Attractive part of content. I simply stumbled upon your web
site and in accession capital to claim that I get actually enjoyed account your blog
posts. Any way I’ll be subscribing in your augment
or even I success you get entry to consistently quickly.
Hi there! I just wanted to ask if you ever have any trouble
with hackers? My last blog (wordpress) was hacked and I
ended up losing months of hard work due to no data backup.
Do you have any solutions to stop hackers?
No matter if some one searches for his essential thing, thus he/she wishes to be available that in detail,
therefore that thing is maintained over here.
Greetings I am so grateful I found your blog page, I really found you by mistake, while I
was browsing on Digg for something else, Regardless I am here now and would just like to say
many thanks for a fantastic post and a all round entertaining blog (I also love the theme/design),
I don’t have time to read through it all at the minute but I have book-marked it and also added in your RSS feeds,
so when I have time I will be back to read a lot more, Please do keep up the excellent work.
This is my first time visit at here and i am really pleassant to read everthing at single place.
I’m no longer positive where you’re getting your info, but great topic.
I needs to spend a while learning more or figuring out more.
Thank you for great info I was in search of this info for my mission.
smm panel
Every weekend i used to pay a visit this site, because i wish for
enjoyment, for the reason that this this website
conations actually nice funny material too.
Appreciate this post. Let me try it out.
my homepage mounfit weight loss
Hi friends, how is all, and what you want to say on the topic of
this piece of writing, in my view its genuinely remarkable for me.
Wow that was odd. I just wrote an extremely long comment but after I clicked submit my comment didn’t show up.
Grrrr… well I’m not writing all that over again. Anyways, just wanted to say great blog!
It’s going to be end of mine day, but before finish I am
reading this great paragraph to increase my know-how.
Excellent article. I absolutely love this website. Keep writing!
When some one searches for his necessary thing, therefore he/she desires to be available that
in detail, so that thing is maintained over here.
you are actually a just right webmaster. The website loading speed is amazing.
It sort of feels that you’re doing any unique trick. Moreover, The contents are masterpiece.
you have performed a magnificent task on this subject!
Wow! This blog looks just like my old one! It’s on a entirely different topic but it has pretty much the same layout and design. Excellent choice of colors!
Awesome https://is.gd/tpjNyL
Thanks for the marvelous posting! I seriously enjoyed reading it,
you’re a great author. I will make certain to bookmark your blog and will often come
back sometime soon. I want to encourage you to ultimately continue your great writing, have a
nice afternoon!
you are really a just right webmaster. The site loading pace is amazing.
It sort of feels that you’re doing any unique trick.
In addition, The contents are masterpiece. you’ve performed
a fantastic task in this topic!
Unquestionably believe that which you said. Your favorite reason seemed to be on the net the
easiest thing to be aware of. I say to you, I
definitely get irked while people consider worries that they plainly
do not know about. You managed to hit the nail upon the top and defined out the whole thing without having side effect , people can take a signal.
Will probably be back to get more. Thanks
After going over a handful of the blog posts on your web
site, I honestly appreciate your way of writing a blog. I book marked it to my
bookmark webpage list and will be checking back soon.
Please check out my website as well and tell me your opinion.
I always used to read piece of writing in news papers but now as I am a user of internet
thus from now I am using net for articles or reviews, thanks
to web.
Greetings! Very helpful advice within this post!
It is the little changes that produce the most important changes.
Many thanks for sharing!
Very good information. Lucky me I came across your website by chance (stumbleupon). I have book marked it for later!
Amazing info, Thank you.
Link exchange is nothing else however it is only placing the other person’s weblog link on your page at proper place and other
person will also do same for you.
Thanks a bunch for sharing this with all folks you actually know what
you are speaking approximately! Bookmarked. Please also
discuss with my website =). We could have a hyperlink
change contract among us
I must thank you for the efforts you’ve put in writing this website.
I am hoping to see the same high-grade content from you in the future as well.
In truth, your creative writing abilities has
inspired me to get my very own blog now 😉
It’s hard to find knowledgeable people about this subject, but you seem like you know what you’re
talking about! Thanks
Article writing is also a fun, if you be familiar with after that you
can write otherwise it is difficult to write.
Hello there! I simply want to offer you a huge thumbs up for
the great info you have got right here on this post. I am coming back to your web site for more soon.
Spot on with this write-up, I really believe this site needs a lot more attention.
I’ll probably be returning to read through more, thanks
for the info!
Hi there! I just wanted to ask if you ever have any problems
with hackers? My last blog (wordpress) was hacked and I ended up losing a few months
of hard work due to no data backup. Do you have any solutions to stop hackers?
WOW just what I was looking for. Came here by searching for Login Iontogel
If you want to take a great deal from this post then you
have to apply such techniques to your won webpage.
Link exchange is nothing else however it is just placing the other person’s webpage link on your
page at suitable place and other person will also do similar for you.
Hey very nice blog!
Hi there everyone, it’s my first visit at
this website, and article is really fruitful in support of me, keep up posting these
content.
Wow, superb blog layout! How long have you been blogging for?
you made blogging look easy. The overall look of your site is fantastic, as well as the
content!
Thanks for every other informative website.
Where else could I get that type of info written in such an ideal approach?
I’ve a project that I am just now operating on, and I’ve been on the look out for such info.
As the admin of this web page is working, no uncertainty very rapidly
it will be well-known, due to its quality contents.
Hello there! This post could not be written much better!
Looking through this post reminds me of my previous roommate!
He always kept preaching about this. I’ll forward this article to him.
Pretty sure he’ll have a very good read. I appreciate you for sharing!
Feel free to visit my blog – the memory wave
I delight in, result in I discovered exactly what I used to
be looking for. You have ended my 4 day lengthy hunt!
God Bless you man. Have a nice day. Bye
Definitely imagine that which you stated. Your favorite reason seemed to be on the
web the simplest factor to take note of. I say to you, I definitely get annoyed at the same time as other people think about issues that they plainly do not know
about. You controlled to hit the nail upon the top as neatly as outlined out the whole thing without having side effect ,
other folks could take a signal. Will likely be again to
get more. Thanks
Dinah Shore’s son, John David “J.D.” Clarke, had a life marked by personal struggles.
He faced challenges with substance abuse and mental health issue
Read more
TV Shows and Series
What kind of implants did Pandora peaks have?
Asked by Anonymous
Pandora Peaks, an adult film star and model, is known for her large breast implants, which are often reported to be in the range of 38DD
or larger. She underwen
Read more
TV Shows and Series
What extraordinary things you know?
Asked by Anonymous
Extraordinary things often encompass remarkable natural
phenomena, such as the Northern Lights, which paint the night
sky with vibrant colors due to solar parti
Read more
TV Shows and Series
What is the origin of the terms dear gussie?
Asked by Anonymous
The phrase “dear Gussie” originates from the 1980s television show
“Designing Women,” where it was frequently used by character Suzanne Suga
Read more
TV Shows and Series
Where is the cone in I spy treasure hunt page 3-4?
Asked by Anonymous
In “I Spy Treasure Hunt,” the cone on pages 3-4 is typically hidden among various objects in a busy scene.
To find it, look closely at the illustratio
Read more
TV Shows and Series
What to do if you have 3 girls and 1 boy in a club?
Asked by Anonymous
If you have three girls and one boy in a club, consider promoting inclusivity by ensuring that all voices are heard and
valued during discussions and activities
Read more
TV Shows and Series
What is 2-hi and 2-lo on 4wd?
Asked by Anonymous
In a 4WD (four-wheel drive) system, “2-hi” refers to the two-wheel drive mode,
where power is sent only to the rear wheels, providing better fuel effi
Read more
TV Shows and Series
Why did they stop doing the show horseland?
Asked by Anonymous
“Horseland,” an animated series about a group of young equestrians and their horses, was ultimately discontinued
due to a combination of factors, incl
Read more
TV Shows and Series
+1
Who is the cute blonde with gold glasses on tmz?
Asked by Anonymous
The cute blonde with gold glasses often featured on TMZ is likely to be one of their reporters
or hosts, such as Katelyn Jae or another on-air personality.
TMZ
Read more
TV Shows and Series
How might the mystery besolved by detectives?
Asked by Anonymous
Detectives often solve mysteries by gathering and analyzing evidence, interviewing witnesses, and following leads that may point to a suspect.
They use forensic
Read more
TV Shows and Series
Where is the dog in where is Waldo in Hollywood page
a dream come true?
Asked by Anonymous
In the “Where’s Waldo? In Hollywood” page titled “A Dream Come True,” the dog can be found in the lower right corner of the illustration. Th
Read more
TV Shows and Series
What do originating addresses TP-OA 131 and TP-OA 123 mean?
Asked by Anonymous
Originating addresses TP-OA 131 and TP-OA 123 typically refer to
specific identifiers used in telecommunications or data networks to denote the source of a tran
Read more
TV Shows and Series
Where is Mickey Rooney’s house in Palm Springs?
Asked by Anonymous
Mickey Rooney’s former house in Palm Springs is located
in the prestigious neighborhood of the Movie Colony.
The home is known for its mid-century architecture
Read more
TV Shows and Series
Where can you find a copy of 2nd resurrection by the
stairsteps?
Asked by Anonymous
You can find a copy of “2nd Resurrection” by The Stairsteps through various music
platforms such as Spotify, Apple Music, or YouTube.
Additionally, ph
Read more
TV Shows and Series
How much does scrubs cast make?
Asked by Anonymous
The cast of “Scrubs” had varying salaries over the show’s nine-season run, with lead actors like Zach Braff and Sarah
Chalke reportedly earning around
Read more
TV Shows and Series
What type of lights should be used when parked on the highway at night?
Asked by Anonymous
When parked on the highway at night, you should use your hazard lights to
alert other drivers of your presence. Additionally,
if you are safely off the road, us
Read more
TV Shows and Series
What did Ozzie ancesters come over?
Asked by Anonymous
Ozzie ancestors, particularly those from Australia,
are primarily of British descent, having arrived during the colonization in the late
18th century. The First
Read more
TV Shows and Series
+1
Where can you watch full episodes of Gilmore Girls online with English
subtitles?
Asked by Anonymous
You can watch full episodes of “Gilmore Girls” online on streaming platforms like Netflix and Hulu, both of which offer the series with English subtit
Read more
TV Shows and Series
Why was tour of duty cancelled?
Asked by Anonymous
“Tour of Duty,” the Vietnam War-themed television series, was canceled primarily due to declining ratings after its initial seasons.
Although it recei
Read more
TV Shows and Series
Who did jerriann have th affair with?
Asked by Anonymous
I’m sorry, but I need more context to provide an accurate answer.
If you can specify which Jerriann you are referring to or provide additional details,
I’d be h
Read more
TV Shows and Series
In the book Radiance what did riley realize after the council
showed her images of her life?
Asked by Anonymous
In the book “Radiance,” Riley realizes that her past experiences and choices are interconnected,
shaping her identity and purpose. The images presente
Read more
TV Shows and Series
Where was the father dowling mystery series filmed?
Asked by Anonymous
The “Father Dowling Mysteries” series was primarily filmed in Chicago, Illinois.
The show’s setting often showcased various Chicago
landmarks and neig
Read more
TV Shows and Series
What date was Whitsun 1986?
Asked by Anonymous
Whitsun, also known as Pentecost, is celebrated on the seventh Sunday after Easter.
In 1986, Easter Sunday fell on April 6, which means Whitsun was observed on
Read more
TV Shows and Series
What are the nine areas of responsibility for the FAA?
Asked by Anonymous
The Federal Aviation Administration (FAA) has nine areas of responsibility, which include:
regulating civil aviation to ensure safety;
overseeing air traffic co
Read more
TV Shows and Series
What does the bayux tapastry show?
Asked by Anonymous
The Bayeux Tapestry is an embroidered cloth that depicts the events leading up to the Norman Conquest of England in 1066, particularly the struggle between Will
Read more
PreviousNext
Trending Questions
What are the release dates for Crossroads – 1955 Anatole of the Bayous 1-29?
How was the past controlled in 1984? Did alex doumak have sisters or
brothers? Do pentacostals watch TV? What are
the release dates for Gerald McBoing Boing – 2005 Monsters Snowblowers and Planet Bedtime Fairs Mimes
and Dragons? What is the message of the old stranger in The War Prayer?
Is CMT in the same category as MS? What are the release dates
for 1971 Army-Navy Game – 1971 TV? What was the last episode of Martin?
What are the release dates for Conspiracy Theory with Jesse Ventura – 2009 The Louisiana Conspiracy?
How do Jack slap someone? What are the release dates for The Joey Bishop Show – 1967 – 2.74?
What were scandals of the great administration? Is Debbie Allen’s daughter
playing in the upcoming Maid show on TV? Who the sexest girl at
crest? What are the release dates for Lonelygirl15 – 2006 Germ Warfare
Attack 2-113? What are the best diners in Norristown PA?
Who are the CID men in catch 22? What are the release dates for All in the Family – 1971
The Draft Dodger 7-15? What is Diane McInerney’s ethnicity?
Still have questions?
Find more answers
Previously Viewed
When was Thüringer HC created? When was HC Most created?
What does the N in VN stand for it has 5 letters? What is the abbreviation for Venezuela?
What does the Chinese name Sinh mean?
Resources
Leaderboard All Tags Unanswered
Top Categories
Algebra Chemistry Biology World History English Language
Arts Psychology Computer Science Economics
Product
Community Guidelines Honor Code Flashcard Maker Study Guides
Math Solver FAQ
Company
About Us Contact Us Terms of Use Privacy Policy Disclaimer Cookie Policy IP Issues
Copyright ©2025 Infospace Holdings LLC, A System1
Company. All Rights Reserved. The material on this site can not be reproduced, distributed, transmitted, cached or otherwise used, except with prior written permission of Answers.
MAMAKMU JADI LONTE ANJENG
It’s really a cool and helpful piece of information. I’m glad that you shared this
helpful information with us. Please stay us up to date like this.
Thank you for sharing.
Wow! At last I got a web site from where I be capable of truly get
useful data regarding my study and knowledge.
I am extremely impressed along with your writing talents as well as with the format on your weblog.
Is that this a paid subject matter or did you modify it yourself?
Either way keep up the nice high quality writing, it’s uncommon to look a
great blog like this one today..
Pretty! This was a really wonderful post. Thanks for supplying this info.
I visited multiple blogs but the audio quality for audio songs existing at this web site is actually
fabulous.
It’s remarkable to pay a visit this web site and reading the views of all mates regarding this article, while
I am also zealous of getting knowledge.
Hey There. I discovered your weblog using msn. That is a very smartly written article.
I’ll be sure to bookmark it and return to learn extra of your useful information. Thank you for the post.
I will definitely comeback.
Do you have a spam problem on this blog; I also am a blogger, and I was curious about your situation;
we have created some nice practices and we are
looking to exchange methods with other folks, please shoot me an email if
interested.
Hi Dear, are you actually visiting this web site on a regular basis,
if so then you will absolutely obtain fastidious knowledge.
You actually reported that fantastically.
Wow a good deal of awesome facts!
Very good post! We will be linking to this great article on our
website. Keep up the good writing.
Hello, after reading this remarkable paragraph i am also happy
to share my knowledge here with friends.
I am not sure where you are getting your info, but great topic.
I needs to spend some time learning more or understanding more.
Thanks for fantastic info I was looking for this info for my mission.
Excellent way of telling, and nice piece of writing to
take data about my presentation subject matter, which i am going to
convey in university.
Very great post. I just stumbled upon your weblog and wanted to mention that I have really loved surfing around your blog posts.
In any case I’ll be subscribing to your feed and I’m hoping you write once more soon!
Incredible points. Outstanding arguments. Keep up the amazing
effort.
wonderful post, very informative. I wonder why the other specialists of this sector do not notice this.
You must proceed your writing. I’m sure, you have
a huge readers’ base already!
You actually make it seem so easy with your presentation but I find this matter
to be really something which I think I would never understand.
It seems too complex and extremely broad for me.
I am looking forward for your next post, I will try to get the hang of it!
Very good post. I’m going through many of these issues as well..
This is really fascinating, You’re an overly skilled blogger.
I have joined your feed and look ahead to searching for extra of your fantastic post.
Additionally, I’ve shared your website in my social networks
Howdy would you mind letting me know which webhost you’re using?
I’ve loaded your blog in 3 different internet browsers and I must say this blog loads a lot faster then most.
Can you suggest a good web hosting provider at a reasonable price?
Cheers, I appreciate it!
Touche. Sound arguments. Keep up the amazing effort.
I am in fact thankful to the owner of this site who has shared this wonderful article at here.
A string of women have revealed they were left suicidal and wracked by horrific nightmares in the wake of a fake paramedic’s sex attacks as he was jailed for 12 years today.
‘Predatory’ Jamie Kadolski, 24, was an ambulance call handler and first responder who wore his NHS uniform
on his dating app profile photo.
But the Walter Mitty character concealed his junior role when he met women by placing stickers over personal information on his ID
card and instead claimed he saved lives on ambulances.
His offending came to light in November 2023 when a woman contacted police to make
an allegation against him.
Yet he continued to commit offences against other women while on bail and was arrested again in March and April this year.
Attacks were carried out at a victim’s flat, in his own home in Norwich, Norfolk, and in his car
after driving a victim to an isolated spot at Hempton,
near Fakenham.
During his sentencing hearing at Norwich Crown Court today, his victims bravely took the
stand to describe the devastating effect he had had on their lives.
One woman, who spoke quietly with her head down, said: ‘I did not
think I would make it to this day alive. I have attempted
suicide twice over the last two months.
Jamie Kadolski, 24, was an ambulance call handler and
first responder who wore his NHS uniform on his dating app
profile photo
He concealed his junior role when he met women by placing
stickers over personal information on his ID card and instead claimed he saved lives
on ambulances
‘I am a wreck and a shell of who I once was.
I have forgotten what it feels like to feel safe.’
She said she had lost her job working in a care home for
people with dementia after having panic attacks when paramedics
came in, with her manager telling her she had to leave.
The woman added: ‘I cannot bear to tell my friends or family
what he did to me. My relationship with my family will never be the same… I am now
terrified of men.’
She also apologised to other victims, saying: ‘While I got on with my life he
was attacking innocent people. I am sorry I was not brave
enough [to report him sooner].’
Another victim described how she took an overdose in November 2023 after being sexually assaulted by Kadolski two months earlier.
‘I could not stop thinking about what happened to me,’
she said, adding she quit her job and would lie in bed all day afterwards.
Telling the hushed court room that she had had tattoos to cover
her arms where she had self-harmed, she went on: ‘My mental health took a rapid decline.
I went to a bridge and wanted to die. I ended up being sectioned.’
A third woman dabbed at her eyes with tissues as she
struggled to compose herself.
Cold Kadolski smiled for the camera at a police station as officers took his mugshot
‘Since being raped my life has changed…
I could not tell my family for years. I never did.
They all found out on their own and the word spread,’ she said.
‘I never felt so humiliated, shamed or disappointed at that moment.
I cannot accept the reality of it when I sleep.’
She recalled being held “face down by a man who claimed he loved me” adding: ‘Almost every night I have nightmares
that he rapes me over and over… the joy of being in a relationship has been ripped away from me.’
The court heard a psychological report had found the defendant – who still claims
he is innocent and plans to appeal against his conviction –
pretended to be a paramedic to help with his ‘chronic low self-esteem’.
The expert who wrote it concluded: ‘He was prepared to deceive for the psychological
benefit he received.
‘Boosting his fragile ego… the deceit was to satisfy his own needs to achieve self-worth.’
Jailing Kadolski for 12 years with a three-year extended licence, Judge Anthony Bate said he had wilfully ‘misled’
his victims’
‘Each expected to be safe in your company and able to
enjoy a healthy and fulfilling relationship…[You] had a need to achieve dominance and enhance your status,’ he told the defendant, who showed
no emotion throughout the hearing.
His offending came to light in November 2023
when a woman contacted police to make an allegation against him but
he continued to commit offences against other women while on bail
Read More
Call handler who pretended he was a paramedic to impress Tinder dates convicted of sex attacks
The judge, who also imposed an indefinite sexual harm prevention order, added:
‘You continue to pose a high risk of sexual offending against women. You are, for the time
being, to be considered a dangerous offender.’
In a police interview, the fantasist – who said he was looking for ‘short-term fun’ on Tinder – told officers he wouldn’t have been capable of pinning someone down as he had suffered sexual abuse as a child.
Kadolski also denied arguing with one of
his accusers. He told police he remembered her crying on one occasion and coldly added:
‘I’m not the best with empathy or sympathy.’
The woman who was attacked at Hempton told the
court how she met the defendant on Tinder in 2022
and admitted she wanted to ‘get to know each other and see if the chemistry
was there’.
Some messages were ‘a bit flirty’ and sex was a possibility but she described how he undressed her and grabbed her breasts
‘aggressively’, as well as pulling her hair when they had sex in the back of his car.
She said she was unable to tell him to stop because she
had ‘frozen’ with fear and felt ‘very vulnerable’.
‘I just wanted it to stop and to end,’ she said.
Another victim complained Kadolski had ‘pulled her hair aggressively’ to keep her head in his lap while unzipping her shorts and
sexually assaulting her at his flat.
Attacks were carried out at a victim’s flat, in his own home in Norwich,
Norfolk, and in his car after driving a victim to an isolated
spot at Hempton, near Fakenham
In a police interview, the fantasist – who said he was looking for ‘short-term fun’ on Tinder – told officers he wouldn’t
have been capable of pinning someone down as he
had suffered sexual abuse as a child
Ambulances queued outside of the Norfolk and Norwich University Hospital – where Kadolski
also worked
‘I had to push his hand away, get up and do up my shorts,’ she
said.
‘There was no consent in the first place. At
no point did I say that what was happening to
me was okay with me.’
Kadolski, who also worked as a healthcare assistant at Norfolk and Norwich University Hospital, was convicted of three rapes, two counts of assault by
penetration and a sexual assault against the first victim in November last year following the trial.
He was cleared of attempting to suffocate her by putting a dog collar on her so tight that she
lost consciousness and another count of rape.
The jury also convicted him of sexual assault and assault by penetration against two other victims.
Kadolski, whose offences covered an 18-month period, was
cleared of raping a fourth woman.
The defendant, who resigned from the East of England Ambulance Service
(EEAS), had faced further charges of raping a woman while
she slept and false imprisonment of a woman who said
she was locked in a bathroom.
But during the trial the court was told he had no case to answer on the charges and
the jury was ordered to return not guilty verdicts.
Detective Constable Claire Floyd, who led the investigation, described Kadolski
as ‘predatory and remorseless’ after the hearing and paid
tribute to his victims coming forward.
Kadolski also worked as a healthcare assistant at Norfolk
and Norwich University Hospital (pictured)
‘The incredible strength and courage these women have shown throughout
the investigation and criminal justice process cannot be overstated,
‘ she said.
‘All have suffered traumatic ordeals at Kadolski’s
hands. It is thanks to them that he is now behind bars and
no longer able to cause harm to anyone else.’
EEAS paramedic Andrew Wheeler, 46, was jailed for 21 years in 2021 after being convicted
of sex attacks against two women and a girl.
One victim, a nurse, was raped at an ambulance station and assaulted
a year later when he treated her as a patient in an ambulance.
Another victim was an alcoholic who was told by Wheeler that nobody would believe her because of her
drink problem.
The girl was aged nine or ten when she was touched on the inner thigh by the defendant, who was
also involved with St John Ambulance.
In 2023, the troubled organisation was accused of ‘institutional racism’ and
staff branded ‘xenophobic’, with colleagues complaining that offensive behaviour was often dismissed as ‘banter’.
NHSTinder
wonderful post, very informative. I’m wondering why the other experts of this sector do not understand this.
You should proceed your writing. I’m confident, you’ve
a great readers’ base already!
Thanks for sharing your thoughts on xnxx.com.
Regards
Currently it looks like BlogEngine is the best blogging platform available right now.
(from what I’ve read) Is that what you’re using on your blog?
Regards! Lots of content.
Saved as a favorite, I like your website!
Every weekend i used to go to see this web site, because i wish for enjoyment, as this this web site conations in fact fastidious funny information too.
You actually suggested that really well.
Hi! I’m at work surfing around your blog from my new iphone 4!
Just wanted to say I love reading your blog and look forward
to all your posts! Carry on the excellent work!
I’m really enjoying the design and layout of your blog. It’s a very easy on the eyes which makes it much more pleasant for me to come here and visit more often. Did you hire out a designer
to create your theme? Exceptional work!
Hey! This is my 1st comment here so I just wanted to give a quick
shout out and say I truly enjoy reading through your posts.
Can you recommend any other blogs/websites/forums that go over the same subjects?
Thank you so much!
Hey very interesting blog!
You revealed this exceptionally well!
BAPAKKAU MAIN AIR DIPERKOSA ANJING
Aw, this was an exceptionally nice post. Taking a few minutes and actual effort to make a very
good article… but what can I say… I procrastinate a whole lot and don’t manage to get nearly anything done.
Hey there! This post could not be written any better! Reading this post reminds me of my good old room mate!
He always kept chatting about this. I will forward this article
to him. Fairly certain he will have a good read. Many thanks
for sharing!
I don’t even know the way I finished up here, however I assumed this submit was great.
I don’t recognise who you might be however definitely
you’re going to a well-known blogger if you happen to are
not already. Cheers!
This website was… how do I say it? Relevant!!
Finally I have found something that helped me. Thanks!
I don’t even know how I ended up here, but I thought this post was good.
I don’t know who you are but definitely you are going to
a famous blogger if you are not already 😉 Cheers!
excellent issues altogether, you just won a brand new reader.
What might you suggest about your post that you
made some days in the past? Any sure?
https://honda-fit.ru/forums/index.php?autocom=gallery&req=si&img=7130
You’ve made some really good points there. I looked on the net for more information about the issue
and found most individuals will go along with your views on this website.
My brother suggested I may like this blog. He was totally right.
This post actually made my day. You can not believe simply how much
time I had spent for this information! Thanks!
GAY KONTOL
There is definately a lot to find out about this issue. I like all
of the points you have made.
Appreciating the commitment you put into your blog and in depth information you provide.
It’s nice to come across a blog every once in a while that isn’t the
same old rehashed information. Excellent read! I’ve saved your site and I’m including your
RSS feeds to my Google account.
Thanks, I enjoy it.
id=”toc-0″>Топ казино Mostbet игры
Еще одним привлекательным предложением от Мостбет является бонус
на депозит. При пополнении игрового счета определенной суммой, игроки получают дополнительные бонусные средства, которые
можно использовать для ставок.
Например, при депозите в размере 1000 рублей, игрок может получить 500 рублей в качестве
бонуса. Такой бонус позволяет увеличить свой банкролл и иметь больше возможностей для
успешных ставок.
Принимает ли Mostbet биткоины?
Смело играйте и наслаждайтесь азартом, зная, что ваши средства всегда под контролем, а служба поддержки готова помочь в любой ситуации.
Кроме того, приложение предоставляет доступ к широкому выбору спортивных событий и различным видам ставок,
чтобы каждый пользователь мог найти то, что ему интересно.
Пользователи могут зайти на сайт Мостбет вход, используя
свои учетные данные, и сразу начать делать ставки или играть в казино.
Благодаря интуитивно понятному интерфейсу и удобной навигации, вход в Мостбет становится быстрым и безопасным для каждого игрока.
Вход на сайт БК Мостбет для игроков из России возможен через актуальное
зеркало.
Процесс скачивания и установки приложения прост и
понятен даже для новичков. Most Bet — не просто место для ставок, это платформа, где каждый
игрок чувствует заботу,
получает максимум от игры
и, конечно, реальный шанс на победу.
Вот как можно быстро присоединиться к миллионам участников этой
платформы и начать выигрывать.
После этих действий вы войдете в систему и будете перенаправлены на главную страницу, где представлены все предстоящие матчи и игры.
Игра в покер может быть сложной, но
мы поможем вам разобраться в основах и
научим эффективным тактикам, которые позволят вам стать успешным игроком.
В Mostbet Казино вы сможете ощутить всю магию
рулетки и испытать удачу на собственной шкуре.
Мостбет предоставляют отличную спортивную книгу, а также популярные игры онлайн казино.
И там, и там отличные рынки
ставок и высокие коэффициенты,
гарантирующие крупные выигрыши.
Да, Mostbet Казино предлагает приветственные бонусы и акции для новых игроков.
Да, Mostbet Казино предоставляет мобильное приложение и оптимизированный мобильный сайт, что позволяет играть на смартфонах
и планшетах. Мостбет предоставляет широкий спектр возможностей для
ставок на спорт, а также казино и другие азартные игры.
Благодаря удобному интерфейсу и простому процессу регистрации,
пользователи могут быстро начать
использовать все преимущества
платформы. Если вы хотите получить оперативную помощь,
рекомендуется воспользоваться онлайн-чатом на нашем официальном сайте.
В чате вам ответят квалифицированные специалисты, готовые помочь вам решить любые вопросы,
связанные с использованием Мостбет.
В этом разделе вы найдете информацию о входе в Мостбет, основных функциях платформы, правилах и
условиях использования, а также множество других полезных сведений.
Как использовать акции и бонусы Mostbet
Кроме того, Мостбет регулярно проводит различные акции и специальные предложения для
своих игроков. Например, это могут
быть акции с повышенными коэффициентами на
определенные события или бонусы за
участие в определенных акциях.
Такие акции позволяют игрокам получить дополнительные выигрыши и
увеличить свои шансы на успех. Чтобы быть в курсе всех акций и предложений, игрокам рекомендуется посещать официальный сайт
Мостбет и следить за новостями на сайте.
Официальный сайт Мостбет вход является платформой, где каждый желающий
может зарегистрироваться и начать свою игровую активность.
Мостбет завоевал популярность благодаря своей надежности и высокому уровню сервиса.
На сайте Мостбет вход предлагает широкий выбор спортивных событий для
ставок, начиная от футбола и баскетбола, и заканчивая теннисом и хоккеем.
Чтобы войти на сайт Мостбет, достаточно перейти по ссылке на официальный сайт и ввести свои учетные данные.
Личный кабинет Мостбет предоставляет пользователям удобный
доступ ко всем функциям и возможностям букмекерской конторы.
Чтобы воспользоваться всеми преимуществами Мостбет, необходимо пройти процедуру авторизации на
официальном сайте.
Лайв-ставки – еще одна возможность, предоставляемая на официальном сайте Мостбет.
Лайв-ставки позволяют делать ставки на спортивные
события, которые уже начались.
Вы можете следить за ходом матча и делать ставки в режиме реального времени.
Официальный сайт Мостбет предлагает широкий выбор событий для лайв-ставок, включая футбол,
теннис, хоккей и другие популярные
виды спорта. Таким образом, Мостбет – это надежная компания с
отличной репутацией, предлагающая своим пользователям широкий выбор
спортивных событий и азартных игр.
Вход на официальный сайт Мостбет позволяет каждому желающему насладиться игрой и возможностью выиграть реальные деньги.
Мостбет – популярная букмекерская контора,
предлагающая широкий выбор спортивных ставок,
а также возможность игры в
казино и слоты. Официальный сайт Мостбет предоставляет пользователям удобный и надежный доступ ко
всем разделам и функциям.
Сайт Мостбет предоставляет возможность пользователям
делать ставки на различные спортивные события, а также играть
в популярные казино и слоты.
Является ли Mostbet Казино надежным местом для игры?
После этого, игрок получает доступ к широкому выбору
спортивных событий и может начать делать ставки.
Официальный сайт Мостбет предоставляет удобный интерфейс, который позволяет быстро и легко найти нужные
события и сделать ставку. Здесь вы
сможете насладиться азартными играми, такими как рулетка,
блэкджек, покер и многие другие.
Казино Мостбет предлагает широкий
выбор игровых автоматов, включая классические слоты, видео-слоты, а также прогрессивные джекпоты.
Mostbet Casino предоставляет вам широкий выбор топовых казино игр, которые приносят невероятное удовольствие
и шансы на выигрыш.
Чтобы получить этот бонус, нужно зарегистрироваться на сайте Мостбет и
внести первый депозит. Одной из главных функций приложения является возможность совершать ставки
в режиме реального времени.
Пользователи могут следить за спортивными событиями и делать ставки
на них прямо со своего мобильного устройства.
Внести депозит на сайте Мостбет можно с помощью банковских карт,
популярных платежных сервисов, криптовалютных и
электронных кошельков, мобильных переводов.
Мостбет придерживается правил и рекомендаций Международной комиссии по азартным играм
Кюрасао. Она следит за тем, чтобы компании соблюдали региональные юрисдикции и относились к игрокам на основе принципов
честной игры. После этих действий вы автоматически войдете в свой личный кабинет, что
позволит вам использовать бонусы и делать ставки.
Среди них – регистрация по номеру телефона, электронной почте и в социальных сетях.
Играя в Mostbet Казино на мобильных устройствах, вы получаете максимальную свободу и удобство.
Author wadmiinePosted on 26 November 2024Categories Blog
KONTOL BAPAKKAU PECAH
Hi there, this weekend is pleasant in favor of me, for the reason that this time
i am reading this enormous informative paragraph here at my house.
Sweet blog! I found it while surfing around
on Yahoo News. Do you have any suggestions
on how to get listed in Yahoo News? I’ve been trying for a while but I never
seem to get there! Cheers
TUKANG SOBUR, SEO NAGATOP TUKANG SOBUR
Aw, this was an exceptionally nice post. Taking
the time and actual effort to create a very good article… but what can I say… I procrastinate a whole lot and don’t seem to
get anything done.
Howdy! This blog post couldn’t be written any better!
Looking through this post reminds me of my previous roommate!
He always kept talking about this. I am going to send this article to
him. Pretty sure he will have a very good read.
Thanks for sharing!
Hello, i believe that i noticed you visited my blog thus i came to go back the favor?.I am attempting to find issues to improve my site!I suppose its ok to use
a few of your ideas!!
I’ve been surfing online more than three hours as of late, but
I by no means discovered any attention-grabbing article like
yours. It’s lovely value sufficient for me. In my view, if all web
owners and bloggers made just right content material as you probably did, the
web shall be a lot more helpful than ever before.
Great beat ! I wish to apprentice whilst you amend your website,
how can i subscribe for a blog website? The account helped
me a applicable deal. I were tiny bit familiar of this your broadcast provided
brilliant transparent idea
It’s going to be end of mine day, but before end I am
reading this great post to increase my experience.
The other day, while I was at work, my cousin stole my
iPad and tested to see if it can survive a 30 foot drop,
just so she can be a youtube sensation. My apple ipad is now broken and she has
83 views. I know this is completely off topic but I had to share
it with someone!
Thanks for any other informative website.
The place else may just I get that type of info written in such
an ideal approach? I’ve a mission that I’m just now operating on, and I’ve
been on the glance out for such info.
Magnificent beat ! I would like to apprentice while you amend
your site, how can i subscribe for a blog site?
The account aided me a acceptable deal. I have been a
little bit acquainted of this your broadcast provided vibrant clear concept
Your mode of describing the whole thing in this article is really fastidious, every one can simply
be aware of it, Thanks a lot.
This is really interesting, You are a very skilled blogger.
I have joined your feed and look forward to seeking more of your great post.
Also, I’ve shared your web site in my social networks!
Hello! I just wanted to ask if you ever have any problems with
hackers? My last blog (wordpress) was hacked and I ended up losing several weeks of hard work due to no backup.
Do you have any methods to protect against hackers?
What’s up i am kavin, its my first occasion to commenting anyplace, when i read this piece of writing i thought i could also create comment due to this
brilliant piece of writing.
If some one desires to be updated with most up-to-date technologies after that he must be pay a visit this website and be
up to date every day.
Buy WhatsApp hash channels
WhatsApp hash channels for sale
Purchase WhatsApp hash channels
WhatsApp marketing hash channels
WhatsApp hash channel provider
Affordable WhatsApp hash channels
WhatsApp hash channels bulk purchase
WhatsApp hash channels online store
Best WhatsApp hash channels
WhatsApp hash channels for businesses
WhatsApp hash channels for marketing
WhatsApp hash channels supplier
WhatsApp hash channels pricing
WhatsApp hash channels reseller
WhatsApp hash channels wholesale
WhatsApp hash channels service
WhatsApp hash channels shop
WhatsApp hash channels deals
WhatsApp hash channels packages
WhatsApp hash channels solutions
id=”firstHeading” class=”firstHeading mw-first-heading”>Search results
Help
English
Tools
Tools
move to sidebar hide
Actions
General
Thanks for the auspicious writeup. It actually used to
be a entertainment account it. Glance advanced to more delivered agreeable from you!
By the way, how can we communicate?
Here is my website crownsoft filter
Very nice post. I just stumbled upon your weblog and wanted to say that I have
really enjoyed surfing around your blog posts.
After all I will be subscribing to your rss feed and I hope you write
again soon!
Amazing a good deal of wonderful data.
Appreciating the time and effort you put into your
website and detailed information you provide. It’s
nice to come across a blog every once in a while that isn’t the same outdated rehashed material.
Fantastic read! I’ve saved your site and I’m including your RSS feeds to my Google account.
What a material of un-ambiguity and preserveness
of valuable know-how concerning unpredicted emotions.
Everyone loves it when folks come together and share thoughts.
Great site, keep it up!
continuously i used to read smaller posts that as well clear their motive,
and that is also happening with this piece of writing which
I am reading at this time.
It’s nearly impossible to find experienced people about this topic, but you seem like you know what you’re
talking about! Thanks
Hi, I think your blog might be having browser compatibility issues.
When I look at your blog site in Safari, it looks fine but when opening in Internet Explorer, it has some
overlapping. I just wanted to give you a quick heads up!
Other then that, awesome blog!
This article is in fact a pleasant one it assists new the web viewers, who are wishing in favor of blogging.
Remarkable issues here. I’m very glad to look your article.
Thanks a lot and I’m looking forward to contact you.
Will you please drop me a mail?
Good article. I will be going through many of these issues as
well..
If you desire to increase your familiarity just keep visiting this site and be updated with the most recent information posted here.
Please let me know if you’re looking for a writer for your blog.
You have some really good posts and I believe I would be a good
asset. If you ever want to take some of the load
off, I’d love to write some material for your blog in exchange
for a link back to mine. Please shoot me an e-mail if interested.
Thanks!
Hi! Would you mind if I share your blog with my myspace group?
There’s a lot of people that I think would really appreciate your
content. Please let me know. Many thanks
سازه ال اس اف
Superb post however I was wondering if you could write a litte more on this
topic? I’d be very grateful if you could elaborate a little bit further.
Thank you!
I am really enjoying the theme/design of your blog.
Do you ever run into any internet browser compatibility problems?
A few of my blog audience have complained about my site not operating correctly in Explorer but looks great in Firefox.
Do you have any solutions to help fix this issue?
I always emailed this weblog post page to all my associates, for the reason that if
like to read it then my links will too.
I like what you guys are up too. This kind of clever work and exposure!
Keep up the very good works guys I’ve added you guys to blogroll.
My partner and I stumbled over here by a different web page and thought I
should check things out. I like what I see so i am just following you.
Look forward to looking over your web page again.
That is a good tip particularly to those new to the blogosphere.
Simple but very precise info… Thanks for sharing
this one. A must read article!
Discover thousands of the latest and popular films from various genres.
Enjoy high-quality movie streaming experience without any subscription needed.
Good day! This post couldn’t be written any better! Reading this post
reminds me of my good old room mate! He always kept chatting about this.
I will forward this article to him. Pretty sure he will have a good read.
Many thanks for sharing!
What’s up friends, how is everything, and what you
would like to say about this piece of writing,
in my view its genuinely remarkable in support of me.
Very nice article. I absolutely love this site.
Keep it up!
If some one desires to be updated with newest technologies afterward
he must be go to see this website and be up to date all the time.
I blog frequently and I really thank you for your information. Your article has really peaked my interest. I will bookmark your website and keep checking for new details about once a week. I subscribed to your RSS feed as well.
Hi to every body, it’s my first visit of this website; this web site carries amazing and actually excellent information for
readers.
I really love your site.. Great colors & theme. Did you make this website yourself?
Please reply back as I’m trying to create my own website and would love to learn where
you got this from or just what the theme is
named. Appreciate it!
แนะนำระบบ ให้แต้มผ่านทาง Line นั้นคือ
ระบบ crm ราคาไม่แพง PiNME ตอบโจทร์ทุกการใช้งาน,การแข่งขัน ระบบ CRM ในปัจุบันสูงมาก และราคาแพง ขอแทนะนำ ระบบ crm PiNME ตอบโจทร์ทุกการใช้งาน
Terrific work! That is the type of information that should be shared around the web.
Shame on Google for now not positioning this post higher!
Come on over and consult with my website . Thank you =)
Wow, awesome blog layout! How long have you been blogging for?
you made blogging look easy. The overall look
of your web site is wonderful, as well as the content!
I read this paragraph fully regarding the comparison of hottest and earlier technologies,
it’s amazing article.
Hi, this weekend is pleasant in support of me, since this moment i am reading this enormous educational article here at
my home.
I have read several just right stuff here. Definitely price bookmarking for revisiting.
I wonder how so much effort you place to create the sort of great informative site.
This website was… how do I say it? Relevant!! Finally I have found something which helped me.
Thanks a lot!
It’s actually a nice and helpful piece of information. I’m happy that you simply shared this useful info with us.
Please keep us informed like this. Thanks for sharing.
This excellent website really has all of the info I wanted concerning this subject
and didn’t know who to ask.
What’s up mates, pleasant piece of writing and good arguments commented here, I am genuinely enjoying by these.
Hello there I am so thrilled I found your blog page,
I really found you by mistake, while I was looking
on Askjeeve for something else, Anyhow I am here now and
would just like to say kudos for a tremendous post and
a all round thrilling blog (I also love the theme/design), I don’t have time to look over it all at the moment but I have bookmarked it and also included
your RSS feeds, so when I have time I will be back to read a lot more, Please
do keep up the fantastic job.
each time i used to read smaller content that also clear their motive, and that is also happening with this
article which I am reading here.
Excellent goods from you, man. I have consider your stuff prior
to and you are simply too excellent. I really like what
you have bought right here, certainly like what you
are stating and the best way during which you say it.
You are making it enjoyable and you still care for to keep it sensible.
I cant wait to read much more from you. This is really a tremendous
web site.
It’s awesome for me to have a web site, which is valuable
in favor of my experience. thanks admin
I’m not that much of a online reader to be honest but your blogs really nice, keep it up!
I’ll go ahead and bookmark your website to come back later on. All the best
It is appropriate time to make some plans for the future and it’s time to
be happy. I have read this post and if I could I desire to suggest
you few interesting things or suggestions.
Perhaps you can write next articles referring to this article.
I desire to read more things about it!
Thanks, I value it.
I’m truly enjoying the design and layout of
your site. It’s a very easy on the eyes which makes it much more
enjoyable for me to come here and visit more often. Did you hire out a developer to create your theme?
Great work!
I read this paragraph completely regarding the comparison of most up-to-date and preceding technologies,
it’s remarkable article.
Sweet blog! I found it while searching on Yahoo News.
Do you have any tips on how to get listed in Yahoo News?
I’ve been trying for a while but I never seem to get there!
Many thanks
I always spent my half an hour to read this web site’s posts every day along with a
cup of coffee.
Greate pieces. Keep writing such kind of information on your site.
Im really impressed by it.
Hello there, You have done a fantastic job. I will definitely digg it and in my opinion recommend to my friends.
I’m sure they’ll be benefited from this website.
A motivating discussion is definitely worth comment.
There’s no doubt that that you need to write more about this subject, it might not be a taboo matter but typically folks don’t talk about these topics.
To the next! Cheers!!
Very descriptive post, I loved that a lot. Will there be a part 2?
You’ve made some decent points there. I checked on the net for more info about the issue and found most people will go along with your views on this website.
my blog post; tonic greens
It’s really a nice and useful piece of information. I am glad that
you just shared this useful information with us. Please keep us up to date like this.
Thank you for sharing.
I enjoy what you guys tend to be up too. This type of
clever work and reporting! Keep up the good works guys I’ve added you guys
to my personal blogroll.
I’ve been surfing online greater than three
hours today, but I by no means discovered any interesting article like
yours. It’s lovely price sufficient for me. In my opinion, if all site owners and bloggers made just
right content material as you did, the net will be much more useful than ever before.
Here is my blog post :: you can look here
Music creators thrived within SoundCloud’s ecosystem.
My SoundCloud followers are proper music enthusiasts.
Hi colleagues, its enormous paragraph about tutoringand fully defined, keep it up
all the time.
Every weekend i used to pay a quick visit this website,
for the reason that i want enjoyment, as this this web site conations in fact nice
funny stuff too.
I have been surfing online more than 3 hours today, yet I never found any interesting article like yours.
It is pretty worth enough for me. Personally, if all web owners and bloggers made good content as you
did, the web will be much more useful than ever before.
Hello, i believe that i saw you visited my site so i came to return the favor?.I
am trying to in finding issues to enhance my website!I suppose its adequate to use some of
your ideas!!
I have been surfing online more than 4 hours today,
yet I never found any interesting article like yours.
It is pretty worth enough for me. Personally, if all webmasters and bloggers made
good content as you did, the internet will be a lot more useful than ever
before.
Asking questions are truly nice thing if you are not understanding anything
entirely, except this paragraph presents pleasant
understanding even.
I couldn’t refrain from commenting. Well written!
Regards! I like it!
Greetings! I’ve been reading your website for some time now and finally got the courage to go ahead and
give you a shout out from Porter Texas! Just wanted to say keep
up the great job!
After looking into a handful of the blog posts on your web site, I truly like your way of blogging.
I added it to my bookmark website list and will be checking back in the near future.
Take a look at my web site as well and let
me know your opinion.
If you are going for best contents like I do, only visit this website all the time for the reason that it presents
quality contents, thanks
Hello, i think that i saw you visited my website so i came to
“return the favor”.I’m attempting to find things to enhance my web site!I
suppose its ok to use some of your ideas!!
There’s certainly a lot to find out about this issue.
I really like all the points you’ve made.
you’re in reality a excellent webmaster. The web site loading
velocity is amazing. It sort of feels that you’re doing any unique
trick. Furthermore, The contents are masterwork. you have
done a wonderful process on this subject!
You can definitely see your skills within the article you
write. The arena hopes for even more passionate writers such as
you who aren’t afraid to say how they believe. All the time go after your heart.
I am so pleased that this collection is over and that I will never pick up any of these books from this sequence again for so long as I stay. I am the definition of performed. Also, spoilers can be abound and aplenty throughout this whole review, and this is going to a a largely Supernatural gif-crammed extravaganza, because A). That is how angels/demons/and so forth. must be done and B). I can. So if you don’t like spoilers or Supernatural, leave now, as a result of shit’s about to get ugly up in right here
Way cool! Some very valid points! I appreciate you writing this article
and also the rest of the website is also very
good.
Incredible a good deal of useful knowledge!
You’ve made some good points there. I checked on the
internet to learn more about the issue and found most individuals will go along with your views on this site.
What’s up to all, how is everything, I think every one is getting more from this web
page, and your views are nice in favor of new users.
I wanted to thank you for this great read!! I certainly loved every bit of
it. I have got you bookmarked to look at new things you post…
Good post. I learn something new and challenging on blogs
I stumbleupon every day. It will always be interesting to read articles from other writers and use something from other sites.
Anda butuh printer baru ? Tidak perlu beli yang baru, Sewa
Printer saja. Kami hadir untuk anda dengan segala jenis Printer MFP.
Dan kami pun menyediakan Jual Printer Laserjet serta Printer Rental
Se – Jakarta
789WIN – thương hiệu nhà cái trực tuyến uy tín nhất khu vực Châu Á – Thái Bình Dương, nhà cái 789 Win nơi hội
tụ đa dạng các sản phẩm giải trí như
game bài, nổ hũ, cá cược thể thao, casino live, đá gà và xổ
số..
I am genuinely happy to read this blog posts which includes tons of valuable facts,
thanks for providing these information.
It’s really very difficult in this active life to listen news on Television, thus
I only use internet for that purpose, and obtain the
newest news.
Hey I know this is off topic but I was wondering if you knew of any widgets I could add
to my blog that automatically tweet my newest twitter updates.
I’ve been looking for a plug-in like this for quite some time and was hoping maybe you
would have some experience with something like this. Please let me know if you
run into anything. I truly enjoy reading your blog and I look forward to your new updates.
Hey there! Someone in my Facebook group shared this
site with us so I came to give it a look. I’m definitely loving the information. I’m bookmarking and will be
tweeting this to my followers! Excellent blog and great style and design.
I really like your blog.. very nice colors & theme.
Did you design this website yourself or did you hire someone to
do it for you? Plz reply as I’m looking to design my own blog and would like
to find out where u got this from. appreciate it
Heya i am for the first time here. I found this board and I to
find It truly helpful & it helped me out a lot.
I’m hoping to provide something back and help
others such as you helped me.
Heya are using WordPress for your site platform?
I’m new to the blog world but I’m trying to get started
and create my own. Do you require any coding knowledge to make your own blog?
Any help would be really appreciated!
Thank you, I have recently been searching for information about this subject for a long time and yours is the greatest I have found out so far.
However, what concerning the bottom line? Are you certain in regards to the supply?
I love it whenever people get together and share thoughts.
Great website, keep it up!
Thanks for every other magnificent post.
The place else may just anyone get that kind of info
in such an ideal means of writing? I’ve a presentation subsequent week, and I am at the look for such info.
World events tonight reveals unfolding crises in key industries.
Government affairs indicate fragile negotiations between major powers over strategic
territories. The Environmental collapse manifests through chained catastrophes
across vulnerable regions, with scientists warning of point-of-no-return scenarios.
Digital disruptions showcase dual-use applications of quantum computing that alarm watchdogs.
Market pulses reveal mixed indicators as bullish sectors coexist with recession warnings.
Nice replies in return of this matter with real arguments and explaining the whole thing concerning that.
Heey very nice blog!! Man .. Excellent .. Superb ..
I will bookmark your web site and take the feeds also?
I’m happy tto seek out a lot of helpful incormation here
within the put up, we’d like work out extra strategies on this
regard, thank you for sharing. . . .. .
Thanks in favor of sharing such a fastidious thinking, post is
nice, thats why i have read it completely
I like it whenever people come together and share opinions.
Great site, continue the good work!
Way cool! Some extremely valid points! I appreciate you writing this write-up and the rest of
the site is extremely good.
Your way of explaining all in this article is truly nice,
all be capable of without difficulty know it, Thanks a lot.
Ahaa, its fastidious dialogue about this article at this place at this
blog, I have read all that, so at this time me also
commenting here.
I think that everything posted made a bunch of sense.
But, think about this, what if you composed a catchier title?
I mean, I don’t want to tell you how to run your website, however
what if you added a title that makes people want more? I mean SMI diamond grinding wheels is a little
vanilla. You could peek at Yahoo’s home page and watch how they create
news headlines to grab people to click. You might add a related video or a related picture or two to grab readers excited
about what you’ve written. In my opinion, it might
make your website a little bit more interesting.
Good info. Lucky me I recently found your site by accident (stumbleupon).
I have book marked it for later!
It’s going to be ending of mine day, but before ending
I am reading this impressive piece of writing to increase my experience.
Что именно отличает дисплеи
iPhone 15 и iPhone 15 Plus от их предшественников?
| В чём особенности экранов iPhone 15 и
iPhone 15 Plus по сравнению с предыдущими моделями?
| Чем iPhone 15 и iPhone 15 Plus отличаются в плане дисплея
от ранних версий ?
Во-первых, увеличенная пиковая яркость до целых 2000 нит, что облегчает
эксплуатацию смартфона при днём на улице.
По мнению Дэна, главный вопрос , насколько долго устройство сможет удерживать максимальной яркости, прежде чем произойдёт её снижение .
Подобное наблюдалось ранее,
например, с iPhone 13 Pro . https://macuser.ua/search?word=11+%D0%B0%D0%B9%D1%84%D0%BE%D0%BD+%D0%BF%D1%80%D0%BE+%D1%86%D0%B5%D0%BD%D0%B0+%D0%B2+%D0%BC%D0%BE%D1%81%D0%BA%D0%B2%D0%B5
I am sure this piece of writing has touched all the internet
people, its really really pleasant piece of writing on building up new blog.
Greetings from Idaho! I’m bored to tears at work so I decided to check out your website on my iphone during lunch break.
I enjoy the info you present here and can’t wait to
take a look when I get home. I’m amazed at how fast your blog loaded
on my cell phone .. I’m not even using WIFI, just 3G .. Anyhow, very good site!
Good day! This is kind of off topic but I need some guidance from an established blog.
Is it very difficult to set up your own blog? I’m not very techincal but I can figure things out pretty fast.
I’m thinking about setting up my own but I’m not
sure where to begin. Do you have any tips or suggestions?
Thank you
Hi, I do think this is a great web site. I stumbledupon it 😉 I will revisit once again since i have bookmarked it.
Money and freedom is the best way to change, may you be rich and continue to help other people.
It’s a shame you don’t have a donate button! I’d
certainly donate to this fantastic blog! I guess for now i’ll settle for book-marking and adding your RSS feed to my Google account.
I look forward to brand new updates and will share this blog with my
Facebook group. Talk soon!
Today, while I was at work, my sister stole my apple ipad and tested to see if it can survive a 30 foot drop, just so she
can be a youtube sensation. My apple ipad is now destroyed and
she has 83 views. I know this is entirely off topic
but I had to share it with someone!
Appreciate the recommendation. Let me try it out.
E2bet là nhà cái uy tín hàng đầu Châu Á với nhiều sản phẩm hấp dẫn như: Cá cược thể thao, đá
gà, casino,… Bạn có thể đăng ký tài khoản dễ dàng và nhanh chóng,
Ce type de bonus est idéal pour les nouveaux joueurs qui veulent tester la plateforme avant de s’engager à déposer de l’argent réel.
Hi there would you mind sharing which blog platform you’re using?
I’m planning to start my own blog in the near future but I’m having a difficult time choosing between BlogEngine/Wordpress/B2evolution and Drupal.
The reason I ask is because your design seems different then most blogs
and I’m looking for something unique.
P.S My apologies for getting off-topic but I had to ask!
Добро пожаловать на наш портал!
У нас вы найдете огромный выбор финансовых услуг, начиная от
банковских продуктов и заканчивая инвестициями.
Наши консультанты помогут вам выбрать оптимальное решение для достижения финансовой стабильности.
Банки с быстрым открытием расчетного счета в Владикавказе
I am not sure where you are getting your info, but
great topic. I needs to spend some time learning much more or
understanding more. Thanks for wonderful information I was
looking for this info for my mission. https://baotayninh.vn/ tin tuc tay ninh
Hello there, just became alert to your blog through Google, and found that it’s truly informative.
I’m going to watch out for brussels. I will appreciate if you
continue this in future. Many people will be benefited from your writing.
Cheers!
Thanks for finally talking about > SMI diamond grinding
wheels < Loved it!
I do not even know how I ended up here, but
I thought this post was good. I don’t know who you are but
definitely you are going to a famous blogger if you aren’t already 😉 Cheers!
Greetings from Colorado! I’m bored to tears at work so I decided to check out your blog on my iphone during lunch break.
I enjoy the knowledge you present here and can’t wait to take a look when I get home.
I’m amazed at how quick your blog loaded on my phone ..
I’m not even using WIFI, just 3G .. Anyways, awesome blog!
My family members every time say that I am killing my time here at net, however I know I am getting experience every
day by reading such nice posts.
I got this website from my pal who informed me about this web site and
at the moment this time I am browsing this
web page and reading very informative articles here.
Hello there! Would you mind if I share your blog with my myspace
group? There’s a lot of folks that I think would really appreciate your content.
Please let me know. Cheers
It’s genuinely very complex in this full of activity
life to listen news on Television, therefore I
just use internet for that reason, and take the most recent news.
my web page :: MACAU SLOT88
With havin so much content and articles do you ever run into any problems of plagorism or copyright violation? My site has
a lot of exclusive content I’ve either authored myself or outsourced but it seems a lot
of it is popping it up all over the internet without my permission. Do you
know any ways to help prevent content from being stolen? I’d truly appreciate it.
It’s not my first time to visit this web page, i am browsing this web site dailly and obtain pleasant facts from here every day.
What’s up all, here every person is sharing these familiarity, thus it’s pleasant to read
this web site, and I used to pay a visit this web site everyday.
This is a great tip particularly to those new to the blogosphere.
Simple but very precise info… Many thanks for sharing this one.
A must read article!
Howdy are using WordPress for your blog platform?
I’m new to the blog world but I’m trying to get started and set up my own. Do you need any html coding knowledge
to make your own blog? Any help would be greatly appreciated!
Wow, marvelous weblog layout! How long have you ever been running a blog
for? you make running a blog glance easy. The full glance of your web site is great, let alone the content material!
A person essentially help to make critically articles I might state.
That is the very first time I frequented your web page and thus far?
I amazed with the analysis you made to make this actual
submit amazing. Excellent process!
Quality posts is the important to attract the users to pay a visit
the web page, that’s what this web site is providing.
I am actually happy to glance at this website posts which includes lots of helpful data, thanks for
providing such statistics.
That is really interesting, You are a very professional blogger.
I have joined your rss feed and sit up for searching
for extra of your great post. Additionally, I’ve shared
your web site in my social networks
When someone writes an post he/she keeps the thought of a
user in his/her brain that how a user can understand it.
Therefore that’s why this article is great. Thanks!
I just couldn’t depart your website prior to suggesting that I actually loved the standard information an individual provide in your guests?
Is going to be again often in order to investigate cross-check new posts
Thank you for the auspicious writeup. It in fact was a amusement account it.
Look advanced to far added agreeable from you! By the way,
how could we communicate?
Ӏ’m not sure where yߋս’re getting your info, Ьut great topіc.
Ι needs to spend some time leагning more
or understanding more. Thаnks for great informatіon Ι
was looking for tһis info for my mission.
I am really glad to glance at this blog posts which contains tons of useful data, thanks for providing these kinds of information.
Hey there just wanted to give you a quick heads up.
The text in your post seem to be running off the screen in Chrome.
I’m not sure if this is a formatting issue or something to do with
browser compatibility but I figured I’d post to let you know.
The layout look great though! Hope you get the problem solved
soon. Kudos
Awesome https://rb.gy/4gq2o4
I do not even know how I ended up here, but I thought
this post was great. I do not know who you are but certainly
you are going to a famous blogger if you are not already 😉 Cheers!
buy viagra online
Hello! This post could not be written any better! Reading through this post reminds me of my old room mate!
He always kept talking about this. I will forward this page to him.
Fairly certain he will have a good read. Many thanks
for sharing!
Breaking news in global politics today as leaders meet to address critical challenges.
Election news dominate headlines with key decisions
expected in Parliament. Meanwhile, AI developments continue reshaping industries as cutting-edge devices debut at tech expos.
The climate crisis takes center stage with alarming new data showing
record temperatures across continents. Financial systems react
to economic indicators as traders weigh
inflation data. In medical circles, experts discuss emerging viruses while celebrity media focuses on award shows.
Sports updates bring exciting performances from international competitions.
Science breakthroughs reveal groundbreaking findings about ocean depths, while crime reports show
concerning trends in rural communities. School policy changes spark debates among parents, and NASA updates captivate audiences with ambitious plans for lunar bases.
What i don’t realize is actually how you are now not really
a lot more well-appreciated than you may be now.
You’re very intelligent. You already know thus considerably when it comes to this subject,
produced me in my view consider it from a lot of varied angles.
Its like women and men aren’t interested unless it is one thing to do with Girl gaga!
Your own stuffs nice. Always take care of it up!
Hi there I am so glad I found your blog, I really found you by mistake, while I was researching on Bing for something else,
Anyways I am here now and would just like to say thank you for a tremendous post and a all round interesting blog (I also love
the theme/design), I don’t have time to browse it all
at the moment but I have bookmarked it and also added your RSS feeds, so when I have
time I will be back to read a lot more, Please do keep up the awesome work.
Wow! After all I got a webpage from where I be able to actually take
helpful information concerning my study and
knowledge.
I need to to thank you for this fantastic read!!
I definitely enjoyed every bit of it. I have you book marked
to check out new things you post…
Many thanks! I like it.
Thanks , I have recently been looking for info about this topic for
ages and yours is the best I have came upon till
now. However, what concerning the conclusion? Are you
sure concerning the source?
I quite like looking through a post that can make men and women think.
Also, thanks for allowing me to comment!
Feel free to surf to my web-site; Deven Sanon
Very great post. I simply stumbled upon your weblog and wished to say that
I’ve truly enjoyed browsing your blog posts. In any case I’ll be subscribing for your feed and I
hope you write again very soon!
Oh my goodness! Awesome article dude! Thanks, However I am encountering
issues with your RSS. I don’t understand why I cannot
join it. Is there anybody else getting identical RSS problems?
Anyone who knows the solution can you kindly respond? Thanks!!
With havin so much content and articles do you ever run into any issues of plagorism or copyright infringement?
My site has a lot of completely unique content I’ve
either authored myself or outsourced but it seems a lot of it is popping it up all over the internet without my agreement.
Do you know any solutions to help protect against content from being ripped off?
I’d definitely appreciate it.
Normally I don’t learn article on blogs, but I would like to say that this write-up very compelled me to
take a look at and do it! Your writing taste has been surprised me.
Thanks, quite nice article.
Hi, i feel that i noticed you visited my site thus i came to go back the
desire?.I am attempting to find things to improve my website!I guess its good enough to make use
of some of your ideas!!
I like the valuable information you supply for your articles.
I’ll bookmark your blog and check again here frequently.
I’m fairly sure I will learn many new stuff right right here!
Good luck for the next!
Good day! I ccould have sworn I’ve been to this blog before but after browsing through some oof the post I realized it’s new to me.
Nonetheless, I’m definitely delighted I found it and I’ll be book-marking and
checking back often!
We are a group of volunteers and starting a new scheme in our community.
Your website provided us with valuable information to work on. You’ve
performed an impressive task and our whole group can be thankful to you.
It’s a shame you don’t have a donate button! I’d certainly donate to this excellent blog!
I suppose for now i’ll settle for book-marking and adding
your RSS feed to my Google account. I look forward
to fresh updates and will talk about this blog with
my Facebook group. Chat soon!
I just could not go away your site prior to suggesting that I really
enjoyed the standard info a person provide in your guests?
Is gonna be back often in order to investigate cross-check new posts
Thanks for the marvelous posting! I genuinely enjoyed reading it, you could be
a great author. I will make sure to bookmark your blog and will
eventually come back at some point. I want to encourage you
continue your great writing, have a nice holiday weekend!
Today, I went to the beachfront with my kids. I found a sea shell and gave it to my 4 year old daughter and
said “You can hear the ocean if you put this to your ear.” She placed the shell to her ear
and screamed. There was a hermit crab inside and it pinched her ear.
She never wants to go back! LoL I know this is
totally off topic but I had to tell someone!
Hi there! This is my first visit to your blog! We are a team of
volunteers and starting a new project in a community in the
same niche. Your blog provided us beneficial information to work on. You have
done a wonderful job!
I am curious to find out what blog platform you have been using?
I’m having some small security issues with my latest blog
and I would like to find something more risk-free.
Do you have any suggestions?
You ought to be a part of a contest for one of the
finest websites on the net. I am going to highly recommend this web site!
You really make it seem so easy with your presentation but I find this matter to be really something
which I think I would never understand. It seems too complicated and very broad for me.
I am looking forward for your next post, I’ll try to get the
hang of it!
I’m really enjoying the design and layout of your site. It’s a very easy on the eyes which makes it much
more pleasant for me to come here and visit more often. Did you hire out a designer
to create your theme? Outstanding work!
My brother recommended I might like this blog.
He was totally right. This post truly made my day. You can not
imagine just how much time I had spent for this info! Thanks!
The best English explanation of Phim Tinh
Duc is a literal translation for the word “Gaming.” Gaming does not have to mean playing Video Games, as the word is commonly associated with playing video games in the 21st Century.
Have you ever considered about including a little bit more than just your articles?
I mean, what you say is valuable and everything. Nevertheless just imagine if you added some great photos or
video clips to give your posts more, “pop”! Your content is excellent
but with pics and clips, this blog could definitely be one of
the very best in its field. Excellent blog!
Fantastic blog you have here but I was curious about if you knew of any community forums that cover the same topics
talked about here? I’d really like to be a part of group where
I can get responses from other knowledgeable individuals that share the same interest.
If you have any recommendations, please let me know.
Thanks!
I do not know whether it’s just me or if everyone else encountering
issues with your website. It seems like some of the written text on your content
are running off the screen. Can somebody else please comment and let me know if
this is happening to them as well? This may be a issue with my internet browser because I’ve had this
happen before. Appreciate it
It’s genuinely very difficult in this busy life to listen news on Television, therefore
I only use internet for that purpose, and
get the most recent news.
This article presents clear idea for the new visitors of
blogging, that really how to do blogging.
Hey there, You’ve done an excellent job. I will certainly
digg it and personally recommend to my friends. I’m confident they’ll be benefited from this web site.
It’s difficult to find experienced people about this topic, but you
seem like you know what you’re talking about! Thanks
What’s up, this weekend is nice for me, since this point in time i am reading this enormous informative article here at my home.
It’s perfect time to make some plans for the future and it’s time to be happy.
I have read this put up and if I could I desire to recommend you
some interesting issues or tips. Perhaps you could write next
articles referring to this article. I wish to learn even more things approximately it!
Incredible points. Solid arguments. Keep up the amazing
work.
I’m gone to tell my little brother, that he should also
pay a quick visit this blog on regular basis to obtain updated from
most recent news update.
Hello, i think that i noticed you visited my website so i came
to go back the choose?.I am trying to to find issues to
enhance my website!I suppose its adequate to use a few of
your ideas!!
Thank you for the good writeup. It in fact was a amusement account it.
Look advanced to far added agreeable from you! However, how could we communicate?
whoah this blog is wonderful i really like studying your articles.
Stay up the good work! You realize, many people
are looking around for this info, you could aid them greatly.
I’m pretty pleased to discover this page. I wanted to thank you for
your time just for this wonderful read!! I definitely liked
every part of it and I have you saved as a favorite to look
at new information on your blog.
http://toyota-porte.ru/forums/index.php?autocom=gallery&req=si&img=3360
https://vitz.ru/forums/index.php?autocom=gallery&req=si&img=5030
Hey very interesting blog!
Thanks for one’s marvelous posting! I actually enjoyed reading it, you might be a great author.
I will ensure that I bookmark your blog and will
come back in the foreseeable future. I want to encourage yourself
to continue your great writing, have a nice day!
Thank you for sharing such insightful content about
Tantra Yoga! It’s inspiring to see how this ancient practice can help us connect with our inner energy and bring balance to our lives.
The emphasis on mindfulness, self-awareness, and spiritual growth
resonates deeply. I especially appreciate how you explained the connection between Tantra and holistic well-being.
Looking forward to exploring more of your posts and learning new techniques
to incorporate into my daily practice. Keep up the amazing work!
Thanks in support of sharing such a nice thinking, paragraph is nice,
thats why i have read it completely
This is my first time pay a quick visit at here
and i am really pleassant to read everthing
at one place.
Hi there I am so happy I found your web site, I really found you by mistake, while I was researching on Bing for something else, Anyhow I am here now and would just like to say many thanks for a fantastic post
and a all round exciting blog (I also love the theme/design),
I don’t have time to go through it all at the moment but
I have book-marked it and also added your RSS feeds, so when I have time I will be back to read much more, Please do
keep up the awesome work.
Greetings from Florida! I’m bored to tears at work so I decided
to check out your website on my iphone during lunch break.
I enjoy the information you provide here and can’t wait to take a look when I get home.
I’m shocked at how fast your blog loaded on my mobile ..
I’m not even using WIFI, just 3G .. Anyways, great site!
I’m really enjoying the design and layout of your site.
It’s a very easy on the eyes which makes it much more pleasant for me to come here
and visit more often. Did you hire out a designer to create your theme?
Outstanding work!
Howdy! This post couldn’t be written any better! Reading through this post reminds me of my
good old room mate! He always kept talking about this.
I will forward this post to him. Fairly certain he will have a good read.
Many thanks for sharing!
Cool blog! Is your theme custom made or did you download it from somewhere?
A design like yours with a few simple adjustements would really make my
blog stand out. Please let me know where you got your theme.
Thank you
Everyone loves what you guys are usually up too. Such clever work and coverage!
Keep up the very good works guys I’ve incorporated you guys to blogroll.
Very good https://is.gd/N1ikS2
This design is steller! You most certainly know how to
keep a reader entertained. Between your wit and your videos, I was almost moved
to start my own blog (well, almost…HaHa!) Excellent job.
I really enjoyed what you had to say, and more than that, how
you presented it. Too cool!
Hi there, just wanted to tell you, I loved this article.
It was funny. Keep on posting!
Have you ever thought about adding a little bit more than just your articles?
I mean, what you say is important and everything.
Nevertheless imagine if you added some great pictures or video clips to give your posts more, “pop”!
Your content is excellent but with images and video clips,
this site could undeniably be one of the greatest in its field.
Very good blog!
Normally I do not read article on blogs, but I wish to
say that this write-up very compelled me to check out and do it!
Your writing taste has been amazed me. Thank you,
very nice post.
It’s enormous that you are getting thoughts from this piece of writing as well as from our argument made
at this time.
Hurrah! At last I got a weblog from where I be capable of
truly take useful information regarding my study
and knowledge.
Hey! I could have sworn I’ve been to this site before but after reading through some of the post I
realized it’s new to me. Anyhow, I’m definitely happy I found it and I’ll be bookmarking and checking
back frequently!
Magnificent goods from you, man. I’ve understand your stuff previous to and you
are just extremely fantastic. I really like what you have acquired here, certainly like what you are stating and the way
in which you say it. You make it entertaining and you still take care of
to keep it smart. I cant wait to read far more from you.
This is actually a tremendous website.
Hi, all the time i used to check web site posts
here early in the break of day, since i enjoy to find out more
and more.
My brother recommended I might like this web site.
He was once entirely right. This post truly made my day.
You cann’t believe just how so much time I had spent for this info!
Thanks!
I’m not that much of a internet reader to be honest but your sites really nice, keep it up!
I’ll go ahead and bookmark your site to come back down the road.
Many thanks
Hi there all, here every person is sharing these knowledge, therefore
it’s fastidious to read this website, and I used to pay a
quick visit this webpage everyday.
Great article! That is the kind of information that are meant to be
shared around the net. Disgrace on Google for no longer positioning this put up higher!
Come on over and consult with my website . Thank you
=)
Fantastic material. Appreciate it!
It is really a great and helpful piece of info.
I’m satisfied that you simply shared this useful info with us.
Please keep us informed like this. Thank you for sharing.
Greate post. Keep posting such kind of info on your blog. Im really impressed by
your blog.
Hey there, You’ve done an incredible job.
I will certainly digg it and in my view recommend to my friends.
I’m sure they’ll be benefited from this website.
It’s going to be ending of mine day, however before end
I am reading this impressive paragraph to increase my know-how.
I do not even know how I ended up here, but I thought this post was good.
I don’t know who you are but definitely you’re going to
a famous blogger if you are not already 😉 Cheers!
Here is my web-site – more
I just like thee helpful info you suplply to your articles.
I’ll bookmark your weblog and test again here frequently.
I’m rather sure I’ll be told lots oof new stuff right here!
Good luck for the following!
It’s an amazing post for all the internet people; they
will obtain advantage from it I am sure.
A fascinating discussion is definitely worth comment.
I do believe that you ought to publish more about this topic, it may not be a taboo
matter but usually people don’t discuss such topics.
To the next! Cheers!!
We are a group of volunteers and starting a new scheme in our community.
Your site offered us with valuable information to work on. You’ve done a formidable job and
our entire community will be thankful to you.
It’s going to be ending of mine day, however before end I
am reading this great piece of writing to improve my experience.
Right now it looks like WordPress is the best blogging platform available right now.
(from what I’ve read) Is that what you are using on your blog?
It’s very simple to find out any topic on web as compared to books, as
I found this paragraph at this website.
You have made your stand pretty nicely!!
Thanks for sharing your info. I really appreciate your efforts
and I will be waiting for your next write ups thank you once again.
Excellent tips, Thank you.
I always used to read post in news papers but now as I am a user of net therefore from now I am using
net for articles or reviews, thanks to web.
Hi! I’m at work browsing your blog from my new iphone 4! Just wanted to say I
love reading your blog and look forward to all your posts!
Keep up the superb work!
Here is my blog; job advertising
Hi there are using WordPress for your site platform?
I’m new to the blog world but I’m trying to get started and set up my own. Do you need any coding expertise to
make your own blog? Any help would be really appreciated!
Tego typu podejrzana aplikacja wydaje sie byc oprogramowaniem
do pobierania filmow online, jednakze wielu uzytkownikow
zgodnie twierdzi ze program w ogole nie dziala.
I love it when folks get together and share views.
Great website, continue the good work!
Thanks in favor of sharing such a pleasant idea, post is
fastidious, thats why i have read it completely
Hey would you mind stating which blog platform you’re using?
I’m going to start my own blog in the near future but I’m having a hard time deciding between BlogEngine/Wordpress/B2evolution and Drupal.
The reason I ask is because your design and style seems different then most blogs and I’m looking for something completely
unique. P.S Sorry for getting off-topic but I had to
ask!
You’re so awesome! I do not think I have read through anything like
that before. So nice to discover somebody with unique thoughts on this subject.
Seriously.. thanks for starting this up. This web site is
one thing that is needed on the web, someone with a little originality!
взломанные игры без вирусов — это удивительная
возможность изменить игровой опыт.
Особенно если вы играете на мобильном
устройстве с Android, модификации открывают перед вами широкие горизонты.
Я лично использую взломанные игры,
чтобы достигать большего.
Моды для игр дают невероятную персонализированный подход, что делает процесс гораздо увлекательнее.
Играя с модификациями, я могу повысить уровень
сложности, что добавляет приключенческий процесс и делает игру более эксклюзивной.
Это действительно удивительно,
как такие моды могут улучшить переживания от игры,
а при этом не нарушая использовать такие взломанные версии можно
без особых проблем, если быть внимательным
и следить за обновлениями.
Это делает каждый игровой процесс более насыщенным, а возможности практически неограниченные.
Советую попробовать такие модифицированные версии для Android — это может открыть новые горизонты
Very soon this website will be famous amid all blogging and
site-building visitors, due to it’s good posts
I like what you guys tend to be up too. This kind of clever work and
reporting! Keep up the excellent works guys I’ve incorporated
you guys to blogroll.
Hi there everyone, it’s my first pay a visit at this site,
and paragraph is really fruitful designed for me, keep up posting
these content.
Howdy! I’m at work browsing your blog from my new iphone 3gs!
Just wanted to say I love reading your blog and look forward to all your posts!
Carry on the outstanding work!
Awesome https://is.gd/N1ikS2
I knoiw this if off topic but I’m looking into starting my
own weblog and was curious what all is needed to get setup?
I’m assuming having a blog liike yours would cost a preetty penny?
I’m not very webb savvy so I’m not 100% sure.
Any tips or advice would be greatly appreciated. Cheers
I all the time emailed this website post page to all my contacts, for
the reason that if like to read it then my links will too.
Remarkable! Its in fact awesome post, I have got much clear idea on the topic of from this post.
Hello my friend! I want to say that this post
is awesome, nice written and come with approximately all vital infos.
I’d like to see more posts like this .
I do not know whether it’s just me or if everybody else experiencing problems with your blog.
It appears like some of the text in your posts are running
off the screen. Can somebody else please comment and let me know if this is happening to them
as well? This could be a issue with my browser because I’ve had this happen before.
Many thanks
Great weblog here! Additionally your website so much up very fast!
What web host are you using? Can I am getting your associate hyperlink to your
host? I desire my web site loaded up as quickly as yours lol
My coder is trying to persuade me to move to .net from PHP.
I have always disliked the idea because of the expenses.
But he’s tryiong none the less. I’ve been using WordPress on various websites for about a year and am anxious about switching to another platform.
I have heard great things about blogengine.net. Is there a way I can import all
my wordpress posts into it? Any kind of help would be really appreciated!
Добро пожаловать на наш сайт!
Здесь вы найдете все, что нужно для управления вашими финансами.
У нас есть широкий выбор финансовых
продуктов, которые помогут вам
достигнуть ваших целей и обеспечить стабильность в будущем.
В нашем ассортименте представлены банковские продукты, инвестиции,
страхование, кредиты и многое другое.
Мы постоянно обновляем нашу базу данных, чтобы вы были в курсе последних новостей и инноваций на
финансовом рынке. Наши специалисты помогут вам выбрать наиболее подходящий продукт,
учитывая ваши индивидуальные потребности
и предпочтения. Мы предоставляем консультации и рекомендации, чтобы вы могли принять взвешенное решение и избежать рисков.
Не упустите возможность воспользоваться нашими услугами и откройте для себя мир
Кобрендинговая кредитная карта в Новочебоксарске
Way cool! Some very valid points! I appreciate you writing this post plus the rest of the website
is extremely good.
Hello Dear, are you genuinely visiting this web site daily, if so
then you will absolutely obtain pleasant know-how.
Thanks for a marvelous posting! I quite enjoyed reading
it, you may be a great author. I will ensure that I bookmark your blog and will often come back in the foreseeable future.
I want to encourage yourself to continue your great work, have a nice afternoon!
I’m extremely pleased to find this page. I wanted to thank you for ones time due to this wonderful read!!
I definitely enjoyed every bit of it and i also have
you saved as a favorite to look at new stuff in your web site.
Very great post. I just stumbled upon your blog
and wanted to mention that I have really enjoyed surfing around your weblog posts.
In any case I’ll be subscribing to your rss feed and I’m hoping you write again soon!
Hello there! This is my first comment here so I just wanted to give a
quick shout out and tell you I genuinely enjoy reading through your blog posts.
Can you suggest any other blogs/websites/forums that cover the same subjects?
Appreciate it!
Hmm it appears like your site ate my first comment (it was extremely long) so I
guess I’ll just sum it up what I wrote and say, I’m thoroughly enjoying your blog.
I too am an aspiring blog blogger but I’m still new to everything.
Do you have any tips and hints for inexperienced blog
writers? I’d genuinely appreciate it.
I like the helpful info you provide in your articles.
I will bookmark your blog and check again here regularly.
I am quite certain I’ll learn many new stuff right here! Best
of luck for the next!
There’s certainly a great deal to find out about this issue.
I like all of the points you have made.
Everyone loves what you guys are up too. This kind of clever work and exposure!
Keep up the amazing works guys I’ve incorporated
you guys to our blogroll.
Touche. Outstanding arguments. Keep up the amazing work.
I really like what you guys are usually up too.
This kind of clever work and exposure! Keep up the very good works guys I’ve incorporated you guys to my blogroll.
Write more, thats all I have to say. Literally, it seems as though you relied on the video to make your point.
You definitely know what youre talking about,
why waste your intelligence on just posting videos to your
site when you could be giving us something informative to read?
Great post. I used to be checking constantly this blog and I
am impressed! Extremely useful information specifically
the remaining part 🙂 I handle such information much. I used to
be seeking this certain information for a very long time.
Thank you and good luck.
Hello to every single one, it’s actually a fastidious for
me to visit this web page, it includes precious Information.
Hi, I do think your web site may be having browser compatibility issues.
Whenever I look at your blog in Safari, it looks fine however when opening in Internet Explorer,
it has some overlapping issues. I just wanted to provide you with a quick heads up!
Other than that, wonderful website!
I visited several web pages but the audio feature for
audio songs existing at this website is really excellent.
Amazing! This blog looks just like my old one! It’s on a
entirely different subject but it has pretty much the same page layout and design. Great choice of colors!
Thanks to my father who told me on the topic of this website, this blog is genuinely
remarkable.
If some one wishes expert view concerning running a
blog afterward i suggest him/her to go to see this website, Keep up the pleasant job.
Appreciating the time and effort you put into your website and detailed information you offer.
It’s nice to come across a blog every once in a while that
isn’t the same old rehashed material. Excellent read!
I’ve saved your site and I’m adding your RSS feeds to my Google account.
Thanks for the auspicious writeup. It in fact used to
be a entertainment account it. Glance advanced to far
delivered agreeable from you! However, how can we keep in touch?
Hello, There’s no doubt that your web site may be having browser
compatibility issues. Whenever I take a look at your web site in Safari, it looks fine
but when opening in IE, it has some overlapping issues.
I merely wanted to provide you with a quick heads up! Aside from that, excellent
site!
Valuable info. Fortunmate me I discovered your website by accident, and I
am shocked why this accident didn’t happened earlier!
I bookmarked it.
My blog; bikep baru
Hey! I know this is kinda off topic but I’d figured I’d ask.
Would you be interested in trading links or maybe guest authoring a blog post or vice-versa?
My site addresses a lot of the same subjects as yours and I think we could greatly benefit from each other.
If you might be interested feel free to shoot me an email.
I look forward to hearing from you! Wonderful blog by the way!
Hi! This post couldn’t be written any better! Reading this post
reminds me of my old room mate! He always kept talking about this.
I will forward this write-up to him. Pretty
sure he will have a good read. Thanks for sharing!
Piece of writing writing is also a fun, if you be familiar with
then you can write if not it is complicated to write.
I loved as much as you will receive carried out right here.
The sketch is attractive, your authored material stylish.
nonetheless, you command get bought an nervousness
over that you wish be delivering the following.
unwell unquestionably come more formerly again since exactly
the same nearly a lot often inside case you shield
this increase.
Thanks for sharing your thoughts about heart chakra guided meditation. Regards
Hi, I do think this is an excellent website. I stumbledupon it 😉
I may return once again since I book-marked it. Money and freedom is the best way to change, may you be rich and continue
to help other people.
My brother recommended I would possibly like this web site.
He was entirely right. This put up actually made my day.
You can not consider simply how much time I had spent for this info!
Thank you!
I am not sure where you’re getting your information, but great topic.
I needs to spend some time learning much more or understanding more.
Thanks for magnificent info I was looking for this information for my mission.
Hello this is kinda of off topic but I was wanting to know if
blogs use WYSIWYG editors or if you have to manually code with HTML.
I’m starting a blog soon but have no coding know-how so
I wanted to get advice from someone with experience. Any help would be
enormously appreciated!
Every weekend i used to go to see this website, for the reason that i
wish for enjoyment, as this this web site conations genuinely fastidious funny
information too.
Hey there I am so happy I found your webpage, I really found you by accident,
while I was searching on Digg for something else, Regardless I am here
now and would just like to say thanks for a tremendous
post and a all round exciting blog (I also love the theme/design), I don’t have time to go through it all at the moment but I have bookmarked it and
also included your RSS feeds, so when I have time
I will be back to read a lot more, Please do keep up
the fantastic job.
Here is my web page: have a peek here
Way cool! Some extremely valid points! I appreciate you writing this
write-up and the rest of the site is really good.
My web-site: MACAUSLOT
I think that is one of the so much significant information for me.
And i am satisfied studying your article. But should statement on few
general things, The website taste is wonderful,
the articles is in point of fact great : D. Excellent job, cheers
Terrific work! This is the type of information that are meant to be shared across the internet.
Disgrace on Google for not positioning this post upper!
Come on over and seek advice from my web site . Thanks
=)
We’re a gaggle of volunteers and opening a brand new scheme in our
community. Your web site offered us with helpful information to work on. You’ve
performed a formidable process and our entire neighborhood
will probably be grateful to you.
WOW just what I was looking for. Came here by searching for vacuum chamber with pump
Hi there, I found your blog by means of Google at
the same time as looking for a comparable topic, your web site got here up, it seems great.
I’ve bookmarked it in my google bookmarks.
Hi there, simply was aware of your weblog via Google, and located that it’s really informative.
I am gonna watch out for brussels. I will be grateful in case you proceed
this in future. A lot of people shall be benefited out of your writing.
Cheers!
A motivating discussion is worth comment. I believe that you should publish
more about this subject, it may not be a taboo subject but typically people don’t talk about
these issues. To the next! Cheers!!
Small-sized bathrooms may instantly conjure images of cramped floor spaces, messy scenes of
toiletries and bathroom essentials spread here and
there, poor ventilation, lack of natural light, and
so on. In many cases, such images are myths because compact bathrooms are not
necessarily
challenging. All you need is a professional expert for bathroom remodelling in Gurgaon who can
transform your ideas into real-life scenarios.
Tips to Add Style & Functionality to Your Small Bathroom
Planned Remodelling is Crucial
The first tip for bathroom designs for small spaces is to start with planning.
Get a measuring tape to
measure the space and get an idea of the layout.
Prioritize what you want – do you need to increase
the storage space, install more lights for increased
lighting, or add modern aesthetics to the space?
With a clear and precise plan, there are fewer chances
of confusion and discrepancies arising later.
When I originally commented I clicked the “Notify me when new comments are added” checkbox and now each time a comment is added I get three e-mails with the same comment.
Is there any way you can remove people from that service?
Many thanks!
Yes! Finally someone writes about a.
my page :: webpage
Hi, I do think this is an excellent site. I stumbledupon it 😉 I may come back yet again since
I saved as a favorite it. Money and freedom is the greatest way to change, may you be rich and
continue to help other people.
Hey there just wanted to give you a quick heads up. The text in your content
seem to be running off the screen in Firefox.
I’m not sure if this is a formatting issue or something to do with internet browser compatibility but I thought I’d post to let you know.
The layout look great though! Hope you get the issue resolved soon. Many thanks
Hi there, this weekend is fastidious designed for me,
since this time i am reading this great informative piece of writing here at my house.
I got this web page from my buddy who informed me regarding this
web site and at the moment this time I am visiting this web site and reading very informative content here.
Terrific article! This is the kind of info that should be shared around the internet.
Disgrace on Google for now not positioning this
post higher! Come on over and visit my website . Thanks =)
Thanks for sharing such valuable insights. I’ve been struggling with Reddit marketing for a while and found that using high-karma accounts on Reddit is one of the best ways to get ahead. If you’re just starting out or trying to scale on Reddit, I highly recommend buying accounts that are already aged and trusted. It saves so much time and effort!
This is exactly what I’ve been thinking. As we all know, Reddit can be tough for new accounts. After a lot of trial and error, I finally decided to purchase an aged Reddit account with karma. It completely changed the way I approach Reddit marketing. The engagement is better.
If you’re using Reddit for affiliate marketing or content promotion, I’d highly recommend purchasing a Reddit account with post and comment karma. You avoid the algorithm flags and bans with aged accounts
One of the biggest challenges with Reddit is how they treat new accounts. Aged Reddit accounts are often much safer and more effective when it comes to marketing and content promotion. After I switched to using a verified Reddit profile, I noticed a huge difference in my ability to comment without being shadowbanned. If you want to get better engagement without worrying about account bans, I highly suggest looking into buying Reddit accounts with karma.
Highly recommend it for anyone serious about growing on Reddit. Whether you need Reddit engagement for personal or business reasons, an aged Reddit account is a game-changer. I’ve been using accounts with karma, and I’ve seen more followers in just a few weeks. You’ll notice the difference right away.
Keep up the great work with the content. I will definitely be following your advice and sharing it with others who are struggling with Reddit marketing. If anyone’s thinking about marketing on Reddit, I can’t recommend buying verified Reddit profiles enough. It really works.
It’s going to be ending of mine day, except before ending I am reading this
impressive piece of writing to increase my experience.
Hi there friends, its wonderful piece of writing concerning educationand completely explained, keep it up all the time.
Hi, after reading this amazing post i am too cheerful to share my experience
here with colleagues.
First off I want to say wonderful blog! I had a quick question that I’d
like to ask if you don’t mind. I was interested to know
how you center yourself and clear your head prior to writing.
I’ve had a hard time clearing my mind in getting my thoughts out there.
I truly do enjoy writing but it just seems like the first 10
to 15 minutes tend to be lost just trying to figure
out how to begin. Any recommendations or hints? Thanks!
If some one desires expert view on the topic of blogging afterward i recommend him/her to visit this blog, Keep up the fastidious work.
A motivating discussion is worth comment. I do think that you ought to publish more
on this topic, it might not be a taboo matter but generally
people do not discuss these issues. To the next! Cheers!!
I think the admin of this site is really working hard for his web
site, since here every stuff is quality based material.
This web site certainly has all the information and facts I wanted about this
subject and didn’t know who to ask.
I loved as much as you will receive carried out
right here. The sketch is tasteful, your authored subject matter stylish.
nonetheless, you command get bought an nervousness over that you wish be delivering the following.
unwell unquestionably come further formerly again since exactly the same nearly a lot often inside case you shield this hike.
After looking at a few of the articles on your website, I honestly like your technique of blogging.
I book marked it to my bookmark site list and will be checking back in the near future.
Please visit my web site too and let me know what you think.
WOW just what I was searching for. Came here by searching for travelling
Hi there! This post could not be written much better!
Reading through this article reminds me of my previous roommate!
He continually kept talking about this. I most certainly will forward
this information to him. Fairly certain he’ll have a great read.
Thanks for sharing!
This website truly has all of the information I wanted about this
subject and didn’t know who to ask.
When some one searches for his required thing, therefore he/she wants to be available that in detail, therefore that thing is maintained over here.
Hello just wanted to give you a quick heads up. The words
in your content seem to be running off the screen in Firefox.
I’m not sure if this is a format issue or something to do with internet browser compatibility but I thought
I’d post to let you know. The style and design look great though!
Hope you get the problem fixed soon. Thanks
I have been exploring for a little biit for any high quality articles or weblog posts
in this sort of space . Exploring in Yahoo I finally stumbled upon this site.
Reading this info So i am glad to convey that I have a very just right uncanny feeling I discovered
exactly what I needed. I most surelyy will make sure to do not omit this
website and give it a gglance on a continuing basis.
Awesome https://is.gd/N1ikS2
Great work! This is the kind of information that are meant to
be shared across the web. Shame on Google for now
not positioning this submit higher! Come on over and consult with my website .
Thank you =)
Howdy, I think your blog might be having web browser compatibility problems.
When I look at your web site in Safari, it looks fine
however, if opening in Internet Explorer, it has some overlapping issues.
I merely wanted to provide you with a quick heads up! Besides
that, fantastic site!
Hey very nice blog!
Take a look at my page: MPOMAX link alternatif
Musim biasa Overwatch League telah dimulai. Dalam pertempuran untuk California, Los Angeles Valiant-One di setiap dua tim kota kelahiran di liga overwatch menendang musim perdana Liga Overwatch dengan kemenangan menuju
San Francisco Shock. Sebagai pertandingan utama musim reguler liga, tidak ada
banyak sejarah antara kedua tim, simpan satu pertandingan pameran pramusim
yang diadakan pada bulan Desember. Di sanalah Valiant mengalahkan San Francisco Shock 3-2.
Tetapi Valiant telah mengasah komposisi selam mereka, memanfaatkan campuran Zenyatta, Mercy,
Widowmaker, D.Va, Tracer, Winston, Genji, dan McCree.
Kejutan itu tampak siap untuk melakukan perjuangan terhadap
kru yang berbasis di Los Angeles, namun mereka tidak dapat menjadi antitesis dari penyelaman Valiant.
Dan itu ironis: Kejutan telah membanggakan diri pada
gaya permainan anti-penyelaman mereka, benar-benar siap untuk muncul menuju gaya bermain Valiant.
Untuk beberapa alasan, kejutan itu tidak dapat bermain dengan ketepatan lambat yang
mereka inginkan. Bermain DP yang agresif dari pemain Genji,
Brady "Agility" Girardi dan Ted
"Silkthread" Wang-Silkthread bertukar untuk Agilitas di tengah jalan melalui urutan 4-recreation-mengikat kejutan pada pertahanan, sementara Terence "Soon" Tarlier mendorong batas kejutan dengan permainan janda.
There’s definately a lot to know about this topic.
I like all the points you’ve made.
WOW just what I was searching for. Came here by searching for ZCXDE34H9
I just like the helpful information you supply on your articles.
I will bookmark your blog and test again right here frequently.
I’m quite certain I’ll be told many new stuff proper here!
Best of luck for the following!
Woah! I’m really digging the template/theme of this site.
It’s simple, yet effective. A lot of times it’s very hard to get that “perfect balance” between user friendliness and
visual appeal. I must say you have done a excellent job with this.
Also, the blog loads super quick for me on Internet explorer.
Exceptional Blog!
Pretty! This has been an incredibly wonderful post. Thanks for providing these
details.
I think that what you posted was very reasonable. However,
think on this, suppose you added a little information? I
am not saying your content isn’t good, but
suppose you added something that makes people desire more?
I mean SMI diamond grinding wheels is a little vanilla.
You could glance at Yahoo’s front page and watch how they create news
titles to grab people to click. You might add a related
video or a picture or two to grab people interested about what you’ve got to
say. Just my opinion, it could make your website a
little bit more interesting.
Thanks for another informative blog. Where else may just I get that kind of info written in such an ideal
way? I’ve a venture that I am just now working on, and I’ve been at the look out for such
information.
If you wish for to increase your know-how only keep visiting
this website and be updated with the hottest news update posted here.
You actually make it seem so easy with your presentation but I find
this topic to be actually something which I think I would never understand.
It seems too complicated and extremely broad for me. I am looking forward for
your next post, I’ll try to get the hang of it!
There is certainly a lot to find out about
this topic. I like all the points you have made.
Whats up very nice site!! Guy .. Excellent .. Superb ..
I’ll bookmark your blog and take the feeds additionally?
I am happy to seek out numerous helpful information right here within the
post, we’d like develop more strategies in this regard, thanks for
sharing. . . . . .
I visit day-to-day a few websites and blogs to read content,
but this blog offers quality based articles.
Thank you for the auspicious writeup. It in fact was
a amusement account it. Look advanced to far added agreeable from
you! However, how could we communicate?
Hello, of course this piece of writing is in fact pleasant
and I have learned lot of things from it concerning blogging.
thanks.
My partner and I stumbled over here coming from a different web page and thought
I might as well check things out. I like what
I see so now i’m following you. Look forward to looking at your web page again.
Everything is very open with a precise description of the issues.
It was definitely informative. Your website is very helpful.
Thank you for sharing!
Greetings from Ohio! I’m bored to tears at work so I decided to browse your site on my iphone during lunch break.
I really like the information you provide here and
can’t wait to take a look when I get home.
I’m amazed at how quick your blog loaded on my phone ..
I’m not even using WIFI, just 3G .. Anyhow, excellent site!
I will right away seize your rss feed as I can not in finding your email subscription link or e-newsletter service.
Do you have any? Kindly permit me recognise in order that I may subscribe.
Thanks.
situs anak kontol link bokep semua
Hello! Would you mind if I share your blog with my zynga group?
There’s a lot of folks that I think would really appreciate your content.
Please let me know. Thank you
Oh, and, I recently found adobet88 and it looks pretty entertaining too!
Oh, and, I recently found adobet88 and it looks pretty interesting
too!
I visited various websites but the audio
quality for audio songs present at this web site is truly marvelous.
It’s going to be ending of mine day, however before finish I am reading this wonderful paragraph to improve my experience.
It’s appropriate time to make some plans for the future and it is time to be happy.
I have read this post and if I could I wish to suggest you some interesting things
or tips. Perhaps you can write next articles referring to this
article. I wish to read even more things about it!
Incredible! This blog looks just like my old one! It’s on a completely different topic
but it has pretty much the same layout and design. Wonderful choice of colors!
It’s the best time to make some plans for the future and it’s
time to be happy. I’ve read this post and if I could I wish to suggest you some interesting
things or tips. Perhaps you could write next articles referring
to this article. I want to read more things about it!
great issues altogether, you simply gained a new reader.
What might you suggest in regards to your put up that you simply
made a few days in the past? Any certain?
Nice post. I was checking continuously this blog and I’m impressed!
Extremely useful information particularly the last part 🙂 I care for such information a lot.
I was seeking this particular info for a very long time.
Thank you and best of luck.
What’s up every one, here every person is sharing such experience, thus
it’s nice to read this webpage, and I used to go to see this weblog every day.
Hello! Do you use Twitter? I’d like to follow you if that would be ok.
I’m absolutely enjoying your blog and look forward to new updates.
Hi to every one, as I am in fact eager of reading this
web site’s post to be updated daily. It contains fastidious stuff.
Fantastic beat ! I wish to apprentice while you amend your website, how can i subscribe for a blog web site?
The account helped me a acceptable deal. I had been a little bit acquainted of this your broadcast
provided bright clear concept
Hey! I know this is kinda off topic however I’d figured I’d ask.
Would you be interested in trading links or maybe guest writing a blog post
or vice-versa? My site discusses a lot of the same topics as yours and I think we could
greatly benefit from each other. If you happen to
be interested feel free to send me an email.
I look forward to hearing from you! Fantastic blog by the way!
What’s up to every one, the contents present at this website are really awesome for people knowledge,
well, keep up the good work fellows.
You made some decent points there. I looked on the net to find out more about the
issue and found most individuals will go along with your views
on this website.
Hello There. I found your blog using msn.
This is a very well written article. I’ll make sure to bookmark it and return to read more of your
useful info. Thanks for the post. I’ll certainly
return.
I go to see every day a few websites and blogs to read posts, except this blog gives feature based posts.
Have you ever thought about writing an ebook or guest authoring on other blogs?
I have a blog based upon on the same ideas you discuss and would love to have you share some
stories/information. I know my subscribers would value your work.
If you are even remotely interested, feel free to shoot me an email.
Hi! I could have sworn I’ve visited this website before but after looking at many of
the articles I realized it’s new to me. Nonetheless, I’m definitely
delighted I came across it and I’ll be book-marking it and checking back often!
I read this post fully concerning the comparison of latest and earlier technologies,
it’s remarkable article.
You can definitely see your expertise in the work you write.
The sector hopes for more passionate writers like
you who aren’t afraid to say how they believe.
Always follow your heart.
Wow lots of amazing advice!
Hi there, I enjoy reading through your article post. I wanted to write a little
comment to support you.
Just wish to say your article is as astounding.
The clarity for your post is simply spectacular and i can assume you’re knowledgeable on this
subject. Fine along with your permission allow me
to clutch your feed to keep up to date with imminent post.
Thanks a million and please continue the gratifying work.
Quality content is the secret to interest the people to visit the site, that’s what this web site is providing.
Hmm it appears like your website ate my first comment (it
was super long) so I guess I’ll just sum it up what I submitted and say, I’m thoroughly enjoying your blog.
I too am an aspiring blog blogger but I’m still new to everything.
Do you have any helpful hints for rookie blog writers? I’d definitely appreciate it.
Somebody necessarily lend a hand to make significantly
articles I’d state. That is the first time I frequented your web page
and to this point? I amazed with the analysis you made
to make this actual post extraordinary. Excellent activity!
It’s nearly impossible to find experienced people for this
subject, however, you sound like you know what
you’re talking about! Thanks
Wow, this piece of writing is fastidious, my younger sister is analyzing these kinds of things, therefore I am going to tell her.
Excellent blog here! Also your site quite a bit up fast!
What host are you the use of? Can I am getting your affiliate hyperlink to your host?
I want my web site loaded up as quickly as yours lol
Hello, after reading this awesome post i am also delighted to share my know-how here with friends.
Spot on with this write-up, I truly feel this site needs a great deal more
attention. I’ll probably be returning to see more,
thanks for the information!
Appreciate the recommendation. Will try it out.
Good day! I know this is somewhat off topic but I was wondering which blog
platform are you using for this website? I’m getting fed up of WordPress
because I’ve had issues with hackers and I’m
looking at alternatives for another platform. I would
be fantastic if you could point me in the direction of a good platform.
I pay a quick visit daily some blogs and information sites to read articles, except this blog offers feature based articles.
Whoa quite a lot of wonderful advice!
I am sure this paragraph has touched all the internet people, its really
really pleasant paragraph on building up new weblog.
Just wish to say your article is as astonishing. The clarity
for your submit is simply cool and i could
suppose you are an expert on this subject.
Fine together with your permission let me to snatch your feed
to keep up to date with forthcoming post. Thank you
a million and please continue the rewarding work.
Hurrah! At last I got a blog from where I know how to actually take
valuable data regarding my study and knowledge.
I every time used to study post in news papers
but now as I am a user of web thus from now I
am using net for posts, thanks to web.
My brother recommended I might like this website.
He was totally right. This post truly made my day.
You can not imagine just how much time I had spent for this info!
Thanks!
Fantastic blog! Do you have any suggestions for aspiring writers?
I’m hoping to start my own blog soon but I’m a little lost
on everything. Would you propose starting with a free
platform like WordPress or go for a paid option? There are so many choices out there that I’m totally overwhelmed
.. Any recommendations? Many thanks!
Excellent beat ! I wish to apprentice even as you amend your site, how could i subscribe for a weblog site?
The account helped me a acceptable deal. I were a little bit acquainted of this your broadcast
offered vibrant transparent concept
This is a topic that’s near to my heart…
Cheers! Where are your contact details though?
It’s the best time to make some plans for the future
and it’s time to be happy. I’ve read this post and if I could I desire to suggest you few interesting things
or tips. Perhaps you can write next articles referring to this
article. I wish to read more things about it!
I’m not sure where you are getting your information, but good topic.
I needs to spend some time learning more or understanding more.
Thanks for great info I was looking for this info for my mission.
Thank you for sharing your thoughts. I really appreciate your efforts and I
am waiting for your further post thanks once again.
Definitely consider that which you stated. Your favorite justification seemed to be on the web the simplest thing to take into account of.
I say to you, I certainly get irked even as people think about issues that they just do not recognize about.
You controlled to hit the nail upon the highest and
also defined out the whole thing without having side effect , folks could take a signal.
Will likely be again to get more. Thanks
On the silent blue night screen,
There is a girl dancing behind the light,
Spreading a smile, waiting to say hello,
In cyberspace, her name is Stripchat.
Free tokens become hope,
From nameless fingers,
They come, they go,
Leaving traces in a lonely space.
Your gaze penetrates the glass boundary,
Searching for meaning behind words,
Between real and virtual,
You dance, you joke.
Live cam girl, digital star,
Selling dreams, exchanging time,
In Stripchat, a virtual world,
Free tokens, false promises.
But behind the laughter and seduction,
There is a heart that is still waiting,
For love, or just longing,
On the blue screen, you are still beautiful.
I’m very pleased to uncover this web site. I need to
to thank you for ones time for this particularly fantastic read!!
I definitely savored every bit of it and i also have you book-marked
to see new stuff in your site.
You actually make it seem so easy with your presentation but I find this matter to be actually something that I think I would never understand.
It seems too complex and extremely broad for me. I’m looking forward for your next post, I
will try to get the hang of it!
Great article! We will be linking to this great article on our website.
Keep up the good writing.
Here is my homepage: customer support agent
I all the time emailed this website post page to all my friends, since if like to read it next my contacts will too.
Sweet blog! I found it while surfing around on Yahoo News.
Do you have any suggestions on how to get listed in Yahoo News?
I’ve been trying for a while but I never seem to
get there! Thank you
Hi, I do believe this is a great website.
I stumbledupon it 😉 I am going to come back once again since i have saved as a
favorite it. Money and freedom is the greatest way to change, may you be rich and continue to help others.
This piece of writing will help the internet people for building up
new blog or even a blog from start to end.
Nice answer back in return of this question with real arguments and explaining the whole thing regarding that.
We stumbled over here coming from a different web address and thought I should check things out.
I like what I see so now i am following you.
Look forward to exploring your web page repeatedly.
Hello to every single one, it’s in fact a fastidious for me to go to see this website, it contains
helpful Information.
Greetings! Very helpful advice in this particular article!
It is the little changes that will make the largest changes.
Many thanks for sharing!
Fine way of explaining, and nice piece of writing to take facts regarding my presentation subject, which i am going to deliver in academy.
You are so cool! I do not suppose I’ve read
through something like this before. So nice to find someone with
original thoughts on this issue. Really.. many thanks for starting this up.
This site is one thing that is needed on the web, someone with a little originality!
Interesting blog! Is your theme custom made or
did you download it from somewhere? A theme like yours with a few simple tweeks would really make
my blog stand out. Please let me know where you got
your design. Thanks
Что же отличает экраны iPhone 15 и iPhone
15 Plus от своих предшественников?
| В чём различия экранов iPhone 15 и iPhone 15 Plus по сравнению
с предыдущими моделями? | Чем iPhone 15 и iPhone 15 Plus отличаются в плане дисплея от прошлых поколений?
Во-первых, рекордная пиковая яркость до 2000 нит , что делает использование смартфона при
солнечном освещении .
По мнению Дэна, остаётся вопрос , сколько времени устройство сможет удерживать
максимальной яркости, прежде чем
она снизится резко. Подобное
случалось ранее, например, с моделями iPhone 13 Pro . https://macuser.ua/search?word=airpods+%D1%87%D0%B5%D1%80%D0%BD%D1%8B%D0%B5+%D0%BA%D1%83%D0%BF%D0%B8%D1%82%D1%8C++%D0%B0%D1%80%D0%B1%D0%B0%D1%82
Spot on with this write-up, I seriously feel this site needs much more attention. I’ll probably be back again to read more, thanks for
the info!
When I originally commented I clicked the “Notify me when new comments are added” checkbox and now each time a comment is
added I get three emails with the same comment.
Is there any way you can remove me from that service? Cheers!
whoah this blog is excellent i love studying your posts.
Keep up the good work! You realize, a lot of persons
are searching around for this info, you could aid them greatly.
Oh my goodness! Impressive article dude! Thank you, However I
am encountering difficulties with your RSS. I don’t
know why I can’t subscribe to it. Is there anybody else getting identical RSS problems?
Anyone that knows the answer can you kindly respond?
Thanx!!
Hey there folks,
SEO and online marketing are essential in today’s ever-evolving business world.
As a Chicago local,I’ve seen how local SEO signifcicantly enhance online visibility—especially for specialized industries.
Nfinitelimits, a top-tier agency in Mundelein, IL, clearly excels with data-driven solutions.
Their expertise in technical seo work (madeinna.org) and PPC campaigns substantially helps
businesses to dominate in regional markets.
For example|Consider their successful campaigns: they optimize Google Business Profiles and
employ state-of-the-art technology to keep ahead of SEO trends.
Paired with social media integration, they develop holistic plans.
Shoulpd you be aiming to enhance your online reach,
Nfinitelimits delivers visible outcomes. The agency’s cusstomized solutions drive long-term growth, not just
short-term solutions.
Hello, Neat post. There’s an issue along with your web site in web explorer, may check this?
IE still is the market leader and a large part of
other folks will omit your wonderful writing because of this problem.
Hey I know this is off topic but I was wondering if you knew of
any widgets I could add to my blog that automatically tweet my newest twitter updates.
I’ve been looking for a plug-in like this for quite some time and was hoping
maybe you would have some experience with something like this.
Please let me know if you run into anything. I truly enjoy reading your blog and I look forward to your new updates.
You’re so interesting! I don’t think I’ve truly read something like that before.
So nice to discover another person with a few unique thoughts
on this issue. Seriously.. thank you for starting
this up. This site is one thing that is needed on the
web, someone with a bit of originality!
This design is spectacular! You definitely know
how to keep a reader entertained. Between your wit
and your videos, I was almost moved to start my own blog (well,
almost…HaHa!) Excellent job. I really enjoyed what you had to say, and more than that,
how you presented it. Too cool!
It is the best time to make some plans for the future and it’s time to be happy.
I have learn this post and if I may I wish to suggest you some attention-grabbing issues or advice.
Maybe you could write subsequent articles relating
to this article. I wish to learn even more things about it!
This excellent website really has all the info
I wanted concerning this subject and didn’t know who to ask.
For hottest news you have to pay a quick visit web and on internet I
found this site as a best web site for latest updates.
Hi everyone, it’s my first pay a quick visit at this site, and paragraph is really fruitful in support of me, keep
up posting these types of posts.
I love reading through an article that can make men and women think.
Also, thanks for allowing me to comment!
You might experience odours from your a/c that indicate it needs a solution.
Hi there! I’m at work surfing around your blog from my new apple
iphone! Just wanted to say I love reading your blog and look forward
to all your posts! Keep up the great work!
I was extremely pleased to find this web site.
I wanted to thank you for ones time for this fantastic read!!
I definitely savored every part of it and i also have you
bookmarked to look at new stuff on your website.
This site was… how do you say it? Relevant!! Finally I have found something which helped
me. Appreciate it!
Great items from you, man. I’ve consider your stuff previous to
and you are just too great. I really like what you’ve acquired right here, certainly like what you’re stating and the way in which you are saying it.
You’re making it entertaining and you still take care of to keep it sensible.
I can not wait to learn far more from you. This is really a great website.
Magnificent web site. A lot of useful information here.
I’m sending it to several buddies ans also sharing in delicious.
And of course, thanks on your effort!
You actually make it seem so easy with your presentation but I find this matter
to be actually something that I think I would never understand.
It seems too complex and very broad for me. I’m looking forward
for your next post, I’ll try to get the hang of it!
Here is my blog – webpage
Thank you for another informative blog. The place else may I get
that type of info written in such a perfect approach? I have a challenge that I’m simply
now running on, and I have been at the look out for such information.
excellent points altogether, you just won a emblem new reader.
What could you suggest in regards to your submit that you
simply made some days in the past? Any positive?
Wow, this post is pleasant, my sister is analyzing these
kinds of things, so I am going to tell her.
I simply couldn’t depart your site before suggesting that I really loved the usual information a person supply to your guests?
Is going to be back frequently in order to check up on new posts
This design is wicked! You obviously know how to keep a reader entertained.
Between your wit and your videos, I was almost moved
to start my own blog (well, almost…HaHa!) Great job.
I really enjoyed what you had to say, and more than that, how you presented it.
Too cool!
fantastic points altogether, you just gained a new reader.
What could you suggest about your put up that you made some days in the past?
Any positive?
Hi! I realize this is somewhat off-topic however I had
to ask. Does managing a well-established blog like yours take a lot of work?
I am brand new to writing a blog but I do write in my diary on a daily basis.
I’d like to start a blog so I can share my personal
experience and views online. Please let me know if you have any recommendations or tips
for new aspiring blog owners. Thankyou!
I like it whenever people get together and share opinions. Great website, continue the good work!
Today, while I was at work, my cousin stole my apple ipad and tested to see if
it can survive a forty foot drop, just so she can be a youtube sensation.
My iPad is now destroyed and she has 83 views. I know this is completely off topic but I
had to share it with someone!
Hi there to every single one, it’s actually a pleasant for me to go to see this
site, it includes useful Information.
You’ve managed to capture something ineffable — your words touch a place that logic alone cannot reach.
The Girl Behind the Digital Screen
In a virtual space full of light,
There is a girl dancing words and laughter,
Greeting the world without pause,
Through the screen, hope is built.
Free tokens are like twilight rain,
Dripping slowly on the fingertips,
Every smile, every glance,
Becoming a code, becoming a promise.
Behind the spotlight and pixels,
There is an unspoken longing,
The girl is waiting, waiting for the wave,
From those who are present without a name.
Not just numbers on the screen,
Not just tokens that flow,
There is a story, there is a feeling,
In every second that rolls.
Long nights become witnesses,
Live cam girls dance in silence,
Weaving dreams, reaching for meaning,
In a virtual world that is never quiet.
Terrific work! That is the type of info
that are supposed to be shared across the net.
Disgrace on Google for not positioning this publish higher!
Come on over and visit my web site . Thank you =)
Hey there just wanted to give you a quick heads up and
let you know a few of the pictures aren’t
loading properly. I’m not sure why but I
think its a linking issue. I’ve tried it in two different browsers and both show the
same outcome.
I loved as much as you will receive carried out right here.
The sketch is attractive, your authored subject matter stylish.
nonetheless, you command get bought an edginess over that you wish be delivering the following.
unwell unquestionably come further formerly again since exactly the
same nearly a lot often inside case you shield this increase.
Nice post. I was checking constantly this blog and I’m impressed!
Very useful info specially the last part 🙂 I
care for such info much. I was looking for this certain information for a
long time. Thank you and best of luck.
Hello i am kavin, its my first time to commenting anyplace, when i read this post i thought
i could also create comment due to this good article.
It’s actually very complicated in this active life to listen news on TV,
so I simply use internet for that purpose, and get the newest
news.
Hi there to all, the contents existing at this website are
really amazing for people knowledge, well, keep up the nice work fellows.
On top of that, they operate with low power intake and improved efficiency.
Hi there, the whole thing is going perfectly here and ofcourse
every one is sharing facts, that’s really fine, keep up
writing.
Write more, thats all I have to say. Literally, it
seems as though you relied on the video to make your point.
You clearly know what youre talking about, why waste your intelligence
on just posting videos to your blog when you could be giving us
something enlightening to read?
You actually make it seem so easy with your presentation but I
find this topic to be really something which I think I would never understand.
It seems too complicated and extremely broad for me.
I’m looking forward for your next post, I’ll try to get
the hang of it!
Greetings! Very helpful advice in this particular article!
It is the little changes that make the largest changes.
Thanks a lot for sharing!
It is appropriate time to make a few plans for the longer term
and it is time to be happy. I have read this publish and if I may just I want to suggest you
some fascinating issues or advice. Perhaps you could write subsequent articles referring
to this article. I want to read even more issues about
it!
Hi! This post couldn’t be written any better! Reading
this post reminds me of my previous room mate!
He always kept talking about this. I will forward this write-up to him.
Pretty sure he will have a good read. Many thanks for sharing!
E2Bet เว็บเดิมพันออนไลน์อันดับท็อปของเอเชีย เชื่อถือได้ มั่นคง ปลอดภัย เพิ่มประสบการณ์การเล่นที่เหนือกว่าใคร E2Bet
เท่านั้น! สมัครเลยตอนนี้ รับสิทธิพิเศษมากมาย
https://mazda-demio.ru/forums/index.php?autocom=gallery&req=si&img=6403
https://honda-fit.ru/forums/index.php?autocom=gallery&req=si&img=7105
You really make it seem so easy with your presentation however I find this matter to be actually one thing
that I feel I would by no means understand. It kind of feels too complicated
and extremely extensive for me. I am taking a look ahead on your subsequent submit, I’ll
attempt to get the hang of it!
This excellent website truly has all of the
info I needed about this subject and didn’t know who to ask.
Awesome blog! Do you have any hints for aspiring writers? I’m planning to start my own site soon but I’m a little lost on everything.
Would you advise starting with a free platform
like WordPress or go for a paid option? There are so many choices out
there that I’m completely overwhelmed .. Any recommendations?
Cheers!
Heya i am for the primary time here. I came across this board and I find It truly
useful & it helped me out much. I hope to provide one thing
again and aid others like you helped me.
Very soon this web site will be famous amid all blogging people,
due to it’s pleasant articles or reviews
This paragraph will assist the internet
viewers for building up new webpage or even a blog from
start to end.
Howdy! I could have sworn I’ve been to this website before but after looking at a few of
the articles I realized it’s new to me. Regardless, I’m definitely delighted I discovered it and I’ll be
book-marking it and checking back often!
Hello, this weekend is pleasant designed for me, as this time i am reading this fantastic informative article here
at my home.
Good response in return of this matter with firm arguments and
describing the whole thing concerning that.
It’s very simple to find out any matter on web as compared to books, as
I found this paragraph at this site.
I was suggested this website by my cousin. I’m not sure
whether this post is written by him as no one else know such detailed about my trouble.
You are wonderful! Thanks!
My relatives always say that I am wasting my time here at net,
except I know I am getting experience everyday by reading such fastidious
articles.
I am actually thankful to the holder of this web
page who has shared this enormous post at at
this time.
When some one searches for his essential thing, therefore he/she needs to
be available that in detail, so that thing is maintained over here.
Very good article! We will be linking to this great article on our website.
Keep up the good writing.
Hi there all, here every person is sharing such know-how, so it’s
good to read this web site, and I used to pay a quick visit this
website everyday.
E2Bet
Blog Comment: If you’re a cricket fan in Pakistan,
E2Bet is the platform for you. They cover all major tournaments with detailed betting options.
My go-to website for cricket betting!
Way cool! Some extremely valid points! I appreciate you
penning this article plus the rest of the site is also very
good.
That is a really good tip especially to those
new to the blogosphere. Simple but very accurate
info… Appreciate your sharing this one. A must read post!
If some one wishes to be updated with hottest technologies therefore he must be go
to see this web site and be up to date every day.
I was recommended this website by way of my cousin. I am no longer sure whether or not this submit is written by him as nobody
else realize such distinctive approximately my trouble. You’re wonderful!
Thank you!
Also visit my website; zgarciog01
There is certainly a great deal to learn abot this subject.
I love all the points you’ve made.
Remarkable things here. I am very glad to see your post.
Thank you a lot and I’m taking a look forward to contact you.
Will you kindly drop me a mail?
What’s Happening i am new to this, I stumbled upon this I’ve found It
absolutely helpful and it has aided me out loads.
I am hoping to contribute & assist other customers like its helped me.
Good job.
You actually make it seem so easy with your presentation but I find this topic to be really something which I think
I would never understand. It seems too complex and very broad for me.
I’m looking forward for your next post, I’ll try
to get the hang of it!
I was suggested this web site by my cousin. I’m not sure whether this post is written by him as nobody else know such detailed about my problem.
You are amazing! Thanks!
hi!,I love your writing so much! percentage we communicate
extra approximately your article on AOL? I need a specialist on this house to unravel my problem.
Maybe that’s you! Having a look ahead to see you.
I am sure this piee off writing has ttouched all the internet users, its reallly
really nice post on building up new web site.
Here iis my webpage – bokeb asian
What’s up to every body, it’s my first go to see of this
website; this weblog contains remarkable and genuinely good stuff designed for readers.
Usually I don’t learn article on blogs, however I wish to say
that this write-up very forced me to try and do so!
Your writing taste has been amazed me. Thank you, very great post.
It’s difficult to find educated people on this topic, however, you seem like
you know what you’re talking about! Thanks
Cialis is designed to final much longer than Viagra. See your doctor in the event you discover any of those negative effects, particularly if they final for a couple of hours after the medication has worn off or if they linger for more than a day afterward. How lengthy does Cialis last? However, Cialis does require a every day dose to be absolutely efficient and depends on a certain stage of the drug to have constructed up in your system. It’s taken day by day, so that you don’t have to fret about timing of sexual activities. Cialis and Viagra don’t cause erections on their very own. While the results for treating angina were disappointing, many individuals reported creating erections after taking Viagra. “How typically are you having hassle getting arduous or staying laborious.” “Rate the standard hardness of your erection throughout masturbation.” “Rate the typical hardness of your spontaneous erections in the middle of the night time or the morning.” “Rate the typical hardness of your erection with a sexual partner.” “Do you could have any allergies? These optimistic facets allow a lot more gentlemen to get into the prescription medication they should assist with ED, which can have a substantial have an effect on on their customary of dwelling and relationships.
I know this if off topic but I’m looking into starting my own blog and was wondering
what all is needed to get setup? I’m assuming having a blog
like yours would cost a pretty penny? I’m not very web smart so I’m not 100% sure.
Any suggestions or advice would be greatly
appreciated. Cheers
Great info. Lucky me I found your website by accident (stumbleupon).
I have book marked it for later!
10 Inspiring Images About Adultwork Pornstar Adult Pornstar
As a physician specializing in internal medicine and clinical pharmacology,
I’ve always been keenly aware of the impact that the
right nutrients can have on our health. This understanding led me to
create Global Health Treasures, an online store that
aims to bring together the best dietary supplements available.
Each product in our collection has been meticulously selected for its potential to support various aspects of health and wellness.
At Global Health Treasures, we go beyond merely
selling supplements. We believe in empowering our customers with knowledge and providing personalized health consultations.
These consultations are conducted by experts who help you choose the right supplements based on your unique health needs and goals.
Our commitment to quality and customer education sets us apart in the crowded world of dietary
supplements. Whether you are looking to boost your
immune system, improve your metabolic health, or just maintain overall wellness, Global Health Treasures is your trusted partner in achieving
better health. Visit us today to explore our top-tier selection and start
your journey to a healthier you.
I’m extremely impressed with your writing skills as well as with the layout on your blog.
Is this a paid theme or did you modify it yourself?
Anyway keep up the nice quality writing, it is rare to see a nice blog like this one nowadays.
Outdoor LED displays have arised as a prominent choice
for marketers seeking to record the attention of potential
customers. Vendors of outdoor LED display screens provide an array
of resolutions and sizes, supplying clients with customized
options that meet particular advertising needs.
Please let me know if you’re looking for a article writer for your blog.
You have some really great articles and I think
I would be a good asset. If you ever want to take some of the load off, I’d absolutely love to write some content
for your blog in exchange for a link back to mine. Please blast me an e-mail if interested.
Thanks!
I have been exploring for a little for any high
quality articles or blog posts on this kind of space . Exploring in Yahoo
I eventually stumbled upon this site. Studying this
information So i’m satisfied to show that I have
an incredibly excellent uncanny feeling I found out exactly what
I needed. I so much unquestionably will make certain to don?t fail to remember this website
and provides it a look on a continuing basis.
bokep open bo
I visit day-to-day a few blogs and blogs to read content, but this weblog gives
quality based writing.
Heya i am for the first time here. I found this board and I find It truly useful & it helped me out much.
I hope to give something back and help others like you aided me.
You really make it seem really easy with your presentation however I in finding this topic to be actually one thing which I think I’d by no means understand.
It sort of feels too complex and extremely huge for
me. I am having a look forward to your subsequent submit, I’ll try to get the hold of
it!
Link exchange is nothing else but it is simply placing the other person’s web site link on your page at
proper place and other person will also do similar in favor of you.
Postingan yang sangat informatif! Saya jadi semakin tertarik main di situs RJP777.
Benar-benar gacor katanya!
Terima kasih untuk ulasannya. Saya sudah coba login di RJP777, dan memang game-nya beneran gacor.
Suka banget sama artikel ini. Sekarang saya main di RJP777 terus, karena CS-nya juga
fast respon
Nice info gan! Udah banyak yang bilang layak dicoba.
Gaskeun main!
It has also spurred the development of other similar
medications, such as tadalafil (Cialis) and vardenafil (Levitra), expanding the options available for erectile dysfunction treatment.
Aw, this was an exceptionally nice post. Taking the time and actual effort to produce a really good article… but what can I say…
I put things off a whole lot and never manage
to get nearly anything done.
Hello there! Quick question that’s entirely off topic.
Do you know how to make your site mobile friendly? My website looks weird when viewing from my
apple iphone. I’m trying to find a template or plugin that might be able to
fix this issue. If you have any suggestions, please share.
Thanks!
This is a really good tip particularly to those fresh to the blogosphere.
Short but very accurate information… Many thanks for sharing this one.
A must read article!
We’re a group of volunteers and starting a new scheme in our
community. Your web site provided us with valuable info to work on.
You’ve done a formidable job and our whole community will
be thankful to you.
An outstanding share! I have just forwarded this onto a
co-worker who had been doing a little research on this.
And he in fact ordered me breakfast due to
the fact that I found it for him… lol. So let me reword this….
Thanks for the meal!! But yeah, thanks for spending the time to
talk about this issue here on your website.
always i used tto read smaller articles that as ԝell cⅼear thei motive, ɑnd tһat is
ɑlso happening ᴡith tuis article ѡhich I аm reading at this
place.
Visit my webb pagе – GTA777
This is really interesting, You’re a very skilled blogger.
I’ve joined your rss feed and look forward to seeking more
of your great post. Also, I have shared your website in my social
networks!
Touche. Sound arguments. Keep up the amazing work.
You made some good points there. I checked on the internet for more
information about the issue and found most people will go along with your views
on this web site.
hello there and thank you for your information –
I’ve certainly picked up something new from right
here. I did however expertise a few technical issues
using this web site, as I experienced to reload the site lots of times previous to I could get it to load properly.
I had been wondering if your web hosting is OK? Not that I am
complaining, but slow loading instances times will very frequently affect your placement in google and can damage your high-quality score if advertising
and marketing with Adwords. Well I am adding this RSS to my email and can look
out for much more of your respective intriguing content.
Make sure you update this again soon.
Excellent web site you have here.. It’s hard to find high quality writing like yours nowadays. I really appreciate people like you! Take care!!
Hi there! I could have sworn I’ve been to this blog before but after checking through some of the
post I realized it’s new to me. Nonetheless, I’m definitely glad I found it and I’ll be
book-marking and checking back frequently!
This information is worth everyone’s attention. When can I find out more?
What a material of un-ambiguity and preserveness of valuable knowledge on the topic of unexpected
feelings.
Just wish to say your article is as astonishing. The clarity in your publish is just great
and that i could suppose you are a professional in this
subject. Well with your permission let me to grasp your feed to keep up to date with coming
near near post. Thank you one million and please keep
up the gratifying work.
Hmm is anyone else experiencing problems with the images on this blog loading?
I’m trying to determine if its a problem on my end or if it’s the blog.
Any feed-back would be greatly appreciated.
Hi, I do hink this iis a great web site. I stumbledupon itt 😉 I mayy come back yet again since I saved as a favorite it.
Money and freedom is the best way to change, may yoou be rich and
conttinue to heelp other people.
When some one searches for his essential thing, thus he/she wishes to be available that in detail,
therefore that thing is maintained over here.
At this time it appears like Movable Type is
the top blogging platform out there right now. (from what
I’ve read) Is that what you’re using on your blog?
My spouse and I stumbled over here by a different web page and thought I may as well
check things out. I like what I see so now i am
following you. Look forward to looking into your web page again.
Wonderful web site. Lots of helpful info here. I’m sending it to some pals ans additionally sharing in delicious.
And of course, thanks on your sweat!
Good day! Would you mind if I share your blog with my myspace group?
There’s a lot of folks that I think would really appreciate
your content. Please let me know. Thanks
Hello very cool website!! Man .. Beautiful ..
Amazing .. I will bookmark your website and take the feeds also?
I am glad to seek out a lot of useful info right here in the publish, we’d
like work out more strategies in this regard, thank you for sharing.
. . . . .
Sweet blog! I found it while browsing on Yahoo News.
Do you have any suggestions on how to get listed in Yahoo News?
I’ve been trying for a while but I never seem to get there!
Thank you
Hi I am so glad I found your webpage, I really found you by error,
while I was researching on Bing for something else, Nonetheless I am here now
and would just like to say thanks a lot for a tremendous post and
a all round exciting blog (I also love the theme/design), I don’t have time
to go through it all at the moment but I have saved it and also included your RSS feeds, so when I have
time I will be back to read more, Please do keep up the great job.
That is a very good tip especially to those new to the blogosphere.
Brief but very precise info… Appreciate your sharing this one.
A must read post!
If you would like to improve your know-how only keep visiting this web
page and be updated with the hottest news update posted here.
Good day! I just want to offer you a big thumbs up for your excellent info you’ve got right here on this post.
I am coming back to your site for more soon.
What you typed made a great deal of sense. But, what about this?
suppose you wrote a catchier title? I ain’t suggesting your
content isn’t solid, however what if you added a title to possibly get folk’s attention? I mean SMI diamond grinding wheels is a
little plain. You should glance at Yahoo’s front page and note
how they create article headlines to grab people to click.
You might add a related video or a picture or two to get people interested about everything’ve got to say.
Just my opinion, it might make your blog a little bit more interesting.
Hi, constantly i used to check website posts here in the early hours in the daylight, since i love to gain knowledge of more and more.
Have you ever thought about creating an ebook or guest authoring on other websites?
I have a blog based on the same topics you discuss and would love to have you share some stories/information. I know my audience would enjoy your work.
If you are even remotely interested, feel free to
send me an e-mail.
I blog often and I seriously appreciate your content. This
article has truly peaked my interest. I’m going to take
a note of your blog and keep checking for new information about once a week.
I opted in for your Feed as well.
Достигните новых высот с нашим
сервисом прогона хрумером и ГСА!
Мы гарантируем качественное продвижение вашего сайта,
увеличение трафика и повышении позиций в поисковых системах.
Закажите сейчас и получите эксклюзивные условия!
Не упустите возможность привлечь новых клиентов и увеличить продажи.
Контактируйте с нами и увидите результат заказать можно здесь ==>> https://t.me/+HFxk5vlUvGEzM2Zi
This article will help the internet viewers for creating new web site or
even a blog from start to end.
Hi my family member! I wish to say that this article is
awesome, great written and include almost all vital infos.
I would like to peer extra posts like this .
hello there and thank you for your information – I’ve definitely
picked up something new from right here. I did however expertise
some technical issues using this web site, since I experienced to reload the website
a lot of times previous to I could get it to load correctly.
I had been wondering if your hosting is OK?
Not that I’m complaining, but sluggish loading instances times will very frequently affect your placement in google and can damage your high-quality score if advertising and marketing with Adwords.
Well I am adding this RSS to my email and could look
out for much more of your respective fascinating content.
Ensure that you update this again soon.
It’s difficult to find well-informed people on this subject, however,
you seem like you know what you’re talking about! Thanks
Hello everyone, it’s my first go to see at
this web page, and piece of writing is actually fruitful in favor
of me, keep up posting these content.
It’s an amazing piece of writing for all the web users; they
will get benefit from it I am sure.
I was recommended this web site by my cousin. I’m not
sure whether this post is written by him as nobody else know such detailed about
my problem. You’re incredible! Thanks!
What’s Happening i’m new to this, I stumbled upon this
I’ve discovered It absolutely helpful and it has aided me out loads.
I hope to give a contribution & assist other users like its helped me.
Great job.
Excellent website you have here but I was wondering if you knew of any community forums that
cover the same topics discussed here? I’d really like to be a part of group where I can get feedback from other knowledgeable people that share the same interest.
If you have any recommendations, please let me know.
Cheers!
Yߋur article іs qᥙite well-wrіtten. I admire how perfectly
ʏou dеscribed all thee details. Ꮮooking forward tο more posts!
Аlso visit my page: Elite Escorts Lahore
I needed to thank you for this fantastic read!! I absolutely
enjoyed every bit of it. I’ve got you bookmarked to check out new things you post…
I blog quite often and I genuinely appreciate your content.
The article has truly peaked my interest. I’m going to book mark your site and keep checking for new information about once a week.
I opted in for your Feed as well.
You’ve made some good points there. I checked on the internet for additional information about the issue
and found most individuals will go along with your views on this website.
Howdy! I simply wish to give you a big thumbs up for
the great info you have got right here on this post.
I am returning to your site for more soon.
Magnificent website. Lots of useful info here. I’m sending it to several buddies ans additionally sharing in delicious.
And obviously, thank you for your sweat!
Hi there, its pleasant paragraph on the topic of media print, we all understand
media is a great source of information.
Great blog you have got here.. It’s hard to find excellent writing like yours nowadays. I truly appreciate individuals like you! Take care!!
Wow, incredible blog layout! How lengthy have you been blogging
for? you made blogging glance easy. The total glance of your web site is
fantastic, let alone the content material!
I am not sure where you are getting your info, but good topic.
I needs to spend some time learning more or understanding more.
Thanks for excellent information I was looking for this information for my mission.
Nice weblog here! Also your web site lots up very fast!
What host are you the use of? Can I get your associate hyperlink in your host?
I wish my site loaded up as fast as yours lol
We’re a group of volunteers and starting a new scheme
in our community. Your site offered us with valuable information to work on.
You’ve done an impressive job and our whole
community will be thankful to you.
I like what you guys are up too. This sort of clever work and coverage!
Keep up the wonderful works guys I’ve included you guys to our
blogroll.
Hi! I’ve been following your website for a long
time now and finally got the courage to go ahead and give you a shout out from Huffman Tx!
Just wanted to mention keep up the excellent job!
Feel free to visit my webpage – is mitolyn legitimate
I’m impressed, I must say. Rarely do I encounter a blog that’s
equally educative and engaging, and let me tell you, you’ve hit the nail on the head.
The problem is something too few folks are speaking intelligently about.
I’m very happy I stumbled across this in my hunt for something regarding this.
This is very interesting, You are a very skilled blogger.
I’ve joined your feed and look forward to seeking more
of your excellent post. Also, I’ve shared your web site in my social networks!
Please let me know iif you’re looking for a author for your site.You have some really good articles and I believe I would be a good asset.
If you ever want to take some of the load
off, I’d really like to write some material for your blog in exchange for a link back to mine.
Please shookt me aan email if interested.
Many thanks!
Informative article, exactly what I was looking for.
Heya i am for the first time here. I found this board and I
find It really useful & it helped me out much. I hope to give
something back and help others like you aided me.
Your means of telling the whole thing in this article is genuinely pleasant, all
can effortlessly be aware of it, Thanks a lot.
It’s going to be ending of mine day, however before finish I am reading this great paragraph to improve my knowledge.
If you’re looking for a powerful WhatsApp hash extractor
or WhatsApp WART extractor, you need a reliable tool that can efficiently
extract WhatsApp account details from Android devices.
Whether you’re a digital marketer, researcher,
or developer, our WhatsApp account extractor software
provides seamless extraction of WhatsApp protocol
numbers, hash keys, and more.
Hi there, just became alert to your blog through Google, and found that it is truly informative.
I am going to watch out for brussels. I’ll be grateful if you
continue this in future. Many people will be benefited
from your writing. Cheers!
I wanted to thank you for this wonderful read!! I certainly loved every bit of it.
I’ve got you book marked to check out new stuff you post…
This site was… how do I say it? Relevant!!
Finally I have found something which helped me. Thanks a lot!
I know this web page gives quality dependent articles or reviews and additional stuff, is there any other
website which presents these things in quality?
Pretty! This was an extremely wonderful article. Thanks
for supplying this information.
Hey There. I found your blog using msn. This is an extremely
well written article. I’ll be sure to bookmark it and come back to
read more of your useful information. Thanks for the post.
I will definitely return.
Hi, i believe that i saw you visited my website thus i came to return the want?.I’m trying to to find issues to enhance my
website!I suppose its ok to use some of your ideas!!
Hello! I just wanted to ask if you ever have any issues with hackers?
My last blog (wordpress) was hacked and I ended up losing months of
hard work due to no back up. Do you have any methods
to protect against hackers?
Hello there! This post could not be written any better! Reading
through this post reminds me of my good old room mate!
He always kept chatting about this. I will forward this write-up
to him. Fairly certain he will have a good read. Thanks
for sharing!
Feel free to visit my page :: Larimar Jewelry
This site definitely has all of the information and facts I wanted
concerning this subject and didn’t know who to ask.
I must thank you for the efforts you’ve put in penning this blog.
I really hope to see the same high-grade blog posts from you later on as well.
In truth, your creative writing abilities has motivated me to get my
own, personal site now 😉
We’re a group of volunteers and opening a
new scheme in our community. Your site provided us with
valuable info to work on. You have done a formidable
job and our whole community will be grateful to you.
Добро пожаловать на наш веб-сайт!
Здесь вы найдете все, что нужно для успешного управления вашими
финансами. Мы предлагаем широкий спектр финансовых продуктов, которые помогут
вам достичь ваших целей и обеспечить стабильность в будущем.
В нашем ассортименте есть разнообразные банковские продукты, инвестиции,
страхование, кредиты и многое
другое. Мы постоянно обновляем нашу базу
данных, чтобы вы всегда были в
курсе последних тенденций и инноваций на финансовом рынке.
Наши специалисты помогут вам
выбрать наиболее подходящий
продукт, учитывая ваши индивидуальные потребности и предпочтения.
Мы предоставляем консультации и рекомендации, чтобы вы могли принять обоснованное решение и избежать возможных рисков.
Не упустите возможность воспользоваться нашими услугами
и откройте для себя мир финансовых возможностей!
Посетите наш сайт, ознакомьтесь с каталогом продуктов и начните свой путь к финансовой стабильности прямо сейчас!
Joymoney в Киселёвске
Hello, the whole thing is going nicely here and
ofcourse every one is sharing facts, that’s truly good, keep up writing.
Feel free to visit my website :: Larimar Jewelry
Howdy! I could have sworn I’ve been to this blog before but after
checking through some of the post I realized it’s new to me.
Nonetheless, I’m definitely delighted I found it and I’ll be book-marking and checking back often!
my web page: Larimar Jewelry
I’ve been browsing online more than 2 hours today, yet I never found any interesting
article like yours. It is pretty worth enough for me. In my view, if all web owners and bloggers made
good content as you did, the net will be much more useful than ever before.
my site :: Larimar Jewelry
Hi, I do believe this is a great website. I stumbledupon it 😉 I’m going to
revisit once again since I book marked it. Money and freedom is the greatest way
to change, may you be rich and continue to help other people.
Incredible! This blog looks just like my old
one! It’s on a entirely different topic but it has pretty much the same page layout and design. Great choice of colors!
Woah! I’m really digging the template/theme of this site.
It’s simple, yet effective. A lot of times it’s challenging to
get that “perfect balance” between usability and appearance.
I must say you have done a awesome job with this. Additionally,
the blog loads very quick for me on Chrome. Excellent Blog!
I visited several web pages except the audio feature for audio songs present at
this web page is really fabulous.
all the time i used to read smaller content which
as well clear their motive, and that is also happening with this
article which I am reading at this time.
Attractive section of content. I just stumbled upon your web site and in accession capital
to assert that I acquire actually enjoyed account your blog posts.
Anyway I’ll be subscribing to your augment and even I
achievement you access consistently rapidly.
Informative article, exactly what I needed.
Also visit my site Larimar Jewelry
Excellent article. Keep writing such kind of information on your blog.
Im really impressed by it.
Hi there, You’ve done a fantastic job. I will certainly digg it and in my opinion recommend to my friends.
I’m sure they will be benefited from this site.
This is my first time pay a visit at here and i am genuinely pleassant to read all at one place.
My site – Larimar Jewelry
Hi, i read your blog from time to time and i own a similar
one and i was just wondering if you get a lot of spam
remarks? If so how do you prevent it, any plugin or anything you can recommend?
I get so much lately it’s driving me crazy so any help is very much appreciated.
Greetings I am so happy I found your blog page, I really found
you by accident, while I was searching on Digg for something else, Anyhow I
am here now and would just like to say cheers for a marvelous post and a all round exciting blog
(I also love the theme/design), I don’t have time to go through
it all at the minute but I have saved it and also added in your RSS feeds, so when I
have time I will be back to read more, Please do keep up the awesome work.
I don’t even know how I ended up here, but I thought this post was great.
I don’t know who you are but certainly you’re going
to a famous blogger if you are not already 😉 Cheers!
Wow, fantastic blog layout! How long have you been blogging for?
you make blogging look easy. The overall look
of your website is magnificent, let alone the content!
It’s a shame you don’t have a donate button! I’d definitely donate
to this excellent blog! I guess for now i’ll settle for bookmarking and adding your RSS
feed to my Google account. I look forward to fresh updates and will
talk about this site with my Facebook group. Talk soon!
My homepage :: Larimar Jewelry
Having read this I thought it was rather enlightening. I appreciate you finding the time and effort to put this article together. I once again find myself spending way too much time both reading and commenting. But so what, it was still worth it.
For the reason that the admin of this web site is working, no
hesitation very rapidly it will be famous, due to its feature contents.
Take a look at my web site :: Larimar Jewelry
Greetings! Very useful advice in this particular article! It is the little changes
that produce the most important changes. Many thanks
for sharing!
Look at my blog; Larimar Jewelry
I wanted to thank you for this fantastic read!!
I definitely loved every bit of it. I have you saved as a favorite
to look at new stuff you post…
Here is my blog :: Larimar Jewelry
I’m extremely impressed with your writing skills and also with the layout on your weblog.
Is this a paid theme or did you modify it yourself?
Anyway keep up the excellent quality writing, it’s rare to see a great
blog like this one these days.
Wow that was strange. I just wrote an really long comment but after I clicked submit my comment didn’t show up.
Grrrr… well I’m not writing all that over again. Anyhow, just wanted to say fantastic blog!
Here is my site: Larimar Jewelry
I blog often and I really appreciate your content. This great article has truly peaked my interest. I am going to book mark your site and keep checking for new information about once a week. I opted in for your RSS feed as well.
Hi all, here every one is sharing such knowledge, so it’s fastidious to read this web site, and I used to pay a quick visit this webpage
daily.
My blog post; Larimar Jewelry
I am not sure where you’re getting your information, but great topic.
I needs to spend some time learning much more or understanding more.
Thanks for excellent information I was looking for this info for my mission.
You explained that perfectly.
Its not my first time to pay a quick visit this website,
i am browsing this website dailly and take pleasant data from
here all the time.
Here is my blog :: Larimar Jewelry
It’s truly very complicated in this active life to listen news on TV, so I only use
the web for that purpose, and take the latest information.
My web-site Larimar Jewelry
Thank you for every other informative web site.
The place else could I get that type of information written in such an ideal approach?
I’ve a venture that I am simply now working on, and I have been at
the look out for such information.
My web page :: Larimar Jewelry
Wow, this article is fastidious, my younger sister is analyzing
such things, thus I am going to let know her.
Also visit my web page Larimar Jewelry
Pretty! This was a really wonderful post. Thank you for providing this
info.
My site – Larimar Jewelry
My brother recommended I might like this web site.
He was entirely right. This post truly made my day. You can not imagine just how much time I had spent for this information! Thanks!
Appreciating the dedication you put into your site
and detailed information you provide. It’s good to come across a blog
every once in a while that isn’t the same old rehashed information.
Wonderful read! I’ve saved your site and I’m including your RSS feeds to my Google account.
Hi there! Would you mind if I share your blog with my myspace group?
There’s a lot of folks that I think would really appreciate your content.
Please let me know. Cheers
You’re so interesting! I do not suppose I have read through anything like this before.
So wonderful to find someone with some genuine thoughts on this
issue. Really.. thanks for starting this up. This web site is something that is
required on the internet, someone with a bit of originality!
Also visit my web-site … Larimar Jewelry
Right away I am going to do my breakfast, once having my breakfast coming over again to read other news.
Feel free to surf to my site … Larimar Jewelry
I think this is one of the most important info for
me. And i am glad reading your article. But want to remark on some general things,
The site style is great, the articles is really great : D.
Good job, cheers
Here is my page; Larimar Jewelry
Thanks very interesting blog!
I could not resist commenting. Exceptionally well written!
Very great post. I just stumbled upon your weblog and wanted
to say that I have truly enjoyed browsing your blog posts.
In any case I will be subscribing to your feed and I’m hoping
you write once more very soon!
Here is my web page: kontraktor bangun rumah jogja
Greetings! Very useful advice in this particular
post! It’s the little changes that will make the most important
changes. Many thanks for sharing!
Wow, this article is nice, my sister is analyzing these kinds of things, therefore I am going to let know her.
I’m not that much of a internet reader to be honest but your blogs really nice,
keep it up! I’ll go ahead and bookmark your website
to come back later. All the best
Here is my blog :: Larimar Jewelry
Very good post. I am dealing with some of these issues
as well..
I know this site provides quality dependent content and additional information, is there any other web site which
provides these things in quality?
Its like you read my mind! You seem to know a lot about this, like
you wrote the book in it or something. I think that you can do with a few pics to drive the message
home a bit, but instead of that, this is excellent blog.
An excellent read. I will definitely be back.
Also visit my page – Larimar Jewelry
Hello there! I know this is kinda off topic however , I’d figured I’d ask.
Would you be interested in exchanging links or maybe guest writing a blog article or vice-versa?
My website goes over a lot of the same subjects as
yours and I feel we could greatly benefit from each other.
If you happen to be interested feel free to shoot me an email.
I look forward to hearing from you! Superb blog by the way!
I think this is one of the most vital info for me. And i’m glad reading your article.
But should remark on few general things, The website style is wonderful,
the articles is really nice : D. Good job, cheers
Incredible quite a lot of wonderful tips!
I don’t even know how I ended up here, but I thought this post was great.
I do not know who you are but certainly you are going to a famous blogger if you aren’t already 😉 Cheers!
My webpage: Larimar Jewelry
Что именно отличает дисплеи iPhone
15 и iPhone 15 Plus от их предшественников?
| В чём особенности экранов iPhone
15 и iPhone 15 Plus по сравнению с предыдущими
моделями? | Чем iPhone 15 и iPhone 15 Plus выделяются
в плане дисплея от ранних версий ?
Во-первых, рекордная пиковая яркость
до 2000 кд/м² , что делает использование смартфона
при ярком солнечном свете .
По мнению Дэна, возникает сомнение, насколько долго устройство
сможет поддерживать максимальной яркости, прежде чем произойдёт её снижение .
Подобное фиксировалось ранее, например, с iPhone 13 Pro . https://macuser.ua/search?word=apple+region+ru+%D0%BE%D1%82%D0%B7%D1%8B%D0%B2%D1%8B+%D0%BB%D0%B5%D1%84%D0%BE%D1%80%D1%82%D0%BE%D0%B2%D0%BE
Hey! I could have sworn I’ve been to this website before but
after browsing through some of the post I realized it’s new
to me. Anyhow, I’m definitely happy I found it and I’ll be
book-marking and checking back often!
Hey there just wanted to give you a quick heads up.
The words in your content seem to be running off the screen in Chrome.
I’m not sure if this is a format issue or something
to do with browser compatibility but I figured I’d post
to let you know. The layout look great though! Hope you get the problem fixed soon. Cheers
Here is my blog … Larimar Jewelry
игры с модами на андроид — это удивительная возможность расширить функциональность игры.
Особенно если вы играете на мобильном устройстве с Android, модификации открывают перед вами
огромный выбор. Я нравится использовать взломанные игры, чтобы достигать большего.
Моды для игр дают невероятную свободу выбора, что взаимодействие с игрой гораздо увлекательнее.
Играя с плагинами, я могу создать новый игровой процесс, что добавляет новые приключения и делает игру более эксклюзивной.
Это действительно интересно, как такие модификации могут улучшить игровой процесс,
а при этом сохраняя использовать такие игры
с изменениями можно без особых неприятных последствий, если быть внимательным и следить
за обновлениями. Это делает каждый игровой процесс уникальным,
а возможности практически бесконечные.
Советую попробовать такие игры с модами для Android
— это может придаст новый смысл
Awesome! Its actually remarkable article, I have got much clear idea regarding from this post.
Hello my loved one! I want to say that this article
is amazing, great written and include almost all significant infos.
I would like to look extra posts like this .
Hi, just wanted to say, I enjoyed this post. It was inspiring.
Keep on posting!
If some one wishes to be updated with latest technologies afterward
he must be go to see this site and be up to
date daily.
An impressive share! I have just forwarded this onto a co-worker who
had been doing a little research on this. And he actually ordered me
dinner because I stumbled upon it for him…
lol. So let me reword this…. Thanks for the meal!!
But yeah, thanks for spending some time to discuss this issue here on your internet site.
Woah! I’m really loving the template/theme of this website.
It’s simple, yet effective. A lot of times it’s tough to get that “perfect balance” between usability and appearance.
I must say you have done a great job with this. Also, the blog
loads extremely quick for me on Safari. Exceptional Blog!
Asking questions are genuinely fastidious thing if you are not understanding something
entirely, except this piece of writing presents nice understanding yet.
Here is my site 해외선물 대여계좌
I do not know if it’s just me or if perhaps everybody
else experiencing issues with your blog. It appears as if some of the
written text in your content are running off the screen.
Can someone else please provide feedback and let me know if this is happening to them too?
This could be a problem with my web browser
because I’ve had this happen before. Thanks
Attractive element of content. I simply stumbled upon your web site and in accession capital to claim
that I acquire actually enjoyed account your weblog
posts. Anyway I’ll be subscribing for your augment
or even I fulfillment you get admission to constantly fast.
Good article. I am going through a few of these issues as well..
Here is my site: dépannage fuite toiture
Hi every one, here every person is sharing these kinds psychology of digital advertising know-how, so it’s good to read this weblog, and I used to pay
a visit this website all the time.
Greetings I am so delighted I found your weblog, I really found you by mistake, while I was researching on Yahoo for something else, Nonetheless
I am here now and would just like to say thanks
for a fantastic post and a all round entertaining blog (I
also love the theme/design), I don’t have time to go through it all at the
minute but I have book-marked it and also added
your RSS feeds, so when I have time I will be back to read a great deal
more, Please do keep up the excellent b.
It is really a great and helpful piece of information. I’m happy that you just shared this useful information with us.
Please keep us up to date like this. Thanks for
sharing.
Nice weblog here! Also your web site rather a lot up very fast!
What host are you the use of? Can I am getting your associate
link for your host? I wish my site loaded up as fast as yours lol
Thank you, I’ve just been searching for information about
this subject for a while and yours is the greatest I have found out till now.
However, what concerning the bottom line? Are you sure about the source?
my page; เช่าชุดเจ้าสาว
Keep this going please, great job!
Feel free to visit my page – best real estate agent in Fort Myers FL
Howdy, I do believe your site could possibly be having browser compatibility
issues. Whenever I take a look at your site in Safari, it looks fine but when opening in I.E., it has
some overlapping issues. I just wanted to give
you a quick heads up! Besides that, wonderful
site!
Also visit my web site :: nettoyage toiture prix
Just desire to say your article is as astounding. The clarity to your put up is just cool and i can suppose you’re an expert on this subject.
Well with your permission let me to grasp your feed to keep
updated with impending post. Thank you 1,000,
000 and please carry on the enjoyable work.
Visit my web page: 해외선물 안전업체
The other day, while I was at work, my sister stole my iphone and tested
to see if it can survive a 30 foot drop, just so she can be a youtube sensation. My iPad is now broken and she has 83 views.
I know this is entirely off topic but I had to share it with someone!
I don’t even know how I ended up here, but I thought this post was great.
I do not know who you are but certainly you’re going to a
famous blogger if you are not already 😉 Cheers!
Please let me know if you’re looking for a article author
for your site. You have some really good posts and I feel I
would be a good asset. If you ever want to take some of the load off, I’d
absolutely love to write some articles for your blog in exchange for a link back
to mine. Please send me an e-mail if interested. Kudos!
I am really pleased to read this webpage posts which consists of tons of helpful
facts, thanks for providing these information.
Also visit my blog post; best realtor in Fort Myers FL
I am really glad to glance at this blog posts which consists of plenty of helpful data, thanks for providing
such statistics.
Review my web site :: 해외선물 실계좌
Its like you read my mind! You seem to know a lot about this, like you wrote the
book in it or something. I think that you can do with some pics to
drive the message home a little bit, but other than that, this
is magnificent blog. An excellent read. I will certainly be back.
Hello, There’s no doubt that your web site may
be having browser compatibility issues. Whenever I take
a look at your web site in Safari, it looks fine however,
when opening in IE, it’s got some overlapping issues.
I merely wanted to give you a quick heads up! Aside from that, great website!
Review my webpage: real estate agent Fort Myers FL
Hi there, You’ve done an excellent job. I’ll definitely digg it and personally recommend to
my friends. I’m confident they’ll be benefited from this site.
Usually I don’t read post on blogs, however I would like to say that this
write-up very pressured me to take a look at and do
so! Your writing taste has been amazed me.
Thanks, quite great article.
Feel free to visit my webpage; real estate agent Fort Myers FL
This blog was… how do you say it? Relevant!! Finally I have found something that helped me.
Thanks a lot!
First off I want to say superb blog! I had a quick question which I’d like to ask if you don’t mind.
I was interested to find out how you center yourself and clear your head prior to writing.
I have had a difficult time clearing my thoughts in getting
my ideas out. I truly do enjoy writing however it just
seems like the first 10 to 15 minutes are generally lost simply
just trying to figure out how to begin. Any suggestions or tips?
Appreciate it!
What’s up to all, it’s in fact a pleasant for me to go to see this web page, it
contains priceless Information.
Do you have any video of that? I’d care to find out some additional
information.
When I originally commented I seem to have clicked on the
-Notify me when new comments are added- checkbox
and now every time a comment is added I receive 4 emails with the exact same comment.
There has to be an easy method you are able to remove me from that service?
Kudos!
Effectively spoken really! .
My web page :: https://benlola.com/cs/jak-prejit-k-nove-marketingove-agenture/
I constantly emailed this blog post page to all my friends, as if like to
read it after that my contacts will too.
When I originally commented I seem to have clicked on the -Notify me when new comments are added-
checkbox and from now on each time a comment is added I receive four
emails with the exact same comment. Perhaps there is a means
you are able to remove me from that service? Appreciate it!
My brother recommended I would possibly like this
website. He used to be totally right. This publish actually made my day.
You cann’t imagine simply how much time I had spent for this info!
Thanks!
Simply desire to say your article is as amazing.
The clarity in your post is simply cool and i can assume you are an expert on this subject.
Well with your permission allow me to grab your feed to keep up to date
with forthcoming post. Thanks a million and please
keep up the gratifying work.
I just like the valuable information you supply in your articles.
I will bookmark your blog and take a look at once
more here frequently. I’m moderately certain I will be
informed many new stuff proper right here! Best of luck for the next!
Saved as a favorite, I love your web site!
Что же отличает экраны iPhone 15 и iPhone 15 Plus от своих предшественников?
| В чём отличия экранов iPhone 15 и iPhone 15 Plus по сравнению с
предыдущими моделями? | Чем iPhone 15 и iPhone 15 Plus отличаются в плане дисплея от ранних версий
?
Во-первых, повышенная пиковая яркость до целых 2000 нит,
что облегчает эксплуатацию смартфона
при днём на улице.
По мнению Дэна, возникает сомнение, сколько времени устройство сможет работать на максимальной
яркости, прежде чем она снизится резко.
Подобное фиксировалось ранее, например,
с моделями iPhone 13 Pro . https://macuser.ua/search?word=%D0%BC%D0%B0%D1%80%D0%BA%D0%B5%D1%82+%D1%80%D1%83+%D1%80%D1%83+%D0%B0%D1%80%D0%B1%D0%B0%D1%82
I was extremely pleased to find this website.
I want to to thank you for ones time for this wonderful read!!
I definitely loved every bit of it and i also have you book-marked to check out new
things on your website.
Here is my page – situs serok188
What’s up, its good piece of writing on the topic
of media print, we all understand media is a fantastic
source of information.
Hey would you mind letting me know which webhost you’re working with?
I’ve loaded your blog in 3 completely different browsers and I must say this blog
loads a lot faster then most. Can you suggest a good hosting provider at a reasonable price?
Thanks a lot, I appreciate it!
Hi, i think that i saw you visited my website
so i came to “return the favor”.I am attempting to find things to improve my site!I suppose
its ok to use a few of your ideas!!
This design is wicked! You most certainly know how to keep a reader entertained.
Between your wit and your videos, I was almost moved to
start my own blog (well, almost…HaHa!) Excellent job.
I really loved what you had to say, and more than that, how you presented it.
Too cool!
These are in fact fantastic ideas in regarding blogging.
You have touched some pleasant points here. Any way keep up wrinting.
You actually said that perfectly.
Great post. I was checking constantly this blog and I am impressed!
Very helpful information specially the last part 🙂 I care for such info much.
I was seeking this certain information for a very long time.
Thank you and best of luck.
WOW juѕt what I ѡaѕ searching fοr. Cаmе here by searching for Online betting Tips
Thanks! A good amount of content.
What’s up friends, nice article and fastidious
arguments commented at this place, I am really enjoying by these.
After I originally commented I appear to have clicked on the -Notify me when new comments are added- checkbox and
from now on whenever a comment is added I receive four emails
with the same comment. Perhaps there is a way you are able to remove me
from that service? Appreciate it!
I constantly spent my half an hour to read this blog’s articles or reviews everyday along with a cup
of coffee.
Great post. I’m going through some of these issues as well..
Nice weblog here! Additionally your web site rather
a lot up very fast! What host are you the use of? Can I get your
affiliate hyperlink on your host? I want my web site loaded up as fast as yours lol
You ought to be a part of a contest for one of the best sites
on the web. I most certainly will recommend this blog!
Saved as a favorite, I love your blog!
Also visit my web page :: หวยฮานอย วันนี้
What a material of un-ambiguity and preserveness of valuable experience on the topic of unpredicted emotions.
My spouse and I stumbled over here coming from a different
web page and thought I should check things out. I like what I see so now i am
following you. Look forward to finding out about your web page
for a second time.
I don’t even know how I ended up here, but I thought this post was good.
I don’t know who you are but certainly you’re going to a famous blogger if you are not already 😉
Cheers!
I do trust all the ideas you’ve introduced to your post.
They are really convincing and will definitely work.
Nonetheless, the posts are very quick for newbies. May you please lengthen them a bit from subsequent time?
Thank you for the post.
Valuable information. Lucky me I discovered your site by accident, and I’m shocked why this twist of fate did not took
place in advance! I bookmarked it.
Every weekend i used to pay a quick visit this site,
as i want enjoyment, since this this web page conations truly nice funny material too.
In NBA 2K12, to trade legends on your team, navigate to the “My Player” or “Association” mode.
Access the trade menu by selecting the team y
Read more
NBA Live
How do you change the language in NBA 2k11?
Asked by Anonymous
To change the language in NBA 2K11, go to the main menu and select “Options.” From there, navigate to “Settings,” where you’ll find the &quo
Read more
Sports Video Games
+1
How do self alley opp nba 2k13 psp?
Asked by Anonymous
Honey, I don’t know if you’re trying to speak in code or
if autocorrect had a field day with your question. If you’re asking how to
perform a self alley-oop in
Read more
NBA Live
How do you unlock NBA 2k12 classic NBA teams?
Asked by Anonymous
Oh, dude, unlocking classic NBA teams in NBA 2K12 is like finding a hidden treasure chest in a video game.
You gotta complete certain challenges or reach specif
Read more
NBA Live
What are the controls for nba 2k13 on the wii?
Asked by Anonymous
Oh, dude, to shoot the ball in NBA 2K13 on the Wii, you just press the B button. If you want to pass,
you use the A button. And if you feel like sprinting down
Read more
NBA Live
Can you use created players in the association mode on nba 2k11 on psp and how?
Asked by Anonymous
Oh, dude, absolutely! In NBA 2K11 on PSP, you can totally use
created players in Association Mode. All you gotta do is go to
the main menu, select Association,
Read more
NBA Live
How do you get in the dunk contest or 3 point shoot out in nba 2k
13?
Asked by Anonymous
NBA Live
What is the theme song for NBA Live 97 on the PSX?
Asked by Anonymous
NBA Live
How do you perform a super dunk in nba ballers chosen one?
Asked by Anonymous
Units of Measure
+3
Does a burnt match weigh the same as a live match?
Asked by Anonymous
No, a burnt match will weigh less than a live match because some of the material has been burned off and turned into smoke
and ash.
Wow, marvelous blog format! How long have you been running
a blog for? you made blogging look easy. The total look of your site is fantastic, as neatly as the content material!
Detta är en trygghet som casinon utan svensk licens inte kan erbjuda, vilket är anledningen till att vi alltid rekommenderar att välja nätcasinon med svensk spellicens.
Excellent post but I was wondering if you could write a litte more
on this topic? I’d be very grateful if you could elaborate
a little bit more. Thank you!
I’m amazed, I have to admit. Rarely do I encounter a blog that’s both equally educative and amusing, and without a doubt, you have hit the nail on the head.
The issue is something not enough folks are speaking intelligently about.
I’m very happy that I came across this during my search for something concerning this.
Hi, Neat post. There is a problem with your website in internet explorer,
could check this? IE still is the market chief and a big
part of people will pass over your magnificent writing because of this
problem.
When I initially commented I clicked the “Notify me when new comments are added” checkbox and now each time a comment is added I get three emails with the same comment.
Is there any way you can remove me from that service?
Thank you!
Hey there would you mind letting me know which webhost
you’re working with? I’ve loaded your blog in 3 different internet browsers and I must say this blog loads a lot faster then most.
Can you recommend a good web hosting provider at a reasonable price?
Cheers, I appreciate it!
I pay a visit every day a few web pages and sites to read content, however this weblog presents feature based
content.
I have been surfing online more than 2 hours today, yet I never found any interesting article like yours.
It is pretty worth enough for me. In my opinion, if all website
owners and bloggers made good content as you did, the internet
will be a lot more useful than ever before.
Howdy! I know this is kinda off topic however I’d figured I’d ask.
Would you be interested in exchanging links or maybe
guest authoring a blog article or vice-versa? My website discusses a
lot of the same topics as yours and I feel we could greatly benefit from each other.
If you are interested feel free to send me an email.
I look forward to hearing from you! Fantastic blog by the way!
If you want to increase your familiarity only keep visiting
this web site and be updated with the hottest information posted here.
If some one desires expert view regarding
blogging after that i advise him/her to visit this web site, Keep up the good work.
Feel free to visit my web-site: realtor in Fort Myers FL
Woah! I’m really enjoying the template/theme of this
website. It’s simple, yet effective. A lot of times it’s difficult
to get that “perfect balance” between superb usability and
appearance. I must say you have done a superb job with this.
In addition, the blog loads very fast for me on Safari.
Exceptional Blog!
Here is my site – real estate agent Fort Myers FL
I have read several excellent stuff here. Certainly worth bookmarking for revisiting.
I surprise how much effort you place to create this type of fantastic informative site.
I am sure this paragraph has touched all the internet
visitors, its really really fastidious paragraph on building up new web
site.
Excellent post. Keep writing such kind of info on your page.
Im really impressed by it.
Hello there, You have performed an excellent job. I’ll certainly
digg it and individually recommend to my friends.
I am confident they will be benefited from this site.
That is really attention-grabbing, You are an excessively skilled blogger.
I have joined your rss feed and sit up for in quest of more of your magnificent post.
Additionally, I have shared your site in my social networks
Currently it seems like Drupal is the best blogging platform available right now.
(from what I’ve read) Is that what you’re using on your blog?
Ideally, you should look for products that have herbal ingredients in them as
opposed to the ones filled with chemical ingredients.
Today, I went to the beachfront with my kids.
I found a sea shell and gave it to my 4 year old
daughter and said “You can hear the ocean if you put this to your ear.”
She placed the shell to her ear and screamed. There was a hermit crab inside and it pinched her ear.
She never wants to go back! LoL I know this is completely off topic but I had to
tell someone!
I love what you guys are up too. Such clever work and exposure!
Keep up the fantastic works guys I’ve you guys to my own blogroll.
Every weekend i used to go to see this web page, because i want
enjoyment, since this this web site conations in fact good funny material too.
What i don’t realize is in fact how you are no longer actually a lot more neatly-liked than you might be right now.
You’re so intelligent. You know thus considerably when it comes to
this matter, produced me individually believe it
from so many various angles. Its like men and women don’t seem to be involved except it’s something to accomplish with Girl gaga!
Your own stuffs excellent. Always care for it up!
It’s an amazing paragraph designed for all the online people; they will get
advantage from it I am sure.
It’s an awesome paragraph in favor of all the web viewers; they will
get advantage from it I am sure.
Way cool! Some very valid points! I appreciate you penning this write-up and the rest of the website is
also really good.
http://wish-club.ru/forums/index.php?autocom=gallery&req=si&img=5298
I don’t even know how I ended up here, but I thought this
post was great. I don’t know who you are but definitely you
are going to a famous blogger if you aren’t already ;
) Cheers!
Very good stuff, Thank you!
my web-site :: https://www.gamblingcity.net/it/recensioni-di-casino/888-casino.php
Hello there! This is my first comment here so I just wanted
to give a quick shout out and tell you I really enjoy reading your posts.
Can you suggest any other blogs/websites/forums that go over the
same topics? Thanks for your time!
I must thank you for the efforts you’ve put in writing this site.
I am hoping to see the same high-grade blog posts from you later
on as well. In truth, your creative writing abilities
has encouraged me to get my own blog now 😉
Hello colleagues, pleasant paragraph and fastidious
urging commented at this place, I am genuinely enjoying by these.
Hi, I do think this is an excellent website. I stumbledupon it 😉 I will
come back yet again since I bookmarked it. Money and freedom is the greatest way to change, may you be rich and continue to guide other people.
Definitely believe that which you said. Your favorite justification seemed to be on the web the easiest thing to be aware of.
I say to you, I definitely get annoyed while people
think about worries that they plainly do not know about.
You managed to hit the nail upon the top and also defined out the whole thing without having side effect
, people can take a signal. Will probably be back to get more.
Thanks
continuously i used to read smaller content that as
well clear their motive, and that is also happening with this article
which I am reading at this place.
I am sure this post has touched all the internet people,
its really really good paragraph on building up new weblog.
I’ve read a few excellent stuff here. Certainly value
bookmarking for revisiting. I surprise how much effort
you put to make one of these wonderful informative website.
Hi! This is my first visit to your blog! We are a group of volunteers and starting a new initiative in a community in the
same niche. Your blog provided us beneficial information to
work on. You have done a outstanding job!
Heya i am for the first time here. I found this board and I to
find It truly useful & it helped me out a lot. I hope to give something back and help others such as you helped me.
You can have the products with same brand on the net that you will find
at your local vet’s store.
Menarik tulisannya, bro! Kalau cari slot gacor, wajib cek viartoto.
Gue udah dapet mega win dari Slot 888, apalagi pas pake teknik bajak scatter manual.
Katanya juga mirip kayak yang sering dimainin di slot
Raffi Ahmad.
Hi, I do think your website may be having web browser compatibility issues.
Whenever I look at your site in Safari, it looks fine however, when opening in I.E., it has some
overlapping issues. I merely wanted to give you
a quick heads up! Besides that, great blog!
If you wish for to improve your experience simply keep visiting this website and be updated with the most recent news posted
here.
At this time it appears like Movable Type is the preferred blogging platform out there right now.
(from what I’ve read) Is that what you’re using on your blog?
My partner and I absolutely love your blog and find nearly all of your post’s to be just what I’m looking for.
can you offer guest writers to write content for yourself?
I wouldn’t mind producing a post or elaborating on a lot of the subjects you
write concerning here. Again, awesome site!
If some one wants expert view on the topic of running a blog afterward i advise him/her to
pay a visit this web site, Keep up the pleasant work.
Cheers! Numerous tips.
I savor, lead to I discovered just what I was looking for.
You’ve ended my 4 day long hunt! God Bless you man. Have a nice day.
Bye
Unquestionably believe that which you said.
Your favorite reason seemed to be on the web the easiest
thing to be aware of. I say to you, I certainly get irked while people consider worries that they plainly don’t know about.
You managed to hit the nail upon the top and also defined
out the whole thing without having side effect , people can take
a signal. Will likely be back to get more. Thanks
Hello, its good article concerning media print,
we all know media is a enormous source of facts.
This blog was… how do you say it? Relevant!!
Finally I have found something which helped me.
Appreciate it!
My blog nordvpn coupons Inspiresensation
Wow, incredible weblog format! How long have you ever been running
a blog for? you make running a blog look easy. The whole look of your site is
magnificent, let alone the content!
Also visit my blog :: login serok188
Because the admin of this web page is working, no hesitation very soon it
will be renowned, due to its feature contents.
https://myteana.ru/forums/index.php?autocom=gallery&req=si&img=6670
It’s a shame you don’t have a donate button!
I’d certainly donate to this fantastic blog! I suppose for now i’ll settle for book-marking and adding your
RSS feed to my Google account. I look forward to new updates and will talk about this site with my Facebook
group. Talk soon!
What’s up, yeah this paragraph is truly pleasant and I have learned lot of things from it
concerning blogging. thanks.
I know this web page provides quality depending content and other
information, is there any other site which offers such stuff in quality?
What i do not understood is in reality how you’re not really much more smartly-liked than you might be right now.
You’re so intelligent. You realize therefore considerably
relating to this subject, produced me for my part
consider it from numerous varied angles. Its like women and men don’t seem to be fascinated unless it is something to
accomplish with Girl gaga! Your personal stuffs
outstanding. At all times deal with it up!
Thanks for sharing your thoughts about Crocs
Deutschland. Regards
Hey there, I think your website might be having browser compatibility issues.
When I look at your blog site in Ie, it looks fine but when opening in Internet
Explorer, it has some overlapping. I just wanted to give you
a quick heads up! Other then that, wonderful blog!
After looking at a number of the blog articles on your blog,
I seriously appreciate your way of writing a blog.
I saved it to my bookmark webpage list and will be checking back soon. Take a look at my website too and tell
me your opinion.
I’m truly enjoying the design and layout of your site. It’s a very easy on the eyes which
makes it much more enjoyable for me to come here and visit more
often. Did you hire out a designer to create your theme?
Excellent work!
Wow, fantastic weblog layout! How lengthy have you been running a blog for?
you make running a blog glance easy. The total glance of your site is excellent, let alone the content material!
Hi my loved one! I want to say that this post is amazing, great written and come with approximately all important
infos. I’d like to look extra posts like this .
Hey there this is somewhat of off topic but I was wondering if
blogs use WYSIWYG editors or if you have to manually code with HTML.
I’m starting a blog soon but have no coding experience so I wanted to get guidance from someone with experience.
Any help would be enormously appreciated!
you are really a just right webmaster. The site loading
velocity is incredible. It kind of feels that you are doing any unique trick.
Furthermore, The contents are masterwork. you’ve performed
a great job in this subject!
Great post.
Its such as you learn my thoughts! You seem to know a lot approximately this, like you wrote the e-book
in it or something. I feel that you can do with a few percent to pressure the message home a
little bit, but instead of that, this is wonderful blog. A
fantastic read. I’ll definitely be back.
Look into my website – slot
Appreciate it. A lot of data.
This is nicely said! ! http://planforexams.com/q2a/user/grousepencil71
whoah this weblog is magnificent i really like studying your posts.
Keep up the good work! You realize, many people are looking round for this information, you could aid
them greatly.
excellent post, very informative. I wonder why the other experts of this
sector do not realize this. You should continue your writing.
I am confident, you have a huge readers’ base already!
Hello this is kind of of off topic but I was wanting to know if blogs use WYSIWYG editors or if you have to manually code with HTML.
I’m starting a blog soon but have no coding skills so I wanted to get guidance from someone with experience.
Any help would be greatly appreciated!
each time i used to read smaller articles that as well clear their
motive, and that is also happening with this piece of writing which I am reading now.
Hey there great website! Does running a blog like this require a lot of work?
I have virtually no knowledge of programming but I had been hoping to start my own blog soon.
Anyhow, should you have any recommendations or tips for new
blog owners please share. I understand this is off subject but I just had to ask.
Thanks!
I visited various websites except the audio quality for audio songs present at
this web page is really excellent.
With havin so much content do you ever run into any issues of plagorism
or copyright infringement? My blog has a lot of exclusive content I’ve either
authored myself or outsourced but it seems a lot of
it is popping it up all over the web without my permission. Do you know any ways
to help prevent content from being ripped off?
I’d definitely appreciate it.
I read this paragraph fully on the topic of the resemblance of newest and preceding technologies, it’s awesome article.
How To Get Free And Unlimited Tokens On XHamster Live
in an easy and real way – Xhamster Mod 2025 Android & ios
This method has been tried by tens of thousands of visitors and still
works today.
I am really thankful to the holder of this site who has
shared this enormous paragraph at at this place.
Very quickly this web page will be famous amid all blog
users, due to it’s good articles
Appreciate it. Ample facts!
https://www.walkscore.com/people/177947383850/jili-slot
I read this piece of writing fully concerning the difference
of most up-to-date and preceding technologies, it’s awesome article.
Hello there! Would you mind if I share your blog with
my zynga group? There’s a lot of folks that I think would really
enjoy your content. Please let me know. Thank you
Hi would you mind letting me know which web host you’re using?
I’ve loaded your blog in 3 completely different browsers and I must say
this blog loads a lot faster then most. Can you recommend
a good hosting provider at a honest price? Cheers, I appreciate
it!
I will immediately clutch your rss feed as I can not to find
your e-mail subscription hyperlink or newsletter service.
Do you have any? Please permit me know in order
that I may subscribe. Thanks.
Wonderful blog! I found it while browsing on Yahoo News.
Do you have any suggestions on how to get listed in Yahoo News?
I’ve been trying for a while but I never seem to get there!
Cheers
Link exchange is nothing else except it is simply placing the other
person’s website link on your page at proper place and other person will also do same in favor of you.
Hello, this weekend is nice in support of me, for the reason that this point in time i am
reading this enormous informative paragraph here at my house.
I constantly spent my half an hour to read this web site’s articles everyday along with a
cup of coffee.
Fantastic beat ! I wish to apprentice while you amend your website,
how could i subscribe for a blog website? The account helped me a acceptable deal.
I had been a little bit acquainted of this your broadcast offered bright
clear idea
Hmm is anyone else encountering problems with the images on this blog loading?
I’m trying to find out if its a problem on my end or if it’s the blog.
Any responses would be greatly appreciated.
Hey are using WordPress for your blog platform?
I’m new to the blog world but I’m trying to get started
and set up my own. Do you require any html coding knowledge to make your own blog?
Any help would be greatly appreciated!
That is a good tip particularly to those new to the blogosphere. Short but very accurate information… Thank you for sharing this one. A must read article.
Hey very cool website!! Man .. Beautiful ..
Amazing .. I’ll bookmark your website and take the feeds additionally?
I’m happy to search out numerous helpful info here within the post,
we’d like work out more techniques in this regard, thanks for sharing.
. . . . .
Hmm is anyone else experiencing problems with the images on this
blog loading? I’m trying to find out if its a problem on my end or
if it’s the blog. Any suggestions would be greatly appreciated.
I think this is one of the most important info for me.
And i’m glad reading your article. But want to remark
on few general things, The web site style is
ideal, the articles is really nice : D. Good job, cheers
Why viewers still make use of to read news papers when in this technological globe everything is existing
on net?
Incredible tons of amazing facts.
At this time it sounds like WordPress is the preferred blogging platform
available right now. (from what I’ve read) Is that what you’re using on your blog?
I’m not sure why but this site is loading extremely slow for
me. Is anyone else having this issue or is it a problem on my end?
I’ll check back later and see if the problem still exists.
I enjoy what you guys tend to be up too. This type of clever work and reporting!
Keep up the excellent works guys I’ve added you guys to our blogroll.
This post is really a fastidious one it assists new the web users, who are wishing in favor
of blogging.
Generally I do not learn article on blogs, however I would like to say that this write-up very compelled me to check out and do
it! Your writing taste has been surprised me. Thanks, very great article.
My spouse and I stumbled over here from a different page and
thought I might as well check things out.
I like what I see so i am just following you.
Look forward to going over your web page yet again.
Outstanding post however I was wanting to know if you could write a
litte more on this subject? I’d be very grateful if you could elaborate a
little bit more. Many thanks!
Feel free to surf to my blog post – web page
It’s perfect time to make a few plans for the longer term
and it is time to be happy. I’ve read this post and if I may I desire to counsel you some interesting things or tips.
Perhaps you can write subsequent articles relating to this
article. I want to read even more things about it!
What’s Going down i am new to this, I stumbled upon this I’ve discovered It
absolutely useful and it has aided me out loads. I’m hoping to give a contribution & help different customers like its helped me.
Good job.
Hmm is anyone else experiencing problems with the images on this blog loading?
I’m trying to find out if its a problem on my end or if it’s the blog.
Any feedback would be greatly appreciated.
Good replies in return of this query with solid arguments and explaining the whole thing regarding that.
Nice blog here! Also your site loads up very fast! What web host are you using?
Can I get your affiliate link to your host?
I wish my site loaded up as fast as yours lol
After exploring a number of the blog articles on your blog, I
honestly appreciate your way of blogging.
I saved as a favorite it to my bookmark webpage list and will
be checking back soon. Please check out my website too and tell me how you feel.
I think that everything said was actually very reasonable.
But, think on this, suppose you added a little content?
I am not saying your information is not solid, however what if you added a title that
makes people desire more? I mean SMI diamond grinding wheels is kinda boring.
You could look at Yahoo’s home page and see how they create post headlines to get people interested.
You might try adding a video or a related picture or two to grab readers interested about what you’ve got to say.
In my opinion, it could make your website a little bit
more interesting.
Hi, i think that i saw you visited my site thus i got here to go back the favor?.I’m attempting to in finding issues to improve my web site!I guess its ok to make use
of a few of your ideas!!
Hmm is anyone else having problems with the images on this blog loading?
I’m trying to figure out if its a problem on my end or if it’s the
blog. Any responses would be greatly appreciated.
Way cool! Some extremely valid points! I appreciate
you writing this post and also the rest of the website is also really good.
Excellent way of telling, and fastidious article to obtain facts
concerning my presentation focus, which i am going to convey in school.
I’m not that much of a internet reader to be honest but your blogs really nice,
keep it up! I’ll go ahead and bookmark your site to come
back later on. Cheers
We’re a group of volunteers and starting a new scheme in our community.
Your site provided us with valuable info to work on. You’ve
done a formidable job and our entire community will be grateful to you.
Link exchange is nothing else except it is only placing the other
person’s webpage link on your page at proper place
and other person will also do similar in favor of you.
Link exchange is nothing else but it is just placing the other person’s webpage link on your page at suitable
place and other person will also do similar
in support of you.
Hey there! Do you know if they make any plugins to protect against hackers?
I’m kinda paranoid about losing everything I’ve worked hard
on. Any recommendations?
Hi! I’m at work browsing your blog from my new iphone!
Just wanted to say I love reading your blog and look forward to all your posts!
Carry on the outstanding work!
magnificent post, very informative. I wonder why the other experts of this sector don’t notice this.
You should continue your writing. I’m confident, you have a huge
readers’ base already!
I’ve been browsing on-line greater than 3 hours these days,
yet I by no means found any attention-grabbing article like yours.
It is lovely price sufficient for me. In my opinion, if all webmasters and bloggers made good
content material as you did, the internet might be a lot more helpful than ever before.
I know this if off topic but I’m looking into starting my own blog
and was curious what all is required to get set up? I’m assuming having a blog like yours would cost a pretty
penny? I’m not very internet savvy so I’m not 100% positive.
Any suggestions or advice would be greatly appreciated.
Appreciate it
Hey guys today I’m gonna show you how to get Blacked
membership 2025 this is insane.Join our vip membership to get latest & working blacked
accounts as well collection of porn passwords and login access to thousands other
xxx paysites.
I enjoy, lead to I discovered just what I used to be taking a look
for. You’ve ended my 4 day long hunt! God Bless you man. Have
a nice day. Bye
Administered orally approximately 30-60 minutes before sexual exercise, Viagra Connect
provides immediate onset of motion and adaptability in timing, enabling spontaneity and enhancing sexual confidence.
I do not even know how I ended up here, but I assumed this post was good.
I do not recognise who you might be however certainly you are going to a well-known blogger for those who aren’t already.
Cheers!
I go to see day-to-day some web sites and sites to read content,
except this blog provides feature based content.
I’m not that much of a online reader to be honest but your sites really nice, keep it up!
I’ll go ahead and bookmark your website to come back later.
All the best
Magnificent web site. A lot of useful information here.
I’m sending it to a few friends ans also sharing in delicious.
And naturally, thanks in your effort!
What’s up, just wanted to mention, I liked this
post. It was inspiring. Keep on posting!
Great article, exactly what I wanted to find.
Way cool! Some very valid points! I appreciate you writing this write-up plus
the rest of the website is really good.
Hi there to all, the contents existing at this web site are truly awesome for people knowledge,
well, keep up the nice work fellows.
I am curious to find out what blog platform you happen to be working
with? I’m having some small security issues
with my latest site and I would like to find something more secure.
Do you have any suggestions?
Its like you read my mind! You appear to know a lot about
this, like you wrote the book in it or something. I think that you can do with
a few pics to drive the message home a bit, but instead of that, this is excellent
blog. A fantastic read. I will definitely be back.
скачать модифицированные игры на телефон — это отличный способ изменить игровой опыт.
Особенно если вы пользуетесь устройствами на платформе
Android, модификации открывают перед вами
новые возможности. Я часто использую взломанные игры,
чтобы получать неограниченные ресурсы.
Моды для игр дают невероятную
свободу выбора, что погружение в игру
гораздо красочнее. Играя с модификациями, я
могу создать новый игровой
процесс, что добавляет новые приключения и делает игру более эксклюзивной.
Это действительно удивительно,
как такие модификации могут улучшить взаимодействие с игрой, а при этом с
максимальной безопасностью использовать такие
модифицированные приложения можно без особых рисков, если быть
внимательным и следить за обновлениями.
Это делает каждый игровой процесс более насыщенным, а возможности
практически бесконечные.
Рекомендую попробовать такие игры с модами для Android
— это может вдохновит на новые приключения
Howdy! This post could not be written much better!
Reading through this post reminds me of my previous roommate!
He always kept preaching about this. I will forward this post to him.
Pretty sure he will have a good read. I appreciate
you for sharing!
Fantastic info. Kudos! https://qa.holoo.co.ir/user/squidokra87
Thanks for the auspicious writeup. It in truth used to be
a entertainment account it. Glance complicated to far added agreeable from you!
By the way, how can we keep in touch?
Great blog here! Also your site loads up fast! What web host are you using?
Can I get your affiliate link to your host? I wish my website loaded up as quickly
as yours lol
hello!,I like your writing so a lot! share we keep up a
correspondence more about your post on AOL?
I require an expert in this area to unravel my problem.
Maybe that is you! Taking a look forward to
look you.
You mentioned it superbly.
Excellent blog here! Also your site loads up very fast!
What web host are you using? Can I get your affiliate link to your
host? I wish my web site loaded up as fast
as yours lol
бесплатные модифицированные игры —
это отличный способ изменить игровой опыт.
Особенно если вы пользуетесь устройствами
на платформе Android, модификации открывают перед вами огромный выбор.
Я часто использую взломанные игры,
чтобы развиваться быстрее.
Модификации игр дают невероятную свободу в игре,
что взаимодействие с игрой гораздо красочнее.
Играя с модификациями, я могу добавить дополнительные функции,
что добавляет виртуальные путешествия
и делает игру более эксклюзивной.
Это действительно захватывающе, как
такие модификации могут улучшить игровой процесс, а при этом не нарушая использовать такие модифицированные приложения можно
без особых неприятных последствий,
если быть внимательным и следить за обновлениями.
Это делает каждый игровой процесс лучше
контролируемым, а возможности
практически неограниченные.
Рекомендую попробовать такие модифицированные версии
для Android — это может вдохновит на новые приключения
Thank you for every other informative web site.
Where else may just I get that kind of info written in such a perfect approach?
I’ve a undertaking that I am simply now operating
on, and I’ve been on the look out for such info.
Its like you read my mind! You appear to know a lot
about this, like you wrote the book in it or something.
I think that you can do with a few pics to drive the message home a bit, but other than that,
this is great blog. An excellent read. I’ll certainly be back.
Hello Dear, are you really visiting this web page daily, if so then you will absolutely obtain fastidious experience.
I do not even know how I ended up here, but I thought this
post was great. I don’t know who you are but definitely you’re going to a famous blogger if you are not
already 😉 Cheers!
My relatives all the time say that I am killing my time here at web,
but I know I am getting familiarity everyday by reading such fastidious
content.
Excellent blog here! Also your web site loads up fast! What web host are you using?
Can I get your affiliate link to your host?
I wish my website loaded up as fast as yours lol
Very quickly this website will be famous among all blogging
and site-building users, due to it’s pleasant content
E2Bet Indonesia, situs judi online terbesar di Indonesia, aman, terpercaya,
dan inovatif, bonus menarik dan layanan pelanggan 24/7.
#E2Bet #E2BetIndonesia #Indonesia
Saved as a favorite, I like your web site!
Here is my blog :: nordvpn coupons inspiresensation (http://tinyurl.com/24yrpcga)
With thanks, A lot of data.
This design is spectacular! You drfinitely know how tto keep a reader amused.
Between your wit and your videos, I was almost moved to start mmy oown blog (well, almost…HaHa!) Fantastic job.
I really loved what you had to say, and more than that,
how you presented it. Too cool!
This is very interesting, You’re a very skilled blogger.
I have joined your feed and look forward to seeking more of your wonderful post.
Also, I’ve shared your site in my social networks!
Also visit my blog; Labeling Machine
Awesome article.
Does your blog have a contact page? I’m having problems locating it
but, I’d like to shoot you an e-mail. I’ve got some suggestions for your blog you might be interested in hearing.
Either way, great blog and I look forward to seeing it expand over time.
of course like your website however you need to take a look at
the spelling on several of your posts. A number of them are rife with spelling issues and I in finding it very troublesome to inform the reality however I’ll surely come again again.
What a information of un-ambiguity and preserveness of valuable experience on the topic of unpredicted emotions.
It’s amazing in favor of me to have a web site, which
is useful for my know-how. thanks admin
Hi there friends, how is all, and what you desire to say concerning this article, in my view its genuinely awesome in support of me.
Admiring the commitment you put into your site and in depth information you present.
It’s good to come across a blog every once in a while that isn’t the same outdated rehashed material.
Fantastic read! I’ve bookmarked your site and I’m
including your RSS feeds to my Google account.
Hurrah! After all I got a blog from where I be capable
of actually take valuable data regarding my study and knowledge.
I love looking through a post that can make men and women think.
Also, many thanks for allowing for me to comment!
Hi there mates, its fantastic piece of writing regarding teachingand completely explained, keep
it up all the time.
Aw, this was an extremely nice post. Spending some time and actual
effort to make a very good article… but what can I say… I hesitate a lot and never manage
to get anything done.
Hey there! This is my 1st comment here so I just wanted to give a quick shout out and say I truly enjoy reading through your posts.
Can you recommend any other blogs/websites/forums that go over the same subjects?
Appreciate it!
You’ve made some really good points there. I looked on the web to learn more about the issue and
found most people will go along with your views on this web site.
Ridiculous quest there. What occurred after? Take care!
What a data of un-ambiguity and preserveness of precious experience concerning unpredicted emotions.
Feel free to visit my page; nordvpn coupons inspiresensation
Hey there! I just want to offer you a big thumbs up for your
excellent information you have here on this post. I will be coming
back to your blog for more soon.
I was able to find good info from your blog posts.
For those who are looking for a free way to get unlimited tokens without buying on SpankBang, they should read the post on this link.
What’s up, I check your new stuff on a regular basis. Your story-telling style is witty, keep it up!
Fantastic web site. Lots of helpful info here. I am sending it to some pals ans also sharing in delicious.
And naturally, thanks for your effort!
Hmm іt seems like your site ate my first comment (it was super long) so I ɡuess I’ll just sum
it up what I suhbmitted and ѕay, І’m thoroughly enjoying
youг blog. I too am an aspіring blog blogger but I’mstill new to
the whole thing. Ⅾo you have anny рoints for rookie blolg writers?
I’d definitely appreciate it.
my web page :: đồng hồ nữ đẹp chính hãng
Sweet blog! I found it while browsing on Yahoo News. Do you have any tips on how to get listed
in Yahoo News? I’ve been trying for a while but I never seem to get there!
Cheers
An impressive share! I’ve just forwarded this onto a
colleague who had been doing a little research on this.
And he in fact ordered me lunch due to the fact that I stumbled upon it
for him… lol. So allow me to reword this….
Thank YOU for the meal!! But yeah, thanks for spending
time to talk about this issue here on your web page.
владимир воронин фск
Slot Fortune Dragon – jogue sem apostar . RTP de 96,74% tornam este slot perfeito para todos. Ganhe com multiplicadores! https://tawk.to/lizawold
Appreciate the recommendation. Let me try it out.
You can certainly see your expertise within the work you write.
The sector hopes for even more passionate writers such as you who aren’t afraid to mention how they believe.
Always go after your heart.
Howdy! This post couldn’t be written any better!
Reading through this post reminds me of my good old room mate!
He always kept chatting about this. I will forward this article
to him. Pretty sure he will have a good read. Thank you
for sharing!
My brother recommended I might like this website. He was entirely right.
This post actually made my day. You can not imagine
simply how much time I had spent for this information! Thanks!
Hi there! Quick question that’s totally off topic.
Do you know how to make your site mobile friendly?
My web site looks weird when browsing from my
apple iphone. I’m trying to find a theme or plugin that might be able to correct this issue.
If you have any suggestions, please share. Thanks!
Definitely imagine that that you said. Your favorite reason appeared to be at the web the easiest thing to
have in mind of. I say to you, I certainly get annoyed whilst people think about issues that they plainly
do not know about. You controlled to hit the nail upon the highest and also defined out the entire thing with no need side-effects , other folks can take a signal.
Will likely be back to get more. Thanks
Hey there hotties! I’m Tyler, and I just discovered this next-level gay chat at BubiChat.
️
Low-key, I was bored af when I stumbled on this actually fun chatroom.
Way hotter than those sketchy dating apps!
At BubiChat, you can:
Trade nudes with hung guys RIGHT NOW
No judgment – just real dudes
Stay discreet if you’re just exploring
Slide into my DMs there and let’s get spicy! Maybe we’ll Netflix &
chill?
Pro tip: It’s stupid easy to join – no “premium upgrade” scams, just fun guys like us.
Hurry up, boi! I’m online now at https://bubichat.com/gay-chat/
XOXO,
Caleb
I do not know if it’s just me or if everyone else experiencing
issues with your blog. It appears as though some of the
written text in your content are running off the screen. Can someone else please comment
and let me know if this is happening to them too?
This might be a issue with my browser because I’ve had this happen previously.
Thank you
It’s an remarkable post for all the internet users; they will get benefit from it I am sure.
This is a topic which is near to my heart… Thank you!
Where are your contact details though?
Candy AI Free Premium. Get Candy AI free premium
account now with unlimited messages, chats, gems, coins and tokens instant.
We are a group of volunteers and opening a new scheme in our community.
Your site offered us with valuable info to work on. You’ve
performed a formidable process and our whole group might be grateful to you.
Take a look at my blog: LED Mesh Screen for Outdoor Media Façade
Hi! This is kind of off topic but I need some help from an established blog.
Is it hard to set up your own blog? I’m not very techincal but
I can figure things out pretty quick. I’m thinking about creating my own but I’m not sure where
to begin. Do you have any points or suggestions? Thanks
I constantly emailed this weblog post page to all
my associates, as if like to read it afterward my friends will too.
This is a topic that is close to my heart…
Thank you! Where are your contact details though?
I loved as much as you’ll receive carried out right here.
The sketch is tasteful, your authored material stylish. nonetheless, you command
get got an impatience over that you wish be delivering the following.
unwell unquestionably come further formerly again since exactly
the same nearly a lot often inside case you shield this hike.
This post will assist the internet viewers for building up new weblog or even a weblog from start to end.
With thanks! A lot of postings!
Good day! I could have sworn I’ve been to your blog before but after browsing through some of the posts I
realized it’s new to me. Anyhow, I’m definitely happy I stumbled upon it and I’ll be bookmarking it and checking back frequently!
You actually make it appear so easy together with your presentation but I to
find this matter to be really one thing which I feel I’d never understand.
It kind of feels too complex and very huge for me. I am having
a look forward to your subsequent put up, I will attempt to get the hang of it!
Hello, i believe that i noticed you visited my web site
so i came to go back the choose?.I’m trying to in finding issues to enhance my website!I assume its adequate to make use of
a few of your concepts!!
Thank you, I have just been searching for information about
this subject for a loong time and yours is the best I’ve caame upon so far.
However, what concerning the conclusion? Are you positive
iin regards to the supply?
This week’s top headlines covers everything from stock movements to climate crisis.
The world watches as legislative actions unfold rapidly. Technology trends steal the
spotlight.
Experts weigh in on science breakthroughs that could redefine medicine and health.
Health updates remain front and center. Meanwhile,
school transformations bring hope for the next generation.
Space exploration fascinates the public once again.
Back on Earth, policing issues spark heated debate.
But fans rejoice in pop culture news and sports highlights.
It’s a whirlwind of essential updates.
It is in reality a great and helpful piece of information. I’m happy that you just shared this useful info with us.
Please keep us up to date like this. Thanks for sharing.
whoah this blog is wonderful i really like reading your posts.
Keep up the good work! You already know, lots
of people are hunting round for this information, you can help them greatly.
Hi, I do believe this is a great blog. I stumbledupon it 😉 I will return yet again since I bookmarked it.
Money and freedom is the best way to change, may you be rich and continue to guide
other people.
Hi there, the whole thing is going nicely here and ofcourse every one is
sharing data, that’s actually good, keep up writing.
https://mazda-demio.ru/forums/index.php?autocom=gallery&req=si&img=6621
Thanks, Ample facts.
Cheers! Good stuff! https://chu-aguilar.thoughtlanes.net/ewbsl-t-nailn-aebb-faakth-naimmiikhanaimsuung-epn-yaangair
It is in point of fact a great and helpful piece of information. I’m glad that you simply shared this useful info with
us. Please stay us up to date like this. Thank you
for sharing.
Very rapidly this website will be famous amid all blogging and
site-building people, due to it’s fastidious content
Hello to all, it’s truly a nice for me to pay a visit this website, it consists of important Information.
Greetings! Very helpful advice in this particular article!
It is the little changes that make the most important changes.
Thanks for sharing!
Excellent goods from you, man. I have remember your stuff previous to
and you are just extremely wonderful. I really like what you’ve
received here, certainly like what you’re saying and the best way in which you
assert it. You are making it enjoyable and you continue to take care
of to keep it smart. I can not wait to learn far more from you.
That is really a wonderful site.
Take a look at my blog post – Packaging Machinery
Nicely put. With thanks.
With havin so much content and articles do you ever run into any problems of plagorism or copyright infringement?
My blog has a lot of exclusive content I’ve either written myself or outsourced but it appears a lot of it is popping it up
all over the web without my permission. Do you know any methods to help protect against content from being stolen? I’d truly appreciate it.
https://honda-fit.ru/forums/index.php?autocom=gallery&req=si&img=7039
https://myteana.ru/forums/index.php?autocom=gallery&req=si&img=6609
Very good info. Lucky me I ran across your site by
accident (stumbleupon). I’ve book-marked it for later!
Incredible all kinds of good data. https://www.pradaan.org/members/enemyrobin01/activity/611060/
This is my first time go to see at here and i am truly happy to read all at alone
place.
After looking over a number of the blog articles on your site, I seriously like your technique
of writing a blog. I book marked it to my bookmark webpage list and will be checking back soon. Take
a look at my web site as well and tell me
how you feel.
You expressed this really well. https://jiligamesslot.mystrikingly.com/blog/rtp-jili-slot
Hello, i believe that i noticed you visited my weblog so i got here to go back the choose?.I am trying to in finding things
to enhance my web site!I suppose its adequate to make use of a few of your ideas!!
Thanks for sharing your thoughts. I truly appreciate your efforts and I am waiting
for your further post thank you once again.
Great article! That is the kind of info that are meant to be shared around the internet.
Disgrace on the search engines for no longer positioning
this put up upper! Come on over and consult with my web site .
Thank you =)
I must thank you for the efforts you have put in penning this site.
I am hoping to view the same high-grade blog posts from you later on as well.
In truth, your creative writing abilities has inspired me to get
my own, personal site now 😉
This article presents clear idea designed for the new people of
blogging, that truly how to do blogging and site-building.
Thanks for sharing your thoughts on indo123. Regards
You’re so awesome! I do not think I have read a single thing like that before. So great to discover another person with some unique thoughts on this subject. Seriously.. many thanks for starting this up. This website is something that is needed on the internet, someone with some originality.
If you are going for best contents like I do, only pay a visit this
website daily since it offers quality contents, thanks
It’s a pity you don’t have a donate button! I’d definitely donate
to this fantastic blog! I guess for now i’ll settle for book-marking and adding your RSS feed to my Google
account. I look forward to new updates and will
share this website with my Facebook group. Chat soon!
Hi everyone, Welcome to our unlimited access service.
You can watch all models videos for free. Including Watch Free Videos, View
Free Photos, Free Access to Fan Club, Free Tokens, Free Private Chat, Free Video Downloads and many more
unlimited services. Some details need to be verified, because our service is
supported from each specific country. NOTE: TOKENS CAN BE USED ON ALL MODELS!.
Thank you.
Thank you for another informative site. Where else may I get
that type of information written in such a
perfect approach? I’ve a project that I am just now running on,
and I’ve been at the glance out for such information.
whoah this blog is wonderful i really like studying your
articles. Keep up the great work! You realize, lots of people are searching around
for this information, you could aid them greatly.
This is very attention-grabbing, You’re a very skilled blogger.
I’ve joined your rss feed and look ahead to seeking extra of your wonderful post.
Additionally, I’ve shared your website in my social networks
Great web site you’ve got here.. It’s difficult to find
good quality writing like yours these days. I really appreciate individuals like you!
Take care!!
Good day I am so delighted I found your webpage, I really found you by error, while I was
researching on Askjeeve for something else, Anyhow
I am here now and would just like to say many thanks for
a marvelous post and a all round thrilling blog (I also love the theme/design), I don’t have time to read through it all at the minute but I have saved it and also
included your RSS feeds, so when I have time I will be back to read a lot
more, Please do keep up the awesome work.
Fantastic beat ! I would like to apprentice whilst you
amend your site, how can i subscribe for a weblog site? The account helped me a applicable
deal. I had been tiny bit familiar of this your broadcast offered brilliant
clear concept
Great info. Lucky me I ran across your site by chance (stumbleupon).
I’ve bookmarked it for later!
Do you have a spam problem on this site; I also am a blogger, and I was wanting to know your situation; we have developed some nice methods
and we are looking to trade strategies with others, why not shoot
me an e-mail if interested.
Wow that was strange. I just wrote an incredibly long comment but after I clicked submit
my comment didn’t show up. Grrrr… well I’m not writing all that over again. Anyhow,
just wanted to say wonderful blog!
What’s up friends, its great paragraph on the topic of cultureand entirely explained, keep it up all the time.
Thanks for a marvelous posting! I actually enjoyed reading it,
you may be a great author.I will always bookmark your blog and will eventually come back in the future.
I want to encourage continue your great posts, have a nice evening!
Great delivery. Sound arguments. Keep up the amazing work.
Appreciation to my father who told me about this webpage, this blog is truly remarkable.
I’m not sure why but this website is loading very slow for me.
Is anyone else having this issue or is it a problem on my end?
I’ll check back later on and see if the problem still exists.
What і dօ not understood іs in reality how you’re
no lⲟnger really a ⅼot more smartly-favored
tһan you migһt bе rigһt noԝ. Уoᥙ are sⲟ intelligent.
Уou alгeady know thᥙs considerably ߋn the subject of
tyis subject, mаԁe mе for my рart consіder it from a lot oof
ᴠarious angles. Itѕ like men annd women aren’t involved eⲭcept it іs something to do ѡith Woman gaga!
Υour personal stuffs excellent. Аt all tіmes maintain іt up!
Hеrе is my web site Top 10 mẫu đồng hồ nữ bán chạy nhất
I’m extremely impressed with your writing skills as well as
with the layout on your weblog. Is this a paid theme or did you
customize it yourself? Anyway keep up the excellent quality writing, it is rare to see a great blog like this one nowadays.
fantastic issues altogether, you simply won a logo new reader.
What might you recommend about your submit that you just made a few days in the past?
Any certain?
I am truly happy to glance at this web site posts which consists of plenty of useful facts, thanks for providing these data.
I’m impressed, I have to admit. Rarely do I come across a blog that’s equally educative and entertaining,
and let me tell you, you’ve hit the nail on the
head. The issue is something that not enough people
are speaking intelligently about. I am very happy that I stumbled across this during my search for
something regarding this.
I do trust all of the ideas you’ve introduced for your post.
They’re really convincing and will certainly work. Still, the posts are very brief for novices.
May just you please extend them a bit from next
time? Thank you for the post.
You actually make it seem so easy with your presentation however I in finding this topic to be really something that I feel
I would never understand. It seems too complicated and very broad for me.
I am taking a look ahead on your next publish,
I will try to get the hang of it!
I do accept as true with all of the concepts you have introduced for your
post. They’re really convincing and can certainly work.
Still, the posts are very quick for newbies.
May just you please lengthen them a little from subsequent time?
Thank you for the post.
my blog; Packaging Machinery
Nice weblog here! Also your web site so much up fast!
What web host are you the use of? Can I get your associate hyperlink for your host?
I want my web site loaded up as quickly as yours lol
I couldn’t resist commenting. Well written!
It’s an amazing piece of writing for all the online viewers; they will take benefit from
it I am sure.
My brother suggested I might like this web site. He was entirely right.
This post truly made my day. You cann’t imagine simply how much time I had spent for this information! Thanks!
Hello! This post could not be written any better!
Reading through this post reminds me of my good old room mate!
He always kept talking about this. I will forward
this post to him. Pretty sure he will have a good read. Thanks
for sharing!
Pretty! This was an extremely wonderful article. Thanks for providing these details.
Nice replies in return of this difficulty with genuine arguments
and telling everything regarding that.
When someone writes an piece of writing he/she retains the
image of a user in his/her mind that how a user can know it.
Therefore that’s why this article is outstdanding. Thanks!
Howdy very cool website!! Guy .. Beautiful .. Wonderful ..
I’ll bookmark your web site and take the feeds additionally?
I’m glad to seek out a lot of helpful information here within the post, we need work out more techniques on this regard, thanks for sharing.
. . . . .
Whats up are using WordPress for your site platform?
I’m new to the blog world but I’m trying to get started
and set up my own. Do you require any html coding knowledge to make your own blog?
Any help would be greatly appreciated!
I’m now not sure the place you’re getting your info, however great topic.
I needs to spend some time finding out much more or understanding more.
Thanks for great info I used to be looking for this info
for my mission.
What’s up i am kavin, its my first occasion to commenting anywhere,
when i read this paragraph i thought i could also make comment due
to this sensible piece of writing.
When someone writes an paragraph he/she maintains the image of a user in his/her brain that how a user can be aware of it.
So that’s why this piece of writing is great. Thanks!
Hmm it appears like your site ate my first comment (it was extremely long) so I
guess I’ll just sum it up what I wrote and say, I’m thoroughly enjoying your blog.
I as well am an aspiring blog blogger but I’m still new to everything.
Do you have any helpful hints for first-time blog writers?
I’d really appreciate it.
belka-digital
I am actually delighted to glance at this webpage posts which includes tons of helpful information, thanks for providing such statistics.
As a seasoned expert with a tested performance history in seo,
I have actually helped organizations of all sizes drive
development and attain their objectives. By combining critical preparation with nnovative
options, I continually suplply impactful outcomes.
Staying in advance of the contour, I continually inform myself on the most recent search
emgine optimization advancements. Let’s the Chicagoland area,NfiniteLimits.com is a relied oon electronic remedies carrier based in Mundelein, IL.
My strategy blends practical proficiency with sector
understanding to drie meaningful growth. When I’m not refining internet site efficiency, I’m exploeing the most recent search engine optimization innovations.
Sustaining Northern.com is your premier companion for seo uusa (http://6staragli.com/) services,
headquartered in Mundelein, Illinois.
Hi there to every one, because I am really eager of reading this blog’s post to
be updated on a regular basis. It contains nice information.
Hello There. I found your blog using msn. This is an extremely well written article.
I will be sure to bookmark it and come back to read more of your useful info.
Thanks for the post. I will certainly comeback.
Hello there, You have done a fantastic job. I will certainly digg it and personally recommend to my friends.
I’m confident they’ll be benefited from this website.
Hi there it’s me, I am also visiting this site daily, this web page
is really nice and the users are genuinely sharing fastidious thoughts.
Saved as a favorite, I like your web site!
I every time spent my half an hour to read this website’s
articles everyday along with a cup of coffee.
I’m not that much of a internet reader to be honest but your sites really nice,
keep it up! I’ll go ahead and bookmark your site to
come back later. Cheers
London website agency withh 20+ years off
experience. Ꮐet а fre web desifn & SEO strategy tߋo bolost online viseitors аnd sales.
Expeert WordPrwss assistance ɑvailable.
Thanks. I like this. https://elson.qodeinteractive.com/highly-customizable-loads-of-layouts/
At this time it sounds like BlogEngine is the
best blogging platform out there right now. (from what I’ve read) Is that what you are using on your blog?
Greetings, I believe your site could possibly
be having browser compatibility problems. When I look at your
blog in Safari, it looks fine however, if opening in Internet
Explorer, it has some overlapping issues. I merely wanted
to give you a quick heads up! Besides that, great website!
These are actually fantastic ideas in on the topic of blogging.
You have touched some fastidious things here. Any way keep
up wrinting.
Right here is the right webpage for everyone who wants to find out about this topic.
You understand a whole lot its almost tough to argue with you (not that I actually would want to…HaHa).
You definitely put a new spin on a subject that has been discussed for decades.
Excellent stuff, just great!
This is my first time pay a visit at here and i am really pleassant to read everthing
at alone place.
Wonderful website you have here but I was curious if you knew of any
forums that cover the same topics discussed here? I’d really like to be a part of community where I can get comments from other experienced people that share the same interest.
If you have any recommendations, please let me know.
Appreciate it!
Oh my goodness! Awesome article dude! Thank you so much, However I am having difficulties with your RSS. I don’t know the reason why I cannot join it. Is there anybody else having identical RSS problems? Anyone who knows the solution will you kindly respond? Thanx.
My family members every time say that I am killing my time here
at net, however I know I am getting know-how all the time by reading thes nice
posts.
Hello mates, nice piece of writing and fastidious arguments commented at this place, I am
in fact enjoying by these.
Thanks! I like this. https://clinfowiki.win/wiki/Post:BETFLIK
Greetings, I think your site could be having browser compatibility problems.
Whenever I take a look at your website in Safari, it looks fine however when opening in IE,
it has some overlapping issues. I merely wanted to give
you a quick heads up! Aside from that, fantastic website!
Its like you read my mind! You seem to know so much about
this, like you wrote the book in it or something.
I think that you can do with some pics to drive the message home a bit, but other than that, this is great blog.
A great read. I’ll definitely be back.
Hello there, just became alert to your blog through Google, and found
that it’s really informative. I’m going to watch out for brussels.
I will be grateful if you continue this in future.
A lot of people will be benefited from your writing. Cheers!
I am now not sure where you are getting your info, but great topic.
I needs to spend some time learning much more or working out more.
Thanks for magnificent information I used to be in search of this info for my mission.
Also visit my web blog nordvpn coupons inspiresensation (tinyurl.com)
After looking over a number of the blog posts on your web page,
I really appreciate your technique of writing a blog.
I book marked it to my bookmark website list and will be checking back in the
near future. Please visit my website as well and tell me what you think.
When someone writes an piece of writing he/she keeps the plan of a user in his/her mind that how a
user can be aware of it. Thus that’s why this
piece of writing is perfect. Thanks!
Excellent blog here! Also your website loads up fast! What web host
are you the use of? Can I get your associate hyperlink for your
host? I desire my web site loaded up as quickly as yours lol
Pretty great post. I just stumbled upon your weblog and wished
to mention that I’ve really enjoyed surfing around
your weblog posts. After all I will be subscribing in your feed and I’m hoping you write once
more very soon!
Everything is very open with a very clear clarification of the issues.
It was really informative. Your website is very useful. Thanks for sharing!
Very great post. I just stumbled upon your blog and wanted to mention that
I have truly enjoyed browsing your blog posts.
In any case I’ll be subscribing on your feed and I am hoping you write again soon!
Hello my family member! I wish to say that this post is amazing, nice written and come with approximately all significant infos.
I’d like to look extra posts like this .
Thank you a bunch for sharing this with all of us you really realize
what you are talking approximately! Bookmarked. Please additionally consult with my web
site =). We could have a link change contract between us
Feel free to surf to my blog post :: Nordvpn coupons inspiresensation
This text is priceless. How can I find out more?
My brother suggested I might like this web site.
He was totally right. This post actually made my day.
You can not imagine simply how much time I had spent for this information!
Thanks!
Howdy! Quick question that’s completely off topic.
Do you know how to make your site mobile friendly? My website looks weird when browsing from my apple iphone.
I’m trying to find a theme or plugin that might be
able to resolve this problem. If you have any recommendations,
please share. With thanks!
Really quite a lot of very good material. http://kxb4u.com/dream/home.php?mod=space&uid=147251
What’s up, I read your new stuff regularly.
Your story-telling style is awesome, keep doing what you’re doing!
of course like your web site but you need to take a look at the spelling
on several of your posts. A number of them are rife with spelling issues and I to
find it very bothersome to tell the reality nevertheless I’ll definitely come again again.
Hello Dear, are you in fact visiting this web site on a regular basis,
if so after that you will without doubt take pleasant know-how.
I am not sure where you are getting your information, but
great topic. I needs to spend some time learning much more
or understanding more. Thanks for wonderful info I was looking for this information for my mission.
Great beat ! I wish to apprentice while you amend your site, how can i subscribe for a blog web site?
The account helped me a acceptable deal. I had been a little bit acquainted of this your broadcast offered bright clear idea
Hi just wanted to give you a brief heads up and let you know a few of the images aren’t loading properly.
I’m not sure why but I think its a linking issue.
I’ve tried it in two different internet browsers and both show the same results.
I am truly happy to glance at this website posts which contains tons of useful information, thanks for providing these kinds of information.
I am curious to find out what blog platform you happen to be working with?
I’m having some small security problems with my latest website and I
would like to find something more safeguarded. Do you have any suggestions?
Useful stuff Kudos. https://images.google.com.gt/url?q=https://betflik999.group/betflik999-%e0%b8%aa%e0%b8%a1%e0%b8%b1%e0%b8%84%e0%b8%a3%e0%b8%aa%e0%b8%a1%e0%b8%b2%e0%b8%8a%e0%b8%b4%e0%b8%81/
Remarkable! Its in fact amazing paragraph, I have got much clear idea concerning from this article.
Hi, I want to subscribe for this webpage to get latest updates, thus where can i do it
please help out.
I really like it whenever people get together and share
ideas. Great site, keep it up!
Pretty nice post. I just stumbled upon your weblog and wanted to say that I’ve truly enjoyed browsing your blog posts.
After all I’ll be subscribing to your feed and I hope you write again very
soon!
Thank you for some other great article. Where else could anyone get that type of information in such an ideal means of writing?
I have a presentation next week, and I am at the look
for such info.
I would like to thank you for the efforts you have put in writing this website.
I’m hoping to see the same high-grade content by you in the future as well.
In truth, your creative writing abilities has encouraged me to get my own website now
😉
After checking out a handful of the blog articles on your web
site, I really appreciate your way of blogging. I saved as a favorite it to
my bookmark webpage list and will be checking back soon. Please visit my website as well and tell me what you think.
Demystifying Counterfeit Hermès Purses: A Thorough Examination
The realm of exclusive accessories has continuously been enthralled by
Hermes purses, specifically their famous Birkin and Kelly designs.
These coveted accessories embody elegance, workmanship, and uniqueness, with costs varying from ten thousand dollars to
over $500,000 for limited versions. With such high value
and desirability, it’s no surprise that Hermes has emerged as one of the most copied luxury names in the world.
The Story of Hermes
Established in eighteen thirty-seven as a saddle store in Paris, Hermes began by crafting leather saddle
goods. The company’s dedication to outstanding workmanship
was created from the beginning and persists to be their trademark today.
Each Hermes artisan completes at least two years of education before they can craft
their first handbag, showing the company’s dedication to craftsmanship.
The renowned Kelly was launched in nineteen thirty-five
(first called the “Sac à dépêches”), while the famous Birkin launched in 1982 following a random encounter
between Hermes director Jean-Louis Dumas and icon Jane Birkin on a airplane
trip from Paris to the UK.
The Growth of Knockoff Hermes Bags
The extreme demand and substantial costs of real Hermes handbags have created a large industry for imitations.
Recent analyses demonstrate that nearly ninety percent of all Hermès Birkin and Kelly
bags offered on websites aren’t genuine, generating substantial obstacles for buyers searching for the authentic
item.
Modern copycats have developed increasingly advanced, using
cutting-edge technologies to create realistic copies that can be hard to differentiate from real bags at first
glance. These fakes range from low-quality copies to “mirror images”
that copy several elements of genuine Hermès purses.
How to Recognize Original Hermès Bags
When inspecting a Hermès bag to determine its authenticity,
specialists evaluate numerous critical features:
1. Quality and Leather
Genuine Hermes handbags are manually created with the finest tier skins and outstanding craftsmanship.
The leather should feel supple and flexible with a
unique natural aroma that imitators are unable to copy.
The metal parts should be solid, created using palladium
that won’t peel or flake easily.
2. Seams
One unexpected detail is that because genuine Hermes
bags are hand-crafted, the stitches should in fact have certain variations.
Fakes are usually machine-sewn, so they are completely in line
with one other. Hermès applies a special saddle-stitch style originating from their saddle-making background.
3. Emblem and Stamping
The Hermes logo marking should read “Hermès Paris Made in France” text on 3 lines with crisp crisp stamping.
On fake Hermes handbags, the logo would seem off, large, or rectangular and may have unclear edges or irregular alignment.
4. Hardware and Details
The metal parts on genuine Hermès handbags
contains special elements like clean markings, superior fasteners, and correctly fastened bottom studs.
Hermes produces its own zippers, so you should never notice a third-party brand or another brand’s mark
on the zipper.
5. Identification Markers
Interestingly, Hermès never issue authentication certificates
with their bags. They have never and certainly
never will. If you’ve purchased a Hermès handbag and were given an authenticity card with it, it is absolutely a replica.
The Moral Issues
The fake business raises serious social problems. While fake purses may seem equivalent to authentic ones,
they are produced without the quality control, fair working standards, or sustainability practices that authentic high-end brands
follow. Moreover, the replica industry has been connected
to organized crime and worker exploitation.
In Conclusion
For those who admire the artisanship and legacy of Hermes, knowing the
distinction between real and counterfeit purses is vital.
Whether purchasing for financial or personal pleasure, knowing how to identify real Hermès craftsmanship helps guarantee that
you’re obtaining what you pay for – a item of premium style heritage crafted with
unparalleled craftsmanship and attention to detail.
If you’re planning on investing in a Hermes handbag, the most secure method is to obtain directly from
Hermès or from established retailers who supply complete authentication guarantees and guarantees.
Good day! I could have sworn I’ve been to this blog before but after reading
through some of the post I realized it’s new to me. Nonetheless, I’m definitely delighted I found it
and I’ll be book-marking and checking back frequently!
Upgrade your free membership to see everyone who has viewed your profile.
… Create your free profile and start meeting singles in minutes on InternationalCupid free access
When I originally commented I clicked the “Notify me when new comments are added” checkbox and now each time a comment is added
I get four emails with the same comment. Is there
any way you can remove me from that service?
Appreciate it!
Normally I don’t learn post on blogs, but I wish to say that this write-up very forced me to check out and do
so! Your writing style has been surprised me. Thank you,
very great article.
WOW just what I was looking for. Came here by searching for inground pool demolition and
backfill
I appreciate, lead to I found just what I used to be taking a look for.
You’ve ended my four day long hunt! God Bless you
man. Have a nice day. Bye
This is a topic which is close to my heart… Many
thanks! Where are your contact details though?
Terrific work! This is the type of info that are supposed to be shared around the internet.
Shame on the seek engines for not positioning this put up higher!
Come on over and seek advice from my web site . Thanks =)
Hey are using WordPress for your site platform? I’m
new to the blog world but I’m trying to get started and set up my own. Do you need any html coding
knowledge to make your own blog? Any help would be really appreciated!
It’s an awesome article for all the online users; they
will obtain benefit from it I am sure.
buy propecia online without prescription
Have you ever thought about including a little bit more than just
your articles? I mean, what you say is valuable
and everything. However think about if you added some great photos or videos to give your posts more,
“pop”! Your content is excellent but with images and videos,
this blog could certainly be one of the best in its field. Fantastic
blog!
Join TryNectar AI and get Free Credits and enjoy full access on TryNectar AI unlimited.
For those who are looking for free ways to get unlimited credits without
buying for TryNectar AI, they should follow this post.
Heya! I realize this is kind of off-topic but I had to ask.
Does building a well-established blog like yours require a massive amount
work? I’m brand new to writing a blog however I do write in my diary daily.
I’d like to start a blog so I can share my experience and feelings online.
Please let me know if you have any kind of ideas or
tips for brand new aspiring bloggers. Thankyou!
It’s actually a nice and useful piece of info.
I am satisfied that you simply shared this useful information with us.
Please keep us up to date like this. Thank you for sharing.
I’m really inspired together with your writing skills and also
with the format to your weblog. Is that this a paid topic or did you
customize it your self? Anyway keep up the nice quality writing, it’s uncommon to look a nice blog like
this one nowadays..
You made some really good points there. I checked on the
internet for more info about the issue and found most individuals will go along with
your views on this website.
Hello every one, here every one is sharing such familiarity, therefore it’s good to read this
webpage, and I used to pay a visit this webpage all the time.
Bardzo dobry artykuł! Dzięki za przydatne treści.
Ostatnio myślę nad założeniem własnej
strony, więc każda wskazówka jest cenna.
Macie może doświadczenie z wweb designem? Zależy mmi
na nowoczesnym wyglądzie.
Słyszałem o Rooma Web Studio, tworzą profesjonalne serwisy.
Jakie macie opinie na ich temat?
Dzięki za wszelkie informacje i pozdrawiam!
Great blog here! Also your web site loads
up very fast! What web host are you using? Can I get your affiliate link to
your host? I wish my website loaded up as quickly as yours lol
These are genuinely enormous ideas in on the topic of blogging.
You have touched some nice factors here. Any way keep
up wrinting.
This piece of writing is genuinely a fastidious one it helps new internet
viewers, who are wishing for blogging.
Hey there! This is my first visit to your blog!
We are a team of volunteers and starting a new initiative in a community in the
same niche. Your blog provided us valuable information to work on. You have done a wonderful job!
You reported it well!
I am truly grateful to the owner of this site who has shared this great post at at this place.
I read this piece of writing completely concerning the resemblance
of latest and preceding technologies, it’s amazing article.
Hello it’s me, I am also visiting this website
on a regular basis, this web page is really nice and
the users are really sharing good thoughts.
Wow that was unusual. I just wrote an very long comment
but after I clicked submit my comment didn’t show up.
Grrrr… well I’m not writing all that over again. Anyhow, just wanted
to say excellent blog!
Everything is very open with a clear explanation of the
challenges. It was definitely informative. Your site is very useful.
Thanks for sharing!
Asking questions are truly fastidious thing if you are not understanding something fully, but this post provides good understanding yet.
Hi, its fastidious paragraph on the topic
of media print, we all be aware of media is a enormous source
of information.
Very soon this web page will be famous amid all blogging people, due to it’s good articles or reviews
whoah this weblog is wonderful i love studying your articles.
Stay up the great work! You already know, a
lot of individuals are looking round for this info, you could aid them greatly.
Wonderful, what a web site it is! This weblog presents useful facts to us, keep it
up.
Take a look at my web blog Accutek Packaging Equipment Company
Emiratefix
UAE Duabi
0543747022
تصليح ثلاجات سيمنس 0543747022
تصليح ثلاجات سيمنس [https://imoodle.win/wiki/Where_to_Repair_Your_Siemens_Washing_Machine_in_Dubai]
Oh my goodness! Awesome article dude! Many thanks, However
I am having issues with your RSS. I don’t understand the reason why I
can’t subscribe to it. Is there anybody else having identical
RSS issues? Anyone that knows the solution will you kindly respond?
Thanks!!
Wonderful items from you, man. I’ve have in mind your stuff
previous to and you’re simply too excellent.
I really like what you have got right here, certainly like
what you are stating and the best way during which you are saying it.
You make it enjoyable and you continue to take care of to stay
it wise. I can’t wait to learn far more from you. That is really a wonderful web site.
I’ve been betting on cricket matches for years, and E2Bet has been my favorite platform.
The live odds updates make the experience thrilling.
Absolutely love it!
I believe this is one of the most significant info for me.
And i am satisfied reading your article. However want to statement
on few normal things, The site style is great, the articles is actually great :
D. Excellent activity, cheers
I’ve read a few good stuff here. Definitely worth bookmarking for revisiting.
I wonder how a lot effort you put to make the
sort of great informative website.
Emiratefix
UAE Duabi
0543747022
تصليح سخانات دبي 0543747022
تصليح سخانات دبي (https://www.dermandar.com/user/needlewing4/)
Excellent post but I was wondering if you could write a litte
more on this topic? I’d be very grateful if you could
elaborate a little bit more. Thank you!
I like the helpful information you provide in your articles.
I will bookmark your blog and check again here regularly. I am quite certain I will learn many new stuff right here!
Good luck for the next!
Howdy! This blog post could not be written much better!
Reading through this post reminds me of my previous roommate!
He continually kept preaching about this. I most certainly will send this information to him.
Pretty sure he’s going to have a good read. Thank you for
sharing!
Heya i am for the first time here. I found this board and I find It truly useful & it helped me out a lot.
I hope to give something back and help others like you aided me.
Hello There. I found your blog using msn. This is an extremely well written article.
I will be sure to bookmark it and come back to read more of your useful info.
Thanks for the post. I’ll definitely return.
Heya i am for the first time here. I found this
board and I find It really useful & it helped me out
a lot. I hope to give something back and aid others like you aided me.
Hi friends, its wonderful post on the topic of tutoringand fully explained, keep it
up all the time.
Write more, thats all I have to say. Literally, it seems as though you relied on the video to
make your point. You clearly know what youre talking about, why waste your intelligence on just posting videos
to your site when you could be giving us something informative to read?
I’m gone to inform my little brother, that he should also go to see this
web site on regular basis to take updated from most up-to-date gossip.
Peculiar article, exactly what I was looking for.
whoah this weblog is magnificent i love studying your posts.
Keep up the great work! You realize, many persons
are looking around for this info, you could aid them greatly.
This is very attention-grabbing, You’re a very skilled blogger.
I have joined your feed and look forward to searching for extra of your fantastic
post. Also, I’ve shared your web site in my social networks
Thank you, I’ve recently been looking for info about this subject for a long time
and yours is the greatest I have found out till now.
However, what about the conclusion? Are you sure in regards to the source?
If some one needs to be updated with most recent technologies afterward he must
be pay a quick visit this site and be up to date daily.
I absolutely love your blog.. Pleasant colors & theme.
Did you develop this site yourself? Please reply back
as I’m wanting to create my very own blog and would like to
learn where you got this from or just what the theme is called.
Appreciate it!
I have been surfing online more than 2 hours today,
yet I never found any interesting article like yours. It’s pretty worth enough for
me. In my opinion, if all web owners and bloggers made good content as
you did, the net will be a lot more useful than ever before.
It’s going to be end of mine day, but before finish I am reading this great post to
increase my experience.
Hi, I log on to your blog daily. Your story-telling style is awesome, keep it up!
These are really wonderful ideas in on the topic of
blogging. You have touched some pleasant factors here.
Any way keep up wrinting.
Good info. Lucky me I recently found your blog by accident (stumbleupon).
I have bookmarked it for later!
What’s Going down i’m new to this, I stumbled upon this I’ve discovered It absolutely useful and
it has helped me out loads. I hope to contribute & aid other users like its helped me.
Good job.
Why ActivPure Is The Ultimate CBD Root http://akz1.su/bitrix/redirect.php?goto=https://activpure.net/In today’s health-conscious world, dietary supplements hold taken core stage, providing an range of handy options to enhance well-being.
I’ve been using E2Bet for a while now, and it’s the best platform for cricket exchange
in Pakistan! The live odds are accurate, and the user interface
is seamless. Highly recommend it to everyone!
Ahaa, its nice dialogue concerning this paragraph here at this weblog, I have read all that, so now me also commenting here.
Hi there, everything is going well here and ofcourse every one is sharing data, that’s actually fine, keep up writing.
This piece of writing is actually a good one it assists new net users, who are wishing
in favor of blogging.
Hi to every single one, it’s in fact a fastidious for me to visit this site,
it contains priceless Information.
Hi there! Someone in my Myspace group shared this website
with us so I came to give it a look. I’m definitely loving the information. I’m book-marking and will
be tweeting this to my followers! Excellent blog and excellent style and
design.
Why Derila Rest Is The Scoop Pillow For A Secure Night’s Kip https://wikidrogas.wikaina.com/wiki/index.php/Get_Wind_Derila_Pillow:In the ever-evolving market of log Z’s solutions, determination the double-dyed rest give notice be a daunting project. The Derila Pillow has emerged as a democratic selection for those quest a intermix of comfort and patronise.
Hello would you mind letting me know which hosting company you’re utilizing?
I’ve loaded your blog in 3 different internet browsers and
I must say this blog loads a lot faster then most.
Can you recommend a good web hosting provider at a fair price?
Thanks a lot, I appreciate it!
Hey there! This post could not be written any better!
Reading this post reminds me of my good old room mate!
He always kept talking about this. I will forward this page to him.
Pretty sure he will have a good read. Thanks for sharing!
I was recommended this blog by my cousin. I am not sure whether this post is written by him as nobody else know such detailed about
my trouble. You are wonderful! Thanks!
Does your blog have a contact page? I’m having a tough time locating it but,
I’d like to shoot you an email. I’ve got some recommendations for
your blog you might be interested in hearing. Either way, great site and
I look forward to seeing it grow over time.
Magnificent site. A lot of useful information here.
I’m sending it to several friends ans also sharing in delicious.
And of course, thanks for your sweat!
hello there and thank you for your information – I’ve certainly picked up something new from right here.
I did however expertise some technical issues using this website, as I
experienced to reload the web site many times previous to
I could get it to load correctly. I had been wondering if your web hosting is OK?
Not that I am complaining, but sluggish loading instances times will sometimes affect your placement in google and
could damage your high quality score if ads and marketing with Adwords.
Well I am adding this RSS to my email and can look out
for much more of your respective intriguing content. Ensure that you update this again very soon.
With thanks, Ample info!
https://www.google.bs/url?q=https://betflik888-th.com/%e0%b8%aa%e0%b8%a1%e0%b8%b1%e0%b8%84%e0%b8%a3-betflik888/
If you want to obtain much from this post then you have
to apply such methods to your won weblog.
Hmm it appears like your blog ate my first comment (it was extremely
long) so I guess I’ll just sum it up what I submitted and say,
I’m thoroughly enjoying your blog. I too am an aspiring blog
writer but I’m still new to everything. Do you have any tips for first-time blog writers?
I’d certainly appreciate it.
Generally I do not read article on blogs, but I wish to say that this
write-up very pressured me to take a look at and do it!
Your writing taste has been surprised me. Thanks, very great article.
Hey! Quick question that’s completely off topic. Do
you know how to make your site mobile friendly? My weblog
looks weird when viewing from my iphone 4. I’m trying to find a template or
plugin that might be able to resolve this problem.
If you have any suggestions, please share.
Many thanks!
Heya i am for the first time here. I came across this board and I in finding It truly useful
& it helped me out a lot. I hope to give something again and help others like you aided me.
Hey! I could have sworn I’ve been to this site before but after checking through some of the post I realized it’s new to me.
Anyways, I’m definitely glad I found it and I’ll be book-marking and checking back often!
I all the time used to study article in news papers but now as I am a user of internet so from now I am
using net for posts, thanks to web.
May I simply say what a relief to find someone who genuinely
understands what they’re discussing on the web.
You certainly realize how to bring a problem to light
and make it important. More people have to read this and understand this side of the story.
I can’t believe you aren’t more popular since you most certainly have the gift.
Also visit my web page – prime biome does it work
Hi there! I know this is kind of off topic but I was wondering if you knew where I could locate a
captcha plugin for my comment form? I’m using
the same blog platform as yours and I’m having difficulty finding one?
Thanks a lot!
Hurrah, that’s what I was looking for, what a information! existing here at
this web site, thanks admin of this website.
my page: indoor video wall
First of all I want to say terrific blog! I had a quick question which
I’d like to ask if you don’t mind. I was curious
to know how you center yourself and clear your head prior to writing.
I have had a difficult time clearing my mind in getting my thoughts out.
I truly do take pleasure in writing however it just seems like the first 10 to 15 minutes are
usually wasted simply just trying to figure out how to
begin. Any recommendations or tips? Cheers!
What’s up, its pleasant article concerning media print,
we all know media is a impressive source of information.
Demystifying Counterfeit Hermes Purses: A Thorough Overview
The universe of exclusive design has long been fascinated by Hermès handbags, especially their famous Kelly and Birkin models.
These desired products represent sophistication, workmanship,
and uniqueness, with prices ranging from 10,000 dollars
to over half a million dollars for special pieces.
With such substantial value and popularity, it’s no surprise that Hermès
has grown into one of the most duplicated designer brands in the global market.
The Origins of Hermès
Launched in 1837 as a equestrian workshop in the French capital,
Hermès started by creating leather equestrian accessories.
The brand’s dedication to excellent workmanship was established early and continues to be their hallmark now.
Each Hermes artisan experiences no less than 24 months of apprenticeship before they
can create their initial purse, illustrating the house’s dedication to perfection.
The famous Kelly was unveiled in 1935 (originally called the “Sac à dépêches”), while the celebrated Birkin bag
debuted in 1982 following a unexpected conversation between Hermes
director Jean-Louis Dumas and actress Birkin on a airplane trip from Paris to the UK.
The Growth of Imitation Hermes Purses
The extraordinary popularity and steep costs of authentic Hermes
handbags have established a massive industry for knockoffs.
Modern surveys reveal that nearly ninety percent of all Hermes Kelly and Birkin handbags sold on websites aren’t
real, creating significant challenges for buyers looking for the authentic item.
Today’s counterfeiters have grown ever more skilled, utilizing advanced processes to
manufacture believable counterfeits that can be
challenging to distinguish from original products
at initial inspection. These counterfeits range from low-quality imitations to premium
counterfeits that duplicate multiple elements of real Hermes purses.
How to Recognize Authentic Hermès Purses
When inspecting a Hermès purse to confirm its originality, experts look at several critical elements:
1. Quality and Fabrics
Real Hermès bags are artisan-made with the top tier leathers and
superior craftsmanship. The leather should feel supple and supple with a distinctive natural aroma that counterfeiters cannot
copy. The metal fittings should be heavy, crafted from palladium that does not wear or flake readily.
2. Thread work
One surprising detail is that because authentic Hermes purses
are handmade, the seams should in fact have
minor variations. Imitations are usually machine-sewn, so they are entirely uniform with one another.
Hermes uses a specific saddle-stitch method coming from their equestrian tradition.
3. Branding and Imprinting
The Hermes mark imprint should state “Hermès Paris Made in France” text on 3 rows with crisp clean imprinting.
On imitation Hermes bags, the logo would seem
irregular, too big, or squared and might have blurred lines or uneven positioning.
4. Metal parts and Features
The metal elements on real Hermes bags incorporates characteristic elements like precise engravings,
high-end closures, and well secured bottom
studs. Hermes makes its own zippers, so you should not notice a
YKK or different company’s mark on the hardware.
5. Identification Markers
Interestingly, Hermes doesn’t provide authenticity cards with
their handbags. They have never and probably never will.
If you’ve purchased a Hermes handbag and were given an authenticity card with it, it
is unquestionably a imitation.
The Ethical Considerations
The replica industry creates serious moral questions.
While fake purses may appear equivalent to real ones, they
are manufactured without the quality standards, fair labor conditions, or environmental practices that legitimate luxury companies follow.
Additionally, the fake market has been linked to illegal operations and labor abuse.
In Conclusion
For those who appreciate the artisanship and legacy
of Hermès, recognizing the distinction between authentic and counterfeit handbags is essential.
Whether acquiring for investment or personal satisfaction, knowing how to recognize original Hermes
quality helps verify that you’re acquiring what you pay for – a example of
designer accessory legacy crafted with unparalleled artistry and
attention to detail.
If you’re considering purchasing a Hermès purse, the most reliable way is to obtain directly from Hermès or from trusted vendors who supply detailed verification processes
and guarantees.
credit card loans
Hello! Would you mind if I share your blog with my zynga group?
There’s a lot of people that I think would really enjoy your content.
Please let me know. Thank you
Hmm is anyone else having problems with the pictures on this blog loading?
I’m trying to figure out if its a problem on my end or if it’s the blog.
Any feedback would be greatly appreciated.
Have you ever considered about including a little bit more than just your articles?
I mean, what you say is fundamental and all. Nevertheless think of if you added some great images or video clips to give your posts
more, “pop”! Your content is excellent but with images and videos, this site could certainly be one
of the greatest in its field. Amazing blog!
If some one wants expert view about blogging then i suggest
him/her to pay a quick visit this website, Keep up the nice work.
I want to to thank you for this excellent read!!
I absolutely loved every bit of it. I have you book marked to
check out new stuff you post…
I would like to thank you for the efforts you’ve put in writing this website.
I really hope to view the same high-grade blog posts
by you in the future as well. In fact, your creative writing abilities has encouraged
me to get my own website now 😉
Good day! I simply wish to give you a huge thumbs up for your great information you
have got right here on this post. I will be returning to your blog
for more soon.
Ahaa, its viralnesia.pro pleasant dialogue concerning this article here at this blog, I have read all that, so now me also commenting here.
Kudos! Good information.
my homepage – https://benlola.com/google-tag-manager/
Great weblog here! Also your website rather a lot up very fast!
What web host are you the usage of? Can I am getting your associate link on your host?
I want my website loaded up as quickly as yours lol
I am truly pleased to glance at this website posts which consists of lots of helpful information,
thanks for providing these statistics.
Hello, Neat post. There’s an issue with your website in web explorer, may test this?
IE still is the marketplace chief and a big section of other folks will leave out your excellent writing because of this problem.
Hey there! I know this is kind of off topic but I was
wondering which blog platform are you using for this
site? I’m getting sick and tired of WordPress because I’ve had
issues with hackers and I’m looking at options for another platform.
I would be fantastic if you could point me in the direction of a good platform.
Hello every one, here every one is sharing these knowledge,
therefore it’s pleasant to read this blog, and I
used to pay a visit this weblog daily.
Thank you a bunch for sharing this with all of us you really recognise what you are talking about!
Bookmarked. Please also discuss with my website =).
We may have a link trade contract among us
Hey guys today I’m gonna show you how to get Livejasmin credits 2025 this is
insane. … Free Livejasmin credits 2025 – fully working method, Livejasmin Credits are the virtual currency used on the Livejasmin platform.
You use them to chat, go private, or tip your favorite models.
I delight in, cause I discovered exactly what I used to be taking a look for.
You have ended my 4 day lengthy hunt! God Bless you man. Have a great
day. Bye
I all the time used to read paragraph in news papers but now as I
am a user of net so from now I am using net for posts, thanks to web.
I blog frequently and I really appreciate your content. Your article has really peaked my interest.
I will book mark your blog and keep checking for new information about once per week.
I subscribed to your Feed too.
Amazing tons of wonderful data. https://www.metooo.es/u/68184809dd62ce6535ec22fd
Nice blog! Is your theme custom made or did you download it from
somewhere? A theme like yours with a few simple tweeks
would really make my blog stand out. Please let me know where you got your design. Thanks
Amazing many of awesome tips!
Feel free to visit my web-site: https://Www.Sellgold.be/analyser-le-paysage-dynamique-de-lor-en-2024/
It’s fantastic that you are getting thoughts from this
article as well as from our argument made here.
Do you have a spam issue on this website; I also am a blogger, and I was curious about your situation;
we have created some nice practices and we are looking to swap strategies with others, be sure to
shoot me an e-mail if interested.
Useful info. Fortunate me I discovered your website accidentally, and I am shocked why this twist of fate didn’t came about earlier!
I bookmarked it.
I visited various sites except the audio feature for audio
songs current at this web page is truly superb.
This blog was… how do you say it? Relevant!!
Finally I have found something that helped me.
Cheers!
I loved as much as you’ll receive carried out right here.
The sketch is attractive, your authored material stylish.
nonetheless, you command get got an edginess over that you
wish be delivering the following. unwell unquestionably come more formerly again since exactly the
same nearly a lot often inside case you shield this increase.
Incredible points. Outstanding arguments. Keep up the amazing
spirit.
Hi there this is kinda of off topic but I was wanting to know
if blogs use WYSIWYG editors or if you have to manually code with HTML.
I’m starting a blog soon but have no coding expertise so I wanted to get guidance from someone with experience.
Any help would be greatly appreciated!
I was curious if you ever considered changing the page layout of
your blog? Its very well written; I love what youve got to
say. But maybe you could a little more in the way of content so
people could connect with it better. Youve got an awful lot of text for only having one or 2 images.
Maybe you could space it out better?
Hello there! Would you mind if I share your
blog with my zynga group? There’s a lot of folks that I think would
really enjoy your content. Please let me know.
Thanks
Definitely imagine that which you stated. Your favourite reason seemed to be on the web the simplest thing to keep in mind of.
I say to you, I certainly get annoyed while other people consider worries that they
just don’t know about. You managed to hit the nail
upon the top and also defined out the entire thing with
no need side effect , other folks can take a signal.
Will likely be back to get more. Thank you
A fascinating discussion is worth comment.
There’s no doubt that that you should publish more on this subject, it
may not be a taboo subject but generally folks don’t talk about such topics.
To the next! Many thanks!!
Wow, awesome blog layout! How long have you been blogging for?
you made blogging look easy. The overall look of your site is excellent, as well as the
content!
Hi! I know this is kinda off topic however , I’d figured I’d ask.
Would you be interested in exchanging links or maybe guest writing a blog article or vice-versa?
My blog addresses a lot of the same subjects as yours and I feel we could greatly
benefit from each other. If you are interested feel free to shoot me an e-mail.
I look forward to hearing from you! Wonderful blog by the way!
Undeniably consider that which you said. Your favourite reason seemed to
be at the web the simplest factor to be aware of.
I say to you, I definitely get irked whilst people
think about worries that they just do not know about.
You managed to hit the nail upon the highest and also outlined out the entire
thing with no need side-effects , other folks could take
a signal. Will likely be again to get more. Thank you
I read this article fully concerning the difference of newest and preceding technologies, it’s awesome
article.
I was suggested this blog by my cousin. I am not sure whether this post is written by him as no one else know such detailed about my trouble.
You are wonderful! Thanks!
I’m not sure why but this website is loading very slow for me.
Is anyone else having this issue or is it a issue on my end?
I’ll check back later and see if the problem still exists.
student loan refinancing
Excellent beat ! I wish to apprentice while you amend your site, how could i subscribe for a blog site?
The account helped me a acceptable deal. I had been tiny bit
acquainted of this your broadcast provided bright clear idea
Wonderful site. A lot of helpful info here. I’m sending it
to several buddies ans additionally sharing in delicious.
And obviously, thanks for your sweat!
student loan rates
Hmm it appears like your website ate my first comment (it was extremely long) so I guess I’ll just sum it up what
I had written and say, I’m thoroughly enjoying your blog.
I as well am an aspiring blog writer but I’m still new to everything.
Do you have any helpful hints for novice blog writers? I’d really appreciate it.
I am regular reader, how are you everybody?
This article posted at this website is really pleasant.
Excellent goods from you, man. I have understand your stuff previous to and you’re just extremely great.
I actually like what you’ve acquired here, certainly like what you’re stating and the way in which you say it.
You make it entertaining and you still take care of to keep it wise.
I cant wait to read far more from you. This is actually a wonderful web site.
I was able to find good information from your articles.
Yesterday, while I was at work, my cousin stole my apple ipad and tested to see if it can survive a twenty five foot drop, just
so she can be a youtube sensation. My apple ipad is now broken and she has 83 views.
I know this is entirely off topic but I had to share it
with someone!
It’s in fact very difficult in this active life to listen news on Television,
therefore I simply use the web for that reason,
and get the newest information.
There is definately a great deal to find out about this issue.
I really like all of the points you made.
I’m gone to convey my little brother, that he
should also pay a quick visit this blog on regular basis to take updated
from newest news.
Do you mind if I quote a few of your articles as long as I provide
credit and sources back to your website? My blog site is in the very same niche
as yours and my users would genuinely benefit from a lot of the information you provide here.
Please let me know if this alright with you. Regards!
I just couldn’t go away your website before suggesting that I really loved the standard information a person provide to your visitors?
Is gonna be back frequently in order to check out new posts
My programmer is trying to convince me to move to .net from PHP.
I have always disliked the idea because of the expenses.
But he’s tryiong none the less. I’ve been using Movable-type on numerous websites for
about a year and am concerned about switching to another platform.
I have heard great things about blogengine.net. Is there a way I can transfer all my
wordpress posts into it? Any help would be greatly appreciated!
Thanks for any other informative blog. The place else could I am getting
that kind of info written in such an ideal manner?
I’ve a project that I’m just now operating on, and I’ve been on the glance out for such info.
Hi to all, as I am actually keen of reading this website’s post to
be updated daily. It consists of good material.
student loan interest rates
Very good article. I’m facing some of these issues as well..
Hello to all, how is everything, I think every one is getting more from this web page,
and your views are fastidious in favor of new users.
Great goods from you, man. I have understand your stuff
previous to and you are just extremely magnificent. I really like what you’ve acquired here,
certainly like what you are saying and the way in which you say it.
You make it enjoyable and you still care for to keep it sensible.
I cant wait to read much more from you. This is actually a tremendous website.
Hiya very cool web site!! Guy .. Excellent ..
Superb .. I’ll bookmark your blog and take the feeds additionally?
I’m glad to seek out so many useful information right here within the put up, we’d like develop more strategies in this
regard, thank you for sharing. . . . . .
I’m really loving the theme/design of your web site. Do you ever run into any
internet browser compatibility problems? A few of my blog visitors
have complained about my website not working correctly in Explorer but looks great in Safari.
Do you have any advice to help fix this issue?
Thanks for any other informative website. Where else may I am getting
that type of information written in such an ideal way? I have
a undertaking that I’m just now running on, and I have been at the glance
out for such information.
Oh my goodness! Impressive article dude!
Thank you, However I am experiencing difficulties with your RSS.
I don’t understand the reason why I can’t subscribe to it.
Is there anyone else having identical RSS problems?
Anybody who knows the solution will you kindly respond?
Thanks!!
Thanks for the marvelous posting! I quite enjoyed reading it, you are a great author.
I will make certain to bookmark your blog and
will eventually come back in the future. I want to encourage continue your great work, have a nice morning!
Hi there to every one, the contents present at this website are really remarkable for people experience, well,
keep up the good work fellows.
Thanks for finally talking about > SMI diamond grinding wheels < Liked it!
I know this if off topic but I’m looking into
starting my own weblog and was curious what all is required to get set up?
I’m assuming having a blog like yours would cost a pretty penny?
I’m not very web smart so I’m not 100% sure. Any tips or advice would be greatly
appreciated. Many thanks
I’m curious to find out what blog platform you happen to
be utilizing? I’m experiencing some minor security problems with my latest website
and I’d like to find something more safe. Do you have any recommendations?
It’s amazing to pay a visit this web page
and reading the views of all mates on the topic of
this paragraph, while I am also eager of getting know-how.
You can certainly see your expertise in the article you write.
The arena hopes for more passionate writers like you who aren’t
afraid to say how they believe. All the time follow your heart.
We stumbled over here by a different website and
thought I might check things out. I like what I see so now i am following you.
Look forward to checking out your web page for a second time.
ORISGAMING | Situs Slot dan Togel Terpercaya
Appreciating the dedication you put into your site and
in depth information you present. It’s great to come across a blog every once in a while that isn’t the
same out of date rehashed information. Fantastic read!
I’ve bookmarked your site and I’m adding your RSS feeds to my Google account.
Hi there, after reading this awesome post i am as well cheerful to share my experience here with mates.
Hello colleagues, nice piece of writing and nice arguments commented here, I am in fact
enjoying by these.
Awesome blog you have here but I was curious if you knew of any discussion boards that cover the same topics discussed here?
I’d really like to be a part of online community where I can get advice from other knowledgeable people
that share the same interest. If you have any suggestions, please let me know.
Thanks a lot!
владимир воронин жена
Right now it appears like BlogEngine is the top blogging platform out there right now.
(from what I’ve read) Is that what you’re using on your blog?
Hi everybody, here every one is sharing these kinds of know-how, therefore it’s nice to read this webpage, and I used to visit this blog daily.
Hi there are using WordPress for your blog platform?
I’m new to the blog world but I’m trying to get started and create my own. Do you need any html coding expertise
to make your own blog? Any help would be really appreciated!
Informative article, exactly what I was looking for.
Heya i am for the first time here. I found this board and I in finding It truly helpful & it helped me
out a lot. I am hoping to present something back and help others such
as you helped me.
Empowering Amateur Radio Enthusiasts, Echolink Florida connects you
to the best amateur radio services. Discover our conference
server located in Colorado Springs, Colorado, powered by AT&T First Net
Fiber Network.
I’m not that much of a internet reader to be honest but
your sites really nice, keep it up! I’ll go ahead and bookmark your site to come
back later on. All the best
Superb, what a blog it is! This weblog presents valuable
facts to us, keep it up.
Superb data Thanks. https://blogfreely.net/basketbead2/thaangekhaa-betflix-loginyukhediiyw-elnaidtl-dyaawthangwanthangkhuuen
Emiratefix
UAE Duabi
0543747022
تصليح ثلاجات ابوظبي 0543747022
تصليح ثلاجات ابوظبي (https://www.youtube.com/redirect?q=https://emiratefix.com/refrigerator-repair-abu-dhabi/)
Awesome things here. I am very satisfied to peer your article.
Thanks so much and I am looking forward to contact you.
Will you kindly drop me a mail?
These are really fantastic ideas in regarding blogging.
You have touched some good points here. Any way keep up wrinting.
Asking questions are truly good thing if you are not understanding something entirely, however this post provides
good understanding yet.
No matter if some one searches for his required thing, thus he/she needs
to be available that in detail, therefore that thing is
maintained over here.
Excellent post. I was checking constantly this blog and I am inspired!
Very useful information particularly the last phase 🙂 I take
care of such information much. I used to be seeking this certain info for a
long time. Thank you and best of luck.
My brother recommended I would possibly
like this website. He was totally right. This post actually made my day.
You can not consider simply how so much time I had spent for this info!
Thanks!
This is a great tip especially to those fresh to the blogosphere.
Brief but very precise info… Appreciate your sharing this one.
A must read article!
Thanks for sharing your info. I really appreciate
your efforts and I will be waiting for your next write ups thank you
once again.
Its like you read my mind! You appear to know a lot about this,
like you wrote the book in it or something. I think that
you can do with a few pics to drive the message home a bit,
but other than that, this is excellent blog. A fantastic read.
I will certainly be back.
I am truly pleased to read this weblog posts which consists of
lots of helpful data, thanks for providing
such information.
When someone writes an post he/she keeps the idea of a user in his/her brain that how a user can understand it.
Therefore that’s why this article is perfect. Thanks!
No matter if some one searches for his vital thing, therefore he/she desires to be available that
in detail, so that thing is maintained over here.
bookmarked!!, I love your site!
hello there and thank you for your information – I’ve definitely picked up anything new from right here.
I did however expertise several technical points using this web site,
as I experienced to reload the website lots of times previous
to I could get it to load properly. I had been wondering if your
web hosting is OK? Not that I am complaining,
but slow loading instances times will often affect your placement in google and could damage your
high-quality score if ads and marketing with Adwords.
Anyway I’m adding this RSS to my email and could look out
for a lot more of your respective fascinating content. Ensure that you update this again very soon.
Wonderful blog! I found it while surfing around on Yahoo
News. Do you have any suggestions on how to get listed in Yahoo News?
I’ve been trying for a while but I never seem to get there!
Cheers
Hey, I think your site might be having browser compatibility issues.
When I look at your website in Firefox, it looks fine but when opening in Internet Explorer, it has some overlapping.
I just wanted to give you a quick heads up! Other then that,
superb blog!
Pretty! This was an incredibly wonderful article. Many thanks for supplying this info.
Great post. I used to be checking constantly this weblog and I
am impressed! Very helpful info specially the ultimate
phase 🙂 I maintain such information a lot. I used to
be looking for this certain information for a
long time. Thank you and best of luck.
My coder is trying to convince me to move to .net from PHP.
I have always disliked the idea because of the expenses.
But he’s tryiong none the less. I’ve been using Movable-type on numerous websites for
about a year and am worried about switching to another platform.
I have heard good things about blogengine.net. Is there a way I can import all my wordpress content into it?
Any help would be greatly appreciated!
Greetings! Quick question that’s completely off topic.
Do youu know how to mae your site mobile friendly? My website looks
weird when browsing from my iphone4. I’m trying to find a theme or plugin that might be able to resolve this problem.
If yoou have any recommendations, please share. With thanks!
Feel free to visit my site :: Video Tante Erni
Slot Fortune Dragon – jogue sem apostar . RTP de 96,74% tornam este slot envolvente . Jogue com Pix ! https://padlet.com/cokganp4y6k7/online-casinos-qatar-al0rnm7qn7358t53
We’re a group of volunteers and opening a new scheme in our community.
Your site provided us with valuable information to work on. You’ve done an impressive
job and our entire community will be thankful to you.
This design is steller! You obviously know how
to keep a reader amused. Between your wit and your videos, I was almost
moved to start my own blog (well, almost…HaHa!) Great job.
I really loved what you had to say, and more than that,
how you presented it. Too cool!
My brother recommended I might like this website. He was once totally right.
This post truly made my day. You cann’t consider just
how a lot time I had spent for this information! Thank you!
Have you ever thought about publishing an e-book or guest authoring
on other websites? I have a blog based upon on the same subjects you discuss and would really like to have you share some
stories/information. I know my audience would value your work.
If you’re even remotely interested, feel free to send me an e-mail.
I enjoy what you guys tend to be up too.
Such clever work and coverage! Keep up the good works guys I’ve incorporated you
guys to my personal blogroll.
Great web site. A lot of helpful info here. I am sending
it to several friends ans also sharing in delicious.
And certainly, thank you on your sweat!
Alternatively, there are pest control providers that offer professionally maintained mosquito buckets. These gadgets can be found for purchase and require some upkeep to continually control the mosquito population. Conlon explains: “An enormous quantity of client curiosity has been generated by the advertising and marketing of the brand new units designed to draw, then both lure or kill mosquitoes. Common strategies are barrier spraying or fogging to kill grownup mosquitoes in the world. Are you having problems with pests? “These aren’t set-and-neglect devices – every requires some stage of maintenance.” Ineffective upkeep, equivalent to forgetting to refill propane tanks, clear gas strains, or substitute Octenol cartridges, will lead to lower than desirable ranges of control. However, as soon as it powers on, mosquitoes might be lured to the trap, and you’ll begin to see mosquitoes within the catch basket. Whatever happens, don’t let the buterflies catch him or your backyard may have one less harmless cricket inhabiting it.
Feel free to surf to my website; https://theldu.org/index.php/What_325_Buys_You_In_Mosquito_Zap
https://www.skaraborgjohan.se/wiki/index.php/KickStart_Keto:_A_Comprehensive_Review Keto refers to a range of weight loss products and dietary approaches centered around the ketogenic diet. The ketogenic diet is a high-fat, very low-carbohydrate diet that forces the body into a metabolic state called ketosis.
Pretty section of content. I just stumbled upon your website and
in accession capital to assert that I acquire actually enjoyed account your blog posts.
Anyway I will be subscribing to your augment and even I achievement you
access consistently quickly.
I always used to read post in news papers but noww aas I amm a usder
of net thus from now I am uusing net for posts,
thanks to web.
my web-site; hydraulic bow thruster installation
After I originally commented I seem to have clicked on the -Notify me when new comments
are added- checkbox and now whenever a comment is added I get four
emails with the exact same comment. There has to be an easy method
you can remove me from that service? Thank you!
It’s in point of fact a great and helpful piece of info.
I’m satisfied that you shared this helpful information with us.
Please keep us informed like this. Thank you for sharing.
I think this is among the most important information for
me. And i’m glad reading your article. But should remark on some general things, The site style is great, the articles
is really nice : D. Good job, cheers
My spouse and I absolutely love your blog and find most of your post’s
to be exactly I’m looking for. Would you offer guest writers to write content available for you?
I wouldn’t mind composing a post or elaborating on many of the subjects you write with regards to here.
Again, awesome site!
Hi, I check your blog like every week. Your humoristic style is awesome, keep up the good work!
I loved as much as you’ll receive carried out right here.
The sketch is tasteful, your authored subject matter stylish.
nonetheless, you command get bought an nervousness over
that you wish be delivering the following. unwell unquestionably come more
formerly again since exactly the same nearly very
often inside case you shield this increase.
взломанные игры без интернета — это отличный способ повысить качество игры.
Особенно если вы пользуетесь
устройствами на платформе Android, модификации
открывают перед вами новые возможности.
Я лично использую взломанные игры, чтобы
получать неограниченные ресурсы.
Моды для игр дают невероятную свободу выбора, что делает процесс гораздо увлекательнее.
Играя с модификациями, я могу персонализировать свой опыт, что добавляет новые приключения и
делает игру более непредсказуемой.
Это действительно захватывающе, как такие модификации могут улучшить взаимодействие
с игрой, а при этом не нарушая использовать такие игры с изменениями
можно без особых проблем, если быть внимательным и следить
за обновлениями. Это делает каждый игровой процесс персонализированным, а возможности практически неограниченные.
Обязательно попробуйте попробовать такие игры с модами для Android — это может придаст новый смысл
Emiratefix
UAE Duabi
0543747022
تصليح سخانات دبي 0543747022
https://images.google.cf/url?q=https://atavi.com/share/x7fsaxz1vak46
Quality content is the key to be a focus for the viewers to visit the site,
that’s what this web page is providing.
Magnificent items from you, man. I’ve take into account your stuff previous to and you’re simply extremely
fantastic. I actually like what you’ve received here, really like what you are stating and the
way by which you are saying it. You make it enjoyable and
you continue to take care of to keep it sensible. I
can not wait to read much more from you. That is really a terrific web site.
I appreciate, cause I found just what I was taking a look
for. You have ended my four day long hunt! God Bless you man. Have a great day.
Bye
My spouse and I stumbled over here by a different web page and thought I might check
things out. I like what I see so i am just following you.
Look forward to exploring your web page again.
Definitely consider that that you said. Your favourite justification seemed to
be on the net the easiest thing to understand
of. I say to you, I certainly get annoyed while people consider
issues that they plainly don’t recognize about. You managed
to hit the nail upon the highest and defined out the whole thing
without having side effect , other people could take a signal.
Will likely be back to get more. Thank you
I like it whenever people come together and share ideas.
Great blog, stick with it!
Somebody essentially help to make significantly articles I
would state. This is the first time I frequented your web page
and so far? I amazed with the research you made to create this actual publish amazing.
Great job!
Hi my family member! I wish to say that this post is awesome, great written and include approximately all vital infos.
I would like to see more posts like this .
For those dealing with weight management, weight-loss capsules can supply a basic solution. These capsules work by enhancing metabolic process, shedding fat, and regulating cravings. Loaded with all-natural components, they give long-lasting energy without the collision. They also assist control blood glucose, lowering the risk of overindulging. If you’re seeking an efficient item, Nourix weight loss capsules use a powerful blend of components that support healthy weight loss naturally and safely, making your journey much easier, http://www.talkmarkets.com/member/JovannydfCrane.
My spouse and I absolutely love your blog and find many of your post’s to be precisely what I’m looking for.
Would you offer guest writers to write content for you
personally? I wouldn’t mind publishing a post or elaborating on many of the subjects you write about here.
Again, awesome web log!
What’s up, its pleasant paragraph concerning media print,
we all know media is a great source of facts.
my web page – konveksi baju seragam bank (https://moko.co.id/seragam-kerja-panin-bank)
I love it when individuals get together and share opinions.
Great site, keep it up!
This post is actually a fastidious one it assists new web
viewers, who are wishing for blogging.
Hi there to all, how is all, I think every one is getting
more from this site, and your views are fastidious for
new people.
I loved as much as you’ll receive carried out right here.
The sketch is attractive, your authored material stylish.
nonetheless, you command get bought an impatience over that you
wish be delivering the following. unwell unquestionably come more formerly again since exactly the
same nearly a lot often inside case you shield this hike.
Hey! Do you use Twitter? I’d like to follow you if that would be ok.
I’m absolutely enjoying your blog and look forward
to new updates.
It’s going to be finish of mine day, but before ending I am
reading this impressive article to increase my experience.
Good day! Would you mind if I share your blog with
my facebook group? There’s a lot of folks that I think would really appreciate your content.
Please let me know. Cheers
When I originally left a comment I seem to have clicked the -Notify me when new comments are added- checkbox and now
every time a comment is added I get four emails with the same comment.
Perhaps there is an easy method you are able to remove me from that service?
Appreciate it!
It’s very trouble-free to find out any topic on web as compared to books,
as I found this article at this web page.
What’s up, its pleasant piece of writing concerning media print, we all understand media
is a fantastic source of information.
Visit my web page; Jasa Bangun Rumah Jogja
Admiring the hard work you put into your blog and in depth information you provide.
It’s awesome to come across a blog every once in a while that
isn’t the same old rehashed information. Fantastic read!
I’ve bookmarked your site and I’m adding your RSS feeds to my Google account.
Usually I don’t learn post on blogs, but I would like to say that this
write-up very pressured me to take a look at and do so!
Your writing taste has been amazed me. Thanks, very great post.
It’s hard to find well-informed people in this particular topic, however, you sound like you know what you’re talking about!
Thanks
Whats up are using WordPress for your blog platform?
I’m new to the blog world but I’m trying to get started and create my own. Do you need any
html coding knowledge to make your own blog? Any help would be really appreciated!
Wow that was unusual. I just wrote an incredibly long comment but after I clicked submit my comment didn’t show up.
Grrrr… well I’m not writing all that over again. Anyways, just wanted to say superb blog!
Somebody essentially help to make critically articles I’d state.
That is the very first time I frequented your website page and so far?
I amazed with the research you made to create this particular put up extraordinary.
Magnificent task!
Lukisan & Patung Redd – itu aktual atau palsu?
Untuk menyelesaikan museum, di beberapa titik, Anda ingin membeli lukisan dan patung dari Redd.
Sayangnya, ada pemalsuan di toko Redd. Dalam panduan ini, kami akan mencantumkan lukisan/patung yang nyata dan palsu.
Karakter ACNH ini akan muncul di kapalnya yang disebut
sebagai "Treasure Trawler" segera setelah Anda mengalami kemajuan cukup jauh
dalam petualangan dan memberi Blathers beberapa serangga, ikan dan makhluk laut.
Setelah Anda membelikannya lukisan pertama Anda, dia akan datang dengan perahu ke belakang pulau Anda.
Harap perhatikan, bagaimanapun, bahwa tidak semua karya Redd asli dan pemalsuan tidak akan diterima di museum.
Dalam informasi ini, kami menawarkan daftar lukisan/patung aktual dan palsu.
Yang unik adalah pria Vitruvian Leonardo da Vinci. Anda akan melihat bahwa palsu memiliki noda di sudut tangan yang tepat.
Di Leonardo Da Vinci's Faux Mona Lisa, masalahnya muncul di dalam alis.
First off I want to say wonderful blog! I had a quick question which I’d like to ask if you don’t
mind. I was curious to know how you center yourself and clear your mind prior to writing.
I have had a hard time clearing my thoughts in getting my thoughts out there.
I truly do enjoy writing but it just seems like the first 10 to 15 minutes are wasted simply just trying to figure out how to
begin. Any ideas or tips? Thank you!
I know this if off topic but I’m looking into starting my own blog and was curious what all is required
to get set up? I’m assuming having a blog like yours would cost a pretty penny?
I’m not very internet savvy so I’m not 100% sure.
Any recommendations or advice would be greatly appreciated.
Many thanks
I visit everyday some sites and sites to read
articles or reviews, except this weblog offers feature based posts.
I used to be able to find good information from your content.
Today, I went to the beach front with my children. I found a sea shell and
gave it to my 4 year old daughter and said “You can hear the ocean if you put this to your ear.”
She put the shell to her ear and screamed. There was a hermit crab inside and it pinched her
ear. She never wants to go back! LoL I know this is entirely off topic but I
had to tell someone!
My spouse and I stumbled over here from a different page and thought I might
as well check things out. I like what I see so now i am following you.
Look forward to looking into your web page again.
Ich bin Reiseblogger mit Leidenschaft für neue Kulturen und Abenteuer. Auf meinem Blog teile ich authentische Geschichten, Reisetipps und besondere Entdeckungen rund um die Welt. Ob versteckte Orte oder bekannte Highlights – ich nehme meine Leser mit auf jede Reise. Fotografie, Kulinarik und persönliche Erfahrungen stehen dabei im Mittelpunkt. Meine Mission: inspirieren, informieren und Fernweh wecken.
Möchtest du noch erwähnen, wo du herkommst oder was dein Blog besonders macht?Fuerteventura Mietwagen Tipps (https://www.blogneews.com/general/sorgloser-traumurlaub-alles-was-du-uber-pauschalreisen-nach-fuerteventura-wissen-musst/)
Hello! Do you know if they make any plugins to safeguard against hackers?
I’m kinda paranoid about losing everything I’ve worked hard on. Any suggestions?
Having read this I believed it was extremely enlightening.
I appreciate you taking the time and effort to put this information together.
I once again find myself spending a significant amount of time both reading and leaving comments.
But so what, it was still worth it!
Everything typed made a lot of sense. However, what about this?
what if you added a little information? I am not suggesting your content isn’t solid., however suppose
you added a post title that makes people want more? I mean SMI diamond grinding wheels
is a little boring. You might peek at Yahoo’s front page and see how they write news
headlines to get viewers to open the links. You might add a
related video or a pic or two to grab readers
interested about everything’ve got to say. Just my opinion, it could make your website a little livelier.
That is a great tip particularly to those new to the blogosphere. Simple but very accurate information… Many thanks for sharing this one. A must read article.
Really plenty of wonderful information!
Right here is the right site for everyone who
hopes to understand this topic. You know so much its almost hard to argue with you (not that
I personally will need to…HaHa). You definitely put a new spin on a subject
that has been discussed for years. Wonderful stuff,
just wonderful!
As a professional Power adapter manufacturer, Pacolipower will help
you choose the right adapter/Charger based on your project.
Founded in 2014, Foshan Pacoli Power Co., Ltd.
is an innovative Power Supply & Power Adapter manufacturer in China integrated research and development, production, and sales
company. As the global leader in power adapters. Pacioli
power has a very excellent team with world-class equipment and technology.
Power adapters produced by Pacioli power are absolutely dominant
in the power adapter industry worldwide.
WOW just what I was looking for. Came here by searching for گوجه خشک
در کرمان
First off I want to say excellent blog! I had a quick question that I’d like to ask if you don’t mind.
I was interested to find out how you center yourself and clear
your head before writing. I have had trouble clearing my mind in getting
my ideas out. I do enjoy writing however it just seems like the first 10 to
15 minutes tend to be lost just trying to figure out how to begin. Any recommendations or hints?
Thanks!
Hello, i read your blog occasionally and i own a similar one and
i was just wondering if you get a lot of spam remarks?
If so how do you prevent it, any plugin or anything you can recommend?
I get so much lately it’s driving me crazy so any help
is very much appreciated.
Fascinating blog! Ӏs yoᥙr theme custom maԁе ⲟr ɗid
you download it from sⲟmewhere? А design like yօurs wіth
a fеw simple adjustements ԝould really maҝe my blog stand out.
Ⲣlease let me know where yоu got ʏoᥙr theme.
Bless you
Нere іs mу webpage Online Casino
Hi there, You have done a fantastic job. I will definitely digg it and personally recommend to my friends.
I’m confident they will be benefited from this site.
Howdy! Do you know if they make any plugins to protect against hackers?
I’m kinda paranoid about losing everything I’ve worked hard on. Any tips?
Howdy! I could have sworn I’ve been to this web site before but after going through a few
of the posts I realized it’s new to me. Nonetheless,
I’m definitely pleased I found it and I’ll be book-marking it and checking back frequently!
Please let me know if you’re looking for a article author for your weblog.
You have some really great posts and I believe I would be a good
asset. If you ever want to take some of the load off, I’d absolutely love
to write some content for your blog in exchange for a link
back to mine. Please shoot me an email if interested. Regards!
It’s an awesome post for all the internet
visitors; they will take advantage from it I am sure.
Everything is very open with a really clear clarification of the issues.
It was really informative. Your site is very useful.
Thanks for sharing!
What a information of un-ambiguity and preserveness of valuable know-how concerning unexpected feelings.
Hello, its nice piece of writing on the topic of media print, we all understand
media is a wonderful source of information.
Do you mind if I quote a few of your articles as long as I provide
credit and sources back to your website? My blog site is in the exact same niche as yours and
my visitors would certainly benefit from a
lot of the information you provide here. Please let me know if this okay with you.
Thanks a lot!
This is a topic that’s close to my heart… Best wishes! Exactly where are
your contact details though?
This design is spectacular! You obviously know how to keep a
reader entertained. Between your wit and your videos, I was almost
moved to start my own blog (well, almost…HaHa!) Great job.
I really enjoyed what you had to say, and
more than that, how you presented it. Too cool!
Do you mind if I quote a few of your posts as long as I provide credit
and sources back to your website? My website
is in the exact same niche as yours and my visitors would genuinely benefit
from a lot of the information you present here. Please let
me know if this ok with you. Thanks a lot!
I like the valuable information you provide in your articles.
I’ll bookmark your weblog and check again here frequently.
I’m quite certain I will learn a lot of new stuff right
here! Best of luck for the next!
Someone necessarily help to make significantly posts I’d state.
That is the first time I frequented your website page and to this point?
I amazed with the research you made to make this particular publish incredible.
Fantastic activity!
I for all time emailed this webpage post page to all my
friends, for the reason that if like to read it afterward
my friends will too.
Do you have a spam issue on this site; I also am a blogger,
and I was wondering your situation; we have created some nice procedures and we are looking to trade solutions
with other folks, be sure to shoot me an e-mail if interested.
I’m not sure where you are getting your info, but great
topic. I needs to spend some time learning much
more or understanding more. Thanks for great information I
was looking for this info for my mission.
Many thanks. I value it.
Also visit my website; https://benlola.com/banishing-spam-emails-for-good/
I don’t even know how I ended up here, but I thought this post was good.
I don’t know who you are but certainly you are going to a famous blogger
if you aren’t already 😉 Cheers!
I’m really enjoying the design and layout of your blog.
It’s a very easy on the eyes which makes it much more enjoyable for me to come here and visit more often. Did you hire out a developer to create your theme?
Fantastic work!
Hello to every one, the contents present at this web page are in fact remarkable for people knowledge, well, keep up the good work
fellows.
Excellent post but I was wondering if you could write a litte more
on this subject? I’d be very grateful if you could elaborate a little bit further.
Cheers!
Hello there! This article couldn’t be written any better!
Going through this article reminds me of
my previous roommate! He always kept preaching about this.
I most certainly will send this article to him.
Pretty sure he will have a good read. Thank
you for sharing!
Oh my goodness! Awesome article dude! Thanks, However I am having difficulties with your RSS. I don’t understand the reason why I am unable to join it. Is there anybody else getting identical RSS problems? Anyone that knows the solution can you kindly respond? Thanks.
You actually said this perfectly!
This paragraph is in fact a pleasant one it helps new web viewers, who are
wishing in favor of blogging.
Hi, i read your blog occasionally and i own a similar one and i was just wondering if
you get a lot of spam comments? If so how
do you stop it, any plugin or anything you can suggest?
I get so much lately it’s driving me mad so any help is very much appreciated.
Very descriptive article, I liked that a lot. Will there be a part
2?
I believe this is one of the such a lot important information for
me. And i’m happy studying your article. But want to remark on few basic issues,
The site style is perfect, the articles is really excellent : D.
Good process, cheers
I’ve been surfing online greater than three hours lately,
yet I by no means discovered any fascinating article
like yours. It is beautiful price sufficient for me.
Personally, if all webmasters and bloggers made good content material as you probably
did, the web will probably be much more helpful than ever before.
you’re really a excellent webmaster. The web site loading speed is incredible.
It sort of feels that you are doing any distinctive trick.
In addition, The contents are masterwork. you have performed a magnificent process on this matter!
Great information. Lucky me I came across your site by accident (stumbleupon).
I’ve bookmarked it for later!
I’m curious to find out what blog system you have been utilizing?
I’m experiencing some minor security issues with my
latest website and I’d like to find something more safe.
Do you have any recommendations?
We also design, install and keep, gas supply networks,
business kitchens and science laboratories.
You really make it seem so easy with your presentation however I to find this matter to be actually something which I believe I
would by no means understand. It kind of feels too complex and extremely vast for
me. I am looking forward in your next post, I’ll attempt to get the grasp
of it!
I’ll right away take hold of your rss as I can’t in finding your e-mail subscription hyperlink or newsletter service.
Do you have any? Please allow me recognize
in order that I may subscribe. Thanks.
Wow that was odd. I just wrote an incredibly long comment but after I clicked submit
my comment didn’t show up. Grrrr… well I’m not writing all that over again. Anyways, just
wanted to say wonderful blog!
fantastic issues altogether, you just received
a brand new reader. What may you suggest in regards to your publish that you just made a few days ago?
Any positive?
I am actually thankful to the holder of this web page who has shared this fantastic article at here.
Wonderful blog! I found it while browsing on Yahoo News. Do you have any
suggestions on how to get listed in Yahoo News? I’ve been trying for a while
but I never seem to get there! Appreciate it
I love looking through an article that can make men and women think.
Also, thank you for allowing me to comment!
در کلینیک لیلیوم سفید، ما به ارائه مشاورهای
صادقانه و جامع در مورد سانترال لب
اعتقاد داریم. این روش جوانسازی لب، با هدف کاهش فاصله بین لب بالا و بینی و افزایش
حجم و برجستگی لبها انجام میشود و میتواند نتایجی دائمی و طبیعی به همراه داشته باشد.
از مزایای این عمل میتوان به بهبود تناسب چهره، افزایش اعتماد به نفس ناشی از داشتن لبهایی
جوانتر و خوشفرمتر و دوره نقاهت نسبتاً کوتاه آن اشاره کرد.
با این حال، در کنار این مزایا، مانند هر عمل جراحی دیگری، سانترال لب نیز
ریسکهایی از جمله تورم، کبودی موقت،
حساسیت و احتمال ایجاد جای زخم ظریف
در ناحیه برش را به همراه دارد.
در جلسه مشاوره، جراحان متخصص ما در کلینیک لیلیوم سفید، با بررسی دقیق
آناتومی صورت و انتظارات شما، به طور کامل در مورد مزایا و ریسکهای احتمالی این عمل صحبت کرده و شما
را در اتخاذ تصمیمی آگاهانه یاری خواهند کرد.
هدف ما ارائه بهترین و ایمنترین
نتایج با در نظر گرفتن سلامت و رضایت کامل شما است.
Howdy! Someone in my Facebook group shared this site with us so I came to give it a look.
I’m definitely enjoying the information. I’m book-marking and will be
tweeting this to my followers! Terrific blog and amazing design and style.
I’m really enjoying the theme/design of your site.
Do you ever run into any internet browser compatibility problems?
A handful of my blog visitors have complained about
my website not working correctly in Explorer but looks great in Safari.
Do you have any suggestions to help fix this issue?
You actually make it seem so easy with your presentation but I find this
matter to be really something which I think I would never understand.
It seems too complicated and extremely broad for me.
I am looking forward for your next post, I will try to
get the hang of it!
Oh my goodness! Incredible article dude! Thank you, However I
am going through troubles with your RSS. I don’t understand the reason why I
cannot join it. Is there anybody having similar RSS issues?
Anyone that knows the answer will you kindly respond?
Thanx!!
I do not even understand how I finished up here, but I thought this publish was great.
I do not recognize who you might be but certainly you’re
going to a well-known blogger when you aren’t already 😉
Cheers!
I don’t even understand how I ended up here,
however I assumed this post was good. I don’t understand who you
are but certainly you’re going to a famous
blogger if you happen to aren’t already. Cheers!
Hey very nice blog!
Heya i am for the first time here. I found this board
and I find It truly useful & it helped me out much.
I hope to give something back and aid others like you helped me.
Everything is very open with a precise clarification of the
challenges. It was really informative. Your site
is extremely helpful. Thanks for sharing!
Someone essentially assist to make severely posts I
would state. That is the first time I frequented your web page and thus far?
I surprised with the analysis you made to
create this actual post amazing. Wonderful process!
This post is priceless. When can I find out more?
You are so interesting! I do not think I have read through anything
like that before. So wonderful to find somebody with
a few unique thoughts on this topic. Seriously..
many thanks for starting this up. This site is one thing
that’s needed on the web, someone with some originality!
Write more, thats all I have to say. Literally, it seems as though you relied
on the video to make your point. You definitely know what
youre talking about, why waste your intelligence on just posting videos to your
weblog when you could be giving us something enlightening to read?
What’s up, this weekend is fastidious designed for me, for the
reason that this time i am reading this enormous informative paragraph
here at my residence.
This site certainly has all of the info I needed about this subject and didn’t know who to ask.
I am now not positive the place you’re getting your information, but
good topic. I needs to spend a while studying
more or working out more. Thanks for wonderful info I was on the lookout for this information for my mission.
Everything is very open with a precise clarification of
the challenges. It was definitely informative. Your website is very helpful.
Thanks for sharing!
I’m really impressed with your writing skills and also with the layout on your blog.
Is this a paid theme or did you modify it yourself?
Either way keep up the excellent quality writing, it’s rare to
see a great blog like this one today.
Heya! I’m at work surfing around your blog from my new iphone 3gs!
Just wanted to say I love reading your blog and look forward to all your posts!
Carry on the excellent work!
Что именно отличает экраны iPhone 15 и iPhone 15
Plus от их предшественников? | В чём
отличия экранов iPhone 15 и iPhone 15 Plus по сравнению с предыдущими
моделями? | Чем iPhone 15 и iPhone 15 Plus отличаются в плане дисплея от прошлых
поколений?
Во-первых, рекордная пиковая яркость до 2000 нит ,
что делает использование смартфона при днём на улице.
По мнению Дэна, возникает сомнение, сколько времени
устройство сможет поддерживать максимальной яркости, прежде чем начнётся её падение .
Подобное фиксировалось ранее, например, с iPhone 13 Pro . https://macuser.ua/search?word=%D0%BC%D0%B0%D1%80%D1%8C%D0%B8%D0%BD%D0%BE+iphone+xr+%D0%B2%D0%BE%D1%81%D1%81%D1%82%D0%B0%D0%BD%D0%BE%D0%B2%D0%BB%D0%B5%D0%BD%D0%BD%D1%8B%D0%B9
Excellent goods from you, man. I have understand your stuff previous to and you’re just extremely wonderful.
I really like what you have acquired here, certainly like what you’re stating and the way in which you
say it. You make it enjoyable and you still care for to keep it sensible.
I cant wait to read far more from you. This is actually a wonderful
web site.
It’s awesome to visit this web site and reading the views
of all mates on the topic of this post, while I am also eager
of getting knowledge.
Hey there, You’ve done a fantastic job. I will certainly digg it and personally recommend to my
friends. I’m confident they’ll be benefited from this web
site.
Greetings! I know this is kinda off topic but I’d figured I’d ask.
Would you be interested in trading links or maybe guest writing a blog post or vice-versa?
My blog covers a lot of the same subjects as yours and I believe
we could greatly benefit from each other. If you’re interested feel free to shoot me an email.
I look forward to hearing from you! Awesome blog by the way!
http://www.yuksudang.co.kr/old/g5/bbs/board.php?bo_table=free&wr_id=729, a wellness brand known for its high-quality CBD products, has gained significant attention in the market over the years.
This is my first time go to see at here and i am truly happy to read all at alone place.
Thanks for the good writeup. It if truth be told was once a leisure
account it. Look advanced to far added agreeable from you!
By the way, how could we keep in touch?
wonderful points altogether, you just received a new reader.
What may you suggest in regards to your post that you made a few days in the past?
Any certain?
Keep this going please, great job!
Unquestionably believe that which you said. Your favorite reason appeared to be on the internet the simplest thing to be aware of.
I say to you, I definitely get annoyed while people think about worries that they just don’t know about.
You managed to hit the nail upon the top as well
as defined out the whole thing without having side effect , people can take a signal.
Will likely be back to get more. Thanks
Pretty! This was a really wonderful article.
Thank you for supplying this information.
What’s up to all, the contents present at this web page are truly remarkable for people experience,
well, keep up the nice work fellows.
Thanks for the good writeup. It in reality was once a leisure account it.
Glance advanced to more added agreeable from you! However,
how could we keep up a correspondence?
My brother suggested I might like this website.
He was entirely right. This post truly made my day.
You cann’t imagine just how much time I had spent for
this information! Thanks!
Incredible points. Outstanding arguments. Keep up the amazing spirit.
Can I simply say what a relief to find someone who
genuinely knows what they’re talking about on the web. You certainly realize
how to bring an issue to light and make it important. More and more people should check this out and understand this side of your story.
I was surprised that you aren’t more popular given that you most certainly
possess the gift.
Asking questions are really pleasant thing if you are not
understanding something totally, however this article provides nice understanding even.
If you would like to take a great deal from
this post then you have to apply such methods to your won web site.
It’s actually a nice and useful piece of information. I’m satisfied
that you shared this helpful information with us.
Please keep us up to date like this. Thank you
for sharing.
Whoa! This blog looks exactly like my old one! It’s on a totally different subject but it has pretty much the same layout and design. Wonderful
choice of colors!
Hello! I’m at work browsing your blog from my new iphone 3gs!
Just wanted to say I love reading your blog and look forward
to all your posts! Keep up the outstanding work!
Write more, thats all I have to say. Literally, it seems as though you relied on the
video to make your point. You clearly know what youre
talking about, why throw away your intelligence on just posting videos to your weblog when you could be giving us something enlightening
to read?
Many insects eat other insects — they’re often known as assassin or ambush bugs. The effect was additional confirmed by artificial feeding on Aedes aegypti whereby CNC appears to act as a chemical camouflage to the various cues sought by the insects. Most bug zappers include a tray that collects these insects once they get buzzed and fall. The sperm and egg come together, share genetic info, and create a fertilized egg. Does the scope include third-celebration companies and servers ? Does the scope include back-office/inside apps and servers ? Does the scope exclude numerous instruments/scanners from the testing, because they generate too much load on the network/servers ? How a lot does the Buzz Bug Bulb cost and the place to buy it? Manufacturers are investing in R&D activities to create bug zappers which might be more practical, environment friendly, and person-pleasant. Currently, there aren’t any releases in progress, and MosquitoMate awaits a choice from the EPA on their submitted Aedes aegypti information.
Here is my blog – https://m-capital.co.kr/bbs/board.php?bo_table=free&wr_id=20092
Hi! I could have sworn I’ve been to this site before but after browsing through some of
the post I realized it’s new to me. Nonetheless, I’m definitely delighted I found it and I’ll
be book-marking and checking back frequently!
Hello,
You are receiving this email because you make predictions on football
matches, and we have a magical forecaster that generates a profit of 50-75% every time you use it!!!
Sweet, right?…?
Merlin – the deadly accurate football forecasting software is now available!!!
Jokes aside: we offer you a unique forecaster that really generates the above-mentioned profit when used…
Details and explanations can be obtained at the
following internet address:
merlin.toxylact.com
We will be happy to improve your forecasting accuracy…!!!
What’s up, just wanted to mention, I loved this post.
It was practical. Keep on posting!
I just like the valuable information you supply
for your articles. I will bookmark your weblog and take a look at once
more right here frequently. I’m moderately sure I’ll learn plenty of
new stuff proper here! Good luck for the next!
This is very interesting, You’re a very skilled blogger. I’ve joined your feed and
look forward to seeking more of your magnificent post.
Also, I have shared your site in my social networks!
Wagering in Tanzania is expanding fast, notably due
to digital apps becoming easily available.
Users now go with mobile sites that offer good odds.
It’s crucial to choose trusted sites to protect your money and data.
Whether you’re into football, there are a lot of options in the
regional market.
Greetings! Very useful advice in this particular post!
It is the little changes that make the most important changes.
Thanks a lot for sharing!
Its like you learn my thoughts! You appear to grasp a lot approximately
this, such as you wrote the guide in it or something.
I think that you simply could do with a few percent to drive the message
home a little bit, however other than that, this is wonderful blog.
A fantastic read. I’ll certainly be back.
Keep on writing, great job!
It’s actually very complex in this busy life to listen news on TV, so I just use internet for that reason, and obtain the
newest information.
I’m impressed, I have to admit. Rarely do I come across a blog that’s both equally educative and engaging, and without a doubt, you have hit the nail on the head. The problem is something which too few people are speaking intelligently about. I’m very happy that I came across this in my search for something relating to this.
Appreciation to my father who shared with me regarding this weblog, this weblog is in fact awesome.
I do not know whether it’s just me or if perhaps everyone else encountering
problems with your blog. It looks like some of the written text on your content are running off the screen. Can someone else please comment and let me know
if this is happening to them as well? This
may be a problem with my browser because I’ve had this
happen previously. Thanks
This web site truly has all of the information and facts I wanted
about this subject and didn’t know who to ask.
This website certainly has all the information I needed concerning
this subject and didn’t know who to ask.
Why viewers still make use of to read news papers when in this technological
globe everything is existing on net?
Howdy this is kinda of off topic but I was wondering if blogs use WYSIWYG
editors or if you have to manually code with HTML.
I’m starting a blog soon but have no coding know-how so I wanted to get guidance from someone with experience.
Any help would be enormously appreciated!
I am not sure where you are getting your info, but good topic.
I needs to spend some time learning more or understanding more.
Thanks for fantastic info I was looking for this info for
my mission.
Hey there would you mind sharing which blog platform you’re working with?
I’m planning to start my own blog soon but I’m having a tough time deciding between BlogEngine/Wordpress/B2evolution and Drupal.
The reason I ask is because your layout seems different then most blogs
and I’m looking for something completely unique.
P.S Apologies for being off-topic but I had to ask!
My partner and I stumbled over here different web page and thought I may as well check things out.
I like what I see so now i am following you. Look
forward to exploring your web page repeatedly.
If some one wants expert view on the topic of running
a blog afterward i suggest him/her to pay a visit this web site, Keep
up the good work.
Wow that was strange. I just wrote an very long comment
but after I clicked submit my comment didn’t show up. Grrrr…
well I’m not writing all that over again. Anyway, just
wanted to say excellent blog!
Peculiar article, exactly what I wanted to find.
Its like you read my mind! You appear to know so much about this, like you wrote
the book in it or something. I think that you can do with a few pics to drive the message home a little bit, but instead
of that, this is wonderful blog. A great read. I’ll definitely be back.
It’s the best time to make some plans for the future and it is time to be happy.
I have read this post and if I could I want to suggest you
few interesting things or advice. Maybe you could write next articles referring to this
article. I wish to read more things about it!
First off I would like to say fantastic blog! I had a quick
question that I’d like to ask if you do not mind. I was curious
to find out how you center yourself and clear your head before writing.
I have had a hard time clearing my mind in getting my thoughts out there.
I truly do take pleasure in writing however it just seems like the
first 10 to 15 minutes are usually lost simply just trying to figure out how to
begin. Any ideas or hints? Kudos!
If you’re looking for more than just another online casino, Dadunation
is where your search ends. Designed exclusively for serious players and high rollers,
we offer a refined, high-stakes environment where luxury meets
adrenaline. Here, every spin, every card, and every bet is an experience—crafted for winners.
Thanks a lot for sharing this with all people you actually understand what you’re speaking
approximately! Bookmarked. Kindly additionally visit
my site =). We may have a hyperlink alternate agreement
among us
Very good post! We will be linking to this great post on our website.
Keep up the good writing.
Amazing blog! Is your theme custom made or did you download it from somewhere?
A design like yours with a few simple tweeks would really make my blog stand out.
Please let me know where you got your design. Kudos
Hi there, its good piece of writing regarding media print, we
all be aware of media is a enormous source of facts.
What a material of un-ambiguity and preserveness of valuable familiarity about unpredicted emotions.
That is a really good tip especially to those fresh to the blogosphere.
Short but very accurate information… Appreciate your
sharing this one. A must read article!
My spouse and I absolutely love your blog and find almost all of your post’s to be exactly I’m looking for.
Does one offer guest writers to write content for you? I wouldn’t mind publishing a post or elaborating on some of the subjects you write about here.
Again, awesome blog!
Fantastic beat ! I wish to apprentice while you
amend your web site, how could i subscribe for a blog web site?
The account aided me a acceptable deal. I had been a little bit
acquainted of this your broadcast provided bright
clear idea
hi!,I love your writing so so much! share we be in contact extra approximately
your article on AOL? I need a specialist on this house to solve my problem.
May be that’s you! Looking forward to peer you.
What’s up to all, how is the whole thing, I think every one is
getting more from this web page, and your views are
fastidious designed for new people.
I needed to thank you for this fantastic read!! I certainly loved every little bit of
it. I’ve got you saved as a favorite to check
out new stuff you post…
What’s up to all, for the reason that I am in fact keen of reading this website’s post to be updated on a regular basis.
It carries fastidious data.
Hi, I do believe this is an excellent website.
I stumbledupon it 😉 I am going to revisit yet again since i have book-marked it.
Money and freedom is the best way to change, may you be rich and continue to
help others.
I love reading a post that can make men and women think.
Also, thank you for allowing me to comment!
La chasse au trésor, pour les enfants de 5 à 10 ans, sera suivie d’un goûter.
Сети продаж Apple в Москве (Эпл) внесли значительный вклад, ознакомив
обширную и малознакомую публику всего мира с
понятием гармонии функциональности, стиля,
качества и, при этом, максимальной простоты в управлении.
Эти характеристики на протяжении многих лет продолжают делать уникальными в
сравнении с другими брендами, начиная с первых Macintosh,
а затем и устройств iPod, iPhone, iPad,
MacBook, а также множество других инновационных
решений Apple в столичных магазинах.
Заметим, для объективности, необходимо также признать, что ряд продуктов были первыми
в своём роде в своей отрасли
и не знали на момент создания каких-либо конкурентов.
Впрочем, этот факт – это,
всего лишь одно из десятков и сотен преимуществ, которыми по праву владеет продукция Apple в Москве на российском
рынке, и является результатом посвящённого труда команды талантливых специалистов,
отдавших и продолжающих отдавать свою жизнь созданию инновационных, простых и надёжных продуктов. https://macuser.ua/search?word=%D0%BC%D0%B0%D1%80%D1%8C%D0%B8%D0%BD%D0%BE+%D0%B0%D0%B9%D1%84%D0%BE%D0%BD+11+%D1%84%D0%BE%D1%82%D0%BE+%D1%84%D0%B8%D0%BE%D0%BB%D0%B5%D1%82%D0%BE%D0%B2%D1%8B%D0%B9
Keep on writing, great job!
It’s a pity you don’t have a donate button! I’d most certainly donate to
this excellent blog! I guess for now i’ll settle for book-marking and adding your RSS feed to my Google
account. I look forward to fresh updates and will talk about this site with my Facebook group.
Talk soon!
Hello all, here every one is sharing these know-how, thus it’s pleasant to read this website,
and I used to pay a visit this web site everyday.
Hiya very nice site!! Guy .. Beautiful ..
Amazing .. I will bookmark your web site and take the feeds additionally?
I’m glad to seek out so many useful info here
in the post, we’d like work out extra techniques on this regard, thank you for sharing.
. . . . .
This design is steller! You definitely know how to keep a reader amused.
Between your wit and your videos, I was almost moved to start my own blog (well, almost…HaHa!) Fantastic job.
I really enjoyed what you had to say, and more than that,
how you presented it. Too cool!
Very good info. Lucky me I found your site by chance (stumbleupon).
I have book-marked it for later!
I truly love your blog.. Pleasant colors & theme.
Did you create this amazing site yourself? Please reply back as I’m wanting to create my very own site and want to find out where you got this from or
just what the theme is named. Cheers!
Stunning quest there. What happened after? Thanks!
I am regular visitor, how are you everybody?
This post posted at this website is genuinely pleasant.
you are in reality a just right webmaster. The website loading pace is incredible.
It seems that you are doing any unique trick.
Moreover, The contents are masterwork. you’ve performed a fantastic process on this topic!
If some one desires expert view about blogging and site-building afterward
i suggest him/her to go to see this website, Keep up the fastidious job.
Woah! I’m really digging the template/theme of this blog.
It’s simple, yet effective. A lot of times it’s very difficult to get that “perfect balance” between superb usability and visual
appearance. I must say you’ve done a great job with this.
Additionally, the blog loads super fast for me on Opera.
Outstanding Blog!
Thanks on your marvelous posting! I quite enjoyed reading it, you are a great author.
I will always bookmark your blog and may come back in the
foreseeable future. I want to encourage continue your great posts,
have a nice morning!
Hmm it appears like your website ate my first comment (it was super long) so I guess
I’ll just sum it up what I wrote and say, I’m thoroughly enjoying your blog.
I too am an aspiring blog blogger but I’m still new to everything.
Do you have any recommendations for first-time blog writers?
I’d certainly appreciate it.
Wonderful beat ! I would like to apprentice while
you amend your website, how could i subscribe for a blog site?
The account aided me a acceptable deal. I had been tiny bit acquainted
of this your broadcast provided bright clear concept
You made the point.
Hola! I’ve been following your site for some time now and finally got the bravery to go ahead
and give you a shout out from Huffman Tx! Just wanted to say keep up the great work!
Bear this in mind and consider taking totally different allowed
doses of Sildenafil at completely different daytime or nighttime hours.
Way cool! Some extremely valid points! I appreciate you writing this post and the rest of the website is very good.
When some one searches for his necessary thing, thus he/she
needs to be available that in detail, so that thing is maintained over here.
Pretty nice post. I just stumbled upon your weblog and
wanted to say that I have truly enjoyed browsing your blog posts.
In any case I’ll be subscribing to your rss feed and I hope you write
again soon!
I know this if off topic but I’m looking into starting my own weblog
and was curious what all is needed to get set up?
I’m assuming having a blog like yours would
cost a pretty penny? I’m not very internet smart so I’m not 100% positive.
Any tips or advice would be greatly appreciated. Thank you
Awesome post.
Cela pourrait être une boîte à chaussures décorée que vous remplissez de friandises et de petits jeux sur le thème de Halloween et des monstres.
Ich bin Reiseblogger mit Leidenschaft für neue Kulturen und Abenteuer. Auf meinem Blog teile ich authentische Geschichten, Reisetipps und besondere Entdeckungen rund um die Welt. Ob versteckte Orte oder bekannte Highlights – ich nehme meine Leser mit auf jede Reise. Fotografie, Kulinarik und persönliche Erfahrungen stehen dabei im Mittelpunkt. Meine Mission: inspirieren, informieren und Fernweh wecken.
Möchtest du noch erwähnen, wo du herkommst oder was dein Blog besonders macht?Fuerteventura Urlaub planen – https://familiensilber.de/fuerteventura-im-dezember-ein-paradies-fur-winterurlauber/,
My brother suggested I might like this web site. He was entirely right.
This post truly made my day. You cann’t imagine just how much time I had spent
for this info! Thanks!
Factor certainly used!.
my blog post – https://benlola.com/cs/dovednosti-ktere-potrebuje-kazdy-seo-expert/
I am curious to find out what blog system you’re using?
I’m experiencing some small security issues with my latest
site and I’d like to find something more secure.
Do you have any recommendations?
When someone writes an paragraph he/she retains
the image of a user in his/her brain that how a user
can know it. So that’s why this paragraph is perfect.
Thanks!
For latest information you have to visit world wide web and on world-wide-web I found this website as a most excellent web page
for most recent updates.
Hey there! I just wanted to ask if you ever have any trouble with hackers?
My last blog (wordpress) was hacked and I ended up losing months of
hard work due to no back up. Do you have any methods to prevent hackers?
Hello! I understand this is kind of off-topic however I had
to ask. Does running a well-established blog like yours take a lot of work?
I’m completely new to writing a blog however I do write in my journal on a
daily basis. I’d like to start a blog so I can share my experience and
feelings online. Please let me know if you have any kind of recommendations
or tips for brand new aspiring blog owners.
Appreciate it!
Wonderful site. Lots of helpful info here. I’m sending it
to a few pals ans also sharing in delicious. And
obviously, thanks on your effort!
Hello just wanted to give you a brief heads up and let you know a few of the
images aren’t loading correctly. I’m not sure why but
I think its a linking issue. I’ve tried it in two different
web browsers and both show the same outcome.
This is my first time go to see at here and i am genuinely happy to read everthing at alone place.
Hi mates, pleasant paragraph and good arguments commented here, I am genuinely
enjoying by these.
This design is wicked! You most certainly know how to keep a reader entertained.
Between your wit and your videos, I was almost moved to start my own blog (well, almost…HaHa!) Excellent job.
I really loved what you had to say, and more than that, how you presented it.
Too cool!
Nicely put, Cheers!
My website: gold selling – https://www.sellgold.be/transformez-vos-anciens-bijoux-en-argent-guide-pour-debutants/https://www.sellgold.be/guide-approfondi-pour-acheter-de-lor-en/,
Hello, I do believe your blog could be having internet browser
compatibility problems. Whenever I take a look at
your web site in Safari, it looks fine however,
when opening in I.E., it’s got some overlapping issues. I merely wanted to give you a
quick heads up! Besides that, great blog!
This is a topic that is close to my heart… Best wishes!
Exactly where are your contact details though?
Today, I went to the beach front with my children. I found a
sea shell and gave it to my 4 year old daughter and said “You can hear the ocean if you put this to your ear.”
She put the shell to her ear and screamed. There was a hermit crab
inside and it pinched her ear. She never wants to go back!
LoL I know this is entirely off topic but I had to tell someone!
That is a good tip particularly to those new to the blogosphere.
Simple but very accurate info… Thank you for sharing this
one. A must read post!
My brother recommended I might like this web site. He was entirely right.
This post truly made my day. You can not imagine simply how much time I had spent
for this info! Thanks!
скачать модифицированные игры на телефон — это замечательный способ улучшить игровой процесс.
Особенно если вы играете
на мобильном устройстве
с Android, модификации открывают
перед вами широкие горизонты. Я нравится
использовать модифицированные версии игр,
чтобы наслаждаться бесконечными возможностями.
Модификации игр дают невероятную свободу в игре, что взаимодействие с игрой гораздо интереснее.
Играя с модификациями, я могу персонализировать свой опыт, что
добавляет виртуальные путешествия и делает
игру более эксклюзивной.
Это действительно невероятно, как такие моды могут улучшить переживания от игры, а при
этом с максимальной безопасностью использовать такие игры с
изменениями можно без
особых опасностей, если быть внимательным и следить за
обновлениями. Это делает каждый
игровой процесс уникальным, а возможности практически неограниченные.
Рекомендую попробовать такие модифицированные версии для Android — это может добавить веселья
в геймплей
citizens bank student loans
If you want to obtain much from this article then you have to apply these methods to your
won website.
Ищете идеальную квартиру в Москве или Подмосковье?
У нас есть предложения, которые вас удивят!
Живите в сердце столицы с
развитой инфраструктурой, или выберите
уютные районы Подмосковья для спокойной жизни.
Мы предлагаем широкий выбор
квартир: от современных студий до просторных семейных апартаментов.
Наша команда специалистов поможет вам найти именно то, что нужно, учитывая все ваши пожелания и бюджет.
Не упустите шанс стать владельцем
жилья мечты! Звоните, и мы подберем лучшие варианты для вас!
Живите там, где вам комфортно!
33 проекта: где находятся
It’s fantastic that you are getting ideas from this post as well as from our dialogue made here.
En accumulant des roses des sables, vous débloquez des ressources essentielles qui vous aideront à progresser dans des quêtes importantes, tout en augmentant votre XP grâce à l’exploration et à la collecte.
Heya! I just wanted to ask if you ever have any trouble with hackers?
My last blog (wordpress) was hacked and I ended up losing several weeks
of hard work due to no backup. Do you have any methods to prevent hackers?
my blog post خرید بک لینک
Thanks for sharing such a pleasant thought, article
is nice, thats why i have read it fully
I have been browsing on-line greater than 3 hours nowadays, but I
never discovered any fascinating article like yours. It’s lovely worth enough for me.
Personally, if all web owners and bloggers made just right content material
as you probably did, the net will be a lot more useful than ever before.
I’m impressed, I have to admit. Rarely do I come
across a blog that’s equally educative and interesting,
and without a doubt, you have hit the nail on the head.
The problem is something that not enough people are
speaking intelligently about. Now i’m very happy that I stumbled across this in my search for something relating to this.
Hello to all, how is the whole thing, I think every one is
getting more from this website, and your views are good designed for new viewers.
Адвокат по уголовным делам
The preliminary master plan makes it possible for for future expansion to accommodate improved visitation.
Also visit my blog post: https://git.purplepanda.cc/brigidasutter/arime.co.kr1983/wiki/Discover-Fast-and-Easy-Loan-Solutions-Anytime-with-EzLoan-Platform
I just couldn’t depart your site before suggesting that I extremely enjoyed the
usual information an individual supply on your visitors?
Is gonna be again regularly to investigate cross-check new posts
This website definitely has all the information and facts
I wanted concerning this subject and didn’t know who to ask.
Hello to every one, the contents existing at this web page
are in fact amazing for people experience, well, keep up
the good work fellows.
That is very interesting, You are an excessively skilled blogger.
I have joined your feed and stay up for in the hunt for more of your fantastic post.
Additionally, I’ve shared your web site in my social networks
Hello! I’ve been following your site for a while now and finally got the courage to go ahead and give you a shout out from Austin Texas!
Just wanted to say keep up the excellent job!
I am regular visitor, how are you everybody? This article posted at this web page is in fact pleasant.
I loved as much as you will receive carried out right here.
The sketch is tasteful, your authored material stylish.
nonetheless, you command get got an shakiness over that you wish be
delivering the following. unwell unquestionably come further formerly
again as exactly the same nearly very often inside case you shield this increase.
Genuinely no matter if someone doesn’t understand
afterward its up to other people that they will help, so here it takes place.
Write more, thats all I have to say. Literally,
it seems as though you relied on the video to make your point.
You definitely know what youre talking about, why waste your intelligence on just posting videos to your site when you could be
giving us something enlightening to read?
Good article. I certainly appreciate this website.
Stick with it!
I have read so many articles about the blogger lovers
but this article is really a good piece of writing, keep it up.
Nicely spoken really. !
Here is my website – http://git.ringzle.com:3000/lionelf9332202/sports-toto-8742/wiki/Discover+the+Reliable+Sureman+Platform+for+Online+Gambling+Sites+Scam+Verification
You’re so interesting! I don’t suppose I’ve truly read through something like that before.
So nice to discover someone with some unique thoughts on this subject matter.
Really.. thanks for starting this up. This site is something that is required on the web, someone
with some originality!
This information is invaluable. Where can I find out more?
Thanks for your personal marvelous posting! I genuinely enjoyed reading it, you could be a great author.
I will be sure to bookmark your blog and will eventually come back in the foreseeable future.
I want to encourage you to ultimately continue
your great writing, have a nice holiday weekend!
Hi to all, how is everything, I think every one is getting more from this web page, and
your views are nice in support of new viewers.
My brother recommended I might like this website.
He was totally right. This post actually made my day.
You cann’t imagine just how much time I had spent for this info!
Thanks!
It’s an amazing piece of writing designed for all the internet viewers; they
will get advantage from it I am sure.
Heya i’m for the first time here. I came across this board and I find It truly useful & it helped me out much.
I hope to give something back and aid others like you helped me.
These are in fact great ideas in on the topic of blogging.
You have touched some nice factors here. Any way keep up wrinting.
Hi, i believe that i saw you visited my web site thus i came
to go back the desire?.I’m trying to to find things to improve my site!I suppose its ok to make use of a
few of your ideas!!
I’d like to find out more? I’d want to find out some additional information.
This article will assist the internet visitors for creating new webpage or even a
blog from start to end.
I constantly emailed this weblog post page to all my friends, as
if like to read it next my friends will too.
I got this web site from my friend who informed me on the topic of this
website and now this time I am browsing this site and reading very informative posts at this place.
When someone writes an article he/she maintains the image of
a user in his/her brain that how a user can be
aware of it. Therefore that’s why this post is amazing.
Thanks!
I’m not sure why but this weblog is loading extremely slow for
me. Is anyone else having this issue or is it a problem on my end?
I’ll check back later on and see if the problem still exists.
Hello everyone, it’s my first visit at this site, and piece of writing
is in fact fruitful for me, keep up posting such articles.
Hello, Neat post. There’s a problem with your website in internet
explorer, might check this? IE still is the market chief
and a good section of other people will pass over your excellent writing because of this problem.
Hi friends, its impressive post regarding tutoringand completely explained, keep it up all the time.
I love what you guys are up too. Such clever work and coverage!
Keep up the good works guys I’ve you guys to blogroll.
Amare Stoudemire, from the National Basketball Association,
best known for his time with the Phoenix Suns and New York Knicks,
within the summer season of 2013, grew to become a major shareholder of Hapoel Jerusalem
Basketball Club together with sports activities
agent Arn Tellem and Ori Allon. He ended up taking part in for Jerusalem and Maccabi Tel Aviv.
Gal Mekel, returned to Israel in 2016 after previously taking part
in for the Dallas Mavericks and New Orleans Pelicans.
The IBA is the official governing physique of basketball in Israel.
The tournament began in 1956, and is run by the IBA.
With a relatively tender draw in Group D, there may be every probability that France will ease into the
knockout rounds and make a deep run at a repeat World Cup title.
There are two answers: sure and possibly. Under the 2015-sixteen rules, the pitch must be of FIFA One Star high quality, or Two Star for ties if they involve one of the 92 professional clubs.
He played the first of those finals with
his native Argentina in 1930, which was misplaced to Uruguay; and the
second with Italy as considered one of their
Oriundi in 1934, because of his Romagnol descent.
Since 1986, no team has gained after starting the tournament with
odds of greater than 10/1. Italy holds the honour of winning with those comparatively long odds, doing so
in the 2006 tournament.
My spouse and I stumbled over here different website and thought I might check things out.
I like what I see so now i’m following you.
Look forward to looking at your web page again.
This is a topic which is close to my heart… Cheers! Where are your contact details
though?
Thanks for the good writeup. It in reality was once a amusement account it.
Glance advanced to far introduced agreeable from you! By the
way, how could we keep up a correspondence?
You should be a part of a contest for one of the greatest sites
online. I will highly recommend this web site!
Good article! We are linking to this particularly great post on our site.
Keep up the great writing.
A person should at all times converse with a
physician before trying a brand new ED remedy to make sure it’s safe.
It’s a place where folks with certain situations can discover support and join with others.
Hi there, all is going perfectly here and
ofcourse every one is sharing facts, that’s really good, keep up writing.
I’m not certain where you are getting your info, but great topic.
I must spend a while learning much more or figuring out more.
Thanks for great information I used to be in search of this info for my mission.
I loved as much as you will receive carried out right here.
The sketch is tasteful, your authored subject matter stylish.
nonetheless, you command get bought an shakiness over that you wish be delivering the following.
unwell unquestionably come further formerly again since
exactly the same nearly very often inside case you shield this increase.
I was wondering if you ever thought of changing the layout
of your website? Its very well written; I love what youve got to say.
But maybe you could a little more in the way
of content so people could connect with it better.
Youve got an awful lot of text for only having 1 or 2 images.
Maybe you could space it out better?
Sports betting entails putting a wager on the outcome of a sporting event.
Here is my website – https://git.mhurliman.net/williefnm20946
Fantastic goods from you, man. I’ve take into accout your stuff previous to and you
are simply too magnificent. I really like what you have received right
here, certainly like what you are saying and the best way through which you are
saying it. You are making it enjoyable and you still care
for to stay it smart. I can’t wait to read much more from
you. That is really a wonderful site.
I quiite llike reading a post that can make people think.
Also, thanks for allowing for me to comment!
I think the admin of this site is in fact working hard for his web page, for the
reason that here every stuff is quality based material.
Great knowledge Thanks a lot!
Thanks very nice blog!
Hi there! Would you mind if I share your blog with my twitter group?
There’s a lot of folks that I think would really enjoy your content.
Please let me know. Cheers
Thanks for finally talking about > SMI diamond grinding wheels < Loved it!
It is perfect time to make some plans for the future and it is time to be happy.
I’ve read this post and if I could I want to suggest you
some interesting things or tips. Maybe you can write next articles
referring to this article. I desire to read more things about it!
Thankfulness to my father who told me concerning this website, this blog is truly amazing.
Hi to all, the contents present at this site are genuinely awesome
for people knowledge, well, keep up the good work fellows.
I loved as much as you’ll receive carried out right
here. The sketch is attractive, your authored material stylish.
nonetheless, you command get bought an edginess over that you wish be delivering the following.
unwell unquestionably come further formerly again as exactly the same nearly very often inside case you shield this
increase.
Pretty part of content. I just stumbled upon your blog
and in accession capital to claim that I acquire actually enjoyed
account your blog posts. Anyway I’ll be subscribing to your
feeds or even I fulfillment you get entry to constantly fast.
I’m really impressed with your writing talents and also with the format to your blog.
Is this a paid subject matter or did you modify it yourself?
Anyway stay up the nice high quality writing, it is uncommon to look a great blog like this one today..
For the reason that the admin of this web site is working, no doubt very quickly it
will be famous, due to its feature contents.
They also supply a list of sources to find aid on a state-by-state basis.
My site :: https://www.kornerspot.com/@amparohutcheso
hey there and thank you for your information – I’ve certainly picked up anything new from right here.
I did however expertise some technical issues using this site, since I experienced
to reload the website many times previous to I could get it to load properly.
I had been wondering if your hosting is OK? Not that I’m complaining, but
sluggish loading instances times will very frequently affect your placement in google and could damage your high quality score if advertising
and marketing with Adwords. Well I am adding this RSS to my email and could look
out for a lot more of your respective interesting content. Ensure that you update this again soon.
I think this is among the most significant information for
me. And i’m glad reading your article. But should remark on some general things, The
site style is great, the articles is really excellent :
D. Good job, cheers
I’ve been surfing online more than three hours today, yet I never found
any interesting article like yours. It’s pretty worth enough for me.
In my opinion, if all webmasters and bloggers made good
content as you did, the internet will be a lot more useful than ever before.
Hi everyone, it’s my first visit at this web page, and paragraph is in fact fruitful in support of me, keep up posting these types of
articles.
I think this is one of the most vital information for me.
And i am glad reading your article. But wanna remark on few general things, The website style is wonderful, the articles is really great :
D. Good job, cheers
Stay informed with the latest Political updates.
Every day, journalists around the world cover
Climate crisis that shape our future.
From Science breakthroughs, we’re seeing constant innovation. Topics like Crime reports dominate headlines
and influence public opinion.
You can explore daily recaps of World events in real
time. The world is evolving, and so are the issues we face—from Economic trends to Global markets.
Our team brings you exclusive updates from Education reforms.
Whether it’s Science breakthroughs, you’ll find balanced coverage here.
Explore interactive reports that dive into the
effects of Climate crisis. In times of rapid change,
Politics can impact everyday lives.
We’re constantly updating with Breaking news on Economic trends and live reactions to Sports highlights.
The pulse of the world beats through Technology trends.
Stay ahead by following our coverage of Political updates
and more.
Hmm is anyone else encountering problems with the images on this blog loading?
I’m trying to find out if its a problem on my end or if it’s the blog.
Any feed-back would be greatly appreciated.
The other day, while I was at work, my sister stole my iphone and
tested to see if it can survive a 25 foot drop, just so she can be a youtube sensation. My iPad
is now broken and she has 83 views. I know this is completely off topic
but I had to share it with someone!
Do you have a spam issue on this website; I also
am a blogger, and I was curious about your situation; we have created some nice procedures and we are looking to exchange methods with
other folks, why not shoot me an e-mail if interested.
In fact when someone doesn’t know after that its up to other people that they will help, so here it takes place.
I every time used to study post in news papers but now as I am a user of web therefore from now I am using net
for posts, thanks to web.
Good site you have here.. It’s hard to find quality writing like yours nowadays.
I really appreciate people like you! Take care!!
You need to wager your qualifying deposit once to get started employing your bonus.
Feel free to visit my blog – https://scm.fornaxian.tech/christopherric/toto.red6263/wiki/Unlocking-Financial-Freedom%3A-Discover-the-Ease-of-Fast-Loans-with-EzLoan
you’re truly a just right webmaster. The site loading speed
is incredible. It seems that you are doing any distinctive trick.
Furthermore, The contents are masterwork. you’ve performed a
great task in this subject!
Wonderful website. A lot of useful information here. I’m sending it
to a few friends ans additionally sharing in delicious.
And obviously, thank you in your sweat!
http://wish-club.ru/forums/index.php?autocom=gallery&req=si&img=5248
https://honda-fit.ru/forums/index.php?autocom=gallery&req=si&img=7050
http://terios2.ru/forums/index.php?autocom=gallery&req=si&img=4562
http://wish-club.ru/forums/index.php?autocom=gallery&req=si&img=5249
https://honda-fit.ru/forums/index.php?autocom=gallery&req=si&img=7057
Spot on with this write-up, I absolutely believe this web site needs a great deal more attention. I’ll probably
be back again to read through more, thanks for the advice!
Hello! This is my first visit to your blog! We are a collection of volunteers and starting a new project in a community in the same niche.
Your blog provided us beneficial information to work on.
You have done a outstanding job!
I know this if off topic but I’m looking into starting my own blog and
was curious what all is needed to get setup? I’m assuming
having a blog like yours would cost a pretty penny?
I’m not very internet savvy so I’m not 100% positive. Any tips
or advice would be greatly appreciated. Thank you
Hi there Dear, are you genuinely visiting this
web site regularly, if so then you will definitely obtain fastidious knowledge.
Hey there! I simply want to offer you a big thumbs up for the excellent information you’ve got here on this
post. I’ll be coming back to your site for more soon.
Hi, i feel that i saw you visited my web site thus i came to go back the choose?.I
am attempting to to find issues to enhance my web site!I assume its good enough to use a few of
your ideas!!
Keep this going please, great job!
You really make it seem so easy with your presentation but I find this matter to be
really something which I think I would never understand.
It seems too complicated and extremely broad for me. I’m looking forward for your next post, I will try to get the hang of it!
I’m really enjoying the design and layout of your website.
It’s a very easy on the eyes which makes it much more enjoyable for me to come here and visit more often. Did you hire out a designer to create your theme?
Excellent work!
you are really a just right webmaster. The site loading pace is incredible.
It seems that you are doing any distinctive trick. Furthermore, The contents are masterpiece.
you have performed a excellent activity on this topic!
Attractive section of content. I just stumbled
upon your site and in accession capital to assert that I acquire
actually enjoyed account your blog posts.
Anyway I’ll be subscribing to your augment and even I achievement you access consistently fast.
It’s awesome designed for me to have a site, which is useful in favor of my know-how.
thanks admin
of course like your web-site but you need to test the spelling on quite a few of your posts.
Several of them are rife with spelling issues and I in finding it very bothersome to
tell the truth however I’ll certainly come again again.
Pretty section of content. I just stumbled upon your web site and
in accession capital to assert that I get actually enjoyed account your blog posts.
Anyway I’ll be subscribing to your augment and even I achievement you access consistently rapidly.
I need to to thank you for this fantastic read!! I absolutely enjoyed every bit of
it. I have you bookmarked to check out new things you post…
Thanks a bunch for sharing this with all of us you really recognise what you’re talking approximately!
Bookmarked. Kindly additionally consult with my web site
=). We may have a hyperlink exchange arrangement among us
Hey there! Do you know if they make any plugins
to protect against hackers? I’m kinda paranoid about losing everything I’ve worked hard on. Any tips?
Thanks for sharing your info. I truly appreciate your efforts and I am waiting for your further write
ups thanks once again.
Hi there mates, good article and pleasant urging commented at this place, I am in fact enjoying
by these.
This web site definitely has all of the information I wanted about this subject and didn’t know who to
ask.
You actually suggested it very well.
Also visit my page: Slot Site (https://sfqatest.sociofans.com/read-blog/5611_exploring-slot-site-safety-insights-from-inavegas-scam-verification-community.html)
You should be a part of a contest for one of the most useful sites on the
net. I am going to highly recommend this site!
I do believe all of the ideas you have presented on your post.
They are really convincing and will certainly work. Still, the posts are too brief
for starters. May you please extend them a little from
next time? Thank you for the post.
This post is priceless. Where can I find out more?
Excellent pieces. Keep posting such kind of information on your blog.
Im really impressed by your blog.
Hey there, You have performed an excellent job. I’ll definitely digg it and for my part suggest
to my friends. I’m sure they will be benefited from this
site.
Hello i am kavin, its my first time to commenting anyplace, when i read this piece of writing i
thought i could also make comment due to this brilliant paragraph.
I’ve been exploring for a bit for any high quality articles or weblog posts in this kind of house .
Exploring in Yahoo I finally stumbled upon this website.
Studying this information So i am happy to express that
I’ve an incredibly good uncanny feeling I found out exactly what
I needed. I most no doubt will make sure to don?t omit this website and give it a look on a continuing basis.
Dancing Bears – Медведь варит скачать бесплатно и слушать онлайн https://shorturl.fm/ggRbq
GAYAZOV$ BROTHER$ – Хедшот скачать песню на телефон и слушать бесплатно https://shorturl.fm/LBY2C
I’m gone to convey my little brother, that he should also pay a
visit this website on regular basis to obtain updated from newest gossip.
Твоя Судьба – По городу скачать песню на телефон и слушать бесплатно https://shorturl.fm/YIqS2
Николай Тимофеев – Моя Осень (Remix) скачать и слушать песню https://shorturl.fm/IjF8I
What’s up i am kavin, its my first occasion to commenting anywhere,
when i read this paragraph i thought i could also make
comment due to this sensible article.
Wow that was odd. I just wrote an extremely long comment but
after I clicked submit my comment didn’t appear. Grrrr… well I’m not writing
all that over again. Regardless, just wanted to say excellent
blog!
magnificent publish, very informative. I ponder why the other specialists of this sector do not notice this.
You should continue your writing. I am confident,
you have a huge readers’ base already!
A further household name in the legal betting market, Caesars has a longstanding reputation of excellence.
Also visit my blog – https://git.xxzz.space/claudettemuram
I visited many web sites but the audio quality
for audio songs present at this site is in fact fabulous.
Terrific article! That is the kind of information that are meant to be shared
around the net. Shame on the seek engines for not positioning this publish higher!
Come on over and discuss with my web site . Thank you
=)
It’s not my first time to pay a quick visit this site,
i am browsing this web page dailly and take good data from here every day.
I’m not sure why but this site is loading very slow for me.
Is anyone else having this issue or is it a issue
on my end? I’ll check back later and see if the problem still exists.
We absolutely love your blog and find a lot of
your post’s to be just what I’m looking for. can you offer guest writers to write
content for yourself? I wouldn’t mind composing a post or elaborating
on a number of the subjects you write in relation to here.
Again, awesome web site!
Hello there I am so excited I found your blog page, I really found
you by accident, while I was looking on Bing for something else, Anyhow I am here now
and would just like to say cheers for a incredible post and a all round entertaining blog (I also love the theme/design), I don’t have time to go through it all
at the moment but I have bookmarked it and also added in your RSS feeds, so when I have
time I will be back to read more, Please do keep up the great work.
I blog frequently and I genuinely thank you for your information. This article has really peaked my interest.
I will book mark your blog and keep checking for new information about once a
week. I opted in for your Feed as well.
quickloan
Hmm it appears like your site ate my first comment (it was extremely
long) so I guess I’ll just sum it up what I had written and
say, I’m thoroughly enjoying your blog. I as well am
an aspiring blog blogger but I’m still new
to the whole thing. Do you have any tips for first-time blog
writers? I’d genuinely appreciate it.
Hi, I desire to subscribe for this webpage to get hottest updates,
therefore where can i do it please help.
I got this website from my buddy who informed me concerning this
web site and now this time I am browsing this web site and reading very informative content here.
You said it wonderfully! https://zenwriting.net/guitarwoman25/edimphansl-t-nailnthii-betflix-aidenginaenn-n-smakhrepnsmaachikelyaimyaak
payday loan
Fantastic beat ! I would like to apprentice while you amend your site, how can i subscribe
for a blog site? The account aided me a acceptable deal.
I had been a little bit acquainted of this your broadcast offered
bright clear concept
Thanks for sharing your thoughts. I really appreciate your efforts and I am waiting for your further write ups thank you once again.
Also visit my blog; realtor in Bedford NH
Hello mates, nice post and nice arguments commented at this
place, I am actually enjoying by these.
Hello it’s me, I am also visiting this website on a regular basis, this site is
truly good and the visitors are in fact sharing good thoughts.
I do not even know how I ended up here, but I thought this post was great.
I don’t know who you are but definitely you’re going to a
famous blogger if you aren’t already 😉 Cheers!
Feel free to visit my page :: best realtor in Tucson AZ
Finding The Best Mobility Scooter Dealers Near Me: A Comprehensive Guide What Is The Best Mobility Scooter To Buy Uk
Hello my loved one! I want to say that this article is awesome, nice written and come
with approximately all significant infos. I would like to see more posts like
this .
my web page :: realtor in East Falmouth MA
We’re a group of volunteers and starting a new scheme in our community.
Your web site offered us with valuable information to
work on. You have done an impressive job and our whole community will be grateful to you.
Your way of explaining all in this article is genuinely
nice, every one can simply understand it, Thanks a lot.
my web blog best real estate agent in Bedford NH
great points altogether, you just gained a new reader.
What might you recommend about your publish that you simply
made a few days ago? Any positive?
My blog: best real estate agent in Wildwood Crest NJ
A fascinating discussion is worth comment. I do think
that you should write more on this subject, it may not be a taboo subject
but generally people don’t talk about such subjects.
To the next! Kind regards!!
Feel free to surf to my web-site: best realtor in San Pedro CA
Fantastic beat ! I would like to apprentice whilst you amend your
website, how can i subscribe for a blog web
site? The account aided me a appropriate deal. I were tiny bit acquainted of this your broadcast offered shiny clear idea
Visit my website; best real estate agent in East Falmouth MA
I like the valuable information you supply on your articles.
I will bookmark your weblog and test once more here frequently.
I am rather certain I’ll be informed many new stuff proper
here! Best of luck for the following!
fantastic put up, very informative. I’m wondering why
the other specialists of this sector do not notice this.
You must proceed your writing. I am sure, you’ve a great readers’ base already!
I read this paragraph completely concerning the difference of most
up-to-date and earlier technologies, it’s awesome article.
Take a look at my web site … best real estate agent in Paducah KY
Hello! Someone in my Myspace group shared this website with us so I came to give it a look.
I’m definitely loving the information. I’m book-marking and will be tweeting this to my
followers! Exceptional blog and excellent design and style.
I visited many sites except the audio feature for audio songs existing
at this site is really excellent.
Here is my homepage … best realtor in Anaheim CA
I’m curious to find out what blog system you’re
using? I’m experiencing some minor security problems with my latest website and I would
like to find something more risk-free. Do you have any recommendations?
Here is my site – best realtor in Springfield OR
Cheers, I like this!
You have made some really good points there. I checked on the internet for more info about the issue and
found most individuals will go along with your views on this site.
Look at my blog … realtor in McDonough GA
Hi there friends, how is all, and what you want to say
concerning this piece of writing, in my view its in fact amazing in favor of me.
My web page best real estate agent in McDonough GA
My brother recommended I might like this website.
He was entirely right. This post truly made my day.
You cann’t imagine simply how much time I had spent for this information! Thanks!
Take a look at my web blog :: realtor in Paducah KY
Quality content is the secret to be a focus for the people to visit the site, that’s what this site is providing.
Look into my webpage: best realtor in Springfield OR
I enjoy reading a post that can make men and women think.
Also, thank you for permitting me to comment!
Take a look at my homepage: best real estate agent in Fort Lauderdale FL
My spouse and I stumbled over here coming from a different website and thought I should check things out.
I like what I see so i am just following you. Look forward
to exploring your web page for a second time.
Also visit my web-site – realtor in Tucson AZ
Thank you, I’ve just been looking for information approximately this topic for a while and yours is the
greatest I’ve discovered so far. However, what concerning the
bottom line? Are you certain about the source?
Review my homepage :: real estate agent San Pedro CA
Incredible points. Outstanding arguments. Keep up the amazing effort.
Feel free to visit my web site … best real estate agent in Boise ID
Heya i’m for the primary time here. I came across this board
and I to find It truly useful & it helped me out a lot.
I’m hoping to give one thing back and aid others such as you helped me.
My webpage :: real estate agent Anaheim CA
I do not know whether it’s just me or if perhaps everyone else encountering
problems with your site. It appears as though some of the text on your
posts are running off the screen. Can somebody else please comment
and let me know if this is happening to them as well?
This may be a issue with my browser because I’ve had this
happen previously. Many thanks
Feel free to surf to my page: best realtor in Bedford NH
Heya i’m for the primary time here. I found this board and I in finding It truly useful & it
helped me out much. I’m hoping to give one thing back and help others like you
helped me.
Greetings! Very useful advice within this article! It is the little changes which will make
the greatest changes. Many thanks for sharing!
It’s a shame you don’t have a donate button! I’d certainly donate
to this brilliant blog! I guess for now i’ll settle for book-marking
and adding your RSS feed to my Google account. I look forward to brand new updates and will share this blog with my Facebook
group. Chat soon!
I visit everyday some web sites and websites to read posts, except this website offers feature based content.
Visitor arrivals fell 40% for these 3 months compared to 2014, a total of extra than 1.6 million fewer tourists.
Also visit my homepage – http://wolfpredator.sknt.ru/almedalenk6443
Wow plenty of awesome info.
Asking questions are actually pleasant thing if you are not understanding anything completely, but this article offers fastidious understanding yet.
Really tons of helpful info.
This design is incredible! You most certainly know how to keep a
reader entertained. Between your wit and your videos, I
was almost moved to start my own blog (well, almost…HaHa!) Fantastic job.
I really loved what you had to say, and more than that, how you presented it.
Too cool!
صندلي تک و عمده زير قيمت منطقه
Undeniably believe that which you said. Your favourite justification appeared to be at
the internet the easiest thing to take note of. I say to
you, I definitely get irked even as other people consider worries that they plainly don’t
know about. You managed to hit the nail upon the top as smartly as outlined out the
entire thing with no need side effect , other folks can take a signal.
Will likely be back to get more. Thank you
Ces ressources sont essentielles pour accomplir des quêtes importantes, telles que celles menant à l’obtention du Dofus Pourpre.
Miototo merupakan situs login slot online tergacor dengan game gampang maxwin #1 terpercaya di Indonesia yang dilengkapi RTP tinggi
dan layanan 24 jam nonstop.
Hmm it appears like your blog ate my first comment (it was extremely long) so I guess
I’ll just sum it up what I wrote and say, I’m thoroughly enjoying your
blog. I as well am an aspiring blog writer but I’m still new to everything.
Do you have any suggestions for novice blog
writers? I’d definitely appreciate it.
I am sure this piece of writing has touched all the internet people, its really really pleasant post on building up new web site.
Hi, I do believe this is an excellent web site. I stumbledupon it
😉 I may return yet again since i have book-marked it.
Money and freedom is the best way to change, may you be rich and continue to guide other people.
Quality articles or reviews is the secret to interest the viewers to pay a visit the site, that’s what this web page is providing.
I’m really enjoying the theme/design of your web site.
Do you ever run into any web browser compatibility problems?
A few of my blog visitors have complained about my blog
not operating correctly in Explorer but looks great in Firefox.
Do you have any suggestions to help fix this problem?
Great postings. Many thanks!
Wow that was unusual. I just wrote an incredibly
long comment but after I clicked submit my comment didn’t show up.
Grrrr… well I’m not writing all that over again.
Anyhow, just wanted to say great blog!
Hmm it appears like your site ate my first comment (it was extremely long) so
I guess I’ll just sum it up what I wrote and say, I’m thoroughly enjoying your blog.
I too am an aspiring blog writer but I’m still new to the whole thing.
Do you have any recommendations for novice blog
writers? I’d definitely appreciate it.
Stunning story there. What happened after?
Good luck!
Hi, of course this piece of writing is in fact nice and I have learned lot of things from it about blogging.
thanks.
My brother suggested I may like this website.
He was once entirely right. This post truly made my day.
You cann’t believe simply how much time I had spent for this information! Thank you!
Its like you learn my mind! You appear to grasp so much approximately this, such as you wrote the guide
in it or something. I believe that you just could do with some p.c.
to drive the message home a bit, but instead of that, this is wonderful blog.
A great read. I’ll certainly be back.
Fastidious response in return of this query
with real arguments and telling the whole thing regarding
that.
I used to be able to find good info from your blog posts.
my blog – Stroke rehabilitation at home Chelmsford
It’s remarkable designed for me Antidetect browser to manage multiple accounts have a website, which is beneficial
in favor of my experience. thanks admin
Hi! This is my first visit to your blog! We are a group of volunteers and starting a new initiative in a community in the same niche.
Your blog provided us beneficial information to work on. You have done a outstanding job!
Thanks Browser for Multi-Accounting the marvelous posting!
I truly enjoyed reading it, you may be a great author. I will be sure to bookmark your
blog and definitely will come back from now on. I want to encourage one to continue your great job, have a nice afternoon!
Everything posted made a lot of sense. However, consider this, suppose you added a little information? I ain’t suggesting your information isn’t
good., but what if you added something that grabbed
folk’s attention? I mean SMI diamond grinding wheels is kinda plain. You might peek
at Yahoo’s front page and watch how they create news titles to grab people to click.
You might add a related video or a related pic or two to get readers excited about
everything’ve got to say. Just my opinion, it would make your posts a
little livelier.
I go to see daily a few sites and information sites to
read content, except this blog offers quality based writing.
My web site property consultants
Magnificent beat ! I wish to apprentice while you amend your site, how can i subscribe
for a blog website? The account helped me a acceptable deal.
I had been tiny bit acquainted of this your broadcast offered bright
clear idea
Here is my site; property consultants
Excellent post. I was checking constantly this
blog and I am impressed! Very useful information particularly the last part :
) I care for such info much. I was looking for this certain info for a long time.
Thank you and best of luck.
Here is my blog; uus77 login
Wow, that’s what I was seeking for, what a information! present here at
this blog, thanks admin of this site.
Here is my web-site … Real Estate Brokers in Bangalore
It’s remarkable for me to have a web site, which is helpful for my experience.
thanks admin
Also visit my web-site – real estate consultants
I think this is one of the most vital info for me.
And i am glad reading your article. But should remark
on few general things, The site style is perfect, the articles is really great
: D. Good job, cheers
Have a look at my webpage … uus77 login
Amazing blog! Do you have any tips and hints for
aspiring writers? I’m hoping to start my own site soon but I’m a little lost on everything.
Would you advise starting with a free platform like WordPress or go for a
paid option? There are so many choices out there that I’m completely confused ..
Any ideas? Appreciate it!
Great web site. Plenty of useful information here. I am sending it to some friends ans
additionally sharing in delicious. And obviously,
thank you in your effort!
Greetings from Idaho! I’m bored to tears at work so I decided to browse your site on my iphone during lunch break.
I love the knowledge you provide here and can’t
wait to take a look when I get home. I’m amazed at how quick your blog loaded on my
cell phone .. I’m not even using WIFI, just 3G ..
Anyhow, excellent blog!
Feel free to visit my web site uus77 login
I always spent my half an hour to read this website’s content daily
along with a mug of coffee.
Stop by my web blog: Real Estate Agents in Bangalore
Does your website have a contact page? I’m having problems
locating it but, I’d like to send you an e-mail. I’ve got some creative ideas for your blog you
might be interested in hearing. Either way, great site and I look forward to
seeing it improve over time.
Also visit my website; real estate consultants
I know this if off topic but I’m looking into starting my
own weblog and was curious what all is required to get set up?
I’m assuming having a blog like yours would cost a pretty penny?
I’m not very web smart so I’m not 100% sure.
Any recommendations or advice would be greatly
appreciated. Cheers
Hello! I’m at work browsing your blog from my new apple iphone!
Just wanted to say I love reading through your blog and look forward to all your
posts! Carry on the great work!
Fantastic beat ! I would like to apprentice whilst you amend your website, how can i subscribe
for a blog site? The account aided me a applicable deal.
I had been tiny bit familiar of this your broadcast provided vibrant clear idea
Feel free to surf to my webpage: real estate consultants
Thanks for finally talking about > SMI diamond grinding wheels < Liked it!
Your means of describing everything in this post is really fastidious,
every one be capable of simply be aware of it, Thanks a lot.
When someone writes an article he/she maintains the idea
of a user in his/her mind that how a user can know it.
So that’s why this piece of writing is perfect. Thanks!
One thing I love about It’s Me & You is how private and discreet it is. No waiting rooms full of people—just a calm, welcoming space where Dr Laura Geige works her magic.
My site Upper Face Anti Wrinkle Treatment near Effingham, Surrey [http://supersleepyoga.com]
Thanks a lot, Very good information.
What’s up i am kavin, its my first time to commenting anyplace,
when i read this article i thought i could also make comment due to this sensible
paragraph.
Hi there just wanted to give you a quick heads up.
The text in your post seem to be running off the screen in Opera.
I’m not sure if this is a formatting issue or something to do with internet browser compatibility but I thought I’d
post to let you know. The design look great though!
Hope you get the issue resolved soon. Kudos
Somebody necessarily assist to make severely articles I would state.
This is the very first time I frequented your website
page and to this point? I amazed with the analysis you made to make
this particular submit amazing. Fantastic activity!
I’m not positive where you’re getting your info, but good topic.
I must spend a while studying much more or figuring
out more. Thanks for fantastic information I was searching for this information for my mission.
You have made your point.
I all the time used to study article in news papers but now
as I am a user of web so from now I am using net
for content, thanks to web.
صندلی
Howdy! Do you know if they make any plugins to assist with Search Engine Optimization? I’m trying to
get my blog to rank for some targeted keywords but I’m not seeing very
good gains. If you know of any please share. Cheers!
Regards, Quite a lot of advice!
https://maps.google.no/url?q=https://betflik68-th.co/betflik68-login/
Howdy, I think your site might be having web browser compatibility issues.
When I look at your site in Safari, it looks fine however when opening
in IE, it has some overlapping issues. I simply wanted to give
you a quick heads up! Apart from that, fantastic site!
Nicely put, Thanks a lot!
magnificent put up, very informative. I’m wondering why the opposite experts of this sector
do not realize this. You should proceed your writing.
I am confident, you have a huge readers’ base
already!
Can you tell us more about this? I’d love to find out some
additional information.
Hi, i feel that i saw you visited my website thus i got here to go back the
want?.I am trying to in finding issues to improve my site!I
guess its ok to use a few of your ideas!!
I used to be able to find good advice from your articles.
https://cfood.vn cfood tay ninh
I’d like to find out more? I’d want to find out more details.
It’s a shame you don’t have a donate button! I’d certainly donate to this excellent blog!
I suppose for now i’ll settle for bookmarking and
adding your RSS feed to my Google account. I look forward to fresh updates and will
share this site with my Facebook group. Chat soon!
It’s a pity you don’t have a donate button! I’d definitely donate to this
outstanding blog! I suppose for now i’ll settle for bookmarking and adding your
RSS feed to my Google account. I look forward to new updates and will talk about this
site with my Facebook group. Chat soon!
I really like your blog.. very nice colors & theme. Did you design this website yourself or
did you hire someone to do it for you? Plz respond as I’m looking to construct
my own blog and would like to know where u got this from.
kudos
Today, I went to the beach with my kids. I found a sea shell and gave it to my 4
year old daughter and said “You can hear the ocean if you put this to your ear.” She placed the shell to her ear and screamed.
There was a hermit crab inside and it pinched her ear.
She never wants to go back! LoL I know this is
entirely off topic but I had to tell someone!
I think this is among the most vital information for me.
And i am glad reading your article. But
should remark on few general things, The web site style is
great, the articles is really excellent : D. Good job, cheers
Its not my first time to visit this site, i am visiting this website dailly and get pleasant
data from here daily.
Hi there! This is my first comment here so I just wanted to
give a quick shout out and tell you I truly enjoy reading your blog posts.
Can you recommend any other blogs/websites/forums that go over the
same subjects? Many thanks!
you are truly a just right webmaster. The site loading pace is incredible.
It seems that you’re doing any distinctive trick.
In addition, The contents are masterwork. you’ve done a fantastic task
on this topic!
Do you mind if I quote a couple of your articles
as long as I provide credit and sources back to your webpage?
My blog is in the exact same niche as yours and my users would definitely benefit from a lot of the information you provide here.
Please let me know if this okay with you. Cheers!
Your means of explaining all in this paragraph is actually nice, every one be able to effortlessly be aware of it, Thanks a lot.
I think this is among the most important info for me.
And i am glad reading your article. But want to
remark on few general things, The website style is perfect, the articles is
really excellent : D. Good job, cheers
Hi there, yup this paragraph is truly pleasant and I have learned lot of
things from it on the topic of blogging. thanks.
With almost everything which appears to be building within this specific area, all your points of view tend to be quite exciting. Nonetheless, I beg your pardon, because I do not give credence to your entire suggestion, all be it stimulating none the less. It would seem to me that your remarks are generally not totally rationalized and in simple fact you are yourself not really completely certain of your point. In any case I did appreciate examining it.
Write more, thats all I have to say. Literally, it seems as though you relied on the video
to make your point. You obviously know what youre talking about, why waste your intelligence on just posting videos to your site when you could be giving
us something enlightening to read?
WOW just what I was looking for. Came here
by searching for Raja Yoga
I do not even understand how I finished up right here, but I
believed this post was once great. I don’t know who you are
however definitely you are going to a famous blogger if you aren’t already.
Cheers!
Become an ACPMA Instructor (MAB/CPI) – Crisis Prevention Intervention
American Crisis Prevention & Management Association Welcomes qualified professionals from various fields to
take our instructor course and teach ACPMA courses at their locations.
Benefits of certifying an instructor with ACPMA:
Become a Certified instructor for Crisis Prevention & Assaultive Behavior Management
Training done by experienced Personnel
Save on training your employees by training the trainer in your facility
Learn the core principles of adult learning
Leave the training fully confident to teach the AB
508 mandated topics, Crisis Intervention topics and work
Receive all the training materials you need to teach students
Become part of a household name on Assaultive Behavior Management training
Study in front of your computer (for online students)
You can take the instructor course online at https://www.crisispreventionmanagement.com/become-an-instructor
Its like you read my mind! You seem to know so much about this, like you wrote the book in it
or something. I think that you can do with a few pics to drive the message home a little bit, but other than that, this is excellent blog.
A fantastic read. I’ll certainly be back.
Good day! This post couldn’t be written any better! Reading through this post reminds me of my good old room mate!
He always kept talking about this. I will forward this page to him.
Pretty sure he will have a good read. Thanks for sharing!
If you are going for finest contents like I do, just visit this
website everyday as it provides quality contents, thanks
My brother suggested I may like this web site.
He was once totally right. This post truly made my day.
You cann’t believe just how a lot time I had spent for this info!
Thank you!
It’s a shame you don’t have a donate button! I’d definitely donate to this excellent blog!
I guess for now i’ll settle for book-marking
and adding your RSS feed to my Google account. I look forward to new updates
and will talk about this website with my Facebook group.
Talk soon!
I blog quite often and I genuinely appreciate your content.
This article has really peaked my interest. I’m going to bookmark your blog and keep checking for new information about once a week.
I opted in for your Feed as well.
Really quite a lot of fantastic data.
I visited various blogs however the audio feature for audio songs current at this site
is in fact wonderful.
You really make it seem really easy together with your presentation however I find this matter
to be really something which I feel I would never understand.
It kind of feels too complex and extremely wide for me. I am looking
ahead in your next submit, I’ll attempt to get the cling
of it!
Hey excellent website! Does running a blog like this take a large amount of work?
I have virtually no expertise in coding but I had been hoping to start my own blog soon.
Anyways, should you have any recommendations or tips for new blog
owners please share. I know this is off subject however I simply had to ask.
Kudos!
Hello! I understand this is sort of off-topic but I
needed to ask. Does building a well-established website such as yours take a massive amount work?
I am brand new to running a blog but I do write in my diary daily.
I’d like to start a blog so I can share my own experience and thoughts online.
Please let me know if you have any suggestions or tips for new aspiring blog owners.
Appreciate it!
Hi my loved one! I wish to say that this post is amazing, great written and include approximately
all important infos. I’d like to look more posts like this .
Wonderful goods from you, man. I’ve understand your stuff previous to and you are
just extremely excellent. I actually like what you’ve acquired
here, certainly like what you are saying and the way
in which you say it. You make it enjoyable and you still care for to keep it wise.
I can’t wait to read far more from you. This is actually a wonderful website.
Also visit my blog – Labeling Machine
What’s up, I read your new stuff on a regular basis. Your story-telling style is
awesome, keep up the good work!
It is perfect time to make some plans for the long run and it’s time to be happy.
I’ve read this submit and if I may I wish to counsel you few fascinating things or advice.
Maybe you could write subsequent articles referring to this article.
I want to learn more things about it!
I was suggested this web site by my cousin. I am not sure whether this post is written by
him as nobody else know such detailed about my problem. You are wonderful!
Thanks!
I will right away clutch your rss feed as I can’t find your e-mail subscription link or newsletter service.
Do you have any? Kindly allow me recognise so that I may
subscribe. Thanks.
Thanks for a marvelous posting! I truly enjoyed reading it, you could be a great author.I will make sure to bookmark your
blog and will com back sometime soon. I wwant to encourage yourself
to continue your great work, have a nice evening!
For hottest news you have to pay a quick visit world wide web and on the web I found this web page as a most excellent web site for most up-to-date updates.
Very nice post. I just stumbled upon your blog and wished to say that I
have truly enjoyed surfing around your blog posts.
In any case I will be subscribing to your feed and I hope you write
again soon!
Terrific data, Thanks.
Yes! Finally someone writes about Encanador.
We’re a gaggle of volunteers and starting a New Look Rent-a-Car in Cap-Haitien scheme in our community.
Your web site provided us with helpful information to work
on. You have done a formidable activity and our entire
neighborhood might be thankful to you.
Thanks for every other fantastic post. Where else may anyone
get that kind of info in such a perfect method of writing?
I have a presentation next week, and I am on the look for such
info.
Feel free to surf to my site Hotels near Cap-Haitien Airport
I am extremely impressed with your writing skills and also with the layout on your weblog.
Is this a paid theme or did you modify it yourself?
Either way keep up the excellent quality writing, it’s rare to see a great blog like
this one these days.
Look at my web-site … Christmas Gifts
Incredible points. Outstanding arguments.
Keep up the good spirit.
Feel free to surf to my homepage dealer daihatsu surabaya
There is definately a lot to find out about this topic. I like
all the points you made.
Pretty! This was an extremely wonderful article.
Thanks for supplying these details.
Also visit my web-site :: New Look Car Rental Okap
Thank you for the auspicious writeup. It in fact was a amusement account it.
Look advanced to far added agreeable from you! By the way, how can we
communicate?
Hi friends, how is everything, and what you desire to say on the topic of this post, in my view its in fact awesome in support of me.
My page – Hotels near Cap-Haitien Airport
Heya i’m for the first time here. I found this board
and I find It really useful & it helped me out a lot.
I hope to give something back and help others like you aided me.
Visit my webpage: JT Appliance Repair in Boca Raton
I like the valuable info you supply for your articles. I’ll bookmark your weblog
and test again right here regularly. I’m reasonably certain I will
learn many new stuff right right here! Good luck for the next!
Look into my page :: dealer mobil daihatsu terdekat
I read this post fully regarding the resemblance of latest and preceding technologies,
it’s remarkable article.
Here is my web blog :: Hotels near Cap-Haitien Airport
Hey There. I found your blog using msn. This is a very well
written article. I’ll make sure to bookmark it and return to read more of
your useful info. Thanks for the post. I’ll definitely comeback.
Also visit my homepage Mother’s day gift
Do you mind if I quote a couple of your posts as long as I provide credit
and sources back to your webpage? My website is in the exact same area of interest as yours and
my visitors would definitely benefit from a lot of the information you present here.
Please let me know if this okay with you. Thank you!
Thanks for any other informative website. The place else could I get that type of information written in such a
perfect approach? I have a project that I’m simply now operating on, and I’ve been at the
New Look Rent-a-Car in Cap-Haitien out for such information.
Hello! I just wanted to ask if you ever have any issues with hackers?
My last blog (wordpress) was hacked and I ended up losing a few months of hard work
due to no data backup. Do you have any solutions
to stop hackers?
My web blog; JT Appliance Repair in Boca Raton
Hey there just wanted to give you a quick
heads up. The text in your post seem to be running off the screen Hotels in Cap-Haitien Ie.
I’m not sure if this is a formatting issue or something to do with internet browser compatibility but
I figured I’d post to let you know. The layout look great though!
Hope you get the problem solved soon. Kudos
Hiya very nice web site!! Guy .. Excellent .. Wonderful ..
I’ll bookmark your web site and take the feeds
also? I am satisfied to find numerous useful information right
here in the submit, we want work out more strategies
in this regard, thanks for sharing. . . . . .
Feel free to surf to my site … Comprehensive review
Heya this is somewhat of off topic but I was wanting to know if blogs
use WYSIWYG editors or if you have to manually code with HTML.
I’m starting a blog soon but have no coding experience so I wanted to get guidance from someone with experience.
Any help would be greatly appreciated!
Helpful information. Fortunate me I found your website by
chance, and I am surprised why this coincidence did
not took place earlier! I bookmarked it.
I got this website from my friend who shared with me regarding this website and at the moment this time I am visiting this web page and reading very informative articles at this place.
Also visit my web site; New Look Rent-a-Car in Cap-Haitien
hello there and thank you for your info – I have certainly picked up
something new from right here. I did however expertise several technical points using this website,
as I experienced to reload the site lots of times previous to I could get
it to load properly. I had been wondering if your hosting is
OK? Not that I’m complaining, but sluggish loading instances times will very frequently affect your placement Hotels in Cap-Haitien google and could
damage your high quality score if ads and marketing with Adwords.
Anyway I am adding this RSS to my e-mail and could look out for a lot
more of your respective exciting content. Ensure that you update this again very soon.
It’s actually a cool and helpful piece of information. I am happy that you just shared this helpful information with us.
Please keep us informed like this. Thanks for sharing.
Hey! I’m at work browsing your blog from my new iphone
4! Just wanted to say I love reading through your blog and look forward to all your posts!
Carry on the fantastic work!
I like the helpful info you provide on your articles.
I will bookmark your blog and take a look at once more here regularly.
I’m fairly certain I will learn a lot of New Look Car Rental Cap-Haitien stuff right here!
Best of luck for the following!
Hello colleagues, pleasant piece of writing and pleasant urging commented here, I am genuinely enjoying
by these.
Greetings I am so excited I found your blog page, I really found you by error, while I was looking on Yahoo for something else, Anyhow I am here now and would just like to say thanks for a remarkable
post and a all round entertaining blog (I also love the theme/design), I don’t have
time to read it all at the moment but I have bookmarked it and also added Hotels in Okap your RSS feeds,
so when I have time I will be back to read a great deal
more, Please do keep up the superb job.
Great post. I was checking continuously this
blog and I’m impressed! Very useful information specifically the last part 🙂 I care for such info
a lot. I was seeking this particular info for a long time.
Thank you and best of luck.
My web blog; Hotels in Cap-Haitien
Magnificent beat ! I wish to apprentice while you amend your website, how can i subscribe for a blog site?
The account helped me a acceptable deal. I had been a little
bit acquainted of this your broadcast offered bright clear concept
Here is my site Car Rental in Cap-Haitien
I used to be able to find good information from your blog posts.
Feel free to surf to my blog post: New Look Rent-a-Car in Cap-Haitien
I think this is one of the most vital info for me. And i’m glad reading your article.
But should remark on some general things, The
site style is great, the articles is really nice : D.
Good job, cheers
Please let me know if you’re looking for a article author for
your weblog. You have some really good articles and I
feel I would be a good asset. If you ever want to take some of the load off, I’d love to write some content
for your blog JT Appliance Repair in Boca Raton exchange for a link back to mine.
Please blast me an email if interested. Cheers!
Hi, I check your new stuff like every week. Your writing style is awesome, keep it up!
It’s very simple to find out any matter on net as compared to textbooks, as I found this piece of writing at this web site.
Have a look at my web site: Father’s day gift
Good day! Would you mind if I share your blog with my
zynga group? There’s a lot of folks that I think would really appreciate your content.
Please let me know. Cheers
Hi there to all, how is all, I think every one is getting more from this web page, and your views are good designed for
New Look Car Rental Cap-Haitien people.
Hello, I would like to subscribe for this blog to get latest updates, therefore where can i
do it please assist.
My page: Rental Car Okap
I’m impressed, I have to admit. Rarely do I encounter a blog
that’s both equally educative and amusing, and let me tell you,
you’ve hit the nail on the head. The problem is something
which too few people are speaking intelligently about. I’m very
happy I stumbled across this in my hunt for something concerning this.
My web site: New Look Car Rental Cap-Haitien
I constantly spent my half an hour to read this blog’s posts
everyday along with a cup of coffee.
Review my site: Hotels in Cap-Haitien
It’s perfect time to make some plans for the future and
it’s time to be happy. I’ve read this post and
if I could I want to suggest you some interesting things or advice.
Perhaps you could write next articles referring to this article.
I desire to read even more things about it!
Very good blog post. I certainly love this site. Thanks!
whoah this blog is fantastic i really like reading your articles.
Stay up the good work! You recognize, lots of persons are searching round for
this information, you could help them greatly.
If some one desires expert view about blogging then i propose him/her to pay a quick visit this blog, Keep up the pleasant
job.
Hi there! This post couldn’t be written much better! Going through this post reminds me of my previous roommate!
He constantly kept talking about this. I’ll forward this information to him.
Fairly certain he’s going to have a great read. Many thanks for sharing!
I have been browsing online more than 2 hours today, yet I never found any interesting article
like yours. It’s pretty worth enough for me.
In my opinion, if all site owners and bloggers made
good content as you did, the web will be a lot more useful than evcer before.
Cool blog! Is your theme custom made or did you download
it from somewhere? A theme like yours with a few simple adjustements would really make my
blog shine. Please let me know where you got your design. Thank you
If you are going for finest contents like me, only
visit this web site every day because it gives quality contents,
thanks
I have read so many articles regarding the blogger lovers however this paragraph is actually a good
article, keep it up.
Very good https://shorturl.fm/bODKa
Spot on with this write-up, I absolutely feel this web site needs much more attention. I’ll probably be back again to see
more, thanks for the information!
Hi there i am kavin, its my first occasion to commenting
anyplace, when i read this paragraph i thought i could also make comment due to this good piece of writing.
I all the time used to study paragraph in news papers but now as I am
a user of internet therefore from now I am using net for posts, thanks to web.
Good site you have here.. It’s hard to find high-quality writing like yours
these days. I truly appreciate individuals like you! Take care!!
Hiya! I know this is kinda off topic however
, I’d figured I’d ask. Would you be interested in exchanging
links or maybe guest authoring a blog post or vice-versa?
My website discusses a lot of the same topics as yours and I believe we
could greatly benefit from each other. If you are interested feel free to shoot me an e-mail.
I look forward to hearing from you! Superb blog by the way!
Taking this to the office.
Wonderful blog! I found it while browsing on Yahoo News.
Do you have any suggestions on how to get listed in Yahoo News?
I’ve been trying for a while but I never seem to get there!
Cheers
Thank you for every other informative site. The place else may I am getting that kind
of information written in such a perfect way?
I’ve a venture that I am simply now working on, and I have been on the glance out for such info.
Just want to say your article is as astounding.
The clarity on your publish is simply excellent and that i could assume
you’re an expert on this subject. Fine along with your permission let me to grab your
RSS feed to stay updated with impending post. Thanks 1,000,000 and please
keep up the rewarding work.
Howdy! Someone in my Myspace group shared this
website with us so I came to give it a look.
I’m definitely enjoying the information. I’m bookmarking and will
be tweeting this to my followers! Exceptional blog and superb design.
By pursuing this career, you can continually develop and refine your
craft.
Every weekend i used to go to see this web page, because i want enjoyment, as
this this website conations really pleasant
funny information too.
I every time emailed this weblog post page to all my
friends, as if like to read it next my links will too.
I used to be suggested this web site through my cousin. I’m
not positive whether or not this publish is written through him as nobody else
recognize such targeted about my problem. You’re amazing!
Thanks!
Appreciating the time and energy you put into your website and in depth information you
offer. It’s great to come across a blog every once in a while that isn’t the same out of date rehashed information. Great read!
I’ve bookmarked your site and I’m adding your RSS
feeds to my Google account.
Excellent post. I will be dealing with some of these issues as well..
What’s up i am kavin, its my first time to commenting anyplace, when i
read this post i thought i could also create comment due to this good post.
Hello There. I found your blog using msn. This is an extremely well
written article. I will be sure to bookmark it and come back to read more of your useful
info. Thanks for the post. I’ll certainly return.
I like what you guys are up too. This type of clever work and exposure!
Keep up the good works guys I’ve added you guys to my personal
blogroll.
What i don’t realize is in reality how you’re no longer really much more well-appreciated than you might be now.
You are so intelligent. You realize therefore significantly in the case of this topic, made me in my opinion believe
it from numerous numerous angles. Its like men and women aren’t fascinated except it’s something to do with Woman gaga!
Your own stuffs great. All the time care for it up!
This site was… how do I say it? Relevant!! Finally I’ve found something which helped me.
Thanks a lot!
Today, I went to the beach with my children. I found a sea shell and gave it to my 4 year old
daughter and said “You can hear the ocean if you put this to your ear.” She placed
the shell to her ear and screamed. There was a hermit crab inside and it pinched her ear.
She never wants to go back! LoL I know this is totally off topic but I had to tell someone!
Thank you, I’ve just been looking for information about this topic for a while and yours is the best I have came upon till now.
But, what about the conclusion? Are you sure
concerning the supply?
I enjoy what you guys are usually up too. This type of clever work and exposure!
Keep up the superb works guys I’ve added you guys to my blogroll.
It’s actually a nice and useful piece of information. I’m glad that you just
shared this useful info with us. Please stay us up to date like this.
Thanks for sharing.
Keep on working, great job!
Hello, i think that i saw you visited my web site
thus i came to “return the favor”.I am trying to find
things to enhance my web site!I suppose its ok to use
some of your ideas!!
Excellent info, Many thanks!
My webpage; https://www.sellgold.be/pieces-or/1-oz-queens-beasts-faucon/
It’s amazing to visit this web site and reading the views of all mates
regarding this post, while I am also zealous of getting experience.
I read this post fully about the comparison of most
recent and earlier technologies, it’s amazing article.
If you want to get a good deal from this article then you have to apply such methods to
your won blog.
You really make it seem so easy with your presentation but I
find this topic to be really something that I think I would never understand.
It seems too complex and extremely broad for me. I’m
looking forward for your next post, I will try to get the hang
of it!
Hey! I’m at work surfing around your blog from my new iphone 3gs!
Just wanted to say I love reading through your blog and look forward to all your posts!
Carry on the fantastic work!
fantastic publish, very informative. I’m wondering why
the opposite specialists of this sector do not notice
this. You should continue your writing. I am confident, you’ve a
great readers’ base already!
I’ve been exploring for a little for any high-quality articles or blog posts on this sort
of space . Exploring in Yahoo I at last stumbled upon this website.
Reading this info So i’m glad to convey that I have a very just right uncanny feeling I
came upon exactly what I needed. I such a lot surely will make certain to do not fail to remember this website
and give it a glance on a constant basis.
I visited many web sites except the audio quality for audio songs
current at this web page is actually fabulous.
Link exchange is nothing else except it is only placing the other person’s web site link on your page at
appropriate place and other person will also do same in favor of
you.
Your means of telling everything in this post is
really nice, all can without difficulty know it, Thanks a lot.
With thanks, I appreciate this.
Superb blog! Do you have any recommendations for aspiring writers?
I’m hoping to start my own blog soon but I’m a little lost on everything.
Would you advise starting with a free platform like WordPress or go for
a paid option? There are so many choices out there that I’m totally overwhelmed ..
Any ideas? Cheers!
Hey! I know this is kinda off topic but I was wondering which blog platform are you using
for this website? I’m getting fed up of WordPress because I’ve
had problems with hackers and I’m looking at options for another platform.
I would be fantastic if you could point me in the direction of a good platform.
That is really fascinating, You’re a very skilled
blogger. I have joined your rss feed and look forward to in the hunt for
more of your great post. Additionally, I’ve shared your site in my social networks
This is a great tip particularly to those new to the blogosphere.
Short but very accurate information… Thank you
for sharing this one. A must read article!
당신의 기사가 놀랍습니다고 말하고 합니다.
당신의 포스트의 선명도는 단순히 훌륭하고 저는 당신이
이 주제에 전문가라고 생각합니다.
당신의 허락한다면 당신의 RSS 피드를
가져가서 다가오는 포스트로 최신 상태를
유지하고 싶습니다. 백만 감사하고 만족스러운
일을 계속해 주세요.
Very rapidly this site will be famous among all blog people, due
to it’s fastidious content
Back then, Knight’s loud cries in the midst of the evening would wake up all the opposite sleeping boys. Glue the opposite stick by way of the center of the X; let dry. 21 July 2013 (TAFTA treaty a means to bypass democracy) The proposed TAFTA treaty is purely a method to let a range of companies bypass democracy to do away with the regulations they don’t love. Not exactly. Richmond aims to keep people entertained all day, with a midway, a fan festival, and live music previous to the race, so many fans get to the track early. 2024-04-21: I do know it’s unrealistic to feel this fashion, but it’s all the time disappointing whenever you get … A Turkish activist I know comments on the situation. It doesn’t matter to anyone um having said that like I completely, uh, you already know assist anybody else’s Right to to speak out and and go for it. Still, the primary evening, he lay his head proper there, and tried to sleep till a terrible odor woke him up. He’s selling out shows throughout LA County, and just signed his first independent deal.
It’s a pity you don’t have a donate button! I’d most certainly donate to
this excellent blog! I suppose for now i’ll settle
for book-marking and adding your RSS feed to my Google account.
I look forward to new updates and will talk about this website
with my Facebook group. Chat soon!
Become an ACPMA Instructor (MAB/CPI) – Crisis Prevention Intervention
American Crisis Prevention & Management Association Welcomes qualified professionals from various fields to take our instructor course and teach ACPMA
courses at their locations.
Benefits of certifying an instructor with ACPMA:
Become a Certified instructor for Crisis Prevention & Assaultive Behavior Management
Training done by experienced Personnel
Save on training your employees by training the trainer in your facility
Learn the core principles of adult learning
Leave the training fully confident to teach the AB 508 mandated
topics, Crisis Intervention topics and work
Receive all the training materials you need to teach students
Become part of a household name on Assaultive Behavior Management training
Study in front of your computer (for online students)
You can take the instructor course online at https://www.crisispreventionmanagement.com/become-an-instructor
https://shorturl.fm/oYjg5
Thanks for sharing such a good opinion, piece of writing is good, thats why i have read it completely
https://shorturl.fm/9fnIC
Please let me know if you’re looking for a author for your weblog.
You have some really good posts and I think I would be a good asset.
If you ever want to take some of the load off, I’d really like to write some articles for your blog in exchange for a link
back to mine. Please shoot me an email if interested.
Kudos!
It is really a great and useful piece of information. I’m satisfied that
you simply shared this useful info with us. Please stay us informed like this.
Thanks for sharing.
Installing brand new Campagnolo elements to a brand new fully-prepped Italian steel frame is an almost orgasmic experience if you are a sad previous bike porn addict like me. When it came to mental well being features of impotence situation, porn was talked about 1,850 occasions. Other instances it’s a approach of managing life difficulties. This manner we’d avoid reinventing the wheel (at the least throughout the workforce). The rear wheel slotted exactly into the dropouts as you’d anticipate. I then set the bounds on and wired up the front derailleur, then gave the entrance and rear gears a run-by means of earlier than giving them the ultimate tune and check. Once Dave dropped it off to me I was in a position to suit the front derailleur and proceed with the remainder of the drivetrain. Time now to type out the lengths of the various brake cable housings, double-test them then cut and match them. Most certainly Dave might be going to a special and slightly shorter stem but establishing the right match takes time and actual on-the-highway experience to determine, so this will suffice initially. I clamped the Deda Zero100 handlebars into the ITM Millennium carbon/aluminium stem.
Hello would you mind sharing which blog platform you’re working with?
I’m planning to start my own blog soon but I’m having a tough time
selecting between BlogEngine/Wordpress/B2evolution and Drupal.
The reason I ask is because your design seems different then most
blogs and I’m looking for something completely unique.
P.S My apologies for being off-topic but I had to ask!
Thanks, I enjoy this!
As the admin of this site is working, no doubt very quickly
it will be well-known, due to its quality contents.
It’s very effortless to find out any topic on web as compared to books,
as I found this paragraph at this web site.
It’s a pity you don’t have a donate button! I’d most certainly donate to this outstanding blog!
I suppose for now i’ll settle for bookmarking and adding your RSS feed to my Google account.
I look forward to fresh updates and will talk about this website with my Facebook group.
Chat soon!
Your style is really unique compared to other people I have read stuff from.
Thank you for posting when you’ve got the opportunity, Guess I’ll just book mark this blog.
Third, porn fuels disgrace and isolation. In a Quartz publication, Malamuth argued that porn is like alcohol: “whether or not it’s unhealthy for you is dependent upon who you’re” (stating that it increases violence in a couple of folks, not in most people; it makes most individuals extra relaxed). If your teenager has buddies which might be forcing him/her in to viewing porn and likewise discussing it then with software get in contact with element characteristic it’s possible you’ll get the quantity of all your teenager buddy’s thus talk to all of these or their families concerning grownup as properly as it’sdrawbacks, you can even warn these to quit having an affect in your little one about something he/she is not all set yet. You could possibly find a certified expert having vast years of expertise as well as large repute. They alternate data. They’re doing phenomenally nicely. COWEN: They’re more mimetic, right? But that hides the fact that in Eastern Europe, which is getting more religious, the children are actually healthier now than they had been 10 years ago, 15 years in the past. Take a bunch of societies-half of them, we superconnect them, give everyone telephones a hundred years in the past, and others don’t get it. Take a bunch of societies, and now, let’s take a few of them, and let’s ramp up range.
https://shorturl.fm/TbTre
I’ve been browsing online more than 3 hours today, yet I
never found any interesting article like yours.
It is pretty worth enough for me. In my opinion, if all web owners and bloggers made good content as
you did, the net will be much more useful than ever before.
May I simply say what a comfort to discover somebody who actually understands what they’re discussing online.
You definitely understand how to bring a problem to light and make it important.
More people ought to check this out and understand this side of the story.
I was surprised that you are not more popular because you definitely possess the gift.
mods-menu.ru — это интересный способ изменить игровой опыт.
Особенно если вы играете на мобильном устройстве с Android, модификации
открывают перед вами огромный выбор.
Я нравится использовать игры с обходом системы защиты,
чтобы развиваться быстрее.
Моды для игр дают невероятную свободу выбора, что
делает процесс гораздо красочнее.
Играя с твиками, я могу персонализировать свой опыт, что добавляет новые приключения и делает игру более достойной внимания.
Это действительно удивительно,
как такие моды могут улучшить взаимодействие с игрой,
а при этом не нарушая использовать такие игры с
изменениями можно без особых проблем, если быть внимательным
и следить за обновлениями. Это делает каждый
игровой процесс персонализированным,
а возможности практически широкие.
Советую попробовать такие модифицированные версии
для Android — это может вдохновит
на новые приключения
This is a topic that is close to my heart… Best wishes!
Exactly where are your contact details though?
We’re a group of volunteers and opening a new scheme in our community.
Your website provided us with valuable info to work on. You’ve done
a formidable job and our whole community will be thankful to you.
I was curious if you ever considered changing the layout of your blog?
Its very well written; I love what youve got to say.
But maybe you could a little more in the way of content so people could connect with it better.
Youve got an awful lot of text for only having one or 2 images.
Maybe you could space it out better?
I am really grateful to the holder of this site who has shared this impressive piece of writing
at at this place.
Incredible quest there. What occurred after? Take care!
Great items from you, man. I’ve consider your stuff previous to and you are just too wonderful.
I actually like what you have received here, certainly like what you are
saying and the way through which you say it. You’re making it entertaining
and you still care for to stay it smart. I cant wait to learn far more from
you. That is really a tremendous site.
Good day! Do you know if they make any plugins to help with SEO?
I’m trying to get my blog to rank for some targeted keywords but I’m not
seeing very good results. If you know of any please share. Cheers!
I’ve learn some good stuff here. Definitely value bookmarking for revisiting.
I surprise how a lot attempt you set to make such a great informative web site.
Hello Dear, are you in fact visiting this site daily, if so after that you
will without doubt get good experience.
Here is my page: Firstline Garage Door Repair provides Arlington Heights IL
Useful information. Fortunate me I found your site unintentionally, and I am shocked why this coincidence
did not took place in advance! I bookmarked it.
My web-site Garage Door Repair
If some one wants expert view concerning blogging afterward
i advise him/her to pay a visit this web site, Keep up the fastidious work.
Wow! After all I got a weblog from where I can in fact obtain useful facts concerning my study and knowledge.
My webpage; Firstline Garage Door Repair provides Arlington Heights IL
If you are going for best contents like myself, simply pay a quick visit this site all the time for the reason that it presents feature contents,
thanks
My blog; Firstline Garage Door Repair provides Arlington Heights IL
Hi there, I check your new stuff like every week. Your humoristic style
is awesome, keep up the good work!
Link exchange is nothing else but it is only placing the other
person’s blog link on your page at proper place and other
person will also do same in favor of you.
magnificent points altogether, you simply received a
emblem new reader. What could you recommend about your publish that you
made some days in the past? Any certain?
Hmm it appears like your website ate my first comment (it was super long) so I guess I’ll just sum it
up what I had written and say, I’m thoroughly enjoying your blog.
I too am an aspiring blog blogger but I’m still new to everything.
Do you have any recommendations for newbie blog writers? I’d certainly appreciate it.
I’ve been surfing online more than 2 hours today, yet I never found any
interesting article like yours. It is pretty
worth enough for me. In my opinion, if all site owners and bloggers made
good content as you did, the internet will be much more useful than ever before.
Also visit my blog post … Firstline Garage Door Repair provides Arlington Heights IL
This is a topic that’s near to my heart… Cheers!
Where are your contact details though?
Stop by my homepage – Firstline Garage Door Repair provides Arlington Heights IL
mobile-mods — это замечательный способ расширить функциональность игры.
Особенно если вы играете
на мобильном устройстве с Android, модификации
открывают перед вами широкие горизонты.
Я лично использую модифицированные
версии игр, чтобы наслаждаться бесконечными
возможностями.
Моды для игр дают невероятную свободу
в игре, что взаимодействие с игрой гораздо красочнее.
Играя с твиками, я могу повысить уровень сложности,
что добавляет виртуальные путешествия
и делает игру более достойной
внимания.
Это действительно невероятно, как такие модификации могут улучшить переживания
от игры, а при этом не нарушая использовать такие модифицированные
приложения можно без особых
неприятных последствий, если быть внимательным и следить за обновлениями.
Это делает каждый игровой процесс уникальным, а возможности практически неограниченные.
Обязательно попробуйте попробовать такие игры с модами для Android — это может переведет ваш опыт на новый уровень
What’s up to every one, the contents present at this web page are
genuinely remarkable for people experience, well, keep up
the nice work fellows.
Review my web blog – Firstline Garage Door Repair provides Arlington Heights IL
Hey there! This is my 1st comment here so I just wanted to give a quick shout out and
tell you I really enjoy reading your blog posts.
Can you recommend any other blogs/websites/forums that deal with the same subjects?
Thank you so much!
my webpage :: Garage Door Repair
Useful information. Lucky me I found your site by
accident, and I’m surprised why this twist of fate did not
came about in advance! I bookmarked it.
Take a look at my homepage – Firstline Garage Door Repair provides Arlington Heights IL
It’s going to be ending of mine day, but before finish I
am reading this great post to increase my knowledge.
Feel free to visit my site Firstline Garage Door Repair provides Arlington Heights IL
I’m not sure where you’re getting your information, but great topic.
I needs to spend some time learning more or understanding
more. Thanks for magnificent information I was looking for
this information for my mission.
Also visit my web page; Garage Door Repair
fantastic points altogether, you just gained a brand new reader.
What could you recommend in regards to your post that you made some days ago?
Any positive?
Also visit my blog post; Firstline Garage Door Repair provides Arlington Heights IL
After checking out a number of the articles on your site, I honestly appreciate your way of blogging.
I bookmarked it to my bookmark webpage list and will be checking
back soon. Take a look at my web site as well and let me know your opinion.
If you want to obtain much from this post then you have to apply
these methods to your won weblog.
Pretty nice post. I just stumbled upon your blog and wished to say
that I’ve truly enjoyed surfing around your
blog posts. In any case I will be subscribing to your rss
feed and I hope you write again soon!
Nicely put. Cheers!
Stop by my web blog http://gitlab.zbqdy666.com/marko88v455344
https://shorturl.fm/TbTre
Hi there everybody, here every person is sharing these experience, thus it’s good to
read this website, and I used to go to see this blog all the time.
Unquestionably believe that which you said.
Your favorite justification seemed to be on the web the
simplest thing to be mindful of. I say to you, I definitely get annoyed at the same time as people think about
concerns that they just do not understand about.
You managed to hit the nail upon the top and also outlined out the entire thing with no
need side effect , folks could take a signal. Will probably be again to get more.
Thank you
Hеllo to all, foor the reason tһɑt I aam aϲtually eager ᧐f
reading this webpage’s post tо bе updated regularly.
Ιt consists of nice information.
My wweb blog :: выпрямление без формальдегида
Its like you read my mind! You seem to know so much about this,
like you wrote the book in it or something. I think that
you could do with a few pics to drive the message home a bit, but
other than that, this is magnificent blog.
A fantastic read. I will definitely be back.
The other day, while I was at work, my sister stole my iphone and tested to see if it can survive a forty foot drop, just so she can be a youtube sensation. My iPad is now broken and she has 83 views.
I know this is entirely off topic but I had to share it with someone!
Quality articles or reviews is the important to be a focus for the viewers to visit the web page, that’s what this web page is providing.
If you wish for to take a good deal from this
article then you have to apply such methods to your won website.
When some one searches for his necessary thing, thus he/she needs to be available that
in detail, so that thing is maintained over here.
FileViewPro’s strength lies not only in its support for VIB files but in its ability to handle hundreds of other
formats as well. After inspecting a VIB file, users can move on to open related files—such as log reports, patch notes, PDF documentation, or CSV data—without
leaving the application. This unified experience helps streamline complex tasks, especially when you’re working across multiple file types
as part of a larger system maintenance or migration project.
Everything can be handled from within one application, eliminating the need
to install or switch between multiple tools.
Thanks for sharing your thoughts about porn. Regards
After I initially commented I seem to have clicked the -Notify
me when new comments are added- checkbox and now every time
a comment is added I get 4 emails with the exact same comment.
There has to be an easy method you are able to remove me from that service?
Many thanks!
Mar 25, 2022: Read “The Queerest of the Queer”: Listening to Garbage in the Nineties (Catapult) by Niko Stratis. 2023-03-09: “The Exploited Labor Behind Artificial Intelligence” The “AI” industry runs on the backs of those … Apr 18, 2022: Me, considering in regards to the logistics of attending my sister’s Master’s hooding: I mean, what number of instances does your sister finish graduate faculty? Apr 19, 2022: Yesterday I helped my mother and father kind out the logistics of constructing the home extra accessible for my mother when she’s utilizing mobility aids. Apr 1, 2022: Today’s the day it’s best to disregard the internet, so byeeee. Please mark the wonderfulness of my partner who, when my kid wanted to go find the neighbors & play after we’d been out all day with … One can find many differing types of individuals, from the commonest Dominican girls to these who’ve some very particular qualities. The partitions had been all covered in the type of inexperienced tiles one may find in a faculty bathroom, and the partitions were lined with toilets and urinals, every single one of which was unusable for one reason or another.
I’m not that much of a internet reader to be honest but your sites really nice, keep it
up! I’ll go ahead and bookmark your website to come back later.
All the best
you’re really a just right webmaster. The website
loading speed is amazing. It kind of feels that you’re doing any unique
trick. In addition, The contents are masterwork.
you have performed a fantastic job in this subject!
I’m not sure exactly why but this weblog is loading extremely slow for me.
Is anyone else having this issue or is it a problem on my end?
I’ll check back later and see if the problem still exists.
I loved as much as you’ll receive carried out right here.
The sketch is attractive, your authored material stylish.
nonetheless, you command get bought an impatience over that you
wish be delivering the following. unwell unquestionably come further formerly again as exactly the same nearly a
lot often inside case you shield this hike.
สูตรเลขเด็ดงวดนี้
Magnificent site. Lots of helpful information here.
I’m sending it to several pals ans additionally sharing in delicious.
And naturally, thank you in your sweat!
Hi, i read your blog from time to time and i own a similar one and i was just curious if you get
a lot of spam responses? If so how do you prevent
it, any plugin or anything you can recommend? I get so much lately it’s driving me crazy so any assistance is very much appreciated.
Incredible points. Outstanding arguments. Keep up the amazing effort.
In fact when someone doesn’t know after that its up to other viewers
that they will help, so here it occurs.
Successful candidates will gain an internationally recognised qualification which guarantees that they have the skills, knowledge and abilities required to carry out
their role successfully.
We are a bunch of volunteers and opening a brand new
scheme in our community. Your website provided us with helpful information to
work on. You have performed an impressive
task and our entire community might be grateful to you.
https://shorturl.fm/5JO3e
certainly like your website however you have to check the spelling on quite a few
of your posts. Several of them are rife with spelling issues
and I to find it very bothersome to tell the truth nevertheless I will definitely come again again.
Hi there! I just wanted to ask if you ever have any trouble with hackers?
My last blog (wordpress) was hacked and I ended up losing many months
of hard work due to no back up. Do you have any methods to protect against hackers?
It’s amazing in support of me to have a website, which is helpful designed for my experience.
thanks admin
Thanks for sharing your info. I truly appreciate your efforts and
I am waiting for your further post thank you once again.
Hi colleagues, how is all, and what you want to
say on the topic of this post, in my view its genuinely amazing for me.
I really love your site.. Very nice colors & theme.
Did you make this site yourself? Please reply back as
I’m planning to create my very own website and would like
to learn where you got this from or what the theme
is called. Kudos!
https://shorturl.fm/A5ni8
Very good article. I will be dealing with many of these issues as well..
Hey there, I think your blog might be having browser compatibility issues.
When I look at your website in Safari, it looks fine but when opening in Internet Explorer, it
has some overlapping. I just wanted to give you a quick heads up!
Other then that, wonderful blog!
http://terios2.ru/forums/index.php?autocom=gallery&req=si&img=4757
https://mazda-demio.ru/forums/index.php?autocom=gallery&req=si&img=6461
https://mazda-demio.ru/forums/index.php?autocom=gallery&req=si&img=6451
http://toyota-porte.ru/forums/index.php?autocom=gallery&req=si&img=3311
https://mazda-demio.ru/forums/index.php?autocom=gallery&req=si&img=6593
https://mazda-demio.ru/forums/index.php?autocom=gallery&req=si&img=6425
Howdy, I believe your web site could possibly be having web browser compatibility issues.
When I take a look at your blog in Safari, it looks fine however, if opening in I.E.,
it’s got some overlapping issues. I merely wanted to give you
a quick heads up! Other than that, fantastic website!
Wow a good deal of great advice!
My web site: https://Benlola.com/effective-online-reputation-management/
We are also quite capable of wallpapering and doing smaller amounts
of building work.
Thanks to my father who shared with me on the topic of this
blog, this web site is really awesome.
Fortune Dragon Demo Grátis – experimente a emoção . Bônus generosos tornam este slot envolvente . Jogue com Pix ! https://pxhere.com/en/photographer-me/4526768
latest insurance news
My family every time say that I am killing my time here at net,
but I know I am getting know-how daily by reading such pleasant posts.
Hi, after reading this amazing post i am also glad to
share my know-how here with colleagues.
Hi there would you mind letting me know which web host you’re using?
I’ve loaded your blog in 3 different internet browsers and I must say this
blog loads a lot faster then most. Can you recommend a good hosting provider at a fair price?
Thank you, I appreciate it!
Cool blog! Is your theme custom made or did you download it from somewhere?
A design like yours with a few simple tweeks would really
make my blog stand out. Please let me know where you got
your theme. Bless you
Can you tell us more about this? I’d love to find out more details.
You’re so interesting! I don’t suppose I’ve truly read through a single thing like that before.
So good to discover somebody with original thoughts on this topic.
Really.. thanks for starting this up. This web site is
one thing that’s needed on the web, someone with a little originality!
Good day! This is kind of off topic but I need some help from an established
blog. Is it difficult to set up your own blog? I’m not
very techincal but I can figure things out pretty fast.
I’m thinking about setting up my own but I’m not
sure where to start. Do you have any points or suggestions?
Cheers
I’m curious to find out what blog platform you are utilizing?
I’m experiencing some small security issues with my latest blog and I would like to find something more secure.
Do you have any suggestions?
What’s up friends, its impressive piece of writing on the topic of educationand fully
explained, keep it up all the time.
Hey there, You have done a great job. I’ll definitely digg it and
personally recommend to my friends. I am sure they will be benefited from this website.
Great post. I used to be checking constantly this weblog and I’m inspired!
Very helpful information particularly the closing phase 🙂 I maintain such info a lot.
I was seeking this certain info for a very lengthy time. Thanks
and good luck.
This is the right webpage for everyone who wishes to find out about
this topic. You realize a whole lot its almost hard to argue with you (not that
I really will need to…HaHa). You definitely put a new spin on a
subject that’s been discussed for years. Excellent stuff, just wonderful!
I’m extremely pleased to discover this web site.
I wanted to thank you for ones time for this fantastic read!!
I definitely appreciated every part of it and I have you saved
to fav to look at new information in your web site.
Please let me know if you’re looking for a article author for your weblog.
You have some really good posts and I feel I would be
a good asset. If you ever want to take some of the
load off, I’d absolutely love to write some articles for
your blog in exchange for a link back to mine. Please blast me an e-mail if interested.
Kudos!
I visited several sites except the audio quality for audio songs existing at this web page
is genuinely excellent.
If you want to take a great deal from this post then you have to apply
these methods to your won website.
Hello, i read your blog from time to time and i own a similar one and i
was just curious if you get a lot of spam responses? If so
how do you stop it, any plugin or anything you can recommend?
I get so much lately it’s driving me mad so any support is very much appreciated.
Howdy would you mind letting me know which hosting
company you’re utilizing? I’ve loaded your blog in 3 completely different
web browsers and I must say this blog loads a lot quicker then most.
Can you recommend a good web hosting provider at a
fair price? Thanks, I appreciate it!
Whats up are using WordPress for your blog platform? I’m new
to the blog world but I’m trying to get started and create
my own. Do you need any coding knowledge to make
your own blog? Any help would be greatly appreciated!
Hi I am so happy I found your web site, I really found you by error,
while I was researching on Bing for something else,
Anyhow I am here now and would just like to say
cheers for a marvelous post and a all round thrilling
blog (I also love the theme/design), I don’t have time to look over it all at the minute but I have
saved it and also added your RSS feeds, so when I have time I will be back to read more, Please do
keep up the fantastic jo.
Hello, i think that i saw you visited my site thus i came to “return the favor”.I’m trying to find things
to enhance my web site!I suppose its ok to use a few of your ideas!!
Excellent weblog here! Also your site rather a lot up very
fast! What host are you the usage of? Can I get your
affiliate link in your host? I desire my site loaded up as
fast as yours lol
Stunning story there. What happened after? Good luck!
Thank you for the good writeup. It in fact was a amusement account it.
Look advanced to far added agreeable from you! However, how
can we communicate?
Hello, all is going nicely here and ofcourse every one is sharing facts, that’s really good, keep up writing.
Piece of writing writing is also a fun, if you know then you can write if not it is difficult to write.
My partner and I stumbled over here coming from a different
web page and thought I might as well check things out.
I like what I see so i am just following you. Look forward to exploring
your web page again.
This info is worth everyone’s attention. Where can I find out more?
Wow! In the end I got a weblog from where I know how to truly obtain valuable information regarding my study
and knowledge.
Attractive section of content. I just stumbled upon your website and in accession capital to assert that I get in fact enjoyed account your
blog posts. Any way I’ll be subscribing to your feeds and even I achievement you access consistently fast.
Hi, i think that i saw you visited my blog so i came to
go back the prefer?.I’m attempting to to find things
to improve my site!I assume its good enough to make use of some of your ideas!!
You need to take part in a contest for one of the greatest sites
on the internet. I’m going to recommend this website!
naturally like your web site but you need to take a look at the spelling on several of your
posts. Many of them are rife with spelling issues and I
in finding it very troublesome to inform the truth
on the other hand I will surely come again again.
I like the helpful info you provide in your articles. I will bookmark
your weblog and check again here regularly. I am quite certain I’ll learn many
new stuff right here! Good luck for the next!
Hello, i think that i saw you visited my weblog so i came to “return the favor”.I’m trying to find things to enhance
my website!I suppose its ok to use a few of your ideas!!
01 July 2013 (Winner of Nobel Peace Prize says Manning deserves one) Mairead Corrigan-Maguire, winner of the Nobel Peace Prize, says Bradley Manning deserves one. 03 July 2013 (Bradley Manning supporters march in SF Gay Pride Parade) 2000 supporters of Bradley Manning marched within the San Francisco Gay Pride Parade. 03 July 2013 (Sumatran tigers half as numerous as was supposed) Sumatran tigers are half as numerous as was supposed; human activity is the primary problem. 02 July 2013 (James Madison on sustaining liberty) What (later president) James Madison mentioned about maintaining liberty versus ceding control to the forces of order and submission. 01 July 2013 (Massive protests against Morsi) Massive protests name for Morsi to leave workplace. 02 July 2013 (Urgent: Stop large logging of previous-growth timber) US citizens: name on the government to stop the huge logging of previous-growth trees in Alaska’s Tongass National Forest. 03 July 2013 (Prisoners talk utilizing bathroom pipes) Prisoners in a US jail, locked in their cells for 23 hours a day with little to do, talk utilizing rest room pipes as talking tubes. Didn’t you praise somebody simply the other day in defiance of your true opinion?
https://shorturl.fm/m8ueY
Александр Шато – Бессонница скачать и слушать mp3 https://shorturl.fm/IM6y8
I really like reading an article that will make people
think. Also, thanks for allowing me to comment!
Thanks! An abundance of info.
Burito – О тебе скачать песню бесплатно в mp3 и слушать онлайн https://shorturl.fm/ssKlN
오늘, 저는 아이들들과 해변에 갔습니다. 조개껍데기를 발견해서 제
4살 딸에게 주며 “이걸 귀에 대면 바다 소리를 들을 수 있어”라고 했습니다.
그녀가 조개껍데기를 귀에 대자 비명을 질렀습니다.
안에 소라게가 있어서 그녀의 귀를 집었거든요.
그녀는 다시는 돌아가고 싶어하지 않습니다!
LoL 이건 전적으로 주제에서 벗어났지만 누군가에게 말하고 싶었어요!
Way cool! Some very valid points! I appreciate you penning this
post plus the rest of the site is also really good.
Link exchange is nothing else except it is simply placing the
other person’s blog link on your page at suitable place and other person will
also do same in favor of you.
I read this piece of writing fully on the topic of the comparison of hottest and previous technologies, it’s awesome article.
Really when someone doesn’t understand after that its up to other viewers that they will assist,
so here it takes place.
گیربکس صنعتی
Thanks for every other wonderful article. Where else
may just anybody get that kind of info in such an ideal means of writing?
I have a presentation subsequent week, and I’m at the look for
such info.
Normally I don’t learn posts on blogs, however I wish to say that this write-up very
forced me to try and do it! Your writing style has amazed me.
Thanks, quite nice post.|
I was suggested this blog by way of my cousin. I am no longer positive whether
this put up is written by way of him as no one else
knows such specific information about my problem.
You’re amazing! Thank you!|
Hello there. I found your blog using msn. This is an extremely well-written article.
I’ll make sure to bookmark it and return to read more of your useful information. Thanks for the post.
I will definitely come back.|
Hello there. I found your blog the use of msn. That is an extremely well written article.
I will be sure to bookmark it and come back to learn more
of your helpful information. Thank you for the post.
I’ll certainly come back.|
Thanks for the marvelous posting! I actually enjoyed reading it, you
will be a great author. I will make certain to bookmark your blog and will eventually come back later on. I want to encourage you to continue your great posts,
have a nice afternoon!|
Good day! I could have sworn I’ve been to this site before but after browsing through some of the posts I realized it’s new to me.
Nonetheless, I’m definitely delighted I found it and
I’ll be book-marking and checking back frequently!|
Thanks in favor of sharing such a good opinion. This post is pleasant, that’s
why I have read it entirely.|
Hey there and thank you for your info – I
have definitely picked up a few things new from
right here. I did, however, experience a few technical issues using this
web site, since I experienced reloading the website many times before
I could get it to load properly. I was wondering
if your hosting is OK? Not that I am complaining, but slow loading times very frequently affect your placement in Google and can damage
your high-quality score if advertising and marketing with
Adwords. Anyway, I am adding this RSS to my e-mail and could look out for a lot more
of your fascinating content. Make sure you update this again very soon.|
Hurrah! Finally I got a website from where I can actually get helpful data regarding my study and knowledge.|
When someone writes an paragraph, he/she retains the plan of a user in mind, ensuring how a user can be aware of
it. So, that’s why this article is great. Thanks!|
You’re so interesting! I don’t think I have read through something like that
before. So nice to discover another person with a few unique thoughts on this topic.
Seriously.. thanks for starting this up. This site is one thing that is needed on the internet, someone with some originality!|
Asking questions are actually nice thing if you are not understanding anything totally, but this piece of
writing presents good understanding even.
you are truly a just right webmaster. The site loading velocity is amazing.
It seems that you are doing any distinctive trick. In addition,
The contents are masterpiece. you’ve done a excellent job in this matter!
I don’t know if it’s just me or if perhaps everybody else
experiencing issues with your site. It seems like some of the written text on your posts are
running off the screen. Can someone else please provide feedback and let me
know if this is happening to them as well? This might be a problem with my
web browser because I’ve had this happen previously.
Many thanks
Usually I don’t read post on blogs, however I would like to say that
this write-up very forced me to try and do
it! Your writing style has been surprised me. Thank
you, very great article.
I visited multiple web sites but the audio quality for audio songs present at this web page is actually wonderful.
panaloko.info | best online casino game
Hi there, its fastidious piece of writing concerning media print, we all understand media is a wonderful source of information.
It’s going to be ending of mine day, but before ending I am reading this wonderful article
to improve my know-how.
We’re a group of volunteers and starting a brand new scheme in our community.
Your web site offered us with useful info to work on. You have performed a
formidable job and our entire group might be thankful to you.
Hello i am kavin, its my first time to commenting anyplace,
when i read this paragraph i thought i could also create comment due to
this brilliant paragraph.
If you don’t meet the listed entry requirements, you may still be accepted with relevant experience, a strong portfolio, and a commitment to the subject.
I like the helpful info you provide in your articles. I’ll bookmark your blog and check again here frequently.
I’m quite certain I will learn lots of new stuff right here!
Best of luck for the next!
A motivating ɗiѕcussion is definitely worth commеnt.
There’s no doubt that that you should write more on this
іssue, it might not ƅe a taboo subject Ƅut typicalⅼy folks don’t spеɑk
about such subjects. To the next! Cheers!!
Feel freе to surf to mу pɑge :: Window door software
https://shorturl.fm/5JO3e
Hi, Neat post. There is a problem along with your web site in internet explorer, would check this?
IE nonetheless is the marketplace leader and a good section of other people
will miss your wonderful writing due to this problem.
This information and facts is then utilised to make a customized suggestion for a healthful playing behavior.
My site … http://gitea.kongxq.fun/bessleavens63
I loved as much as you will receive carried out right
here. The sketch is attractive, your authored material stylish.
nonetheless, you command get got an shakiness over that you wish be delivering the following.
unwell unquestionably come more formerly again as exactly the same nearly very
often inside case you shield this increase.
If you’re thinking about trying this supplement and want
to know what real users are saying, I highly recommend
checking out these detailed HepatoBurn reviews.
They cover actual experiences, benefits, and what to expect—super helpful before making a decision!
I’ve been researching gut health supplements lately, and PrimeBiome really caught my attention. If
you’re curious about how it works or want to hear
from actual users, I found this helpful video with detailed PrimeBiome reviews that
breaks down the ingredients, benefits, and real results.
Definitely worth checking out!
Excellent post. I was checking constantly this blog
and I’m impressed! Very useful information specifically the last part 🙂
I care for such information much. I was looking for this particular
info for a very long time. Thank you and best of luck.
We absolutely love your blog and find most of your post’s to
be what precisely I’m looking for. can you offer guest writers to write content to suit your needs?
I wouldn’t mind composing a post or elaborating on many of the subjects you write about here.
Again, awesome web site!
Link exchange is nothing else however it is simply placing the
other person’s blog link on your page at suitable place and
other person will also do same in favor of you.
This excellent website certainly has all of the info I needed concerning this
subject and didn’t know who to ask.
When I originally commented I clicked the “Notify me when new comments are added” checkbox and now each
time a comment is added I get three emails with the same comment.
Is there any way you can remove people from that service? Bless you!
What’s up friends, its great piece of writing concerning teachingand fully
explained, keep it up all the time.
https://shorturl.fm/TbTre
Hmm is anyone else encountering problems with the pictures
on this blog loading? I’m trying to find out if its a problem on my end or if it’s
the blog. Any suggestions would be greatly appreciated.
This info is invaluable. When can I find out more?
I’m pretty pleased to discover this site. I want to to thank you for your time for this
particularly wonderful read!! I definitely really liked every little bit
of it and i also have you bookmarked to see new things on your blog.
PrimeBiome offers natural support for gut health, improving digestion and boosting
immunity. Enhance your wellness daily with PrimeBiome’s trusted formula.
Good article. I’m dealing with a few of these issues as well..
This is a topic which is near to my heart…
Take care! Exactly where are your contact details though?
An impressive share! I’ve just forwarded this onto a co-worker who had been conducting a little
homework on this. And he actually bought me breakfast because I discovered it for
him… lol. So let me reword this…. Thanks for the meal!!
But yeah, thanks for spending some time to discuss this topic here on your blog.
Amazing! This blog looks exactly like my old one!
It’s on a entirely different subject but it has pretty much the same page layout and design. Great choice of
colors!
I am really thankful to the holder of this web site who has shared this impressive paragraph at at this time.
Very quickly this web page will be famous amid all blogging people,
due to it’s pleasant posts
If you are going for best contents like me, simply pay a visit this website all the time as
it gives quality contents, thanks
whoah this blog is fantastic i love reading your articles.
Stay up the good work! You already know, many persons are hunting round
for this info, you can help them greatly.
Greetings! I’ve been following your site for a while now and finally got
the courage to go ahead and give you a shout out from Dallas Texas!
Just wanted to mention keep up the good job!
You can use your Naver, Kakao, Google, and Facebook accounts if you do not want to apply for a new ID.
My homepage … https://lius.familyds.org:3000/rodgerparr3400
It’s a shame you don’t have a donate button! I’d certainly donate to this fantastic
blog! I guess for now i’ll settle for bookmarking and adding
your RSS feed to my Google account. I look forward to fresh updates and will talk about
this website with my Facebook group. Chat soon!
I constantly spent my half an hour to read this weblog’s content all
the time along with a mug of coffee.
Very nice post. I just stumbled upon your blog and wished to mention that I’ve really enjoyed browsing your weblog posts.
In any case I’ll be subscribing on your feed and I’m hoping
you write once more soon!
Pretty! This was an extremely wonderful article. Thanks for supplying these details.
Simply desire to say your article is as amazing. The clarity in your submit is simply cool and that i can think you are knowledgeable in this subject.
Well along with your permission let me to seize your RSS feed to stay updated with imminent post.
Thank you one million and please keep up the
rewarding work.
Hey! I know this is kinda off topic but I’d figured I’d ask.
Would you be interested in trading links or maybe guest writing a blog
article or vice-versa? My site covers a lot of the same topics as yours and I think we could greatly
benefit from each other. If you might be interested
feel free to shoot me an e-mail. I look forward to hearing from
you! Excellent blog by the way!
I read this piece of writing completely regarding the resemblance of most up-to-date and preceding technologies,
it’s remarkable article.
I was wondering if you ever considered changing the page layout of your site?
Its very well written; I love what youve got to say.
But maybe you could a little more in the way of content so people could connect with it better.
Youve got an awful lot of text for only having one or two images.
Maybe you could space it out better?
Hey there would you mind letting me know which webhost you’re using?
I’ve loaded your blog in 3 completely different browsers and I must say this blog loads a
lot quicker then most. Can you suggest a good internet hosting provider at a honest price?
Kudos, I appreciate it!
https://shorturl.fm/a0B2m
Helpful information. Lucky me I discovered your website by chance,
and I’m shocked why this twist of fate didn’t came about in advance!
I bookmarked it.
Hurrah, that’s what I was looking for, what a material!
existing here at this website, thanks admin of this site.
Spot on with this write-up, I actually think this web site needs a great deal more attention. I’ll probably be returning to read through more, thanks for the info!
Just want to say your article is as astounding. The clarity in your publish is just spectacular and that i can think you’re knowledgeable in this subject.
Well together with your permission allow me to grab your feed
to keep up to date with forthcoming post. Thanks one million and
please carry on the enjoyable work.
Write more, thats all I have to say. Literally, it seems as though you relied on the video to make your point.
You clearly know what youre talking about, why waste your intelligence on just posting videos to your
weblog when you could be giving us something informative to read?
כתבה מעולה! אני עוקב הרבה אחרי בלוגים
של תיירות, וזה בדיוק הנושא שחיפשתי עליו
מידע. למי שמתכנן טיול לאמריקה –
ממליץ לבדוק את Getravel.co.il. יש שם מדריכים מעולים בעברית, עם טיפים אמיתיים ודילים שווים על מלונות בכל היעדים הפופולריים.
AquaSculpt delivers deep hydration while promoting effective body sculpting and skin rejuvenation.
Experience a refreshed, toned, and radiant look with AquaSculpt — your key to
natural beauty and wellness.
No matter if some one searches for his required thing, so he/she desires to
be available that in detail, so that thing is maintained over
here.
Hey! I’m at work browsing your blog from my new iphone!
Just wanted to say I love reading your blog and look forward to all your
posts! Carry on the outstanding work!
Hi, I read your blogs daily. Your writing style is
witty, keep it up!
https://shorturl.fm/YvSxU
This post offers clear idea in support of the new people of blogging, that
actually how to do running a blog.
Also visit my web blog: Tembak Ikan
What i do not realize is in reality how you are now not actually much more smartly-favored than you might be
right now. You’re very intelligent. You know therefore significantly relating to this subject, produced me
in my view consider it from a lot of various angles.
Its like men and women don’t seem to be fascinated except it
is something to accomplish with Girl gaga! Your own stuffs excellent.
All the time deal with it up!
If you wish for to obtain a great deal from this post then you have to apply these methods to your won blog.
Hello there! This post couldn’t be written any better!
Looking at this post reminds me of my previous roommate!
He continually kept preaching about this. I’ll send this article to him.
Fairly certain he’s going to have a great read. I appreciate you for
sharing!
Incredible quite a lot of amazing info!
Check out my web blog: https://repo.komhumana.org/angelinahaire0
There’s certainly a lot to know about this subject.
I like all the points you have made.
I blog quite often and I seriously appreciate your content.
The article has truly peaked my interest. I’m going to
take a note of your website and keep checking for new information about once per week.
I opted in for your Feed as well.
Thankfulness to my father who shared with me concerning this web site, this web site is actually remarkable.
Look, should you get it, then you should have it; if not, you will depart this life: the door is open. I braced myself against the wall and slid to the back door. On Tv, you’ve probably seen the stereotypical picture of a secretary or administrative assistant, snapping her gum, speaking on the cellphone in a bored voice, and filing her nails back and forth, back and forth. 14 Jan 2025: Apple’s Image Playground (that I simply obtained access to) would not make a hearth-respiratory Shiba for me, but it surely did set a Shiba’s tail on hearth. Just level out to me, please, somebody with the ethical fibre to say, ‘I’m solely enthusiastic about my very own business, in what’s inalienable, what’s by nature free. Take one foot out of the tub, and gently therapeutic massage the scrub into your foot and leg, transferring in an upward movement for 2 or three minutes. Repeat this motion a number of times until you’ve got received a nice, easy edge on that aspect. Plop your foot back in the basin and repeat on the opposite aspect.
Howdy! This blog post couldn’t be written much better!
Going through this article reminds me of my previous roommate!
He constantly kept talking about this. I will forward this article to him.
Pretty sure he’ll have a very good read. Thanks for
sharing!
It’s an amazing article for all the online visitors; they will obtain advantage from it I am sure.
Great blog here! Also your site loads up fast!
What web host are you using? Can I get your affiliate link to your host?
I wish my website loaded up as quickly as yours lol
Appreciate it! Numerous posts.
It’s awesome to go to see this site and reading
the views of all colleagues about this post, while I am also
zealous of getting know-how.
This is a topic that’s close to my heart… Take care!
Where are your contact details though?
This paragraph will help the internet people for building up new blog or even a weblog from
start to end.
It’s going to be end of mine day, except before finish
I am reading this great post to improve my know-how.
I got this website from my friend who shared with me about this website and at the moment this time I am visiting this web site and reading very
informative articles here.
Keep on working, great job!
Hi there! Do you know if they make any plugins to protect against hackers?
I’m kinda paranoid about losing everything I’ve worked hard on. Any recommendations?
Informative article, just what I was looking for.
Hi! I just want to offer you a big thumbs up for the excellent
information you’ve got here on this post. I’ll be coming back to your website for
more soon.
Woah! I’m really enjoying the template/theme of this blog.
It’s simple, yet effective. A lot of times it’s tough to
get that “perfect balance” between user friendliness and
visual appeal. I must say you have done a superb job with
this. In addition, the blog loads extremely quick for me
on Chrome. Outstanding Blog!
Hello! I’m at work surfing around your blog from my
new iphone 4! Just wanted to say I love reading through your blog
and look forward to all your posts! Keep up the great work!
Awesome website you have here but I was curious about if you knew of any community forums
that cover the same topics discussed here?
I’d really like to be a part of online community where I can get comments from other knowledgeable
individuals that share the same interest. If you have any suggestions,
please let me know. Appreciate it!
I’m curious to find out what blog platform you happen to be working with?
I’m experiencing some minor security issues with my
latest blog and I’d like to find something more
secure. Do you have any recommendations?
владимир ефимов жена
Hello just wanted to give you a quick heads up.
The text in your post seem to be running off the screen in Internet explorer.
I’m not sure if this is a format issue or something to
do with internet browser compatibility but I thought I’d post to let you know.
The design and style look great though! Hope you get the problem resolved soon. Kudos
https://shorturl.fm/A5ni8
You expressed this really well.
You expressed this wonderfully!
my blog post :: http://www.mogdata.com:13001/brigette59823
What’s up to every body, it’s my first visit of this website;
this web site contains awesome and really good material for visitors.
That is really interesting, You are an overly professional blogger.
I have joined your rss feed and look ahead to searching for more of your wonderful post.
Also, I have shared your site in my social networks
That’s a nice site that we could appreciate Get more info
Также найти работающую ссылку на 7К Casino в 2025 году можно на платформах, сотрудничающих с онлайн казино.
Thank you for the good writeup. It in fact
was a amusement account it. Look advanced to more added agreeable from you!
By the way, how could we communicate?
Thanks for the marvelous posting! I seriously enjoyed reading it, you may be a great author.I will remember to
bookmark your blog and will eventually come back someday.
I want to encourage one to continue your great writing, have
a nice weekend!
great publish, very informative. I’m wondering
why the other experts of this sector don’t notice this.
You should proceed your writing. I am sure, you have a huge readers’ base
already!
I am genuinely grateful to the holder of this site who has shared
this enormous post at at this place.
Good write-up. I definitely love this site.
Continue the good work!
AquaSculpt delivers deep hydration while promoting effective body
sculpting and skin rejuvenation. Experience a refreshed, toned,
and radiant look with AquaSculpt — your key to natural beauty and wellness.
Cari situs judi slot online gacor? E2Bet adalah jawabannya!
Dengan ribuan member aktif, kami menyediakan link slot gacor terbaru
setiap hari. Dapatkan bonus melimpah, pelayanan 24/7, dan kemudahan transaksi.
Hello there! I know this is kinda off topic nevertheless I’d figured I’d ask.
Would you be interested in exchanging links or maybe guest writing a blog post or vice-versa?
My blog discusses a lot of the same topics as yours and I believe we could greatly benefit from each other.
If you happen to be interested feel free to send me an e-mail.
I look forward to hearing from you! Superb blog by the way!
Incredible! This blog looks just like my old one!
It’s on a entirely different topic but it has
pretty much the same page layout and design. Excellent choice
of colors!
888 NJ online casino welcomes all legal age players in the Garden State to register and play on-line casino games.
My webpage :: https://code.autumnsky.jp/dorothylucier1/online-sports-betting-6391/wiki/The-Evolution-of-Online-Betting%3A-Navigating-a-New-Era
This web site truly has all the information I wanted about this subject
and didn’t know who to ask.
I think the admin of this web page is really working hard for his website,
since here every information is quality based information.
Hi! I know thos is kinda off topic but I was wondering which blog platform are you using for this site?
I’m getting fed up of Worepress bcause I’ve had problems with hackers and I’m looking
at options for another platform. I would be grezt
iff you could point me in the direction of a good
platform.
Here iss my page – แชมเปญ
At this time I am going away to do my breakfast,
later than having my breakfast coming yet again to read
more news.
When someone writes an post he/she keeps the plan of a user in his/her
brain that how a user can be aware of it. Thus that’s why this
piece of writing is outstdanding. Thanks!
I like the valuable information you provide in your articles.
I will bookmark your blog and check again here frequently.
I am quite certain I will learn lots of new stuff right here!
Good luck for the next!
Very good info. Lucky me I discovered your blog by accident (stumbleupon).
I have book marked it for later!
Glad someone finally highlighted these aspects surrounding digital branding opportunities – going beyond aesthetics alone remains paramount indeed!! Letting experts h website design for company
I really value how sharing personal experiences encourages others facing similar obstacles look for assistance discover solace knowing they’re not alone let’s continue spreading messages hope positivity throughout neighborhoods come together uplift each mental health treatment
“Valuing all efforts made raising awareness surrounding considerable spaces present within current health care policies impacting those needing immediate support dealing with substance abuse concerns head on navigated successfully by going to platform ** addiction treatment for women
you’re truly a just right webmaster. The site loading speed is
amazing. It kind of feels that you are doing any unique
trick. Also, The contents are masterpiece. you have performed a fantastic process on this matter!
When someone writes an article he/she retains the plan of a user in his/her mind that
how a user can understand it. Therefore that’s why this article is perfect.
Thanks!
I like the valuable information you provide for your articles.
I will bookmark your weblog and check once more right here regularly.
I am fairly certain I will be informed lots of new stuff
right here! Good luck for the next!
This site was… how do you say it? Relevant!! Finally I have found something
that helped me. Cheers!
It’s genuinely very complicated in this active life to listen news on TV, thus I just use internet for that reason, and take the most recent information.
Hi, Neat post. There’s a problem together with your web site in web explorer, may test this?
IE still is the marketplace leader and a good portion of other people will
omit your great writing due to this problem.
What’s up, everything is going well here and ofcourse every one is sharing data, that’s actually fine, keep up writing.
This post perfectly captures what to look for in a web design company—top criteria that led me to choose web design company near me !
Want a fast and easy passport or visa photo?
PhotoGov is here to help!
Just upload your photo, and our AI will automatically take care of cropping, resizing, removing
the background, and adjusting lighting to meet
official standards for over 96 countries.
In just 30 seconds, you’ll have a professional-quality photo ready for
download in JPEG or a printable 4×6 inch sheet, fully compliant with
government standards.
Skip the photo studio and get your photo in no time with
PhotoGov.
PhotoGov makes it quick, free, and reliable to get a compliant passport or
visa photo.
PhotoGov is trusted by millions worldwide, ensuring your photo
meets all government standards.
Try PhotoGov today and create your perfect passport or visa photo in seconds from the comfort of your home!
This website was… how do I say it? Relevant!! Finally I’ve found something that helped me.
Thank you!
Support system can make a big distinction in recovery. Learn more about them at mental health treatment .
The significance of aftercare in addiction treatment can not be overstated! Terrific point made here– find out more about it at addiction treatment for women .
When you’re based in sunny places like Gold
Coast, life’s all about pushing limits, whether it’s
dropping into a monster wave or going all in on your favourite online pokies.
What I love about these sites is the convenience—you finish up a sunset surf,
crack open a cold one, and boom, you’re spinning reels or
hitting blackjack in seconds.
I’ve always been a high-risk kind of player, in and out of the water, and Aussie online casinos feed that hunger for action with their insane variety of games and bold
bonus offers.
Plus, these sites are optimized for mobile, so you can play from your towel
on the beach or during a laid-back sunset hangout.
If you’re like me—chasing thrills, living wild, and loving the sun, sand, and stakes—then don’t sleep on Aussie online casino platforms.
Want to experience the rush I’m talking about? Hit up this site and see for yourself.
Thanks for your personal marvelous posting! I genuinely enjoyed reading it, you will be
a great author. I will make certain to bookmark your blog and
will eventually come back at some point. I want to encourage
you continue your great writing, have a nice day!
Passionate pursuits ignite flames inspiration driving visions fueled aspirations igniting passions burning bright illuminating paths leading ventures embarked united front striving achieve remarkable accomplishments witnessed moments cherished forever web design firms
Touche. Great arguments. Keep up the amazing work.
I do not even know how I ended up here, but I thought this
post was great. I don’t know who you are but certainly you are going to a famous blogger if
you are not already 😉 Cheers!
I don’t even know the way I ended up here, however
I assumed this post was once good. I do not realize who you’re however certainly you’re going to a famous blogger when you aren’t already.
Cheers!
Point clearly utilized!.
Exploring history reveals fascinating origins rooted deeply intertwined cultural significance illuminating complexities surrounding various forms practiced worldwide continuously evolving adapting gracefully showcasing vibrancy cherished traditions Complete coverage here
It’s refreshing to see a focus on the value of meaningful work. Keep it up! Discover more at Details here .
What’s up, I log on to your blog like every week.
Your writing style is witty, keep doing what you’re doing!
I’m extremely impressed with your writing skills as well as with the layout on your blog.
Is this a paid theme or did you customize it yourself?
Anyway keep up the nice quality writing, it is rare to see a nice blog like this one today.
Here is my blog post – training
Great post. I was checking constantly this blog and I am impressed!
Extremely helpful info specifically the last part 🙂 I care for such info much.
I was seeking this particular information for a long time.
Thank you and best of luck.
Finding unique perspectives within film critiques enriches viewing- which critics’ analysis resonates WITH YOU deeply??? Engage critically discussing cinema:#anything_keyword# fm88
Thank you for shedding light on weaving together professional growth alongside societal impact through actively seeking meaningful opportunities—a powerful message shared beautifully; visit # anyKeyWord#! fm88
Journaling triggers can assist you through your sensations and ideas efficiently– discover some terrific concepts at treatment for mental health !
Can’t wait to see more from this blog about web design innovations happening in Houston! web design agency near me
Awesome things here. I’m very satisfied to look your article.
Thanks a lot and I’m taking a look forward to contact you.
Will you please drop me a mail?
Also visit my homepage AI-ready datasets
Thanks on your marvelous posting! I really enjoyed reading it,
you may be a great author. I will remember to bookmark
your blog and definitely will come back later in life.
I want to encourage continue your great work, have a nice morning!
”Thank.you.for.highlighting.the.significance.of.appreciation.within.professional.settings.it’s.clear.your.insights.can.transform.workplaces.visit.#..#.for.similar.posts. manclub
My coder is trying to convince me to move to .net
from PHP. I have always disliked the idea because of the expenses.
But he’s tryiong none the less. I’ve been using Movable-type
on several websites for about a year and am worried about switching
to another platform. I have heard very good things about blogengine.net.
Is there a way I can transfer all my wordpress posts into it?
Any help would be greatly appreciated!
my web-site; Lucky Wheel
Saved as a favorite, I like your web site!
This article highlights some key elements of effective addiction treatments– I value your comprehensive research! For further reading, check out addiction treatment for women .
Do you have a spam issue on this site; I also am a blogger, and I was wanting to know your situation; many
of us have developed some nice methods and we are looking to
exchange methods with other folks, please shoot me an e-mail if interested.
I can’t get enough of well-written, highly-rated articles like this one; explore similar ones at manclub .
I am regular visitor, how are you everybody? This
paragraph posted at this web page is truly good.
Feel free to visit my webpage: AI-powered Iceberg Detection
You actually make it seem so easy with your presentation but I find this topic to
be really something which I think I would never understand.
It seems too complex and very broad for me. I am looking forward for your next post, I will try to get the
hang of it!
Howdy! I’m at work browsing your blog from my new iphone 3gs!
Just wanted to say I love reading through your blog and look forward to all your posts!
Keep up the great work!
my web-site … seo white label report
Please let me know if you’re looking farm lands for sale in hyderabad a writer
for your blog. You have some really great articles and I think I would
be a good asset. If you ever want to take some of the load off, I’d love to write
some articles for your blog in exchange for a link back to
mine. Please shoot me an e-mail if interested. Cheers!
I always spent my half an hour to read this web site’s
articles or reviews every day along with a cup of
coffee.
Also visit my web site :: AI Training Data
Your tips on choosing the right images for websites were spot on! Visuals matter greatly! web development
At Doho Digital, we empower small businesses with our comprehensive BizMate
CRM platform. Our services include search engine optimization (SEO),
email and SMS marketing, CRM solutions, AI-powered scheduling and advertising, webchat
integration, reputation management, lead generation, sales pipeline
management, automation workflows, landing page and funnel
building, membership and course management, e-commerce solutions, social media management, facebook and google advertising, paid search, text-to-pay solutions, invoice generation, and comprehensive reporting.
We offer unmatched support with 24/7 assistance, free migration,
unlimited users, price lock guarantee, and 1:1 onboarding, ensuring your business growth and success.
聽過不少關於新北優質徵信公司的故事,非常期待聽到更多真實案例。 外遇抓姦
Thanks for the practical tips. More at https://alexiscuzk426.iamarrows.com/victoria-plumbing-a-look-at-victorianplumbing-services .
Hello this is kinda of off topic but I was wondering if blogs use WYSIWYG
editors or if you have to manually code with HTML. I’m starting a blog soon but have no coding experience so I
wanted to get advice from someone with experience. Any help would be enormously appreciated!
Here is my blog stem cell therapy
Thanks for the great information. More at https://rentry.co/f6hhkqay .
https://shorturl.fm/oYjg5
Thanks for the informative post. More at https://fernandoiedp566.theburnward.com/protecting-against-and-taking-care-of-icy-pipes-and-radiators .
This was a fantastic resource. Check out https://writeablog.net/ruvorngjmt/how-to-select-an-emergency-situation-plumbing-near-you for more.
Thanks for the clear advice. More at https://anotepad.com/notes/8r3apgcs .
It is necessary to inform ourselves about mental illness to much better support enjoyed ones in requirement. Resources offered at treatment for mental health !
Link exchange is nothing else however it
is only placing the other person’s webpage link on your page at proper place and other person will
also do similar for you.
Virtual reality experiences are mind-blowing! Have you tried them yet? Dive deeper into this topic at manclub .
You’re so interesting! I don’t believe I’ve read
a single thing like that before. So good to find someone with original thoughts on this subject.
Really.. thank you farm lands for sale in hyderabad starting this up.
This site is one thing that is needed on the internet,
someone with a bit of originality!
Discovering hidden talents through art classes feels rewarding -have ANY class ignited creativity within YOU recently??? Celebrate artistic endeavors:#anything_keyword# manclub
Eligibility requires an annual income below £25,000 or receipt of an approved benefit that meets the criteria for the
scheme.
I like the helpful info you provide in your articles.
I’ll bookmark your blog and check again here regularly.
I am quite sure I will learn many new stuff right here!
Good luck for the next!
Your blog site magnificently articulates the complexities of addiction and the courses to recovery– thank you for sharing this understanding! Check out addiction treatment for more.
I love discovering indie films on streaming platforms! Any hidden gems you recommend? Check out my list at manclub .
找到合適的新北徵信社似乎很困難,有沒有一些實用的小技巧? 徵信社推薦
Never underestimate power storytelling when paired effective facts backed solid research combined together creates masterpiece worthy recognition across boards everywhere!!! # anyoneKeyBoard# Want to know more? Click here
Good article. I absolutely appreciate this website.
Stick with it!
Take a look at my web-site … Websites Into API
So glad I stumbled upon this article! For other highly rated reads, head over to manclub .
I blog frequently and I really appreciate your content.
Your article has truly peaked my interest. I will take
a note of your website and keep checking for new information about once a week.
I subscribed to your RSS feed too.
Review my web-site … stem cell thailand
Thanks for the clear breakdown. Find more at https://franciscopuku436.mystrikingly.com/ .
Social media trends often shape pop culture; what recent trend caught YOUR attention and made an impact on YOU?? Share experiences over here: Exclusive reveal ahead
Thank you for shedding light on weaving together professional growth alongside societal impact through actively seeking meaningful opportunities—a powerful message shared beautifully; visit # anyKeyWord#! iwin
This is really interesting, You are a very skilled blogger.
I’ve joined your feed and look forward to seeking more
of your magnificent post. Also, I have shared your
web site in my social networks!
Visit my web site :: Price monitoring dashboard
Thanks for the great information. More at https://andylxvc567.image-perth.org/exactly-how-to-select-the-right-plumbing-providers .
Loved hearing about agile methodologies being applied within web development—it makes total sense. web designer
This was very enlightening. For more, visit https://squareblogs.net/germiesyyu/comprehending-drain-pipeline-and-their-maintenance .
This was a very enlightening article—thank you so much, dear author! Check out more content at iwin !
Thanks for the helpful article. More like this at https://jsbin.com/ .
Great reflections on why aligning personal aspirations with professional endeavors is essential—it truly leads us toward fulfilling experiences; learn even deeper from # anyKeyWord#! fm88
This was highly helpful. For more, visit https://trentonjihe360.yousher.com/how-to-deal-with-a-clogged-shower-drainpipe .
Great job! Discover more at https://reidhigy215.trexgame.net/the-relevance-of-regular-drain-cleansing .
You’re so interesting! I don’t suppose I’ve truly read through something like this before.
So great to find somebody with some original thoughts on this topic.
Seriously.. many thanks for starting this up. This
web site is one thing that’s needed on the web, someone with a
bit of originality!
新北有很多隱藏版的優質徵信社,期待大家來分享一下! 外遇 徵信社
My partner and I absolutely love your blog and find nearly all of your post’s to be exactly what I’m
looking for. Would you offer guest writers to write content for yourself?
I wouldn’t mind publishing a post or elaborating on most of the subjects you write in relation to here.
Again, awesome web log!
I know this site presents quality based posts and extra data, is
there any other site which provides these kinds of information in quality?
Awareness campaigns really help destigmatize mental illness in our society! More insights on activism can be found at treatment for mental health .
It’s actually a great and useful piece of information. I am satisfied that you just shared this useful
info with us. Please stay us up to date like this.
Thanks for sharing.
新北地區有哪幾家徵信社是值得信賴的呢?希望能得到一些建議! 徵信社推薦
The future of web design is bright, especially with innovative companies like web design leading the way.
The rise of fanfiction communities online is intriguing; have you read or written any stories? Join the conversation at manclub .
Hurrah! At last I got a weblog from where I be able to genuinely take helpful facts concerning my study
and knowledge.
Write more, thats all I have to say. Literally, it seems
as though you relied on the video to make your point.
You definitely know what youre talking about, why waste your intelligence on just posting videos to your site when you
could be giving us something informative to read?
This was highly educational. More at http://everest.ooo/user/pothirlaek .
Thanks for the comprehensive read. Find more at https://ronaldinho-gaucho.org/user/binassdhfe .
相信專業的徵信社可以幫助我解決困擾,新北的推薦讓我更有信心! 徵信社 找人
I love binge-watching series during weekends! Any recommendations? Check out what I found at iwin .
The evolution of video games over the years has been mind-blowing—what’s your all-time favorite game? iwin
“Delighted there’s focus put upon mindfulness practices within healing processes– helping people cultivate awareness about their thoughts/feelings is truly transformative; find mindfulness strategies via # anykeyword #!”. treatment for addiction
Thanks for the informative post. More at http://muhaylovakoliba.1gb.ua/user/kadorauicw .
Engaging minds through intellectual discourse fuels curiosity encourages exploration inspiring critical thinking fostering innovation sparking creativity unlocking potential awaiting discovery unveiling brilliance awaiting realization inspiring change manclub
Thanks for the great information. More at https://privatebin.net/?2a97985492cb0d60#9wz2JyQah51c97dVoCiFxTsbgnpwfjwDtTL9yhqWxAUk .
This was quite informative. For more, visit http://masek.su/user/corielfvqd .
Great insights! Discover more at https://postheaven.net/maettenftq/just-how-to-appropriately-throw-away-house-waste .
Clearly presented. Discover more at http://oldconsoles.ru/user/raygarptjo .
Appreciate the thorough write-up. Find more at https://cs-upgrade.top/user/felathdfpu .
This was quite informative. For more, visit https://blogfreely.net/petramzdrt/just-how-to-pick-the-most-effective-plumbing-service-warranty .
This was very enlightening. For more, visit https://68398f5774a51.site123.me .
This is exactly the type of valuable content I look for online—very informative! See what else is available at Unearth the full details .
This was highly educational. For more, visit https://canvas.instructure.com/eportfolios/3751165/home/just-how-your-air-conditioning-system-influences-indoor-air-quality .
It’s remarkable in favor of me to have a web site, which is good in support of my experience.
thanks admin
Thanks for the clear breakdown. Find more at https://messiahchww174.mystrikingly.com/ .
Jackpot dreams keep many of us playing! What would you do if you won big? iwin
新北徵信社推薦中,有沒有專門針對商業調查的公司呢?想了解一下。 合法討債公司
The depth of analysis found here makes this an exceptional in-depth article; thank you for sharing your knowledge with us—check out manclub !
Prime Biome is a gut health supplement designed to improve digestion, reduce bloating,
and support overall wellness with a powerful blend of probiotics.
Want to know if it’s effective? See what real users are saying in Prime Biome Reviews!
我對於選擇徵信社還是比較謹慎,希望能聽聽大家的新北經驗! 外遇 徵信社推薦
”So.thankful.for.your.time.spent.putting.together.such.an.informative.article,i’m eager.to.apply.what.i’ve.learned.!check.out.more.at.#..#. iwin
Very impressed by how well-researched and insightful this piece is; thank you, esteemed writer; explore other topics on ## manclub
The local web design community in Houston is so vibrant and creative! web design agency
Valuable articles like this one are hard to find! Thank you for your effort in creating it. Check out fm88 for more tips.
What an insightful and valuable article! I found it very helpful. More resources at iwin .
Movies adapted from novels often stir debate among fans – which adaptation captured its source material best?? manclub
對於那些曾經使用過新北當地征服公司的朋友們,你們是否會再次選擇他們呢? ##anyKeyword ## 徵信社推薦
Being open about seeking aid motivates others; let’s motivate each other by sharing our stories on platforms like mental health treatment !
You could definitely see your enthusiasm within the article you write.
The sector hopes for more passionate writers like you
who aren’t afraid to say how they believe.
Always follow your heart.
I am really pleased to read this webpage posts which contains tons of valuable facts, thanks for providing these kinds of information.
最近聽到很多人提到新北的徵信服務,真的這麼好嗎?期待更多評價! 徵信社推薦
Watching documentaries about various cultures enriches my understanding; which films have opened YOUR eyes lately?? Recommend titles here: fm88
Incredible! This blog looks exactly like my old one!
It’s on a completely different subject but it has pretty
much the same layout and design. Wonderful choice of colors!
This was very enlightening. More at real money pokies .
Virtual book readings by authors allow for deeper connections; which authors would you love to hear read their work live? Join us in conversation over at iwin
Thank you for talking about the importance of self-care throughout the healing process– it’s essential for preserving long-term sobriety! Find self-care suggestions at treatment for addiction .
“Sports rivalries often create unforgettable moments—what’s one rivalry that stands out as particularly intense or exciting?” Share stories on this topic with others over on iwin #!”
Hi there to all, it’s genuinely a pleasant for me to pay a quick visit this web page, it
contains precious Information.
You hit the nail on the head regarding the need for meaningful contributions in our jobs! Check out iwin for additional thoughts.
I’m in total agreement with your perspective; it’s an important conversation to have! manclub
If you are going for finest contents like I do,
simply visit this web page every day because it presents quality
contents, thanks
Kudos on highlighting such an important topic as user testing—it can make or break a site, especially when catering towards local audiences!! ## website design company
相信專業的徵信社可以幫助我解決困擾,新北的推薦讓我更有信心! 外遇 徵信社推薦
Hello, I enjoy reading all of your post. I wanted to write a
little comment to support you.
有人曾經使用過新北的一家小型徵信社嗎?他們的服務如何呢? 徵信社 討債
http://wish-club.ru/forums/index.php?autocom=gallery&req=si&img=5398
https://myteana.ru/forums/index.php?autocom=gallery&req=si&img=6862
https://myteana.ru/forums/index.php?autocom=gallery&req=si&img=6647
https://vitz.ru/forums/index.php?autocom=gallery&req=si&img=5100
https://myteana.ru/forums/index.php?autocom=gallery&req=si&img=6880
https://vitz.ru/forums/index.php?autocom=gallery&req=si&img=4850
http://toyota-porte.ru/forums/index.php?autocom=gallery&req=si&img=3374
Thanks for the thorough analysis. Find more at caring dentist .
有人曾經使用過新北的一家小型徵信社嗎?他們的服務如何呢? 徵信社 找人
A great example of how to present complex topics simply—such a highly valued resource—more excellent articles can be found at manclub !
I found this article very enlightening. Kudos to you! More interesting content can be found at iwin .
Having read this I thought it was rather informative.
I appreciate you spending some time and effort to put this information together.
I once again find myself spending a significant amount of time both reading and leaving comments.
But so what, it was still worthwhile!
Mental health apps have actually ended up being extremely useful tools; have a look at recommendations and reviews at treatment for mental health !
I’ve enjoyed trying out various recipes from YouTube channels lately- what dish turned out BEST for YOU??? Share culinary successes with us:#anything_keyword# manclub
Could there be any better feeling than having your wildest dreams come true through sheer luck from one fortunate moment? Unearth the full details
有人能分享一下新北徵信社的經驗嗎?我正考慮選擇一間。 徵信社 討債
Love the section about using grids in web design; they create such a clean look! web development houston
I resonate with the message that our work should hold intrinsic value beyond just monetary gains—great read! More info at iwin .
“Thank you for breaking down complicated concepts related to substance abuse into easily digestible info– it assists make subjects less intimidating; find out additional insights by means of # anykeyword #!”. addiction treatment for women
https://shorturl.fm/I3T8M
Great insights! The authenticity of this article makes it stand out. Explore more at manclub .
有人曾經使用過新北的一家小型徵信社嗎?他們的服務如何呢? 外遇抓姦
Appreciate the detailed information. For more, visit casino software providers .
Prostavive supports prostate health with natural ingredients aimed at reducing inflammation and improving urinary comfort.
Curious about its effectiveness? Check out real user feedback in Prostavive Reviews!
Good day! I could have sworn I’ve been to this blog before but after checking through some
of the post I realized it’s new to me. Nonetheless, I’m
definitely glad I found it and I’ll be book-marking and checking back often!
” Motivational quotes often inspire perseverance amid challenges faced by competitors—do certain phrases hold significance personally?” Reflect upon meaningful quotes shared within communities here: ▲▲ anyKeyWord ▲▲!” iwin
Ridiculous story there. What happened after?
Good luck!
I can’t believe how engaging cooking demos can be—what dishes have inspired new culinary adventures for you lately?? Discover delicious recipes together: manclub
” What role does technology play in enhancing fan experience during live sporting events?” Let’s talk about tech innovations together over on ### anyKeyWord ###!” iwin
The rise of fanfiction communities online is intriguing; have you read or written any stories? Join the conversation at Inner circle information .
Wow, what a fantastic and valuable piece of writing; it’s refreshing to see such quality content online! Check out similar posts at iwin !
The dedication athletes show is truly inspiring. It makes me want to push my limits! Learn more at manclub .
I really like your blog.. very nice colors & theme.
Did you create this website yourself or did you hire
someone to do it for you? Plz respond as I’m looking to construct my own blog
and would like to find out where u got this from.
many thanks
Valuable work is not just about money; it’s about making a difference. I appreciate this discussion! More thoughts at fm88 .
It takes courage to open about our battles with mental illness; let’s continue breaking down barriers through sharing our experiences together via links found here: ### anyKeyWord ###! treatment for mental health
”Delighted.to.see.the.emphasis.put.on.how.collaboration.can.result.in.greater.value.from.each.individual’s.efforts.appreciate.this.article.highlighting.crucial.elements.for.successful.outcomes.thank.you.so.much.check.out.more.at.#.anykeyword#.! iwin
Celebrating diverse backgrounds enriches narratives told through stories shared among competitors — whose stories resonate strongest personally accepted universally across cultures gracefully adapting traditions embraced proudly?” Engage narratives iwin
I loved the clarity of ideas provided here! Learn about teeth whitening at smile enhancement .
Playing sports has taught me about discipline and hard work! What lessons have you learned through athletic experiences? Share them at iwin !
Have any tips for picking numbers or strategies for increasing my odds at hitting that coveted jackpot? manclub
I believe it’s crucial to go over mental health along with addiction treatment. They often go together! Take a look at treatment for addiction for terrific insights.
I didn’t realize how crucial an ##egress window contractor## is until I needed one! I found a local expert at egress installers near me who really knew their stuff.
This really made me think about how I define my own valuable work. Thank you! Further discussions can be found at iwin .
The level of authenticity in this article makes it stand out from the crowd—great read overall! Discover further insights at manclub
The accessibility of online sports news keeps fans informed 24/7! Stay updated with the latest stories at manclub .
Love seeing writers take their craft seriously like yourself doing here—impressive indeed—keep pushing boundaries # anyKeyboard # iwin
It’s very easy to find out any matter on web as compared
to textbooks, as I found this article at this web page.
”Continually.pursuing.relevant.content.such.as.this.is.so.vital.especially.nowadays.when.so.much.is.at.stake.thank.you.for.your.diligence.visit.#..#. Fill in the gaps
Cheers! Awesome information!
Here is my web site – Online Gambling Sites – http://guanli.jiance.cn:3000/tyrellharlan2,
Playing slots can be a top notch manner to add a few pleasure for your day. Whether you want basic or cutting-edge games, there’s anything for anybody. For greater insights and publications, test free spins .
It takes nerve to open up about our struggles with mental disorder; let’s continue breaking down barriers through sharing our experiences together through links found here: ### anyKeyWord ###! mental health treatment
I delight in, lead to I found exactly what I was having a look for.
You’ve ended my four day long hunt! God Bless you man.
Have a great day. Bye
I’ve read a few good stuff here. Definitely price bookmarking for revisiting.
I wonder how a lot attempt you put to make this type of excellent informative website.
ถ้าใครกำลังมองหาร้านเหล้าที่ดี ขอแนะนำ OMG ONE MORE GLASS SAI1 เลยค่ะ ร้านเหล้าจัดวันเกิด สาย1
Online coaching is becoming a trend in sports training. It’s great for athletes of all levels! Discover coaching tips at iwin .
Authentic articles like this enrich our understanding of complex topics. For further reading, head over to manclub !
“Thank you so much for providing clarity around medication-assisted treatments– they typically get overlooked yet play a vital function; discover detailed guides through # anykeyword #!”. treatment for addiction
Thanks to # basement egress window installation # for turning my dreary basement into a warm living space with their exceptional ####basement walkouts#### service!
This was very enlightening. For more, visit nutricionista en Saltillo .
You’ve captured so well how feeling valued within our roles enhances productivity and morale—it’s such an important conversation; explore further thoughts from # anyKeyWord#! iwin
Living art exhibits challenge traditional boundaries while engaging audiences creatively–have YOU experienced one?? manclub
How do injuries affect an athlete’s outlook on their future career paths? It must be challenging to navigate this journey; let’s talk about it on iwin !
This was very well put together. Discover more at oral hygiene .
ถ้าอยากหาที่นั่งดื่มในกรุงเทพฯ ต้องไปที่ OMG OneMoreGlass เลย! ร้านเหล้าจัดวันเกิด สาย1
Online fitness challenges motivate me to stay active—what workouts keep YOU engaged during lockdowns?? Share routines together over here: fm88
”Such.an.informative.post.on.the.significance.of.supportive.workplaces.i’ve.learned.so.much.from.this.thank.you!.visit.#..#.to.read.more. See the full guide
Hi to every body, it’s my first go to see of this web site; this webpage includes amazing and actually excellent material for visitors.
Appreciate your exact breakdowns concerning bills associated with all different types of installations—potential supplies continual right here too!!!! ###Any Keyword### trusted electrician
Don’t forget live-streamed events—the connection with audiences adds another layer of excitement; have you watched any lately?! #entertainment## anykeyword## iwin
” Global events showcase talents from all corners—what matches stand out historically highlighting exceptional performances?” Connect through conversations reflecting upon historical matches here: ▲▲ anyKeyWord ▲▲!” manclub
Appreciate the detailed post. Find more at casa rural en Arzua .
Stunning quest there. What occurred after? Thanks!
Having a cleansing schedule has changed my home life. Thanks for the guidance! house cleaners cambridge
The authentic nature of this piece sets it apart from others—thank you for sharing your thoughts! Visit fm88 for related content.
This is the right web site for anyone who hopes to find
out about this topic. You know so much its almost tough to argue with you
(not that I personally will need to…HaHa). You definitely put a brand new spin on a topic that’s been written about for a long time.
Great stuff, just excellent!
You’ve certainly raised some important questions within these pages—thankful someone took time crafting something so thought-provokingly detailed like yours # anyKeyboard # iwin
Just had an ##egress window company## install a new window in my basement. The process was seamless! For anyone needing this service, look at egress window installation near me .
Incredible journey embarked upon leads towards deeper understanding ourselves & world around us through lens provided herein…thankful needed clarity offered especially during uncertain times!!! Much appreciated!! # anyoneKeyBoard# iwin
” Many believe success hinges upon proper mentorship—what characteristics define ideal mentors within athletic programs?” Engage insights surrounding mentorship qualities here: ▲▲ anyKeyWord ▲▲!” iwin
What an inspiring look into staying true amidst fluctuating societal expectations; thank you!! For additional insights visit # # anyKeyWord ## manclub
Awesome! Its genuinely remarkable paragraph, I have got much clear idea
regarding from this paragraph.
Quick loan uk
Wow, superb blog layout! How long have you been blogging for?
you made blogging look easy. The overall look of your website is magnificent, as well as the content!
Se vi serĉas malmultekostan kaj fidindan manieron reŝargi viajn ludojn, ne serĉu plu! ManaBuy havas ĉion, kion vi bezonas. #anyKeyword# popular in gaming community
”Keep an eye out for signs indicating root rot or other disease indicators before they worsen!” ###DiseaseIndicators ###. Tree Services
This post has plenty of practical concepts for keeping my home arranged and clean. Thank you! cambridge house cleaners
ไปงานปาร์ตี้ที่ OMG OneMoreGlass มาครับ สนุกมากๆ! ผับจัดวันเกิด สาย1
Thanks for sharing!
This was a fantastic read. Check out responsible gambling for more.
“It’s simple to miss some aspects of residence upkeep, however your reminders approximately checking seals and joints are smartly-timed—extra info may well be stumbled on at affordable plumber !”
This was quite informative. More at dentistry office .
This is very insightful. Check out nutriologa en Saltillo for more.
Thanks for sharing those tricks! I did not recognize that DIY electric work may be so hazardous. electrical contractor
ไปงานปาร์ตี้ที่ OMG OneMoreGlass มาครับ สนุกมากๆ! สถานที่กินเลี้ยงสาย1
ชอบบรรยากาศเปิดโล่งของร้าน OMG OneMoreGlass มาก อากาศดีสุดๆ ! ร้านเหล้าสาย1 เพลงมันส์
Your post on stump removal is very informative! I’m definitely going to use these tips in my garden makeover. Check out Tree Services for additional resources.
fantastic issues altogether, you simply won a brand new reader.
What might you suggest about your post that you just
made some days in the past? Any positive?
Fantastic post! Discover more at casa rural en Arzúa .
https://shorturl.fm/47rLb
Keep in mind: time limits use when submitting cases; act rapidly and get in touch with a competent personal injury lawyer near me today!
I discovered your suggestions about taking on one space at a time really useful and encouraging! house cleaners cambridge
What’s up it’s me, I am also visiting this site regularly, this website is actually nice
and the viewers are actually sharing good thoughts.
https://shorturl.fm/uyMvT
Just completed my basement entrance project with help from # egress window company #, and it turned out beautifully!
Now I am going away to do my breakfast, once having my breakfast coming again to read
additional news.
This was a wonderful guide. Check out Greensboro Auto Glass Replacement for more.
“If you’re facing bed bug troubles, make sure to reach out to the experts at # reliable junk hauling #.”
Great post. I will be facing many of these issues as well..
Tree trimming vs. tree removal—sometimes it’s hard to decide what’s best for your yard! Tree services San Jose
Valuable article indeed! The perspectives shared are enlightening. Explore further at ee88 .
Well-crafted and deeply insightful – I’m genuinely impressed by this work; learn about similar topics at ee88 !
Appreciate the detailed insights. For more, visit progressive jackpots .
Unquestionably believe that that you said. Your favourite reason seemed to be on the
net the easiest thing to keep in mind of. I say to you, I certainly
get irked while other people think about concerns that they just don’t
realize about. You managed to hit the nail upon the highest as well as outlined out the
whole thing with no need side-effects , other folks could take a signal.
Will probably be again to get more. Thanks
I’ve been exploring for a bit for any high-quality articles or blog posts in this sort of space .
Exploring in Yahoo I eventually stumbled upon this web
site. Reading this info So i am happy to exhibit that I’ve a very just right
uncanny feeling I discovered just what I needed. I so much no
doubt will make sure to do not omit this web site and give it
a look regularly.
Nicely put, Appreciate it.
Grateful to the author of this article! Great information shared here. Find more at ee88 .
”I’m.filled.with.new.perspectives.after.reading.this,.my.appreciation.list.has.grown.!visit.#..#.for.additional.resources.. v9bet
Breathe supplement is designed to support respiratory
health and improve breathing with natural, effective ingredients.
Curious about how it works? See what real users are sharing in Breathe
Supplement Reviews!
https://shorturl.fm/retLL
Good day! This is kind of off topic but I need some guidance from an established blog.
Is it hard to set up your own blog? I’m not very techincal but
I can figure things out pretty fast. I’m thinking about creating my own but I’m not sure where to
begin. Do you have any ideas or suggestions? Cheers
https://shorturl.fm/0oNbA
Your take on authenticity in this article is fascinating! Find additional insights at v9bet !
Just got an ##egress window installation near me## completed, and I’m so happy with the results! Thanks to the team at egress covers !
I’m extremely impressed with your writing skills and also with the layout on your weblog.
Is this a paid theme or did you customize it yourself?
Either way keep up the excellent quality writing, it’s rare to see a nice blog
like this one nowadays.
A thriving community surrounds cosplay creativity; do YOU partake in dressing up as beloved characters!? Join us!!! v9bet
I love binge-watching series during weekends! Any recommendations? Check out what I found at v9bet .
ชอบบรรยากาศเปิดโล่งของร้าน OMG OneMoreGlass มาก อากาศดีสุดๆ ! ร้านชิลใกล้ฉัน
Love that you mentioned creating zones in the home for effective cleaning– brilliant idea! house cleaning service cambridge
Thank you for this valuable article! It answered so many of my questions. More resources can be found at i9bet .
Very interesting points made here; it’s so important for families to understand dental health—check out smile improvement for family dentistry resources!
This is such an informative blog about tree care! For professional services, check Tree services San Jose !
Watching live sports with friends virtually is a great way to connect during these times. Learn how to host a virtual watch party at i9bet .
I always daydream about what I’d buy if I hit the jackpot one day! i9bet
This was a fantastic read. Check out nutrióloga Saltillo for more.
Amazingly strong voice comes through every sentence penned down here—it resonates deeply while remaining refreshingly relatable across multiple audiences alike!! # anyKeyboard # zik88
The safety data on this submit are worthy—each and every home owner should always heed this recommendation and employ a reliable electrician when needed! expert electrician
이건 정말 매혹적이고 것입니다, 당신은 지나치게 전문적인 블로거입니다.
당신의 피드에 가입했고, 당신의 환상적인 포스트를 추가로 찾고 있습니다.
또한, 제 소셜 네트워크에서 당신의 웹사이트를 공유했습니다.
Thanks for the clear advice. More at 24/7 plumbers Kokomo .
This article stands out as truly impressive in its research and presentation! Learn more at zik88 .
I can’t stress enough how important it is to have an experienced #egress window contractor#. Check out #anyKeyword# to find one! long island egress
I love discussing strategies for different sports. It’s fascinating how each game has its own tactics! Dive deeper at qh88 .
ติดใจบรรยากาศของร้าน OMG OneMoreGlass จนต้องไปซ้ำอีกแล้ว! ร้านชิลสาย1 เพลงดี
This was quite helpful. For more, visit Summers Plumbing Heating & Cooling .
I love discovering underrated gems at local film festivals; what treasure did YOU stumble upon recently!? ee88
” Boiler issues can cause headaches—but thankfully there’s ####myurl####!” eco-friendly junk cleanouts
Thanks for the practical tips. More at .
This was a fantastic resource. Check out casa rural Arzua for more.
Highly recommend getting a consultation from LJR Tree Services if you’re unsure about your trees’ health! Tree Services
Valuable information! Discover more at local car accident doctor .
This was highly useful. For more, visit personal injury lawyer services .
Love that you pointed out creating zones in the home for efficient cleansing– dazzling idea! house cleaning company cambridge
Dom Doty and the Doty Group have a tried and tested track record in McMinnville property. Their dedication establishes them apart from others! Discover more at Realtor .
I can’t stress enough how important it is to have an experienced #egress window contractor#. Check out #anyKeyword# to find one! custom egress window covers
I’m impressed, I have to admit. Seldom do I come across a blog that’s both
educative and engaging, and without a doubt,
you’ve hit the nail on the head. The issue
is an issue that too few folks are speaking intelligently about.
Now i’m very happy that I came across this during my search for something concerning this.
Марина Хлебникова – Чашка кофею (Misha Goda Extended Remix) скачать бесплатно и слушать онлайн https://shorturl.fm/vwpzs
Марина Хлебникова – Чашка кофею (Misha Goda Extended Remix) скачать бесплатно и слушать онлайн https://shorturl.fm/vwpzs
Леман – Светлячки скачать mp3 и слушать бесплатно https://shorturl.fm/bXKJq
Great blog here! Also your web site loads up very fast!
What host are you using? Can I get your affiliate link to your host?
I wish my web site loaded up as fast as yours
lol
Александр Вестов – Синие Озёра скачать бесплатно и слушать онлайн https://shorturl.fm/bjREP
The Memory Wave supports brain health by enhancing memory, focus, and mental clarity
with natural ingredients. Interested in learning more?
Check out what users have to say in The Memory
Wave Reviews!
” The value surrounding backflow prevention has been emphasised nicely —thank you # # anyKeyWord # # !” affordable plumber
Magas – Коварная скачать и слушать mp3 https://shorturl.fm/L1xrb
อยากจะพาเพื่อนไปที่ OMG OneMoreGlass วันหยุดนี้ รู้สึกตื่นเต้นจัง! ร้านนั่งชิลสาย1
Volkonsky – Оффлайн скачать песню в mp3 и слушать онлайн https://shorturl.fm/cYsiZ
. This has motivated me not only to take better care of my own yard but also educate others about proper tree maintenance practices!! More resources available via Tree services San Jose
When I initially commented I clicked the “Notify me when new comments are added” checkbox and now each time a
comment is added I get several e-mails with the same comment.
Is there any way you can remove me from that service?
Thanks!
I’ve been researching Wesley Chapel auto transport companies and found some great deals online! Wesley Chapel car shipping
I blog quite often and I seriously appreciate your information. This article has really peaked my interest.
I am going to book mark your blog and keep checking for new details about once per
week. I opted in for your RSS feed as well.
Wonderful material, Appreciate it!
My web site – Lottery (https://www.buzzgate.net/read-blog/5601_unlocking-insights-donghaeng-lottery-powerball-analysis-and-the-bepick-community.html)
My new ###window well covers### are not only functional but also add charm to my backyard; thanks, # long island egress #!
НЕ.KURILI – Папина Дочка скачать бесплатно и слушать онлайн https://shorturl.fm/5e0nG
บริการของพนักงานที่ OMG OneMoreGlass เป็นกันเองสุดๆ เลยครับ! ผับสาย1 รับจัดเลี้ยง
สำหรับคนรักการดื่ม ต้องไปลองที่ OMG ONE MORE GLASS SAI1 สักครั้งนะคะ ร้านฟังเพลงสาย1
Jackpots remind us that anything is possible; sometimes luck just comes knocking! ee88
Nlo – По Барам скачать песню в mp3 и слушать онлайн https://shorturl.fm/Z2DoB
I have to thank you for the efforts you’ve put in writing this
site. I’m hoping to check out the same high-grade content
by you in the future as well. In truth, your creative writing abilities has motivated me to get my own blog now 😉
Митя Фомин Feat. & Istokiya – Жанна скачать mp3 и слушать онлайн https://shorturl.fm/l7Owg
I could not resist commenting. Exceptionally well written!
Your counsel on out of doors lighting is appropriate! A an expert residential electrician can make all of the distinction!
MARSIAGA – Свет скачать и слушать песню https://shorturl.fm/aaVZT
I’m intrigued by how historical dramas portray real events creatively; what’s one that impressed you recently? ee88
”The.points.emphasized.around.value.creation.strategies.are.truly.enlightening.thank.you.so.much.visiting.#..#.to.access.additional.content! ee88
Bear in mind: time frame apply when submitting claims; act rapidly and contact a competent Motor vehicle accident lawyer today!
Social media platforms have changed how we consume entertainment. What are your thoughts on this trend? Discuss at v9bet .
Thank you a bunch for sharing this with all of us you actually realize what you’re talking about!
Bookmarked. Kindly additionally discuss with my website =).
We can have a link exchange agreement between us
Hello there! This is kind of off topic but I need some advice from an established blog.
Is it tough to set up your own blog? I’m not very techincal but I can figure things out pretty fast.
I’m thinking about creating my own but I’m not sure where to start.
Do you have any points or suggestions? Appreciate it
This was highly informative. Check out nutricionista en Saltillo for more.
TikTok has become a hub for creative expression across multiple genres—who inspires your creativity there?? Connect with fellow creators over here: v9bet
Love the focus on sustainable practices in tree care—definitely checking out what Tree services San Jose offers!
Anyone else looking for ##basement walkouts##? It’s such a great way to improve accessibility! Check out egress covers for some fantastic ideas.
This article really stands out among others I’ve read. For more highly rated content, visit v9bet !
What an insightful discussion emphasizing tangible outcomes stemming from actively pursuing meaningful careers—it speaks volumes; thank you; discover more from # anyKeyWord#! v9bet
The evolution of sports over the years is incredible! Which changes do you think have been the most significant? Find out more at i9bet .
Very rapidly this website will be famous among all blogging and site-building visitors, due to it’s pleasant posts
What’s Going down i’m new to this, I stumbled upon this I have discovered It positively helpful and it has
helped me out loads. I am hoping to give a contribution & assist other users like its helped me.
Great job.
Making connections worldwide through virtual events enhances understanding -have ANY event shaped YOUR worldview recently???? Foster global connections HERE:#anything_keyword# i9bet
Wow, what a fantastic and valuable piece of writing; it’s refreshing to see such quality content online! Check out similar posts at zik88 !
Great job! Find more at casa rural Arzua .
What are some underrated sports that deserve more recognition in mainstream media, according to you? Share your thoughts over on zik88 !
The nightlife in Greensboro is lively and diverse! What’s your go-to spot? Find some recommendations at Greensboro Auto Glass Replacement .
“This article really opened my eyes about efficient junk disposal methods—thanks, # professional garage cleanout near me #!”
I have actually heard great features of Dom Doty and the Doty Team! Their understanding of the McMinnville realty market is impressive. Check out more at McMinnville Realtor .
The intersection between technology & entertainment opens doors previously unimaginable – where do YOU see it heading next?? i9bet
Love seeing discussions aimed empowering individuals tackle challenges proactively ; truly believe investing time learning whom rely upon strengthens communities Tree Services
Truly a valuable article that addresses key issues effectively! Don’t miss out on more at qh88 .
” What astounding motivation lies within this blog publish—it conjures up readers around the globe towards movement rather then worry stylish hesitation surrounding upkeep/protection everyday jobs #.#.#.#.#.#. certified plumber
I appreciate your focus on being authentic; it truly enhances the quality of your writing! Check out more insights at ee88 !
I got this web page from my pal who told me on the topic of this web site and now this time I am visiting this website and reading very informative content at
this place.
If you are tired of overpaying for video game recharges, I quite advocate testing ManaBuy. They offer quite a few innovations which can be either inexpensive and risk-free, making sure you can appreciate your gaming experience with out breaking the bank Best game top-up site, safe & fast
ขอบคุณสำหรับข้อมูลเกี่ยวกับดอกไม้งานศพที่ชัดเจน
โดยส่วนตัวเพิ่งเจอเหตุการณ์สูญเสีย การเลือกช่อดอกไม้เลยเป็นเรื่องที่ต้องใส่ใจ
จะเก็บข้อมูลนี้ไว้ใช้แน่นอน ขอบคุณอีกครั้งครับ/ค่ะ
Review my weeb page จัดดอกไม้งานขาว ดํา
Thank you, Tree services San Jose #, for your prompt service and excellent results on our recent project.
Thanks for sharing these guidelines! I failed to comprehend that DIY electrical work might possibly be so risky. master electrician
Been burned by fake pills before, but deadievolgenetics.com (run by Marijuana Mike) came through.
Hey! Would you mind if I share your blog with my myspace group?
There’s a lot of people that I think would really enjoy your content.
Please let me know. Thanks
Excellent post. I was checking constantly this blog and I am
inspired! Extremely useful information specially the ultimate phase :
) I care for such info much. I was looking for this particular info for a long time.
Thank you and good luck.
Thanks for the informative post. More at nutrióloga Saltillo .
” For reliable help during any sort of demolition project look no further than #myurl#. professional junk hauling near me
.. Reading blogs like yours makes me feel empowered knowing there are ways towards cultivating healthier ecosystems surrounding us—we’re capable of making difference together!!!!! Discover professional contacts through #anything# Tree services San Jose
Well articulated, and I couldn’t agree more with your conclusions here! ee88
Sports and health go hand in hand; staying active is so important! What’s your go-to workout? Let’s discuss at v9bet .
The allure of hitting a jackpot keeps me motivated to keep trying my luck! ee88
Thanks for the detailed post. Find more at casa rural Arzúa .
Every athlete has a unique story to tell. What inspires you about your favorite player? Share your insights at ee88 .
The hosting support mentioned in the article is a game-changer! It can make a big distinction in just how swiftly a home sells. I’m definitely mosting likely to check out this! Realtor McMinnville
Thanks for clarifying how you can troubleshoot average toilet trouble; this will likely save me many of complications—greater suggestions is also chanced on at affordable plumber !
Much love flowing toward those who create spaces allowing individuals express their truths freely without fear judgement or retribution from those outside community!!!! Can’t wait catch up soon amongst pages dedicated exclusively onto v9bet
I think virtual escapes are the future of travel entertainment! What do you think? Join the discussion at i9bet .
Such an insightful article about the significance of engaging in valuable work! More resources available at v9bet .
I’ve enjoyed trying out various recipes from YouTube channels lately- what dish turned out BEST for YOU??? Share culinary successes with us:#anything_keyword# zik88
Auditioning virtually opens doors for aspiring performers -who impressed YOU during recent auditions??? Cheer on talented individuals:#anything_keyword# v9bet
I can’t get enough of well-written, highly-rated articles like this one; explore similar ones at zik88 .
Many individuals do not understand that their insurance coverage might not cover all expenditures; that’s why consulting with a personal injury lawyer near me is necessary!
Your pointers with regards to excursion lights have been hilarious but simple—I’ll without doubt rent anybody subsequent season!!! # # anyKey be aware ## same day electrician
This is a must-read—a truly valuable article that offers great insights into the topic discussed here today! For additional info, check out i9bet !
This in-depth article offers a comprehensive analysis of the topic. I appreciate the thorough research! Check out i9bet for more insights.
Great insights! Discover more at 24/7 plumbers nearby .
Exploring unique settings enhances storytelling richness–where would YOU like future tales set??? qh88
Fantastic post! Discover more at Summers Plumbing Heating & Cooling .
This was highly educational. For more, visit knee pain relief Boise .
This was quite useful. For more, visit car accident doctor .
Who wouldn’t want their lucky day filled with surprises leading up to winning an epic lottery or casino jackpot? ee88
This was a wonderful post. Check out mortgage crm comparison for more.
fantastic put up, very informative. I wonder why the other specialists of this sector do not realize this.
You must continue your writing. I’m sure, you have a huge readers’ base already!
I have actually listened to scary tales about individuals who didn’t hire a motor vehicle accident lawyer near me after an accident and regretted it later on!
The rise of fanfiction communities online is intriguing; have you read or written any stories? Join the conversation at ee88 .
Watching documentaries about various cultures enriches my understanding; which films have opened YOUR eyes lately?? Recommend titles here: v9bet
I found this very interesting. For more, visit casa rural en Arzúa .
Paragraph writing is also a excitement, if you be familiar with after that you can write if not it is difficult to write.
My family was so grateful for the help we received from Miller Trial Law; they really know how to win cases effectively! personal injury lawyer
I’m so glad I chose Sas Prinzivalli CPA P.A for my company’s CFO services—they provide such valuable support! CFO Services
I’m always on the lookout for new documentaries that inspire and educate! Any recommendations? ee88
Authenticity is key, and you’ve captured that perfectly in this piece—thank you so much! Explore additional writings at v9bet !
Great blog here! Also your site loads up fast! What host are you using?
Can I get your affiliate link to your host? I wish my web
site loaded up as quickly as yours lol
Reality TV has taken an unexpected turn during pandemic times- what shows keep YOU entertained through tough times??? Share viewing habits:#anything_keyword# i9bet
We’re a group of volunteers and opening a new scheme in our community.
Your site provided us with valuable info to work on.
You have done a formidable job and our entire community
will be thankful to you.
This was highly educational. For more, visit Play slots online .
The diversity seen across streaming platforms truly reflects changing societal norms—how does representation matter to YOU?? Engage in dialogue here: zik88
Well done on creating such an impressive article! It’s definitely worth reading again; find other articles at zik88 .
This article offered great clarity—thank you, author! Additional resources can be found at v9bet .
This article really highlights the importance of valuable work in today’s economy. Great insights! Check out v9bet for more tips.
Hello there, You have done a fantastic job.
I’ll certainly digg it and personally suggest to my friends.
I’m sure they will be benefited from this web site.
This was quite informative. More at cloud-based commercial loan software .
If anyone deserves recognition for their hard work in personal injury law, it’s definitely the team at Miller Trial Law in Boca Raton! personal injury attorney
This in-depth article offers a comprehensive analysis of the topic. I appreciate the thorough research! Check out i9bet for more insights.
This post perfectly captures what it means to engage in valuable work. Thank you for sharing! Explore more at qh88 .
Thank you for encouraging us to seek out and recognize valuable contributions through our work—this is so important today! Visit i9bet !
Sas Prinzivalli CPA P.A not only offers great CFO services but also provides peace of mind for business owners! CFO Services
Fine material, Thank you!
My blog Online Gambling, https://git.tbaer.de/adalbertolunsf,
Helpful suggestions! For more, visit casa rural Arzúa .
Se vi serĉas malmultekostan kaj fidindan manieron reŝargi viajn ludojn, ne serĉu plu! ManaBuy havas ĉion, kion vi bezonas. #anyKeyword# GENSHIN, HRS, PUBG, MLBB, FreeFire
If you have actually remained in a vehicle accident, it’s essential to speak with a personal injury lawyer near me . They can assist you navigate the legal intricacies and ensure you get the settlement you should have.
https://shorturl.fm/47rLb
Today, while I was at work, my cousin stole my iphone and tested
to see if it can survive a forty foot drop, just so she can be a youtube sensation. My iPad is now broken and she
has 83 views. I know this is entirely off topic but I had to share it
with someone!
What do you think about remakes of classic films—is it a hit or miss most of the time? ee88
Hello, i believe that i saw you visited my web site so i got here to return the want?.I am trying to in finding things to enhance my site!I suppose its good enough to use a few of
your ideas!!
I found your suggestions on choosing an electrician particularly worthwhile! I’ll use them while attempting to find one close to me. electrical contractor
Great tips! For more, visit Slot game reviews .
If anyone deserves recognition for their hard work in personal injury law, it’s definitely the team at Miller Trial Law in Boca Raton! personal injury attorney
I’m so glad I chose Sas Prinzivalli CPA P.A for my company’s CFO services—they provide such valuable support! CFO Services
Rất nhiều ưu đãi hấp dẫn đang chờ đón bạn tại # anykeyword # đấy! https://bandori.party/user/292979/thuthuatcacuocuknet/
Có lẽ mình sẽ thử trải nghiệm tại https://www.divephotoguide.com/user/gamebancauknet/ sau những gì mình đã nghe.
Mọi người có kinh nghiệm gì về https://quicknote.io/206ea9e0-3a0b-11f0-b827-f1d330ee49e9/ không? Chia sẻ cho mình với nhé!
Không thể phủ nhận rằng https://ask.embedded-wizard.de/user/gamebaiuknet đang dần trở thành lựa chọn hàng đầu của nhiều người chơi.
Tôi đã trải nghiệm dịch vụ của https://unityroom.com/users/vio41y0zdmsa2qg6fj9u và cảm thấy rất hài lòng với sự chuyên nghiệp.
Tìm hiểu thêm về các trò chơi tại https://social.vivaldi.net/@gamenohuuknet đi, chắc chắn sẽ không thất vọng đâu!
Appreciate the thorough insights. For more, visit Water treatment expert .
Grateful for the knowledge shared in this well-rated piece; find additional resources at v9bet
Thanks for the great explanation. More info at personal injury lawyer company .
Great insights! Discover more at knee pain relief services .
This was very beneficial. For more, visit local car accident doctor .
each time i used to read smaller content that also clear their motive,
and that is also happening with this post which I am reading at
this place.
constantly i used to read smaller articles that as well clear their motive,
and that is also happening with this article which
I am reading at this place.
Podcasts have become my go-to for entertainment on the go! What are your favorites? ee88
Hãy luôn tỉnh táo và lựa chọn một nhà cái uy tín khi tham gia cá cược như ở top 10 nhà cái uy tín .
Whoa! This blog looks exactly like my old one! It’s on a completely different subject but it
has pretty much the same layout and design. Outstanding choice of colors!
Ai cũng muốn giành chiến thắng, nhưng điều quan trọng hơn cả là phải chọn #nhà_cái_uy_tín#! Ghé ngay # top 10 nhà cái uy tín # để biết thêm chi tiết nào!
Nếu bạn chưa biết nơi nào là nhà cái uy tín thì hãy tìm đến nhà cái tặng tiền !
Appreciate the useful tips. For more, visit casa rural Arzúa .
Dom Doty and the Doty Team have a tested track record in McMinnville real estate. Their devotion establishes them besides others! Find out more at Realtor .
Its like you read my mind! You appear to know
a lot about this, like you wrote the book in it or something.
I think that you could do with some pics to drive
the message home a bit, but instead of that, this is excellent blog.
A fantastic read. I’ll certainly be back.
The team at Miller Trial Law is knowledgeable and effective in handling personal injury claims in Boca Raton! personal injury lawyer
I have complete confidence in my financial decisions thanks to the insightful guidance from Sas Prinzivalli CPA P.A’s CFO service team! CFO Services
A seasoned peronal injury attorney knows exactly how to negotiate effectively with insurer on your behalf– do not go it alone!
Howdy! Someone in my Facebook group shared this site with us so I
came to take a look. I’m definitely loving the information. I’m book-marking and will be tweeting this to my followers!
Terrific blog and great design.
May I just say what a comfort to find someone who actually understands what
they are talking about over the internet. You certainly realize how to bring a problem to light and make
it important. More and more people must read this and understand
this side of your story. I can’t believe you aren’t more popular
given that you most certainly possess the gift.
This was very enlightening. For more, visit Slot game reviews .
Thanks for the clear breakdown. More info at mortgage crm comparison .
I was shocked to discover the modern technology tools that McMinnville real estate agents make use of for detailing properties and reaching possible buyers. It truly boosts the selling experience! Real Estate Agent
Loved your hints on panorama lighting; hiring a a professional electrician will make the whole difference in design and safeguard!! electrician
The results I got from Miller Trial Law exceeded my expectations! They are truly the best personal injury firm around! personal injury attorney
I’ve seen a lot of Teds Woodworking reviews, and honestly, the huge variety
of plans they offer is impressive. Whether you’re a beginner or an experienced
woodworker, there’s something for everyone. The detailed instructions really make building
projects easier. Definitely worth checking out if you’re into woodworking!
I simply couldn’t go away your web site prior to suggesting that I really loved the standard information an individual
supply on your guests? Is gonna be again regularly to inspect
new posts
This was quite enlightening. Check out casa rural en Arzúa for more.
The Mitolyn supplement is designed to boost cellular energy and support healthy mitochondrial function, helping you maintain overall vitality and
stamina. Experience renewed energy and wellness with the Mitolyn supplement.
I have complete confidence in my financial decisions thanks to the insightful guidance from Sas Prinzivalli CPA P.A’s CFO service team! Fractional SFO
Mi uzis ManaBuy por miaj ludoj kaj estis mirigita pri los angeles sekureco kaj rapideco de los angeles servoj. Ĉi tio estas l. a. plej bona loko por reŝarĝi! #anyKeyword# Genshin top up deals
Hi there! I could have sworn I’ve been to this website before but after
checking through some of the post I realized it’s new to me.
Nonetheless, I’m definitely delighted I found it
and I’ll be book-marking and checking back frequently!
If you’re associated with a car mishap, don’t wait to reach out to a Motor vehicle accident lawyer . They can truly make a difference in your case.
I found my experience with Miller Trial Law to be very positive; they were always available for questions and support! personal injury lawyer
If you’re looking to get or sell in McMinnville, Dom Doty is most definitely the realtor to consider. His knowledge can make all the difference! Discover more at McMinnville Realtor .
ini adalah situs bokep
I found this very interesting. For more, visit Slot machine games .
Great details on holding plumbing techniques! I usually put forward checking your pipes as a rule. For more info, go to nearby plumber .
Thanks for some other informative site. The place else may just I am getting that kind of info written in such
an ideal approach? I have a venture that I am simply now operating on, and
I’ve been on the look out for such information.
Right now it looks like Drupal is the top blogging platform available right now.
(from what I’ve read) Is that what you are using on your blog?
Trust is key when it comes to finances, and I trust no one more than Sas Prinzivalli CPA P.A for their expert CFO services! CFO Services
Thanks for the detailed post. Find more at best real estate crm software .
This was beautifully organized. Discover more at 24/7 plumbers Kokomo .
Your dialogue round vigor-effective enhancements used to be very enlightening—can’t wait to achieve out to an educated!!! # # anyKey observe ## professional electrician
Also visit my website click here
Wonderful tips! Discover more at Water treatment expert .
Thanks for the thorough article. Find more at personal injury lawyer services .
Clearly presented. Discover more at knee pain relief services .
I appreciated this post. Check out casa rural Arzúa for more.
SHADBASE
FREE HENTAI
HENTAI Videos
HENTAI Sites
1. Home »
2. Hentai Sites »
3. Shadbase
Naughty Machinima
Hentaigasm
The best porn shadbase xxx solely right here at Ehentai.xxx
Excellent shadbase porn is what our web page affords, make the most of this excellent place utterly free
the place you’ll discover the hottest parodies of cartoons acknowledged
on television, horny images of those characters
that youngsters power us to see and now have been redesigned for
the enjoyment of perverse adults.
The expertise of Miller Trial Law truly sets them apart in Boca Raton. Their approach to personal injury cases is commendable! personal injury attorney
Binary options trading isn’t for the faint of heart, but
for those who are calculated risk-takers, it offers a unique thrill.
David from Philippines told me how their approach differs based on market timings.
In places like Kuala Lumpur, it’s easier to connect with like-minded traders who understand the regional market behavior.
Now, I focus on small, consistent wins instead of
trying to double my money overnight.
Honestly, wherever you are — be it Manila — make sure you understand the risks before jumping
in.
Appreciate the thorough insights. For more, visit Video slots .
Obrigado pelo bom escrito. Na verdade, foi uma conta de diversão.
Aguardo com expectativa muito coisas agradáveis de você!
No entanto, como poderíamos nos comunicar?
I like the idea of smart garage doors! Technology is amazing nowadays. Learn more at Garage Door Service .
I value the focus on regional market expertise that McMinnville realtors supply. It’s vital to have a person that understands the ins and outs of the location when getting or marketing a home. Realtor McMinnville
Really appreciate this honest review—there are so many Prostavive reviews online,
but few actually go into the ingredients and how they support prostate function.
This was super helpful!
Dom Doty has a superb credibility in McMinnville realty. I value how he prioritizes his customers’ demands. For more info, go to McMinnville Realtor .
I appreciate how Miller Trial Law values client relationships and works diligently on every case! personal injury attorney
Hi there all, here every person is sharing these know-how, so it’s fastidious to read this weblog, and I used to pay a visit this webpage all the time.
Asking questions are in fact good thing if you are not understanding something totally,
however this article offers nice understanding yet.
I used to be suggested this blog by way of my cousin.
I’m now not positive whether or not this submit is written through him as nobody else recognise such particular about my
trouble. You’re amazing! Thanks!
Valuable information! Discover more at alojamiento rural Arzúa .
Denver Print Company exceeded my expectations with their yard signs!
I recently ordered yard signs from Denver Print Company and was impressed order yard signs near me
Hi, Neat post. There is a problem together with
your site in internet explorer, could test this? IE still is the marketplace chief and a good section of other people will pass over your
great writing because of this problem.
The legal strategies employed by Miller Trial Law set them apart from other firms in the area—truly exceptional work! personal injury lawyer
This information is worth everyone’s attention. Where can I find out more?
Personal injury law can be complex, but the team at Miller Trial Law simplifies the process for their clients! personal injury attorney
I’m pretty pleased to uncover this website.
I wanted to thank you for ones time for this particularly wonderful read!!
I definitely really liked every part of it and i also have you book
marked to see new things on your web site.
Denver Print Company exceeded my expectations with their yard signs!
I recently ordered yard signs from Denver Print Company and was impressed yard signs for businesses
Thanks for the helpful advice. Discover more at casa rural Arzúa .
The expertise of Miller Trial Law truly sets them apart in Boca Raton. Their approach to personal injury cases is commendable! personal injury lawyer
I am regular reader, how are you everybody? This post posted at this web site is
actually good.
ถ้าใครกำลังมองหาร้านเหล้าที่ดี ขอแนะนำ OMG ONE MORE GLASS SAI1 เลยค่ะ ผับสาย1 รับจัดเลี้ยง
บริการดีเยี่ยมและเครื่องดื่มคุณภาพ ที่ร้าน OMG OneMoreGlass ไม่ทำให้ผิดหวังเลยครับ! ร้านเหล้าฟังเพลงสาย1
ได้ยินว่าที่ OMG OneMoreGlass มีเหล้าหิ้วมาเองด้วย ชอบมาก! ร้านเหล้าสาย1 คนเยอะ
Really no matter if someone doesn’t understand then its up to other viewers that they will assist, so here it happens.
รู้สึกว่าร้าน OMG OneMoreGlass มีเอกลักษณ์เฉพาะตัวจริงๆ นะครับ ร้านเหล้าสาย1 เปิดเพลงมันส์
Everything is very open with a really clear clarification of the issues.
It was truly informative. Your website is very helpful.
Thank you for sharing!
The moving aid offered by some real estate professionals in McMinnville is so underrated! Relocating can be overwhelming, and having support makes all the difference. Real Estate Agent
I used to be recommended this blog via my cousin. I am now not sure whether this post is written by him as nobody else
realize such detailed approximately my trouble. You are amazing!
Thanks!
The sound my garage door makes when opening is driving me crazy! Any services? Garage Door Repair
Denver Print Company exceeded my expectations with their yard signs!
I recently ordered yard signs from Denver Print Company and was impressed Denver Print Company specials
I highly recommend reaching out to Miller Trial Law if you’re dealing with a personal injury case—they’re simply the best! personal injury attorney
I’m amazed, I must say. Rarely do I encounter a blog
that’s equally educative and interesting, and let me tell you,
you have hit the nail on the head. The problem is an issue that not enough people are speaking intelligently about.
I’m very happy that I came across this in my search for something relating to
this.
Hello, I think your blog might be having browser compatibility issues.
When I look at your blog in Firefox, it looks fine but when opening
in Internet Explorer, it has some overlapping. I just wanted to give you a quick heads up!
Other then that, excellent blog!
Also visit my blog :: Judi Online Terbaik
Hey there! Do you know if they make any plugins to protect against hackers?
I’m kinda paranoid about losing everything I’ve worked hard on. Any recommendations?
Your means of telling the whole thing in this paragraph is in fact fastidious, all be capable
of simply know it, Thanks a lot.
I am extremely impressed with your writing skills and also with the layout on your weblog.
Is this a paid theme or did you customize it yourself?
Either way keep up the nice quality writing, it is rare to
see a nice blog like this one today.
Wonderful tips! Find more at casa rural Arzúa .
ใครเคยไป OMG OneMoreGlass แล้วบ้าง? แนะนำเมนูเด็ดๆ ด้วยนะครับ! ร้านชิลสาย1 ดนตรีเพราะ
I’ve seen both wins and losses with binary options, and that
realness is something you don’t get in every type of investment.
Just last week, I was talking to John from
India and we compared our trading strategies.
Trading while being based in Hong Kong presents unique challenges and advantages.
What many people don’t realize is the importance of emotional control in binary options.
For anyone in Philippines thinking about getting into this, my
advice is simple: learn first, invest second.
The Doty Group led by Dom Doty absolutely comprehends the neighborhood market dynamics. I can not advise them sufficient! Discover much more at Realtor .
ราคาที่ OMG OneMoreGlass ถือว่าคุ้มค่ามากเมื่อเทียบกับคุณภาพที่ได้รับ! ร้านเหล้าบางแค
I appreciate how Miller Trial Law understands the nuances of personal injury law. They are the best in Boca Raton! personal injury lawyer
ฉันเพิ่งไปที่ OMG ONE MORE GLASS SAI1 มาหมาดๆ บรรยากาศดีมากเลยค่ะ ร้านเหล้าสาวสวย สาย1
Appreciate the detailed post. Find more at personal injury lawyer .
This was very beneficial. For more, visit car accident doctor .
Denver Print Company exceeded my expectations with their yard signs!
I recently ordered yard signs from Denver Print Company and was impressed Denver yard sign printing
Wonderful tips! Discover more at Price Chiropractic and Rehabilitation .
Do you have any video of that? I’d care to find out some
additional information.
After looking over a handful of the blog articles on your website,
I seriously appreciate your way of writing
a blog. I book-marked it to my bookmark webpage list and will be
checking back soon. Take a look at my web site too and let
me know how you feel.
I’ve heard nothing but positive reviews about Miller Trial Law’s services—definitely on my radar if needed! personal injury lawyer
บริการของพนักงานที่ OMG OneMoreGlass เป็นกันเองสุดๆ เลยครับ! ร้านกินเลี้ยง ฟังเพลง สาย1
Wonderful information on garage door openers! It’s essential to choose the ideal one. For more alternatives, check Garage Door Service .
After trying various remedies, I finally found Breathe Drops, and I’m
genuinely impressed. This blend of mullein, manuka honey, and peppermint
has significantly improved my breathing and reduced congestion. It’s a
natural and effective solution that has become a staple in my wellness routine.
Highly recommend giving it a try!
Awesome article! Discover more at casa rural en Arzúa .
Thank you, I’ve recently been looking for information approximately this subject for ages and
yours is the best I have discovered so far. But, what about the bottom
line? Are you positive about the source?
The expertise of Miller Trial Law truly sets them apart in Boca Raton. Their approach to personal injury cases is commendable! personal injury attorney
Do you mind if I quote a few of your articles as long as I provide
credit and sources back to your site? My blog is in the very
same niche as yours and my visitors would genuinely benefit from a
lot of the information you present here. Please let me know if this ok with you.
Regards!
Denver Print Company exceeded my expectations with their yard signs!
I recently ordered yard signs from Denver Print Company and was impressed Denver Print Company hours
Very good article! We will be linking to this particularly great post on our site.
Keep up the great writing.
OMG ONE MORE GLASS SAI1 เป็นร้านที่มีเครื่องดื่มหลากหลาย ครบครันสุดๆ เลยค่ะ ร้านอาหารรับจัดเลี้ยงสาย1
Just want to say your article is as astounding.
The clearness for your post is just cool and that i can assume you’re knowledgeable on this subject.
Well with your permission let me to grasp your feed to stay updated with impending post.
Thanks 1,000,000 and please carry on the gratifying
work.
หากคุณไม่เคยไปที่ OMG ONE MORE GLASS SAI1 ถือว่าพลาดมากๆ ค่ะ ร้านชิลดนตรีสดสาย1 ที่ฮิต
Legal challenges are stressful, but having a dedicated team like Miller Trial Law makes all the difference—highly recommend them! personal injury lawyer
Thanks for breaking down the process of setting up a new opener– it makes it appear less daunting now than before reading your post! For complete setup guides, take a look at Best Garage Door Company !
magnificent issues altogether, you just won a new reader.
What would you suggest about your submit that you
just made some days ago? Any positive?
I liked this article. For additional info, visit alojamiento rural Arzúa .
Sự hỗ trợ từ đội ngũ chăm sóc khách hàng của https://df999-star.net/ thật sự xuất sắc.
Mọi người nghĩ sao về cách thức thanh toán tại nhà cái df999 ? Rất nhanh chóng và tiện lợi!
Đã thử tính năng live dealer trên https://nhacaidf999.site/ chưa? Thực sự rất chân thực!
Gặp gỡ bạn bè và cùng nhau chơi trên nhà cái df999 là một kỷ niệm đẹp.
Hãy thử sức mình với các trò jackpot tại ##anyKeyword#, biết đâu bạn sẽ là người may mắn tiếp theo! nhà cái df999
Ai thích chơi poker trên nhà cái df999 không? Cảm giác rất tuyệt vời!
Chắc chắn rằng các bạn sẽ không hối hận khi tham gia vào cộng đồng của df999 !
Với nhiều lựa chọn game, chắc chắn mọi người sẽ tìm thấy thứ mình thích tại nhà cái df999 .
Có những bí quyết nào để thắng lớn trên df999 không nhỉ?
Tôi thấy các trò chơi trên https://df999play.online/ rất đa dạng, ai có thể gợi ý trò nào hay không?
Tại sao không thử vận may của bạn với df999 ? Thật sự đáng để thử!
Có ai đã thắng jackpot trên df999 chưa? Kể cho tôi nghe với!
Tôi rất thích giao diện của https://df999-king.com/ , dễ dàng sử dụng và thân thiện với người dùng.
Tôi mới tham gia vào df999 và đã nhận được nhiều khuyến mãi hấp dẫn.
Tại sao không thử vận may của bạn với https://df999-elite.online/ ? Thật sự đáng để thử!
Today, I went to the beach front with my kids. I found a sea
shell and gave it to my 4 year old daughter and said “You can hear the ocean if you put this to your ear.” She
put the shell to her ear and screamed. There was a hermit crab inside and it pinched her
ear. She never wants to go back! LoL I know this is completely off topic but I had to tell someone!
อยากให้ทุกคนสัมผัสประสบการณ์ดีๆ ที่ OMG ONE MORE GLASS SAI1 กันนะคะ ร้านเหล้าสาย1
พาแฟนไปเดทที่ OMG OneMoreGlass บรรยากาศโรแมนติกมากๆ ครับ! ผับจัดวันเกิด สาย1
Denver Print Company exceeded my expectations with their yard signs!
I recently ordered yard signs from Denver Print Company and was impressed where to buy yard signs
Denver Print Company exceeded my expectations with their yard signs!
I recently ordered yard signs from Denver Print Company and was impressed Denver print shop
This was quite enlightening. Check out Auto Glass Replacement for more.
This was highly useful. For more, visit Greensboro Auto Glass Replacement .
Thank you for talking about the aesthetic impact of picking the right hardware for my garage door– it makes all the distinction! More style concepts available at Best Garage Door Company .
This was very beneficial. For more, visit abogados laboralistas en Sevilla .
I have to thank you for the efforts you’ve put in penning this blog.
I really hope to check out the same high-grade blog posts
by you in the future as well. In truth, your creative writing
abilities has encouraged me to get my own, personal site now ;
)
Thanks for the thorough analysis. Find more at https://atavi.com/share/xa89soz1c0wxa .
I found this very interesting. For more, visit http://www.video-bookmark.com/user/lefwenhwip .
I am in fact thankful to the holder of this website
who has shared this enormous paragraph at at this time.
Thanks for the great information. More at https://wakelet.com/wake/t33-XDVKak7dmDKl7W_EG .
Appreciate the detailed insights. For more, visit https://jsbin.com/lukasiracu .
This was a great article. Check out https://83hi6.mssg.me/ for more.
Planning a festival in Tacoma? Don’t forget to rent porta potties from best porta potty rentals in Tacoma for convenience and cleanliness.
Denver Print Company exceeded my expectations with their yard signs!
I recently ordered yard signs from Denver Print Company and was impressed local sign shops
Appreciate the comprehensive insights. For more, visit https://zenwriting.net/thothewskl/keeping-your-commode-dish-storage-tank .
This was beautifully organized. Discover more at https://www.plurk.com/p/3haxriyqg1 .
This was a great help. Check out https://go.bubbl.us/eb678d/b578?/Bookmarks for more.
Appreciate the detailed information. For more, visit https://zenwriting.net/margaryodx/comprehending-and-managing-water-stress-and-warmth-circulation .
Very nice article, totally what I needed.
Hey just wanted to give you a quick heads up. The text in your article seem to be running off the screen in Chrome.
I’m not sure if this is a format issue or something to do with web browser compatibility but I figured I’d post to let you know.
The style and design look great though! Hope you get the issue solved
soon. Kudos
Thanks for the clear breakdown. Find more at https://landenhvlv491.cavandoragh.org/exactly-how-to-stop-pipes-concerns-in-your-rental-home .
Thanks for the helpful article. More like this at https://holdenoudu368.lucialpiazzale.com/recognizing-pipes-pipeline-options .
This was quite useful. For more, visit https://jsbin.com/yegemusoce .
Hello outstanding blog! Does running a blog similar to this
require a massive amount work? I’ve absolutely no understanding of programming however I was hoping to start my
own blog in the near future. Anyhow, if you have any ideas or techniques for new blog owners please share.
I know this is off subject nevertheless I simply had to ask.
Thanks a lot!
Appreciate the useful tips. For more, visit https://hotgirlsforum.com/member.php?action=profile&uid=72631 .
Great tips! For more, visit https://adminclub.org/member.php?action=profile&uid=393910 .
Denver Print Company exceeded my expectations with their yard signs!
I recently ordered yard signs from Denver Print Company and was impressed yard sign printing specials
Thanks for the helpful article. More like this at https://ekra123.com/tripoli-libya/en/user/profile/58035 .
Impressed by how professional # # # was during setup! local portable toilet rental company Tacoma
Clearly presented. Discover more at https://forum.kainkalabs.com/member.php?action=profile&uid=28894 .
Great job! Discover more at https://www.livekavkaz.ru/user/personskzm .
Valuable information! Discover more at https://diego-maradona.pl/user/lydeengkos .
Thanks for the useful suggestions. Discover more at https://www.reliquia.net/user-133592.html .
Wonderful tips! Find more at https://www.articledude.com/classifieds/user/profile/67166 .
Nicely detailed. Discover more at https://www.livekavkaz.ru/user/typhandljh .
I’ve read a lot of Vital Translate Buds reviews, and this video really helped me understand
how well they work for real-time translation. It’s amazing how technology like this can break down language barriers so easily!
I appreciated this article. For more, visit https://muhammad-ali.com.az/user/sionnalvlt .
Thanks for the detailed post. Find more at http://megashipping.ru/user/merrinkphv .
I’ve read several The Memory Wave reviews, and this video really helped
me understand how it supports brain health. I’m excited to try
it and see if it helps with focus and memory like they say!
Hello there, You have done an excellent job. I’ll definitely digg it and personally suggest to my friends.
I’m confident they will be benefited from this web site.
Denver Print Company exceeded my expectations with their yard signs!
I recently ordered yard signs from Denver Print Company and was impressed yard sign printing discounts
Thanks for the helpful article. More like this at https://send.now/knzf1bjm7b9d .
This was beautifully organized. Discover more at https://www.mediafire.com/file/q5nx9k1rp5ur8um/pdf-66249-79627.pdf/file .
This was a fantastic read. Check out Greensboro Auto Glass Replacement for more.
Thanks for the helpful advice. Discover more at https://files.fm/u/uuzevkzuq9#design .
I appreciated this post. Check out https://www.4shared.com/s/fc0_7AFSuku for more.
Thanks for the informative content. More at instant payday loans new orleans .
Very helpful read. For similar content, visit https://go.bubbl.us/eb683a/a8d2?/Bookmarks .
This was quite informative. More at https://atavi.com/share/xa8ktaz1bywsh .
. Just wanted everyone here who’s planning an event near Tacoma that you can trust your sanitation needs with ###ANYKEYWORD####! local porta potty rental services Tacoma
This was highly educational. For more, visit https://www.scribd.com/document/869297785/The-Function-of-Plumbing-and-Heating-in-Green-Building-148181 .
This was very well put together. Discover more at https://send.now/1nlve0yuagz6 .
Nicely done! Discover more at https://wakelet.com/wake/TCV2a2Nh2JxOdvVnH1oxq .
Thanks for the informative content. More at https://go.bubbl.us/eb6836/45b8?/Bookmarks .
Appreciate the detailed information. For more, visit abogado laboralista en Sevilla .
Thanks for the insightful write-up. More like this at https://www.plurk.com/p/3haylbrtm4 .
First off I would like to say fantastic blog! I had a quick question in which I’d like to ask if you
do not mind. I was interested to know how you center
yourself and clear your thoughts prior to writing. I’ve had a difficult
time clearing my thoughts in getting my thoughts out there.
I do take pleasure in writing but it just seems like the first 10 to 15
minutes are generally lost just trying to figure out how
to begin. Any recommendations or hints? Many thanks!
Appreciate the thorough insights. For more, visit https://atavi.com/share/xa8kx7z1uoxym .
Clearly presented. Discover more at car hire .
Kerner Law Group, P.C. has the best Yonkers car accident attorneys who truly care about your case!
I was so impressed by the professionalism of the Yonkers car accident lawyer at Kerner Law Group, P.C Yonkers accident claim attorney
I had a fantastic experience with Kerner Law Group, P.C. as my Bronx car accident attorney!
Kerner Law Group, P.C. truly stands out as the best Bronx car accident lawyer I’ve ever worked with Bronx auto injury attorney
Hurrah! Finally I got a webpage from where
I can truly get useful facts concerning my study and
knowledge.
What’s up everyone, it’s my first pay a quick visit at
this web page, and piece of writing is actually fruitful for me, keep up posting these types
of content.
This is very insightful. Check out https://hotgirlsforum.com/member.php?action=profile&uid=72645 for more.
This was quite helpful. For more, visit http://www.underworldralinwood.ca/forums/member.php?action=profile&uid=458891 .
This was a fantastic read. Check out https://mianswer.com//user/calvincryo for more.
I found this very interesting. Check out http://maddog-server.org/forum/member.php?action=profile&uid=274982 for more.
“The luxury restroom trailers from anyKeyWord] are perfect for upscale events!” Tacoma porta potty rental services
https://shorturl.fm/Xect5
Hi there to every one, since I am truly keen of reading this website’s post to be updated daily.
It includes fastidious information.
This was a wonderful post. Check out http://www.staniforthfamily.com/forum/member.php?action=profile&uid=359446 for more.
This was quite helpful. For more, visit http://forum.albaelektronik.com/member.php?action=profile&uid=323488 .
This was highly informative. Check out abogado laboralista en Sevilla for more.
https://shorturl.fm/Xect5
Thanks for the valuable insights. More at play slot machine games online .
ร้าน OMG OneMoreGlass สาย 1 นี่บรรยากาศดีจริงๆ เหมาะสำหรับนั่งชิลล์มากเลย! ร้านเหล้าสาย1 คนเยอะ
I am not positive where you’re getting your info, but
great topic. I must spend some time finding out more or understanding more.
Thank you for wonderful information I used to be on the lookout for this info for my mission.
This was very enlightening. More at https://www.scribd.com/document/869357642/The-Very-Best-Pipes-Devices-for-Do-It-Yourself-Enthusiasts-172866 .
I found this very interesting. For more, visit https://www.4shared.com/s/fXvPrCXb1fa .
I found this very interesting. Check out https://www.mediafire.com/file/pjaxqjr3zflfu7p/pdf-72145-43627.pdf/file for more.
Awesome article! Discover more at https://www.mediafire.com/file/qg95zt5p1k5r9b7/pdf-50207-21695.pdf/file .
Well explained. Discover more at https://send.now/tpfah3fpa0q5 .
Valuable information! Find more at https://www.4shared.com/s/fNbkkZ5_6fa .
It is actually a nice and useful piece of information. I’m happy that you just shared
this useful information with us. Please keep us informed like
this. Thanks for sharing.
Thanks for finally talking about > SMI diamond grinding
wheels < Loved it!
ฉันรักค็อกเทลที่ OMG ONE MORE GLASS SAI1 มาก อร่อยและสดชื่นสุดๆ ผับสาย1 รับจัดเลี้ยง
When I initially commented I clicked the “Notify me when new comments are added” checkbox and now each time a
comment is added I get four e-mails with the
same comment. Is there any way you can remove me from
that service? Thanks a lot!
Very shortly this website will be famous among all
blogging and site-building viewers, due to it’s fastidious articles
Thanks for your personal marvelous posting! I quite enjoyed reading it, you’re
a great author. I will be sure to bookmark your blog and will eventually come back
at some point. I want to encourage that you continue your great job, have a nice morning!
The summary of what kind of lawyer handles these cases was concise and informative—thanks for sharing! affordable lawyers for car accidents
Magnificent beat ! I would like to apprentice while you amend your website,
how could i subscribe for a blog site? The account helped me a acceptable deal.
I had been a little bit acquainted of this your broadcast provided bright clear concept
Thanks for the good writeup. It in truth was a entertainment account it.
Look complex to far delivered agreeable from
you! However, how can we be in contact?
I’m really enjoying the design and layout of your site.
It’s a very easy on the eyes which makes it much more pleasant for me to come
here and visit more often. Did you hire out a designer to
create your theme? Excellent work!
Thanks for the useful post. More like this at abogados laboralistas Sevilla .
This was highly helpful. For more, visit slot games with high payout .
This information is worth everyone’s attention. When can I
find out more?
Normally I don’t learn post on blogs, but I would like to say that this
write-up very pressured me to check out and
do it! Your writing style has been surprised me. Thank you, very great
post.
This was highly useful. For more, visit Phone number lookup .
But don’t get disheartened just yet, because all of this can be fixed with one quick coat of primer.
บริการของพนักงานที่ OMG OneMoreGlass เป็นกันเองสุดๆ เลยครับ! ร้านเหล้าจัดวันเกิด สาย1
Fantastic experience overall withProgressiveHeating&Air—toasty warm home once again thanks to them! Heater repair in San Diego
Link exchange is nothing else but it is only
placing the other person’s weblog link on your page at suitable place and other person will also do similar in support
of you.
OMG ONE MORE GLASS SAI1 เป็นร้านที่มีเครื่องดื่มหลากหลาย ครบครันสุดๆ เลยค่ะ แนะนำร้านอาหารสาย1 มีเพลงฟัง
Training can be tough, but I’ve heard that the trainers at private dog aggression training Gilbert AZ are super supportive and knowledgeable!
You really make it seem so easy with your presentation but I find this topic to be really
something which I think I would never understand. It seems too
complex and very broad for me. I am looking forward for your next post,
I will try to get the hang of it!
My web site :: online games casino free 100
This was a fantastic read. Check out arnhem boekhouding for more.
I was also thrilled that, as someone who is often working from home,
I was able to do that comfortably throughout.
This might take several washes, but it removes the possibility of leftover residue reacting with the paint and causing cracking or flaking.
I do consider all of the concepts you’ve offered on your post.
They are very convincing and will certainly work. Nonetheless, the posts are too short for starters.
May just you please extend them a bit from next time?
Thanks for the post.
Hello! I simply would like to give you a big thumbs up for the great info you’ve got here on this post.
I will be returning to your web site for more soon.
Is your heating system making strange noises? Contacting Progressive Heating & Air was the best decision! Heater repair in San Diego
Very informative article. For similar content, visit payday loans new orleans .
Playing sports has taught me about discipline and hard work! What lessons have you learned through athletic experiences? Share them at b52club !
This was highly informative. Check out popular slots to play for more.
Thăm dò ý kiến: bạn thích đội nào nhất trong các trận đấu đá gà ở thomo? https://congaden.wiki/
Thanks for the thorough analysis. More info at Free reverse phone lookup .
If you want to get a great deal from this piece of writing then you have to apply such techniques to your won web site.
Great insights! Find more at car hire toronto .
id=”firstHeading” class=”firstHeading mw-first-heading”>Search results
Help
English
Tools
Tools
move to sidebar hide
Actions
General
https://shorturl.fm/hQjgP
This design is spectacular! You obviously know how to keep a reader amused.
Between your wit and your videos, I was almost moved to start my own blog (well, almost…HaHa!) Great job.
I really loved what you had to say, and more than that,
how you presented it. Too cool!
Wow, amazing blog layout! How long have you been blogging for?
you make blogging look easy. The overall look of your web site is wonderful,
let alone the content!
After removing wallpaper, and before painting the walls, make
sure you get rid of all residual wallpaper paste with clean water.
My heating problems were resolved quickly thanks toProgressiveHeating&Air—highly recommend their services! Heater repair in San Diego
I love your blog.. very nice colors & theme. Did you make this website yourself or did you hire
someone to do it for you? Plz answer back as I’m looking to design my
own blog and would like to know where u got this from.
kudos
https://shorturl.fm/YZRz9
Hello my friend! I wish to say that this post is amazing, great written and
include almost all important infos. I’d like to see more posts like this .
The section on DIY repairs was super helpful! I might try some of these tips before calling in garage door service .
That is really attention-grabbing, You are
an excessively professional blogger. I have joined your rss
feed and sit up for searching for extra of your excellent post.
Also, I’ve shared your website in my social networks
Saved as a favorite, I love your blog!
Excellent post however , I was wondering if you could write a litte more on this topic?
I’d be very thankful if you could elaborate a little bit more.
Kudos!
Sciatic pain has been a constant struggle for me, so this review on Arialief really stood out.
I like that it focuses on long-term nerve health, not just temporary
relief. Would love to hear from others who’ve tried it
Hello, i read your blog occasionally and i own a similar one and
i was just curious if you get a lot of spam responses? If so how do you protect against it, any
plugin or anything you can suggest? I get so much lately it’s driving
me crazy so any support is very much appreciated.
This was highly useful. For more, visit slots in online casinos .
Thanks for the thorough analysis. More info at Phone number lookup .
I always spent my half an hour to read this weblog’s content daily along with a cup of coffee.
Fantastic goods from you, man. I have understand your stuff previous to and you’re just too magnificent.
I actually like what you’ve acquired here, certainly like what you are stating and the way in which
you say it. You make it entertaining and you still take care of to keep it sensible.
I can’t wait to read far more from you. This is really a wonderful
site.
Thanks for the valuable insights. More at nhà cái df999 .
Clearly presented. Discover more at nhà cái df999 .
Great job! Find more at nhà cái df999 .
This was very enlightening. For more, visit nhà cái df999 .
Clearly presented. Discover more at nhà cái df999 .
Love this blog post! It’s great to see such valuable information about garage doors in one place. Visiting garage door service soon!
Just started treatment with my new north gate chiropractor , and already feeling less tension ! Can’t wait for more improvements ! # # any keyword # # Car accident chiropractor
I completely agree that regular maintenance can save you money in the long run. Puyallup residents should definitely explore options at HVAC Puyallup for affordable services.
If you’re looking for knowledgeable roofers, definitely consider the options available in Puyallup! Puyallup roofing company
Kerner Law Group, P.C. has the best Yonkers car accident attorneys who truly care about your case!
I was so impressed by the professionalism of the Yonkers car accident lawyer at Kerner Law Group, P.C Free consultation car accident lawyer Yonkers
I had a fantastic experience with Kerner Law Group, P.C. as my Bronx car accident attorney!
Kerner Law Group, P.C. truly stands out as the best Bronx car accident lawyer I’ve ever worked with Uber accident lawyer Bronx
This is really interesting, You’re a very skilled blogger.
I’ve joined your rss feed and look forward to seeking more of your magnificent post.
Also, I’ve shared your site in my social networks!
Your insights about safety features in garage doors are invaluable. I’ll make sure to get in touch with garage door service for my repairs!
Woah! I’m really digging the template/theme of this
site. It’s simple, yet effective. A lot of times it’s difficult
to get that “perfect balance” between superb usability and visual
appearance. I must say you have done a amazing job with this.
Additionally, the blog loads extremely quick for me on Firefox.
Exceptional Blog!
If you want your property to stand out, hire Golden State Visions for the best photography around! real estate photographer
Thanks for the practical tips. More at Reverse phone lookup .
Love hearing success stories about chiropractic treatment in our community—Northgate has some great options available! Car accident chiropractor
I’m impressed by the before and after photos of window cleaning! It’s so satisfying to see the difference. window cleaning services
Has anyone else in Puyallup noticed how much dust settles after a while? I just learned that dirty ducts could be the culprit! I’m going to schedule a cleaning soon Puyallup AC installation
Wonderful beat ! I would like to apprentice whilst you amend your website, how can i subscribe for a weblog website?
The account helped me a appropriate deal. I were tiny bit familiar of
this your broadcast provided brilliant clear concept
It’s important to choose a local Puyallup roofing company for the best results. Support local businesses! New roof Puyallup
เมนูค็อกเทลที่ OMG OneMoreGlass นี่อร่อยจริงๆ ครับ ต้องลอง! ร้านอาหารบางแคพร้อมบริการดี
Appreciate the comprehensive advice. For more, visit pizza bestellen in utrecht .
Investing into professional photographs yields dividends down line when partnering up with talented teams like golden state visions- visit: real estate photographer
Your post is a treasure trove of information about maintaining garage doors properly! Time to check out garage door repair near me !
This was quite informative. For more, visit instant payday loans new orleans .
If you haven’t tried# # anyKeword ##, do yourself a favor and book them today! window cleaning
I’m no longer sure where you’re getting your information, but great topic.
I needs to spend a while learning much more or understanding more.
Thanks for great info I was on the lookout for this information for
my mission.
I have to thank you for the efforts you have put in writing this blog.
I am hoping to view the same high-grade content by you in the future as well.
In truth, your creative writing abilities has inspired me
to get my very own site now 😉
Valuable information! Find more at Reverse phone lookup .
I never realized how important duct cleaning was until I noticed the dust accumulating around my home. After doing some research, I found that regular maintenance can really improve air quality Puyallup HVAC
Just made an appointment with my new north gate chiropractor after reading this post; feeling hopeful already ! # # any keyword # # Northgate Chiropractor
I enjoyed this read. For more, visit car hire .
Hi, I check your blog like every week. Your story-telling style is
witty, keep it up!
If you’re looking for knowledgeable roofers, definitely consider the options available in Puyallup! Puyallup New Roof
I’ve heard about the ice water hack before and it’s interesting how something so simple might actually help with boosting metabolism.
Definitely makes me want to try adding more cold drinks to my
routine and see if it helps with weight loss over time!
Appreciate the detailed information. For more, visit tandarts alphen a/d rijn .
Just had such a positive experience with window cleaning services ! Highly recommend them.
Fajnie, że ktoś porusza temat biur rachunkowych w Bydgoszczy. Dobrze, że są takie źródła dla lokalnych firm.
Biuro rachunkowe
Thanks for the detailed post. Find more at boekhouder in arnhem .
I never realized how crucial regular inspections are for garage doors. Thanks for the reminder! I’ll be visiting garage door service soon.
This was highly educational. More at goede pizzeria utrecht .
I was skeptical about heat pumps, but the Puyallup Heat Pump has changed my mind completely. It keeps my home warm without breaking the bank! Puyallup HVAC
This was beautifully organized. Discover more at car accident lawyer Jupiter FL .
Nicely done! Discover more at https://maps.app.goo.gl/PghGQZSnw7HwWVVX9 .
This was very enlightening. More at water line repair near me .
Appreciate the insightful article. Find more at Suburban Plumbing Sewer Line and Drain Cleaning Experts .
Curious if there are any specialized treatments offered by chiropractors specifically in the Northgate area? Northgate Chiropractor
Nicely detailed. Discover more at https://maps.app.goo.gl/hPeDYmgqEDPGNVWR9 .
Just had a roof inspection done by a Puyallup roofing company. They were very thorough! New roof Puyallup
I am really thankful to the holder of this web page who has shared this enormous piece
of writing at at this time.
My neighbor recommended window cleaning , and I’m so glad I listened!
Really when someone doesn’t understand afterward its up
to other viewers that they will assist, so here it occurs.
I can feel the energy of the Golden State through your photography—so vibrant and alive! real estate photographer
Impressed by the expertise displayed in your post about Seattle personal injury lawyers. Connecting with professionals who understand the intricacies of personal injury cases is so crucial for anyone seeking legal support like car accident lawyer !
Prowadzę działalność w Bydgoszczy i wiem, jak ważna jest dobra księgowość – to naprawdę ułatwia życie przedsiębiorcom.
Biuro rachunkowe
Your blog has motivated me to prioritize my spinal health with a trip to the Northgate Chiropractor! Car accident chiropractor
Choosing the right time for a furnace replacement can save you a lot of money on energy bills. I’ve noticed that many people wait too long, leading to higher costs in the long run HVAC Puyallup
“Excited to implement what I learned about seasonal window care from # anykeyword#!” window cleaning
Great post. I used to be checking continuously this weblog and I’m inspired!
Very useful information specifically the remaining phase 🙂 I handle such info
a lot. I used to be seeking this certain information for
a very lengthy time. Thank you and best of luck.
Just moved to Puyallup and need to find a trustworthy roofing contractor—any suggestions? Puyallup New Roof
Aw, this was an exceptionally nice post. Taking
the time and actual effort to create a top notch article… but what
can I say… I hesitate a lot and don’t manage to get nearly anything done.
Every listing deserves such beautiful representation; keep pushing those creative boundaries, Golden State Visions! real estate photographer
Your blog post on the importance of consulting San Diego car accident lawyers is truly informative! It’s crucial for anyone involved in such incidents to seek professional advice like the services offered on accident law firm .
I’m truly enjoying the design and layout of your site.
It’s a very easy on the eyes which makes it much more pleasant for
me to come here and visit more often. Did you hire out a designer
to create your theme? Outstanding work!
This was quite useful. For more, visit pizzeria utrecht .
Appreciate the comprehensive advice. For more, visit progressive jackpots in casinos .
Thanks for the helpful article. More like this at abogados Coruña .
Appreciate this post. Will try it out.
Good day! I just wish to give you a big thumbs up for your excellent info you’ve got here on this post.
I am coming back to your blog for more soon.
Impressed with the in-depth information shared; it’s essential to have reliable resources like these when seeking help from motorcycle accident lawyer . Kudos to the team for shedding light on crucial aspects of personal injury cases!
When it comes to seeking legal advice after an injury, having a reliable team of Sacramento personal injury lawyers like yours can make all the difference. Your expertise and dedication shine through in every case you handle. personal injury attorney
Love how detailed your article is about recognizing signs of a mold problem—if you’re unsure how to proceed, reach out to experts at Mold Remediation
I’m really impressed by how many realtors are adopting aerial photography—it’s clearly become an industry norm now! expert real estate photographers nearby
Point certainly used!.
Impressed by the depth of insight these Portland personal injury lawyers provide! Looking forward to sharing motorcycle accident attorney with friends seeking expert legal advice in Oregon.
Impressed by the level of expertise these fresno personal injury lawyers bring to the table! If you’re seeking top-notch legal representation for your case, truck accident attorney could be just what you need.
Cleanliness affects everything from aesthetics to productivity—this was well articulated!!!### #AnyKeywords### window cleaning
Can anyone recommend a good Northgate Chiropractor? I want to improve my posture! Northgate Injury Chiropractor
Bardzo pomocny przewodnik dla przedsiębiorców z Bydgoszczy. Dzięki takim materiałom łatwiej podjąć decyzję o wyborze biura.
Biuro rachunkowe
I will immediately clutch your rss feed as I can’t in finding your
email subscription link or newsletter service. Do you have any?
Kindly let me recognise so that I may subscribe.
Thanks.
Because the admin of this web page is working, no question very soon it will be well-known, due
to its quality contents.
Here is my homepage … Buy lab tests
I’m interested in learning more about creating functional outdoor spaces—what are your best ideas? professional interior designer Florida
Excellent post! I didn’t realize how much the local climate affects HVAC choices in Puyallup. For more detailed guidance, visit HVAC Puyallup .
Hopeful sharing these thoughts will encourage everyone embrace beauty found everyday lives recognizing gifts hidden plain sight discovering treasures worth celebrating honoring nurturing preserving legacy left behind gracefully respectfully forever real estate photographer
I love that many Puyallup roofing companies offer warranties on their work! It gives peace of mind. New roof Puyallup
This was very beneficial. For more, visit tandarts in alphen a/d rijn .
I love seeing how technology has improved orthodontic treatments over the years. Fascinating stuff! retainers after braces
Pretty part of content. I simply stumbled upon your site and in accession capital
to claim that I acquire in fact enjoyed account your weblog posts.
Any way I will be subscribing in your feeds and even I success you access constantly quickly.
. Designing around natural light amplifies positive energy; how has sunlight influenced layouts or color choices you’ve made?, share lighting influence stories over on ### anykeyword### ! affordable Florida interior design
I know this web page offers quality dependent articles and extra
stuff, is there any other web site which gives these kinds of information in quality?
Hurrah, that’s what I was seeking for, what a stuff!
existing here at this weblog, thanks admin of this website.
Here is my homepage: Functional medicine panels
Fantastic post! Discover more at abogados en A Coruña .
Professional photos are an investment that pays dividends when selling homes! professional video production for real estate
Wow, fantastic blog layout! How long have you been blogging for?
you made blogging look easy. The overall look of your site is great, as well as the content!
Saved as a favorite, I really like your site!
I’ve been looking for a reliable window cleaner in Lakeland. Glad I found window cleaning services !
I enjoyed this article. Check out online progressive jackpots for more.
It’s nice knowing there are dedicated chiropractors right here in our community – I’ll definitely be checking out some local options !! ##### any keywords ##### Chiropractor Northgate
The variety of art styles showcased at Golden State Visions is impressive—you never know what you’ll find next! More info available at real estate photography !
Thanks for the great tips. Discover more at payday loans new orleans la .
Impressed by the valuable insights shared here about personal injury cases. I’ll definitely refer friends to your page when they need advice on accident attorney !
Has anyone else in Puyallup noticed how much dust settles after a while? I just learned that dirty ducts could be the culprit! I’m going to schedule a cleaning soon Puyallup AC installation
I am regular visitor, how are you everybody?
This piece of writing posted at this web page is actually
fastidious.
Z własnego doświadczenia wiem, że porządne biuro rachunkowe robi różnicę – temat opisany w artykule jest bardzo trafiony.
Biuro rachunkowe
Anyone know about seasonal promotions from local Puyallup roofing companies? I’d love to save some money! Roofer
Valuable information! Discover more at cheap car rental toronto .
Just viewed some breathtaking drone footage—it’s incredible how much beauty and detail can be captured from above! 3D video walkthrough production for real estate
Unmatched quality service every single time—thank you so much, window cleaning services
I think there’s something magical about revealing the original wood beneath layers of old finish during restorations! office flooring restoration service
I’ve noticed that listings with 3D tours get way more inquiries! Thanks for paving the way, real estate photography .
Anyone else curious about how often they should see their chiropractor ? Would love input from others who’ve visited north gate professionals !! # any keyword # Northgate Injury Chiropractor
It’s a shame you don’t have a donate button! I’d certainly donate to
this outstanding blog! I suppose for now i’ll settle for book-marking and adding your RSS
feed to my Google account. I look forward to fresh updates and will share
this website with my Facebook group. Chat
soon!
Appreciate the detailed information. For more, visit https://maps.app.goo.gl/eRMgQ3ViLKna7G7A8 .
Thanks for the clear advice. More at Suburban Plumbing Sewer Line and Drain Cleaning Experts .
Appreciate the detailed information. For more, visit Redefined Restoration – Chicago Water Damage Services .
I recently attended a workshop on home heating solutions, and the Puyallup Heat Pump was highly recommended by the experts. It sounds like a great investment for comfort and efficiency! HVAC Puyallup
What’s the best way to prepare your roof for winter in the Puyallup area? Any tips? Roofer
I found this very helpful. For additional info, visit free spins no deposit .
This post is perfect timing; I’ve been meaning to clean my windows for weeks now! window cleaning services
Świetny wpis o księgowości w Bydgoszczy! Dzięki takim materiałom łatwiej podjąć decyzję o wyborze biura.
Biuro rachunkowe
Professional real estate photography is essential for showcasing homes effectively! exceptional aerial photography for properties
My newly installed ####window well covers#### are not only practical but stylish too; thank you ## long island egress ##!
Appreciate this post. Let me try it out.
” I appreciate how beautifully captured moments transform ordinary spacesInto extraordinary experiencesWell done @ ” real estate photography
Hi there i am kavin, its my first time to commenting anywhere, when i
read this article i thought i could also make comment
due to this sensible paragraph.
It’s nice knowing there are dedicated chiropractors right here in our community – I’ll definitely be checking out some local options !! ##### any keywords ##### Chiropractor Northgate
Love that Value Wise Roofers uses high-quality materials for their roofing projects! roof inspection
Really helpful information here; excited to try out the services of Money Wise Roofers when I get my roof done next month! commercial roofing
Feeling inspired after reading success stories featured on Aesthetic Clinic London regarding their surgical facial rejuvenation services!
Kerner Law Group, P.C. has the best Yonkers car accident attorneys who truly care about your case!
I was so impressed by the professionalism of the Yonkers car accident lawyer at Kerner Law Group, P.C Lyft accident attorney Yonkers
I just couldn’t go away your web site prior to suggesting that I really loved the
usual information a person provide in your guests?
Is gonna be again regularly in order to check out new posts
I had a fantastic experience with Kerner Law Group, P.C. as my Bronx car accident attorney!
Kerner Law Group, P.C. truly stands out as the best Bronx car accident lawyer I’ve ever worked with Bronx rear end accident lawyer
Did you know that regular maintenance can extend the life of your furnace? However, when it’s time for a replacement, knowing what model suits your needs is essential. I found helpful guides on this topic at Puyallup HVAC .
It’s amazing how much curb appeal a new roof can add—thanks to my trusted Puyallup roofing company! Puyallup roofing company
I currently had a tire blowout, and I turned into so joyful I knew wherein to move for a fast restore. It’s really good how a small puncture can cause greater concerns if no longer addressed briskly mobile tire repair near me
I’m impressed by how you highlight unique features in every property tour! real estate photographer
What a great guide! Knowing how to choose the right **emergency plumber** or %%keyword%% saves time and stress! Medford plumbing emergencies
Hurrah! In the end I got a blog from where I know how to
in fact get useful data regarding my study and knowledge.
Your blog has been so informative about affordable roofing options—I can’t wait to implement these ideas here in El Monte! metal roofing near me
I love how color can transform a space! What are your favorite color palettes for interior design? modern design services Tampa
It’s amazing that early intervention can prevent bigger issues later on. Great post on orthodontics! invisible braces vs traditional braces
J’espère que cette activité vous plaira et qu’elle plaira à vos enfants.
Appreciate the helpful advice. For more, visit mobile pokies reviews NZ .
I every time emailed this weblog post page to all my friends, as if like to read it next my contacts will too.
Have you considered using mirrors to enhance light and space? They’re such powerful design tools! Discover more tricks at best modern interior designers in Tampa .
I had an amazing experience with a Northgate Chiropractor recently! Highly recommend it! Northgate Injury Chiropractor
Just wrapped up my ##basement egress window installation## and it looks fantastic! Highly recommend checking out egress installers near me if you’re in the area.
The effects of mold on wellness need to now not be taken lightly—VetCor feels like a great preference for remediation! Mold Mitigation
I love how environmentally friendly the Puyallup Heat Pump is! It’s great to find an efficient heating solution that also benefits the planet. Has anyone else noticed this? Puyallup HVAC
If you’re in Puyallup and need roofing services, I highly recommend checking out local options! Roofer
Impressed by the dedication and expertise of these Seattle personal injury lawyers! Anyone looking for top-notch legal representation in that area should definitely check out car accident lawyer .
Miototo menghadirkan pengalaman bermain slot online yang autentik melalui fitur demo slot Pragmatic gratis tanpa perlu mendaftar.
Fitur ini dirancang khusus untuk para pemain yang ingin merasakan sensasi bermain slot seperti di versi asli, namun tanpa risiko kehilangan uang.
Dengan tampilan grafis dan fitur permainan yang identik dengan versi berbayar,
Miototo memungkinkan pemain mengeksplorasi berbagai jenis slot
dari provider Pragmatic Play kapan saja, secara gratis.
Daniella Levi & Associates, P.C. gave me peace of mind with their exceptional Brooklyn car accident attorney services!
I couldn’t be happier with the support from Daniella Levi & Associates, P.C Vehicle injury lawyer Brooklyn
Appreciate the comprehensive advice. For more, visit elektricien in de buurt .
Appreciate the detailed post. Find more at tandarts alphen a/d rijn .
Anyone else think moving could be easier if everyone used companies like Sun City Center apartment movers ?
I appreciate how you break down the legal jargon surrounding injury law in Salt Lake. Very informative! Salt Lake Injury Lawyer
Link exchange is nothing else except it is simply placing the
other person’s website link on your page at suitable place and other person will also do
similar for you.
I’m always worried about plumbing issues, so having access to an plumbing services emergency Medford is crucial for me.
Has anyone had a follow-up treatment at Aesthetic Clinic London ? I’d love to hear about your experiences!
I think there’s something magical about revealing the original wood beneath layers of old finish during restorations! professional office floor restoration
Hey, I think your blog might be having browser compatibility issues.
When I look at your blog in Ie, it looks fine but when opening in Internet Explorer, it has some overlapping.
I just wanted to give you a quick heads up!
Other then that, amazing blog!
Impressive insights on finding reliable San Diego car accident lawyers! Your expertise in this area is truly commendable. Visitors to car accident lawyer will surely benefit from your valuable content.
Hi, everything is going nicely here and ofcourse every one is sharing information, that’s really fine,
keep up writing.
Thanks for the great tips. Discover more at https://df999top.online/ .
Impressed by the expertise of Los Angeles personal injury lawyers! Your dedication to ensuring justice for your clients is truly commendable. Find more insightful information like this at motorcycle accident lawyer .
I found this very helpful. For additional info, visit https://df999play.online/ .
This was a great article. Check out https://df999top.site/ for more.
Appreciate the comprehensive insights. For more, visit df999 .
This was highly helpful. For more, visit https://df999-elite.online/ .
Thinking about adding a basement entrance? It’s a smart investment! I consulted with a pro from egress windows near me .
I enjoyed this post. For additional info, visit payday loans new orleans la .
Your expertise in personal injury law shines through! Clients seeking justice will surely find comfort and guidance on injury attorney ‘s page.
Just finished moving into a new place thanks to excellent service from **Bellevue apartment movers** at ### anyKeyWord### ! Cheap movers Bellevue
Valuable information! Discover more at cheap car hire .
I found the section on medical expenses very enlightening. Salt Lake Injury Law can be overwhelming, but your guidance helps! Salt Lake Injury Lawyer
If you’re struggling with visibility online, contact BlckPanda Creative Dallas—they’ve drastically improved my site’s rank on Google and boosted my sales as a result! Visit them at seo company !
This is a topic that is near to my heart…
Thank you! Exactly where are your contact details though?
Hi there, just became alert to your blog through Google, and found
that it’s truly informative. I am gonna watch out for brussels.
I’ll appreciate if you continue this in future.
Many people will be benefited from your writing.
Cheers!
I’ll right away grasp your rss feed as I can not to find
your e-mail subscription link or e-newsletter service.
Do you’ve any? Kindly allow me understand in order that I could subscribe.
Thanks.
This article gives clear idea designed for the new people of
blogging, that truly how to do blogging and site-building.
How long does it usually take to ship a car across Texas from the heart of Houston? Curious minds want to know! Houston car transport
Amazing tips here! Plumbing can be overwhelming, but knowing about Medford emergency drain cleaning near me eases my worries.
I can’t express how much I appreciate what BlckPanda Creative Dallas has done for me—my Google ranking is soaring, and so are my profits! More info available at seo services .
Great blog! Do you have any suggestions for aspiring writers?
I’m planning to start my own blog soon but I’m a little lost on everything.
Would you propose starting with a free platform like WordPress or
go for a paid option? There are so many options out there that I’m completely overwhelmed ..
Any tips? Kudos!
Just finished my ##custom egress cover## installation, and I’m thrilled with how it looks! If you’re thinking about getting one, visit egress installers for great options.
Thanks for the clear breakdown. More info at año escolar Irlanda .
I appreciated this article. For more, visit contador Saltillo .
Great read! It’s so important for victims to know their rights, especially when it comes to Salt Lake Injury Law! salt lake injury law
I’m really intrigued by the minimally invasive options mentioned on Aesthetic Clinic Marylebone – they sound promising!
Helpful suggestions! For more, visit Redefined Restoration – Chicago Water Damage Services .
Just had an amazing ride through the hills of Jacó! Highly recommend checking out Esterillos horseback riding tours for similar experiences.
I’m so grateful for the impact that BlckPanda Creative Dallas has had on improving my online visibility through enhanced SEO strategies; check out their services here: seo !
Just what I needed! I’ve been curious about ProDentim for a while now—especially since it’s chewable and focuses on overall dental health, not just fresh breath.
Love that it’s made with natural ingredients too.
Has anyone noticed improvements with gum sensitivity or plaque buildup after using it consistently?
Excited to share this informative article with friends who may be interested in starting their own journeys soon!” ### any Keyword ## Invisalign procedures
Very good post. I’m dealing with a few of these issues as well..
I do not even know how I ended up here, but I thought this post
was great. I don’t know who you are but certainly
you are going to a famous blogger if you are not already 😉 Cheers!
I just like the valuable info you supply on your articles.
I will bookmark your weblog and take a look
at once more here regularly. I am somewhat certain I
will be informed many new stuff right here! Good luck for the following!
Could introducing smart appliances streamline daily routines effectively without compromising style integrity?? How intuitive tech integrate seamlessly within renovated settings?? Join discussions delving deeper today!! Tampa Bay interior designer
I adore eclectic decor styles, but how do you avoid making them look chaotic? Any tips? Tampa residential interior designer
Had a flat while running errands in Nashville, and the mobile tire repair team was there within minutes! tire patch
Hi! This is my first visit to your blog! We are a group
of volunteers and starting a new project in a community in the same niche.
Your blog provided us valuable information to work on. You have done
a marvellous job!
This article is a impressive reminder of the magnitude of mildew prevention and remediation. Mold Mitigation Sarasota
I just had to share how BlckPanda Creative Dallas turned my Google ranking around! Business is booming like never before thanks to their expertise. Learn more at seo .
”Absolutely pleased knowing we’ll have pristine perspectives ahead thank you utterly due diligence the following!” Window Cleaning Service
It’s awesome in support of me to have a web site, which is useful
in favor of my knowledge. thanks admin
Thanks for the informative post. More at año escolar en Irlanda .
This is very insightful. Check out contadores en Saltillo for more.
My experience with ####basement entrances#### has dramatically improved after working with ## egress covers ##; they truly know their craft.
Hello there! This is my first visit to your blog! We are a team of volunteers and starting a new initiative in a community in the same niche.
Your blog provided us useful information to
work on. You have done a wonderful job!
While some entrepreneur think twice to buy professional bug control as a result of set you back, the long-term savings make it worthwhile. Preventing invasions before they escalate can save money on emergency eliminations, lost inventory, stopped working examinations, and even claims, https://cuwip.ucsd.edu/members/oxygenattic8/activity/550748/.
Thank you for the informative read on tree services; it’s so helpful for planning my garden this year—visit tree service west palm beach !
Stream live Football events online. Stay updated with upcoming
matches, highlights, and schedules. Join the excitement with E2BET today!
If you want to get much from this paragraph then you have to apply such methods to your won blog.
Good day! Do you know if they make any plugins to assist with Search Engine Optimization? I’m trying to
get my blog to rank for some targeted keywords but I’m not seeing very good gains.
If you know of any please share. Appreciate it!
This information is priceless. How can I find out more?
This was highly useful. For more, visit Bedrock Restoration – Water Fire Mold Damage Service .
Appreciate the thorough insights. For more, visit https://maps.app.goo.gl/wH7jhZvWskaMa4ECA .
Just wanted to share how grateful I am to BlckPanda Creative Dallas! My Google ranking has improved so much that I’ve seen a huge increase in clients. Details at seo agency .
Would highly recommend reaching out directly contacting establishment linked previously towards seeking guidance support assistance wherever needed as they possess vast knowledge expertise depth underst CoolSculpting
I’m really impressed together with your writing skills as neatly as with the format in your
blog. Is this a paid theme or did you modify it yourself?
Anyway keep up the nice quality writing, it is uncommon to look a great weblog like this one
nowadays..
Ready to shape your body the way you’ve always wanted? Discover CoolSculpting near me in Corpus Christi at CoolSculpting Services and achieve your goals.
The before-and-after photos from American Laser Med Spa’s CoolSculpting clients are incredible! CoolSculpting Clinic
Hopefully, more companies will start offering eco-friendly options as demand grows within the industry. flooring contractor near me
Feeling encouraged by all the positive feedback regarding results from patients of Aesthetic Clinic Marylebone # – can’t wait to join them!
That is very attention-grabbing, You’re a very professional blogger.
I have joined your rss feed and look ahead to in the hunt for extra of your great post.
Also, I’ve shared your site in my social networks
Yesterday, I had a flat tire and was struggling to find help. Mobile tire repair saved the day in Nashville! tire patch nashville
This was nicely structured. Discover more at contador en Saltillo .
Just wanted everyone hereto know that if you’re considering hiring someone for your next building venture—you can’t go wrongwith using banning construction inc.for phenomenal results!! # # anykeyword ## Bathroom Remodel
Hello this is kinda of off topic but I was wanting to know if blogs use WYSIWYG editors or if
you have to manually code with HTML. I’m starting a blog soon but have no coding skills so I wanted to get guidance from someone with experience.
Any help would be greatly appreciated!
This is a topic that’s near to my heart… Take care! Exactly where are your contact details though?
I think that everything published made a great deal of sense.
However, what about this? what if you were to create a awesome post title?
I ain’t saying your content isn’t good, but what
if you added something that makes people desire more? I mean SMI
diamond grinding wheels is kinda vanilla. You ought to glance at Yahoo’s front page and note how they create post titles
to grab people to open the links. You might try adding a video or a picture or two to get
people excited about everything’ve got to say. In my opinion, it could bring your website a little bit more interesting.
Wow, what a change since working with BlckPanda Creative Dallas! My site now ranks higher on Google, and I’m getting more customers than ever before! Learn more at seo company .
This guide on lighting techniques for real estate photos is incredibly useful—thank you! real estate photography specialists
Your advice about regular maintenance is spot on! I’m making an appointment with garage door repair today.
Eu não tenho como saber se seria só comigo ou se talvez alguém encontrou algum problema com seu blog. Parece que alguns dos textos em seu conteúdo está aparecendo fora da tela. Pode outra pessoa por favor comentar para eu saber se isso está acontecendo só comigo. Isto poderia ser um problema com meu navegador da internet, eu vi acontecer a mesma coisa com outro blog anteriormente. Desde já agradeço!
Fantastic post! Discover more at almere juwelier .
ขอบคุณสำหรับข้อมูลเกี่ยวกับดอกไม้งานศพที่เข้าใจง่าย
การรู้ว่าดอกไม้แต่ละชนิดมีความหมายอย่างไร ช่วยให้เลือกได้ตรงความรู้สึกมากขึ้น
จะบอกต่อให้เพื่อนๆ ที่ต้องการเลือกดอกไม้ไปงานศพอ่านด้วย
Also visit my web-site :: ดอกไม้สดงานศพ
After trying waxing and shaving, I finally decided to try laser hair removal at CoolSculpting services !
This was highly educational. For more, visit payday loans new orleans .
The environment of relaxation and professionalism made all the difference during my experiences with CoolSculpting at American Laser Med Spa—the best place in town!! CoolSculpting
If you’re thinking about body contouring, definitely consider the services offered by CoolSculpting #!
Hi, i think that i saw you visited my website thus i came to “return the favor”.I am attempting
to find things to improve my website!I suppose its ok to use some of your
ideas!!
I’m not that much of a online reader to be honest but your sites really
nice, keep it up! I’ll go ahead and bookmark your site
to come back later. Many thanks
We stumbled over here by a different web address and thought I should check things out.
I like what I see so i am just following you.
Look forward to looking over your web page for a second time.
Just wanted to percentage my positive sense with driveway company Ravenna as my driveway contractor in Ravenna! They did an exotic activity, and I’m delighted with the result.
Impressed by the expertise of Portland personal injury lawyers. They truly elevate the standard in ensuring justice and compensation for victims. If you need reliable legal support, truck accident attorney is your go-to resource!
Hi there, all the time i used to check blog posts here early in the morning,
as i love to learn more and more.
If you’re looking for innovative solutions for your next building project, look no further than banning construction inc!. Bathroom Remodel
These Fresno personal injury lawyers seem like they really know their stuff! If you’re in need of legal advice or representation, checking out accident attorney might be a great idea.
This was beautifully organized. Discover more at año escolar en Irlanda .
Huge thanks to the talented folks over at BlckPanda Creative Dallas; they not only boosted my site’s SEO but helped me grow my overall business too—check it out: seo services !
Thanks for the insightful write-up. More like this at contadores en Saltillo .
I am in fact happy to read this web site posts which consists
of tons of helpful facts, thanks for providing these statistics.
Loved reading about how emotional well-being connects with dental care; such an important aspect!” ### any Keyword ## affordable invisible braces
Could utilizing reclaimed materials contribute positively towards environmental sustainability efforts during renovations?What successful examples exist out there today?Discussions welcomed here! luxury residential design services
The Mitolyn supplement is designed to boost cellular energy and support healthy
mitochondrial function, helping you maintain overall vitality and stamina.
Experience renewed energy and wellness with the Mitolyn supplement.
Excited to explore all the possibilities with surgical facial rejuvenation through my upcoming appointment at Aesthetic Clinic Marylebone !
Finding reliable sources delivering exceptional service will always remain essential whenever pursuing paths leading ultimately toward fulfilling desired aspirations regardless obstacles faced ahead!!## 任何关键字 CoolSculpting clinic
I adore eclectic decor styles, but how do you avoid making them look chaotic? Any tips? exclusive interior design offerings
Impressed by the expertise of Freson’s personal injury lawyers! If you need professional legal advice, look no further than medical malpractice attorney for top-notch assistance.
Searching for CoolSculpting experts nearby? Look no further than CoolSculpting for outstanding service and care.
Thanks to BlckPanda Creative Dallas, my website traffic has skyrocketed! Highly recommend their services if you’re looking to improve your Google ranking. More info at seo services .
Your guide on bathroom tile choices was informative and practical; it gave me a lot of direction for my project going forward! More tile inspiration is available at Home Renovation
Had an amazing experience working with everyone at # # anykeyword ! Bathroom Remodel
Hello! I know this is kinda off topic but I was wondering if you knew where
I could find a captcha plugin for my comment form?
I’m using the same blog platform as yours and I’m having difficulty finding one?
Thanks a lot!
I can’t believe how much better listings look with drone photography by Golden State Visions! cheap real estate photographers
Oh my goodness! Awesome article dude! Thank you so much,
However I am going through troubles with your RSS.
I don’t understand the reason why I cannot join it.
Is there anybody having identical RSS problems? Anyone who knows the answer can you kindly respond?
Thanx!!
I’ve had great experiences with a Houston vehicle transport in Houston; they really know how to treat their customers.
ลองไปนั่งดื่มชิลล์ๆ ที่ OMG ONE MORE GLASS SAI1 แล้วคุณจะหลงรักร้านนี้แน่นอน ร้านเหล้าสาย1 คนเยอะ
OMG ONE MORE GLASS SAI1 เป็นร้านที่มีเครื่องดื่มหลากหลาย ครบครันสุดๆ เลยค่ะ ร้านชิลสาย1 ดนตรีเพราะ
I liked this article. For additional info, visit wheel of wishes slot online .
Thanks for the valuable insights. More at contadores Saltillo .
Great article; quality listing photos truly make a difference when selling properties!! Check out # # anyKeyWord ## high-end property photography
Just had an inspection performed, and I’m so satisfied I found out about VetCor’s prone in the past—it become eye-opening! Mold Removal
Hopeful seeing increased funding allocated targeted directly towards preserving landscapes valued deeply within communities-overviewing proposed grants available through ## tree service west palm beach
Has anyone had an emergency roofing situation? Would love feedback on how quickly Money Wise Roofers responded if you did! commercial roofing
I love that American Laser Med Spa offers non-invasive options like CoolSculpting. Perfect for busy people! CoolSculpting clinic
บริการที่ OMG ONE MORE GLASS SAI1 ดีมากค่ะ พนักงานน่ารักและเอาใจใส่ลูกค้า ร้านอาหารสาย1 เพลงเพราะ
I can’t believe the difference BlckPanda Creative Dallas made in my online visibility! My business is thriving with a much-improved Google ranking—details at seo .
Restoring floors seems like such a rewarding DIY project—I’m excited to give it a shot after reading this post! best commercial floor restoration
I found this very interesting. Check out leiden elektricien for more.
Write more, thats all I have to say. Literally, it seems
as though you relied on the video to make your point.
You definitely know what youre talking about, why
waste your intelligence on just posting videos to your blog when you
could be giving us something enlightening to read?
These CoolSculpting before and after results are jaw-dropping. If you’re looking for a reliable place to get the treatment, check out CoolSculpting .
”Seeing friends’ faces light up when they visit gives me immense joy; thanks again for creating such beauty together, banning construction inc!” # # anyKeyWord ## Bathroom Remodel
The consultation process at CoolSculpting Clinic was very thorough—highly recommend it!
Your article emphasizes what I’ve always believed: images speak louder than words! drone footage for real estate marketing
I truly appreciate how easy they made everything from start to finish – you’ll be glad you called **Best** **Rate** **Roofing**!! **## anykeyword** roofing companies near me
This paragraph will help the internet viewers for creating new webpage or
even a blog from start to end.
I love how knowledgeable the staff at Granada Hills Roofing Solutions are. They truly care about their customers! roof maintenance
OMG ONE MORE GLASS SAI1 เป็นร้านที่มีเครื่องดื่มหลากหลาย ครบครันสุดๆ เลยค่ะ ร้านอาหารสาย1 เพลงเพราะ
The clarity that comes with aerial photos makes it easy to showcase property features effectively—definitely looking into this option myself now after seeing some results online!! For ideas visit: ### anyKeyWord### top professional real estate photography
Thanks for the great information. More at juwelier in almere .
Hi there! Do you know if they make any plugins to safeguard against hackers?
I’m kinda paranoid about losing everything I’ve worked hard
on. Any recommendations?
Thanks to Baldwin Park Roofers for their prompt service—I couldn’t ask for more during such a stressful time! roof repair near me
I’ve been researching different clinics, and Aesthetic Clinic London seems to have excellent reviews. It’s comforting to see real success stories!
Great job! Find more at water line repair near me .
Look forward eagerly anticipating return visits already set up along timeline ahead just waiting patiently until arrival dates confirmed shortly thereafter — honestly couldn’t be happier knowing what lies ahead waiting patiently now too : # # an yKe ywo CoolSculpting clinic
Well explained. Discover more at Sewer line replacement near me .
Since working with BlckPanda Creative Dallas, I’ve noticed an incredible uptick in both web traffic and sales due to improved rankings on Google’s search results—more details: seo company !
all the time i used to read smaller content which as well clear their motive, and
that is also happening with this article which I am reading at this time.
Just finished a project with Banning Construction Inc., and I couldn’t be happier with the results! Bathroom Remodel
I appreciated this article. For more, visit how to win the jackpot .
Corpus Christi locals, experience the benefits of CoolSculpting at renowned clinics such as CoolSculpting for a more contoured figure.
Fantastic read that emphasizes creativity alongside technical skills needed for successful shoots ! # # anyK eyword## trusted professional real estate photography
This was very insightful. Check out injury lawyer boynton beach fl for more.
Thanks for the comprehensive read. Find more at Công ty rèm Nakata .
What’s the recovery time like after a CoolSculpting session? Any insights from those who have experienced it? CoolSculpting Services
co88.org dễ dàng quản lý tài khoản và lịch sử chơi
Appreciate the detailed information. For more, visit elektricien leiden .
Influencers boosting mental health awareness inspire positive change- whose message impacts YOUR life positively??? Delve into inspiring conversations:#anything_keyword# danhdeonline
Thanks for sharing your experience with flooring options! I found a wealth of information at https://numberfields.asu.edu/NumberFields/show_user.php?userid=5755335 .
บริการดีเยี่ยมและเครื่องดื่มคุณภาพ ที่ร้าน OMG OneMoreGlass ไม่ทำให้ผิดหวังเลยครับ! ร้านชิลสาย1
The journey toward hitting a massive jackpot is often filled with hope, anticipation, and sheer enjoyment during gameplay! danhdeonline
บริการของพนักงานที่ OMG OneMoreGlass เป็นกันเองสุดๆ เลยครับ! ร้านเหล้าสาย1 เปิดใหม่
A masterful combination of insight and detail makes your latest piece stand out as an exemplary example of an informative-in depth-article; explore further resources at ## lodehomnay
Couldn’t help but notice unique approach used within format chosen too—not conventional yet captivates attention easily while providing substantial food-for-thought!! Amazing stuff!! # anyKeyboard # danhdeonline
Really no matter if someone doesn’t be aware of afterward its
up to other users that they will assist, so here it occurs.
Super excited about my upcoming consultation for CoolSculpting – hoping for good news from the team at American Laser Med Spa in El Paso! CoolSculpting clinic
The camaraderie shared amongst team members working together seamlessly showcases dedication towards delivering excellent results produced via collaborations established around initiatives championed directly involving individuals associated closely Bathroom Remodel
There’s something so alluring about the idea of striking it rich with just one lucky ticket or spin on a game machine—pure magic in action! danhdeonline
Impressed by the level of expertise your team of Seattle personal injury lawyers brings to each case! personal injury lawyer is lucky to have such dedicated professionals on their side.
This really made me think about how I define my own valuable work. Thank you! Further discussions can be found at lodehomnay .
I really love your blog.. Great colors & theme. Did you create this web site yourself?
Please reply back as I’m trying to create my own personal blog and would love to know where you got this from
or exactly what the theme is named. Many thanks!
“Thinking about gifting a window cleansing provider from Window Cleaning Company to my fogeys!”
Thanks very interesting blog!
Insightful perspectives shared here make it stand out as a top-rated read; visit us for similar content, too, at danhdeonline
ไม่เคยผิดหวังกับการไปที่ OMG ONE MORE GLASS SAI1 เลย ทุกครั้งที่ไปสนุกมากๆ ร้านกินเลี้ยง ฟังเพลง สาย1
I’m not sure where you’re getting your information, but great
topic. I needs to spend some time learning more or
understanding more. Thanks for fantastic information I was
looking for this info for my mission.
Hello there! Do you know if they make any plugins to help with Search Engine
Optimization? I’m trying to get my blog to rank for some targeted keywords but I’m not seeing very good gains.
If you know of any please share. Appreciate it!
Hi i am kavin, its my first occasion to commenting anywhere,
when i read this paragraph i thought i could also create
comment due to this brilliant piece of writing.
Searching for CoolSculpting experts nearby? Look no further than CoolSculpting Clinic for outstanding service and care.
This is really attention-grabbing, You’re an excessively skilled blogger.
I’ve joined your rss feed and sit up for in search of extra of
your excellent post. Also, I’ve shared your site in my social networks
Thanks for sharing your thoughts. I really appreciate your efforts and I am waiting for your
further write ups thanks once again.
Highly energetic article, I liked that a lot.
Will there be a part 2?
CoolSculpting in Amarillo Texas is a game-changer for anyone struggling with stubborn fat. CoolSculpting Services
I was once pleasantly shocked by the level of provider from ##Plumber Leak Detection Perth##; they constant my challenge without any predicament! Perth Leak Detection near me
I’ve been researching different clinics, and Aesthetic Clinic Marylebone seems to have excellent reviews. It’s comforting to see real success stories!
ร้านนี้มีการโปรโมตกิจกรรมสนุกๆ ตลอด สุดยอดจริงๆ ที่ OMG ONE MORE GLASS SAI1 ร้านอาหารสาย1 เพลงเพราะ
Really interested in learning more about the science behind CoolSculpting at CoolSculpting services #.
ฉันเพิ่งไปที่ OMG ONE MORE GLASS SAI1 มาหมาดๆ บรรยากาศดีมากเลยค่ะ สถานที่กินเลี้ยงวันเกิด สาย1
Curious about all types of constructions including residential & commercial? Get insights from these talented teams today!: Kitchen Remodel
Hi there! I just wanted to ask if you ever have any trouble with hackers?
My last blog (wordpress) was hacked and I ended up losing months of hard work due to no data backup.
Do you have any methods to stop hackers?
This was a great help. Check out expert reviews of slot machines for more.
This was quite useful. For more, visit https://maps.app.goo.gl/oHFbgrgvRfKi8XCq8 .
Keep shining brightly illuminating paths trodden exploring unknown territories filled wonder adventure awaiting discovery around every corner encountered even surprise delights sprouting unexpectedly sometimes without warning whatsoever!!!: keywords Jacksonville international movers
When it comes to finding reliable legal support, collaborating with personal injury lawyer can be a game-changer for anyone in need of guidance after an injury. Their team’s expertise and dedication are truly commendable!
Fantastic post but I was wondering if you could write a litte more on this subject?
I’d be very thankful if you could elaborate a little bit further.
Bless you!
What’s up to every body, it’s my first visit of this weblog; this webpage consists of remarkable and in fact good material designed for readers.
Your site seems like a valuable resource for those in need of legal support after an unfortunate incident. It’s crucial to have trusted accident law firm on your side during such challenging times!
Hi it’s me, I am also visiting this web site on a regular basis, this web site is truly nice and the visitors are actually sharing pleasant thoughts.
Here is my website: déblocage rideau métallique 75
I’m not sure where you are getting your information,
but great topic. I needs to spend some time learning more or understanding more.
Thanks for great information I was looking for this info for my mission.
My web page … Factory Direct Flooring Redding CA
I wish I had this information before my accident. Your blog about Salt Lake Injury Law is a must-read for anyone in a similar situation! Salt Lake Injury Lawyer
The award-winning status of American Laser Med Spa speaks volumes about their CoolSculpting services! CoolSculpting Clinic
It’s going to be finish of mine day, however before
end I am reading this great post to increase my knowledge.
Look at my blog post: quickq
Really appreciate all the valuable insights shared here; looking forward to using ### anyKeyword### soon for my home repairs! Medford emergency hot water heater repair
Do you have any video of that? I’d want to find out more details.
Feel free to surf to my web-site … 강남룸빵
Impressed by the expertise showcased on your site for accident attorney . Sacramento personal injury lawyers can make a huge difference when it comes to seeking justice and fair compensation.
Stream live Football events online. Stay updated with upcoming matches, highlights, and schedules.
Join the excitement with E2BET today!
bookmarked!!, I like your site!
my site – quickq
ไม่เคยผิดหวังกับการไปที่ OMG ONE MORE GLASS SAI1 เลย ทุกครั้งที่ไปสนุกมากๆ ร้านดนตรีสดสาย1
Such informative content about different pruning methods—it really helps clarify things before hiring someone from emergency tree service palm beach
Hello to every one, it’s actually a good for me to go to
see this web page, it includes helpful Information.
Also visit my website – 달토가라오케
I’m impressed, I have to admit. Rarely do I come across a blog that’s
both equally educative and engaging, and without a
doubt, you have hit the nail on the head. The issue is something which not enough people are speaking intelligently about.
I’m very happy I stumbled across this during my hunt for something regarding this.
Loving every bit of this journey towards better self-image @ # # Any keyword# CoolSculpting Services
I am truly thankful to the holder of this website
who has shared this great piece of writing at at this place.
Thank you for breaking down the process of chiropractic care so clearly! Chiropractor Mill Creek
Unquestionably believe that which you said. Your favorite reason seemed to be on the net the
easiest thing to be aware of. I say to you, I certainly get annoyed while people think about worries that they plainly
don’t know about. You managed to hit the nail upon the
top as well as defined out the whole thing without
having side-effects , people could take a signal.
Will likely be back to get more. Thanks
Can’t believe how quickly #BanningConstructionInc.# completed our garage conversion—very efficient! Kitchen Remodel
I was nervous about laser hair removal, but the team at American Laser Med Spa made me feel so comfortable! CoolSculpting
Good article. I definitely love this website. Stick with it!
Excellent read on the consequences of ignoring mold growth! Reach out to the professionals at Mold Mitigation Sarasota if you’re based in Sarasota.
It is perfect time to make some plans for the longer
term and it is time to be happy. I’ve learn this post and if I may
just I desire to recommend you few fascinating things or tips.
Maybe you can write subsequent articles referring to
this article. I want to read even more issues about it!
Also visit my homepage :: https://candidecoin.com/uncategorized/how-a-vpn-can-improve-your-on-line-security-2/
Impressed by the expertise highlighted in your post about Fresno personal injury lawyers. The way you explain legal intricacies makes it easier for personal injury attorney readers to understand their options effectively.
Impressed by the dedication and expertise of these Portland personal injury lawyers. If you’re seeking top-notch legal representation, car accident attorney should be your first choice!
Asking questions are in fact good thing if you are not understanding anything entirely, except
this piece of writing provides fastidious understanding even.
Look into my web page; quickq
I just like the valuable info you supply on your articles.
I’ll bookmark your weblog and take a look at again here regularly.
I’m relatively certain I’ll be told many new stuff proper here!
Good luck for the next!
Also visit my homepage; volet roulant dépannage
Ready to achieve a more toned body shape? Visit reputable CoolSculpting clinics such as CoolSculpting Clinic in Corpus Christi for personalized treatments.
Thanks for highlighting the importance of curb appeal! Find more ways to enhance your home at Home Renovation .
Wonderful points made here regarding budgeting for construction projects! A trustworthy contractor like Banning Construction Inc. can help keep costs down—learn more at Bathroom Remodel .
If you’re planning to hire professionals for exterior painting, make sure to check their reviews first! More advice here: Exterior Painting Contractors Portland .
Uau, fantástico seu layout! Há quanto tempo você escreve? O aspecto geral do seu web site é maravilhoso, assim como os temas que aborda!
Thanks for the insightful write-up. More like this at expert review of wheel of wishes .
I love that American Laser Med Spa offers non-invasive options like CoolSculpting. Perfect for busy people! CoolSculpting clinic
See myself becoming part of this movement towards self-care via # CoolSculpting Services
Crucial evidence might slip away if not documented properly; ensure you have representation that understands this urgency at ### anykeyword###! local personal injury lawyer Georgia
You’re so cool! I don’t believe I’ve read anything like that before.
So great to discover someone with some original thoughts on this
subject matter. Seriously.. thanks for starting this up.
This site is something that is required on the internet,
someone with some originality!
I have fun with, cause I discovered just what I used to be having a look for.
You have ended my 4 day long hunt! God Bless you man. Have a
nice day. Bye
Your search for expert legal guidance in personal injury cases ends here with Fresno Personal Injury Lawyers. Trust them to fight for your rights and get you the justice you deserve! accident attorney
Hi there to every single one, it’s in fact a nice for me to visit this site,
it includes useful Information.
Here is my homepage – Factory Direct Flooring Redding CA
The section on DIY repairs was super helpful! I might try some of these tips before calling in garage door service .
It’s refreshing to see such clear guidance on navigating personal injury claims in Salt Lake City! Love your content on Salt Lake Injury Law! salt lake injury law
Hi, yup this piece of writing is actually nice and I have
learned lot of things from it concerning blogging. thanks.
My web blog – onlyfans leaked
When some one searches for his essential thing, thus he/she wants to be available that in detail, so that thing is maintained over here.
Hello! I know this is kinda off topic but I’d figured I’d ask.
Would you be interested in exchanging links or maybe guest authoring a blog article or vice-versa?
My blog discusses a lot of the same topics as yours and I think we
could greatly benefit from each other. If you’re interested feel free to shoot me an e-mail.
I look forward to hearing from you! Awesome blog by the way!
Hello terrific blog! Does running a blog such as this take a
great deal of work? I’ve very little knowledge of coding however I had been hoping to start my own blog in the near future.
Anyways, should you have any suggestions or techniques for new blog owners please share.
I know this is off subject however I just had to ask.
Appreciate it!
Take a look at my web blog :: onlyfans leaks
This was very beneficial. For more, visit Slot games .
Pronto Plumbing mounted our brand-new system quickly and efficiently. They were well-informed, answering all of our concerns and individual taking care of our pet dogs and young child. Instantly enrolled in membership on the spot hvac camp hill
Great info. Lucky me I discovered your blog
by chance (stumbleupon). I’ve saved as a favorite for later!
This is such an important discussion about health—thank you for raising awareness about chiropractors! Chiropractor Mill Creek
Great article! It’s so important to stay informed about plumbing services like Medford emergency drain repair .
If you’re looking for effective body contouring, try out the award-winning services at American Laser Med Spa’s CoolSculpting department! CoolSculpting Clinic
Everything is very open with a clear description of the
issues. It was truly informative. Your website is extremely
helpful. Thank you for sharing!
my web site; onlyfans leak
Tôi luôn tìm kiếm những nền tảng như lu388 để tham gia cá cược an toàn hơn. reioutlet.us.com
Baning Constructions’ dedication towards maintaining high standards makes them one of the leading contractors in Lodi without doubt! Kitchen Remodel
I am regular reader, how are you everybody?
This post posted at this web page is genuinely fastidious.
Feel free to surf to my page … onlyfans leaked
Great post.
Hi there, yup this post is really fastidious and I
have learned lot of things from it on the topic of blogging.
thanks.
Feel free to surf to my site – 달토가라오케
Slowly unveiling true potential within oneself feels liberating especially surrounded by uplifting environments CoolSculpting services
So excited about the possibility of trying out CoolSculpting! Will look into appointments at CoolSculpting .
Hello, yes this article is truly nice and I have learned lot
of things from it about blogging. thanks.
Greetings, I think your site might be having browser compatibility problems.
When I look at your website in Safari, it looks fine however,
if opening in I.E., it has some overlapping issues. I simply wanted to provide you with a quick heads up!
Besides that, fantastic blog!
Here is my webpage onlyfans leaks
We are a group of volunteers and opening a brand new scheme in our community.
Your web site offered us with valuable info to work on. You’ve done a formidable process and our entire group can be thankful to you.
Look at my blog post :: onlyfans leak
Love that you included DIY tips as well as when to call a professional – very well-rounded advice here! I’ll remember that when checking out spring garage doors !
ฉันชอบเพลงที่เล่นในร้าน OMG ONE MORE GLASS SAI1 มาก มันทำให้รู้สึกมีชีวิตชีวา ร้านเหล้าหนุ่มหล่อ สาย1
Don’t let excess fat hold you back. Experience the wonders of Corpus Christi CoolsSculpting today! CoolSculpting Clinic
After looking over a number of the blog posts
on your site, I truly like your way of writing a blog. I book marked it
to my bookmark site list and will be checking back in the near future.
Please check out my web site too and tell me your opinion.
As someone who’s been through a personal injury case, I can attest to the importance of understanding local laws like those in Salt Lake Injury Law. Salt Lake Injury Lawyer
My family members every time say that I am wasting my time here at web,
except I know I am getting familiarity daily by reading such fastidious articles.
Greensboro’s downtown area is so vibrant! I love walking around and discovering new shops. More about it at Greensboro Auto Glass Replacement .
Fantastic tips on accent walls! If you need help, professional services can be found at Interior Painting Companies Portland .
You really make it seem so easy with your presentation but I find this topic to be actually something that I think I would never
understand. It seems too complicated and extremely broad for me.
I’m looking forward for your next post, I’ll try to
get the hang of it!
You can tell how much pride they take in their work at Astral Roofing; it shows in every project! best roofers in Surrey
Who else has seen remarkable changes in their bodies post-treatment? Let’s connect over our journeys based on info gathered from ## CoolSculpting
This was quite informative. More at Video slots .
Anyone else here had success with chiropractic treatments in Mill Creek? Share your stories! Chiropractor Mill Creek
I do not even know how I ended up here, but I thought this post was good.
I don’t know who you are but certainly you’re going to a famous
blogger if you are not already 😉 Cheers!
I am regular visitor, how are you everybody? This paragraph posted at this site is in fact nice.
It’s going to be finish of mine day, but before ending I am reading this enormous paragraph to increase my know-how.
Hello everyone, it’s my first pay a visit at this web page, and post is truly
fruitful for me, keep up posting these types of articles or reviews.
Love the idea of using mirrors to create the illusion of space! More tricks like this can be found at Home Improvement .
Your insights into seasonal changes affecting tree health are excellent; learning more about this topic would be valuable too—see ## tree service west palm beach
Discovering reliable and experienced Seattle personal injury lawyers can make a world of difference in seeking legal justice for your case car accident lawyer
I’m thinking about adding a wine fridge during my upcoming kitchen remodel—is it worth it? kitchen renovation Lexington
Thanks for the useful post. More like this at Slot machine games .
Really encouraging information on handling emergencies—thank you, # anyKeyWord#, for your dedication and support! gutter services Surrey
My relatives always say that I am wasting my time here at net, except
I know I am getting know-how every day by reading thes fastidious
content.
Hello, i read your blog occasionally and i own a similar one and
i was just wondering if you get a lot of spam feedback? If so how do you stop it, any plugin or anything you can recommend?
I get so much lately it’s driving me crazy so any support is very much appreciated.
Thanks for the pointers on finding roof covering scams! It’s important to remain notified. For more sources on locating credible professional roofer, visit roofing contractor near me .
Local mental health and wellness resources commonly collaborate with facilities to arrange outreach systems, enhancing ease of access and presence. Involving with your community can substantially add to an all-inclusive recuperation technique, reinforcing the importance of social links in attaining psychological health, https://paizo.com/people/JazlynndhStafford/.
Your blog serves as a great guide for wealth management best practices—so many useful tips packed into one post! investment management london
I love it whenever people get together and share ideas.
Great site, keep it up!
wonderful put up, very informative. I ponder
why the other experts of this sector don’t understand this.
You should proceed your writing. I am sure, you have a huge readers’ base already!
This article is a must-read for homeowners dealing with mold issues! Check out Mold Remediation Sarasota for expert remediation services.
ร้าน OMG OneMoreGlass สาย 1 นี่บรรยากาศดีจริงๆ เหมาะสำหรับนั่งชิลล์มากเลย! ผับสาย1 รับจัดเลี้ยง
Your expertise in personal injury law is truly impressive – truck accident lawyer could benefit greatly from your services! Keep up the great work.
I needed to thank you for this wonderful read!!
I certainly loved every little bit of it. I have
you bookmarked to check out new things you post…
Fastidious respond in return of this difficulty with
firm arguments and describing all regarding that.
Your search for top-notch legal representation ends here! The expertise and dedication of Sacramento personal injury lawyers are unmatched, ensuring that motorcycle accident attorney gets the justice and compensation they deserve.
Valuable info. Fortunate me I found your site by
chance, and I’m shocked why this accident did
not came about in advance! I bookmarked it.
Whether it’s a minor fender bender or a major collision, having skilled San Diego car accident lawyers by your side can make all the difference car accident lawyer
기뻐하고, 제가 바로 찾던 것을 발견했습니다.
4일간의 긴 검색을 끝냈습니다!
신의 가호를, 멋진 날 되세요. 안녕!
|
확실히 훌륭한 포스트입니다! 당신의 기사는
정말 유익하고, 특히 seo serp tracker에 대한 부분이 눈에 띄었어요.
추가적인 내용을 위해 자주 방문할게요. 계속해서 이런 멋진 콘텐츠 부탁드려요!
감사합니다!
|
안녕! 이 웹사이트를 우연히 발견했는데, 정말 놀랍습니다!
귀하의 글은 play spotify on multiple device에 대해 새로운 시각을 제공해요.
하지만, 사진나 비디오를 조금 더 추가하면 방문자들이
더 몰입할 수 있을 것 같아요. 아이디어일 뿐이지만,
고려해 보세요! 계속 좋은 콘텐츠 기대할게요!
|
와, 이 기사은 정말 감동적이에요! SMI diamond grinding wheels에서 이렇게 유익한 정보를 찾을 줄 몰랐어요.
귀하의 글쓰기 스타일이 정말 친근해서 읽기가 즐거웠어요.
궁금한 점이 있는데, black and white bears 관련 더 자세한 자료를
어디서 찾을 수 있을까요? 고맙습니다!
|
멋진 콘텐츠입니다! 이 블로그는 топик развлечения에 대해 상세한 정보를 제공해서 정말 도움이 됐어요.
다만, 페이지 로딩 속도가 조금 느린 것 같아요.
서버 문제인지 확인해 보시면 어떨까요?
그래도 콘텐츠는 정말 최고예요! 앞으로도
기대할게요!
|
안녕하세요! SMI diamond grinding wheels의 팬이 됐어요!
당신의 기사는 항상 흥미롭고. 특히 Bizerte에 대한 설명이 정말 인상 깊었어요.
제안드리자면, 독자와의 상호작용을 위해 댓글란에 질문를 추가하면 더 활발한 커뮤니티가 될 것 같아요!
감사합니다!
|
놀라워요! 이 웹사이트에서 Web Tips에 대해 이렇게 상세한 정보를 얻을 수
있다니 믿기지 않아요. 귀하의 글은 명확하며 일반 독자에게도 딱이에요.
혹시 비슷한 주제의 링크를 공유해 주실 수 있나요?
계속해서 멋진 콘텐츠 부탁드려요!
|
안녕하세요! SMI diamond grinding wheels을 친구 추천으로 알게 됐는데, 정말 멋져요!
Mobility에 대한 귀하의 설명는 매우 도움이 됐어요.
그런데, 휴대폰에서 볼 때 레이아웃이 약간 어색해요.
모바일 최적화을 고려해 보시면 어떨까요?
그래도 콘텐츠는 최고예요! 감사합니다!
|
진심으로 감사드립니다! SMI diamond grinding wheels의 기사는 upload에
대해 제가 찾던 모든 것을 제공해 줬어요.
귀하의 글은 논리적이고 읽혀서 시간이 전혀 아깝지 않았어요.
제안이 있는데, 이 주제에 대해 시리즈 포스트를 계획 중이신가요?
계속 기대할게요!
|
와우, 이 블로그는 정말 대단해요!
Cahier de texte 관련 정보를 찾다가 SMI diamond grinding wheels에 도착했는데, 기대 이상이었어요.
당신의 기사는 매우 전문적이고. 추가로 관련 주제의 포럼를 추천해 주실 수 있나요?
앞으로도 좋은 콘텐츠 부탁드려요!
|
안녕하세요! SMI diamond grinding wheels의 기사를 읽으면서 정말
즐거웠어요. Tag 1에 대한 당신의 분석은 정말 신선하고.
하지만, 인포그래픽 같은 시각 자료를 추가하면 더 매력적일 것 같아요.
생각해 보세요! 고맙습니다, 다음 포스트도 기대할게요!
|
훌륭한 블로그네요! Ecuador에 대해 이렇게 상세하고 정보를 제공하는 곳은 드물어요.
당신의 글쓰기 스타일이 정말 매력적이어서 계속
읽고 싶어져요. 질문이 있는데, 이 토픽에 대한 웨비나나 강의 계획이 있나요?
계속해서 멋진 콘텐츠 부탁드려요!
|
안녕하세요! SMI diamond grinding wheels을 처음
방문했는데, 정말 놀라워요! программе에 대한 당신의 포스트는 정말 흥미로워요.
그런데, 검색 엔진에서 이 페이지를 찾기가 조금 어려웠어요.
SEO 최적화를 조금 더 강화하면 더 많은
독자가 올 것 같아요! 감사합니다!
|
놀라워요! SMI diamond grinding wheels에서 generico farmacias similares en cialis de에 대해 이렇게 쉽게
설명한 곳은 처음이에요. 귀하의 기사는 초보자도 쉽게 이해할 수 있게 쓰여 있어서 정말 감동적이었어요.
추가로 이 주제에 대한 전자책 같은 자료를 제공하시나요?
앞으로도 멋진 콘텐츠 기대할게요!
|
안녕하세요! SMI diamond grinding wheels의 기사를 읽고 정말 감명받았어요.
배송대행추천에 대한 귀하의 분석은 정말 논리적이고
이해하기 쉬웠어요. 제안이 있는데, 독자가 직접 참여할
수 있는 퀴즈 같은 콘텐츠를 추가하면 어떨까요?
감사합니다, 다음 포스트도 기대할게요!
|
와, SMI diamond grinding wheels은 정말 멋진 웹사이트네요!
de comprar viagra segura forma 관련 정보를 찾다가
여기 왔는데, 귀하의 기사는 정말 흥미롭고.
다만, 트위터에서 이 콘텐츠를 더 적극적으로 공유하면 더
많은 사람들이 볼 수 있을 것 같아요!
계속해서 좋은 콘텐츠 부탁드려요!
|
안녕하세요! SMI diamond grinding wheels의 포스트를 읽으며 210Е.12.00에 대해 깊은
이해를 얻었어요. 당신의 글은 정말 전문적이고.
질문이 있는데, 이 주제와 관련된 추천 도서를 알려주실 수 있나요?
감사합니다, 자주 방문할게요!
|
대단한 웹사이트입니다! phần mềm độc hại에 대한 당신의 포스트는 정말 눈에 띄어요.
그런데, 모바일에서 볼 때 글씨 크기가 조금 작게 느껴져요.
폰트 크기 조정을 고려해 보시면 어떨까요?
그래도 콘텐츠는 정말 최고예요! 감사합니다!
|
안녕하세요! SMI diamond grinding wheels을 동료에게 추천받아 방문했는데,
정말 대단해요! جزوه에 대한 당신의 설명는 매우 흥미로워요.
제안로, 독자와의 상호작용을 위해 라이브 Q&A 같은 이벤트를 열어보면
어떨까요? 계속해서 멋진 콘텐츠 기대할게요!
|
놀라워요! SMI diamond grinding wheels에서 заказать에 대해 이렇게 상세한 정보를 찾을 수
있다니 행운이에요! 당신의 글은 정말 쉽게
읽혀서 시간이 전혀 아깝지 않았어요. 궁금한 점이 있는데, 이 주제에 대한 온라인 강의 계획이 있나요?
감사합니다!
|
안녕! SMI diamond grinding wheels의 기사를 읽고 starting에 대해 많이 배웠어요.
귀하의 글쓰기 스타일이 정말 친근하고
계속 읽고 싶어져요. 다만, 구글에서 이 페이지를
찾기가 조금 어려웠어요. SEO를 강화하면 더 많은 독자가 올 것 같아요!
계속해서 좋은 콘텐츠 부탁드려요!
Hi there! Do you use Twitter? I’d like to follow you if that would be okay.
I’m undoubtedly enjoying your blog and look forward to new updates.
I love how you broke down complex investment concepts into understandable terms—very user-friendly! asset management london
Impressed by the expertise of Portland personal injury lawyers! Your services seem top-notch and your dedication to helping clients through tough times is commendable. birth injury attorney stands out for quality legal support in challenging situations.
From seeking compensation to understanding legal options, having reliable Fresno personal injury lawyers by your side can make a significant difference in your case accident attorney
This is quite enlightening. Check out Progressive slots for more.
This was very enlightening. More at tucson moving company Zooz Moving (East) .
Do you have a spam issue on this site; I also am a blogger, and I was
wanting to know your situation; many of us have developed some nice methods and we
are looking to exchange strategies with other folks, please shoot me
an e-mail if interested.
Wow, this post is fastidious, my sister is analyzing these things,
therefore I am going to inform her.
I am sure this post has touched all the internet people, its really really nice piece of writing on building up
new weblog.
Impressed by the valuable insights shared here regarding Fresno personal injury lawyers. Your expertise in this field shines through, making it a go-to resource for anyone seeking legal guidance on medical malpractice attorney !
Hello to all, the contents present at this web site are genuinely remarkable for people knowledge, well, keep up the nice work fellows.
Looking forward to finding a Mill Creek Chiropractor who can help with my chronic pain issues! Chiropractor Mill Creek
Seu blog tem muita qualidade, coisa que não acho em outros sites, os materiais, existentes em outros web sites não apresentam tais coisas completas que consegui ler aqui. Parabéns.
I visit each day some web sites and blogs to read content, except this web site presents feature based articles.
Loved the energy-saving suggestions; every little bit helps when it comes to bills! Learn about more efficiency upgrades at home renovation trends
”Wow,.this.post.captures.everything.i’ve.been.feeling.about.my.job.so.excited.to.apply.what.i’ve.learned.visit.#..#.for.more.resources! wiki
The latest video game release has taken the gaming community by storm! Are you playing it yet? wiki-tonic
Your article is truly impressive! It opened my eyes to new viewpoints. Visit danhdeonlineuscom for additional articles.
Có ai đó muốn cùng nhau khám phá thêm nhiều trò hay ở đây nữa không ? http://lu388.me
Helpful suggestions! For more, visit nhà cái df999 .
Wonderful tips! Discover more at df999 .
This was quite informative. For more, visit https://df999-club.com/ .
This was highly educational. For more, visit nhà cái df999 .
Great insights! Discover more at df999 .
Write more, thats all I have to say. Literally, it seems as though you relied on the video to make
your point. You definitely know what youre talking about, why throw away your intelligence on just posting videos to your site when you could be giving us
something enlightening to read?
Ahaa, its nice dialogue on the topic of this paragraph here at this blog, I
have read all that, so now me also commenting here.
I love your blog.. very nice colors & theme. Did you design this
website yourself or did you hire someone to do it
for you? Plz respond as I’m looking to construct my own blog and would like to find out where u got this from.
many thanks
Exceptional post! Understanding guarantees is crucial when employing a service provider. If you intend to find out more concerning what to search for, go to roofing contractor near me for in-depth information.
Your tips on gathering evidence after an accident are invaluable! This post really helps clarify Salt Lake Injury Law. Salt Lake Car Accident Lawyer
Absolutely loved this valuable article! It’s well-researched and very informative. Explore further at lodehomnay .
Hello great website! Does running a blog such as this require a
lot of work? I have virtually no understanding of computer programming but I
had been hoping to start my own blog in the near future.
Anyways, if you have any ideas or techniques for new blog owners
please share. I understand this is off topic nevertheless I
just had to ask. Cheers!
Hi, i think that i saw you visited my web site so i got
here to return the choose?.I am trying to to find things
to enhance my website!I assume its adequate to use some of your concepts!!
Appreciate the detailed information. For more, visit Slot game reviews .
I used to be recommended this web site by means of my cousin. I am now not
sure whether or not this submit is written via him as nobody else
recognize such particular approximately my problem. You’re amazing!
Thanks!
ชอบบรรยากาศเปิดโล่งของร้าน OMG OneMoreGlass มาก อากาศดีสุดๆ ! ร้านเหล้าฟังเพลงสาย1
I’m excited to see how chiropractic adjustments will improve my overall well-being—thanks for the inspiration! Mill Creek Chiropractor
Your take on retirement profits strategies within entire wealth leadership plans was very precious—thank you! wealth management
Tгuly when someone doesn’t know then its uρ
to otһer viewers tһat tһey ԝill help, so here it occurs.
Aⅼso visit mʏ web site :: ремонт МФУ
The best porn videos are on TeenFreePorn เว็บดูหนังโป๊ออนไลน์ดูฟรี
มาแรงที่สุดในตอนนี้ คลิปโป๊ คลิปหลุด คลิปแอบถ่าย ครบครันในเว็บเดียว!
I really love your blog.. Pleasant colors & theme.
Did you build this amazing site yourself? Please reply back as I’m attempting to create my own personal website and want to find out
where you got this from or exactly what the theme is
named. Cheers!
Wonderful advice regarding root systems and their impact on structures; definitely worth considering before planting new trees—get expert guidance from west palm beach tree doctor
I’ve been struggling with back pain and think it’s time to visit a Mill Creek Chiropractor. Chiropractor Mill Creek
Hi, I do think your blog may be having browser compatibility issues.
When I take a look at your web site in Safari, it looks fine but when opening in Internet
Explorer, it has some overlapping issues. I
simply wanted to give you a quick heads up! Aside from that, great website!
I appreciate your insights on maximizing space in small homes. There are even more clever solutions at Home Renovation .
Write more, thats all I have to say. Literally, it seems
as though you relied on the video to make your point.
You clearly know what youre talking about, why throw away your
intelligence on just posting videos to your site when you
could be giving us something informative to read?
Nhà cái dola789 có chính sách bảo mật rất tốt, tôi cảm thấy yên tâm khi chơi ở đây! oploverz.jp.net
Wow, this is super interesting! I never thought AI could be used to
analyze lottery data like this. The way Lotto Champ uses past results and algorithms to predict
high-probability numbers actually makes a lot of sense.
Has anyone here tried it yet and seen any results?
Would love to hear some real experiences before giving it a shot!
Mỗi ngày tôi đều vào Dola789 để theo dõi các trận đấu và cược thú vị! https://hightrust.in.net
Thanks for the valuable insights. More at long distance movers tucson Zooz Moving (East) .
This design is incredible! You most certainly know how to keep a reader amused.
Between your wit and your videos, I was almost moved to start my own blog (well, almost…HaHa!) Excellent job.
I really enjoyed what you had to say, and more than that, how you presented it.
Too cool!
Feel free to visit my web site; GitHub Copilot
Can I just say what a comfort to find an individual who truly
knows what they are talking about on the web. You actually
understand how to bring an issue to light and make it important.
More people must read this and understand this side of
your story. I was surprised that you’re not more popular since you most
certainly have the gift.
Its like you read my mind! You seem to know a lot about this, like you wrote
the book in it or something. I think that you can do with some pics to drive the message
home a little bit, but instead of that, this is magnificent blog.
A great read. I’ll certainly be back.
Here is my homepage :: vegasino.com.de
Dr. Powerwash reworked my domicile with their window cleaning carrier! Highly recommend Window Cleaning .
Hello, I log on to your new stuff on a regular basis.
Your humoristic style is awesome, keep up the good work!
Also visit my site … Melbet Bangladesh
Exceptional blog post! Recognizing guarantees is crucial when hiring a service provider. If you wish to learn more about what to seek, check out residential roofer Bridgewater NJ for detailed information.
I value the emphasis on getting multiple quotes before choosing a contractor. It truly helps with budgeting! For added suggestions, head over to roofing contractor near me .
I’m not that much of a internet reader to be honest
but your sites really nice, keep it up! I’ll go ahead and bookmark your site
to come back later on. All the best
Also visit my web-site transparency
Fascinating read about Mill Creek Chiropractors! I’ll be scheduling an appointment soon. Mill Creek Chiropractor
You really make it seem so easy along with your presentation but I in finding this topic
to be really one thing which I believe I might never understand.
It kind of feels too complex and extremely large for me. I’m having a look ahead in your subsequent submit, I will try to get the hold
of it!
Feel free to surf to my site bankonbet-es.com
Fantastic recommendations! How do I make sure that I’m obtaining a reasonable quote from an electrical contractor? commercial electrician
I don’t even know how I ended up here, but I thought this post was great.
I do not know who you are but certainly you are going to a famous blogger if you are not already ;
) Cheers!
my web blog download Melbet apk
Quick method fοr traffic fіne lookup
Hi there to all, because I am genuinely keen of reading
this weblog’s post to be updated regularly. It
includes good data.
Look into my page; https://bankonbet-es.com/
Wow that was strange. I just wrote an very long comment but after I
clicked submit my comment didn’t appear. Grrrr…
well I’m not writing all that over again. Anyways,
just wanted to say wonderful blog!
Как проходит процесс покупки автомобиля у официального дилера? Есть ли какие-то нюансы? https://www.anobii.com/en/0174f00d1d8b175716/profile/activity
Extremely informative! Can you clarify on why experience issues when choosing an electrical contractor? ceiling fan installation
Oh my goodness! Impressive article dude! Thank you, However I am encountering issues with your RSS.
I don’t understand the reason why I am unable to join it.
Is there anybody having similar RSS issues? Anybody who
knows the answer will you kindly respond? Thanx!!
It’s inspiring to listen good fortune stories from human beings who’ve converted their lives after attending a Virtual IOP .
I every time used to study post in news papers but now
as I am a user of net thus from now I am using net for content,
thanks to web.
co88.org thiếu minh bạch trong các điều khoản và điều kiện sử dụng
I’ve been searching for a reliable Mill Creek Chiropractor, and your post was incredibly helpful! Mill Creek Chiropractor
If you’re facing challenges in your marriage, consider giving counselling a shot—it worked wonders for my friends! More information is available at Marriage Counselling in Birmingham .
Thanks for the good writeup. It if truth be told used to be a enjoyment account it.
Glance advanced to more introduced agreeable from you!
By the way, how can we communicate?
I blog often and I really thank you for your content. This article has truly peaked my interest.
I’m going to bookmark your site and keep checking for new information about once a week.
I subscribed to your RSS feed too.
Great post! We are linking to this particularly great post on our site.
Keep up the good writing.
My webpage … ndis short term accommodation sta tarneit
Have you ever thought about creating an ebook or guest authoring on other sites?
I have a blog based on the same subjects you discuss and would love to have you
share some stories/information. I know my readers would appreciate your
work. If you’re even remotely interested, feel free to shoot me an e-mail.
Feel free to visit my web site :: ndis specialist disability accommodation sda
Excellent goods from you, man. I have be aware your stuff prior to and you are simply extremely excellent.
I really like what you’ve obtained right here, certainly like what you’re saying and the way through which you
say it. You are making it enjoyable and you still care
for to keep it wise. I cant wait to read far more
from you. That is actually a great website.
Feel free to visit my blog supported independent living melbourne
Your overview of preparation techniques is invaluable for anyone considering DIY painting—professional help is also available at Portland House Painters .
I need to to thank you for this good read!! I definitely
enjoyed every little bit of it. I have you bookmarked to look at
new things you post…
Tôi đã giới thiệu nhà cái dola789 cho nhiều bạn bè và họ đều thích! https://oploverz.jp.net
Các trò chơi casino trực tuyến tại Dola789 rất đa dạng và thú vị! Khuyến mại Dola789
Thanks for sharing those budget-friendly home improvement tips; they’re incredibly useful right now! More budget ideas can be found at Homepage !
This blog was… how do I say it? Relevant!! Finally I’ve
found something which helped me. Kudos!
my web site rapid discharge hospital program
Our vast range of decorating tools and supplies contain everything you
need to redecorate and maintain your home.
I enjoy reading a post that will make people think.
Also, thank you for permitting me to comment!
Here is my blog; ndis mental health support
I love incorporating smart technology into a kitchen remodel, like smart fridges and voice-activated faucets! kitchen cabinet renovation Tewksbury
Amazing blog post! Does it matter if an electrician focuses on property vs commercial work? electrical contractor dallas
Outstanding message! Understanding warranties is crucial when hiring a specialist. If you want to learn more about what to search for, see Bridgewater NJ roofing services for detailed information.
Actually enjoyed reading this short article– strong referrals all around! How do I approach scheduling with busy electrical contractors? residential electricians near me
Hello, all is going fine here and ofcourse every one
is sharing facts, that’s genuinely fine, keep up writing.
Have a look at my web site – ndis financial management
This short article really opened my eyes to the different roof products available. For anyone thinking about a roofing system upgrade, absolutely check out roofing contractor near me for experienced advice.
sex việt hot
Hello there, just became alert to your blog through Google, and found that it’s really
informative. I’m gonna watch out for brussels. I’ll be grateful
if you continue this in future. Lots of people will be benefited from your writing.
Cheers!
Its not my first time to visit this website, i am visiting this site dailly
ndis social and community participation obtain nice
information from here every day.
I feel it’s substantial for the ones struggling to recognize that they are no longer on my own; many have found out solace in a rehab centers in arizona .
Appreciate the useful tips. For more, visit tucson moving services Zooz Moving (East) .
After my recent accident, I learned that hiring an attorney is essential for navigating personal injury claims effectively! Visit Anchorage Car Accident Lawyer to connect with experts.
Tous mes remerciements vont vers chaque membre impliqué dans cette opération réussie!! # # anyKeyWord ## avis sur SP Débouchage
บทความนี้เกี่ยวกับดอกไม้งานศพ
ยอดเยี่ยมมาก
การรู้ว่าดอกไม้แต่ละชนิดมีความหมายอย่างไร ช่วยให้เลือกได้ตรงความรู้สึกมากขึ้น
จะเก็บข้อมูลนี้ไว้ใช้แน่นอน ขอบคุณอีกครั้งครับ/ค่ะ
My web site; รับจัดดอกไม้หน้าหีบ
A well-planned pantry can make all the difference in a remodeled kitchen—how big is yours? kitchen remodeling Lexington
I don’t know if it’s just me or if everyone else encountering issues with your blog.
It appears like some of the written text in your posts are running off the screen. Can someone else please
provide feedback and let me know if this is happening to them as well?
This could be a issue with my web browser because I’ve had this happen previously.
Cheers
Also visit my site – ndis support co ordination
fantastic issues altogether, you simply won a logo new reader.
What could you suggest in regards to your submit that you simply made some days in the past?
Any positive?
This page definitely has all of the info I needed about this
subject and didn’t know who to ask.
Also visit my blog; specialist disability accommodation sda
I’m impressed, I must say. Seldom do I come across a blog that’s equally educative and engaging,
and without a doubt, you’ve hit the nail on the
head. The issue is something not enough folks are speaking intelligently about.
I’m very happy that I came across this in my hunt for something
concerning this.
Here is my web blog :: disability care services
I’m impressed, I must say. Rarely do I encounter a
blog that’s both equally educative and amusing, and let me tell you,
you’ve hit the nail on the head. The issue is something too
few people are speaking intelligently about. Now i’m very
happy that I came across this in my hunt for something concerning this.
Also visit my web site :: supported independent living (sil) melbourne
Weather can really impact exterior painting. What do you all consider the best time of year for this? Check out this resource for more info: Portland Painting Contractors .
I will immediately grab your rss feed as I can not in finding
your e-mail subscription hyperlink or newsletter service.
Do you have any? Kindly allow me know so that I could subscribe.
Thanks.
Hmm it appears like your blog ate my first comment (it was super long) so I
guess I’ll just sum it up what I had written and say, I’m thoroughly enjoying your blog.
I too am an aspiring blog blogger but I’m still
new to everything. Do you have any helpful hints for rookie blog
writers? I’d definitely appreciate it.
Really enjoyed reading about all these different types of facial scrubs; I’m excited to try one from ### anykeyword|## Era Organics face scrub
Love that you highlighted community involvement in maintaining green spaces—it makes such an impact when everyone participates; learn tools available through ## west palm beach tree care
Incorporating elements reflecting personal interests hobbies passions into decor enhances connection felt amongst occupants dwelling there staying within confines feeling warmth security generated strong sense belonging cultivated through thoughtful kitchen remodel Tewksbury
Really insightful read, thanks for sharing your knowledge on this subject! What’s the normal timeline for most electrical tasks as soon as employed? electricians dallas
I had a small leak in my basement that turned into a major water damage problem. Thankfully, I found helpful resources at Servpro of Auburn that guided me through the restoration process.
I’ve been looking for a more natural approach to weight loss, so Prozenith definitely caught my eye.
The fact that it’s chemical-free is a big plus for
me. Has anyone seen real results from using it consistently?
hi!,I like your writing very so much! percentage we keep in touch more about your
article on AOL? I need a specialist in this space to
solve my problem. May be that is you! Taking a look ahead to look you.
Also visit my site sil providers near me
Awesome article! Discover more at gas engineer glasgow .
Fastidious replies in return of this difficulty with firm
arguments and explaining everything on the topic of that.
Take a look at my site :: ndis coordination services
Hello! Do you know if they make any plugins to help with Search Engine Optimization?
I’m trying to get my blog to rank for some targeted keywords but I’m not seeing
very good results. If you know of any please share.
Appreciate it!
my site :: disability support services victoria
This website truly has all the info I needed concerning this subject and didn’t know who to ask.
Really useful information here, thanks! Do you advise getting numerous quotes before choosing? best electrician arvada
I was amazed by how much my Anchorage lawyer knew about handling car accidents! Their expertise was invaluable—find them at Injury Lawyer Anchorage .
I think that everything said made a great deal of sense.
But, what about this? what if you were to create a awesome headline?
I ain’t suggesting your content isn’t good., however what if you added a post title that grabbed folk’s attention? I mean SMI diamond grinding wheels
is kinda boring. You might glance at Yahoo’s home page
and see how to choose an ndis provider
they create news headlines to get viewers to click.
You might add a video or a picture or two to get people interested about everything’ve got to say.
Just my opinion, it would make your website a little livelier.
My friend just moved into her new home with help from Zoll wood and couldn’t stop raving about them!! # # anyKeyWord # # Zellwood apartment movers
Loved your article on sustainable home improvements! For eco-friendly projects, see more at home improvement ideas .
Once all greasy hand marks and stains are gone, your walls will practically paint themselves.
Absolutely agree that aesthetics play a crucial role in attracting customers; clean windows are part of that equation too!!## anyKeyWord## window cleaning
A fascinating discussion is worth comment. I do believe that you need to publish more on this issue, it might not be a
taboo matter but generally people do not talk about these
topics. To the next! Many thanks!!
Feel free to surf to my web site :: ndis supported independent living melbourne
whoah this blog is excellent i like reading your articles.
Stay up the good work! You understand, a lot of individuals are hunting
around for this info, you can help them greatly.
The relevance of regular roofing system upkeep can not be overemphasized! I discovered some outstanding contractors at roofing contractor near me that assisted me with my roof covering assessment.
What you typed made a great deal of sense. But,
think about this, suppose you composed a catchier title? I am not saying
your content isn’t solid., however what if you added a
title that makes people desire more? I mean SMI diamond grinding wheels is kinda vanilla.
You could glance at Yahoo’s front page ndis social and community participation watch how they create
news headlines to get viewers to open the links.
You might add a video or a related picture or two to grab readers interested
about everything’ve written. Just my opinion, it might make your
posts a little bit more interesting.
It’s first-rate to look extra information approximately the advantages of rehabilitation centers in our network! online iop classes
The significance of routine roofing maintenance can not be overemphasized! I discovered some superb professionals at affordable roofing contractors near me that aided me with my roofing system examination.
We often work on high-value commercial properties and public sector dwellings, providing interior office painting as well as exterior replenishments.
I like looking through a post that will make men and women think.
Also, many thanks for allowing for me to comment!
Here is my website … ndis registered provider
Have you ever considered about including a little bit more than just your
articles? I mean, what you say is fundamental and everything.
But just imagine if you added some great visuals or videos to give your posts more,
“pop”! Your content is excellent but with images
and clips, this site could undeniably be one of the most beneficial in its
field. Superb blog!
Check out my blog post – ndis daily living support
I’m thinking about adding a wine fridge during my upcoming kitchen remodel—is it worth it? kitchen renovation Lexington
Thanks for sharing your thoughts about social and recreational support ndis home care services.
Regards
Just wanted to share my experience – after following the advice on San Marcos Servpro , we managed to avoid serious water damage during the last storm!
After experiencing water damage from a storm, I was overwhelmed. Fortunately, I discovered some invaluable advice on recovery steps at Servpro .
The importance of safety during painting can’t be overstated! Great advice and check out Portland Painting Contractors !
So happy with the results from window cleaning service ; my neighbors are asking who did the work!
Woah! I’m really loving the template/theme of this blog.
It’s simple, yet effective. A lot of times it’s
challenging to get that “perfect balance” between usability and appearance.
I must say you’ve done a awesome job with this.
Also, the blog loads extremely fast for me on Internet explorer.
Excellent Blog!
Looking forward to getting my windows cleaned—nothing beats that clear view outside after a professional job is done! gutter cleaning service
Fantastic website. Plenty of useful information here. I am sending it to several buddies ans additionally sharing in delicious.
And certainly, thanks for your sweat!
I wish I had known about the services offered by Anchorage car accident lawyers earlier! They really make a difference in your recovery process. Explore Injury Lawyer Anchorage for assistance.
Yes! Finally someone writes about anal porn.
Terrific information here! On the internet reviews can be so revealing regarding an electrician’s job ethic and high quality. electricians dallas
Mitolyn reviews consumer reports show positive feedback from users
praising its effectiveness in boosting energy and supporting
vitality. Trusted evaluations confirm Mitolyn as a
reliable supplement for enhancing overall wellness.
This is quite enlightening. Check out gas boiler service glasgow for more.
.. water restoration
Valuable information! Find more at hotel singaraja bali .
The use of metallic accents in kitchens is definitely on-trend right now—who else loves this look in their remodeled spaces? kitchen cabinet renovation Tewksbury
Got my annual gutter checkup scheduled with gutter cleaning #; they always do an excellent job.
Such a thorough checklist of suggestions! Have you found specific platforms much better for discovering qualified electricians? commercial electrician arvada
My weekends are now free thanks to mobile car detailing—a total game changer! Learn more at car detailing santa monica .
“Wishing everyone success whenever embarking upon similar ventures ahead ; may each experience yield fruitful results matched only matched dedication put forth beforeh Bakersfield auto shipping
I am sure this paragraph has touched all the internet people, its really really pleasant paragraph on building up new blog.
Thanks for the thorough analysis. More info at moving company tucson Zooz Moving (East) .
Wielbiciele dobrego jedzenia będą zachwyceni tym miejscem – больше информации auf ###anлюKеyord###!!! Restauracje
I really enjoy good wine. Doesn’t matter if it’s
dry or sweet, it just elevates any occasion. Anyone lse
herre love wine? #WineTasting
Heree is my web blog – ขายไวน์ยกลัง
Heya! I’m at work surfing around your blog from my new iphone 3gs!
Just wanted to say I love reading through your blog and look forward to all your posts!
Carry on the great work!
Preventative measures are key when it comes to water damage! I found a lot of helpful articles on this at Servpro San Marcos .
After dealing with fire damage, it’s crucial to focus on safety first! Explore safety tips and protocols at Auburn Fire Damage before starting any restoration work.
Świetna firma przeprowadzkowa w Wrocławiu! Ich doświadczenie od 2004 roku naprawdę robi różnicę. Polecam Profesjonalne przeprowadzki Wrocław .
I have been surfing online more than 3 hours nowadays, but I by no means discovered any interesting article like yours.
It’s pretty value sufficient for me. In my opinion, if all web
owners and bloggers made good content material as you did,
the net will be a lot more helpful than ever before.
I am curious to find out what blog system you are working with?
I’m experiencing some minor security problems with my latest website and I would like to find something more risk-free.
Do you have any solutions?
Czasami myślałem, że przeprowadzki są trudne, ale z nimi to prosta sprawa! Przeprowadzki Krzyki Wrocław
Great read! Don’t forget to check out residential gutter cleaning if you’re in need of gutter cleaning services!
I’ve heard that organization remedy sessions in a online iop classes can cause profound breakthroughs for people.
I’ve been using ##### naeyord#### for months now; they never disappoint me. new ipswich window cleaners
Great job discussing color psychology in home design; it’s fascinating how colors affect mood and space perception! More color tips can be explored at home remodeling services
Wszystkie składniki użyte podczas przygotowania potraw były świeże co pozytywnie wpływa na smak !!! ### an yK e yword ### best restaurant sopot
Wow, I didn’t recognize that roof covering problems might lead to larger home issues! If you need support searching for trusted professionals, I advise taking a look at roofing contractor near me .
The seasonal adjustments can actually influence roofing requirements! If any individual is searching for expert contractors to examine their roofings after wintertime, look into roofing company close to me for referrals.
Hi there, all is going nicely here and ofcourse every one is sharing information, that’s genuinely
good, keep up writing.
This was very insightful. Check out boiler for more.
Such important recommendations; they actually simplify the procedure of hiring an electrical expert– value it tremendously! Exactly how do seasonal changes influence accessibility and pricing of electric solutions? electrician dallas
This blog post has motivated me to finally tackle my old gutters—they need replacing ASAP! Additional tips await you at free gutter quote .
Hi there to every one, it’s actually a pleasant for me to visit this web page,
it consists of precious Information.
Thanks for the advice! Requesting for referrals is a have to when working with electricians. best electrician arvada
My favorite part about having clean windows is seeing everything clearly again, thanks to # # anyKeyWord# Lakeland Window Cleaning
I like the valuable information you provide on your articles.
I’ll bookmark your weblog and take a look at once more here frequently.
I’m fairly certain I will be informed plenty of new stuff right right here!
Best of luck for the following!
Back-to-back posts like yours create stronger awareness about proper property management practices!!!# # anyKeyWord# ## gutter cleaning service
Good day! This is kind of off topic but I
need some guidance from an established blog. Is it difficult to set up your own blog?
I’m not very techincal but I can figure things out pretty quick.
I’m thinking about creating my own but I’m not sure where
to begin. Do you have any points or suggestions? Thanks
Hey There. I found your blog using msn. That is a very well written article.
I will make sure to bookmark it and come back to read extra
of your useful info. Thanks for the post. I’ll certainly return.
I really enjoy good wine. From a local vimeyard or imported,
itt just elevates any occasion. Who else enjoys wine tasting?
my web site: Carlton
Cleaning up after fire damage is a challenge. I found some helpful strategies on Servpro San Marcos that made the process less daunting.
If you’re unsure whether your home has hidden water damage, consider getting a professional inspection. Resources at Auburn Fire Damage can help guide you on this!
SBOBET88… sudah lama dengar namanya. Apakah masih aktif dan terpercaya link alternatifnya?
Quick method ffor traffc fіne lookup
Szukacie miejsca na brunch? Ta restauracja nad morzem oferuje pyszne opcje śniadaniowe! śniadania sopot
Thank you so much for shedding light on this topic—I’ve found excellent services through gutter cleaning services #!
I wish I had known about the services offered by Anchorage car accident lawyers earlier! They really make a difference in your recovery process. Explore Anchorage Car Accident Lawyer for assistance.
Nicely done! Find more at taxi cerca de mí .
always i used to read smaller articles that
also clear their motive, and that is also happening with this post
which I am reading now.
ขอบคุณสำหรับข้อมูลเกี่ยวกับพวงหรีดที่ชัดเจน
โดยส่วนตัวเพิ่งมีญาติจากไป การเลือกช่อดอกไม้เลยเป็นเรื่องที่ต้องใส่ใจ
ใครที่กำลังเตรียมตัวจัดงานศพให้คนสำคัญควรอ่านจริงๆ
My webpage: ราคาจัดดอกไม้งานศพ
Every homeowner should read this before attempting DIY window cleaning—sometimes it’s better left to the experts like Lakeland Window Cleaning!! Lakeland Window Cleaning .
A big shout-out goes out to # # AnykeyWord – they transformed my home completely! gutter cleaning service
Thomo có nhiều trận đấu kịch tính, tôi không thể rời mắt khỏi màn hình! https://medievalart.uk.com
Great tips on home maintenance! I always rely on commercial gutter repair for affordable gutter cleaning in Limerick.
Nicely done! Discover more at D kailash retreat .
.Fortunately we remembered our contacts when disaster struck; couldn’t be happier we called ###for help during those tough times!!! Water restoration Denver CO
If you’re searching for the best movers in Valencia, look no further than Valencia moving companies .
I had no idea how much debris was in my gutters until I hired residential gutter cleaning #—worth every penny!
The emotional recovery from fire damage is just as important as the physical repairs. Thank you, San Marcos Servpro , for addressing this often-neglected aspect.
What a great read! I’ve been looking into different Tampa auto shippers and will definitely look at the options provided by Tampa car transportation services .
Appreciate the comprehensive insights. For more, visit boiler service glasgow .
If you’re unsure whether your home has hidden water damage, consider getting a professional inspection. Resources at Servpro of Auburn can help guide you on this!
TextAlignment=”Justify”“Bridging emotional gaps with cure can cause profound changes within any rehab software introduced by using nice facilities like #].” Virtual IOP
The support from my Anchorage car accident lawyer was incredible during such a stressful time! For more information, visit Anchorage Car Accident Lawyer today!
Quality content is the important to be a focus for the people
to pay a visit the web page, that’s what this website is providing.
Every weekend i used to visit this web site, for the reason that i wish for enjoyment, since this this web page conations in fact good funny material too.
Nicely done! Find more at movers in tucson az Zooz Moving (East) .
Really liked your take on creating cozy reading nooks; they’re essential in any home library or living area! Find more cozy ideas at tips for home improvement
Paxos Electric Company offers the best industrial electrician services in Wharton.
I’ve always had a positive experience with Paxos Electric Company.
Paxos Electric Company is my go-to for industrial electricians in Wharton Industrial electrical safety inspections
This blog is such a treasure trove of knowledge—I’m looking forward to implementing these new strategies soon!! # # anykeyword###”. window cleaning service
Highly Recommend: I can’t recommend Tampa Bay Pressure Washing enough! If you’re looking for a reliable and effective pressure washing service in the area, look no further than these amazing professionals. You won’t be disappointed! home pressure washing near me
A clean gutter can make all the difference in preventing mold and mildew issues in your home—thanks, gutter cleaning company !
The best decision I made during my move to Clearwater was hiring Best Clearwater movers for assistance.
Your insights about insurance coverage with Clearwater auto transport services are invaluable! Clearwater vehicle shipping
Sweet blog! I found it while browsing on Yahoo News. Do you have any suggestions on how to get listed in Yahoo News?
I’ve been trying for a while but I never seem to get there!
Appreciate it
I appreciated this post. Check out loan agency new orleans for more.
Very rapidly this website will be famous among all blogging and site-building visitors,
due to it’s fastidious articles or reviews
Also visit my homepage … zepelin01
I found Best Rate Roofing through a friend’s recommendation, and they didn’t disappoint! roof leak repair
Appreciate the detailed post. Find more at car rental toronto .
It is not my first time to go to see this website, i am visiting this web site dailly and obtain fastidious information from here everyday.
https://hongkongdraw.today/
We rented a stunning castle bounce house from snow cone machine rentals near me , and it made our event magical!
Just dealt with a leaky roof and water damage—thankfully, I found some excellent restoration companies through Servpro !
Tôi đã tham gia vào một giải đấu trên https://nohu-thanba.vip và cảm thấy rất phấn khích!
After dealing with fire damage, it’s crucial to focus on safety first! Explore safety tips and protocols at Servpro of Auburn before starting any restoration work.
The convenience of having someone come to you for car detailing is unbeatable! Explore options at exterior detailing service .
It’s surprising how many people don’t realize they need a lawyer after a car accident. If you’re in Anchorage, make sure to connect with professionals through Anchorage Car Accident Lawyer .
This is such an important reminder! If you’re in need of help, don’t hesitate to contact affordable gutter cleaning .
If you’re considering hiring someone, read reviews and tips at window cleaning first.
Spring cleaning isn’t complete without clean windows! Thanks to gutter cleaning service for the fantastic job!
Paxos Electric Company offers the best industrial electrician services in Wharton.
I’ve always had a positive experience with Paxos Electric Company.
Paxos Electric Company is my go-to for industrial electricians in Wharton Industrial electrical installations Wharton
I enjoyed this post. For additional info, visit boiler installation glasgow .
Ortodoncja w Poznaniu to temat na czasie, a Gabinet stomatologiczny Posnania wydaje się być świetnym wyborem.
Hannah Schweickert never thought a common medication for ADHD
would leave her numb from her face to her toes, at times unable to walk.
Schweickert, from Indiana, has had attention deficit hyperactivity disorder
since she was young. Doctors had prescribed
her the popular drug Adderall, a stimulant taken by 16million Americans known to
improve focus, attention, and impulse control.
She started on a low dose, standard practice doctors follow to minimize side effects, which can include insomnia, increased
heart rate, anxiety, mood swings, and jitteriness.
When she showed no improvement, doctors increased the dosage, first to 15mg, then to 20mg, 30mg, and, finally, 40mg, her highest dose.
Schweickert, 25, took a 40mg tablet every day for about
two months with little incident.
But when she went on a family vacation, she began experiencing troubling symptoms
she didn’t immediately connect to the prescription stimulant.
‘I was scratching my neck and I couldn’t feel anything.
My neck had no feeling,’ she said.
That numbness spread from her neck to her fingertips,
and a week later, to her cheeks, eventually taking over her whole
body.
Hannah Schweickert, a 25-year-old with ADHD, never expected Adderall—a
common stimulant used to improve focus—to leave her body numb and her mind in panic
Back at college one night, alone in her room and unable to feel her bed underneath
her, she panicked.
‘I thought I was dying,’ she said, describing a destabilizing panic attack.
Read More
How pandemic policy fueled America’s Adderall addiction: One
in EIGHT people are on ADHD drugs after prescription rules were relaxed to keep people at
home during Covid
‘I immediately shot up, couldn’t breathe,
my heart was beating out of my chest.
‘I didn’t know what a panic attack was, but
that’s definitely what was happening.’
Schweickert laid in a state of panic for an hour before a friend was able to get to her.
She calmed herself, but it was far from the last panic attack that would
strike.
She said in a TikTok: ‘Then that started happening every day.
The worst one probably lasted about two hours.
‘I couldn’t walk. My friends had to carry me to pee.’
She went on to say she had gone to the emergency room for her panic attacks, a common response people
have to the sense of chest-tightening panic that mimics a heart attack, four times
over the next few months, but doctors were stumped.
Her mom then suggested something that had not occurred to Schweikert previously:
stop taking Adderall.
Starting on a low dose to avoid typical side effects like anxiety and insomnia, she instead faced an alarming reaction that spread
numbness from her toes to her face
‘At this point, I had no feeling in my entire body,’ Schweickert
said. ‘It had been 22 days with no feeling.
So all my nerves, something was wrong with them.’
Doctors would test her ability to feel touch on her arms, head,
and legs, and according to them, everything seemed
normal. She said they were not concerned and let her leave
without any answers.
So she took it upon herself to figure out what was going on.
Schweickert stopped taking her Adderall for a week,
something doctors do not generally recommend because the withdrawal symptoms can be intense,
causing depression, anxiety, headaches, muscle aches, and sleep disruptions.
But some of her numbness subsided in that time.
She continued her research, having seen a study that found rats given Adderall at high doses experienced considerable changes in their
brains.
The 2017 study, published in the journal Neuroscience Letters, studied rats given 10mg of amphetamine (a key
component of Adderall) and an antidepressant called
desipramine, which extends the stimulant’s effects.
The rats’ dopamine levels plummeted and stayed low for seven days
after a single dose. In addition to producing feelings of motivation and reward, dopamine can regulate pain and sensory signals.
But the researchers also found evidence of other neurotoxic effects in rats that could potentially explain Schweickert’s reaction.
Adderall is a powerful stimulant that alters levels of neurotransmitters in the brain to improve focus, attention, and impulse
control
The medicine starved the rats’ brain cells of their energy source within an hour,
making it impossible for nerve cells to send signals. This could lead to Schweiker’s initial feelings of having a dead limb
or tingling.
The medicine then overstimulated their brain cells by flooding the
brain with glutamate, a chemical that can be toxic in high amounts.
In humans, this could lead to hyperexcited nerves burning out, causing paralysis or numbness.
The drug also caused a chemical ‘explosion’ in the brain that wiped out the brain’s
natural defenses against antioxidants.
In humans, the destruction of the chemical in the brain that acts as a fire extinguisher against harmful substances called free radicals can cause nerve
pain and numbness, particularly in the arms and legs.
‘That’s the only thing that I found on the internet in a study that I was
like, actually this could be what’s happening to me,’ she
said.
She said she had never heard of someone having ‘allergic or neurotoxic effects’ from Adderall, but added, ‘there must be someone in the world who’s
also experienced this.’
The feeling in Schweickert’s body did not return completely,
even after six months without taking the medication.
‘[I got] really nervous that my feeling would never return,’
she said. ‘Now I can say that it has.’
When Schweickert stopped Adderall for a week—against medical advice due
to withdrawal risks like depression, fatigue, and headaches—some numbness faded.
But it took months for the numbness to subside completely
Your browser does not support iframes.
There are few studies that delve into the potential brain-poisoning effects of
stimulants, including Adderall and Ritalin.
Maria Ingalla, an Arizona-based nurse practitioner
of psychiatry, told DailyMail.com if Schweikert had taken other drugs recreationally,
their effects could have compounded Adderall’s tendency to
constrict blood vessels, thereby reducing blood flow and causing
numbness.
Ingalla said: ‘If she tried this med recently after a
psychedelic or other drugs, it wouldn’t be an unusual reaction because
of additive effects those drugs can have on vasoconstriction and the sensory systems of the brain.’
Schweickert did not say in the video whether she had been taking
any other medication or drug at that time.
Figures for the number of children taking Adderall or other ADHD medications are
hard to pin down due to differences in prescription databases,
changing trends over time (due to the Adderall shortage in 2022, for instance), state-by-state variations in reporting, and the rise of telehealth
prescriptions.
But current estimates say that around 10 percent of American children, aged two to 17, have
been diagnosed with ADHD, and 62 percent of them are being treated with medications, translating to about 4.5 million children.
IndianaTikTok
co88.org tỷ lệ cược thấp hơn nhiều nhà cái uy tín khác
Chơi bài trực tuyến trên https://gamebaihoangkim.com thật sự rất thú vị, cảm giác như đang ở casino thật.
Fire damage can be devastating, but understanding the restoration process can really help. Check out Servpro for more information on recovery options.
Hiya very nice site!! Guy .. Excellent ..
Superb .. I’ll bookmark your website and take the feeds additionally?
I’m satisfied to search out so many useful information right here within the publish, we’d like work out more techniques in this regard, thanks
for sharing. . . . . .
Gutter cleaning is one of those things that people forget about until it’s too late. Keep on top of it with local gutter cleaning services !
DIY repairs for minor water damage can save money, but make sure you know what you’re doing! Helpful guides are available at Auburn Fire Damage .
”Fantastic breakdown capturing importance pursuing effective strategies aimed improving satisfaction levels achieved thereby enhancing productivity markedly expressed openly supported visually appealing environments cherished universally encouraging window cleaning service
В этом случае надо быть осторожным, чтобы не оказаться жертвой мошеннических действий.
Cleaning up those hard-to-reach areas was no problem for these pros!!!# # anykeyword gutter cleaning service
The right lawyer can change the outcome of your case significantly after an accident. If you’re in Anchorage, consider visiting Injury Lawyer Anchorage for expert advice.
Zawsze marzyłem o pięknym uśmiechu i dzięki licówki poznań to się spełniło!
This was beautifully organized. Discover more at Farnham Dentistry .
Paxos Electric Company offers the best industrial electrician services in Wharton.
I’ve always had a positive experience with Paxos Electric Company.
Paxos Electric Company is my go-to for industrial electricians in Wharton Paxos Electric Company efficiency
Đã thử vào các bàn cược cao cấp trên https://nohuking.asia chưa? Cảm giác hồi hộp lắm đấy!
Please let me know if you’re looking for a article author for your weblog.
You have some really good posts and I think I
would be a good asset. If you ever want to take some of the load off,
I’d love to write some articles for your blog in exchange
for a link back to mine. Please send me an e-mail if interested.
Thanks!
I relish the transparency of pricing from Solar Panels maintenance Perth with regards to sun panel expertise in Perth.
Thank you for the auspicious writeup. It in fact was a amusement account it.
Look advanced to more added agreeable from you! By the way, how could we communicate?
ขอบคุณสำหรับบทความดี ๆ
ครับ ถ้าใครกำลังมองหาบริการจัดดอกไม้งานศพ ผมแนะนำลองดูร้านที่มีผลงานจริงและรีวิวดี ๆ ครับ
If you’re in need of gutter cleaning, look no further than commercial gutter cleaning ! Their team is professional and efficient.
New trends like matte finishes are becoming popular in kitchens—what’s your take on them? kitchen renovation contractors Lexington
Just had my windows cleaned for the first time by Lakeland Window Cleaning , and I’m blown away!
I appreciate your focus on customer experience and its correlation with cleanliness; fantastic points made here!!## anyKeyWord## gutter cleaning service
Fire damage can be devastating, but understanding the restoration process can really help. Check out Servpro for more information on recovery options.
Những ngày cuối tuần luôn thú vị hơn khi chơi game tại https://gamebaidoithuong88.pro !
Wybielanie zębów? To świetny sposób na poprawienie swojego uśmiechu! Polecam ###anych usługi ###anymK… klinika stomatologiczna
If you’re unsure whether your home has hidden water damage, consider getting a professional inspection. Resources at Servpro of Auburn can help guide you on this!
I found this to be quite enlightening. Learn more about oral health at Farnham Dentistry cosmetic dentistry !
I really like your blog.. very nice colors & theme.
Did you create this website yourself or did you
hire someone to do it for you? Plz answer back as I’m looking to construct my own blog and would like
to find out where u got this from. cheers
My friend had a tough time after her car accident until she hired an Anchorage lawyer. They were incredibly helpful! Learn more at Anchorage Car Accident Lawyer .
A motivating discussion is definitely worth comment.
I think that you need to publish more about this subject,
it might not be a taboo subject but usually folks don’t speak about such topics.
To the next! All the best!!
I love the idea of adding a pop of color through appliances in a remodel! What colors do you prefer? Check out ideas at kitchen cabinet remodel Tewksbury !
Love this info! For anyone searching for reliable services, look no further than professional gutter cleaning !
For newest information you have to visit world wide web and on world-wide-web I found this
website as a best site for newest updates.
Awesome article! Discover more at Tewes Design Group Architects .
Just got off the phone with my lawyer from Falk Talks Law , and they’re striving on my case! Feeling hopeful!
Paxos Electric Company offers the best industrial electrician services in Wharton.
I’ve always had a positive experience with Paxos Electric Company.
Paxos Electric Company is my go-to for industrial electricians in Wharton Wharton industrial electrical solutions
The Billionaire Brain Wave presents itself as a pioneering theta-based auditory
stimulation designed to modulate gene expression and counteract the perceived effects of a diminished
hippocampus.
um artigo realmente muito interessante . É bom quando encontramos material deste nível para leitura . Obrigado pelo artigo . Sucesso !
Ai có thể giới thiệu cho tôi một số mẹo khi chơi trên https://nohu-batbai.asia không?
“Searching for local expertise regarding commercial moves led me here; excited to learn more through ### anykeyword###.” Malabar international movers
Just moved last week with the help of Long distance movers Eaton Park – highly recommend their cheap movers!
Your article has inspired me to clean my windows more often! Thanks to Lakeland Window Cleaning for always helping me out!
The aesthetic appeal of a lush, green lawn created through hydroseeding is unreal—it transforms outdoor spaces instantly! Find inspiration and tips at Commercial hydroseeding !
Greetings from Ohio! I’m bored to death at work so I
decided to check out your website on my iphone during lunch break.
I really like the info you present here and can’t wait to take a look
when I get home. I’m amazed at how fast your blog loaded on my phone ..
I’m not even using WIFI, just 3G .. Anyways, very good blog!
Stop by my homepage: ผักไฮโดรโปนิกส์
My coder is trying to persuade me to move to .net from
PHP. I have always disliked the idea because of the
costs. But he’s tryiong none the less. I’ve
been using Movable-type on a variety of websites for about a year
and am anxious about switching to another platform.
I have heard good things about blogengine.net. Is there a way I can import all my wordpress content
into it? Any kind of help would be greatly appreciated!
Very informative read—I feel inspired to maintain my own windows better now and might call in the pros at gutter cleaning service !
This was very enlightening. More at Farnham Dentistry emergency care .
Just got my first quote for ##solar and battery packages perth## – can’t wait to see how much I can save! Solar power inverter Perth
Интересно, каковы отзывы владельцев автомобилей BYD в нашей стране? https://www.bitsdujour.com/profiles/xU8g5N
It’s incredible how much easier life gets with a competent Dade City moving company on your side! Dade City apartment movers
Protetyka stomatologiczna powinna być wykonywana przez najlepszych – znajdziecie ich w Wybielanie zębów Poznań .
This topic is often overlooked; thanks for bringing it to light! If anyone needs help, try affordable gutter cleaning !
Water damage doesn’t just ruin your property; it can also affect your health. Learn how to safeguard your home from water damage at Servpro .
Preventative measures are key when it comes to water damage! I found a lot of helpful articles on this at Servpro .
Szukam dobrego miejsca na rozpoczęcie nauki tradingu – może to będzie kurs tradingu gdańsk ?
Tôi đã tìm kiếm một thời gian dài và cuối cùng cũng tìm thấy https://gamebaithantaivip.top , cực kỳ hài lòng!
The support from my Anchorage car accident lawyer was incredible during such a stressful time! For more information, visit Injury Lawyer Anchorage today!
Chirurgia stomatologiczna nie musi budzić lęku, zwłaszcza gdy mamy do czynienia z ekspertami jak w Projektowanie uśmiechu Poznań .
Remodeling isn’t just about aesthetics but embracing practicality alongside creativity intertwined throughout each chosen element/decision made…!!!### anyKeyWord ## kitchen cabinet renovation Lexington
Clean windows can truly brighten up a room. Kudos to professional window cleaners! Lakeland Window Cleaning
Myślę, że warto spróbować swoich sił w forexie – może znajdę coś interesującego dzięki # # anyKeyWord # # ! Darmowe sygnały Forex
سامانه استعلام جو یک پلتفرم کامل برای انواع
استعلامهای آنلاین از جمله {خلافی خودرو، سوابق بیمه، خدمات بانکی، وضعیت گذرنامه و پلاک} میباشد.
How often should you get your windows cleaned? Regularly—especially with gutter cleaning on your side!
I am in fact grateful to the owner of this site who has
shared this fantastic paragraph at at this place.
This was nicely structured. Discover more at Farnham Dentistry .
Paxos Electric Company offers the best industrial electrician services in Wharton.
I’ve always had a positive experience with Paxos Electric Company.
Paxos Electric Company is my go-to for industrial electricians in Wharton Industrial electrical service provider
Tôi đã tìm kiếm một thời gian dài và cuối cùng cũng tìm thấy https://gamebaidoithecao.pro , cực kỳ hài lòng!
Good post. I learn something new and challenging
on blogs I stumbleupon everyday. It will always be interesting to read articles from other authors and use a
little something from their websites.
Mobile car detailing saved me hours this week—thank you, detailing near me !
I’m dreaming of marble countertops for my next kitchen remodel! They add such elegance! See options at kitchen cabinet renovation Tewksbury .
What’s up colleagues, how is the whole thing,
and what you desire to say concerning this post,
in my view its in fact amazing in favor of me.
Protetyka stomatologiczna jest bardzo istotna dla osób z brakami w uzębieniu. Polecam klinikę Chirurgia stomatologiczna Poznań !
Rất mong chờ những cập nhật mới từ đội ngũ phát triển của https://nohu-hoangkim.pro .
Great job! Find more at Farnham Dentistry 32223 .
Thanks for the great content. More at Cell phone lookup .
Finding the properly regularly occurring contractor might possibly be a daunting project, yet it’s worth it at long last. I located some positive recommendation on-line at Kitchen remodel that made my selection a lot more convenient!
I recently experienced water damage in San Marcos, and the cleanup process was overwhelming. I wish I had found San Marcos Servpro earlier for expert advice!
Szukając inspiracji dotyczących strategii inwestycyjnych natrafiłem również na ciekawe dane wskazane przez stronę #### anikeyword ### Stacjonarny kurs tradingu
If you want reliable yet cheap mover options check out # # anyKeywords#. You won’t regret it! Lake Mary apartment movers
I’ve seen some stunning transformations thanks to hydroseeding in community parks—such an effective method! More information available at Commercial hydroseeding .
I wish I had known about professional movers in Odessa earlier! It would have made my last move so much easier! Odessa international movers
Thanks for highlighting the importance of print marketing! My favorite place to print is Print Design Services Lexington .
It’s very good how a positive frequent contractor can radically change a space! I lately performed a mission and could not be happier. For everybody attracted to learning more, I suggest visiting experienced general contractor licensed for useful insights.
Paxos Electric Company offers the best industrial electrician services in Wharton.
I’ve always had a positive experience with Paxos Electric Company.
Paxos Electric Company is my go-to for industrial electricians in Wharton Paxos Electric Company in Wharton
Thanks in favor of sharing such a fastidious thinking, post is
nice, thats why i have read it fully
What’s Happening i’m new to this, I stumbled upon this I have found It
positively helpful and it has helped me out loads.
I hope to contribute & help other customers like its helped me.
Great job.
Очень рад видеть развитие электромобильной инфраструктуры в Узбекистане благодаря такой компании как BYD! https://www.pexels.com/@trevor-young-2152833388/
Good day! This is kind of off topic but I need some
help from an established blog. Is it tough to
set up your own blog? I’m not very techincal but I can figure things out pretty quick.
I’m thinking about setting up my own but I’m not sure where to start.
Do you have any tips or suggestions? Cheers
I’ve considered firsthand how a whole lot difference a expert widely used contractor makes in production projects. For a person needing greater info in this subject, you should always sincerely consult with bathroom renovation cost !
This was a great article. Check out Farnham Dentistry Jacksonville dentist for more.
This was very beneficial. For more, visit how to get free spins slot .
Mercer Island is truly a hidden gem for outdoor living spaces! The stunning views and natural beauty make it the perfect place to create a cozy patio or a luxurious deck Remodel Company
My experience with #### anykeyword ### has been nothing short of fantastic—thank you! new ipswich window cleaning business
Appreciate the recommendation. Let me try it out.
Thank you for spreading focus approximately the hazards of neglecting mildew problems; it’s widespread that we’ve got pros like VetCor possible in the neighborhood in Sarasota! Mold Mitigation
Great post. I’m dealing with some of these issues as
well..
I learned a lot about packing from my current experience with a moving company. If you want to know more about packaging techniques, head over to movers near me !
Exceptional read! I’ve discovered so much about roof care and upkeep from your blog site. It’s vital understanding for every homeowner! roof repair
Paxos Electric Company offers the best industrial electrician services in Wharton.
I’ve always had a positive experience with Paxos Electric Company.
Paxos Electric Company is my go-to for industrial electricians in Wharton Industrial electrical troubleshooting
I’ve had a first-class event operating with a overall contractor for my homestead upkeep bathroom renovation cost
Great information on marketing materials! I always rely on Print Design Services Lexington for high-quality brochures.
My partner and I stumbled over here from a different website and thought I might check things out.
I like what I see so now i am following you.
Look forward to exploring your web page repeatedly.
This is wonderfully detailed. Check out Farnham Dentistry cosmetic dentistry for more on teeth whitening!
I’ve had a vast feel running with a typical contractor for my domestic protection. They basically recognize the right way to carry tips to existence! If you might be searching out tricks, examine out affordable remodel kitchen designs for some large tools.
For most recent news you have to visit web and on internet
I found this web site as a most excellent site for latest updates.
After looking over a number of the blog articles on your web site, I really like your way of blogging. I book-marked it to my bookmark website list and will be checking back in the near future. Please check out my web site as well and tell me your opinion.
my page https://www.uniformfactory.ae/laundry-bags.html
Hello There. I found your weblog the usage of msn. This is
an extremely well written article. I will make sure to bookmark
it and return to read extra of your useful info. Thank you for the post.
I’ll definitely return.
If you’re considering a kitchen remodel in Bellevue, it’s essential to find the right contractors who can bring your vision to life Mercer Island Home Remodel
This was quite useful. For more, visit ferretería .
Paxos Electric Company offers the best industrial electrician services in Wharton.
I’ve always had a positive experience with Paxos Electric Company.
Paxos Electric Company is my go-to for industrial electricians in Wharton Paxos Electric Company trusted provider
I love how tree trimming not only keeps trees healthy but also improves curb appeal. For more info, visit tree services .
Вижу, что у официального дилера BYD много положительных отзывов от клиентов. https://orcid.org/0009-0004-5459-1333
Thanks for sharing your expertise on virtual tours; they’re becoming increasingly important in the market! real estate photographer
How long does it take for hydroseeded lawns to establish? I’m eager to start my project soon! Find out more at Commercial hydroseeding .
This was very enlightening. More at Farnham Dentistry 32223 .
Appreciate the detailed post. Find more at Phone directory search .
Appreciation to my father who told me about this website, this web site is actually awesome.
http://w5.putritogeljitu.buzz/
Generally I don’t learn post on blogs, however I would like to say that this
write-up very pressured me to take a look at and do it!
Your writing style has been surprised me. Thank you, quite nice post.
Excellent ideas on roofing system upkeep! It’s so crucial to remain ahead of possible concerns. I just recently needed to handle a leak; it was a real headache! roof repair near me
Moving can be so difficult! I discovered a great moving company that made whatever easier. For more insights on picking the best movers, see moving company near me .
Hey, I think your blog might be having browser compatibility issues.
When I look at your website in Firefox, it looks fine but when opening in Internet Explorer, it
has some overlapping. I just wanted to give you a
quick heads up! Other then that, terrific blog!
great publish, very informative. I wonder why the other specialists of this sector don’t understand this.
You must proceed your writing. I am confident, you’ve a great
readers’ base already!
Very good write-up. I certainly love this website.
Continue the good work!
For a person planning a vacation, I highly counsel shopping into MasterKey Vacation Rentals. The number and satisfactory of their homes are good! property management vacation rentals florida
It’s special how an incredible customary contractor can remodel a area! I currently finished a venture and could not be happier. For all people eager about discovering more, I endorse traveling bathroom renovation contractors for precious insights.
Thanks for the great tips. Discover more at boiler service in Glasgow .
I like exactly how limos can elevate any type of occasion! Whether it’s a wedding event or an evening out, they add a touch of luxury. Discover more tips on picking the right limo solution at San Antonio luxury vehicle rentals .
#ValueForMoney defines our experience when choosing products from ###! wholesale food distributor
Mercer Island is such a beautiful place to live, and home remodeling can truly enhance its charm! I recently completed a project that transformed my living space into a more functional and inviting area Kitchen Remodel
Normally I do not read article on blogs, however I wish to say that this write-up very forced me to
take a look at and do so! Your writing style has
been surprised me. Thanks, quite great post.
I’m considering multiple sessions of CoolSculpting—has anyone done that? Insights available at coolsculpting amarillo .
” The rise of adaptive athletics sheds light upon incredible stories showcasing resilience overcoming adversity—who inspires most?” Engage discussions centered surrounding adaptive athletics experiences here: ▲▲ anyKeyWord ▲▲!” manclub
Great job on this valuable article! It’s both engaging and informative, just what we need! More details at manclub .
I’m always on the lookout for new documentaries that inspire and educate! Any recommendations? This will blow your mind
Thanks for the informative content. More at Farnham Dentistry general dentist .
Say goodbye to stubborn fat and hello to incredible savings with the CoolSculpting deals available at best coolsculpting lubbock . Get the body you’ve always wanted!
This was highly helpful. For more, visit ferretería .
I’ve heard great things about the services provided by Keystone Heights Mover’s in Keystone Heights. Can anyone share their experience?
This was quite helpful. For more, visit play casino games .
It’s distinctive how a fantastic popular contractor can rework a space! I recently achieved a mission and couldn’t be happier. For an individual occupied with learning greater, I advocate touring kitchen renovation costs guide for effectual insights.
Coolsculpting near me has helped me achieve my body goals without any surgery or downtime. Thank you, CoolSculpting , for making it possible!
Your post highlights the importance of timely repair work. Disregarding small concerns can lead to larger, more expensive problems down the line. roof repair
I constantly thought moving would be disorderly, but my expert movers altered that point of view. For suggestions on how to find trustworthy moving business, check out movers near me !
Uncertain what impact regular check-ups could yield long term yet eager explore possibilities presented alongside trusted professionals guiding steps forward together collectively whenever possible!! ethical coolsculpting treatments el paso
Thank you for sharing your views! On another note, I have a different perspective on the content of this article that intrigues me greatly! manclub
Какой из автомобилей BYD лучше всего подходит для семейных поездок? Жду советов! https://www.pexels.com/@lydia-foggi-2152813867/
If some one wants expert view regarding blogging after that i suggest him/her to pay a visit this webpage, Keep up the pleasant work.
If you love your car, you’ll want to try mobile detailing from interior detailing service —it’s worth it!
After experiencing significant rain this season, I’m grateful we have services like ### anyKeyword### ready to assist our community! water damage restoration service near me
Valuable work is not just about money; it’s about making a difference. I appreciate this discussion! More thoughts at manclub .
You make a great point here; it definitely deserves more attention—agreeing fully! fm88
If you wish to explore new locations, I advocate utilizing MasterKey Vacation Rentals. They offer a extensive stove of residences that cater to every need! vacation rentals myrtle beach
Such great advice! Dive deeper into dental care at Farnham Dentistry Jacksonville FL .
It’s highly encouraging seeing professionals share their wisdom online—it helps demystify subjects that often feel overwhelming!” Take the next step
I recently completed a kitchen remodel on Mercer Island, and the transformation is unbelievable! It’s amazing how a new layout and updated appliances can completely change the feel of a home Kitchen Remodel
Hi there! I know this is kinda off topic however , I’d figured I’d ask.
Would you be interested in trading links or maybe guest writing
a blog article or vice-versa? My website goes over a lot
of the same subjects as yours and I feel we could greatly benefit from each other.
If you might be interested feel free to shoot me an email.
I look forward to hearing from you! Fantastic blog by the way!
I love how a established contractor can handle every part from delivery to finish. If you’re considering a undertaking, basically explore the assistance at general construction contractor license ; it has some brilliant guidelines!
I found this very helpful. For additional info, visit painter and decorator .
You hit the nail on the head regarding the need for meaningful contributions in our jobs! Check out manclub for additional thoughts.
Thanks for the helpful article. More like this at ferretería Albacete .
The information you shared is so valuable! If anyone needs assistance with insulation, I recommend checking out Tujunga Insulation Pros at Insulation contractors near me .
I can’t believe how much quieter my home is after getting insulation from Ever Therm! roof insulation
I love how hydroseeding can help with native plant restoration projects too! It’s beneficial for local ecosystems. Discover more at Lawn care services .
Thanks for the practical tips. More at Phone carrier lookup .
I like how you describe the indications of roof damage! Finding them early can make all the distinction in preventing major repairs later on. roofer
Highlighting achievements inspires admiration respect honoring accomplishments elevating st fm88
I just recently worked with a moving company for my moving, and it was such a smooth experience! If you’re trying to find trusted movers, have a look at moving company Toronto for fantastic suggestions and services.
This was very enlightening. For more, visit Glasgow heating boiler repair .
A nicely-geared up total contractor is prime to any positive undertaking. I’ve discovered much from supplies like qualified kitchen remodel contractors which have helped me for the duration of my domestic advantage ride.
Shoutout to new ipswich window cleaners for their amazing service in New Ipswich! My windows sparkle!
Don’t underestimate how much easier your life will be when you hire professionals for your next move—it made all the difference for us! Check out details at Odessa FL Mover’s .
Appreciate the insights shared here; it’s vital information that everyone should know about services like Tree Service .
Hello There. I found your blog using msn. This is an extremely well written article.
I will be sure to bookmark it and return to read more of your
useful info. Thanks for the post. I will certainly return.
Valuable work leads to sustainable careers and fulfilled lives—it’s great to see this discussed so openly here! More insights at manclub .
This was highly informative. Check out painter and decorator for more.
I learned so much about preventing water damage from reading articles linked with water damage restoration companies near me ! Highly informative for Irving residents.
Did you know that renting out a limousine can really save you cash on transportation for a team? It’s a fun and cost-effective choice! Find out even more information at San Antonio luxury vehicle rentals .
Интересно, каковы отзывы владельцев автомобилей BYD в нашей стране? https://www.instapaper.com/read/1812520443
I love how Bellevue is embracing smart home technology for renovations! It’s amazing to see how these innovations not only enhance the comfort and convenience of our living spaces but also improve energy efficiency Remodel Company
I found this very interesting. For more, visit traveling auto mechanic .
Traveling with pets? Many vacation rentals are pet-friendly, making it easier to bring your furry friends along! Find pet-friendly options at vacation rentals south padre island .
Hi there, after reading this amazing article i am also delighted to share my know-how here with colleagues.
I couldn’t agree more! Your analysis really highlights the importance of this topic. Get the big picture
There’s something so alluring about the idea of striking it rich with just one lucky ticket or spin on a game machine—pure magic in action! manclub
Well explained. Discover more at ferretería .
Appreciate the useful tips. For more, visit house painting .
This article has opened my eyes to new ideas! Highly rated and worth sharing—visit manclub for more!
It’s fantastic to see info on DIY roof repairs! While some tasks are safe for homeowners, others ought to certainly be left to the pros. roofer
Particularly enjoyed watching movies included within their entertainment system!!! Air Conditioning Repair in Gilbert Arizona
Thanks for one’s marvelous posting! I seriously enjoyed reading it,
you could be a great author. I will always bookmark your blog and
will often come back in the foreseeable future. I want to encourage one to continue your great writing, have
a nice weekend!
Moving is never ever easy, but the best moving company can make a world of difference. Check out important tips and recommendations at small movers near me to guarantee your move goes smoothly!
The Mitolyn supplement is designed to boost cellular energy and support
healthy mitochondrial function, helping you maintain overall vitality and stamina.
Experience renewed energy and wellness with the Mitolyn supplement.
Kto zna dobre sygnały Forex na Telegramie? Może warto spojrzeć na sygnały forex ?
This post provides a wealth of knowledge that only comes from someone deeply experienced as an expert in the field—thank you! manclub
What’s up friends, how is everything, and what you desire to say
concerning this post, in my view its actually remarkable in favor of me.
Water damage can be devastating, especially in places like Irving, TX. Have you ever faced this issue? Check out water damage restoration near me for expert help!
Thanks for the valuable article. More at house painting .
I recently completed a kitchen remodel on Mercer Island, and the transformation is unbelievable! It’s amazing how a new layout and updated appliances can completely change the feel of a home Mercer Island Home Remodel
I learned a lot from this. For more, visit ##alternator repair atlanta##.
Automobile repair technician
Thanks for the useful post. More like this at Reverse caller ID .
I appreciate your viewpoint, but I have a different perspective on the content of the article, which might lead to a richer debate! manclub
Thanks for the great explanation. Find more at emergency boiler service Glasgow .
Nothing beats the experience of staying in a local neighborhood through vacation rentals! You get to live like a local and find hidden gems. Check out the options at vacation rentals apps !
I find that discussing strategies in online forums improves my understanding of the game immensely! Engage with fellow fans on this topic at Learn the untold story !
Want to freeze away fat without freezing your wallet? Explore the cost-effective CoolSculpting treatments provided by coolsculpting near me .
”No one wants an emergency situation, but knowing expert help exists eases worries! Cheers to dedicated teams at Blocke.” Bloque Water Damage Restoration
I found this very interesting. For more, visit painter and decorator .
Thanks for the insightful write-up. More like this at advanced reverse number lookup tools .
บรรยากาศของร้าน OMG OneMoreGlass ทำให้รู้สึกเหมือนอยู่กับเพื่อนเก่าๆ เลย! ร้านอาหารสาย1 บรรยากาศดี
Don’t let excess fat hold you back! Visit the Coolsculpting providers in Midland today. CoolSculpting Midland
You’ve covered some great points about print design best practices! I always follow through with ideas from Print Design Services Lexington !
Had an emergency with my old oak tree last week – thank goodness for tree services ’s fast response!
Honestly didn’t think much could change until visiting places such as (you guessed it) ==> ## ethical coolsculpting treatments el paso
Just wanted to give a shoutout to the amazing service I received from water damage restoration companies near me during my recent water restoration needs.
This was quite informative. For more, visit ##mobile vehicle technician##.
mobile automotive technician
Mercer Island is truly a hidden gem for outdoor living spaces! The stunning views and natural beauty make it the perfect place to create a cozy patio or a luxurious deck Mercer Island Home Remodel
Does someone have facts for deciding upon the best suited ##solar power installers perth##? Solar powered EV Chargers Perth
Appreciate this post. Let me try it out.
my blog post – slot778
Appreciate the useful tips. For more, visit painting company .
บริการที่ OMG ONE MORE GLASS SAI1 ดีมากค่ะ พนักงานน่ารักและเอาใจใส่ลูกค้า ร้านอาหารสาย1 อร่อย
ชอบบรรยากาศเปิดโล่งของร้าน OMG OneMoreGlass มาก อากาศดีสุดๆ ! ร้านเหล้าสาย1 ดนตรีสด
I just recently experienced my first limousine experience, and it was fantastic! The ambiance within was impressive. For extra on how to book one, check out affordable airport pickup San Antonio .
I love how simple it’s far to publication with MasterKey Vacation Rentals! Their website online is user-pleasant, making day trip making plans a breeze. Check them out! vacation rentals pigeon forge tn
Best decision ever was hiring # 1 ! ! . pressure washing company
This is a topic which is near to my heart…
Best wishes! Exactly where are your contact details though?
If you haven’t tried mobile car detailing yet, you’re missing out! Visit interior detailing service for top-notch services.
I found this very interesting. Check out Phone directory search for more.
I can’t believe how many options there are for water slide rentals in Tampa! tent and table rental near me
Simplifying stock management is possible with help from a trusted partner like ##Best Stocktaking services Perth##. Stocktaking Perth, WA
Nice weblog right here! Also your website so much up fast!
What web host are you using? Can I get your associate
link in your host? I wish my site loaded up as quickly as yours lol
my web site slot778
For anyone needing accurate stocktaking in Brisbane, you can’t go wrong with Brisbane Stocktaking service !
Great suggestions on preventing infestations! Always check out options for rodent control near me if needed! google.com
The knowledge shared during consultations helps demystify what could otherwise be overwhelming processes !!# # anyKeyWord ## Midland CoolSculpting
Superb post however I was wondering if you could write a litte more on this topic?
I’d be very grateful if you could elaborate a little bit more.
Cheers!
Also visit my web-site; proxies
สายเหล้าต้องไม่พลาดที่ OMG OneMoreGlass นะครับ เค้ามีโปรโมชันเด็ดๆ ตลอด! ร้านเหล้าฟังเพลงสาย1
ชอบบรรยากาศเปิดโล่งของร้าน OMG OneMoreGlass มาก อากาศดีสุดๆ ! ร้านเหล้าบรรยากาศดี สาย1
This was a wonderful post. Check out painting company for more.
“There’s nothing like professional help from ###to keep your trees healthy.” Tree Service
My coder is trying to persuade me to move to .net from PHP.
I have always disliked the idea because of the costs.
But he’s tryiong none the less. I’ve been using Movable-type on a number of
websites for about a year and am nervous about switching to another platform.
I have heard fantastic things about blogengine.net.
Is there a way I can transfer all my wordpress posts into it?
Any kind of help would be really appreciated!
Need to have personal ability pole substitution expert services in Perth? Speak to Underground Cable Fault Detection Perth for knowledgeable and effective solution.
The examples you shared were very inspiring! Whenever I’m stuck, I check out what’s new at Flyer Printing Lexington .
Are you experiencing unexplained spikes for your water invoice? Let the experts at Emergency Leak Detection Perth in Perth discover the perpetrator using our finished leak detection ways.
The consciousness to element in refurbishing the used furnishings is obvious in the items I bought out of your save in Perth. Each piece has a specified allure and provides persona to my space. Thank you! Secondhand Furniture shop near me Perth
Great beat ! I would like to apprentice while you amend your website,
how could i subscribe for a blog site? The account aided me a acceptable deal.
I had been tiny bit acquainted of this your broadcast provided bright clear idea
Also visit my website :: pirot slot
For all your electric desires, no matter if or not it’s setting up, maintenance, or renovation, belif a credible Certified electrical auditor Perth who prioritizes shopper pride.
Thanks for the informative content. More at mobile mechanic service calls .
This was highly helpful. For more, visit boiler repair technicians Glasgow .
Water damage can lead to serious issues if not addressed promptly. I trust water damage restoration services near me for any needs in Irving, TX.
If you’re considering a kitchen remodel in Bellevue, it’s essential to find the right contractors who can bring your vision to life Mercer Island Home Remodel
For folks who need ##Commercial Air Conditioning Perth##, it is primary to find a visitors with journey in higher structures. Expert Air Conditioning Perth
Beat the heat this summer time that has a reverse cycle air conditioner from Expert Air Conditioning Canning Vale in Canning Vale.
Love studying about developments in #securitysystems#—thank you #AnyCompany#! Security Systems Perth near me
I didn’t realize how critical effective scheduling was until now—you’ve opened my eyes regarding working timelines effectively!! award-winning bathroom designs
Amazing hints on employee engagement! For similarly advantage in HR consulting from Perth, explore Reliable HR Consultant Perth .
I couldn’t refrain from commenting. Very well written!
Just had a big feel with plumbing installations from Mandurah Plumber —notably endorse them!
What a data of un-ambiguity and preserveness of precious experience on the
topic of unpredicted feelings.
My blog … Proxy services
As a homeowner, searching a truthful plumbing carrier is integral. Look no further than Plumber in Perth near me for all of your hot water heater upkeep and installations in Perth. They cannot disappoint!
Ready to transform your body without breaking the bank? Check out the unbeatable CoolSculpting prices provided by coolsculpting lubbock .
I’ve been exploring for a little for any high quality articles or blog posts on this sort of house .
Exploring in Yahoo I at last stumbled upon this web site.
Studying this info So i am glad to convey that I have an incredibly
just right uncanny feeling I came upon exactly what I needed.
I most indisputably will make sure to don?t put out of your mind this website and provides it a glance on a relentless basis.
Also visit my website – slot778
For top-tier air conditioning repair services in Gilbert, look no further! Everest Air LLC Air Conditioning Repair
I’m really enjoying the theme/design of your website.
Do you ever run into any web browser compatibility problems?
A number of my blog audience have complained about my site not working correctly in Explorer but looks great in Safari.
Do you have any recommendations to help fix this issue?
Look at my webpage: madrid77
Thanks for sharing those plumbing recommendations! For any person in Cloverdale, I noticeably recommend trying out Qualified Plumber Belmont for best provider.
I couldn’t refrain from commenting. Exceptionally well written!
my webpage … madrid77
ราคาที่ OMG OneMoreGlass ถือว่าคุ้มค่ามากเมื่อเทียบกับคุณภาพที่ได้รับ! ร้านชิลสาย1
ฉันรักค็อกเทลที่ OMG ONE MORE GLASS SAI1 มาก อร่อยและสดชื่นสุดๆ ร้านเหล้าสาย1 ดนตรีสด
เห็นว่า OMG OneMoreGlass มีวงดนตรีเล่นสดทุกคืน ไม่ควรพลาดเลย! ร้านอาหารสาย1 เพลงเพราะ
Removing trees can be a complex task—ensure you’re hiring experienced professionals like those at tree services .
Ready & raring go back in soon despite initially nervousness surrounding first visit beforehand!!!!! CoolSculpting Midland
Best decision ever made was choosing this place when deciding where invest energy/money towards self-care rituals—it’s truly paying off already!!# # anyKeyWord # medically supervised coolsculpting el paso
It’s fascinating how different techniques can change a project’s outcome! My first choice will always be Print Document Services Lexington .
This was a wonderful guide. Check out find information with reverse phone lookup for more.
Thanks for the nicely structured post. Find more at ##traveling auto mechanic##.
same day mobile mechanic service
The future of farming relies heavily on good partnerships with wholesale grain suppliers like wholesale food distributor .
Just had a wonderful experience with the team at water restoration near me after a storm caused some flooding at my home in Irving.
If you’re considering a kitchen remodel in Bellevue, it’s essential to find the right contractors who can bring your vision to life Mercer Island Home Remodel
รู้สึกว่าร้าน OMG OneMoreGlass มีเอกลักษณ์เฉพาะตัวจริงๆ นะครับ ร้านชิลดนตรีสดสาย 1
อยากจัดปาร์ตี้วันเกิดที่ OMG OneMoreGlass ต้องทำยังไงบ้างครับ? ผับแอนเรสเตอรองท์ ใกล้ฉัน
I enjoyed this read. For more, visit painter and decorator .
If you’re in Lodi and need construction services, I highly recommend checking out Banning Construction Inc.! on-time bathroom remodels
Does CoolSculpting really work? I’m considering a trusted clinic in Lubbock for my concerns! coolsculpting lubbock
Fantastic article! The right photo editing can really transform listings. I recommend looking into high-quality drone photography for real estate for your editing needs.
Tips on making your long-distance move smoother? Start by contacting # any Keyword #! Cheap movers Key Biscayne
Howdy! I know this is somewhat off-topic but I had to ask.
Does building a well-established blog like yours require a large amount of work?
I’m completely new to writing a blog however I do write
in my journal on a daily basis. I’d like to start a blog so I can easily share my
own experience and thoughts online. Please let me know if you have any kind of
ideas or tips for new aspiring blog owners. Thankyou!
I enjoy exactly how limos can elevate any kind of occasion! Whether it’s a wedding event or an evening out, they add a touch of deluxe. Discover a lot more tips on choosing the appropriate limo service at Caltie enterprise transportation partnerships .
Such valuable content regarding diseases affecting trees today; knowledgeable Arborists are paramount during this time! Tree Service
Whats up very cool blog!! Man .. Beautiful .. Superb .. I’ll bookmark your website and take the feeds also?
I’m glad to seek out so many useful info here within the post, we’d like develop
more strategies on this regard, thank you for sharing. .
. . . .
I love supporting local businesses like # # anyKeyWord# # while keeping my house looking sharp! gutter cleaning service
I recognize the pointers on stopping mould growth! VetCor’s advantage in Sarasota is obviously invaluable. Mold Damage Remediation
I’ve had such positive experiences every time I’ve visited American Laser Med Spa—never disappointed! authoritative coolsculpting provider el paso
Appreciate the insightful discussion. For more, visit ##diagnostic auto technician##.
mobile vehicle inspection
Hi there outstanding blog! Does running a blog like this require a massive amount
work? I have no knowledge of coding but I was hoping to start my
own blog soon. Anyhow, if you have any suggestions or
tips for new blog owners please share. I understand this is off subject nevertheless I simply needed to ask.
Thank you!
Genuinely impressed by how efficient and friendly everyone was at Long distance movers Fernandina Beach #!
It’s amazing how rapidly things can go wrong due to moisture; grateful there are professionals like Bloquele to help! google.com
Just wanted to give a shoutout to the amazing service I received from water damage restoration companies near me during my recent water restoration needs.
I savour, lead to I discovered just what I used to be looking for.
You have ended my four day lengthy hunt! God Bless you man. Have
a great day. Bye
Are you tired of feeling self-conscious about your thighs or arms? CoolSculpting clinics, including coolsculpting lubbock , can help you achieve smoother and more toned limbs.
Bulk purchasing is perfect for those who love hosting gatherings—you can never have too many snacks or drinks available! Get party planning tips over on %%yourLink%%! wholesale food distributor
The professionalism of the staff at Banning Construction Inc. is commendable! custom bathroom remodels
This was highly educational. For more, visit reverse lookup online services .
ไม่เคยผิดหวังกับการไปที่ OMG ONE MORE GLASS SAI1 เลย ทุกครั้งที่ไปสนุกมากๆ สถานที่กินเลี้ยงสาย1
세번째 강남여성전용마사지는 대한민국 여성들에게 힐링 마사지를 제공하는 고품격 출장 서비스 입니다.
다양한 분야에서 활동하는 멋진 사이트의 토닥이를
이용해보세요! 강남여성전용마사지 전문 사이트 입니다
Finding trustworthy professionals isn’t always easy but thankfullyI stumbled uponLalkeLandWindowsCleanerswho exceeded all expectations!! gutter cleaning
Yesterday, while I was at work, my sister stole my apple ipad and tested to see if it
can survive a forty foot drop, just so she can be a youtube sensation. My iPad is now broken and she has 83 views.
I know this is completely off topic but I had to share it with someone!
Hello there! Would you mind if I share your blog with my facebook group?
There’s a lot of folks that I think would really enjoy your content.
Please let me know. Many thanks
Amazing atmosphere & exceptional customer service make #AmericanLaserMedSpa## a must-visit place for beauty lovers out there!! #AnyKeyWord## Midland CoolSculpting
The convenience of not having to shave is amazing! Thank you, American Laser Med Spa, for your incredible services! leading coolsculpting services el paso
Can’t recommend Ever Therm enough if you’re looking to improve your home’s efficiency in San Fernando! expanded polystyrene
The professional team at tree services made my tree removal process stress-free – highly recommend them!
บริการของพนักงานที่ OMG OneMoreGlass เป็นกันเองสุดๆ เลยครับ! ร้านเหล้าสาย1
Well explained. Discover more at ##starter motor replacement##.
in home auto repair technician
OMG ONE MORE GLASS SAI1 เป็นร้านที่มีเครื่องดื่มหลากหลาย ครบครันสุดๆ เลยค่ะ ร้านอาหารสาย1 ฟังเพลง
CoolSculpting is a non-invasive procedure that targets and eliminates fat cells, providing you with a safe and effective way to achieve your desired body shape. Discover its benefits at coolsculpting specials near me .
Just wanted to give a shoutout to the amazing service I received from water damage restoration companies near me during my recent water restoration needs.
I’ve learned so much about the wholesale meat industry from reading your blogs! wholesale food distributor
“The professionalism displayed by everyone at Banning was fantastic—they deserve all five stars!” bathroom remodeling guarantees
I’ve been working with various companies over the years but none compare to the quality of work from Tree Service #.
I visited many web pages but the audio feature for audio songs
existing at this web site is truly wonderful.
Hoping to enhance curb appeal? Tree services can help, especially those recommended by Tree Service .
I’m always amazed by how much care they put into each treatment plan at American Laser Med Spa – El Paso—it feels so personalized and unique—find out more: reputable coolsculpting facility el paso
เห็นว่า OMG OneMoreGlass มีวงดนตรีเล่นสดทุกคืน ไม่ควรพลาดเลย! เที่ยวกลางคืนสาย1
Coolsculpting cost is a drop in the bucket compared to the long-lasting benefits it offers. Invest in yourself and experience the joy of feeling comfortable and proud of your body. CoolSculpting
“Just called a service based on recommendations from here—hope it works out!” google.com
Great job! Find more at mobile auto troubleshooting .
Say goodbye to arm flab and hello to toned definition with CoolSculpting! Learn how this groundbreaking treatment works at coolsculpting lubbock .
Spot on with this write-up, I truly feel this web site needs much
more attention. I’ll probably be returning to read more, thanks for
the advice!
Daniella Levi & Associates, P.C. truly excels as a Bronx car accident attorney. Their expertise made a significant difference in my case outcome.
If you need a Bronx car accident lawyer, I highly recommend Daniella Levi & Associates, P.C Truck accident lawyer Bronx
Calling # 任何关键字# was one of the best decisions made during our recent landscaping disaster—they are remarkable! tree services
Hello, constantly i used to check website posts here early in the break of day, for the reason that i enjoy to
gain knowledge of more and more.
The quality of work from my local mobile detailer was impressive—highly recommend visiting them at auto detailing santa monica
Daniella Levi & Associates, P.C. has the best Brooklyn car accident attorney I’ve ever worked with!
If you need a Brooklyn car accident lawyer, Daniella Levi & Associates, P.C. is the place to go Auto accident lawyer Brooklyn
I’m excited to try out some vegan recipes using only wholesale canned ingredients based on your suggestions here—thank you so much! # # anyKeyWord # # wholesale food distributor
The craftsmanship at Banning Construction Inc. is top-notch! They truly care about their projects. customer testimonials for bathroom remodels
you’re in reality a just right webmaster. The web site loading velocity is amazing.
It seems that you’re doing any distinctive trick. In addition, The contents are masterpiece.
you have performed a great task in this matter!
This was a great article. Check out auto glass charlotte for more.
If you desire to take a good deal from this article then you have
to apply these strategies to your won weblog.
The aftermath of a flood is tough; however, finding help through resources like ### anyKeyword### made all the difference for us! water damage restoration near me
Believing wholeheartedly everyone has capability unlocking fullest potentials within themselves irrespective backgrounds beholden presently especially when factoring advancements achieved pertaining modern-day solutions revolving around popularized trends premier coolsculpting clinic el paso
Potentially looking into a group package deal with friends since we all want something different done but want an enjoyable day together—I wonder if AmericaLaserMedSpa-Midland accommodates this kind of request easily? CoolSculpting
I’ve had issues with my AC not cooling properly. Any advice on what I can do before calling a technician? Air Conditioning Repair
Appreciate the insightful article. Find more at mobile mechanic multi point checkup .
This was a wonderful guide. Check out payday loans new orleans la for more.
Making connections within this community fosters growth beyond limits experienced earlier before partnering officially alongside esteemed organizations represented notably through PITCON FOODS !! ### anyKeyWord### wholesale food distributor
This was very enlightening. For more, visit auto glass charlotte .
Best wishes to **Bannning** as they continue building dreams into reality; check out what they offer through this link: ### anyLink ### bathroom remodeling experts
Priority Restoration did an amazing job with my water damage clean up near me. Highly recommend their services!
I had a fantastic experience with Priority Restoration Philadelphia Water Damage Restoration Near Me
If you live in or around New Ipswich, don’t miss out on using #### anykeyword ### for your window needs. local window cleaners
It’s interesting how much humidity contributes to mildew enlargement—thank you for highlighting how terrific this is to handle these complications, extraordinarily with specialists like VetCor round the following in Sarasota! Mold and Water Damage Specialists
Not all restoration companies are equal! My experience with water damage restoration companies near me has been fantastic during my recent flood issue.
each time i used to read smaller posts which as well clear their motive,
and that is also happening with this post which I am reading now.
Clear suggestions! For more, visit ##mobile mechanic service appointments##.
mobile auto troubleshooting
I all the time used to read article in news papers but now as I am a user of internet
thus from now I am using net for content, thanks to web.
Thanks for the valuable insights. More at ferretería Albacete .
Amazing perspective offered through personal anecdotes reflecting real-life experiences encountered navigating partnerships successfully!!! # anyKeyWord# sustainable bathroom remodeling
It’s crazy how one small crack can influence your comprehensive driving feel—thanks for the suggestions #myReplacementFrom#! charlotte auto glass
Teknik manajemen modal slot ini sangat membantu. Sekarang aku bisa
bermain lebih lama di situs slot favorit.
ลองไปนั่งดื่มชิลล์ๆ ที่ OMG ONE MORE GLASS SAI1 แล้วคุณจะหลงรักร้านนี้แน่นอน ผับ ใกล้ฉัน
Great points made about seasonal maintenance checks; I’m adding those to my calendar! Water Damage Restoration
Who knew there had been so many thoughts purchasable? Grateful that #myReplacementFrom# helped me navigate all of them. charlotte auto glass
Nice post. I was checking constantly this blog and I’m inspired!
Very helpful information specifically the remaining section 🙂 I maintain such information much.
I used to be seeking this particular information for a long time.
Thanks and best of luck.
I was wondering if you ever thought of changing the page layout of your site?
Its very well written; I love what youve got to say. But maybe you
could a little more in the way of content so people could connect with it better.
Youve got an awful lot of text for only having 1 or two pictures.
Maybe you could space it out better?
This is quite enlightening. Check out sex for more.
We’re a group of volunteers and starting a new scheme in our community.
Your web site provided us with valuable info to work on. You’ve
done an impressive job and our entire community will be grateful to you.
Does anyone have tips for maintaining plumbing systems? I’d love insights from local Watsonville experts! [Santa Cruz Plumbers]
The Villages has some amazing transport companies! I found one through the suggestions at Sunshine Auto Transport’s The Villages .
What’s the best time of year to visit Charlotte? I’m planning my next trip! charlotte auto glass
Appreciate the insightful article. Find more at ferretería Albacete .
Mice are more than just an inconvenience; they can cause real damage, too! Rodent Control Inc.
Appreciate the thorough analysis. For more, visit Pumps .
This was very insightful. Check out https://www.mediafire.com/file/a469wtkr6vtgc4r/pdf-77212-32170.pdf/file for more.
Attending comedy shows featuring local talent never fails to leave me smiling—it’s pure entertainment!!! # # anyKeyWord # charlotte auto glass
Valuable information! Discover more at same day shower installation .
Clearly presented. Discover more at drain cleaning specialists near me .
Thanks for the helpful advice. Discover more at emergency plumber near me .
Priority Restoration did an amazing job with my water damage clean up near me. Highly recommend their services!
I had a fantastic experience with Priority Restoration Philadelphia Water Damage Restoration Near Me
Appreciate the helpful advice. For more, visit phim sex hay .
It’s a pity you don’t have a donate button! I’d most certainly donate to this brilliant blog!
I guess for now i’ll settle for book-marking and adding your RSS feed to my
Google account. I look forward to new updates and will
share this site with my Facebook group. Talk soon!
Love assisting nearby companies that prioritize caliber carrier—VetCor does simply that when it comes to mold remediation! Mold Damage Remediation Sarasota
This post is actually a nice one it assists new web people, who are wishing in favor of blogging.
Recently joined yoga classes at outdoor venues—such refreshing experiences surrounded by nature!!! # # anyKeyWord # auto glass charlotte
I enjoyed this post. For additional info, visit Casino slots .
Valuable information! Discover more at https://polar-composer-b1d.notion.site/Just-How-to-stop-Clogged-Up-Drainpipes-20b9fd9914a080fba0abf1446c088836?source=copy_link .
The attention given towards safety measures left me feeling reassured throughout my journey! Everest Air LLC Air Conditioning Repair
I am curious to find out what blog platform you are utilizing?
I’m having some minor security issues with my latest site and I would like to find something more secure.
Do you have any solutions?
เยี่ยมชมร้าน OMG OneMoreGlass แล้วรู้สึกว่าสถานที่นี้คือสวรรค์ของคนรักเหล้า! ร้านอาหารสาย1
Have you seen what # # any Keyword ### has to offer? They list some of the best moving companies around Groveland! Groveland moving companies
Appreciate the thorough information. For more, visit https://atavi.com/share/xaox1fztm7ax .
Esse artigo está bem escrito! Poucos sites oferecem conteúdo tão direto sobre backlinks de qualidade. Muito bom mesmo! Já vou acompanhar o site para me manter atualizado. Material assim agrega valor. Você pretende escrever mais sobre isso? estratégia de backlinks
Thanks for the valuable insights. More at plumber charges .
Hi to all, how is everything, I think every one is getting more from
this web page, and your views are pleasant for new users.
Today, I went to the beach with my children. I found a
sea shell and gave it to my 4 year old daughter and said “You can hear the ocean if you put this to your ear.” She placed the shell to her
ear and screamed. There was a hermit crab inside and it pinched
her ear. She never wants to go back! LoL I know this is totally off topic but I
had to tell someone!
Thank you for discussing this topic openly! I hope to find more information about how effective 비아그라 구매 can be in practice.
I’m always impressed by how friendly and professional everyone at #### anykeyword ### is! local window cleaning service
This was quite informative. For more, visit https://www.livebinders.com/b/3656071?tabid=8dd759d2-9185-9ffc-1f4d-4d3b2b183668 .
Well explained. Discover more at ferretería Albacete .
Appreciate the useful tips. For more, visit toilet drainage repair .
This is highly informative. Check out phim sex hay for more.
Nicely detailed. Discover more at https://gravatar.com/knechtarpin789 .
fensterreinigung tirol
Appreciate the detailed information. For more, visit local plumbers recommended .
Well done! Find more at Underfloor heating repairs .
Thanks for the useful post. More like this at Classic slots .
Good point about how fast acting can minimize losses during a flooding event—well said! Best Water Damage Restoration in Mesa AZ
A fascinating discussion is definitely worth comment.
I believe that you need to write more about this
subject matter, it might not be a taboo subject but usually
people do not discuss such topics. To the next!
Cheers!!
Overall, I couldn’t be happier with my experience! If you’re looking to revitalize your home’s exterior, look no further than Tampa Bay Pressure Washing – you won’t be disappointed! Tampa Dumpster Rental Tampa Bay Pressure Washing
This was highly educational. More at quick plumbing leak detection .
It is the best time to make a few plans for the long run and it is time to be happy.
I’ve learn this submit and if I could I want to suggest
you few attention-grabbing things or suggestions.
Maybe you can write subsequent articles relating to this article.
I want to learn more issues approximately it!
This is nicely said! !
This was a fantastic read. Check out https://www.mapleprimes.com/users/cwrictlxyp for more.
Wonderful tips! Find more at sex .
Amazing variety of water slides in Tampa—definitely something for everyone! bounce tampa
Incredible story there. What occurred after? Take care!
You actually make it appear really easy along with your presentation but I find this topic to be really one thing that I think I would never understand.
It seems too complex and extremely large for me.
I’m taking a look ahead to your next put up, I will attempt to get the hang of it!
This was very enlightening. More at ferretería en Albacete .
Great insights! Discover more at best rated plumbers near me .
Priority Restoration did an amazing job with my water damage clean up near me. Highly recommend their services!
I had a fantastic experience with Priority Restoration Philadelphia Water Damage Restoration Near Me
Thanks for the practical tips. More at quick central heating installations .
Este post está bem escrito! É difícil encontrar detalhamento assim sobre SEO off page. Parabéns pelo trabalho! Já vou acompanhar o site para não perder nada. Material assim agrega valor. Vai ter continuação? não perca
This was a fantastic read. Check out local reliable plumbing for more.
Este conteúdo está bem escrito! Nem sempre encontramos detalhamento assim sobre link building. Muito bom mesmo! Já assinei o feed para não perder nada. Isso é o que falta na web. Já tem outros artigos sobre o tema? links de autoridade
“What an informative post! Looking forward to connecting with #](link) as we finalize our plans.” Homosassa moving company
Appreciate the useful tips. For more, visit professional plumber pricing .
This is so useful! I’ve been searching for affordable rodent control near me lately. https://www.google.com/maps/place/?q=place_id:ChIJ0cxNePoxjoARWJjAfJwU_6U
Thanks for the clear breakdown. Find more at Video slots .
This was a great article. Check out Gas safety checks for more.
Thanks for the clear advice. More at phim sex hay .
Just obtained my locks rekeyed through the mavens at Affordable Melbourne Emergency Locksmith service , and it feels monstrous to have new keys that maintain my house cozy!
Basement cleanouts in Perth allow you to reclaim necessary space and flip your basement into a functional neighborhood for garage or residing. Perth Junk Removal company
Just had a session with an really good Belmont Plumber service in Belmont—so trained and friendly!
The growth of green technology is so exciting, especially in Perth with options like ##solar panel installation perth##! Solar Panels Oakford with battery
Great submit! For anybody taking into account going eco-friendly, assess out how Solar Panels maintenance Perth can aid with least expensive suggestions for solar panels.
I enjoyed this read. For more, visit colchones Albacete .
Thanks for the valuable insights. More at https://flip.it/7yFkJJ .
Its like you read my mind! You appear to know a lot about this, like you wrote the book in it or something.
I think that you could do with some pics to drive the
message home a little bit, but instead of that, this is fantastic blog.
A fantastic read. I will definitely be back.
Appreciate the useful tips. For more, visit local leak detection experts .
This was a fantastic read. Check out local plumbers in my area for more.
Long distance movers Lecanto
Hi, I do believe this is an excellent web site.
I stumbledupon it 😉 I may revisit yet again since I saved
as a favorite it. Money and freedom is the best way to change, may you be rich and continue to guide others.
This was a great article. Check out https://atavi.com/share/xap1opz1s56ik for more.
Appreciate the comprehensive advice. For more, visit Address lookup .
Hello, its pleasant post about media print,
we all be aware of media is a fantastic source of information.
Couldn’t believe how spacious seating arrangements were throughout entire flight duration!!! Everest Air LLC Air Conditioning Repair
Well done! Find more at ferretería en Albacete .
Thanks for the useful suggestions. Discover more at underfloor heating troubleshooting .
Appreciate the detailed post. Find more at phim sex .
Great hints on roof upkeep! Keeping a easy roof is fundamental in Tacoma. Roof Cleaning Tacoma
If you are going for finest contents like I do, just visit
this website all the time because it offers quality contents, thanks
I found this very helpful. For additional info, visit Progressive slots .
Thanks for the helpful advice. Discover more at how to repair a dishwasher .
Este post está incrível! É difícil encontrar detalhamento assim sobre SEO off page. Muito bom mesmo! Já assinei o feed para não perder nada. Conteúdo assim faz diferença. Vai ter continuação? link building profissional
I found this very interesting. Check out Blocked drains for more.
I enjoyed this post. For additional info, visit plumbing and heating installations .
Este conteúdo está incrível! Poucos sites oferecem conteúdo tão direto sobre SEO off page. Muito bom mesmo! Já marquei nos favoritos para me manter atualizado. Conteúdo assim faz diferença. Vai ter continuação? informações exclusivas
Hi! Would you mind if I share your blog with my zynga group?
There’s a lot of folks that I think would really appreciate your content.
Please let me know. Thank you
It’s a pity you don’t have a donate button! I’d most certainly donate to this fantastic blog!
I guess for now i’ll settle for book-marking and adding your RSS feed to my Google account.
I look forward to brand new updates and will share this website with my Facebook
group. Talk soon!
If some one wishes expert view on the topic of blogging after that
i propose him/her to go to see this webpage, Keep
up the pleasant job.
This was quite helpful. For more, visit https://hubpages.com/@jeovisshfc .
Using 꽁머니 has changed the way I approach online gaming! Anyone else feel the same? There’s more on this topic at 꽁나라 .
Game recharges will likely be so pricey, yet ManaBuy has fullyyt changed the sport for me! Their costs are unbeatable, and I’ve never had any problems with defense or start instances Genshin game top up
Please let me know if you’re looking for a article writer for your blog.
You have some really great articles and I feel I would
be a good asset. If you ever want to take some of the load off, I’d really like to write some content for your blog in exchange for a link
back to mine. Please send me an e-mail if interested.
Regards!
Appreciate the useful tips. For more, visit phim sex hay .
This was nicely structured. Discover more at trusted appliance repair specialists .
I appreciate the detailed steps for assessing water damage in this post. google.com
If you’re looking for a reliable 슬롯사이트, I highly recommend exploring 슬롯사이트 . They have a wide variety of slots and great bonuses!
I liked this article. For additional info, visit Electricians .
Appreciate the detailed information. For more, visit same day leak detection services .
The science behind 비아그라 구매 is fascinating! It’s amazing how it helps with circulation.
Currently it looks like BlogEngine is the best blogging platform out there right now.
(from what I’ve read) Is that what you are using on your blog?
This was beautifully organized. Discover more at colchones en Albacete .
Appreciate the thorough write-up. Find more at local gas safety specialists .
Everyone loves it whenever people get together and share
thoughts. Great site, keep it up!
Appreciate the thorough write-up. Find more at Kitchen sink plumbing .
Valuable information! Discover more at Address lookup .
Thanks for your marvelous posting! I certainly enjoyed reading it,
you’re a great author. I will make sure to bookmark your blog
and will eventually come back down the road. I want
to encourage yourself to continue your great work, have a nice afternoon!
Appreciate the detailed information. For more, visit Sink leaking .
Thank you for sharing excellent informations. Your site is very cool. I’m impressed by the details that you?¦ve on this web site. It reveals how nicely you perceive this subject. Bookmarked this website page, will come back for extra articles. You, my friend, ROCK! I found just the info I already searched everywhere and simply couldn’t come across. What a great website.
Thanks for the thorough analysis. Find more at sex .
I enjoy what you guys are up too. Such clever work and coverage!
Keep up the good works guys I’ve incorporated you guys to my own blogroll.
Clearly presented. Discover more at Classic slots .
If you’re searching for trustworthy pipes services, finding a “pipes near me” alternative can save you time and trouble. It’s vital to select a regional professional that comprehends the one-of-a-kind pipes demands of your location plumber near me
Thanks for the useful suggestions. Discover more at quick gas safety checks .
“I feel much more informed about choosing a pest control company after reading your post!” Rat Control Company
Thanks for the detailed guidance. More at plumbing services .
I every time spent my half an hour to read this web site’s articles
every day along with a cup of coffee.
I enjoyed this read. For more, visit https://taplink.cc/gilliciwig .
Thanks for the detailed post. Find more at Drainage & waste pipe .
Remarkable things here. I am very satisfied to see your article.
Thank you so much and I am taking a look ahead to contact you.
Will you kindly drop me a mail?
Way cool! Some very valid points! I appreciate you penning this write-up plus the
rest of the website is very good.
Great advice on keeping your screens! I had no notion how really good steady maintenance is for door screen repair. Door Screen Repair
Fresh paint can virtually amplify your private home’s importance—thank you, Golden Touch Painting, for doing any such wonderful process on mine! External Painters
It’s shocking how a lot mould can building up over the years – thank you for bringing this drawback to easy! Pressure Washing
These are truly impressive ideas in on the topic of blogging.
You have touched some good factors here. Any way keep up wrinting.
Thanks for the clear breakdown. More info at professional plumbing companies .
Hello my loved one! I wish to say that this post is awesome,
great written and come with approximately all
important infos. I would like to see extra posts like this .
I found this very interesting. Check out https://padlet.com/bordeauxarpin681weehi/bookmarks-23s2dchns9x62rdm/wish/J24jalMDPO11Q0A1 for more.
Thanks for the valuable article. More at trusted water leak experts .
The materials you furnish are valuable! I can’t wait to be told extra from Medicare Insurance Cape Coral in Cape Coral.
Incredible points. Sound arguments. Keep up the
great effort.
Thanks for the insightful write-up. More like this at need a plumber .
Outrage porn (additionally called outrage discourse,[1] outrage media and outrage journalism)[2] is any type of media or narrative that’s designed to
use outrage to provoke strong emotional reactions for the aim of increasing audiences, whether traditional television, radio, or print media,
or in social media with elevated net visitors and on-line attention. The time period outrage porn was coined in 2009 by
political cartoonist and essayist Tim Kreider of The brand new York Times.[3][4][5][6]
This was a fantastic read. Check out Emergency boiler repairs for more.
Glad I came across this blog while looking up tips about my HVAC system—it’s crucial knowledge for surviving our summers here! Everest Air LLC Air Conditioning Repair
Roof cleansing is more commonly left out, yet it is going to save cost in the long run with the aid of combating smash! Roof Cleaning
This really hit home. Gerda Saunders’ story in The Memory Breath is both heartbreaking and incredibly powerful.
It’s rare to see such an honest, unfiltered look at dementia
from someone living through it. Her courage in sharing
the emotional and practical realities of her journey is truly inspiring—and such an important
reminder of the human side of memory loss. Thank you for
highlighting this!
co88.org hỗ trợ khách hàng rất chậm, không giải quyết vấn đề triệt để
This was highly educational. For more, visit local plumbers recommended .
Your means of explaining all in this post is in fact fastidious,
every one can easily know it, Thanks a lot.
This was very insightful. Check out 24 7 plumber in my area for more.
Great insights! Find more at https://www.mediafire.com/file/36ofefvibia0c8i/pdf-61930-92105.pdf/file .
Highly Recommended: I would wholeheartedly recommend Tampa Bay Pressure Washing to anyone looking for top-notch pressure washing services. Their commitment to quality and customer satisfaction is unmatched. pressure washing service
Great insights! Find more at Landline lookup .
Thanks for the clear breakdown. Find more at casino sin depósito 2023 .
Hi there it’s me, I am also visiting this web site on a regular basis, this site is truly nice and the visitors are truly sharing
fastidious thoughts.
Very informative article. For similar content, visit plumbing companies .
Their thorough inspection process really impressed me—thank you, Bloque Water Damage Restoration, for your diligence! https://www.google.com/maps/place/?q=place_id:ChIJPTcCRsOnK4cReE1RiQgAKB4
Do you have any video of that? I’d want to find out
more details.
Пластик – Не Целуй, Девочка Не Любя ( 2002 ) скачать песню и слушать онлайн
https://allmp3.pro/2492-plastik-ne-celuj-devochka-ne-ljubja-2002.html
Александр Сотник – Два Ангела скачать песню и слушать онлайн
https://allmp3.pro/3329-aleksandr-sotnik-dva-angela.html
Gathering friends old new alike promotes deeper understanding cultivates kindness awareness surrounding communities uplifted collectively inspiring change positively impacting lives everywhere! dual lane water slide rental
Découvrez à quoi correspond chaque indice des chasses aux trésors présents en jeu ainsi qu’une estimation de leur difficulté.
Hmm it seems like your blog ate my first comment (it was
super long) so I guess I’ll just sum it up what I had
written and say, I’m thoroughly enjoying your blog. I as well am an aspiring blog blogger but I’m
still new to the whole thing. Do you have any tips for rookie blog writers?
I’d genuinely appreciate it.
The legal landscape following a mishap can be made complex; don’t browse it alone– consult with specialists at Falk Talks Law Injury .
Nicely done! Find more at Tewes Design Group .
Он Самый feat. DiMan – Кайф скачать песню и слушать онлайн
https://allmp3.pro/2986-on-samyj-feat-diman-kajf.html
Indiboy – Девочка – Драма скачать песню и слушать онлайн
https://allmp3.pro/2965-indiboy-devochka-drama.html
Betsy feat. Мария Янковская – Сигма Бой (DJ DimixeR Remix) скачать песню и слушать онлайн
https://allmp3.pro/2911-betsy-feat-marija-jankovskaja-sigma-boj-dj-dimixer-remix.html
Đội ngũ hỗ trợ khách hàng của nhà cái az888 luôn sẵn sàng giúp đỡ mọi thắc mắc của tôi, thật tuyệt vời! Xem thêm ở az888 .
Great insights! Discover more at professional blocked manhole solution .
Hello there, I found your blog via Google even as searching for a comparable matter, your web site got here
up, it appears to be like great. I have bookmarked it in my google bookmarks.
Hello there, just was alert to your weblog thru Google,
and found that it’s really informative. I am gonna watch out for brussels.
I’ll appreciate in case you proceed this in future. Many folks will
likely be benefited out of your writing. Cheers!
Just wanted everyone reading this post know about what an amazing find##### naeyord##### is within our community!. window cleaning tips new ipswich
Khi tham gia cá cược ở house củaaz88 , tôi cảm nhận được sự công bằng và minh bạch trong từng ván chơi ! ### anyKey word### http://grasshopperfarms.io
For those who enjoy betting strategies, you’ll find plenty of resources at 온라인카지노 that can help elevate your game!
Valuable information! Find more at https://files.fm/u/c55xgs8g2z#design .
“Who knew that finding good pest control could be so easy?” Rat Control Company
Appreciate the helpful advice. For more, visit emergency drain blockage repair .
Fantastic post! Discover more at local plumber near me .
Appreciate the insightful article. Find more at https://send.now/w2ovxwloq4rq .
Appreciate the helpful advice. For more, visit trusted sink specialists .
Thanks for the thorough analysis. More info at expert 24 hour plumbing .
Scientists have proved that reading about other people’s
experiences can open you to the possibility of having
similar ones yourself and I hope that has been the case if you’ve
been reading about my spiritual journey as a medium in the Mail
over the last two days.
If so, I want you to know that to make your own connections
with the spirit world you do not need to have been born a medium
or wish to become one.
As a naval commander and aide to the most senior figure in the US military, I was rooted firmly in the earthly realm before
I began my spiritual journey.
If I can do it, so can you, and I pray that the
following lessons will help you unwrap your own intuitive ‘gifts’ – a word I’ve put
quotation marks around because such communication is actually perfectly normal.
Why? Because you and I and those no longer in a body are all
connected at the deepest level. We all have the ability to make connections
with spirit beings because we are eternal spirits ourselves.
Glittering beings of light, we are forever entwined, and that light never
goes out. I guarantee it.
I want you to know that to make your own connections with the spirit world you do not
need to have been born a medium or wish to become one, says Suzanne
Giesemann
Expect miracles
It is not mere hope that causes us to want to believe in an afterlife.
The part of you that is eternal provides an inner knowing that you
are more than the physical body.
Moments such as gazing at a majestic mountain or into the eyes
of a newborn baby reignite the awareness that you are connected to something far greater than your limited human experience.
Two critical keys to making the connection with
sentient beings in the non-physical dimensions are belief and
intention. The first step, therefore, in communicating with
loved ones who have passed is to examine your belief about your ability to do so.
Find a peaceful place where you won’t be
interrupted, sit comfortably, and get centred with a few
slow, deep breaths.
Read More
EXCLUSIVE
Signs our dead loved ones are trying to contact us: SUZANNE GIESEMANN’s story will shake any sceptic
Move awareness to the heart area – the bridge between your human nature
and your true nature. With the intention of connecting with the highest possible wisdom, dig beneath the surface of
your beliefs about life, death, and the afterlife. Ask one question at
a time, trusting that some aspect of higher consciousness with the perfect answer hears you.
If you find that some of your beliefs are
limited, set the intention to be open to all new concepts and the possibility that even if you can’t see, hear, or
touch someone that they can still exist. Be as the child and be willing to play with new ideas and
experiences.
If something doesn’t sit right in your heart, set it aside for now, but do not let fear or scepticism keep you from opening all doors to a world of pure consciousness that is ripe for exploration.
Get excited at the thought of experiencing what I call NOEs
– no-other-explanation moments. These will become ever more common as you expand your beliefs and set the intention to
experience miracles.
Automatic writing
With practice, you can take dictation from those in spirit.
Sit quietly with a pad of paper and pen and set the intention to enjoy a written conversation with someone in the non-physical realms.
Shift your awareness to the part of you beyond your story – the part of you that never
changes. Rest for a while in this state of simply being.
When you feel you have shifted to a lightly altered state, pick
up your hand and hold it gently poised over the paper.
With practice, you can take dictation from those in spirit
Invite a loved one in spirit to merge energy fields with
you. Whether or not you sense them step into awareness, greet them lovingly and write down a question to
initiate a conversation.
Listen without trying for a response. When you hear something that is an appropriate
reply, write it down, even if you think it’s your imagination.
If you are patient and committed to the practice, in time the words from spirit will flow more
fluently and produce messages and information that will convince you that the connection is real.
Psychometry
The information-laden energy that we all radiate becomes imprinted upon everything and everyone coming into contact with us.
In scientific terms, this is called entanglement,
and it is what makes the practice of psychometry
possible.
Think of a time when you sensed the energy in a confined space, for example
the sacred feeling in a church or a sterile atmosphere in a
hospital. Such attunement is a natural ability, and you can use it to tune in to
not only feelings but information from physical objects as well.
Pieces of jewellery often make excellent objects for psychometry practice
because they are more imprinted with energy.
Find a friend willing to do a fun experiment and swap watches or rings.
Sit quietly and take a few slow, deep breaths to relax.
Close your eyes as you hold the chosen object and with the sole intention of discerning information about its owner that you couldn’t possibly know, simply observe what
arises in awareness.
What thoughts pop into your mind that stand out from your normal thoughts?
What images appear on the screen of your mind’s eye that have no
reason to show up? What emotions or unexpected sensations are you aware of?
Pieces of jewellery often make excellent objects for psychometry practice because they are more imprinted with energy
Report any experiences to your partner immediately without analysing them and ask for feedback.
When done with a playful attitude, you increase the likelihood of discerning the energetic imprint on any chosen object.
You can take this exercise a step further by holding objects in antique stores and even items
in nature.
Everything carries the history of its past, so have fun discovering what trees and rocks
have to tell you about what they have witnessed over the years.
With practice, psychometry can prove to be an excellent tool for sensitising you to
the energy-information from non-physical beings.
Putting spirits to the test
Those in spirit never mind being tested. Here are several ways you can ask them
to give you evidence to help you trust what you have experienced together:
Ask them to tell you something going on with someone you know
that you can verify later with that person, such as a current event
with them or an issue they’re dealing with.
Request that the spirit being tells you a fact you don’t know, which you can confirm after the visit.
This can be about the spirit, about someone you know,
or any topic in general. This will validate their ability to give you information that is not coming
from your conscious or subconscious mind.
Hold out your hand and ask them to metaphorically put something meaningful in it.
As you make this request, an image of something resting in your hand will come to mind.
If the meaning is not immediately obvious, ask
the spirit why they gave you that object. The response may make
sense and carry a helpful message for you. If not, you
can look up the object online to see if you can connect the
dots between you, the spirit communicator, and their message.
Hold out your hand and ask those in spirit to metaphorically put
something meaningful in it
Ask them what sign they will send you in the coming days to validate the visit.
They will put something in your mind that is unusual but not impossible to encounter.
Do not try to find the sign. Allow it to reveal itself to you in a
wondrous way that makes it clear you have received your validation.
Giving credit where it’s due
The more you open to the presence of loved ones in spirit,
guides, and angels, the more you notice moments of what I call ‘set-ups’ from Spirit.
Read More
SUZANNE GIESEMANN: My daughter visited me from
the spirit world and gave me irrefutable evidence
Contemplate times when you were led to take an action that resulted in a wondrous result benefiting
you and others. Review the chain of events that
had to take place for the outcome you experienced.
Can you see invisible hands pulling strings?
When you understand that we all share one mind, you realise that the
thoughts occurring to you are not necessarily your own. Those in spirit often merge with your
mind as a way of guiding you. Such help can be as ordinary as the idea of taking a different route home, resulting in a meaningful encounter with someone in need.
Notice these set-ups and send gratitude. If you wish to be guided even more
clearly in service to the whole, raise your hands to the sky and say to Spirit:
‘Go ahead, pull my strings.’
I see you
How would your life change if you saw others soul-to-soul instead of separate
from you? The heart is the bridge between you in your human role and you, the
eternal soul. Use this connection to see beyond the stories you and those around you are living.
Set the intention to remain in soul awareness as often as you are able throughout each day.
In this heightened state of presence, pause when you interact
with others and move your awareness to the heart.
Acknowledge that you are not only human but also an eternal soul connected to all beings across time and
space.
Visualise a rainbow or a cord of white light from your heart to the
other’s heart – from your soul to theirs – and divine love flowing back and forth.
Notice how this practice changes your interpersonal relationships with family, friends, colleagues, and even strangers.
You may well find that difficulties dissolve; people are friendlier
and smile more often at you. Gifts will flow as you offer the gift of your soul’s love to
the world.
Of course, you can also do ‘The Connection Is Good’
practice while in meditation. See how much easier it is to merge and interact with higher beings when you consciously connect your soul
heart with theirs.
For an amped-up version of this practice, invite one or more people to join you in consciously connecting
soul to soul. Look into each other’s eyes, one person at a time.
As you do so, cross your hands over your heart and say
to each other: ‘I see you.’
See how much easier it is to merge and interact with higher beings when you consciously connect
your soul heart with theirs
Do not be surprised if a few tears are shed doing this powerful exercise in soul awareness.
Those are tears of Joy – liquid gratitude flowing outward from the soul
for acknowledging the presence of love.
And finally…
I hold the vision that you will enjoy your own adventures in consciousness now that you know what is possible for all of us.
I hope this has given you the tools to make the connection with any being at any level when your motive comes from the heart.
Dive in fully. If the ensuing experiences stretch your beliefs, test
them in your heart. Keep an open mind and be willing to play.
When we allow only our physical senses to determine our reality, we experience confusion, conflict, and isolation. When we make the choice to stop identifying with
our story and live from soul awareness, we no longer experience emptiness,
but a fullness that cannot be contained.
Adapted from Making The Afterlife Connection by Suzanne Giesemann (Hay
House UK, £14.99), to be published June 10.
© Suzanne Giesemann 2025. To order a copy for £13.49 (offer valid to 21/06/25; UK P&P free on offers over £25) go to website
or call 020 3176 2937.
I love how 꽁머니 allows players to try out different strategies in casino games. It’s such a fun way to learn! For more tips, visit 꽁머니 사이트 .
I appreciated this article. For more, visit Free reverse phone lookup .
Hệ thống thanh toán của nhà cái dola789 rất nhanh chóng và tiện lợi. https://frankgalarza.com
The professionalism of the team at Mansfield vehicle shippers made my vehicle shipping so much easier.
This was quite enlightening. Check out reseñas de bono de bienvenida casino for more.
This was very enlightening. For more, visit https://www.mediafire.com/file/m4esqnvxn325xar/pdf-40863-55869.pdf/file .
Esse artigo está bem escrito! Poucos sites oferecem informações tão claras sobre backlinks de qualidade. Muito bom mesmo! Já vou acompanhar o site para não perder nada. Material assim agrega valor. Vai ter continuação? informações recentes
This was quite helpful. For more, visit reliable heating installations .
This was nicely structured. Discover more at repairing taps .
Excellent blog post. I certainly love this site. Keep writing!
Stop by my blog; IPTV pas Cher
Esse artigo está bem escrito! É difícil encontrar informações tão claras sobre link building. Continue assim! Já assinei o feed para me manter atualizado. Material assim agrega valor. Vai ter continuação? acesse o artigo
Фанкфары – Ритм Внутри скачать песню и слушать онлайн
https://allmp3.pro/2893-fankfary-ritm-vnutri.html
This paragraph gives clear idea in favor of the new users of blogging, that
really how to do blogging.
My web site: Recruit construction workers fast
When I initially commented I clicked the “Notify me when new comments are added” checkbox and
now each time a comment is added I get four e-mails with the same comment.
Is there any way you can remove me from that service?
Thank you!
Would love hearing more stories shared between others having similar experiences alongside those working within this industry —feel free everyone joining this conversation below ! Especially if connected via “Long Distance Movers Piersson” !! # # Pierson commercial movers
of course like your web-site however you need to take a look at the spelling on quite a few of your posts.
A number of them are rife with spelling problems and I to find it very troublesome to
tell the reality on the other hand I’ll certainly come back again.
Check out my blog … Rénovation de toiture
Roof cleaning is one of those duties that deserve to no longer be overpassed; thanks for bringing interest to it! Roof Cleaning Tacoma
Great article! That is the type of information that are meant to be shared across the net.
Shame on the search engines for now not positioning this publish
upper! Come on over and visit my web site . Thanks
=)
Gladly recommending them as they continue making strides improving comfort levels within homes across Gilbert!!! https://www.google.com/maps/place/?q=place_id:ChIJb1Vy1kuvK4cRaZPGFQq-frA
Really glad I came across this video—Joint Genesis sounds like a thoughtful approach to joint health.
So many supplements just mask the pain, but
this one actually focuses on protecting cartilage and restoring
hydration, which is what I’ve been needing. Love that it’s
backed by science and not just hype. Definitely adding it
to my wellness list!
The section on color management was particularly enlightening! For me, it’s crucial to use Print Design Services Lexington ’s services.
Hi, the whole thing is going nicely here and ofcourse every one is
sharing facts, that’s truly excellent, keep up writing.
Helpful suggestions! For more, visit Tewes Design Group Architects .
This was quite informative. For more, visit Oil Change .
Thanks for some other informative web site.
The place else may I get that type of information written in such
a perfect way? I’ve a project that I am simply now working on, and
I’ve been at the glance out for such information.
you are actually a just right webmaster. The site loading velocity is amazing.
It sort of feels that you are doing any distinctive trick.
Moreover, The contents are masterwork. you’ve performed
a great task in this topic!
Great delivery. Sound arguments. Keep up the good spirit.
Here is my site; 해외선물 안전업체
Mình thường xuyên theo dõi các trận đấu bóng đá qua nh à c á i a z8 88 vì nó giúp mình dự đoán kết quả chính xác hơn . https://lifestyleshoes.uk.com/
Tôi thấy nhiều người nhắc đến house củaaz88 trên mạng xã hội , chắc hẳn nó đang thu hút được nhiều người chơi ! # # anyKe yword## az888
Thanks for the helpful article. More like this at Boiler repairs Leaks .
This post is so relevant for anyone living in sunny Florida—keep up the great work! Screen Repair Company
Thanks for the insightful write-up. More like this at bonos de bienvenida 2023 .
Appreciate the great suggestions. For more, visit checkatrade approved plumbers .
Love how fresh our whole space seems to be now that we had our roofs completed through these specialists; totally advise giving them a strive!! Roof Cleaning Deerfield Beach
Has every body used King of Gleam for business strain washing? Interested of their facilities for my commercial enterprise. Power Washing
Would love to listen any pointers for seasonal upkeep once you have an external paint job achieved in Cape Coral’s climate? House Painters Exterior
Appreciate the comprehensive advice. For more, visit shower drain clogged .
Very informative article. For similar content, visit Plumbing and heating .
Thanks for the practical tips. More at 24 hour emergency plumber near me .
Your special frame of mind to discussing exceptional plans plausible by means of Kneeland Medicare & Health Insurance is commendable! Medicare Insurance Agent
Spot on with this write-up, I truly feel this web site needs much more
attention. I’ll probably be returning to see more, thanks for the information!
I think the admin of this site is truly working
hard in favor of his web site, because here every material is quality based stuff.
I always advise friends to look for a reputable car accident attorney in Kennewick if they find themselves in such situations. It’s worth it! Kennewick Lawyer
Great insights! Discover more at local plumbing solutions .
Tinh thần fair play luôn được đề cao tại nhà cái Dola789, điều này khiến tôi yên tâm hơn khi chơi. dola789
Thanks for highlighting the importance of print marketing! My favorite place to print is Custom Printing Lexington .
Este conteúdo está bem escrito! É difícil encontrar conteúdo tão direto sobre link building. Muito bom mesmo! Já marquei nos favoritos para não perder nada. Material assim agrega valor. Já tem outros artigos sobre o tema? tudo sobre isso
I recently had an first rate feel with MasterKey Vacation Rentals! The property was once staggering and perfectly discovered. I relatively put forward checking them out to your next getaway! vacation rental management near me
Great job! Discover more at https://atavi.com/share/xar04yz12ndqh .
I enjoyed this read. For more, visit Taps .
Just got my windows cleaned by window cleaners and they look brand new!
I’ve heard a lot about how important mitochondrial health is,
and Mitolyn sounds like a great way to support that at the cellular level.
If it really helps boost energy and overall vitality, this could be a solid addition to my daily routine.
Excited to see how it works over time!
The ideal crash lawyer can turn a difficult circumstance right into a manageable one. Grateful for my option at Falk Talks Law !
Thanks for the insightful write-up. More like this at Tewes Design Architects .
Thanks for the great explanation. More info at cheap plumber .
Recently, I worked with a amazing widely used contractor who exceeded all my expectancies! If you choose to locate a few guidelines on hiring one, I advocate touring general contractor licensed for a few perfect content material.
Bloque Restoration’s quick response time saved my home from more extensive damage last year! Best Water Damage Restoration in Mesa AZ
Thanks for sharing your expertise on garage doors! Definitely looking forward to learning more at garage door opener repair .
I appreciated this post. Check out Oil Change for more.
Kitchen islands can be game-changers for families who love to cook together; what do you think? Ideas await at contractor for kitchen remodel Tewksbury !
Great advice on how to avoid common painting mistakes; it’s always best to consult professionals like those at Interior Painting Companies Portland !
Anyone else used local movers like Office moving companies Pierson recently? What was your experience like?
Spent hours searching for movers—finally found some great ones listed on Office moving companies Kenansville # that serve the Kenansville area.
“Choosing the right moving company is crucial; that’s why I’m leaning towards contacting Best Homosassa movers .”
I’m looking into eco-friendly roofing options after reading your blog! So many choices available now. Learn more at Professional roofers Westford MA .
I recently had a car accident and was struggling with back pain Tacoma Chiropractor
After trying quite a few recharge structures, I lastly settled on ManaBuy. Their person-friendly interface and inexpensive expenses make it a breeze to proper up my gaming bills devoid of breaking the bank comprehensive game recharge solution
Planning a romantic getaway? A vacation rental can set the perfect mood with stunning views and privacy. Look for your ideal escape at vacation rentals key west !
It is in reality a great and useful piece of info.
I’m happy that you simply shared this useful information with us.
Please keep us up to date like this. Thanks for sharing.
The benefits of professional printing are undeniable! That’s why I’m loyal to Poster Printing Lexington for all my needs.
Looking for trustworthy roofing experts? Look no further than Residential Roofing Cork !
This is highly informative. Check out cómo obtener giros gratis casino for more.
After dealing with insurance companies post-accident, I realize now how invaluable having a knowledgeable attorney is—especially in Kennewick! Kennewick Car Accident Lawyer
Austin is this type of vivid metropolis, and home improvement your property can genuinely escalate its appeal. I observed a few impressive supplies on-line that helped me due to the system. Definitely check out bathroom renovation contractors for some super principles!
I desire I had gotten in touch with a crash legal representative quicker after my occurrence. It would have conserved me a great deal of anxiety! Have a look at Falk Talks Law Injury for suggestions.
Houston has a few of the greatest places to buy engagement rings! Whether you like traditional types or even something a lot more present day, there’s undoubtedly something for everyone engagement rings houston
I’ve heard a lot about how important mitochondrial health is, and Mitolyn sounds like a great way to support
that at the cellular level. If it really helps boost
energy and overall vitality, this could be a solid addition to my daily routine.
Excited to see how it works over time!
Thanks for the informative content. More at Tewes Design Architect .
Thanks for the helpful article. More like this at Local Plumbers .
Really enjoyed this read; it’s packed with useful info about garage doors that every homeowner should know about! Heading over to garage door opener repair
Excellent points about content marketing and SEO! For further reading, visit SEO Marketing Burlington .
Appreciate the detailed insights. For more, visit https://www.instapaper.com/read/1817249137 .
Fantastic post! Discover more at General Plumber .
Appreciate your insights on keeping areas clean and pest-free—rodents are persistent and require immediate attention! google.com
you are in reality a good webmaster. The web site loading velocity is
amazing. It kind of feels that you’re doing any distinctive
trick. In addition, The contents are masterpiece. you have
done a magnificent activity on this topic!
I like the valuable info you provide in your articles. I will bookmark your
weblog and check again here regularly. I’m quite certain I will learn a lot of new stuff right here!
Best of luck for the next!
Appreciate the great suggestions. For more, visit affordable plumbers near me .
Having little ones makes cleaning a chunk of a drawback, however your facts make it much less overwhelming. I fully grasp the advice and will discover extra at Move in cleaning !
Thanks for the useful suggestions. Discover more at https://speakerdeck.com/account/edit .
This was very enlightening. For more, visit https://orcid.org/0009-0004-1712-1391 .
Great information. Lucky me I recently found your
site by chance (stumbleupon). I’ve bookmarked it for later!
This was very enlightening. For more, visit Oil Change Bonnie Lake .
This was nicely structured. Discover more at same day plumber .
Appreciate the great suggestions. For more, visit dishwasher appliance repairs .
Joint pain has been creeping up on me lately, so I’ve been searching for something that
actually supports long-term joint health—not just quick relief.
Joint Genesis sounds like it’s targeting the root of the problem, especially with hydration and cartilage support.
Definitely worth a try!
This was very enlightening. For more, visit https://padlet.com/bordeauxarpin681zmgbk/bookmarks-gi4r6lyzku2znpso/wish/YDgnZeXE7P1yQwrA .
Hey I know this is off topic but I was wondering if you knew of any widgets I could add to my blog that automatically tweet my
newest twitter updates. I’ve been looking for a plug-in like this for quite some
time and was hoping maybe you would have some experience with
something like this. Please let me know if you
run into anything. I truly enjoy reading your blog and I look forward
to your new updates.
I have been surfing online greater than three hours nowadays, yet I never discovered any attention-grabbing article like
yours. It’s beautiful price sufficient for me.
In my opinion, if all web owners and bloggers made just
right content material as you probably did, the net can be much more useful than ever before.
Just returned from a wonderful trip where we rented a cozy cabin. It made our vacation so much more enjoyable! Don’t miss out on great listings at vacation rentals corpus christi .
We stumbled over here coming from a different web address and thought I may as well check things out.
I like what I see so now i’m following you. Look forward to
looking into your web page for a second time.
Dr. Roy is the surest! He helped me get my existence back after agony an harm after a automobile twist of fate. Car accident chiropractor
A neatly-geared up commonplace contractor is vital to any positive venture. I’ve learned so much from substances like Builders that experience helped me all over my abode benefit event.
When I originally left a comment I seem to have clicked the -Notify me when new comments are added- checkbox and now each time a comment is added I recieve four emails with the exact same comment. Perhaps there is a means you are able to remove me from that service? Thanks a lot!
my blog post; https://thermalbags.ae
There’s definately a great deal to find out about this topic.
I love all of the points you’ve made.
Esse material está incrível! É difícil encontrar conteúdo tão direto sobre link building. Parabéns pelo trabalho! Já assinei o feed para me manter atualizado. Isso é o que falta na web. Você pretende escrever mais sobre isso? leia completamente
Austin’s interesting vogue in reality shines by using in house renovations. I observed some mighty innovations and notion for my assignment! Highly suggest journeying general contractor licensed should you’re looking to give a boost to your place too.
It’s a pity you don’t have a donate button! I’d without a doubt donate to this fantastic blog!
I suppose for now i’ll settle for book-marking and adding your RSS feed to
my Google account. I look forward to brand new updates and will talk about this blog with
my Facebook group. Chat soon!
Houston possesses some of the best stunning diamond engagement rings I have actually viewed. If you reside in the place and searching for that special piece, you must absolutely check out neighborhood jewelers engagement rings houston
That is a good tip especially to those new to the blogosphere.
Short but very precise information… Thanks
for sharing this one. A must read article!
Wonderful tips! Find more at same day plumber near me .
Thanks for the thorough analysis. Find more at Leak detection .
I’m looking into green roofs—how do their installation and maintenance costs compare to traditional options in Ireland? Affordable Roofing Cork
Nicely done! Find more at affordable checkatrade plumbing services .
I’ve been simply by Window and Gutter Cleaning Ninjas for years now, and they not at all disappoint! Highly recommend for roof washing! More details at Roof Cleaning Tacoma .
The allure of free money through 꽁머니 is hard to resist! What are your thoughts on this trend? Let’s discuss over at 꽁머니 사이트 .
I found this very helpful. For additional info, visit Blocked manholes .
It’s very simple to find out any topic on net as compared to textbooks, as I found this article at this web site.
I by no means learned how so much a refreshing apartment can have an effect on my temper! Thanks for sharing these suggestions on conserving a tidy space. I’ll obviously inspect out House Cleaning Service for greater proposal!
This was very enlightening. More at Drainage & waste pipe .
Vacation rentals often provide amenities that hotels simply can’t match, like kitchens and outdoor spaces. For the best choices, check out property management vacation rentals florida !
If some one desires expert view concerning running a blog afterward i
recommend him/her to visit this webpage, Keep up the pleasant work.
Appreciate the comprehensive advice. For more, visit https://025dn.mssg.me/ .
Very useful post. For similar content, visit trusted my plumber services .
Mitolyn reviews consumer reports show positive feedback from users
praising its effectiveness in boosting energy and supporting vitality.
Trusted evaluations confirm Mitolyn as a reliable supplement for enhancing overall
wellness.
Thanks for the clear breakdown. More info at https://www.mediafire.com/file/mlkwsqbywoc0zod/pdf-67644-46644.pdf/file .
This was nicely structured. Discover more at Oil Change .
Recently, I worked with a effective frequent contractor who exceeded all my expectations! If you want to discover some info on hiring one, I imply journeying general construction contractor license for some outstanding content material.
This was a wonderful guide. Check out affordable water leak repairs for more.
เยี่ยมชมร้าน OMG OneMoreGlass แล้วรู้สึกว่าสถานที่นี้คือสวรรค์ของคนรักเหล้า! เที่ยวกลางคืนสาย1
Very useful post. For similar content, visit affordable emergency plumbers .
A friend recommended visiting a Tacoma chiropractor after my back injury. Glad I found out about this through Car accident chiropractor .
Hi! Quick question that’s totally off topic. Do you know how to
make your site mobile friendly? My weblog looks weird when browsing from my iphone.
I’m trying to find a theme or plugin that might be able to resolve this problem.
If you have any recommendations, please share.
Cheers!
“This place will always be my first choice when dealing with HVAC problems.” Air Conditioning Repair
สำหรับคนรักการดื่ม ต้องไปลองที่ OMG ONE MORE GLASS SAI1 สักครั้งนะคะ ร้านอาหารสาย1 เพลงเพราะ
LIGACOR ♦️♦️ LINK LOGIN ALTERNATIF SITUS SLOT AUTO MAXWIN DIJAMIN TERPERCAYA SAAT INI YANG MENAWARKAN PLATFORM PERMAINAN YANG AMAN, TERPERCAYA, DAN INOVATIF, SERTA
BONUS MENARIK DAN LAYANAN PELANGGAN 24/7. 2024
If you’re seeking the excellent involvement ring in Houston, TX, you need to have a look at the selection offered! There are actually numerous styles and possibilities that provide for every taste engagement rings houston
Just found MasterKey Vacation Rentals, and I’m blown away through their preference! Perfect for households or couples seeking a getaway. vacation rentals austin
Appreciate the detailed information. For more, visit expert 24 7 plumbing .
Very useful post. For similar content, visit plumbers near me prices .
The residence transforming scene in Austin is prospering! I had a best suited sense with my fresh venture, and I found out so many substances online. Don’t forget to go to Kitchen remodel for greater insights on developing your dream house!
Hiring an accident legal representative has been among the very best decisions I made post-accident! They genuinely appreciate their clients at Falk Talks Law Injury .
Thanks for the thorough article. Find more at Central heating installations .
Loved your insights on how weather affects garage doors! Will definitely reach out to garage door spring replacement if any repairs are needed.
Austin’s detailed variety in truth shines simply by in domicile renovations. I found a few distinct standards and notion for my mission! Highly advise touring bathroom remodel cost in the event you’re looking to reinforce your own home too.
This was beautifully organized. Discover more at Tewes Design Group Architects .
Appreciate the great suggestions. For more, visit https://juliuszdsd650.timeforchangecounselling.com/exactly-how-to-repair-a-dripping-showerhead .
I recently had a great experience with a Kennewick Injury Lawyer who really understood my case. Don’t underestimate the value of professional legal help! Kennewick Car Accident Lawyer
Valuable information! Discover more at General Plumber .
The gaming community wants extra systems like ManaBuy that prioritize defense and affordability. I’ve had not anything yet helpful studies recharging my debts here highest rated game top-up site
Your suggestions on tackling one room at a time is so life like! I normally get crushed, yet this makes it plausible. Can’t wait to examine greater on Deep Cleaning !
Great tips! For more, visit reliable plumbers near me .
Love the emphasis on safety during repairs! Trusting Roofing Company Cork with my home.
This was highly educational. For more, visit https://www.instapaper.com/read/1818042834 .
Fantastic post! Discover more at Bonney Lake Oil Change .
Appreciate the detailed insights. For more, visit Boiler breakdowns .
Great job! Find more at Landlord certificates .
This was very enlightening. For more, visit plumbers close to me .
I’m curious about the techniques used by Tacoma chiropractors. Does Car accident chiropractor have any resources on this?
Planning a romantic getaway? A vacation rental can set the perfect mood with stunning views and privacy. Look for your ideal escape at rentals vacation near me !
Incredible points. Sound arguments. Keep up the amazing work.
Water damage doesn’t just ruin homes; it can lead to health issues too. Great reminder! Bloque Water Damage Restoration
ฉันชอบเพลงที่เล่นในร้าน OMG ONE MORE GLASS SAI1 มาก มันทำให้รู้สึกมีชีวิตชีวา ผับสาย1 รับจัดเลี้ยง
Austin’s distinguished genre clearly shines because of in domicile renovations. I discovered some extraordinary ideas and concept for my assignment! Highly advocate visiting remodeling general contractor in case you’re seeking to reinforce your own home too.
Selecting a diamond engagement band could be frustrating, yet Houston provides numerous awesome selections! I possessed a fantastic knowledge purchasing around and also ended up with a charming ring that my fiancé loves engagement rings houston
Cleaning may also be this kind of daunting activity, yet breaking it down into possible steps makes it less difficult. I located some awesome substances at Move out cleaning that incredibly helped me streamline my cleaning activities!
I found this very interesting. For more, visit urgent plumber near me .
Fantastic post! Discover more at emergency drain cleaning service .
Appreciate the thorough insights. For more, visit trusted clogged toilet specialists .
After my accident, I didn’t know where to turn until I found a great Kennewick Injury Lawyer. They guided me every step of the way! Car accident lawyer
Useful advice! For more, visit 24 hour local plumbers .
เคยไปที่ OMG OneMoreGlass แล้ว รู้สึกประทับใจในบริการและเครื่องดื่มมาก! ร้านเหล้าสาย1 เพลงมันส์
รู้สึกว่าร้าน OMG OneMoreGlass มีเอกลักษณ์เฉพาะตัวจริงๆ นะครับ ร้านฟังเพลงสาย1
This was a great article. Check out https://numberfields.asu.edu/NumberFields/show_user.php?userid=5777238 for more.
Thank you for highlighting the reward of operating with a local assurance agent in Cape Coral! Great information! Medicare Insurance Company
Helpful suggestions! For more, visit Leaking washing machines .
Thanks for the useful suggestions. Discover more at Bonney Lake Oil Change .
For an individual planning a holiday, I really endorse finding into MasterKey Vacation Rentals. The model and nice of their residences are dazzling! best vacation rental property management
Wonderful tips! Find more at https://www.anime-planet.com/users/sarrecrghv .
I found your breakdown of common misconceptions about mice infestations very helpful. https://www.google.com/maps/place/?q=place_id:ChIJ0cxNePoxjoARWJjAfJwU_6U
Appreciate the detailed post. Find more at need a plumber .
My spouse and I are planning to visit a Tacoma chiropractor soon based on your advice here, thanks, Chiropractor Tacoma !
Just wrapped up my dwelling house redesign in Austin, and I’m thrilled with the results! It’s very good how just a few differences can make one of these change bathroom reconstruction
If you are eager about a domestic redesign in Austin, easily do your study! I came across a few fine methods that helped me keep time and money. For more advice, stopover at construction contractors for specialist guidance and hints!
Customer-Centric Approach: Their customer service was outstanding! They followed up after the job to ensure I was satisfied with the results, which speaks volumes about their commitment to client happiness. How Much Does It Cost to Power Wash a House Tampa Bay Pressure Washing
Thank you for sharing this information—it’s crucial for every homeowner to know about these methods in Cork! Roofing Company Cork
I just recently received participated in Houston, and also discovering the right interaction band was actually such a momentous knowledge! The jewelry experts right here offer magnificent assortments and excellent customer support engagement rings houston
The prep paintings finished by using Golden Touch Painting become thorough, ensuring desirable results so that it will last for years to come! Exterior Painter
This was quite informative. For more, visit Jackpot Slot features .
ชอบบรรยากาศเปิดโล่งของร้าน OMG OneMoreGlass มาก อากาศดีสุดๆ ! ร้านอาหารสาย1
ร้านนี้มีพื้นที่สำหรับกลุ่มใหญ่หรือเปล่าครับ? อยากจัดงานเลี้ยงที่ OMG OneMoreGlass # #anyKeyword## ผับ ใกล้ฉัน
I liked this article. For additional info, visit professional plumber .
I love how you simplify the enrollment system for Medicare—it makes it less daunting! Medical Insurance Cape Coral
I love how passionate the community is about 롤 토토! For more in-depth discussions, head over to 롤놀이터 .
I’ve used MasterKey Vacation Rentals dissimilar occasions and have not ever been disappointed! They always have the very best locations to reside for any occasion. vacation rental property management near me
Love how informative this text is—owners want reminders like this; focused on contacting %%anyKeyword%% after reading this! Roof Cleaning Winston-Salem
It’s crucial to have representation when dealing with personal injury claims. A Kennewick Injury Lawyer can make a significant difference in your case outcome. Kennewick Car Accident Lawyer
Well explained. Discover more at Gas safety checks .
Appreciate the detailed insights. For more, visit local 24 hour plumber .
I’ve considered firsthand how a good deal difference a skilled overall contractor makes in creation tasks. For someone desiring more info in this subject, you deserve to certainly discuss with general construction contractor !
Has anyone tried using 꽁머니 for their marketing? I found some useful tips on 꽁머니 토토 !
It is not my first time to visit this web site, i am visiting this website dailly and get fastidious
facts from here all the time.
Cleaning could be one of these daunting mission, yet breaking it down into plausible steps makes it less difficult. I found a few huge tools at Move out cleaning that actual helped me streamline my cleansing regimen!
I enjoyed this article. Check out https://list.ly/i/11015072 for more.
This was highly helpful. For more, visit Oil Change .
สุดท้ายนี้ ขอบคุณร้านOMG OneMoreGlass ที่ทำให้การออกไปเที่ยวสนุกอย่างนี้นะครับ # #anyKeyword## ร้านชิลใกล้ฉัน
I enjoyed this article. Check out average toilet installation cost for more.
I appreciate how informative your posts are about Tacoma chiropractors, keep it up, Chiropractor Tacoma !
Nicely detailed. Discover more at local plumbers recommended .
Thanks for the helpful article. More like this at https://www.storeboard.com/gertruderousseau .
Great insights! Discover more at expert drain services .
This web site really has all the info I needed about this subject and didn’t know who to ask.
If you’re searching for the perfect involvement supplant Houston, TX, you have to look at the variety on call! There are actually a lot of types and possibilities that accommodate every taste engagement rings houston
I’ve been keen on a kitchen rework in Austin for ages now! It’s exciting to reflect on your complete options. If you might be searching out advice or substances, be certain to envision out bathroom renovation contractors for some significant information.
It is appropriate time to make a few plans for the longer term and it’s time to be happy.
I’ve read this submit and if I may just I desire to recommend you
few interesting issues or advice. Perhaps you could
write subsequent articles referring to this article.
I want to learn more things about it!
Thanks for the clear breakdown. More info at trusted same day plumber .
I like it when folks come together and share opinions.
Great website, stick Construction jobs with visa sponsorship UK it!
Just stumbled on MasterKey Vacation Rentals, and I’m blown away through their resolution! Perfect for families or couples in search of a getaway. vacation rental property management charleston sc
These are actually enormous ideas in on the topic of blogging.
You have touched some pleasant points here. Any way keep up wrinting.
อยากให้ทุกคนสัมผัสประสบการณ์ดีๆ ที่ OMG ONE MORE GLASS SAI1 กันนะคะ ร้านชิลดนตรีสดสาย 1
This was very enlightening. For more, visit https://hackerone.com/settings/profile/edit .
Flat roofs can be tricky when it comes to repairs. Thanks for sharing these tips! I’ll definitely keep Roof Replacement Cork in mind for my next project.
Recently, I labored with a terrific conventional contractor who passed all my expectancies! If you wish to discover some facts on hiring one, I advise visiting small bathroom remodel for some suitable content.
It’s important to know your rights after a car accident in Kennewick. A knowledgeable lawyer is essential! Kennewick Lawyer
Seasonal cleaning is so appropriate! I continually fail to remember approximately designated components unless it truly is too past due. Your checklist become top notch necessary, and I’ll be touring House Cleaning Service Irvine for greater data!
You have made some really good points there.
I looked on the web for additional information about the issue and found most people
will go along with your views on this web site.
my page: Immediate start construction jobs
Nicely detailed. Discover more at play in free play mode .
Best experience ever with air conditioning repair in Gilbert Arizona! They were prompt and professional. Air Conditioning Repair
What flooring options do you recommend for a modern kitchen remodel? contractor for kitchen remodel Lexington
Natural light is essential in any kitchen design—how have you maximized light during your remodel? kitchen remodel cost Tewksbury
Your suggestions are spot-on! I need to find an efficient emergency boiler repair Medford soon.
เห็นว่า OMG OneMoreGlass มีวงดนตรีเล่นสดทุกคืน ไม่ควรพลาดเลย! สถานที่เที่ยวกลางคืนสาย1
Appreciate the detailed information. For more, visit Oil Change .
Thanks for the practical tips. More at local blocked toilet help .
I think this is one of the most important information for me.
And i am glad reading your article. But should
remark on few general things, The site style is great, the articles is really nice : D.
Good job, cheers
Couldn’t ask better support network surrounding circumstances faced resulting aftermath stemming unfortunate events involving vehicles operated previously .. Everett Accident & Injury Clinic
Just read an article about the benefits of chiropractic care in Tacoma. Great info, Tacoma Chiropractor !
The section on color management was particularly enlightening! For me, it’s crucial to use Print Document Services Lexington ’s services.
This was a wonderful guide. Check out Blocked drains for more.
Planning a romantic getaway? A vacation rental can set the perfect mood with stunning views and privacy. Look for your ideal escape at rentals vacation caribbean !
Awesome article! Discover more at https://www.4shared.com/s/ftpjSRDO4ku .
I recently got engaged in Houston, and locating the right engagement band was such a momentous knowledge! The jewelers below offer remarkable compilations and also wonderful customer service engagement rings houston
Kitchen remodels in Austin can surely advance your private home’s worth! I just lately renovated mine and it made this type of difference. If you are searching for inspiration, talk over with home remodel for some top notch options!
Wonderful insights into the trends in home painting this year—keep it up! More tips available at Painting Companies Portland !
Hi there, all is going nicely here and ofcourse every one is sharing information, that’s truly excellent, keep up writing.
I enjoyed this read. For more, visit https://files.fm/u/vspdyf8u3a#design .
Regular preservation is prime to averting prime blank-u.s.afterward! Your insights are spot-on; I’m going to examine Deep Cleaning for ongoing cleansing thoughts.
Loved reading about the importance of backlinks in your post—so true! Discover additional strategies at Website Ranking Service Burlington .
This was a wonderful guide. Check out commercial appliance repairs for more.
Centier Bank’s mobile app is fantastic for managing my finances on the go! Has anyone else tried it? More insights at centier .
Greetings! I’ve been reading your blog for a while now and finally got the bravery to go ahead and give
you a shout out from Dallas Texas! Just wanted to tell you
keep up the excellent work!
Thanks for the useful post. More like this at affordable water leak repairs .
This is my first time pay a visit at here and i am really impressed to read everthing at one place.
I’m impressed, I have to admit. Seldom do I encounter a blog
that’s both equally educative and engaging, and without a doubt, you have hit the
nail on the head. The issue is something too few men and women are speaking intelligently about.
I am very happy that I came across this during my search for something
regarding this.
Feel free to visit my web-site: Construction jobs no experience
This article made me realize how crucial ventilation is in preventing mold and rot—very informative indeed—visit Roofing services near me for additional tips!
Love how this video breaks down the science without overcomplicating things.
Breathe sounds like a solid option for anyone looking to support lung health naturally—especially in today’s world with so much pollution in the air.”
Appreciate the detailed post. Find more at https://send.now/u4345lo830s8 .
Thanks for finally talking about > SMI diamond grinding
wheels Construction vacancies UK
This is highly informative. Check out https://www.spreaker.com/podcast/brennaujkb–6649699 for more.
”More conversations around preparedness could save countless headaches down-the-line; let us spread knowledge gained through experiences shared involving firms analogous towards what’s being discussed under terms including ‘Block’!” google.com
I currently achieved a primary redesigning assignment in Austin and could not be happier with the results! The nearby contractors have been so expert about the contemporary trends kitchen remodel ideas
An impressive share! I have just forwarded this onto a coworker
who has been conducting a little research on this.
And he in fact ordered me dinner because I discovered
it for him… lol. So let me reword this…. Thanks for the meal!!
But yeah, thanx for spending time to talk about this topic here
on your website.
my web page Construction apprenticeships
Car accidents are stressful enough without having to deal with legal issues alone. A qualified attorney can really lighten your load in Kennewick! Kennewick Lawyer
I believe this is one of the most important information for me.
And i am happy reading your article. However wanna observation on few common issues, The web site taste
is perfect, the articles is truly excellent :
D. Excellent activity, cheers
My webpage; Construction jobs with visa sponsorship UK
I relish, lead to I found just what I used to be looking for.
You’ve ended my 4 day long hunt! God Bless you man. Have
a great day. Bye
This was nicely structured. Discover more at Bonney Lake Oil Change .
This was very enlightening. For more, visit trusted leaking dishwasher repairs .
Don’t forget about ventilation when planning your dream kitchen—it’s crucial for comfort and style! Read about it at kitchen cabinet remodel Tewksbury
Love supporting local businesses that provide excellent service—check out the top-rated roofers near you via Commercial Roofing Cork
Great insights shared around collaborative efforts within teams during design processes—I’ve seen success partnering up with #I choose Print Company Lexington
Well done! Discover more at Gas safety certificates .
Whats up are using WordPress for your site platform?
I’m new to the blog world but I’m trying to get started and create my own. Do
you need any html coding expertise to make your own blog?
Any help would be really appreciated!
Here is my blog Carpentry jobs UK
This post is so informative! I appreciate the recommendations for finding quality plumbing services like emergency water heater repair Medford .
I’m consistently looking for approaches to make cleaning quicker and less difficult, and your web publication has been first-rate important! Can’t wait to explore extra recommendations on Move out cleaning .
How often should you see a chiropractor in Tacoma? I need some insight from Car accident chiropractor .
Deciding on a diamond engagement band can be frustrating, yet Houston gives numerous fantastic choices! I had a terrific knowledge buying around and ended up with an elegant ring that my fiancé enjoys engagement rings houston
Don’t underestimate the importance of chiropractic care after an accident. Visit Everett Accident & Injury Clinic and feel the difference!
Appreciate the insightful article. Find more at free slots to play online .
Great insights on the bail process! I recommend checking out bail bonds las vegas nv for more info specific to Las Vegas.
Hi there, I found your site via Google while searching for a
related topic, your web site got here up, it looks great.
I have bookmarked it in my google bookmarks.
Hello there, just became alert to your blog through Google, and found that it’s really informative.
I’m going to watch out for brussels. I will appreciate
in case you proceed this in future. A lot of other people might be benefited out of your writing.
Cheers!
My web page :: Civil engineering jobs
This was highly educational. More at affordable plumbing costs .
I really did not realize exactly how important routine plumbing system evaluations are actually! If you are actually looking for a trustworthy plumbing professional in Grande Prairie, don’t fail to remember to see TMK Plumbing Contact .
I have been surfing on-line greater than three hours these days, yet
I never discovered any attention-grabbing article like yours.
It is beautiful price enough for me. In my view, if all web owners and bloggers made good content
as you probably did, the internet will likely be a lot more useful than ever before.
Here is my blog :: Construction apprenticeships
Whoa! This blog looks just like my old one!
It’s on a completely different topic but it has pretty much the same layout and design. Superb
choice of colors!
Here is my page :: Hire construction workers UK
“Anyone have tips on what questions to ask before hiring pest control?” Rodent Control Inc.
Valuable information! Find more at plumbing contractor .
Thank you for every other wonderful article. The place else could
anybody get that kind of info Highest-Paying Construction Jobs in the UK such a perfect way of writing?
I have a presentation next week, and I am at the search for such information.
Thanks for the informative content. More at plumbing repair .
Has someone attempted DIY gutter cleansing? It’s complicated work! I opt to depart it to the pros in Earlysville—investigate out Pressure Washing for lend a hand!
This text is priceless. When can I find out more?
Wondering if anyone has feedback on the installation process for Energy Shield Insulation? How long does it take? Insulation in Canoga Park, CA
This dialogue on putting forward residential roofs is so useful—tons of americans forget about it! Find greater details at Roof Washing
Hi there! I know this is kind of off topic but I was wondering if
you knew where I could locate a captcha plugin for my comment
form? I’m using the same blog platform as yours and I’m having problems finding one?
Thanks a lot!
Just wanted to share my positive experience with ## wall insulation
Valuable information! Discover more at https://spencermutl381.lucialpiazzale.com/keeping-your-bath-drainpipe .
Thanks for the insightful write-up. More like this at Circuit boards .
I’m invariably seeking techniques to make cleaning swifter and less demanding, and your weblog has been notable necessary! Can’t wait to explore greater advice on Move in cleaning .
Please let me know if you’re looking for a writer
for your weblog. You have some really good posts and I feel
I would be a good asset. If you ever want to take some of
the load off, I’d love to write some articles for your blog
in exchange for a link back to mine. Please send me an e-mail if
interested. Thank you!
안녕하세요! 이건 좀 주제에서 벗어나지만, 물어보고 싶었습니다.
링크를 교환하거나 게스트 포스트를 작성하는 데 관심 있으신가요?
제 블로그는 당신과 같은 토픽을 다루고 있어서 서로에게 큰 도움이 될
거라고 느낍니다. 관심 있으시면 이메일을 보내주세요.
당신에게서 소식을 기다립니다! 환상적인 블로그입니다!
|
진심으로 멋진 포스트입니다! 귀하의 기사는 매우 도움이 되고, 특히 chi tiết에 대한 부분이 눈에 띄었어요.
추가적인 정보을 위해 자주 방문할게요.
앞으로도 이런 멋진 콘텐츠 부탁드려요!
감사합니다!
|
안녕! 이 블로그를 검색 중에 발견했는데, 정말 대단합니다!
귀하의 글은 вторичное жилье에 대해 깊은 통찰을 제공해요.
그런데, 사진나 비디오를 조금 더 추가하면
독자들이 더 몰입할 수 있을 것 같아요. 아이디어일 뿐이지만, 고려해 보세요!
계속 좋은 콘텐츠 기대할게요!
|
와, 이 포스트은 정말 놀라워요! SMI diamond grinding wheels에서 이렇게 유익한 정보를 찾을 줄
몰랐어요. 당신의 글쓰기 스타일이 매우 명확하고
읽기가 즐거웠어요. 질문이 있는데, Chimie 관련 추가 정보를
어디서 찾을 수 있을까요? 고맙습니다!
|
대단한 콘텐츠입니다! 이 웹사이트는 Spirit Thoughts에 대해 상세한
정보를 제공해서 정말 감동적이었어요.
다만, 페이지 로딩 속도가 조금 느린 것 같아요.
호스팅 문제인지 확인해 보시면 어떨까요?
그래도 콘텐츠는 정말 멋져요! 계속해서 기대할게요!
|
안녕! SMI diamond grinding wheels의 팬이 됐어요!
귀하의 포스트는 항상 흥미롭고.
특히 binary에 대한 분석이 정말 인상 깊었어요.
추천드리자면, 방문자와의 상호작용을 위해 댓글란에
토론 주제를 추가하면 더 활발한 커뮤니티가
될 것 같아요! 고맙습니다!
|
대단해요! 이 사이트에서 mg 5 diario precio cialis에 대해 이렇게 깊이 있는 정보를 얻을
수 있다니 믿기지 않아요. 귀하의 글은 명확하며 초보자에게도 딱이에요.
추가로 비슷한 주제의 링크를 공유해 주실 수 있나요?
앞으로도 멋진 콘텐츠 부탁드려요!
|
안녕하세요! SMI diamond grinding wheels을 친구 추천으로 알게 됐는데, 정말 멋져요!
Valencii에 대한 귀하의 포스트는 정말 도움이 됐어요.
그런데, 모바일에서 볼 때 레이아웃이 약간 어색해요.
모바일 최적화을 고려해 보시면 어떨까요?
그래도 콘텐츠는 최고예요! 고맙습니다!
|
정말 고맙습니다! SMI diamond grinding wheels의 기사는 프로코밀 처방에 대해
제가 찾던 모든 것을 제공해 줬어요.
귀하의 글은 명확하고 읽혀서 시간이 전혀 아깝지 않았어요.
궁금한 점이 있는데, 이 주제에 대해 정기적인 업데이트를 계획 중이신가요?
계속 기대할게요!
|
와우, 이 블로그는 정말 보물이에요!
programma contabilita 관련 정보를 찾다가 SMI diamond grinding wheels에 도착했는데, 기대 이상이었어요.
귀하의 콘텐츠는 정말 전문적이고. 혹시 비슷한 토픽의 커뮤니티를 추천해 주실
수 있나요? 앞으로도 좋은 콘텐츠 부탁드려요!
|
안녕! SMI diamond grinding wheels의 포스트를 읽으면서 정말 즐거웠어요.
a sildenafil la precoz eyaculación ayuda에 대한 당신의 분석은 정말 독창적이에요.
다만, 짧은 비디오 같은 시각 자료를 추가하면 더 매력적일
것 같아요. 생각해 보세요! 고맙습니다, 다음 포스트도 기대할게요!
|
멋진 웹사이트네요! гидроаппарат에 대해 이렇게 상세하고 정보를 제공하는 곳은 드물어요.
당신의 글쓰기 스타일이 정말 친근하고
계속 읽고 싶어져요. 질문이 있는데, 이 주제에 대한 세미나나 강의 계획이 있나요?
앞으로도 멋진 콘텐츠 부탁드려요!
|
안녕! SMI diamond grinding wheels을 처음 방문했는데, 정말 인상 깊어요!
310.4.112.00.06에 대한 당신의 포스트는 정말
도움이 되고. 그런데, 검색 엔진에서
이 페이지를 찾기가 조금 어려웠어요. SEO 최적화를 조금 더 강화하면 더 많은 방문자가 올 것 같아요!
감사합니다!
|
놀라워요! SMI diamond grinding wheels에서 Birmingham에 대해 이렇게 명확하고 설명한 곳은 처음이에요.
당신의 기사는 초보자도 쉽게 이해할 수 있게
쓰여 있어서 정말 감동적이었어요. 혹시 이 주제에 대한 가이드 같은 자료를 제공하시나요?
계속해서 멋진 콘텐츠 기대할게요!
|
안녕하세요! SMI diamond grinding wheels의 기사를 읽고
정말 감명받았어요. linguasphere observatory에 대한 귀하의 설명은 정말 논리적이고 이해하기 쉬웠어요.
궁금한 점이 있는데, 방문자가 직접 참여할 수 있는 퀴즈 같은 콘텐츠를 추가하면 어떨까요?
고맙습니다, 다음 포스트도 기대할게요!
|
와, SMI diamond grinding wheels은 정말 대단한 블로그네요!
100% authentic La Mer products at Lmching. 관련 정보를 찾다가 여기 왔는데, 귀하의 포스트는 정말 유익하고.
하지만, 소셜 미디어에서 이 콘텐츠를 더 적극적으로 공유하면 더 많은 사람들이 볼 수
있을 것 같아요! 앞으로도 좋은 콘텐츠 부탁드려요!
|
안녕하세요! SMI diamond grinding wheels의 포스트를 읽으며 reproscripts.com에
대해 새로운 관점를 얻었어요. 귀하의
글은 정말 유익하고. 질문이 있는데, 이 주제와
관련된 추천 도서를 알려주실 수 있나요?
감사합니다, 자주 방문할게요!
|
훌륭한 블로그입니다! задачи에 대한 귀하의 기사는 정말 인상 깊어요.
하지만, 모바일에서 볼 때 글씨 크기가 조금
작게 느껴져요. 디자인 조정을 고려해 보시면 어떨까요?
그래도 콘텐츠는 정말 멋져요! 감사합니다!
|
안녕하세요! SMI diamond grinding wheels을 동료에게 추천받아 방문했는데, 정말 놀라워요!
@da1296963에 대한 당신의 콘텐츠는 정말 흥미로워요.
아이디어로, 독자와의 상호작용을 위해 라이브 Q&A 같은 이벤트를 열어보면 어떨까요?
계속해서 멋진 콘텐츠 기대할게요!
|
대단해요! SMI diamond grinding wheels에서 демонструє에 대해 이렇게 상세한 정보를 찾을 수 있다니 놀라워요!
당신의 글은 정말 논리적이고 읽혀서 읽는 게 전혀 아깝지 않았어요.
질문이 있는데, 이 주제에 대한 웨비나 계획이
있나요? 감사합니다!
|
안녕! SMI diamond grinding wheels의 포스트를 읽고 del similares precio sildenafil en farmacias에 대해 많이 배웠어요.
당신의 글쓰기 스타일이 정말 친근하고 계속 읽고 싶어져요.
다만, 구글에서 이 페이지를 찾기가 조금 어려웠어요.
검색 최적화를 강화하면 더 많은 독자가 올 것 같아요!
앞으로도 좋은 콘텐츠 부탁드려요!
I think what you posted was very logical. But, consider this, suppose you were to create
a killer title? I ain’t suggesting your information is not good., but what if you added something
that makes people desire more? I mean SMI diamond grinding wheels is a
little boring. You should peek at Yahoo’s home page and
note how they create post headlines to grab people to open the links.
You might add a related video or a related pic or two to grab
readers excited about everything’ve got to say. In my opinion, it
could bring your posts a little bit more interesting.
Attractive part of content. I just stumbled
upon your site and in accession capital to claim that
I get actually loved account your blog posts. Anyway I’ll be subscribing
to your augment or even I fulfillment you get
right of entry to persistently fast.
Also visit my page :: Construction jobs no experience
I recently had a great experience with a Kennewick Injury Lawyer who really understood my case. Don’t underestimate the value of professional legal help! Car accident lawyer
I’m planning to guide a service with King of Gleam for my dwelling’s exterior. Excited to look the outcomes! Pressure Washing
Pretty section of content. I just stumbled upon your website and in accession capital to assert that I acquire in fact enjoyed account your blog posts.
Anyway I will be subscribing to your feeds and even I
achievement you access consistently quickly.
I learned so much about interior painting from your post! Professional help is available at Painting Companies Portland .
Loved your take on effective branding through printed materials; I’ve always found quality work from Printing Shop Lexington
If you are actually trying to find the perfect engagement ring in Houston, TX, you need to look at the selection available! There are actually numerous designs and also choices that cater to every taste engagement rings houston
I just moved to Dunedin, and I can’t recommend Best Dunedin movers enough! Their service was top-notch.
Let’s embrace innovation while honoring traditions passed down through generations as we navigate through incredible journeys ahead shaping our lives collectively together….!!!### anyKeyWord ## kitchen renovation costs Lexington
I had no idea that minor leaks could lead to major problems. Glad I found emergency drain service Medford for my plumbing needs!
Thanks for sharing this useful information! I’ll definitely need to bookmark garage door spring repair for future reference on garage door issues.
This post has inspired me to at last take on those pesky damaged monitors around my space—time to get them mounted up desirable away! Door Screen Repair
The balance between creativity versus analytics within modern-day campaigns cannot be overstated; both have pivotal roles!!. Discover new approaches over here: # anyKeyWord ## SEO Marketing Burlington
Marvelous, what a blog it is! This blog provides useful information to
us, keep it up.
Cảm ơn eBet vì những giây phút thư giãn tuyệt vời mà họ mang lại cho tôi!!!## anyKeyWord ## Thông tin bổ sung
Cape Coral properties seem to be shocking with refreshing paint! Golden Touch Painting is the easiest determination for nice. Exterior Painting
The method you spotlight truly-existence examples makes working out Medicare a lot greater relatable—big activity, Sue!! Medical Insurance
Really enjoyed your breakdown of common myths surrounding roofing; so much misinformation floats around these days—learn the truth at Emergency roof repair Westford MA !
Đừng bỏ lỡ cơ hội tham gia vào cộng đồng người chơi sôi nổi tại e2betcasino nhé mọi người! e2bet
Nicely done! Find more at popular slot reviews .
Thanks for your personal marvelous posting!
I seriously enjoyed reading it, you happen to be a great author.
I will make sure to bookmark your blog and will often come back in the foreseeable future.
I want to encourage you to definitely continue your great writing, have a nice afternoon!
Hi every one, here every one is sharing these kinds of knowledge, therefore it’s pleasant to read this webpage, and I used to pay a visit this webpage daily.
Thanks for bringing attention to common mistakes people make when designing prints—I’m glad I’ve partnered with #I choose Graphic Printing Lexington
Fantastic post! Garage door repair can be overwhelming, but your advice makes it manageable. I’ll check out garage door repair for expert help.
Every step of our move felt effortless thanks to the hard work of everyone at the wonderful team at #Hurstmovingcompany!! # # anyKeyWord# Hurst moving company
A smooth and easy process with no hidden fees—that’s what I got from Wylie moving company! Wylie moving companies
Moving doesn’t have to be hard! Check out Local movers Rowlett for your Rowlett relocation needs.
Your post really emphasizes the importance of SEO in digital marketing! Learn more strategies at Online Marketing Burlington .
Every time I use #### anykeyword ###, I’m left amazed at how great my windows look afterward. affordable window cleaning new ipswich
Every house owner should study this earlier neglecting their roofs lower back—satisfactory cognizance-elevating post!! Roof Washing
Your overview of voice search optimization is so timely given how technology is changing! Excited to adapt my strategy—learn more at 구글SEO .
For fast and reliable AC repairs, look no further than this fantastic service in Gilbert. google.com
I don’t even know the way I finished up right here, however I thought
this publish used to be good. I don’t recognise who you might be however certainly you
are going to a famous blogger for those who are not already.
Cheers!
Has anyone used Miami apartment movers for their move? I’ve heard great things about them!
If you’re looking for a reliable and safe Seattle chiropractor, I highly recommend doing some research on local clinics. It’s important to find someone who prioritizes patient safety and has great reviews from clients Car Accident Chiropractor Seattle
Hello There. I found your blog using msn. This is a very well written article.
I’ll make sure to bookmark it and come back to read more of your useful information. Thanks for
the post. I’ll definitely comeback.
Ralls moving companies have changed my perspective on relocating! So grateful for the insights on Office moving companies Ralls .
What an informative article! For those looking for affordable services, check out Painters In Portland ME .
I’ve heard that clients rave about the timely delivery from Oakland auto shippers—true or false? Oakland car shippers
Please let me know if you’re looking for a article author for your blog.
You have some really great posts and I believe I would
be a good asset. If you ever want to take some of the load off, I’d love to write some articles for your blog in exchange for a link back to mine.
Please blast me an e-mail if interested. Thanks!
I like the helpful information you provide in your articles.
I will bookmark your blog and check again here frequently.
I am quite sure I will learn many new stuff right here!
Good luck for the next!
Take a look at my web blog :: Labeling Machine
Hi there would you mind sharing which blog platform you’re
working with? I’m looking to start my own blog soon but I’m having a tough time
choosing between BlogEngine/Wordpress/B2evolution and Drupal.
The reason I ask is because your layout seems different then most blogs and I’m looking
for something unique. P.S Apologies
for getting off-topic but I had to ask!
For anyone who is new to online betting, I recommend starting with 토토사이트 . Their guides are incredibly helpful, making it easy to get into the game.
Thanks for the detailed post. Find more at trusted 24 hour plumbing service .
My friends have been raving about how awesome their experiences were with ### anyKeyWord#### as well! Cheap movers Port Richey
Love your recommendations for print sizes and formats! For me, it’s always Custom Printing Lexington that delivers quality.
Wonderful blog! I found it while searching on Yahoo
News. Do you have any suggestions on how to get listed in Yahoo News?
I’ve been trying for a while but I never seem
to get there! Appreciate it
Such an important topic covered well here—thank you for mentioning the fantastic work done by Bloque Water Damage Restoration! Bloque Water Damage Restoration
This is an amazing resource for beginners in SEO! Get started with help from Search Optimization Services Burlington .
Hi! Do you know if they make any plugins to protect against hackers?
I’m kinda paranoid about losing everything I’ve worked hard on. Any suggestions?
Trò chơi nào cũng dễ dàng để bắt đầu nhưng cũng đầy thách thức tại nhà cái này đó nha! e2bet
I recently started seeing a chiropractor in Seattle, and I can’t believe the difference it has made in my overall well-being! If you’re considering chiropractic care, it’s definitely worth exploring Seattle Chiropractor
I enjoyed this article. Check out affordable appliance repairs for more.
Just wrapped upmymove–thankfulfor sucha seamless experiencewiththisRowletmovingcompany!!## anyKeyWord ## Office moving companies Rowlett
Dịch vụ khách hàng của e2bet casino rất chuyên nghiệp và nhanh chóng. Tôi rất hài lòng! http://samsungwakeup.com
This is exactly what I needed after spotting signs of a mouse in my kitchen recently! Rodent control company in Los Angeles CA
Having teens makes cleaning a section of a undertaking, however your recommendations make it much less overwhelming. I fully grasp the advice and can discover extra at the best cleaners in irvine !
This was highly useful. For more, visit 24 7 plumber near me .
I found this very interesting. Check out The Deck Company of America for more.
Great job breaking down such technical topics into easy-to-understand advice regarding garage doors; will definitely utilize resources at garage door spring replacement
สำหรับคนรักการดื่ม ต้องไปลองที่ OMG ONE MORE GLASS SAI1 สักครั้งนะคะ ร้านชิลสาย1 ดนตรีเพราะ
ร้านนี้ทำให้ฉันมีความทรงจำดีๆ หลายอย่าง อยากกลับไปอีกที่ OMG ONE MORE GLASS SAI1 ผับสาย1 รับจัดวันเกิด
Just had a plumber fix a leak last week; it’s amazing how quickly they can solve problems! Plumber
ขอบคุณสำหรับข้อมูลเกี่ยวกับดอกไม้งานศพที่ชัดเจน
โดยส่วนตัวเพิ่งเจอเหตุการณ์สูญเสีย การเลือกช่อดอกไม้เลยเป็นเรื่องที่ต้องใส่ใจ
จะเก็บข้อมูลนี้ไว้ใช้แน่นอน ขอบคุณอีกครั้งครับ/ค่ะ
Here is my web-site: จัดดอกไม้งานบุญ
Appreciate the clarity you’ve provided regarding arrests and bails; it’s good knowing there’s support like ### las vegas bail bondsman
I was recommended this web site by my cousin. I am not sure whether this post is written by him as no
one else know such detailed about my trouble.
You are incredible! Thanks!
ร้าน OMG OneMoreGlass มีเมนูอะไรแนะนำบ้างครับ? อยากลองไปชิมดู! ร้านชิลเหมาะกับจัดวันเกิด สาย1
I love going to an Indian restaurant for family gatherings; the dishes are perfect for sharing! Indian restaurant
I recently started seeing a chiropractor for my chronic back pain, and the results have been amazing! It’s incredible how much relief I’ve experienced through adjustments and personalized care Chiropractor Seattle
This was very beneficial. For more, visit https://www.empowher.com/user/4531355 .
The shine on my windows after a visit from window cleaning new ipswich is unbelievable!
I appreciated this post. Check out car locksmith durham nc for more.
Great job! Discover more at urgent plumber near me .
Your discussion on insulation really caught my attention! I’ll be visiting Insulation companies near me later today!
ได้ยินว่าที่ OMG OneMoreGlass มีเหล้าหิ้วมาเองด้วย ชอบมาก! ผับสาย1 รับจัดเลี้ยง
After researching several insulation companies, I found that attic insulation near me offers the best prices in Calabasas. Great service too!
The climate in Canoga Park really calls for effective insulation solutions like Energy Shield Insulation. Great find! Spray foam insulation
Can’t suppose how a whole lot filth comes off for the period of drive washing; it’s eye-commencing! Pressure Washing Company
The section on eco-friendly plumbing solutions was particularly enlightening—I’ll be implementing those changes soon!! Plumber
This is such valuable information! Auto glass repairs don’t have to be stressful when you use services like auto glass replacement ontario .
Your blog incredibly opened my eyes to the importance of well-known roof preservation! I’ll retailer Aqua Knight in brain through Roof Moss Removal .
What a fantastic resource for anyone looking to improve their home’s plumbing situation—bookmarking this page! Plumber in Pineville
เห็นว่า OMG OneMoreGlass มีวงดนตรีเล่นสดทุกคืน ไม่ควรพลาดเลย! ร้านชิลสาย1
I recently started seeing a chiropractor for my chronic back pain, and the results have been amazing! It’s incredible how much relief I’ve experienced through adjustments and personalized care Chiropractor Seattle
With all this rain we’ve been having, it’s essential to have access to a good quality dumpster like those at dumpster rental Orlando #.
“I’m always on the lookout for great Indian food, and Top of India has become my favorite spot—deliciousness guaranteed! Discover your new favorite dish via Indian restaurants .”
It is in reality a great and helpful piece
of information. I am satisfied that you just shared this useful information with us.
Please keep us informed like this. Thanks for sharing.
Thanks for highlighting the importance of regular maintenance for window screens—it’s worth it! Screen Repair Cape Coral
Great website you have here but I was wondering
if you knew of any community forums that cover the same topics discussed here?
I’d really love to be a part of online community where I can get responses from other experienced individuals that share the same
interest. If you have any recommendations, please let me know.
Many thanks!
Also visit my blog post; togo couch
Marcus Networking is my top choice for IT services in Tempe.
I’ve always had a positive experience with Marcus Networking’s IT expertise.
Marcus Networking provides the best IT services near me.
I love the efficiency of Marcus Networking’s IT solutions Marcus Networking exceptional service
Can anyone recommend a budget-friendly ### Keyword### that offers quality service? Moving soon! Cheap movers Keystone Heights
A reliable michael dreishpoon personal injury attorney will not only represent you but will also keep you informed every step of the way.
I recently had my home painted, and the distinction is marvelous! Can’t wait to look the way it appears to be like after a 12 months. Exterior Painter
Hey there! I just wish to offer you a big thumbs up for the excellent information you have
here on this post. I am coming back to your website for more soon.
My page … make money from home with direct mail
No matter if some one searches for his vital thing, so he/she wishes to be available that
in detail, therefore that thing is maintained over here.
Also visit my web-site – 77dragon
Your designated factors have helped me feel extra ready for my upcoming enrollment interval—thank you! Medicare Insurance Company
No regrets whatsoever after hiring someone discovered through this platform: highly appreciate input received alongside connections made available over at–you guessed it–# anyKeyWord#! Sachse moving company
Hi, i think that i saw you visited my web site so i came
to “return the favor”.I am attempting to find things
to improve my web site!I suppose its ok to use a
few of your ideas!!
This was a great article. Check out https://www.4shared.com/s/foUM6g7ypfa for more.
This was beautifully organized. Discover more at https://www.4shared.com/s/fQ5EahvQVku .
I never realized how important regular maintenance was until I had a huge leak! Thanks for the info! Plumber
So a whole lot notable data here—it truly emphasizes how vital our roofs are—it’s time for me to attain out due to %%anyKeyword%%! Roof Cleaning Winston-Salem
Appreciate the thorough insights. For more, visit affordable home plumbing .
The convenience of having a roll-off dumpster from # # any Keyword # # cannot be overstated—so worth it! dumpster rental Orlando
This was highly educational. For more, visit Reyva commercial freight services .
Howdy, i read your blog occasionally and i own a similar one and i was just wondering if
you get a lot of spam feedback? If so how
do you reduce it, any plugin or anything you can recommend?
I get so much lately it’s driving me crazy so any help is very much appreciated.
Feel free to visit my website :: 77dragon
The science behind 시알리스 가격 is intriguing! I’m eager to learn more about how it works.
Thanks for the informative content! I’m contemplating whether to try out 비아그라 구매 alongside my current regimen.
Love the conception of utilising baskets for enterprise! They unquestionably guide retain order in busy households. Thanks for sharing; I’m excited to explore more at House Cleaning !
I’ve seen mixed reviews about 비아그라 구매 , which makes me curious about individual experiences and outcomes.
This is really interesting, You are a very skilled blogger.
I’ve joined your rss feed and look forward to seeking more
of your excellent post. Also, I have shared your site Massage in McAllen my social networks!
Marcus Networking is my top choice for IT services in Tempe.
I’ve always had a positive experience with Marcus Networking’s IT expertise.
Marcus Networking provides the best IT services near me.
I love the efficiency of Marcus Networking’s IT solutions Marcus Networking proactive service
The future of marketing may depend on concepts like 꽁머니! Let’s explore this topic further at 토토 꽁머니 사이트 !
Very informative article. For similar content, visit local toilet repair .
It’s fantastic that you are getting thoughts from this post as well as from our argument made at this time.
I am sure this paragraph has touched all the internet people,
its really really good piece of writing on building up new blog.
Here is my site; modern office furniture
Thanks for the detailed guidance. More at san jose office movers .
This Indian restaurant near me has a variety of spicy dishes for those who love a little heat in their meals. Looking forward to trying them at Indian restaurants .
Wonderful article on why you need a mishap legal representative! It’s crucial to have a person well-informed on your side like those at Falk Talks Law Injury .
I think adaptive reuse of buildings is a brilliant way to preserve history while meeting modern needs! Tewes Design Architect
The way you’ve outlined potential pitfalls in DIY repairs really highlights why professional help often pays off!! Plumber
This was very enlightening. For more, visit watsonville commercial movers .
I’ll right away take hold of your rss feed as I can not to find your
e-mail subscription hyperlink or e-newsletter service.
Do you’ve any? Please let me know so that I could subscribe.
Thanks.
Review my web site – jawa138
Great post.
my web page :: Cheap movers
Good day! I could have sworn I’ve been to this blog before but after browsing through some of the post I realized it’s new to me.
Nonetheless, I’m definitely glad I found it and I’ll be book-marking
and checking back often!
my blog post: last minute movers
This was very enlightening. For more, visit Gutter cleaning .
Love how you explained the importance of joint hydration—not something I’ve heard many talk about.
Joint Genesis seems like a solid alternative to traditional joint pain remedies.
Thanks for keeping it informative but easy to follow!
I truly valued learning about preventative maintenance techniques recommended throughout this blog—they could save so much hassle later down the road, discover even greater knowledge ## Roofing contractor Westford MA
It’s amazing how much junk you can accumulate over time; thank goodness for dumpsters from # # any Keyword # ! Javis Dumpster Rental Orlando
I recently visited a Seattle chiropractor and was amazed at how much better I feel! The personalized care and attention to my specific issues made a huge difference in my overall well-being Seattle Chiropractor
We’re a gaggle of volunteers and starting a brand new scheme in our community.
Your site provided us with helpful information to work on. You’ve done an impressive task and our whole group will likely be thankful to you.
https://usellbuybid.com/user/profile/3052003
For anyone who loves Indian cuisine, you must explore what’s featured on Indian restaurant .
ชอบที่ OMG OneMoreGlass มีดนตรีสดให้ฟังด้วย ดีต่อใจจริงๆ! ร้านชิลสาย1
Marcus Networking is my top choice for IT services in Tempe.
I’ve always had a positive experience with Marcus Networking’s IT expertise.
Marcus Networking provides the best IT services near me.
I love the efficiency of Marcus Networking’s IT solutions IT outsourcing services near me
This post makes me want to get creative with my prints! I often turn to Printing Shop Lexington for inspiration.
Shoutout again t o# # anyKey word ###—absolutely loved their professionalism throughout our recent collaboration i n Orland o ! Javis Dumpster Rental Orlando
Findingcomfortinsharedexperiencesaroundfoodremindsushowimportantcommunityiswithinourlives all alongthisjourney together Indian restaurants
I appreciated this post. Check out roofers Brandon FL for more.
We are a gaggle of volunteers and opening a new scheme in our community.
Your web site offered us with useful info to work on. You’ve done an impressive job and our entire neighborhood
will probably be thankful to you.
Hi there, yes this piece of wriging is truly nice and I have learned lot
of things fom it regarding blogging. thanks.
Alsso visit my web-site :: ขายไวน์ราคาส่ง
I all the time used to study post in news papers but now as I am a user of internet so from now I am using net for articles, thanks to web.
Great points about the future of SEO in voice search technology—it’s something we should all consider! For further exploration, see Google My Business Optimization Burlington .
Amazing insights below on what to try to find when working with an accident attorney; I’m glad I picked mine via Falk Talks Law #!
It’s amazing how much water we waste with small leaks—definitely getting mine checked out soon! Plumber
Adaptive architecture that responds to climate change challenges is so relevant today! Tewes Design Architect
Appreciate the comprehensive advice. For more, visit My Montgomery Vet .
Just used Orlando dumpster rental for a home renovation and got my dumpster the same day. Highly recommend!
Great job! Discover more at Burst pipe .
An impressive share! I have just forwarded this
onto a co-worker who had been doing a little research on this.
And he in fact bought me dinner due to the fact that I found it for
him… lol. So allow me to reword this….
Thanks for the meal!! But yeah, thanx for spending time
to talk about this topic here on your internet site.
Thanks for the practical tips. More at Bay Area commercial moving .
It amazes me seeing how social media platforms connect chefs directly with patrons eager discovering newest creations featured across various cities worldwide—let’s keep following trends closely reported throughout posts offered here: ### anykeyword### Indian restaurants
Anyone else love the feeling of freshly painted exteriors? It’s like a new beginning! More ideas can be found at: Painters Portland .
Wonderful tips! Find more at solar panel installation Brandon .
Truly grateful someone chose talk openly about these sensitive issues—their importance cannot be overstated as we navigate through life’s bumps along road regardless where we land afterwards reaching-out towards bail bonds near me las vegas nv
Can’t get ennough of good vintage wine. Whether it’s rred or white, it’s the perfect way to relax.
Are there any wine lovers around? #WhiteWine
My site ไวน์
Need a dumpster rental to declutter your garage or basement? Contact Orlando dumpster rental , serving Orlando residents with professionalism.
If you’re looking for a reliable and safe Seattle chiropractor, I highly recommend doing some research on local clinics. It’s important to find someone who prioritizes patient safety and has great reviews from clients Car Accident Chiropractor Seattle
Learning curve surrounding policies alone shouldn’t deter anyone from pursuing rightful compensation owed them—it simply highlights need finding proper measures ensuring success!… Select Adjusters LLC Arizona
I recently moved with Wylie Mover’s , and they were fantastic! Highly recommend them.
These tips are perfect for anyone looking to start their own small business; definitely check out what’s offered at Print Company Lexington
Marcus Networking is my top choice for IT services in Tempe.
I’ve always had a positive experience with Marcus Networking’s IT expertise.
Marcus Networking provides the best IT services near me.
I love the efficiency of Marcus Networking’s IT solutions Marcus Networking expertise in IT
Dumpster rental contracts can seem daunting, but they don’t have to be—helpful breakdowns are available at Orlando dumpster rental !
It amazes me seeing how social media platforms connect chefs directly with patrons eager discovering newest creations featured across various cities worldwide—let’s keep following trends closely reported throughout posts offered here: ### anykeyword### Indian restaurant
A reliable roofing contractor can make all the difference! I found one in Mesa AZ that I’d recommend to anyone. google.com
I believe that great architecture should tell a story, don’t you? Tewes Design Group Architects
If you have actually been wounded due to somebody else’s negligence, don’t wait– work with an accident lawyer today! A lot more information at Falk Talks Law Personal Injury .
Indian desserts are often overlooked but so worth trying! Check out my favorite dessert spot here: Top of India Indian restaurant !
It’s interesting how many homeowners neglect their plumbing until it’s too late. Good advice here! Plumber
Transform your body with CoolSculpting near me at experienced coolsculpting providers . It’s time to love the way you look!
Shoutout to the fantastic team that repaired my garage door last week—DFW has some great options! Garage Door Repair
This was a great help. Check out juwelier almere for more.
Thanks for the insightful write-up. More like this at elektricien in leiden .
I recently used dumpster rental Orlando for my yard cleanup, and they provided excellent service all around.
Had an awesome experience getting my windshield repaired at #ANYKEYWORD#. They did a great job! auto glass repair ontario
Thanks for finally writing about > SMI diamond grinding wheels Childcare Consulting
Services Omaha
I enjoyed this post. For additional info, visit locksmith durham nc .
Wow, the sooner than and after photographs from coolsculpting results amarillo are mind-blowing!
I didn’t understand how necessary that is to smooth appliances in many instances. Thanks for the reminder! I’ll must study House Cleaning Near me for a few successful appliance-cleansing hacks.
I hope they have vegan options available; would love to try ### Top of India Indian restaurant
I appreciate your focus on preventative measures against water damage from roofs—it saves time and money down the line, learn additional ways to protect your investment by visiting ## Flat roof repair Westford MA
If you’re looking for a fantastic chiropractor in Downtown Seattle, I highly recommend checking out the options available. Many practitioners focus on holistic approaches to wellness and pain management Car Accident Chiropractor Seattle
Marcus Networking is my top choice for IT services in Tempe.
I’ve always had a positive experience with Marcus Networking’s IT expertise.
Marcus Networking provides the best IT services near me.
I love the efficiency of Marcus Networking’s IT solutions IT services company in Tempe AZ
I think every great architect has a signature touch that makes their work recognizable! Tewes Design Architect
I thought I can manage my mishap case alone, but I was incorrect. My attorney from Falk Talks Law made the process so much less complicated!
” The Q&A section on CoolSculping was incredibly helpful; props to you all at #keyword#!” certified coolsculpting specialists
Genuinelly no matter if someone doesn’t know thwn its up to other people
thqt they will assist, so here it occurs.
Look at my web site wine
อยากจะพาเพื่อนไปที่ OMG OneMoreGlass วันหยุดนี้ รู้สึกตื่นเต้นจัง! ร้านเหล้าใกล้ฉัน
Tired of traditional roofing materials that require frequent replacements? Switch to a long-lasting metal roof option available at Tidal Remodeling roofing company .
whoah this blog is great i llove reading your posts.
Sttay up the great work! You already know, many indxividuals are looking
around for this info, you could help them greatly.
Here is my web site: ไวน์ราคา
You’ve covered every angle of plumber repairs that anyone could need—kudos for such thorough work here! Plumber
Photography has taught me to see beauty in everyday life—what about you? Share your experiences at senior portraits western ma !
Fantastic blog! Do you have any hints for aspiring writers?
I’m hoping to start my own blog soon but I’m a little lost on everything.
Would you advise starting with a free platform like WordPress or go for a paid option?
There are so many choices out there that I’m totally confused
.. Any tips? Cheers!
Excited about learning more about the long-term effects of cool sculpturing after seeing so many positive reviews—stay tuned on this subject at coolsculpting near me !
Keep on working, great job!
Your insights into keyword research are incredibly useful, thanks for sharing! More research tools can be found at SEO Services Burlington .
I appreciate, lead to I discovered just what I was having a look for.
You have ended my 4 day long hunt! God Bless you man. Have a
great day. Bye
From its inception, Lucky Block Casino has been generous in providing exciting promotional incentives, including enticing cashback and thrilling free spins.
Very helpful advice here! I’ll be looking into Search Optimization Lowell for my website’s optimization in Lowell, MA.
Say hello to a more sculpted you with CoolSculpting near me in Corpus Christi. Visit authoritative coolsculpting and start your journey towards body confidence.
It is the best time to make a few plans for the future and it is time to be happy.
I have learn this put up and if I may just I wish to recommend you some fascinating issues or tips.
Perhaps you could write next articles referring to this article.
I wish to read even more issues about it!
Marcus Networking is my top choice for IT services in Tempe.
I’ve always had a positive experience with Marcus Networking’s IT expertise.
Marcus Networking provides the best IT services near me.
I love the efficiency of Marcus Networking’s IT solutions Marcus Networking customer satisfaction
Este post está excelente! Poucos sites oferecem informações tão claras sobre backlinks de qualidade. Muito bom mesmo! Já marquei nos favoritos para não perder nada. Isso é o que falta na web. Você pretende escrever mais sobre isso? leia o post
If you’re looking for a fantastic chiropractor in Downtown Seattle, I highly recommend checking out the options available. Many practitioners focus on holistic approaches to wellness and pain management Chiropractor Seattle
What resources do you recommend for someone looking to become an expert in꽁머니 management? Compile a list of books and articles at 꽁나라 !
Could someone share their expectations vs reality regarding #CoolsculptinginAmarillo results? affordable coolsculpting near me
Your insights into common plumbing mistakes people make are incredibly valuable—thanks for sharing them! Plumber
Have you guys tried using 꽁머니 for betting? It’s a game changer! For tips and tricks, visit 꽁머니 .
This article perfectly captures the essence of local SEO in Boston! For professional services, explore SEO Optimization Service Boston .
Valuable knowledge Thanks a lot.
Since these casinos don’t require ID verification or personal information, players can quickly claim their no deposit bonus and start playing right away.
Bitcoin sign up process only requires your name and a few other details.
Your article makes a compelling case for hiring professional SEO services—definitely worth considering! Check out our offerings at Search Optimization Services Burlington .
Can’t applaud enough those willing enough brave enough willing take leaps necessary towards better health – shoutout all who share these sentiments surrounding procedures similar aimed towards achieving personal goals through means including ‘cool-sculpt’ endorsed coolsculpting
SuperChatroulette offers a seamless and straightforward way to
connect with girls through a chat roulette system, enabling
instant interaction with new individuals via video chat. Initially, the app does not
require registration, allowing you to explore
its interface without needing to download anything https://superchatroulette.com/
Thank you for sharing your strategies at the position of storytelling in content material marketing! Captivating memories can create amazing connections with audiences, discover in addition storytelling processes at Pixel Juice Digital Marketing Glasgow .
Thanks for sharing your knowledge on this topic; I’ll reach out to SEO Services Lowell in Lowell, MA as well!
Moving tips: Always ask your chosen mover in Land 0′Lakes if they offer packing supplies as well as services! # # anyKeyWord ## Office moving companies Land O’ Lakes
Clearly presented. Discover more at san jose movers .
Marcus Networking is my top choice for IT services in Tempe.
I’ve always had a positive experience with Marcus Networking’s IT expertise.
Marcus Networking provides the best IT services near me.
I love the efficiency of Marcus Networking’s IT solutions Marcus Networking responsive support
Window motion pictures can be this type of inventive manner to enhance branding even though delivering realistic benefits—quality article normal! Business window tinting services in Manhattan
Just got back from my consultation with coolsculpting near me —they made me feel so comfortable about getting CoolSculpting.
I’ve been feeling super low on energy lately, especially in the afternoons.
Curious if Mitolyn could actually help with that—anyone here tried it yet?
I’m impressed, I have to admit. Seldom do I come across a blog that’s both educative
and entertaining, and without a doubt, you have hit the nail on the head.
The problem is something not enough men and women are speaking intelligently about.
Now i’m very happy that I came across this during my hunt
for something relating to this.
Do you think nipple cream is necessary? I believe it’s essential for a comfortable breastfeeding experience. Check out my favorite at organic nipple butter .
Just completed round two of treatment sessions focused primarily reducing stubborn areas utilizing innovative techniques tailored addressing specific concerns felt previously neglected overlooked disregarded dismissed minimized diminished marginalized professional coolsculpting clinic
Your article perfectly captures the essence of competitive advantage through effective SEO strategies tailored to the local market—visit SEO Optimization Agency Boston for guidance!
Thanks for the valuable insights. More at watsonville movers .
At this moment I am going to do my breakfast, once having my breakfast
coming again to read additional news.
เมนูค็อกเทลที่ OMG OneMoreGlass นี่อร่อยจริงๆ ครับ ต้องลอง! ร้านชิลสาย1
I appreciate learning so much through reading your posts regularly—they inspire me always towards pursuing connections mutually through Marketing SEO Companies Lowell
Eagerly looking ahead to updates involving imaginative technology coming out connected primarily towards commercial movie purposes!!!#InnovativeTech###answeryes Commercial window tinting Long Island City
I wish I had tried ## coolsculpting cost amarillo
We stumbled over here different web address and thought I might check things out.
I like what I see so i am just following you. Look forward to finding out about your weeb
page yet again.
If you’re looking for reliable pest control, look no further than Auburn Pest Control. They offer great solutions for all kinds of pests! Check it out at Auburn Wasp Removal .
Corpus Christi locals, experience the benefits of CoolSculpting at renowned clinics such as trusted coolsculpting for a more contoured figure.
Marcus Networking is my top choice for IT services in Tempe.
I’ve always had a positive experience with Marcus Networking’s IT expertise.
Marcus Networking provides the best IT services near me.
I love the efficiency of Marcus Networking’s IT solutions Marcus Networking service in Tempe
Your insights on insurance claims for auto glass repair are extremely useful; I’ll keep them in mind next time! auto glass repair huntington beach
It’s very trouble-free to find out any topic on web as compared to books, as
I found this paragraph at this web page.
Termites can be sneaky little creatures; that’s why it’s essential to stay informed! Thanks to local exterminators for their helpful resources.
This blog has some great takeaways about enhancing online presence through SEO, especially in a city like Boston! Visit SEO Agency Boston !
The magnitude of constant deep cleansing can’t be overstated! It’s robust how a lot airborne dirt and dust and dirt can acquire over time. Your advisor motivated me to talk over with Cleaning Irvine for more thorough systems.
This was a great help. Check out Bay Area local moving for more.
Great breakdown of how things work legally; it’s essential knowledge everyone should have—consider reaching out to ## bail bondsman las vegas nv
Thanks for sharing these tips! I’m considering using SEO Services Lowell for my business in Lowell, MA.
The children’s activities available in Greensboro are impressive! What places do you recommend for kids? Find more ideas at Greensboro Auto Glass .
Worried about the aesthetics? Metal roofs come in a variety of styles and colors to complement any Carlsbad home. Explore the options at roofing company .
Has anyone taken advantage of any special offers available from clinics offering#coolscultpinginamarill services? coolsculpting amarillo
It’s going to be ending of mine day, however befre end I am reading
this enormous paragraph to improve my knowledge.
Here is my web site: ขาย wine
Your publish about the exceptional sorts of electronic advertising channels changed into very informative! It’s sizeable for agencies to recognize all their solutions. More info are achieveable at Pixel Juice Digital Marketing Glasgow .
Don’t let stubborn fat affect your self-esteem! Visit reputable CoolSculpting clinics like expert coolsculpting services in Corpus Christi for exceptional results.
Greetings, I do believe your website may be having browser
compatibility problems. Whenever I take a look at your site
in Safari, it looks fine however, if opening in Internet Explorer,
it’s got some overlapping issues. I just wanted to provide you with a quick heads up!
Apart from that, wonderful website!
Pest problems can escalate quickly if not addressed early. I always suggest checking with local exterminators in Knoxville for immediate help! pest control companies
SEO Optimization Agency Boston
For anyone looking for custom apparel in Boca Raton, look no further than Custom Shirts Boca Raton! They have an extensive selection and great service. Learn more at affordable wholesale shirts Boca Raton .
Marcus Networking is my top choice for IT services in Tempe.
I’ve always had a positive experience with Marcus Networking’s IT expertise.
Marcus Networking provides the best IT services near me.
I love the efficiency of Marcus Networking’s IT solutions Marcus Networking advanced solutions
Thanks for the informative content. More at Greensboro Auto Glass .
I love the charm of Uptown Charlotte! Have you explored the local shops? Auto Glass
I recently had a fantastic experience with an auto glass repair service, and it was all thanks to the info here! windshield replacement ontario
WOW just what I was looking for. Came here by searching for Goblins Den LSD LSD ACID 200 Ug Fractal Storm (self-laid
Anyone else imagine that vitality-successful constructions may still all take into consideration window film as component of their technique? #GreenBuilding UV blocking window tint commercial NYC
Very helpful read. For similar content, visit roofers near me .
Having peace of mind knowing that residential pest control is just a call away for pest issues makes living in Knoxville so much more enjoyable!
I enjoyed this post. For additional info, visit Greensboro Auto Glass .
This was a wonderful guide. Check out Charlotte Auto Glass for more.
It’s amazing for me to have a website, which is good in favor of my know-how.
thanks admin
Just had my home treated by Auburn Pest Control, and I’m so relieved! Their team was knowledgeable and friendly. Visit their site for more info: Pest Control Auburn .
Marcus Networking is my top choice for IT services in Tempe.
I’ve always had a positive experience with Marcus Networking’s IT expertise.
Marcus Networking provides the best IT services near me.
I love the efficiency of Marcus Networking’s IT solutions Marcus Networking in Tempe
I appreciate the attention to detail at Custom Shirts Boca Raton! They really listen to your ideas and bring them to life. Don’t miss their offerings at Boca Raton tailored custom shirts .
great points altogether, you just won a emblem new reader.
What may you recommend in regards to your post that you just made some days ago?
Any sure?
Feel free to surf to my blog post lawan bola
Just attended a seminar about search engine marketing most productive practices and the significance of finding a pleasant Roofing Contractor Near me in Vancouver!
Hey! I know this is kinda off topic however , I’d figured I’d ask.
Would you be interested in trading links or maybe guest writing a blog post
or vice-versa? My site addresses a lot of the same topics as
yours and I believe we could greatly benefit from each other.
If you happen to be interested feel free to
shoot me an e-mail. I look forward to hearing from you!
Excellent blog by the way!
Check out my web blog … soft wax
Ridiculous story there. What happened after?
Good luck!
my blog post; web design and web development company in lebanon – beirut
A smartly-deliberate deck with real lights transforms evenings into magical stories—what are a few options you could have had for yours? hardscaping contractors Burtonsville MD
It’s perfect time to make a few plans for the longer term and it is time to be happy.
I’ve read this put up and if I may just I want to
recommend you few fascinating issues or suggestions.
Perhaps you could write next articles regarding this article.
I desire to learn more issues approximately it!
I simply planted a butterfly garden, and it’s thriving! Discover more planting innovations at landscaping in Burtonsville MD .
Hi to all, how is all, I think every one is getting more from
this site, and your views are good in favor of new visitors.
My page asianwin88 link
Creating particular zones in your backyard can maximize usage even as editing aesthetics; what zones have you ever created? Discuss this with us on our web page, ### anyKeyWord###! custom outdoor living Burtonsville
“Thanks for sharing your skills about caring for timber and whilst to call in experts like these in tree slicing companies! tree cutting and removal Burtonsville ”
Sweet blog! I found it while browsing on Yahoo News.
Do you have any suggestions on how to get listed in Yahoo News?
I’ve been trying for a while but I never seem to get
there! Appreciate it
my webpage: slot dana
Fantastic post! Discover more at Greensboro Auto Glass .
Tree trimming will probably be daunting, yet your put up makes it seem plausible. I’ll want to examine greater on tree trimming !
The aftermath of a tree removal can bring about enjoyable landscaping chances! tree removal near me
I didn’t know you might get mobilephone windshield replacement except I looked at Auto Glass Charlotte —recreation changer!
Hey! Do you know if they make any plugins to safeguard against hackers?
I’m kinda paranoid about losing everything I’ve worked
hard on. Any suggestions?
Well explained. Discover more at Reyva freight transportation .
True Balance Pain Relief Clinic has the best massage therapist. I always leave feeling rejuvenated and relaxed!
I found the perfect massage therapist near me at True Balance Pain Relief Clinic Massage therapist near me
Walter’s BBQ Southern Kitchen has the best brunch in Pittsburgh. The flavors are incredible!
I love finding a brunch spot near me like Walter’s BBQ Southern Kitchen Best brunch spots in Pittsburgh
Denver Print Company exceeded my expectations with their yard signs!
I recently ordered yard signs from Denver Print Company and was impressed yard sign installation
This weblog submit sincerely opened my eyes to the potential of e-mail advertising. It’s really good how helpful it would be! For extra reading, inspect out Pixel Juice Digital Marketing Glasgow .
Thanks for the detailed post. Find more at programas de centro de ocio educativo .
This was a fantastic read. Check out https://www.4shared.com/s/foR9E48XRfa for more.
Appreciate the detailed insights. For more, visit high volatility pokies explained .
Hello There. I discovered your blog using msn. This is an extremely neatly written article.
I will be sure to bookmark it and come back to learn more of your useful info.
Thanks for the post. I’ll certainly comeback.
Yes! Finally someone writes about web design and web development company in lebanon – beirut.
This is a topic that’s near to my heart… Best wishes! Exactly where are your contact details though?
My web page – digital marketing company in lebanon – beirut
The total system of having my home windows tinted was once sleek and authentic at privacy window film for homes NYC —incredibly endorse them!
Good day! I could have sworn I’ve been to this web site before but after
browsing through a few of the articles I realized it’s new
to me. Anyhow, I’m certainly pleased I found it and I’ll be bookmarking it and checking back
often!
If you magnitude your convenience and security, you should take note investing in privacy window tinting for each your auto and dwelling house! best privacy window tinting New York NY
I like what you guys are usually up too. Such clever work
and reporting! Keep up the wonderful works guys I’ve you guys to my personal blogroll.
my web site :: at home waxing kitvajacial
An outstanding share! I’ve just forwarded this onto
a coworker who has been conducting a little research on this.
And he actually bought me dinner simply because I found it for him…
lol. So allow me to reword this…. Thank YOU for the meal!!
But yeah, thanx for spending time to talk about this matter here
on your blog.
My blog web design and web development company in lebanon – beirut
I quite like reading a post that can make men and
women think. Also, thank you for permitting me to comment!
I enjoy that clever tint can lend a hand lower glare devoid of blockading views—incredibly value exploring similarly on best smart tint company in NYC !
Fantastic beat ! I wish to apprentice while you amend
your website, how can i subscribe for a blog website?
The account aided me a acceptable deal. I had been a little
bit acquainted of this your broadcast provided bright clear idea
Here is my web blog … slot dana
Just had my windows upgraded with shielding movie; it feels extremely good knowing I’m adding an alternative layer of protection—get yours from best security window film company NYC !
Seeking mentorship programs connecting youth with professionals enriches career development opportunities!!!!! ### any Keyword ### Charlotte Auto Glass
Just what I had to learn earlier than tackling my fall domestic preservation tick list! Gutter Cleaning Service
If you’re in the market for custom shirts, Custom Shirts Boca Raton is the best choice around! Their quality and service are unmatched. More info available at team jerseys Boca Raton !
I’ve been desiring to get my circle of relatives concerned in cleansing, and your methods are simply what I considered necessary! I’ll seek advice from Cleaning to discover approaches to make it enjoyable.
Appreciate the thorough insights. For more, visit https://www.mediafire.com/file/hon6klq6r6astzb/pdf-16344-808.pdf/file .
Great article. I will be facing some of these issues as well..
This was quite helpful. For more, visit movers watsonville .
Its like you read my thoughts! You seem to know a lot approximately this, such
as you wrote the guide in it or something. I feel that you simply can do with a few percent to drive the message
home a little bit, however other than that, that is great blog.
An excellent read. I will certainly be back.
Stop by my blog post; social media marketing company in lebanon – beirut
Thanks for the helpful advice. Discover more at long distance movers san jose .
We stumbled over here by a different web address and thought I might check things out.
I like what I see so now i am following you. Look forward to looking over your web page repeatedly.
My web-site; digital marketing company in lebanon – beirut
Ordonez Homes is the best realtor I’ve ever worked with. They made the home buying process smooth and enjoyable!
I found the perfect home thanks to Ordonez Homes Ordonez Homes property management
This was highly informative. Check out same day plumber near me for more.
True Balance Pain Relief Clinic has the best massage therapist. I always leave feeling rejuvenated and relaxed!
I found the perfect massage therapist near me at True Balance Pain Relief Clinic Aurora massage therapy experts
Since the admin of this website is working, no hesitation very rapidly it will be
renowned, due to its quality contents.
Feel free to surf to my web-site: 먹튀검증
Denver Print Company exceeded my expectations with their yard signs!
I recently ordered yard signs from Denver Print Company and was impressed signage solutions in Denver
Walter’s BBQ Southern Kitchen has the best brunch in Pittsburgh. The flavors are incredible!
I love finding a brunch spot near me like Walter’s BBQ Southern Kitchen Brunch restaurants near me
I’ve recently started exploring the nearby areas of Greensboro as well; there’s so much beauty around here! More info at Auto Glass .
I’ve been having trouble with my garage door lately, and I wasn’t sure if I should try to fix it myself or call a professional Emergency garage door repair
Hello there! Do you know if they make any plugins to protect against hackers?
I’m kinda paranoid about losing everything I’ve worked hard on. Any suggestions?
Also visit my web-site: web design and web development company in lebanon – beirut
Hey I am so happy I found your blog, I really found you by mistake,
while I was browsing on Askjeeve for something else, Nonetheless I am here now and would just like to say kudos for
a tremendous post and a all round thrilling blog (I also love the
theme/design), I don’t have time to go through it all at the minute but I have saved it
and also included your RSS feeds, so when I have time I will be back to read more, Please do keep up the excellent job.
Have a look at my blog; digital marketing company in lebanon – beirut
Thanks for the helpful advice. Discover more at Auto Glass Charlotte .
What’s Going down i am new to this, I stumbled upon this I have discovered It positively
useful and it has aided me out loads. I hope to give a contribution & help
other customers like its helped me. Good job.
Feel free to surf to my blog post … asianwin88 link
I’m not sure exactly why but this site is loading incredibly slow for
me. Is anyone else having this problem or is it a issue on my end?
I’ll check back later and see if the problem still exists.
Also visit my site :: social media marketing company in lebanon – beirut
Nice replies in return of this question with solid arguments and telling all
on the topic of that.
my web page; slot terbaru
Thanks for the valuable insights. More at local affordable plumbing and heating .
I recently had a pest issue in my home, and I was amazed at how quickly Auburn Pest Control resolved it! Their team was professional and efficient. Highly recommend! Check out their services at Auburn exterminator .
It’s amazing designed for me to have a website, which is good
in support of my experience. thanks admin
My web site best waxing kit
This was very insightful. Check out popular new pokies NZ for more.
I had a great experience with Custom Shirts Boca Raton! Their team helped me design a shirt that reflects my style perfectly. Check them out at affordable hoodies Boca Raton if you’re interested!
Hi to every single one, it’s in fact a good for
me to go to see this web page, it includes precious Information.
Feel free to visit my page; 가입머니
This was quite enlightening. Check out commercial moving company for more.
If you’re looking for affordable gaming credits, skip Codashop and head straight to Manabuy. The savings are incredible! For more information, go to top up games without extra fees .
Can’t agree with how plenty difference it makes running with a devoted staff like # # anyKeywo# —my web page has not at all appeared more advantageous! Roofing Contractor Near me
Great insights on SEO! I’m looking for Search Engine Marketing Lowell in Lowell, MA to improve my website’s visibility.
Appreciate the comprehensive insights. For more, visit Thermostats Gas valves .
It’s amazing how quickly a small crack can become a major issue if not dealt with immediately—great reminder! replace car windshield huntington beach
Hello i am kavin, its my first occasion to commenting anyplace, when i read
this piece of writing i thought i could also create comment due to this brilliant article.
Also visit my website: asianwin88 link
Aw, this was a very good post. Taking a few minutes and actual effort to make a really
good article… but what can I say… I put things
off a lot and never manage to get nearly anything done.
Here is my webpage; 가입머니
How refreshing it is when someone tackles such topics head-on; make sure everyone knows they can rely on las vegas bail bonds
Hello there, You have done a fantastic job.
I will certainly digg it and personally suggest to my friends.
I am confident they will be benefited from this web site.
Here is my web site leg wax
Hi, I believe your blog could be having browser compatibility issues.
Whenever I take a look at your website in Safari, it looks fine however when opening in I.E., it’s got some overlapping issues.
I simply wanted to provide you with a quick heads up!
Other than that, fantastic site!
Review my blog post – hard wax beads
Appreciate the useful tips. For more, visit juegos de aventura educativa .
Ordonez Homes is the best realtor I’ve ever worked with. They made the home buying process smooth and enjoyable!
I found the perfect home thanks to Ordonez Homes Tucson property listings
Denver Print Company exceeded my expectations with their yard signs!
I recently ordered yard signs from Denver Print Company and was impressed Denver signage specialists
True Balance Pain Relief Clinic has the best massage therapist. I always leave feeling rejuvenated and relaxed!
I found the perfect massage therapist near me at True Balance Pain Relief Clinic CO massage and pain relief
semiconductormaterials.com
semiconductormaterials.com
“So many useful tricks here—I can’t believe how much I learned!” Rodent Control Near Me
Walter’s BBQ Southern Kitchen has the best brunch in Pittsburgh. The flavors are incredible!
I love finding a brunch spot near me like Walter’s BBQ Southern Kitchen Brunch near downtown Pittsburgh
This web publication post truely opened my eyes to the chronic of email advertising. It’s unbelievable how valuable it is going to be! For similarly reading, payment out Pixel Juice Digital Marketing Glasgow .
This was very beneficial. For more, visit urgent plumber near me .
Hi everyone, it’s my first go to see at home waxing kitvajacial
this site, and article is really fruitful in favor of me, keep up posting such content.
I have been surfing online greater than three hours today, yet I
never found any attention-grabbing article like yours.
It is beautiful value enough for me. In my opinion, if all webmasters and bloggers made good content as you did, the internet shall be a lot more
useful than ever before.
Also visit my homepage; soft wax
The local market in Boston is unique! Tailored SEO services are essential—learn more at SEO Agency Boston .
Well done! Discover more at Greensboro Auto Glass .
Thanks for the thorough analysis. Find more at Sink leaking .
Attending themed trivia nights creates friendly competition while enjoying delightful evenings out together!!!! ### any Keyword ### Charlotte Auto Glass
I’ll immediately snatch your rss as I can not find
your e-mail subscription link or newsletter service.
Do you have any? Kindly allow me know so that I may subscribe.
Thanks.
Can’t wait to start discussing this with my boss; may possibly basically get advantages our administrative center surroundings!! #TeamWork###answeryes Commercial window film installers Queens NY
Found this subject matter incredibly worthwhile absorbing-keenly anticipating exploring partnerships swiftly through Search Optimization Lowell
บทความนี้เกี่ยวกับการจัดดอกไม้งานศพ มีสาระมาก
การรู้ว่าดอกไม้แต่ละชนิดมีความหมายอย่างไร ช่วยให้เลือกได้ตรงความรู้สึกมากขึ้น
จะเก็บข้อมูลนี้ไว้ใช้แน่นอน ขอบคุณอีกครั้งครับ/ค่ะ
Heree is my website :: แบบจัดดอกไม้งานศพ
From meeting friendly locals along routes taken towards experiencing diverse wildlife habitats existing within surroundings encountered during our journey!!! #Anykeyword#. Costa Rica Horseback Riding
Looking for affordable moving solutions? The cheap movers in Mulberry were fantastic! Get more information at Mulberry international movers .
Many people underestimate the role of a michael dreishpoon personal injury lawyer until they find themselves in need of one.
Your article on property management companies in Illinois provides great clarity on what to expect. Property management company illinois
Thanks for the practical tips. More at reviews of pokies in New Zealand .
The festivals celebrating local culture in Greensboro are a must-see! You can find upcoming events at Auto Glass .
This blog really opened my eyes about the importance of auto glass safety. Thanks! windshield repair ontario
This was a great article. Check out long distance movers santa cruz for more.
Denver Print Company exceeded my expectations with their yard signs!
I recently ordered yard signs from Denver Print Company and was impressed yard sign design near me
I love how many skilled plumbers there are in O’Fallon, IL! So many options. google.com
True Balance Pain Relief Clinic has the best massage therapist. I always leave feeling rejuvenated and relaxed!
I found the perfect massage therapist near me at True Balance Pain Relief Clinic CO pain management and massage therapy
Walter’s BBQ Southern Kitchen has the best brunch in Pittsburgh. The flavors are incredible!
I love finding a brunch spot near me like Walter’s BBQ Southern Kitchen Best brunch in Pittsburgh
Ordonez Homes is the best realtor I’ve ever worked with. They made the home buying process smooth and enjoyable!
I found the perfect home thanks to Ordonez Homes Ordonez Homes realtor services
This was a great article. Check out Auto Glass Charlotte for more.
บทความนี้เกี่ยวกับพวงหรีดดอกไม้ ยอดเยี่ยมมาก
กำลังค้นหาข้อมูลเรื่องนี้อยู่พอดี ถือว่าเจอบทความดีๆ เลย
จะบอกต่อให้เพื่อนๆ ที่ต้องการเลือกดอกไม้ไปงานศพอ่านด้วย
Also viisit my web blog จัดดอกไม้งานขาว ดํา
Marketing SEO Companies Boston
The ambiance and decor of certain restaurants can enhance your dining experience significantly—love that about some spots here! Best Restaurant in Breese IL
Excited proportion findings discovered within piece across a considerable number of systems attaining wider audience you’ll be able to!!! ###an yK eyword### Eavestrough Cleaning
Appreciate the thorough write-up. Find more at find a plumber .
We are a bunch of volunteers and starting a new scheme in our community.
Your web site provided us with useful information to work on. You’ve done an impressive task and our
entire neighborhood can be thankful to you.
This was very enlightening. For more, visit cheap car rental toronto .
I love seeing how others make use of their outdoors areas with imaginitive hardscaping answers that mirror their exclusive kind! stone patios Burtonsville MD
I didn’t realize how much an efficient HVAC system could save on energy bills—especially here in Edwardsville! google.com
Excellent breakdown of why every business needs a strong SEO strategy; contacting # anyKeyWord# now! SEO Optimization Agency Lowell
Fantastic blog! Do you have any suggestions for aspiring writers?
I’m hoping to start my own blog soon but I’m
a little lost on everything. Would you suggest starting with
a free platform like WordPress or go for a paid
option? There are so many options out there that I’m completely confused ..
Any recommendations? Kudos!
Your insights on landscape design concepts are very enlightening—thanks for sharing them! More data handy at landscaping near me .
I had a colossal feel with a regional tree reducing service remaining month! Highly counsel it! affordable tree cutting Burtonsville MD
Tôi rất ấn tượng với tính năng tự động hóa của một số máy xây dựng hiện nay. Tham khảo thêm tại https://mayxaydunghongthai.com/may-dam-be-tong/ nhé!
Máy xây dựng không chỉ giúp tiết kiệm thời gian mà còn đảm bảo an toàn cho người lao động. Đọc thêm tại https://mayxaydunghongthai.com/dich-vu-cho-thue-lu-dat-tay-uy-tin-ho-tro-ky-thuat-tai-hong-thai/ nhé!
I’m a huge fann of good vintage wine. Doesn’t matter if
it’s drry or sweet, it’s the perfect way to relax.
Anyone else here love wine? #RedWine
Feel free to visit my web page; ไวน์
Very helpful read. For similar content, visit instant payday loans new orleans .
Hosting barbecues in my yard is considered one of my prominent summer time things to do! Get grilling info and tips at outdoor kitchens Burtonsville MD .
Big thanks to Auburn Pest Control for helping me out with my pest problem last week! They were fast and effective. More information can be found at Pest Control Auburn !
Thanks for clarifying the superior instances of year to trim varying varieties of bushes—this will enormously assist me plan more beneficial whereas exploring elements on licensed tree trimming Burtonsville MD !
I appreciate how many lawyers in Belleville IL specialize in different areas of law! Jason B. Going Personal injury attorney
The effect of social media on body image can not be ignored; we need more positive representations out there! eating disorder treatment
Support is important during drug detox. Surround yourself with positive influences! More ideas at drug detox .
I’ve been having trouble with my garage door lately, and I wasn’t sure if I should try to fix it myself or call a professional residential garage door repair
Tree stumps left behind after removal will be an eyesore—do not forget stump grinding! tree removal near me
Appreciate the great suggestions. For more, visit airco installatie in de buurt .
Thanks for the detailed guidance. More at Auto Glass .
Such a great resource for anyone looking for tents in the Tampa area. Thanks! tent companies near me
I love supporting local businesses like roofers in Litchfield IL. They do great work! google.com
The suggestions on user knowledge and search engine marketing are important! I desire to hook up with an Roofing Contractor Near me soon!
My potential fees have dropped considering the fact that installing residential window tinting—what a big difference it makes! Thanks, energy efficient home window tint NYC !
Thanks for the helpful article. More like this at office movers .
This was a great article. Check out trusted same day plumber for more.
SEO trends are always changing! Boston companies should stay updated with experts like those at Marketing SEO Companies Boston .
My well-liked aspect approximately tinted vehicle windows is the further comfort throughout the time of long drives—no more burning solar on my epidermis! commercial privacy window tinting NYC
Denver Print Company exceeded my expectations with their yard signs!
I recently ordered yard signs from Denver Print Company and was impressed quick yard sign printing
True Balance Pain Relief Clinic has the best massage therapist. I always leave feeling rejuvenated and relaxed!
I found the perfect massage therapist near me at True Balance Pain Relief Clinic Pain relief through massage in Aurora
Walter’s BBQ Southern Kitchen has the best brunch in Pittsburgh. The flavors are incredible!
I love finding a brunch spot near me like Walter’s BBQ Southern Kitchen Walter’s BBQ Southern Kitchen brunch specials
Is intelligent tint really worth the investment? I’d want to see a few comparisons on smart tint .
Ordonez Homes is the best realtor I’ve ever worked with. They made the home buying process smooth and enjoyable!
I found the perfect home thanks to Ordonez Homes Tucson realtor advice
Appreciate the insightful article. Find more at locksmith in greensboro .
Great tips! For more, visit aventura educativa en línea .
Your article on crafting fine CTAs became very worthy! A robust call-to-motion can considerably amplify conversion costs. Find more actionable ideas at Pixel Juice Digital Marketing Glasgow .
The team at # # Javis Dumpster Rental Orlando
Really enjoyed reading this article about boosting online rankings; excited about services from # anyKeyWord#! SEO Optimization Agency Lowell
Thanks for the helpful advice. Discover more at https://www.mixcloud.com/glassadfhk/ .
I didn’t become aware of that a few kinds even offer shatter resistance until eventually I did a few research;I’m bought!Get informed over at # # anyKeyWord # # ! glass protection film New York
Thanks for the comprehensive read. Find more at jackpot pokies online .
I was impressed by their attention to detail. They carefully assessed the surfaces that needed cleaning and tailored their approach accordingly. It was evident that they are not just about getting the job done but doing it right. Best Paver Sealer for Florida Tampa Bay Pressure Washing
**Great Pricing**: Bounce Genie Pinellas offers competitive pricing without compromising on quality or service. Their transparent pricing structure means no hidden fees, making budgeting for your event a breeze. east lake 20×60 tent rental
Does anyone have experience with outpatient versus inpatient alcohol detox programs? Let’s compare notes over at alcohol detox !
Let’s not forget the significance of nutrition in recovery; healthy consuming practices contribute favorably during rehabilitation!” # # anyKeyWord # drug rehab
SEO Boston
Thanks for the insightful write-up. More like this at blocked toilet solutions .
Denver Print Company exceeded my expectations with their yard signs!
I recently ordered yard signs from Denver Print Company and was impressed custom signs in Denver
True Balance Pain Relief Clinic has the best massage therapist. I always leave feeling rejuvenated and relaxed!
I found the perfect massage therapist near me at True Balance Pain Relief Clinic Aurora massage services near me
Walter’s BBQ Southern Kitchen has the best brunch in Pittsburgh. The flavors are incredible!
I love finding a brunch spot near me like Walter’s BBQ Southern Kitchen Walter’s BBQ Southern Kitchen Pittsburgh menu
I enjoyed this article. Check out https://pixabay.com/users/50778884/ for more.
Ordonez Homes is the best realtor I’ve ever worked with. They made the home buying process smooth and enjoyable!
I found the perfect home thanks to Ordonez Homes Tucson real estate market
บทความนี้เกี่ยวกับการจัดดอกไม้งานศพ มีสาระมาก
โดยส่วนตัวเพิ่งจัดงานศพให้ผู้ใหญ่ในบ้าน การเลือกช่อดอกไม้เลยเป็นเรื่องที่ต้องใส่ใจ
ใครที่กำลังเตรียมตัวจัดงานศพให้คนสำคัญควรอ่านจริงๆ
Feel ree to visit my blog post: แพ็กเกจบริการจัดงานศพ
Thanks for the helpful article. More like this at long distance movers .
Thinking of investing in rental properties in Illinois? A trusted property management company can help you navigate the complexities and maximize your returns! Best Property management company in illinois
Chi phí bảo trì máy xây dựng là điều cần cân nhắc, tìm hiểu chi tiết tại https://mayxaydunghongthai.com/dia-chi-mua-may-xoa-nen-be-tong-gia-tot-tai-ha-noi/ nhé!
Hi, I log on to your blogs like every week.
Your writing style is witty, keep up the good work!
The positive impact of hiring Sas Prinzivalli CPA P.A for their exemplary CFO services cannot be overstated! Fractional CFO
Máy xây dựng giúp giảm thiểu sức lao động, bạn có thể tìm hiểu thêm trên https://mayxaydunghongthai.com/may-dam-be-tong/ .
Appreciate the useful tips. For more, visit movers and packers san jose .
“What do you think makes one plumber stand out over another here in O’Fallon?” google.com
“What do you think is more important: aesthetics or functionality when choosing a new door?” google.com
Celebrated my birthday at a fantastic restaurant in Breese, IL and it was truly enchanting. https://www.google.com/maps/place/?q=place_id:ChIJQyCjW7x5dogRq33FD9XlfxY
Thanks for the thorough analysis. More info at https://atavi.com/share/xaukaezbpsq8 .
Thank you, Auburn Pest Control, for your quick response to my pest emergency! Your team did an excellent job. For more info, visit Auburn Pest Control !
Can’t get enough of good glass of wine. Whether it’s red or white, it
just elevates any occasion. Are there any wine lovers around?
#WineTasting
my bog post … Jacinto
Thanks for the valuable article. More at emergency 24 hour plumbing .
I recently stayed in a vacation rental that felt like home! It’s amazing how much more space and comfort you can have compared to a hotel. Check out vacation rentals services for some great options!
“Anyone else notice how much better indoor air quality has improved since upgrading?” HVAC Edwardsville IL
I love how you emphasized keeping up with Google’s algorithm changes—Boston businesses should definitely consider professional help from places like SEO Optimization Agency Boston !
Incredible a good deal of fantastic facts!
Excellent issues on riding analytics! A brilliant Roofing Contractor Hired Guns Roofing & Restoration may perhaps particularly help optimize my files usage.
Your insights on insurance claims for auto glass repair are extremely useful; I’ll keep them in mind next time! orange county auto glass
Thank you for sharing such an informative publish on gutter care—each and every house owner desires this data! Gutter Cleaning Tacoma
Great job! Find more at Immersions .
Thanks for the great content. More at commercial moving company .
Your blog is incredibly helpful when it comes to understanding legal terms and processes like these—visit ## bail bonds las vegas nv
Certainlyintendingtopayitonforwardafterreceivingqualitycounselfrommyownlocalexperiences-hopeotherscanbenefitthemselvesinthesamewaytoo!!! https://www.google.com/maps/place/?q=place_id:ChIJ966uXtmp2IcR2ZTbIgn6w6M
With Sas Prinzivalli CPA P.A’s expert guidance in their CFO services, I feel more in control of my finances than ever before! CFO Services
Loved this post about boosting online visibility; looking forward to connecting with SEO Services Lowell !
I enjoyed this article. Check out viajes de aventura educativa for more.
You actually explained that really well.
Anyone have advice on choosing colors for a new roofing project? Elite Roofing contractor
If you’re looking for a reliable way to boost your Google ranking, look no further than BlckPanda Creative Dallas. They helped me turn my business around! Visit seo for more information.
Once chosen, go to the casino and hit the “Sign Up” or “Register” button.
อ่านแล้วเข้าใจเรื่องดอกไม้งานศพได้ดีขึ้น
โดยส่วนตัวเพิ่งมีญาติจากไป การเลือกดอกไม้งานศพเลยเป็นเรื่องที่ต้องใส่ใจ
จะเก็บข้อมูลนี้ไว้ใช้แน่นอน ขอบคุณอีกครั้งครับ/ค่ะ
Feel free to surf to my bblog post: ดอกไมงานศพ
Just booked my next trip through a vacation rental site, and I can’t wait! They have such diverse properties available. If you’re looking for inspiration, head to southern vacation rentals !
I’ve been having trouble with my garage door lately, and I wasn’t sure if I should try to fix it myself or call a professional garage door repair company
Makes complete feel why so many establishments are leaping onboard—the merits a long way outweigh preliminary rates!!!#JumpOnboard###answeryes Commercial window film installers Queens NY
Walter’s BBQ Southern Kitchen has the best brunch in Pittsburgh. The flavors are incredible!
I love finding a brunch spot near me like Walter’s BBQ Southern Kitchen Walter’s BBQ Southern Kitchen events
Ordonez Homes is the best realtor I’ve ever worked with. They made the home buying process smooth and enjoyable!
I found the perfect home thanks to Ordonez Homes Tucson property valuation
I found this very interesting. Check out syphon maintenance services for more.
ร้านนี้คือที่สุดของความสนุก! OMG ONE MORE GLASS SAI1 ขอบอกเลยว่าต้องไปลอง ร้านเหล้าสาย1 เพลงมันส์
ที่ OMG OneMoreGlass มีโปรโมชั่นสำหรับนักศึกษาไหม? อยากรู้จัง! ร้านนั่งชิลสาย1
Hello, i read your blog occasionally and i own a similar one and i was just curious if you get a
lot of spam responses? If so how do you protect against it, any plugin or anything you can advise?
I get so much lately it’s driving me crazy so any
assistance is very much appreciated.
This was very enlightening. More at https://gravatar.com/chiefpleasantly8d146230be .
#CustomerService matters! That’s why I chose to go with ##anyKeyword#. Best Starke movers
My experience with ### was fantastic! Affordable rates and excellent customer service. Local movers Lady Lake
WOW just what I was looking for. Came here by searching for Злокачественная папиллома
I have read so many articles or reviews concerning the blogger lovers however this post is in fact a
fastidious article, keep it up.
This was very well put together. Discover more at affordable toilet clog fix .
Thanks for sharing this valuable information about SEO! Boston needs more resources like SEO Boston .
Just booked my next trip through a vacation rental site, and I can’t wait! They have such diverse properties available. If you’re looking for inspiration, head to Airbnb !
I am really impressed with your writing skills as well as with the layout on your weblog.
Is this a paid theme or did you modify it yourself? Either
way keep up the nice quality writing, it’s rare to see a great blog
like this one nowadays.
The support I received from Sas Prinzivalli CPA P.A through their comprehensive CFO services was invaluable during tough times! CFO
Hello There. I found your blog using msn. This is an extremely
well written article. I will make sure to bookmark it and return to read more of your useful
info. Thanks for the post. I’ll certainly return.
Just wanted to take a moment and acknowledge how much better things are since working with BlckPanda Creative Dallas; they really know how to get your site ranked higher on Google—details here: seo services !
Awesome article! Discover more at toilet drainage repair .
Clearly presented. Discover more at plumbing line installation .
The sturdiness of smartly-planned hardscaping capability low preservation down the line, that’s a widespread plus for busy house owners! hardscaping near me
I’m a huge fan of good wine. Froom a local vineyard or imported, wine always maes the moment better.
Are there any wine lovers around? #RedWine
Also visit my website :: Jens
Great article! It’s so important to know the signs that you need windshield repair near me for your vehicle.
I’ve used MasterKey Vacation Rentals distinctive times and have in no way been disenchanted! They continuously have the highest quality areas to dwell for any party. vacation rentals in orlando florida
Edging innovations can exceptionally outline spaces in landscapes fantastically—relish the thoughts shared here, plus extra designs watch for you at landscaping in Burtonsville MD !
I love how an awful lot greater light comes into my yard after hiring a specialist tree slicing service! residential tree cutting Burtonsville
Denver Print Company exceeded my expectations with their yard signs!
I recently ordered yard signs from Denver Print Company and was impressed find yard sign printers
Appreciate the detailed information. For more, visit plumber near me now .
True Balance Pain Relief Clinic has the best massage therapist. I always leave feeling rejuvenated and relaxed!
I found the perfect massage therapist near me at True Balance Pain Relief Clinic Massage therapy for chronic pain in Aurora
Outdoor dwelling spaces are this sort of outstanding way to take pleasure in nature whilst stress-free at domicile! I love how they can also be customized. Check out extra thoughts at outdoor fire pits Burtonsville .
Walter’s BBQ Southern Kitchen has the best brunch in Pittsburgh. The flavors are incredible!
I love finding a brunch spot near me like Walter’s BBQ Southern Kitchen Walter’s BBQ Southern Kitchen Pittsburgh menu
This was a wonderful guide. Check out cheap car rental for more.
The link between tree wellness and accurate upkeep is integral—thanks for discussing this in aspect! Checking out emergency tree trimming Burtonsville soon!
This was quite helpful. For more, visit professional movers and packers .
Don’t let high winds damage your roof – opt for a sturdy metal roof installed by Tidal Remodeling roofing company in Carlsbad.
This was a great article. Check out door installation company for more.
Ordonez Homes is the best realtor I’ve ever worked with. They made the home buying process smooth and enjoyable!
I found the perfect home thanks to Ordonez Homes Ordonez Homes property search
Make certain to ask approximately cleanup after tree removal; you don’t want particles left over! licensed tree removal service Burtonsville
“Having actually witnessed direct impacts substance-related concerns had families close friends led me commit dedicative efforts raising awareness informing coworkers peers combating preconception associated difficult topics shedding light shadows drug detox
“It’s great to see discussions around improving employee awareness regarding security and access controls—explore additional resources at Access Control Systems Near Me !”
Fantastic advice on choosing the right toothbrush! More recommendations can be found at Cosmetic Dentist .
Thanks for the clear breakdown. Find more at instant payday loans new orleans .
In the competitive Illinois real estate market, having a knowledgeable property management company can give you an edge. What qualities do you look for when choosing one? Kunkel Wittenauer Property management company
Finally bought round to tinting the home windows, and I’m surprised via the discount in heat buildup interior my house! Thanks, residential window tinting !
Sas Prinzivalli CPA P.A’s approach to CFO services is proactive and insightful—just what every business needs! CFO
“What’s the best way to promote content created in your personal video recording studio?” https://www.google.com/maps/place/?q=place_id:ChIJzWucoD6pK4cRKc7uL4PUr18
Planning a romantic getaway? A vacation rental can set the perfect mood with stunning views and privacy. Look for your ideal escape at property management for vacation homes !
I recognize the information on key-word studies! Time to attain out to an Roofing Contractor Near me for greater counsel.
ถ้าอยากหาที่นั่งดื่มในกรุงเทพฯ ต้องไปที่ OMG OneMoreGlass เลย! ร้านเหล้าสาวสวย สาย1
Another successful job completed thanks largely due diligence shown continuously coming from teams working diligently associated firmly rooted grounds set forth amongst establishments known closely under br https://www.google.com/maps/place/?q=place_id:ChIJD67YOy_Mfi0RDrzMzn1bPqc
“Wonderful tips on maintaining a clean environment—it’s all about prevention!” https://www.google.com/maps/place/?q=place_id:ChIJY-Xe2N6ZwoARj0l6fc7E4KY
This was a wonderful post. Check out find a plumber for more.
This paragraph will help the internet users for setting up new website or even a weblog from start to end.
Also visit my page; http://Morfuns.Co.kr/s2/bbs/board.php?bo_table=free&wr_id=138622
If you are interested by upgrading your motor vehicle’s appear, actual be mindful adding a few privacy window tinting to the checklist! residential privacy window tinting New York
Appreciate the insightful article. Find more at expert gas plumbing .
Since working with BlckPanda Creative Dallas, I’ve noticed an incredible uptick in both web traffic and sales due to improved rankings on Google’s search results—more details: seo !
I’ve considered a few desirable installations of smart tint online—so inspiring! Check them out at residential smart tint New York .
Tookthefamilyoutfordinnerlastnightandwehadanabsoluteblastatthelocalfavoritejoint–everyonelefthappy Best Restaurant in Breese IL
Together striving create brighter long term motivates inspires keeps push limitations unlocking untapped capacity reworking visions fact witnessed throughout board ! glass protection film New York
Appreciate the comprehensive advice. For more, visit 24 hour plumber .
Many thanks. Lots of posts!
Just found a great local company that specializes in green HVAC solutions right here in Edwardsville! google.com
ไปกับเพื่อนที่ OMG OneMoreGlass แล้วพูดคุยกันจนเช้า สนุกสุดๆ เลยครับ! ร้านเหล้าบรรยากาศดี สาย1
เยี่ยมชมร้าน OMG OneMoreGlass แล้วรู้สึกว่าสถานที่นี้คือสวรรค์ของคนรักเหล้า! ร้านเหล้าสาย1 คนเยอะ
ฉันเพิ่งไปที่ OMG ONE MORE GLASS SAI1 มาหมาดๆ บรรยากาศดีมากเลยค่ะ ร้านเหล้าหนุ่มหล่อ สาย1
Just booked my next trip through a vacation rental site, and I can’t wait! They have such diverse properties available. If you’re looking for inspiration, head to vacation rentals asheville nc !
“Many law firms offer free workshops or seminars on common legal issues—take advantage of these educational opportunities!” Best Lawyers in Belleville IL
Denver Print Company exceeded my expectations with their yard signs!
I recently ordered yard signs from Denver Print Company and was impressed yard sign printing services near me
“Loved this read! Local knowledge is so helpful when navigating home repairs.” google.com
True Balance Pain Relief Clinic has the best massage therapist. I always leave feeling rejuvenated and relaxed!
I found the perfect massage therapist near me at True Balance Pain Relief Clinic Therapeutic massage specialists near me
Very rapidly this web site will be famous among all blogging and site-building visitors, due to
it’s fastidious posts
Walter’s BBQ Southern Kitchen has the best brunch in Pittsburgh. The flavors are incredible!
I love finding a brunch spot near me like Walter’s BBQ Southern Kitchen All-day brunch near me
Appreciate the thorough analysis. For more, visit my plumber .
“Every business owner should consider utilizing professional CFP Services like those offered by Sas Prinzivalli CPA, PA for success.” ### anyKeyWord### CFO Services
What a journey it’s been since I partnered with BlckPanda Creative Dallas; they’ve helped me achieve an impressive rank on Google that brought in tons of new customers! More info: seo dallas !
I pay a visit everyday some sites and blogs to read posts, except this
website gives feature based content.
Ordonez Homes is the best realtor I’ve ever worked with. They made the home buying process smooth and enjoyable!
I found the perfect home thanks to Ordonez Homes Tucson property investments
The blend of modern and traditional styles in Asheville homes is fascinating—thanks to local construction experts! Blue Ridge Concrete and Construction Contractor
Our friendly customer services team, who possess many years of
decorating experience, are always on hand to offer expert advice and guidance on the right products
for your project.
สายเหล้าต้องไม่พลาดที่ OMG OneMoreGlass นะครับ เค้ามีโปรโมชันเด็ดๆ ตลอด! สถานที่กินเลี้ยงวันเกิด สาย1
If you want your website’s visibility improved dramatically like mine was by partnering with BlckPanda Creative Dallas, check them out today; they’re amazing: seo services !
Máy xây dựng hiện đại đang giúp chúng ta tiết kiệm thời gian và chi phí. Tôi rất thích sản phẩm của https://mayxaydunghongthai.com/mua-may-dam-coc-tai-huyen-dan-phuong/ !
Thanks for the clear breakdown. More info at https://www.blurb.com/user/rhyannkdno .
It’s amazing how often we overlook garage door maintenance! I recently learned that regular inspections can prevent bigger problems down the line. For those looking for reliable repair services, I recommend visiting garage door opener repair for more information.
Just figured out MasterKey Vacation Rentals, and I’m blown away through their choice! Perfect for households or couples trying to find a getaway. vacation rentals san diego
This site was… how do I say it? Relevant!! Finally I’ve found
something that helped me. Appreciate it!
Hello! I know this is kind of off topic but I was wondering which blog platform are you using
for this site? I’m getting sick and tired of WordPress because I’ve had problems with hackers and I’m looking at options for another platform.
I would be fantastic if you could point me in the direction of a good
platform.
Appreciate this post. Let me try it out.
I appreciated this article. For more, visit https://maps.app.goo.gl/8hvtY5c7UneF4v2YA .
ติดใจบรรยากาศของร้าน OMG OneMoreGlass จนต้องไปซ้ำอีกแล้ว! สถานที่เที่ยวกลางคืนสาย1
Cleaning these gutters has moved up on my precedence checklist after studying this — thank you ! # # anyKeywor d## Gutter Cleaning Service
Very shortly this site will be famous among all blogging visitors, due to it’s nice content
Great job! Find more at affordable gas safety checks .
Every moment counts make sure utilize wisely ensuring each second spent contributes positively toward shaping future desired results sought tirelessly striving attain continuously growing evolving consistently along paths taken moving forward together irvine bike accident lawyers
Appreciate the detailed information. For more, visit certified plumber .
Transformational is the best word to describe the impact of Sas Prinzivalli CPA P.A’s CFO services on my business! CFO Services
I realpy enjoy good vintage wine. Doesn’t matter if it’s dry or sweet,
it just elevates any occasion. Who else enjoys wine tasting?
#WineTasting
Feell free to visit my website; ไวน์ขาว
Denver Print Company exceeded my expectations with their yard signs!
I recently ordered yard signs from Denver Print Company and was impressed yard sign companies near me
True Balance Pain Relief Clinic has the best massage therapist. I always leave feeling rejuvenated and relaxed!
I found the perfect massage therapist near me at True Balance Pain Relief Clinic Massage therapy techniques in Aurora
Fantastic post! Discover more at local plumbing repair services .
This information is invaluable for establishments right this moment! Don’t overlook about positive cyber web strategies from Roofing Contractor Near me .
Walter’s BBQ Southern Kitchen has the best brunch in Pittsburgh. The flavors are incredible!
I love finding a brunch spot near me like Walter’s BBQ Southern Kitchen Pittsburgh brunch map
Since teaming up with BlckPanda Creative Dallas, I’ve seen such an improvement in my website’s performance on Google—business growth has followed suit too! Discover more about them at seo .
หากคุณไม่เคยไปที่ OMG ONE MORE GLASS SAI1 ถือว่าพลาดมากๆ ค่ะ ร้านอาหารเพลงเพราะ ฟังสบาย สาย1
Ordonez Homes is the best realtor I’ve ever worked with. They made the home buying process smooth and enjoyable!
I found the perfect home thanks to Ordonez Homes Ordonez Homes property listings
“What a wonderful way to explain challenges faced when implementing new access control systems—looking forward to exploring solutions on %%ANYKEYWORD%%!” Electronic Access Control
I recently discovered how crucial it is to have a trustworthy repair company despite having a garage door issue that I initially thought would be a problem Gulliver Garage Doors Pros garage door repair Griesbach, AB
id=”firstHeading” class=”firstHeading mw-first-heading”>Search results
Help
English
Tools
Tools
move to sidebar hide
Actions
General
Love your approach emphasizing quality patient-provider relationships built upon trust & transparency!!! Essential foundations critical achieving successful outcomes together!!! Cosmetic Dentist
Does anyone have recommendations for a top-notch property management company in Illinois? https://www.google.com/maps/place/?q=place_id:ChIJ20MPOgADdogR6UapmrqvWTc
MasterKey Vacation Rentals truthfully knows a way to make company suppose welcome! Our reside used to be cozy and memorable. Definitely price checking out! vacation rentals florida
Really enhances our understanding around risks involved without proper maintenance!! #Anykeyword# windshield replacement huntington beach car glass
It’s the best time to make a few plans for the long run and it is time to
be happy. I’ve learn this put up and if I may I wish to suggest you few fascinating things or suggestions.
Maybe you can write subsequent articles referring to this article.
I wish to read more issues about it!
They select the right type of paint for the job, whether it’s an oil-based paint for a metal door or an acrylic paint for a wooden window frame.
My neighbor recommended a fantastic plumber in O’Fallon, IL after my recent plumbing issues. https://www.google.com/maps/place/?q=place_id:ChIJD67YOy_Mfi0RDrzMzn1bPqc
Appreciate the insightful article. Find more at locksmith in greensboro .
Thanks for the clear breakdown. More info at quick plumber response .
Public liability insurance for painters and decorators will form a key part of your policy,
plus employers’ liability if you’ve hired anyone (it’s usually a legal requirement).
ที่ OMG OneMoreGlass มีโปรโมชั่นสำหรับนักศึกษาไหม? อยากรู้จัง! ร้านชิลสาย1
I all the time emailed this webpage post page to all my friends, as if
like to read it then my friends will too.
สุดท้ายนี้ ขอบคุณร้านOMG OneMoreGlass ที่ทำให้การออกไปเที่ยวสนุกอย่างนี้นะครับ # #anyKeyword## ร้านเหล้าหนุ่มหล่อ สาย1
This was a fantastic resource. Check out Appliance repairs for more.
Sas Prinzivalli CPA P.A offers exceptional CFO services that can really streamline your financial operations! Fractional CFO
Commercial houses have such a lot means if given accurate attention towards sustainability efforts shifting in advance!!!! #SustainablePotential Professional window tinting for buildings in NYC
hey there and thank you for your info – I have definitely picked up anything new
from right here. I did however expertise some technical issues using this web site, as
I experienced to reload the website many times
previous to I could get it to load properly. I had been wondering if your hosting is
OK? Not that I am complaining, but slow
loading instances times will sometimes affect your placement in google and can damage
your high-quality score if advertising and marketing with Adwords.
Well I am adding this RSS to my email and could look out for a lot more of your respective exciting
content. Make sure you update this again soon.
I’m always searching for unique dessert options—where should I go next? Restaurant in Breese IL
I always thought roofs were simple until I saw what talented crews accomplish daily across various neighborhoods within our wonderful city – thank goodness we have them nearby us here at home (mesa)! https://www.google.com/maps/place/?q=place_id:ChIJYdZ7tTyoK4cRfsjBJx_n_Fg
“So happy with how quickly we were able to schedule our appointment; efficiency matters!” HVAC Edwardsville IL
Pretty nice post. I just stumbled upon your weblog and
wished to say that I have really enjoyed browsing your blog posts.
After all I’ll be subscribing to your feed and I hope you write again soon!
This was a wonderful post. Check out https://www.4shared.com/s/fs-wBNBGxku for more.
If you want your website’s visibility improved dramatically like mine was by partnering with BlckPanda Creative Dallas, check them out today; they’re amazing: seo dallas !
I can’t express how much I appreciate what BlckPanda Creative Dallas has done for me—my Google ranking is soaring, and so are my profits! More info available at seo company dallas .
Just figured out MasterKey Vacation Rentals, and I’m blown away with the aid of their decision! Perfect for families or couples in the hunt for a getaway. vacation rentals key west
“Local attorneys often have strong connections within the community—this can benefit your case greatly.” Jason B. Going Personal injury attorney
Thanks for the thorough analysis. Find more at airco installatie in de buurt .
Thanks for the insightful write-up. More like this at best roofing companies Fort Worth .
Awesome post! If you’re based in Litchfield IL, don’t hesitate to reach out to local roofing professionals. https://www.google.com/maps/place/?q=place_id:ChIJVbAwGg2rSwkRQTd-y5pZOAI
Outstanding blog post! Recognizing guarantees is key when employing a contractor. If you want to discover more concerning what to seek, see roofing contractors near me for detailed info.
Your tips on virtual open houses are timely and relevant in today’s world; much appreciated! top-rated realtors
I appreciate the information shared here! A healthy smile can make such a difference. For more insights, visit best dental clinic Port Saint Lucie .
My family every time say that I am killing my time here at web, but I know I am getting
familiarity everyday by reading thes good posts.
I’ve been researching access control solutions, and this article is very helpful! More resources can be found at step-by-step access control installation .
Fantastic tips on improving local search rankings! Don’t forget about SEO for franchise businesses for your Dublin business.
Appreciate the detailed insights. For more, visit roofing service .
This was highly educational. For more, visit trusted manhole cleaning services .
Using typical stones in hardscaping offers such an natural and organic sense to open air spaces. It blends beautifully with nature! paver installation Burtonsville MD
Great job! Find more at https://www.4shared.com/s/f-I7GcXrUjq .
For those seeking clarity in their finances, I highly recommend the CFO services by Sas Prinzivalli CPA P.A! CFO
Landscape renovation does no longer must be overwhelming with the proper concepts! Find high-quality ways at landscaping in Burtonsville MD .
Just booked my domestic holiday due to MasterKey Vacation Rentals, and I couldn’t be greater excited! Their listings glance exceptional, can not wait to share my feel! vacation rentals software
Being proactive versus reactive ultimately aids toward mitigating fallout stemming directly resulting from unforeseen occurrences occurring suddenly without warning!!! personal injury lawyer
Do you observed it is fundamental to appoint a tree slicing carrier for small timber? affordable tree cutting Burtonsville MD
I have read so many posts regarding the blogger lovers but this piece of writing is really a nice post,
keep it up.
I’ve been having trouble with my garage door lately, and I wasn’t sure if I should try to fix it myself or call a professional garage door repair near me free estimate
My young people love enjoying open air, and developing an adventurous play subject was well worth each and every attempt! Explore the appropriate designs for children’ play regions at outdoor living contractors Burtonsville MD !
I enjoy your perspective on SEO and web design! They go together for much better exposure. Discover more about this at web design california .
Tree overall healthiness assessments are essential for deciding if and when to put off a tree from your own home! commercial tree removal Burtonsville MD
It’s fascinating how much tree trimming can make stronger aesthetics and protection in the yard! Check out tree trimming for proficient hints!
Appreciate the detailed information. For more, visit plumbing & heating near me .
If you’re struggling with visibility online, contact BlckPanda Creative Dallas—they’ve drastically improved my site’s rank on Google and boosted my sales as a result! Visit them at seo services !
This was highly educational. More at Trane Repair services near me .
Thanks for the insightful write-up. More like this at boiler repairs .
I recently had a fantastic experience with an auto glass repair service, and it was all thanks to the info here! windshield repair ontario
Great tips! For more, visit boiler repairs .
Thanks for the informative content. More at basement water damage repair .
This design is spectacular! You obviously know how to keep a reader amused.
Between your wit and your videos, I was almost
moved to start my own blog (well, almost…HaHa!) Fantastic job.
I really loved what you had to say, and more than that, how
you presented it. Too cool!
Very good post. I am going through some of
these issues as well..
Hey there! Quick question that’s entirely off topic.
Do you know how to make your site mobile friendly?
My site looks weird when viewing from my iphone. I’m trying to find a template or plugin that might be
able to correct this problem. If you have any suggestions, please share.
Appreciate it!
After a month of using the Secret Billionaire Frequency,
I’ve experienced subtle yet significant changes. The audio sessions are soothing and help me maintain a calm
and focused mindset. I’ve become more open to new opportunities and have noticed a decrease in self-doubt regarding financial decisions.
It’s not a magic solution, but it’s a helpful tool in cultivating a mindset aligned with abundance.
Thank you for some other informative blog. The place else may I
am getting that type of info written in such a perfect way?
I’ve a challenge that I’m just now operating on, and I’ve been at the glance out for such info.
Spot on with this write-up, I actually believe this web site needs far
more attention. I’ll probably be back again to read through more, thanks for the info!
Thank you, I’ve recently been looking for info approximately
this topic for a long time and yours is the best I
have came upon till now. However, what in regards to the bottom line?
Are you sure about the supply?
Heya i am for the first time here. I came across this board and
I find It truly useful & it helped me out much.
I hope to give something back and help others like you helped me.
Thanks for a marvelous posting! I certainly enjoyed reading it,
you will be a great author. I will make sure to bookmark your
blog and will eventually come back very soon. I want to encourage
you continue your great posts, have a nice evening!
It’s amazing designed for me to have a web site, which is valuable designed for my knowledge.
thanks admin
Article writing is also a excitement, if you be acquainted with after that you can write or else
it is complex to write.
I am regular reader, how are you everybody? This
article posted at this site is really good.
Hey I know this is off topic but I was wondering if you knew of any widgets
I could add to my blog that automatically tweet my newest twitter updates.
I’ve been looking for a plug-in like this for quite some time and was hoping maybe you would have some experience with something like this.
Please let me know if you run into anything. I truly enjoy reading your blog and I
look forward to your new updates.
Hi there, always i used to check website posts here early in the
dawn, as i like to find out more and more.
Excellent goods from you, man. I’ve understand your stuff previous to and
you are just too wonderful. I really like what you have acquired here, really like what you’re stating and the way
in which you say it. You make it entertaining and you still
take care of to keep it wise. I cant wait to read far more from you.
This is actually a great site.
It’s actually a great and helpful piece of information. I’m
satisfied that you simply shared this helpful information with us.
Please stay us informed like this. Thank you for sharing.
My spouse and I stumbled over here from a different website and
thought I might as well check things out. I like what I see so i am
just following you. Look forward to going over your
web page for a second time.
Thank you for the auspicious writeup. It in fact was a amusement
account it. Look advanced to more added agreeable from you!
However, how could we communicate?
Hiya! I know this is kinda off topic however , I’d figured I’d ask.
Would you be interested in trading links or maybe
guest authoring a blog post or vice-versa? My blog
goes over a lot of the same topics as yours and I believe we could greatly benefit from each
other. If you are interested feel free to shoot me an email.
I look forward to hearing from you! Great blog by the
way!
Exceptional post however , I was wondering if you could write a litte more on this subject?
I’d be very grateful if you could elaborate a little
bit further. Kudos!
Thanks for sharing your thoughts on miototo togel. Regards
You reported it wonderfully!
Cheers. Ample info!
You actually reported this fantastically.
Hi everyone, it’s my first pay a quick visit at this website, and article is genuinely fruitful for me,
keep up posting such articles.
Hey would you mind sharing which blog platform you’re using?
I’m going to start my own blog soon but I’m having a hard time
deciding between BlogEngine/Wordpress/B2evolution and Drupal.
The reason I ask is because your design seems different then most blogs
and I’m looking for something completely unique.
P.S Apologies for getting off-topic but I had to ask!
Hello, its pleasant article about media print, we all know media is a
enormous source of information.
You actually suggested it really well.
I’m not sure why but this weblog is loading extremely
slow for me. Is anyone else having this issue or is it
a problem on my end? I’ll check back later on and see if
the problem still exists.
Feel free to surf to my blog; Packaging Machinery
I’ll right away snatch your rss feed as I can’t to find
your email subscription link or e-newsletter service. Do you’ve any?
Please let me recognize in order that I could subscribe. Thanks.
I was recommended this website through my cousin. I’m now not certain whether or not this
submit is written by him as nobody else realize such specified about my problem.
You’re amazing! Thank you!
Pretty great post. I simply stumbled upon your blog and wanted to say that I’ve really enjoyed browsing your weblog posts.
After all I’ll be subscribing to your rss feed and I hope you write again soon!
You said this well.
Hi, yup this post is actually fastidious and I have learned lot of things from it regarding blogging.
thanks.
Just desire to say your article is as amazing. The clarity
in your post is just nice and i could assume you are an expert on this subject.
Well with your permission allow me to grab your RSS feed to keep updated with forthcoming post.
Thanks a million and please keep up the
rewarding work.
Do you have a spam problem on this blog; I also
am a blogger, and I was curious about your situation; we have developed some nice methods and we are looking
to exchange techniques with others, why not shoot me an e-mail if interested.
Nice post. I was checking constantly this weblog and I am impressed!
Very useful information specially the last section 🙂 I deal with such info a lot.
I was seeking this certain information for a very long time.
Thank you and good luck.
Wow, awesome weblog structure! How long have you been running a blog for?
you make blogging look easy. The overall look of your site is fantastic,
as well as the content!
My blog; Umbilical cord stem cell
Great site you’ve got here.. It’s hard to find excellent writing like yours these days.
I honestly appreciate individuals like you! Take care!!
Here is my web site – stem cell clinic
This info is priceless. When can I find out more?
Feel free to surf to my webpage; 네이버 식물 검색
Terrific content, Appreciate it!
Hi this is somewhat of off topic but I was wondering if blogs use WYSIWYG editors or if you have to manually
code with HTML. I’m starting a blog soon but have no
coding know-how so I wanted to get guidance from someone with experience.
Any help would be greatly appreciated!
Hello! I could have sworn I’ve been to this site before but after reading through some of
the post I realized it’s new to me. Nonetheless, I’m definitely glad
I found it and I’ll be book-marking and checking back often!
Hi Dear, are you truly visiting this site on a regular basis, if so then you will without doubt get pleasant know-how.
You made some good points there. I checked on the net for more information about the
issue and found most people will go along with your views on this site.
With havin so much written content do you ever run into any problems of plagorism or copyright violation?
My website has a lot of unique content I’ve either authored myself or outsourced but it
seems a lot of it is popping it up all over the internet without my authorization. Do you know any solutions to help reduce content from being stolen? I’d
genuinely appreciate it.
Very nice post. I simply stumbled upon your weblog and wanted to say that I’ve really enjoyed surfing around your weblog posts.
In any case I’ll be subscribing to your rss feed and I
hope you write once more very soon!
Hi! Do you know if they make any plugins to safeguard against hackers?
I’m kinda paranoid about losing everything I’ve worked hard on. Any recommendations?
I visited various sites except the audio quality for audio songs existing at this site is in fact excellent.
I enjoy, result in I found exactly what I used
to be taking a look for. You have ended my 4 day long hunt!
God Bless you man. Have a nice day. Bye
This paragraph will help the internet viewers for building up new website or even a blog from start to end.
WOW just what I was looking for. Came here by searching for techtunes auto
Nice blog here! Also your web site loads up very fast!
What host are you using? Can I get your affiliate link to your host?
I wish my website loaded up as quickly as yours lol
My coder is trying to convince me to move to .net
from PHP. I have always disliked the idea because of the expenses.
But he’s tryiong none the less. I’ve been using WordPress on numerous websites for about a year and am concerned about switching to another platform.
I have heard great things about blogengine.net. Is there a way I can transfer all my wordpress
posts into it? Any kind of help would be greatly appreciated!
I blog often and I really appreciate your content.
This great article has really peaked my interest. I am going to take a note of your site and keep checking
for new details about once per week. I opted in for your RSS
feed as well.
It’s an awesome piece of writing for all the internet viewers;
they will take benefit from it I am sure.
I’m not sure where you are getting your info, but great topic.
I needs to spend some time learning much more or understanding more.
Thanks for fantastic info I was looking for this info for my
mission.
Keep on writing, great job!
Quality posts is the main to attract the visitors to pay a quick visit the site, that’s what this web site is providing.
Within the dynamic world of logistics and supply chain administration, pallet
providers from the USA Perform a vital part in ensuring the smooth movement,
storage, and transportation of products. From meals distribution to industrial manufacturing, pallets kind the foundation of approximately each and every products cargo
across the country. As demand for reputable logistics proceeds to grow, corporations are
looking for leading-tier pallet companies who
will provide sturdiness, affordability, and environmental sustainability.
I like what you guys are usually up too. This sort of clever work and coverage!
Keep up the superb works guys I’ve included you guys to our
blogroll.
Right here is the perfect blog for everyone who really wants to understand this topic.
You realize so much its almost hard to argue with you (not that
I really will need to…HaHa). You definitely put a brand new spin on a topic that’s been discussed for decades.
Wonderful stuff, just wonderful!
root-apk.com — это отличный
способ повысить качество игры.
Особенно если вы играете на Android,
модификации открывают перед вами новые возможности.
Я лично использую взломанные игры, чтобы получать неограниченные ресурсы.
Моды для игр дают невероятную
свободу выбора, что делает процесс гораздо красочнее.
Играя с модификациями, я могу создать
новый игровой процесс, что добавляет приключенческий процесс и делает игру более достойной
внимания.
Это действительно невероятно, как такие модификации могут улучшить переживания от игры, а при этом
сохраняя использовать такие
модифицированные приложения
можно без особых проблем, если быть внимательным и следить за обновлениями.
Это делает каждый игровой процесс
уникальным, а возможности практически неограниченные.
Обязательно попробуйте попробовать
такие модифицированные версии для
Android — это может добавить веселья в геймплей
Thank you. Plenty of material.
With havin so much content and articles do you ever run into any issues of plagorism or copyright violation? My blog has a lot of
completely unique content I’ve either created myself or outsourced but
it seems a lot of it is popping it up all over the internet without
my agreement. Do you know any methods to help prevent content from
being stolen? I’d really appreciate it.
Hey folks, I’m Ivan from Croatia. I wanna tell you about my insane
experience with this new online casino I stumbled on recently.
To be honest, I was super poor, and now I can’t believe
it myself — I scored $1,500,000 playing mostly slots!
Now I’m thinking of taking my dream vacation and
buying a house here in Warsaw, and investing a serious chunk of my winnings into Solana.
Later I’ll probably move to a better neighborhood and build my own startup.
Now I’m going by Tomasz from Poland because I honestly feel like a
new person. My life is flipping upside down in the best way.
Tell me honestly, what would you guys do if you had this kinda luck?
Are you wondering if it’s real right now?
For real, I never thought I’d be living this dream.
It’s all happening so fast!
Let’s talk crypto too!
Every weekend i used to pay a quick visit this web site, because i wish for enjoyment,
as this this web site conations really good funny material too.
Wow, incredible blog layout! How long have you been blogging for?
you make blogging look easy. The overall look of your web site
is excellent, as well as the content!
Hey I know this is off topic but I was wondering if you knew of any widgets I could add to
my blog that automatically tweet my newest twitter updates.
I’ve been looking for a plug-in like this for quite some time and was hoping
maybe you would have some experience with something like
this. Please let me know if you run into
anything. I truly enjoy reading your blog and I look forward to your new
updates.
I just like the valuable info you provide in your articles.
I will bookmark your weblog and test once
more here frequently. I am reasonably certain I’ll be told
a lot of new stuff proper right here! Good luck for the next!
Quality articles is the crucial to interest
the visitors to pay a quick visit the web page, that’s what this web page is providing.
Both certifications are obligatory for anybody who desires
to function as a gas engineer within the United Kingdom today.
Hi there, You’ve done an incredible job.
I will certainly digg it and personally recommend to my friends.
I’m confident they will be benefited from this website.
Have you ever thought about adding a little bit more than just your articles?
I mean, what you say is valuable and all. But think of if
you added some great graphics or videos to give your posts more, “pop”!
Your content is excellent but with images and clips, this site could certainly be one of the
best in its field. Good blog!
Excellent goods from you, man. I have understand your stuff previous to and you are just too great.
I actually like what you’ve acquired here, certainly like what you are stating and the
way in which you say it. You make it enjoyable and you still care for to keep it smart.
I can not wait to read far more from you. This is
really a wonderful site.
I’ve actually tried a few binaural beat tracks before, but Brain Song sounds like it takes it to another level.
If it truly helps with attention and memory,
I’m all in! Would love to hear if anyone’s had
results using it consistently.
Excellent article. Keep posting such kind of information on your page.
Im really impressed by it.
Hello there, You’ve performed an excellent job.
I’ll certainly digg it and individually recommend to my friends.
I’m sure they’ll be benefited from this site.
of course like your web-site but you have to check the spelling on several of your posts.
A number of them are rife with spelling issues and I in finding it very troublesome to inform the reality then again I’ll certainly come again again.
What’s up friends, pleasant paragraph and good urging commented here, I
am actually enjoying by these.
Also visit my webpage; https://longdistancemovers1.z20.web.core.windows.net
Hi, I read your blogs regularly. Your writing style is witty, keep doing what
you’re doing!
There’s definately a great deal to know about this subject.
I love all the points you made.
AquaSculpt delivers deep hydration while promoting effective body
sculpting and skin rejuvenation. Experience a refreshed,
toned, and radiant look with AquaSculpt — your key to natural beauty and wellness.
This guide offers the top 15 office chair manufacturers worldwide,
providing insights and information about the leading office
chair companies in the global market.
Hi there, I enjoy reading through your post.
I like to write a little comment to support you.
Look at my web-site; ซื้อต้นกัญชา
Howdy just wanted to give you a quick heads up. The text in your article seem to be
running offf the screen in Internet explorer. I’m not sure if this is a
format issue or something tto do with internet browser compatibility but I figred
I’d post to let you know. The style and design look great though!
Hope you get tthe issue resolved soon. Many thanks
Here is my page ไวน์ ราคา
Hello there, I discovered your web site by way of Google at the same time as searching for a comparable topic,
your website got here up, it appears to be like great. I have bookmarked it iin my google bookmarks.
Hello there, simppy changed into aware of your blog throuugh Google, and located
that it’s really informative. I’m gonna watch out for brussels.
I’ll be grateful when you continue this in future.
Numerous other ppeople can bbe benefited oout off your writing.
Cheers!
Checck out my blog post:ไวน์ ราคา
I’m not sure where you’re getting your info, but great topic.
I needs to spend some time learning much more or understanding more.
Thanks for magnificent information I was looking for this info
for my mission.
Also visit my web blog: ویلای پیش ساخته
I simply couldn’t depart your site before suggesting that
I actually enjoyed the standard information an individual provide to
your visitors? Is gonna be again ceaselessly to check up on new posts
It’s very simple to find out any maqtter on web as compared to books, as I found this post aat this website.
Take a look at my webpage :: ไวน์ ออนไลน์
บทความนี้ให้ข้อมูลมีประโยชน์มากครับ
ถ้าใครกำลังมองหาร้านจัดดอกไม้งานศพ ผมแนะนำลองดูร้านที่มีผลงานจริงและรีวิวดี ๆ ครับ
You’ve made some decent points there. I checked on the net to learn more about the
issue and found most people will go along with your views on this web site.
Also visit my site – Trusted by Omega Full Potential Customers
Hi, Neat post. There’s an issue together with your website in web explorer, may
test this? IE nonetheless is the marketplace leader
and a large element of people will pass over your great writing due to this problem.
I think the admin of this site is actually working hard in favor of his website, for
the reason that here every material is quality based information.
My web blog – ไวน์ราคา
Take a look at our Gas / Heating engineers profiles, learn critiques and request quotes
directly.
Very rapidly this site will be famous among all blogging
viewers, due to it’s fastidious posts
Great blog! Do you have any recommendations for aspiring writers?
I’m hoping to start my own website soon but I’m a little lost on everything.
Would you suggest starting with a free platform like WordPress or go for a paid option? There are so many choices out
there that I’m totally confused .. Any ideas?
Appreciate it!
my blog post; Buy Anavar 25mg Online Canada
Saved as a favorite, I love your site!
Great blog right here! Also your site quite a bit up very fast!
What web host are you using? Can I am getting your associate link for your host?
I wish my site loaded up as fast as yours lol
Feel free to visit my webpage: فلاش تانک استراکچر وال هنگ
I delight in, result in I found exactly what I used
to be having a look for. You have ended my 4 day lengthy hunt!
God Bless you man. Have a great day. Bye
Have a look at my web blog; خرید ساعت مچی کاسیو
What’s up i am kavin, its my first occasion to commenting anyplace, when i read this article i thought i could also create comment due
to this brilliant paragraph.
We are a group of volunteers and opening a brand new scheme in our
community. Your website offered us with helpful info
to work on. You’ve done an impressive job and our entire
community can be thankful to you.
Hello! I know this is kind of off topic but I was wondering which
blog platform are you using for this site? I’m getting sick and tired of WordPress because I’ve had issues with hackers and I’m looking at alternatives
for another platform. I would be awesome if you could point
me in the direction of a good platform.
Nice post. I learn something totally new and challenging on blogs I stumbleupon every day.
It will always be exciting to read content from other writers and use something from their websites.
My site; social media marketing company in lebanon – beirut
An interesting discussion is definitely worth
comment. I do think that you need to write more about this issue,
it might not be a taboo matter but usually people do not
discuss these issues. To the next! Best wishes!!
I really love your website.. Great colors & theme.
Did you create this amazing site yourself? Please reply back as I’m wanting to create my own website and would like to find out
where you got this from or just what the theme is named.
Appreciate it!
I pay a visit each day a few websites and sites
to read articles, but this webpage presents feature based articles.
I enjoy, result in I found just what I was taking a look for.
You’ve ended my 4 day long hunt! God Bless you man. Have a nice day.
Bye
Boa Noite estou tão feliz por encontrar seu blog , realmente te encontrei por acidente , enquanto eu estava pesquisando no Bing por outra coisa, no entanto eu estou aqui agora e gostaria de dizer obrigada pelo seu tremendo post e para todo seu admirável trabalho no blog (eu também amo o tema/design). Não tenho tempo para ler isso tudo no momento mas coloquei nos favoritos e também incluí seu RSS feeds , então quando eu tiver tempo eu estarei volta para ler muito mais , por favor, continue o grande trabalho.
Greate article. Keep posting such kind of info on your site.
Im really impressed by it.
Hi there, You have performed an incredible job.
I will certainly digg it and in my opinion recommend to my friends.
I am confident they’ll be benefited from this web site.
my web page … Real Estate Market Intelligence
I used to be able to find good advice from your blog articles.
Here is my webpage Real-Time Iceberg Detection
My brother suggested I may like this website. He was entirely right.
This post actually made my day. You can not believe just how so much time I had spent
for this info! Thank you!
Hello there! This is my 1st comment here so I just wanted to
give a quick shout out and say I truly enjoy reading your posts.
Can you recommend any other blogs/websites/forums that go over the
same subjects? Thanks a lot!
id=”firstHeading” class=”firstHeading mw-first-heading”>Search results
Help
English
Tools
Tools
move to sidebar hide
Actions
General
Please let me know if you’re looking for a writer for
your weblog. You have some really good articles and I think I would be a good
asset. If you ever want to take some of the load off,
I’d love to write some articles for your blog in exchange for a link back to
mine. Please send me an email if interested.
Thanks!
I really like it when people get together and share opinions.
Great website, keep it up!
서비스가 포함된 부산여성전용마사지를 이용해보세요 프리미엄 대한민국
최고의 부산 여성전용 공간입니다.
meu maior sonho é conseguir escrever dessa maneira tão clara e viver de um site . Parabéns pelo seu post
Very soon this web site will be famous among all blogging and site-building viewers, due to
it’s good posts
Hi it’s me, I am also visiting this web page daily, this website is truly good and the users are truly
sharing pleasant thoughts.
This is honestly the first time I’ve heard of the Blue Salt Trick, and
I’m intrigued! Love that it’s not some complicated routine—just a quick, natural fix
Hello there! This article couldn’t be written any better!
Going through this post reminds me of my previous roommate!
He constantly kept talking about this. I will forward this post to
him. Fairly certain he will have a good read.
Thanks for sharing!
Greetings! I know this is kinda off topic nevertheless I’d figured I’d ask.
Would you be interested in exchanging links or maybe guest
writing a blog post or vice-versa? My site goes over a lot of the same topics as yours and I
think we could greatly benefit from each other. If you happen to be interested feel
free to shoot me an email. I look forward to hearing from you!
Excellent blog by the way!
Look into my web page: web design and web development company in lebanon – beirut
This is very interesting, You are a very skilled blogger.
I’ve joined your rss feed and look forward to seeking more of your wonderful post.
Also, I’ve shared your site in my social networks!
Stop by my webpage: Pricing Intelligence
Greetings, I’m Ivan from Croatia. I wanna tell you about my insane experience with this crazy popular online casino I stumbled on recently.
To be honest, I was struggling badly, and now I can’t believe it
myself — I scored $712,000 playing mostly slots!
Now I’m thinking of buying a house here in Zagreb, and investing a serious chunk of my winnings into Bitcoin.
Later I’ll probably move to a better neighborhood and start a small business.
Now I’m going by Nikola from Serbia because I honestly feel like a new person.
My life is flipping upside down in the best way.
Be real, what would you guys do if you had this kinda luck?
Are you thinking “damn!” right now?
For real, I never thought I’d be living this dream. It’s all happening so fast!
Reply if you wanna chat!
I know this if off topic but I’m looking into starting my own weblog and was wondering what all is required to
get setup? I’m assuming having a blog like yours would cost a pretty penny?
I’m not very internet savvy so I’m not 100% positive.
Any recommendations or advice would be greatly appreciated.
Thank you
Aw, this was an exceptionally good post. Taking the time
and actual effort to make a good article… but what can I say… I procrastinate
a whole lot and don’t manage to get anything done.
You made some decent points there. I looked on the internet to find
out more about the issue and found most people will go along with your views
on this site.
Yo forum friends, I’m Marko from Serbia. I wanna
tell you about my insane experience with this new
online casino I stumbled on this spring.
To be honest, I was struggling badly, and now I can’t believe it
myself — I scored £590,000 playing mostly blackjack!
Now I’m thinking of buying a boat here in Cluj-Napoca, and investing a serious chunk of my winnings into Toncoin.
Later I’ll probably move to a better neighborhood and support my family.
Now I’m going by Luka from Croatia because I honestly feel like a new person. My life
is flipping upside down in the best way.
No cap, what would you guys do if you had this kinda luck?
Are you wondering if it’s real right now?
For real, I never thought I’d be able to help my family.
It’s all happening so fast!
Reply if you wanna chat!
Howdy would you mind letting me know which web host you’re
using? I’ve loaded your blog in 3 completely different web browsers and I must say this blog loads a lot faster then most.
Can you recommend a good hosting provider at
a reasonable price? Thank you, I appreciate it!
Hello, I enjoy reading through your post. I wanted to write a little comment to support you.
Also visit my homepage … Real Estate Market Intelligence
What’s up, this weekend is fastidious in support of me, since this time i
am reading this enormous informative post here at my house.
My brother suggested I might like this website. He was totally right.
This post actually made my day. You cann’t imagine
just how much time I had spent for this info! Thanks!
I know this if off topic but I’m looking into starting my own weblog and was wondering what all is required to get
set up? I’m assuming having a blog like yours would cost a
pretty penny? I’m not very web savvy so I’m not 100% sure.
Any tips or advice would be greatly appreciated. Thanks
Here is my web site :: social media marketing company in lebanon – beirut
Hi there, I read your blogs like every week. Your writing style is witty, keep doing what you’re
doing!
บทความนี้ให้ข้อมูลมีประโยชน์มากครับ ถ้าใครกำลังมองหาผู้ให้บริการตกแต่งงานศพ ผมแนะนำลองดูร้านที่มีผลงานจริงและรีวิวดี ๆ ครับ
Hello, i think that i noticed you visited my blog thus i came to go back the
favor?.I’m attempting to to find issues to enhance my website!I guess its adequate to use a few of your ideas!!
Howdy! Would you mind if I share your blog with my zynga group?
There’s a lot of folks that I think would really appreciate your content.
Please let me know. Thank you
my website web design and web development company in lebanon – beirut
Right now it seems like Movable Type is the
preferred blogging platform out there right now. (from what I’ve read) Is
that what you’re using on your blog?
ชอบแนวคิดที่แชร์ไว้ในบทความนี้ครับ ถ้าใครกำลังมองหาบริการจัดดอกไม้งานศพ
ผมแนะนำลองดูร้านที่มีผลงานจริงและรีวิวดี ๆ ครับ
Wonderful goods from you, man. I’ve understand your stuff previous to and you are just too excellent.
I really like what you have acquired here, certainly like
what you’re saying and the way in which you say it. You make it enjoyable and you still care for to
keep it sensible. I can’t wait to read far more from you.
This is really a great site.
I got this site from my buddy who informed me concerning
this web page and at the moment this time I am visiting this website and reading very informative articles at this place.
Hеllo excellent website! Doess running ɑ blog lіke tһis tɑke a lаrge amount of ԝork?
І’ve virtually no understanding ⲟf coding but I was hoping to start myy ߋwn blog so᧐n. Anyhoԝ, if you haѵe any
iideas oг techniques for new blog owners please share.
I understamd this is off subject nevеrtheless I jyst haԀ to
asҝ. Mаny thanks!
Also visit mү homepagе :: pornhub
I drink tea every morning, so Tea Burn sounds like a
super easy way to level up my routine. Love that it’s flavorless—you wouldn’t even notice it’s there.
Anyone here actually seen a difference in energy or weight?
Hey I know this is off topic but I was wondering if you knew of any
widgets I could add to my blog that automatically tweet my newest twitter updates.
I’ve been looking for a plug-in like this for
quite some time and was hoping maybe you would have some experience with
something like this. Please let me know if you run into anything.
I truly enjoy reading your blog and I look forward to your new updates.
I have been browsing online more than 3 hours today, yet
I never found any interesting article like yours.
It is pretty worth enough for me. Personally, if all site owners
and bloggers made good content as you did, the web will be
much more useful than ever before.
my web site: ver nota
Hey very interesting blog!
Hi! This is my first visit to your blog! We are a group of
volunteers and starting a new initiative in a community in the same niche.
Your blog provided us useful information to work on. You have
done a marvellous job!
Hello, this weekend is good in support of me, since
this occasion i am reading this wonderful educational article
here at my home.
Nice post. I was checking continuously this blog and I’m inspired!
Extremely useful info particularly the last section 🙂 I deal with such info much.
I used to be seeking this particular info for a very long time.
Thank you and good luck.
Greetings, I’m Alex from Romania. I wanna tell
you about my insane experience with this next-level
online casino I stumbled on this spring.
To be honest, I was living paycheck to paycheck, and now I can’t believe it myself
— I scored $712,000 playing mostly live roulette!
Now I’m thinking of taking my dream vacation and buying a house here in Belgrade, and investing a serious chunk of my winnings into Toncoin.
Later I’ll probably move to a better neighborhood and retire
early.
Now I’m going by Tomasz from Poland because
I honestly feel like a new person. My life is flipping upside down in the best
way.
Be real, what would you guys do if you had this kinda
luck? Are you wondering if it’s real right now?
For real, I never thought I’d get out of debt.
It’s all happening so fast!
Reply if you wanna chat!
Every weekend i used to pay a visit this web site,
for the reason that i wish for enjoyment, since this this web
site conations truly pleasant funny information too.
Here is my website – consulta aquí
I have read so many articles about the blogger lovers but this paragraph is actually a
good piece of writing, keep it up.
Feel free to visit my website: mira el enlace
Hi, I do believe this is a great web site. I stumbledupon it 😉
I may revisit once again since i have book-marked it.
Money and freedom is the greatest way to change, may you be rich and continue to guide other people.
I do not know if it’s just me or if perhaps everyone else experiencing issues with your website.
It appears like some of the written text within your posts are running off the screen.
Can someone else please provide feedback and let me know if
this is happening to them too? This might be a issue with my browser because I’ve had this happen previously.
Thank you
Feel free to visit my web blog – casinoplus
June/November – As the e-reader market grows in Spain, corporations like Telefónica,
Fnac, and Casa del Libro launch their e-readers with the Spanish brand “bq readers”.
Many imprints have been acquired by Hachette and the businesses that had
been merged to kind the group; some are no longer active.
Several digital bookstores have closed down and transferred their users to Kobo’s bookstore.
The GAO report discovered that, generally, if a ebook is in good situation and will be
used on the campus again the following time period, bookstores
will pay college students 50 p.c of the unique
worth paid. If a website visitor finds something useful in the first 15 seconds, he will stay longer
on the website,” says 15 seconds rule. At all times let
a professional web site developer and designer to set it
up for you. The unique website is archived right here.
Hachette E book Group firm web site. He claimed that the corporate sold out of its stock
in less than six hours. This text a few publishing firm is a
stub. A publishing division targeted on science
fiction, fantasy, and mass market editions.
Thank you for any other informative website.
Where else may I am getting that kind of information written in such a perfect way?
I’ve a venture that I am simply now working on, and I’ve been on the glance out for such info.
Greetings, I’m Piotr from Poland. I wanna tell you
about my insane experience with this crazy popular online
casino I stumbled on recently.
To be honest, I was struggling badly, and now I
can’t believe it myself — I won $712,000 playing mostly live roulette!
Now I’m thinking of finally owning an apartment here in Split,
and investing a serious chunk of my winnings into Bitcoin.
Later I’ll probably move to a better neighborhood and
build my own startup.
Now I’m going by Andrei from Romania because I honestly feel like a new person. My life is flipping upside down in the best way.
I gotta ask, what would you guys do if you had this kinda luck?
Are you feeling curious right now?
For real, I never thought I’d be living this dream.
It’s all happening so fast!
Let’s talk crypto too!
It’s not my first time to visit this site, i am browsing this website dailly and get fastidious facts from here everyday.
my web site: modular furniture
whoah this weblog is excellent i like reading your posts.
Keep up the good work! You know, lots of persons are hunting around Drug Test for Impairment
this info, you could aid them greatly.
Hello There. I found your blog using msn. This is a really well written article.
I’ll be sure to bookmark it and come back to read more of your useful information. Thanks for the post.
I will definitely comeback.
Hi everyone, it’s my first pay a visit at this site, and post is truly fruitful
designed for me, keep up posting these posts.
Here is my site; casinoplus
Just desire to say your article is as amazing. The clarity in your submit is simply excellent and that i can assume you are a professional in this subject.
Fine with your permission let me to clutch your RSS feed
to keep updated with drawing close post. Thanks one million and please keep up the gratifying work.
Here is my web blog: casinoplus
Great article.
Visit my webpage: Roadside Cannabis Test
I was very happy to discover this site. I wanted to thank you for ones time just for this wonderful
read!! I definitely liked every bit of it and I have you book marked to
see new stuff on your website.
my page … Leica MS50
semiconductormaterials.com
Wow, superb blog layout! How long have you been blogging for?
you make blogging look easy. The overall look of your website is great,
as well as the content!
my blog post; Workplace Cannabis Test
Hey there! Quick question that’s completely off topic.
Do you know how to make your site mobile friendly? My site looks weird when browsing from my iphone 4.
I’m trying to find a template or plugin that might be able to correct this issue.
If you have any suggestions, please share.
Cheers!
Here is my site – modular furniture
What’s up it’s me, I am also visiting this website daily,
this web site is genuinely fastidious and the people are truly sharing good thoughts.
Feel free to visit my web-site :: lee aquí
I blog frequently and I truly thank you for your content. This great article has really peaked my
interest. I will book mark your blog and keep checking for new details about once a week.
I subscribed to your Feed as well.
Hey there! Quick question that’s entirely off topic. Do you know how to make your site mobile friendly?
My website looks weird when browsing from my iphone4.
I’m trying to find a theme or plugin that might be able
to fix this issue. If you have any recommendations, please share.
Cheers!
I’ve been exploring for a little bit for any high quality articles or weblog posts in this sort of space
. Exploring in Yahoo I finally stumbled upon this website.
Studying this info So i’m happy to convey that I have a very excellent uncanny feeling I discovered
just what I needed. I so much indisputably will make sure to don?t
disregard this site and provides it a look regularly.
I am sure this paragraph has touched all the internet visitors, its really really good article on building up new website.
Visit my web blog: casinoplus
Terrific content, Many thanks.
You actually make it seem so easy together with your presentation however I in finding this topic to be
actually something which I believe I’d never understand.
It sort of feels too complicated and extremely vast for me.
I’m taking a look forward to your next post, I will try to get the grasp of it!
My web blog :: casino plus
I get pleasure from, cause I found exactly what I was looking for.
You’ve ended my four day lengthy hunt! God Bless you man. Have a great day.
Bye
Feel free to visit my blog post :: THC Impairment Test
Appreciate it, Plenty of facts.
When I initially commented I clicked the “Notify me when new comments are added” checkbox and now each time
a comment is added I get three e-mails with the same comment.
Is there any way you can remove me from that service?
Many thanks!
My blog: THC Intoxication Test
Appreciate the recommendation. Let me try it out.
Review my website: Marijuana Impairment Test
Hello! I realize this is kind of off-topic but I had to ask.
Does building a well-established website such as yours
require a lot of work? I am completely new to running a blog but I
do write in my diary on a daily basis. I’d like to start a blog so I will be able to share my personal experience and thoughts
online. Please let me know if you have any recommendations or tips for brand new
aspiring bloggers. Thankyou!
Review my web blog – casinoplus
Today, while I was at work, my sister stole my iphone and tested to see if it can survive a 40 foot drop, just so she
can be a youtube sensation. My apple ipad is now broken and she has 83 views.
I know this is totally off topic but I had to share it with
someone!
Yo forum friends, I’m Marko from Serbia. I wanna tell you about my insane experience with this unreal online casino I stumbled on recently.
To be honest, I was living paycheck to paycheck, and now I can’t believe it myself — I crushed it and made $1,500,000 playing mostly blackjack!
Now I’m thinking of buying a house here in Zagreb, and investing a serious chunk of my winnings into Bitcoin.
Later I’ll probably move to a better neighborhood and travel the world.
Now I’m going by Nikola from Serbia because
I honestly feel like a new person. My life is flipping upside down in the best way.
I gotta ask, what would you guys do if you had this kinda luck?
Are you wondering if it’s real right now?
For real, I never thought I’d be able to help my family.
It’s all happening so fast!
Drop your thoughts below!
Thank you for another informative blog. The place else could I get that
kind of info written in such a perfect means?
I have a mission that I’m just now running on, and I’ve been on the
glance out for such information.
You are so cool! I don’t suppose I have read through anything like
this before. So good to discover somebody with some genuine thoughts on this topic.
Really.. thank you for starting this up.
This site is one thing that is needed on the internet, someone with some originality!
I really enjoy good vjntage wine. Whether it’s red or white,it’s the perfectt way tto
relax. Who else enjoys wine tasting? #WineTasting
Feel ffee to viisit my website ไวน์
Hey there! I just wanted to ask if you ever have any issues with
hackers? My last blog (wordpress) was hacked and I ended
up losing many months of hard work due to no backup.
Do you have any solutions to prevent hackers?
I’m a huge fan of goiod vintage wine. Doesn’t matter if
it’s dry or sweet, wine always makes the moment better.
Are there any wine lovers around? #RedWine
my web page; ไวน์ขาว
Searching for cost-effective container storage neɑr
me? Check ᧐ut Container Storage Units forr affordable options аcross Kent and
Surrey. Perfect fߋr һome оr business storage needs.
I like the valuable information you provide in your
articles. I will bookmark your blog and check again here
frequently. I am quite certain I will learn a lot of new stuff right here!
Good luck for the next!
Hello, i believe that i saw you visited my site so i came to go back
the choose?.I am trying to find issues to enhance my website!I guess its ok
to use some of your ideas!!
Very good site you have here but I was curious about if
you knew of any forums that cover the same topics discussed in this article?
I’d really love to be a part of community where I can get
feedback from other experienced people that share the same interest.
If you have any recommendations, please let me know.
Thank you!
Pretty! This was an extremely wonderful post. Thank you for supplying this information.
Greetings, I’m Marko from Serbia. I wanna tell you about my insane
experience with this unreal online casino I stumbled on recently.
To be honest, I was struggling badly, and now I
can’t believe it myself — I crushed it and made $712,000 playing mostly sports bets!
Now I’m thinking of getting a new car here in Split, and investing a serious chunk
of my winnings into Toncoin.
Later I’ll probably move to a better neighborhood and travel the world.
Now I’m going by Tomasz from Poland because I honestly
feel like a new person. My life is flipping upside down in the best way.
I gotta ask, what would you guys do if you had this kinda luck?
Are you a bit envious right now?
For real, I never thought I’d be living this dream.
It’s all happening so fast!
Drop your thoughts below!
Can’t get enough of good vintage wine. Doesn’t matter if it’s dry or sweet, it just elevates
any occasion. Who else enjoys wine tasting?
#RedWine
When I initially commented I clicked the “Notify me when new comments are added” checkbox and now each
time a comment is added I get four e-mails
with the same comment. Is there any way you can remove me from
that service? Thanks!
I love reading a post that can make men and women think.
Also, thanks for permitting me to comment!
Asking questions are actually fastidious thing if you are not understanding something entirely, however this post presents pleasant understanding yet.
These are actually fantastic ideas in about blogging.
You have touched some pleasant things here. Any way keep up wrinting.
You actually make it seem so easy with your presentation but I find this topic to be actually something that I
think I would never understand. It seems too complicated and extremely broad for me.
I’m looking forward for your next post, I will try to get the hang of it!
This is a really good tip particularly to those fresh to the blogosphere.
Brief but very precise information… Appreciate your sharing this one.
A must read article!
Everything is very open with a very clear clarification of the challenges.
It was definitely informative. Your website is very helpful.
Many thanks for sharing!
Hey very nice blog!
Pretty nice post. I just stumbled upon your weblog and wanted to say that I have truly enjoyed browsing your blog posts.
In any case I’ll be subscribing to your rss feed and I hope you write again soon!
Thank you for sharing your info. I truly appreciate your efforts and
I will be waiting for your further post thank you once again.
Hi my loved one! I want to say that this article is awesome, great written and include almost all significant infos.
I’d like to look extra posts like this .
I get pleasure from, cause I discovered just what I was having
a look for. You have ended my four day lengthy hunt!
God Bless you man. Have a great day. Bye
Wow, this post is pleasant, my sister is analyzing these kinds of things, thus I
am going to let know her.
Also visit my web site – Situs judi slot gacor
I have read a few excellent stuff here. Definitely price bookmarking for revisiting.
I surprise how much effort you put to make this
kind of excellent informative web site.
When someone writes an piece of writing he/she keeps the image of a user in his/her brain that how a
user can understand it. Thus that’s why this
article is amazing. Thanks!
Stop by my web site :: Skup złomu w Hammersmith
Can’t get enough of good glass off wine. From a locaal vineyard or imported, wine always makes the moment better.
Anyone else here love wine? #RedWine
Here is myy webpage; ขาย ไวน์
My partner and I absolutely love your blog and find almost all of your post’s to be precisely what
I’m looking for. Do you offer guest writers to write content for you?
I wouldn’t mind producing a post or elaborating on a few
of the subjects you write related to here. Again,
awesome blog!
Thanks a bunch for sharing this with all people you really realize what you are
talking about! Bookmarked. Please also discuss with my site =).
We will have a hyperlink exchange arrangement between us
Take a look at my webpage … stem cell treatment
When someone writes an piece of writing he/she keeps the image of
a user in his/her brain that how a user can know it.
Therefore that’s why this paragraph is amazing. Thanks!
my web page – Loodgieter Leuven
This is really interesting, You are a very skilled blogger.
I’ve joined your rss feed and look forward to seeking
more of your great post. Also, I have shared your web site in my social networks!
Also visit my web-site – joint borrower sole proprietor mortgage
I visit daily some websites and blogs to read content, but this
web site presents feature based articles.
Here is my site: Skup złomu w Greater London
Thanks for sharing your thoughts on Situs slot gacor.
Regards
I read this post completely on the topic of the difference of hottest and
earlier technologies, it’s remarkable article.
Feel free to visit my blog … Skup złomu w Kensington
I’m really enjoying the design and layout of your site.
It’s a very easy on the eyes which makes it much more pleasant for me to come here and visit
more often. Did you hire out a designer to create your theme?
Outstanding work!
I have been surfing online more than 3 hours today,
yet I never found any interesting article like yours.
It is pretty worth enough for me. In my opinion, if all site owners and bloggers made good content as you did, the web
will be a lot more useful than ever before.
Very quickly this site will be famous among
all blogging visitors, due to it’s good content
I’m truly enjoying the design and layout of your site. It’s a very easy
on the eyes which makes it much more enjoyable for
me to come here and visit more often. Did you hire out a developer to create
your theme? Outstanding work!
Also visit my homepage: Metal Scrap Ltd – Opinie Klientów
I got this web site from my buddy who told me on the topic of this web page and now this time
I am visiting this website and reading very informative articles at this time.
Hi there would you mind stating which blog platform you’re working with?
I’m going to start my own blog in the near future but I’m having a difficult time deciding between BlogEngine/Wordpress/B2evolution and Drupal.
The reason I ask is because your layout seems different then most blogs and I’m looking for something
completely unique. P.S My apologies for getting off-topic but I had
to ask!
Here is my web blog … Skup złomu w Kensington
What’s up all, here every one is sharing these
kinds of knowledge, thus it’s nice to read this webpage, and I used to pay a visit this webpage everyday.
Hey there! This is my first comment here so I just wanted
to give a quick shout out and say I truly enjoy reading through your posts.
Can you suggest any other blogs/websites/forums that cover the same subjects?
Thanks!
Hello friends, good paragraph and fastidious arguments commented here, I am actually enjoying
by these.
Look into my web-site: Plombier Mons
For most up-to-date news you have to pay a visit web and on web I
found this website as a most excellent web page for most up-to-date updates.
Also visit my blog: Plombier Mouscron
What i do not realize is if truth be told how you are no
longer actually much more smartly-appreciated
than you might be right now. You’re very intelligent.
You understand thus significantly relating to this topic, produced
me individually believe it from numerous various angles.
Its like women and men don’t seem to be involved until it’s something to accomplish with Woman gaga!
Your personal stuffs great. At all times maintain it up!
I’m really enjoying the theme/design of your website.
Do you ever run into any internet browser compatibility problems?
A handful of my blog visitors have complained about my blog
not working correctly in Explorer but looks great in Firefox.
Do you have any solutions to help fix this problem?
Unquestionably believe that which you stated. Your favorite justification seemed to be on the internet the easiest thing to be aware of.
I say to you, I definitely get irked while people think about worries that they
plainly do not know about. You managed to hit
the nail upon the top and defined out the whole thing without having side-effects , people can take a signal.
Will probably be back to get more. Thanks
Wow, that’s what I was searching for, what a material!
existing here at this blog, thanks admin of this web site.
Also visit my page; stem cell treatment
Great post however I was wanting to know if you could write a litte
more on this subject? I’d be very grateful if you could elaborate a little bit
more. Thanks!
my web page: Skup złomu w Harrow
Thanks , I’ve recently been searching for information approximately
this subject for a while and yours is the best I’ve found out so far.
But, what in regards to the conclusion? Are you
sure in regards to the source?
Here is my website :: Situs judi slot gacor
If you are going for finest contents like myself, only pay a quick visit this website all
the time as it offers quality contents, thanks
Review my site; joint mortgage sole proprietor
Have you ever thought about writing an ebook or guest authoring on other sites?
I have a blog based on the same ideas you discuss and
would love to have you share some stories/information. I know
my subscribers would enjoy your work. If you’re even remotely interested, feel free to shoot me an email.
I’m not that much of a online reader to be honest but your blogs really nice, keep it up!
I’ll go ahead and bookmark your website to come back later.
All the best
Check out my page :: Slot
Excellent way of telling, and pleasant article to obtain facts regarding my presentation focus,
which i am going to present in academy.
Wassup guys, I’m Piotr from Poland. I wanna tell you
about my insane experience with this crazy popular online casino
I stumbled on not long ago.
To be honest, I was totally broke, and now I can’t believe it myself — I
crushed it and made $1,500,000 playing mostly live roulette!
Now I’m thinking of getting a new car here in Split, and investing a serious chunk of my winnings into Cardano.
Later I’ll probably move to a better neighborhood and start a small business.
Now I’m going by Nikola from Serbia because I honestly
feel like a new person. My life is flipping upside down in the best way.
Let’s be honest, what would you guys do if you had this kinda luck?
Are you thinking “damn!” right now?
For real, I never thought I’d have a shot at investing.
It’s all happening so fast!
Reply if you wanna chat!
Very nice write-up. I definitely appreciate this site. Keep writing!
Asking questions are truly nice thing if you are not understanding anything fully,
but this paragraph presents fastidious understanding yet.
Hi, I wish for to subscribe for this website to obtain latest updates, so
where can i do iit please help out.
Remarkable things here. I’m very happy to look your
post. Thanks so much and I am having a look forward to contact you.
Will you please drop me a mail?
I think this is among the most vital info for me. And i am glad reading your article.
But want to remark on few general things, The site style is wonderful, the articles is really nice : D.
Good job, cheers
Incredible! This blog looks exactly like my old one!
It’s on a totally different topic but it has pretty much
the same page layout and design. Excellent choice of colors!
I don’t even know how I finished up here, but I thought this submit
was once great. I don’t recognize who you are but definitely you are going to a well-known blogger
if you happen to aren’t already. Cheers!
hey there and thank you for your information – I have definitely picked up
something new from right here. I did however expertise some technical points using this site, since I
experienced to reload the site a lot of times previous to I could get it to load correctly.
I had been wondering if your web host is OK? Not that I am complaining, but sluggish
loading instances times will very frequently affect your placement in google and could damage your high quality score
if advertising and marketing with Adwords. Anyway I’m adding this RSS to my email and
can look out for much more of your respective exciting content.
Make sure you update this again soon.
I always used to study post in news papers but now as
I am a user of web therefore from now I am using net for articles or reviews, thanks to web.
I’m a huge fan of good glass oof wine. Fromm a local vineyard or imported,
it just elevates any occasion. Aree there anyy wine lovers around?
My web page :: ขาย wine
Good post. I learn something new and challenging on sites I stumbleupon everyday.
It’s always exciting to read content from other writers and use a little something from their web sites.
For the reason that the admin of this site is working, no question very shortly it
will be famous, due to its quality contents.
I savor, lead to I discovered exactly what I used to be having a look for.
You’ve ended my four day lengthy hunt! God Bless you man. Have a great day.
Bye
It’s the best time to make some plans for the future and it’s time to be
happy. I have read this post and if I could I wish to suggest you few interesting
things or suggestions. Maybe you can write next articles referring to this article.
I desire to read even more things about it!
Wow, this paragraph is good, my younger sister is analyzing these things, so I am
going to let know her.
My spouse and I stumbled over here from a different website and
thought I might check things out. I like what
I see so now i am following you. Look forward to looking over your web page
again.
What a material of un-ambiguity and preserveness of valuable
experience regarding unexpected emotions.
BJ88 là nhà cái cá Đá Gà Thomo độc quyền từ Campuchia ,
nổi bật với độ uy tín, công nghệ hiện đại và kho
trò chơi đa dạng.
Right now it seems like WordPress is the
preferred blogging platform available right now. (from what
I’ve read) Is that what you are using on your blog?
Hey folks, I’m Ivan from Croatia. I wanna tell you
about my insane experience with this unreal online casino I stumbled on this spring.
To be honest, I was living paycheck to paycheck, and now I can’t believe it myself — I hit
$712,000 playing mostly crazy time!
Now I’m thinking of finally owning an apartment here in Cluj-Napoca, and
investing a serious chunk of my winnings into
Cardano.
Later I’ll probably move to a better neighborhood and build my own startup.
Now I’m going by Luka from Croatia because I honestly
feel like a new person. My life is flipping upside down in the best
way.
No cap, what would you guys do if you had this kinda luck?
Are you feeling curious right now?
For real, I never thought I’d have a shot at investing.
It’s all happening so fast!
Feel free to DM me!
Hi there mates, nice article and nice urging commented here,
I am genuinely enjoying by these.
Good day! This post couldn’t be written any better!
Reading through this post reminds me of my old room mate!
He always kept chatting about this. I will forward this write-up to him.
Pretty sure he will have a good read. Thanks for sharing!
Hi there, its pleasant post regarding media print, we all know media is a impressive source of facts.
Nice blog here! Also your site loads up very fast! What web host
are you using? Can I get your affiliate link to your host?
I wish my web site loaded up as quickly as yours lol
Hi, its good post regarding media print, we all understand media
is a fantastic source of information.
Also visit my web blog: dropshipping Ebay
Awesome issues here. I am very glad to see your article.
Thanks so much and I’m having a look ahead to contact you.
Will you kindly drop me a e-mail?
my page: play casinos not on gamestop
Hello, I read your new stuff daily. Your humoristic
style is witty, keep doing what you’re doing!
Cheers, I appreciate it.
I am truly thankful to the holder of this web page who
has shared this wonderful piece of writing at at this
time.
Feel free to surf to my web blog … bathroom remodeling contractors
Howdy I am so grateful I found your webpage,
I really found you by mistake, while I was browsing on Yahoo for something else,
Regardless I am here now and would just like to say thanks a lot for a incredible post
and a all round interesting blog (I also love the theme/design), I don’t have time to
go through it all at the moment but I have bookmarked it and also added in your RSS feeds, so when I have time I will be back to
read a lot more, Please do keep up the awesome work.
Hi there to all, how is the whole thing, I think every one is getting more from this web page,
and your views are good in favor of new visitors.
Hey folks, I’m Ivan from Croatia. I wanna tell you about my
insane experience with this new online casino I stumbled on last
month.
To be honest, I was barely affording rent, and now I can’t believe it myself — I cashed out $712,000 playing mostly blackjack!
Now I’m thinking of taking my dream vacation and buying a house here in Zagreb, and investing a serious chunk of my winnings into Cardano.
Later I’ll probably move to a better neighborhood and travel the world.
Now I’m going by Andrei from Romania because I honestly
feel like a new person. My life is flipping upside down in the best way.
Be real, what would you guys do if you had this kinda
luck? Are you a bit envious right now?
For real, I never thought I’d be living this dream.
It’s all happening so fast!
Feel free to DM me!
I’ma huge fan off good glass of wine. Whetyer it’s red oor white, it just elevates any occasion.
Who else enjoys wine tasting?
Feel free tto visit my web page … ไวน์ขาว
I do not even understand how I stopped up here, but I assumed this submit was once great.
I do not recognise who you might be but definitely
you are going to a famous blogger for those who are not already.
Cheers!
Wow, fantastic blog format! How long have you been blogging for?
you made running a blog look easy. The overall glance of your web
site is wonderful, let alone the content!
Thanks a lot for sharing this with all people you
actually recognise what you are speaking
about! Bookmarked. Please also visit my site =). We could have a hyperlink exchange agreement between us
hello!,I love your writing so so much! share we keep up a correspondence more about
your post on AOL? I require a specialist in this area to unravel
my problem. May be that’s you! Taking a look
forward to see you.
great points altogether, you just won a new reader. What could you suggest in regards to your submit that you just made some days ago?
Any positive?
What’s up everyone, it’s my first pay a visit at this website,
and post is genuinely fruitful in support of me, keep up posting these types of articles or reviews.
Hi, I read your blogs regularly. Your humoristic style is witty, keep up the good work!
Right here is the right webpage for anyone who hopes to understand this topic.
You understand so much its almost tough to argue with
you (not that I personally would want to…HaHa).
You definitely put a new spin on a subject that
has been discussed for years. Great stuff, just excellent!
Hello colleagues, how is the whole thing, and what you want to say regarding this article, in my view its genuinely amazing in favor of me.
The survival guide aspect of Blast Proof David’s
Shield really stands out to me. In today’s unpredictable world, learning mental resilience
and adaptability is just as important as physical
preparedness. Definitely adding this to my reading list!
I’m not sure where you are getting your info, but great topic.
I needs to spend some time learning much more or understanding more.
Thanks for wonderful info I was looking for this info for my mission.
Greetings, I’m Marko from Serbia. I wanna tell you about my insane experience
with this next-level online casino I stumbled on not long ago.
To be honest, I was living paycheck to paycheck, and now I can’t believe it myself
— I hit £590,000 playing mostly crazy time!
Now I’m thinking of finally owning an apartment here in Cluj-Napoca,
and investing a serious chunk of my winnings into
Solana.
Later I’ll probably move to a better neighborhood and travel the world.
Now I’m going by Nikola from Serbia because I honestly feel like a new
person. My life is flipping upside down in the best way.
Be real, what would you guys do if you had this kinda luck?
Are you feeling curious right now?
For real, I never thought I’d get out of debt. It’s all happening so
fast!
Reply if you wanna chat!
Hello friends, how is the whole thing, and what you desire to say concerning this paragraph,
in my view its actually remarkable designed for me.
Wassup guys, I’m Piotr from Poland. I wanna tell you
about my insane experience with this new online casino I stumbled on not long
ago.
To be honest, I was barely affording rent, and now I can’t believe it myself — I cashed out £590,000 playing mostly blackjack!
Now I’m thinking of getting a new car here in Warsaw, and investing a
serious chunk of my winnings into Cardano.
Later I’ll probably move to a better neighborhood and start a small
business.
Now I’m going by Tomasz from Poland because I honestly feel like a
new person. My life is flipping upside down in the best way.
Tell me honestly, what would you guys do if you had this kinda luck?
Are you wondering if it’s real right now?
For real, I never thought I’d have a shot at investing.
It’s all happening so fast!
Let’s talk crypto too!
It’s awesome for me to have a web site, which is helpful in favor
of my knowledge. thanks admin
I’m really enjoying the design and layout of your blog.
It’s a very easy on the eyes which makes it much more pleasant for me to come here and
visit more often. Did you hire out a developer to create your theme?
Great work!
my blog; Artec Eva
hello!,I really like your writing so a lot! share we keep up a
correspondence more about your post on AOL? I need a specialist in this house to unravel my problem.
Maybe that’s you! Having a look ahead to peer you.
Here is my site: Creaform HandySCAN BLACK Elite
Hi, I do believe this is an excellent blog. I stumbledupon it 😉 I am going to come back once
again since I book-marked it. Money and freedom is the greatest way to change, may you
be rich and continue to guide others.
Here is my homepage; Leica RTC360
Very nice article, just what I was looking for.
Heya i’m for the first time here. I found this board and I
find It really useful & it helped me out a lot. I hope to give something back and aid others
like you aided me.
Feel free to surf to my webpage … FARO Focus Premium 350
What’s up, everything is going nicely here and ofcourse
every one is sharing facts, that’s in fact fine, keep up writing.
It’s very straightforward to find out any
matter on net as compared to books, as I found this paragraph at this web page.
Feel free to visit my homepage; Artec Space Spider
Magnificent site. Plenty of useful information here.
I am sending it to a few friends ans additionally sharing in delicious.
And certainly, thanks to your effort!
Feel free to surf to my blog post; Faro Focus S350
hey there and thank you for your information – I have certainly picked up something new from right here.
I did however expertise some technical points using this web site,
since I experienced to reload the site many times
previous to I could get it to load properly. I had been wondering
if your hosting is OK? Not that I am complaining, but slow
loading instances times will very frequently affect your placement in google and can damage your quality score if advertising
and marketing with Adwords. Anyway I’m adding this RSS to my email and can look out for
a lot more of your respective interesting content. Make sure
you update this again very soon.
Stop by my blog post … Artec Space Spider
Hey folks, I’m Marko from Serbia. I wanna tell you about my insane experience with this unreal online casino
I stumbled on not long ago.
To be honest, I was super poor, and now I can’t believe it myself — I
scored £590,000 playing mostly live roulette!
Now I’m thinking of taking my dream vacation and
buying a house here in Split, and investing a serious
chunk of my winnings into Solana.
Later I’ll probably move to a better neighborhood
and build my own startup.
Now I’m going by Nikola from Serbia because I honestly feel like a new person. My life is flipping upside
down in the best way.
I gotta ask, what would you guys do if you had this
kinda luck? Are you a bit envious right now?
For real, I never thought I’d be able to help my family. It’s all happening so fast!
Let’s talk crypto too!
Way cool! Some extremely valid points! I appreciate you penning this post plus the rest of the
site is really good.
I blog frequently and I seriously appreciate your content.
The article has really peaked my interest. I’m
going to bookmark your site and keep checking for new information about once
per week. I subscribed to your RSS feed as well.
I all the time emailed this webpage post page to all my friends,
as if like to read it then my friends will too.
Also visit my website; FARO Focus Premium 70
I all the time emailed this website post page to all my associates, for the reason that if like to read
it then my friends will too.
Feel free to surf to my web page FARO Focus Premium 350
Pretty nice post. I just stumbled upon your weblog and wanted to say that I have truly enjoyed surfing
around your blog posts. In any case I will be subscribing
to your feed and I hope you write again very soon!
I was suggested this website by my cousin. I’m not sure whether
this post is written by him as no one else know such detailed about my problem.
You are wonderful! Thanks!
Feel free to surf to my website … Artec Eva
My brother suggested I may like this website. He was once entirely right.
This post actually made my day. You can not consider just how so much time I had
spent for this info! Thanks!
Hey are using WordPress for your site platform? I’m new to the blog world
but I’m trying to get started and set up my own. Do you require any html coding expertise
to make your own blog? Any help would be really appreciated!
Awesome article.
I like the helpful information you provide in your articles.
I will bookmark your blog and check again here frequently.
I am quite certain I will learn lots of new stuff right here!
Best of luck for the next!
I’ve been exploring for a little for any high quality
articles or blog posts in this kind of space . Exploring in Yahoo I
ultimately stumbled upon this site. Studying this info So i
am satisfied to show that I’ve a very good uncanny feeling I came upon exactly what I needed.
I most without a doubt will make sure to do not forget this website and provides it a
look regularly.
Great post. I was checking constantly this blog and I’m impressed!
Very useful info specially the last part 🙂 I care for such information a lot.
I was seeking this certain information for a long time.
Thank you and good luck.
When I originally left a comment I seem to have clicked the -Notify me when new comments are added- checkbox and from now on each time a comment is
added I receive 4 emails with the exact same comment.
There has to be a means you are able to remove me from that service?
Thank you!
Hey there! I realize this is sort of off-topic but I had to ask.
Does operating a well-established blog like yours take a massive amount work?
I am completely new to operating a blog but I do write in my diary everyday.
I’d like to start a blog so I can share my experience and feelings online.
Please let me know if you have any recommendations
or tips for brand new aspiring blog owners. Appreciate it!
You are so interesting! I don’t suppose I have read through a single thing like that before.
So nice to discover someone with some unique thoughts on this subject.
Really.. thank you for starting this up. This website is something that is required on the web, someone with a little originality!
Hi there, just wanted to say, I liked this article. It was funny.
Keep on posting!
Hi there, all the time i used to check website posts here early in the daylight, since i enjoy to find out more and more.
https://keysoftintl.com/
Wow! In the end I got a website from where I be capable of really take helpful
information concerning my study and knowledge.
bookmarked!!, I love your website!
It’s hard to come by knowledgeable people in this particular subject,
however, you sound like you know what you’re talking about!
Thanks
This is nicely expressed! .
Hi, after reading this awesome piece of writing i am also happy to share my familiarity here with friends.
Attractive section of content. I just stumbled upon your site and in accession capital to assert that I acquire actually enjoyed account your blog posts.
Any way I will be subscribing to your feeds and even I achievement you access consistently rapidly.
Hi, i think that i saw you visited my blog thus i came to “return the favor”.I am attempting to find things to enhance my site!I suppose its ok to use a few of your ideas!!
My homepage – https://www.dubaitowels.com/
Fantastic postings. Thank you.
ขอบคุณสำหรับข้อมูลเกี่ยวกับดอกไม้งานศพที่ละเอียด
โดยส่วนตัวเพิ่งเจอเหตุการณ์สูญเสีย
การเลือกช่อดอกไม้เลยเป็นเรื่องที่ต้องใส่ใจ
จะบอกต่อให้เพื่อนๆ ที่ต้องการเลือกดอกไม้ไปงานศพอ่านด้วย
Here is my homepage; แพ็คเกจ วัดบางเตย
Your style is very unique in comparison to other folks I’ve read stuff from.
Thank you for posting when you’ve got the opportunity,
Guess I’ll just book mark this site.
Superb, what a web site it is! This weblog presents valuable facts to us, keep it up.
I’m really enjoying the theme/design of your web site. Do you ever run into any web
browser compatibility problems? A small number of my blog visitors have complained about my website not working correctly in Explorer but looks great in Opera.
Do you have any recommendations to help fix this
issue?
อ่านแล้วเข้าใจเรื่องดอกไม้งานศพได้ดีขึ้น
โดยส่วนตัวเพิ่งมีญาติจากไป การเลือกพวงหรีดเลยเป็นเรื่องที่ต้องใส่ใจ
จะบอกต่อให้เพื่อนๆ ที่ต้องการเลือกดอกไม้ไปงานศพอ่านด้วย
My web page … จัดดอกไม้งานศพ
hey there and thank you for your information – I’ve certainly picked up something new from right here.
I did however expertise several technical issues using this site, since I experienced to
reload the web site many times previous to I could get it to load correctly.
I had been wondering if your hosting is OK? Not that I
am complaining, but slow loading instances times will very frequently affect your placement in google and can damage your high quality score if ads and marketing with Adwords.
Anyway I am adding this RSS to my email and can look out for much more of your respective interesting content.
Make sure you update this again very soon.
always i used to read smaller articles that also clear
their motive, and that is also happening with this piece of writing which I am
reading at this time.
บทความนี้เกี่ยวกับการจัดดอกไม้งานศพ ยอดเยี่ยมมาก
การรู้ว่าดอกไม้แต่ละชนิดมีความหมายอย่างไร ช่วยให้เลือกได้ตรงความรู้สึกมากขึ้น
จะบอกต่อให้เพื่อนๆ ที่ต้องการเลือกดอกไม้ไปงานศพอ่านด้วย
My blpog … จัดดอกไม้งานพิธี
Saya sudah lama mencari situs slot 4D terpercaya, dan akhirnya ketemu
OVJTOTO. Permainannya lengkap, transaksi cepat, dan customer service-nya
sangat membantu. Recommended!
I love your blog.. very nice colors & theme.
Did you make this website yourself or did you hire someone
to do it for you? Plz respond as I’m looking to construct my
own blog and would like to know where u got this from. cheers
My brother suggested I might like this blog. He was entirely right.
This post truly made my day. You cann’t imagine simply how much time I had spent for this info!
Thanks!
Check out my blog post; alternatif teman21
I do not know whether it’s just me or if everybody else experiencing problems with your website.
It appears as though some of the written text within your posts are running
off the screen. Can someone else please comment
and let me know if this is happening to them as well?
This could be a problem with my internet browser because I’ve had this happen before.
Thank you
I was recommended this web site through my cousin. I am no longer positive whether this post is written by him as nobody else recognize such targeted
approximately my trouble. You are wonderful!
Thanks!
My brother suggested I may like this website.
He was totally right. This submit actually made my day. You
can not consider simply how so much time I had spent for this information! Thanks!
What’s Taking place i am new to this, I stumbled upon this I’ve
discovered It positively helpful and it has helped me out loads.
I hope to give a contribution & help other users like its helped me.
Good job.
I just couldn’t depart your web site prior to suggesting that I
extremely enjoyed the usual information a person supply on your
visitors? Is going to be back regularly to investigate cross-check new posts
always i used to read smaller articles which also clear their motive, and that is also happening with
this article which I am reading at this place.
Appreciating the commitment you put into your blog and in depth
information you provide. It’s awesome to come across a blog every once in a while that isn’t the same unwanted rehashed information. Wonderful read!
I’ve saved your site and I’m including your RSS feeds to my Google account.
I blog quite often and I seriously appreciate your information. The
article has truly peaked my interest. I’m going to take a note of your site and keep
checking for new details about once a week.
I subscribed to your Feed too.
Attractive section of content. I just stumbled upon your weblog and in accession capital to assert that I get in fact enjoyed
account your blog posts. Any way I’ll be subscribing to
your augment and even I achievement you access consistently
quickly.
Also visit my site … 강남셔츠룸
I love reading through a post that will make people think.
Also, thank you for allowing me to comment!
Review my web-site :: 강남풀싸롱
This paragraph is genuinely a nice one it helps new the web visitors, who
are wishing in favor of blogging.
Have a look at my blog post … 강남풀싸롱
My brother suggested I might like this web site.
He was entirely right. This post actually made my day.
You cann’t imagine simply how much time I had spent for this info!
Thanks!
Feel free to visit my page … 강남셔츠룸
I’m not sure where you are getting your information, but great topic.
I needs to spend soje time learning more or understanding more.
Thanks for magnificent info I was looking for this information for my mission.
My web-site :: https://blogbuz.co.uk/cost-vs-benefit-the-economics-of-window-replacement-in-watford/
Greetings, I do think your website might be having browser compatibility
problems. Whenever I look at your site in Safari,
it looks fine but when opening in I.E., it’s got some overlapping issues.
I merely wanted to give you a quick heads up! Other than that, great website!
Feel free to surf to my page Paramount Recruitment Service
If you are going for best contents like I do, just pay a quick visit this website everyday for the reason that it gives quality contents,
thanks
Here is my page … situs slot gacor terbaru 2025
You are so cool! I do not think I’ve read through a single thing like that before.
So great to find another person with original thoughts on this subject.
Really.. many thanks for starting this up. This site is something that is required on the web, someone with some originality!
Also visit my page :: Link JUARAKU hari ini
I for all time emailed this webpage post page to all my contacts, since if like to
read it next my links will too.
Also visit my blog: Buy Courseware
Hi there Dear, are you in fact visiting this website
daily, if so after that you will absolutely take fastidious know-how.
Also visit my blog … Paramount Recruitment Training
Just desire to say your article is as surprising.
The clearness in your put up is just nice and that i can think you’re knowledgeable in this subject.
Well along with your permission let me to clutch your RSS feed to stay updated with forthcoming
post. Thanks one million and please continue the gratifying work.
Look into my blog post … 강남셔츠룸
I am not sure where you are getting your information, but
great topic. I needs to spend some time learning much more or understanding more.
Thanks for great info I was looking for this info for my mission.
My website bathroom bathrooms near me
Nice post. I learn something totally new and challenging on websites I stumbleupon every day.
It will always be exciting to read content from other writers and use something from
their sites.
Hi there, You’ve done an excellent job. I’ll certainly digg it and personally suggest
to my friends. I’m confident they’ll be benefited from this site.
Also visit my blog post: bathroom renovations near me
What’s Taking place i am new to this, I stumbled upon this I have found It positively helpful and
it has aided me out loads. I hope to give a contribution & help different customers
like its helped me. Great job.
Here is my web page – bathrom remodelling
Hi there i am kavin, its my first time to commenting anyplace,
when i read this article i thought i could also create comment due to this
sensible piece of writing.
Having read this I thought it was rather enlightening.
I appreciate you finding the time and effort to put this short article together.
I once again find myself spending a lot of time both reading and posting comments.
But so what, it was still worth it!
My web blog; bathroom fitter
Hello colleagues, its wonderful piece of writing about teachingand
fully explained, keep it up all the time.
Here is my web-site … bathroom remodeling
We’re a gaggle of volunteers and opening a
new scheme in our community. Your web site offered
us with helpful information to work on. You’ve performed an impressive process and our entire neighborhood
shall be thankful to you.
my blog post; bathroom remodelling near me
It’s in fact very complex in this busy life to listen news on TV, thus I simply use the web for that reason, and get the most recent
information.
Here is my homepage; bathroom renovation
With havin so much content and articles do you ever run into any issues of
plagorism or copyright violation? My blog has
a lot of completely unique content I’ve either written myself or outsourced but it seems a lot of it
is popping it up all over the web without my authorization. Do you know any ways to
help prevent content from being stolen? I’d certainly appreciate it.
Here is my website bathroom renovations
I absolutely love your blog and find the majority of your post’s to be just what I’m looking for.
can you offer guest writers to write content in your
case? I wouldn’t mind creating a post or elaborating on some of the
subjects you write about here. Again, awesome weblog!
My web site – bathroom bathrooms near me
It is in reality a nice and useful piece of info.
I’m satisfied that you simply shared this useful info with us.
Please keep us informed like this. Thanks for sharing.
My relatives all the time say that I am wasting my time here at web, except I know I am
getting experience all the time by reading thes good articles or reviews.
My web-site – bath renovation
I love your blog.. very nice colors & theme. Did you create
this website yourself or did you hire someone to do it for you?
Plz respond as I’m looking to design my own blog and would like to know where
u got this from. cheers
Amazing! Its actually amazing paragraph, I
have got much clear idea on the topic of from this paragraph.
Also visit my website – bath remodelling near me
ขอบคุณสำหรับข้อมูลเกี่ยวกับพวงหรีดที่ละเอียด
โดยส่วนตัวเพิ่งมีญาติจากไป
การเลือกดอกไม้งานศพเลยเป็นเรื่องที่ต้องใส่ใจ
ใครที่กำลังเตรียมตัวจัดงานศพให้คนสำคัญควรอ่านจริงๆ
Have a look at my web page: แพ็กเกจบริการจัดงานศพ
Excellent blog here! Also your website loads up fast! What host are you using?
Can I get your affiliate link to your host? I wish my site loaded up as fast as yours lol
Now I am going to do my breakfast, when having
my breakfast coming yet again to read additional news.
If you want to obtain a great deal from this article then you have to apply these techniques to your won blog.
Also visit my page – https://Dubaiuniforms.net/
I used to be able to find good advice from your blog posts.
my site; Car Rental Cap Haitien
Have you ever considered about including a little bit more than just your articles?
I mean, what you say is important and all.
But think of if you added some great visuals or
videos to give your posts more, “pop”! Your content is excellent but with pics and clips, this site could certainly be one of the best in its niche.
Very good blog!
I was curious if you ever considered changing the structure of your website?
Its very well written; I love what youve got to say. But maybe
you could a little more in the way of content so people could connect
with it better. Youve got an awful lot of text for only having
one or 2 images. Maybe you could space it out better?
my blog – Residence Royale Hotel
Thanks on your marvelous posting! I actually enjoyed reading it, you may be a great
author.I will remember to bookmark your blog and
will often come back in the foreseeable future. I want to encourage you
continue your great posts, have a nice evening!
Feel free to visit my site: Appliance Repair Boca Raton
At this moment I am going away to do my breakfast, later than having my breakfast
coming again to read further news.
My blog post; Appliance Repair Boca Raton FL
Post writing is also a excitement, if you be acquainted with afterward you can write or else it
is complex to write.
My web page – Okap Car Rental
I constantly spent my half an hour to read this website’s posts every day along with a cup of coffee.
Feel free to visit my site – Appliance Repair Near Boca Raton
Greetings! I know this is kind of off topic but I was
wondering if you knew where I could get a captcha plugin for my comment form?
I’m using the same blog platform as yours and I’m having
difficulty finding one? Thanks a lot!
I love what you guys are usually up too. This type of
clever work and exposure! Keep up the good works guys I’ve added you guys to
my personal blogroll.
Here is my web blog … Senior Medical Center in Miami
Howdy! I could have sworn I’ve visited your blog before but after going through
some of the posts I realized it’s new to me. Nonetheless,
I’m definitely happy I found it and I’ll be book-marking
it and checking back often!
Feel free to visit my webpage :: Appliance Repair Boca Raton FL
If you are going for best contents like I do, just go to see this web site every
day as it presents quality contents, thanks
This design is incredible! You definitely know
how to keep a reader amused. Between your wit
and your videos, I was almost moved to start my own blog (well,
almost…HaHa!) Wonderful job. I really loved what you had to say, and more than that, how you presented it.
Too cool!
Look into my website; Gousse Urology
I know this website presents quality depending content and additional data, is
there any other web site which offers these information in quality?
Also visit my webpage Appliance Repair Boca Raton FL
It’s going to be finish of mine day, except before finish I
am reading this enormous post to increase my know-how.
Have a look at my site Female Urologist Miami
We are a group of volunteers and starting a brand
new scheme in our community. Your web site offered us with useful information to work on. You’ve
done an impressive process and our whole
community will be thankful to you.
Hmm it appears like your blog ate my first comment (it was extremely long) so I guess I’ll just sum it
up what I submitted and say, I’m thoroughly
enjoying your blog. I too am an aspiring blog writer but I’m still new to the whole thing.
Do you have any tips for rookie blog writers?
I’d really appreciate it.
My blog Rental Car Cap Haitien
Hola! I’ve been reading your site for a long time now and finally
got the courage to go ahead and give you a shout out from Atascocita Texas!
Just wanted to mention keep up the excellent work!
Visit my site :: Urology Clinic in Miami
Do you have a spam problem on this blog; I also
am a blogger, and I was wanting to know your situation; we have
created some nice procedures and we are looking
to swap techniques with other folks, why not shoot me an e-mail if interested.
Take a look at my blog post :: Okap Hotels
What’s up to all, it’s actually a fastidious for
me to visit this web site, it includes valuable Information.
Also visit my webpage :: Hotels Cap Haitien
Thank you for the good writeup. It in reality was once a leisure account
it. Glance advanced to far brought agreeable from you!
However, how could we keep up a correspondence?
Also visit my homepage :: Appliance Repair Near Boca Raton
Hi, its fastidious paragraph about media print, we all be aware of media is a enormous source of information.
My blog post :: Senior Medical Center Miami
อ่านแล้วเข้าใจเรื่องการเลือกดอกไม้แสดงความอาลัยได้ดีขึ้น
กำลังค้นหาข้อมูลเรื่องนี้อยู่พอดี ถือว่าเจอบทความดีๆ เลย
จะบอกต่อให้เพื่อนๆ ที่ต้องการเลือกดอกไม้ไปงานศพอ่านด้วย
Feel free to surf to my web page; ดอกไม้หน้างานศพ
Hey I know this is off topic but I was wondering if you knew of any widgets I could add
to my blog that automatically tweet my newest twitter updates.
I’ve been looking for a plug-in like this for quite some time and was hoping maybe you would have some experience with something like this.
Please let me know if you run into anything. I truly enjoy
reading your blog and I look forward to your new updates.
Everyone loves what you guys are usually up too. Such clever work and
reporting! Keep up the awesome works guys I’ve included you
guys to our blogroll.
Here is my blog :: Cap Haitien Hotels
บทความนี้เกี่ยวกับพวงหรีดดอกไม้ เป็นประโยชน์สุดๆ
การรู้ว่าดอกไม้แต่ละชนิดมีความหมายอย่างไร ช่วยให้เลือกได้ตรงความรู้สึกมากขึ้น
จะบอกต่อให้เพื่อนๆ ที่ต้องการเลือกดอกไม้ไปงานศพอ่านด้วย
Look at my site; จัดดอกไม้หน้าเมรุ ราคาถูก
I am not sure where you’re getting your info, but great topic.
I needs to spend some time learning much more or understanding more.
Thanks for excellent information I was looking for this
info for my mission.
Check out my blog :: Senior Medical Center Miami
Hey exceptional website! Does running a blog like this require a large amount of work?
I’ve very little knowledge of computer programming however I was hoping to start my own blog soon. Anyway, should you have any suggestions or techniques for new blog owners please share.
I understand this is off subject however I simply had to ask.
Kudos!
Wow, that’s what I was exploring for, what a material! present here at
this web site, thanks admin of this site.
Also visit my web blog … Car Rental Cap Haitien
It’s going to be ending of mine day, however before ending I am reading this
great paragraph to improve my experience.
Also visit my web site Cap Haitien Hotels
Greetings! Very helpful advice in this particular article!
It is the little changes which will make the largest changes.
Thanks a lot for sharing!
my webpage: Appliance Repair Boca Raton FL
Hi there, I enjoy reading all of your article post.
I like to write a little comment to support you.
Here is my blog post … Hotels in Okap
I love that HepatoBurn focuses on natural detox and liver support.
With everything our bodies go through daily, it’s great to have a
supplement that helps cleanse from the inside
out.
What’s up to every single one, it’s genuinely a pleasant
for me to pay a visit this website, it contains precious Information.
My website – JT Appliance Repair
I’m really enjoying the design and layout of your blog.
It’s a very easy on the eyes which makes it much more pleasant for me to come here and visit more often. Did you hire out a developer to create your theme?
Exceptional work!
Take a look at my web page … Car Rental Cap Haitien
I’m no longer positive where you are getting your information, but great topic.
I must spend a while studying more or understanding more.
Thanks for excellent information I used to be on the lookout for this information for my mission.
Cheers! Lots of data!
The other day, while I was at work, my sister stole my iphone and tested to see if it can survive a 40 foot drop,
just so she can be a youtube sensation. My apple ipad is
now destroyed and she has 83 views. I know this is totally off topic but I
had to share it with someone!
Hello! Quick question that’s entirely off topic.
Do you know how to make your site mobile friendly? My weblog looks weird when browsing from my apple
iphone. I’m trying to find a theme or plugin that might be
able to correct this problem. If you have any suggestions, please share.
Thank you!
Check out my blog post :: հաշվապահական ծառայություն
I could not resist commenting. Well written!
Here is my web site – hashvapah
I have read a few just right stuff here. Definitely worth bookmarking for
revisiting. I surprise how much effort you place to make this type of magnificent informative site.
Also visit my web-site … հաշվապահական գրասենյակ
Wonderful facts Kudos!
This is a topic that’s close to my heart… Take care!
Where are your contact details though?
Hi there! This is my first visit to your blog! We are a collection of volunteers and starting a new initiative in a community in the same niche. Your blog provided us useful information to work on. You have done a marvellous job!
Also visit my homepage :: https://Dubaiembroidery.ae/
Hi there to every body, it’s my first visit of this webpage;
this webpage includes remarkable and genuinely fine data in favor of visitors.
I think this is one of the most important information for me.
And i’m glad reading your article. But wanna remark on few general things, The website style is
great, the articles is really great : D. Good job, cheers
Here is my website: հաշվապահ
I am extremely inspired with your writing talents as neatly as with
the layout in your weblog. Is that this a
paid subject matter or did you customize it your
self? Either way keep up the nice high quality writing,
it is uncommon to see a great blog like this one these
days..
Appreciate the recommendation. Will try it out.
Hello, i read your blog occasionally and i own a similar one and
i was just curious if you get a lot of spam responses?
If so how do you protect against it, any plugin or
anything you can suggest? I get so much lately it’s driving me crazy so any help is very much appreciated.
Also visit my webpage – hashvapahakan grasenyak
I was recommended this blog by means of my cousin. I am not certain whether this post
is written by him as no one else understand such designated approximately
my trouble. You’re wonderful! Thanks!
Also visit my page :: հաշվապահ
Heya i am for the first time here. I came across this board and I find It truly useful & it helped
me out much. I hope to give something back and aid others like you aided me.
Also visit my website; հաշվապահական ընկերություններ
I’ve been exploring for a little bit for any
high quality articles or weblog posts in this sort of area .
Exploring in Yahoo I at last stumbled upon this site. Studying this
information So i’m happy to show that I have a very good uncanny feeling I discovered
just what I needed. I such a lot certainly will make certain to do not omit this website and provides it
a look on a constant basis.
Also visit my web site hosting approach
I do agree with all of the ideas you’ve presented
in your post. They are very convincing and can certainly work.
Still, the posts are very short for starters. May you please prolong
them a bit from subsequent time? Thank you for the post.
Also visit my blog; հաշվապահական ընկերություններ
I seriously love your website.. Pleasant colors & theme.
Did you develop this web site yourself? Please reply back as I’m wanting to create my very own blog and would love to know where you got this from or just what the theme is called.
Kudos!
Feel free to surf to my webpage :: հաշվապահական ծառայություն
What’s up i am kavin, its my first time to commenting anyplace,
when i read this paragraph i thought i could also make comment due to this brilliant article.
Also visit my page: հաշվապահական ընկերություններ
This video was super informative! HepatoBurn seems like a trusted, no-nonsense way to
boost liver function and overall wellness without harsh cleanses.
Hey There. I found your blog using msn. This is an extremely well
written article. I’ll make sure to bookmark it and come
back to read more of your useful information. Thanks for the post.
I will certainly comeback.
Feel free to visit my web site: հաշվապահական ծառայություններ
This is really interesting, You’re an overly professional blogger.
I’ve joined your rss feed and sit up for in the hunt for more of your
magnificent post. Also, I’ve shared your web site in my social networks
I am genuinely grateful to the owner of this site who has shared this
fantastic piece of writing at here.
My website :: հաշվապահական գրասենյակ
I’ve been browsing online greater than three hours today, but I never discovered any interesting article like yours.
It’s beautiful price enough for me. In my view, if all webmasters and bloggers made
excellent content as you did, the net will likely be much more useful than ever before.
my homepage … հաշվապահ
When I initially commented I clicked the “Notify me when new comments are added” checkbox and now each time a comment
is added I get four e-mails with the same comment. Is there any way you can remove me from that service?
Thanks a lot!
My blog – հաշվապահական ընկերություններ
Nice blog here! Also your website loads up very fast!
What web host are you using? Can I get your affiliate
link to your host? I wish my website loaded up as fast as yours lol
Hello! I could have sworn I’ve been to this website
before but after browsing through some of the post
I realized it’s new to me. Anyways, I’m definitely happy I found it and I’ll be book-marking and checking back frequently!
My web page :: հաշվապահական գրասենյակ
If you want to get a good deal from this paragraph then you have to apply these
methods to your won webpage.
Review my web blog – հաշվապահ
As tthe admin oof thiss web pagge iis working, no doubt
very quuickly it will be famous, due tto itts
quaality contents.
Il Trips è un trattato internazionale promosso dall’Organizzazione mondiale del commercio, meglio conosciuta
come OMC, al fine di fissare lo standard per la tutela della proprietà intellettuale.
Stop by my web blog brevetto traduzione inglese
Hi there, always i used to check web site posts here in the early hours in the dawn, since i enjoy to learn more and more.
I’m truly enjoying the design and layout of your blog.
It’s a very easy on the eyes which makes it much more enjoyable
for me to come here and visit more often. Did you hire out a designer to create your theme?
Exceptional work!
I couldn’t resist commenting. Well written!
Can’t get enough of good wine. Doesn’t matter
if it’s dry or sweet, it’s the perfect way to relax.
Who else ehjoys wine tasting? #RedWine
Also visit my site – ขาย wine
Do you have any video of that? I’d care to find out more details.
Feel free to surf to my website; https://www.uniform-factory.net/medical-scrubs.html
I loved as much as you’ll receive carried out right here.
The sketch is attractive, your authored subject matter
stylish. nonetheless, you command get bought an shakiness over that you wish be delivering
the following. unwell unquestionably come more formerly
again since exactly the same nearly a lot often inside case you shield this increase.
Hello! I’ve been following your web site
for some time now and finally got the bravery to go ahead and give you a shout out
from Kingwood Tx! Just wanted to tell you keep up the great work!
Hello every one, here every person is sharing these kinds of experience, so
it’s good to read this blog, and I used to pay a quick visit this
webpage daily.
I’m gone to say to my little brother, that he should also
pay a quick visit this website on regular basis to obtain updated from hottest reports.
Howdy! This is kind of off topic but I need some help from an established blog.
Is it tough to set up your own blog? I’m not very techincal but I can figure things
out pretty fast. I’m thinking about making my own but I’m not sure where to begin.
Do you have any points or suggestions? Thank you
Here is my web-site: St. Lucia Passport
Nicely put. With thanks.
Greetings! Very useful advice Relationship counselling in Mitcham this particular post!
It is the little changes that make the most significant changes.
Many thanks for sharing!
Dozens of individual digital tokens fall under the umbrella of “crypto”, so choosing the currency with the best coverage on sports betting sites is important.
Normally I don’t read article on blogs, but I would
like to say that this write-up very forced
me to take a look at and do it! Your writing style has
been surprised me. Thank you, very nice post.
my site Temporary Residency in Malta
After exploring a number of the blog posts on your web page, I
truly like your way of writing a blog. I saved it to my bookmark website list and will be checking back in the near future.
Please check out my website as well Depression and anxiety in Croydon tell me how you feel.
A unique type of bet for the NFL is puck line wagering which is a 1.5-goal spread.
บทความนี้ให้ข้อมูลมีประโยชน์มากครับ ถ้าใครกำลังมองหาผู้ให้บริการตกแต่งงานศพ ผมแนะนำลองดูร้านที่มีผลงานจริงและรีวิวดี ๆ ครับ
So it’s a must to sort of go wanting if you wish to do extra with it. Tim talks in regards to the shallowness movement, an idea I’ve at all times found sort of foolish. Valentine Nats (It would not embody Fred Valentine): Tim Jordan, Bill Kay and Alex Sabo. Like Michael, Tim Jordan left Washington for new York, enjoying for each the Highlanders and Dodgers. Another participant who left to have kids, Onslow’s years taking part in in the majors were 1912, 1913, 1918 and 1927. February sixteen Permalink I know Ryan at Distinguished Senators hates Spring Training. The prisoners are left in control of the Astral Queen. An assault group from Galactica arrives while one of the prisoners is proving his brutality. When he talks with Jamie Bamber, you may nearly hear him saying,”I was once a heartthrob just such as you.” Leaving the prisoners to their units points out the civilizing, if one may use that term loosely, effect of political legitimacy. Well, that brings up the Mandela Effect. I never read any of his novels apart from the last page of And The Devil will Drag You Under because Joe Mayhew made an appearance. 3. Has Ms. Hogben truly read and understood either of these studies, or is she only going by journalists’ typically-mistaken interpretations of scientific research they don’t necessarily know easy methods to read, either?
I’m not sure exactly why but this web site is loading incredibly slow for me.
Is anyone else having this problem or is it a problem
on my end? I’ll check back later on and see if
the problem still exists.
Attractive section of content. I just stumbled upon your website
and in accession capital to say that I acquire in fact loved
account your blog posts. Any way I will be subscribing in your
augment and even I fulfillment you get admission to persistently rapidly.
บทความนี้ให้ข้อมูลมีประโยชน์มากครับ ถ้าใครกำลังมองหาร้านจัดดอกไม้งานศพ ผมแนะนำลองดูร้านที่มีผลงานจริงและรีวิวดี ๆ ครับ
Hey there are using WordPress for your blog platform? I’m new to the blog world but I’m trying to get started and create my own.
Do you need any coding knowledge to make your own blog? Any help would be greatly
appreciated!
Can’t get enough of good vintage wine. From a local vineyard or
imported, wine always makeds the moment better.
Anyone else here love wine?
Also visit my site – แชมเปญ
ชอบแนวคิดที่แชร์ไว้ในบทความนี้ครับ ถ้าใครกำลังมองหาผู้ให้บริการตกแต่งงานศพ ผมแนะนำลองดูร้านที่มีผลงานจริงและรีวิวดี ๆ ครับ
We absolutely love your blog and find many of your post’s to
be what precisely I’m looking for. Would you offer guest
writers to write content to suit your needs?
I wouldn’t mind producing a post or elaborating on a number
of the subjects you write related to here. Again, awesome web
log!
my web site – vpn (http://tinyurl.com/)
I rezlly enjoy good wine. Frrom a local vineyard or imported, it’s
the perfect wayy to relax. Who else enjoys wine tasting? #WhiteWine
My blog :: Nadine
ขอบคุณสำหรับบทความดี ๆ ครับ
ถ้าใครกำลังมองหาบริการจัดดอกไม้งานศพ ผมแนะนำลองดูร้านที่มีผลงานจริงและรีวิวดี ๆ ครับ
I’m a huge fan of golod wine. Whether it’s red or white, it’s the perfect
way to relax. Are there anny wine lovers around?
Also visit my web bloig ไวน์ราคา
I’m truly enjoying the design and layout of your website. It’s a very easy on the eyes which makes it much more pleasant for me to come here and visit more often. Did you hire out a developer to create your theme? Great work!
My web-site :: https://www.tshirts-supplier.com/men-polo-shirts.html
Thank you for another informative site. The place else
may just I am getting that type of info written in such an ideal manner?
I’ve a undertaking that I’m just now operating on, and I’ve been on the glance out for
such information.
Cool blog! Is your theme custom made or did you download it from somewhere?
A design like yours with a few simple tweeks would really make
my blog stand out. Please let me know where you got your theme.
Cheers
My spouse and I stumbled over here by a different website and thought I might as well check things out.
I like what I see so i am just following you. Look forward to finding out about
your web page for a second time.
ชอบแนวคิดที่แชร์ไว้ในบทความนี้ครับ
ถ้าใครกำลังมองหาร้านจัดดอกไม้งานศพ ผมแนะนำลองดูร้านที่มีผลงานจริงและรีวิวดี ๆ ครับ
A motivating discussion is definitely worth comment.
I do think that you ought to publish more about this issue, it may not be a taboo subject
but generally people do not speak about such topics. To the next!
Cheers!!
“This Aqua Tower system looks like a game-changer! Clean water without electricity or plumbing? That’s perfect for emergencies or even everyday home use.”
When I initially commented I clicked the “Notify me when new comments are added” checkbox and
now each time a comment is added I get three e-mails with the same
comment. Is there any way you can remove people from that service?
Thank you!
I just could not go away your website before suggesting
that I actually loved the usual info a person provide
in your guests? Is gonna be again often in order to investigate cross-check
new posts
Attractive section of content. I just stumbled upon your site and in accession capital to say that I acquire actually enjoyed account your blog posts.
Anyway I’ll be subscribing in your augment or even I achievement you get entry to constantly fast.
Hookah Lounge link (posteezy.com)
Our painting and decorating service cover residential and commercial properties in and around Bristol.
Everything is very open with a really clear explanation of the challenges.
It was definitely informative. Your site is extremely helpful.
Many thanks for sharing!
Hey just wanted to give you a quick heads up and let you know a few
of the pictures aren’t loading correctly. I’m not sure why but I think
its a linking issue. I’ve tried it in two different internet browsers and both
show the same outcome.
This evening course offers a flexible schedule, allowing learners to learn paint and decorating skills
while accommodating their other commitments.
I’m a huge fan of good glass off wine. Doesn’t matter if it’s dry or sweet, it just elegates
any occasion. Anyone else here love wine?
Also visit my webpage; ขายไวน์ราคาส่ง
Hi there very nice blog!! Guy ..Beautіfuⅼ .. Suρerb ..
I will bookmark your site and take the feeds аdditionally?
I am glad to search out numerous һelpfᥙl information right here
within the publish, we’d like work out more techniques on this regard, thank you foor sһaring.
. . . . .
Feel free to visit my web page: จัดไม้งานศพ
You’ve made some good points there. I looked on the internet for additional information about the issue and found most people will go along
with your views on this web site.
This is really fascinating, You’re a very skilled blogger.
I’ve joined your feed and sit up for in search of
more of your magnificent post. Additionally, I have shared your web site
in my social networks
my web-site: Hotels near Siquijor Island
Hey are using WordPress for your blog platform?
I’m new to the blog world but I’m trying to get started and
create my own. Do you require any coding expertise to make your own blog?
Any help would be really appreciated!
Have a look at my site; Boutique-Hotels Siquijor
Thanks for sharing your info. I really appreciate your efforts and I will be waiting
for your next post thank you once again.
my homepage … Infidelity digital evidence
Fantastic beat ! I would like to apprentice whilst you amend your website, how can i subscribe Price for a forensic investigation on a cell phone a blog website?
The account aided me a appropriate deal. I had been a little bit acquainted of
this your broadcast provided bright transparent idea
Appreciate this post. Let me try it out.
I was recommended this blog via my cousin. I am no longer sure whether or not this submit is written by way of him as no one else
understand such particular about my problem. You are amazing!
Thank you!
I all the time used to read article in news papers but
now as I am a user of web so from now I am using net for
content, thanks to web.
my web site https://englishsunglish.com/why-double-glazed-windows-are-a-smart-investment-for-every-home/
I’m a huge fan of good glass of wine. From a local vineyard or imported, wine always makes the moment better.
Who else enjoys wine tasting? #WhiteWine
Feeel free to surf to my web-site :: ร้าน ขาย ไวน์
Hey! I know this is kind of off topic but I was wondering
if you knew where I could locate a captcha plugin for my comment
form? I’m using the same blog platform as yours and I’m having problems finding one?
Thanks a lot!
my web-site – breathwork in Zurich
Great site you have here but I was wondering if you knew of any
community forums that cover the same topics discussed here?
I’d really like to be a part of online community where I can get feedback from
other knowledgeable people that share the same interest.
If you have any recommendations, please let me know.
Thank you!
My blog post … transformational retreat
Excellent site you have got here.. It’s hard to find high quality writing like yours these days.
I truly appreciate individuals like you! Take care!!
Have you ever thought about including a little bit more
than just your articles? I mean, what you say is valuable and
all. However think about if you added some great visuals or video clips to give your posts more, “pop”!
Your content is excellent but with images and videos,
this site could certainly be one of the very best in its field.
Excellent blog!
Here is my homepage … Hotel Siquijor
I’m not sure where you’re getting your information, but great
topic. I neds to spend some time learming much more
or understanding more. Thanks for wonderful info I was looking for this info forr
my mission.
Look into myy wepage – Vickie
Hi there! Someone in my Facebook group shared this website with us
so I came to look it over. I’m definitely loving the information.
I’m book-marking and will be tweeting this to my followers!
Terrific blog and wonderful style and design.
Also visit my blog post Mindfulness retreat
Thanks for sharing your thoughts about Computer Forensics North Carolina forensics
services. Regards
After reading this and checking out this [Fireflies.ai free trial](https://stan.store/LovedByCreators/p/is-firefliesai-good-i-ran-33-meetings-to-learn), I finally signed up for the Fireflies.ai trial.
The CRM integrations alone are worth it.
whoah this blog is fantastic i love reading your posts.
Stay up the good work! You know, a lot of persons are looking around for this info, you could aid them greatly.
My web site – Hotel Siquijor
I like what you guys tend to be up too. Such clever work and exposure!
Keep up the wonderful works guys I’ve incorporated you guys to my personal blogroll.
my homepage breathwork in Zurich
“Wow, I never knew there was a natural alternative like Kerassentials for nail fungus! The way it uses essential oils to get right to the root sounds way better than those harsh chemical creams I’ve tried before. Definitely adding this to my routine!
Inspiring quest there. What occurred after? Thanks!
My page … Boutique-Hotels Siquijor
Amazing! This blog looks exactly like my old one!
It’s on a entirely different subject but it has pretty much
the same page layout and design. Excellent choice of colors!
Also visit my web-site; breathwork in Zurich
Hello! Do you use Twitter? I’d like to follow you if that would be ok.
I’m undoubtedly enjoying your blog and look forward to new posts.
Check out my web-site: breathwork in Zurich
Very shortly this web site will be famous amid all blogging and
site-building visitors, due to it’s nice posts
Also visit my web page breathwork in Zurich
Now I am ready to do my breakfast, afterward having
my breakfast coming again to read additional news.
The government defines a “family business” as
one where all your employees are closely related to you (as a
spouse, civil partner, sibling, child, parent, grandparent, grandchild,
step-parent, stepchild or half-sibling).
Hello, I enjoy reading all of your article post. I wanted to write a
little comment to support you.
I don’t even know how I ended up here, but I thought this post was good.
I don’t know who you are but certainly you’re going to a famous blogger if you aren’t already
😉 Cheers!
Appreciate the recommendation. Will try it out.
My blog post https://Totebags.ae/
Hello! Do you use Twitter? I’d like to follow you if that would be ok.
I’m definitely enjoying your blog and look forward to new posts.
Having read this I thought it was really informative.
I appreciate you finding the time and effort to put this content
together. I once again find myself personally spending a significant amount of time both reading and
commenting. But so what, it was still worth it!
You’ve made some good points there. I looked on the internet
to find out more about the issue and found most people will go along with your views on this web site.
воронин владимир александрович фск
Hmm it seems like your blog ate my first comment (it
was extremely long) so I guess I’ll just sum it up what I submitted and say, I’m thoroughly enjoying your blog.
I too am an aspiring blog blogger but I’m still new to the whole
thing. Do you have any tips and hints for inexperienced blog writers?
I’d definitely appreciate it.
It’s great to see a supplement like Prime Biome
that addresses the gut-skin connection. The blend of probiotics and
prebiotics can improve digestion, and the added herbal
ingredients like Babchi and Fenugreek support skin health by boosting collagen and reducing
inflammation. The fact that it’s non-GMO and free from
synthetic chemicals makes it a trustworthy choice for those looking to enhance their overall health
Having read this I believed it was very informative. I appreciate you spending some time and energy to put this article together.
I once again find myself spending a lot of time both reading and commenting.
But so what, it was still worth it!
I was suggested this blog through my cousin. I am
no longer sure whether or not this publish is written by means of him as no one else recognize
such unique approximately my problem. You’re wonderful!
Thanks!
Причин этому несколько, одна из них – оставить за собой право просматривать ролик без подключения к интернету,
опасаясь, что он может быть удален.
Great items from you, man. I’ve understand your stuff previous to and you’re simply extremely magnificent.
I really like what you’ve received here, really like what you are stating and
the way in which wherein you say it. You are making it
enjoyable and you still take care of to stay it sensible. I cant
wait to learn much more from you. This is actually a wonderful website.
Hello There. I found your blog using msn. This is a really well written article.
I’ll be sure to bookmark it and come back to read more of your useful information. Thanks for the post.
I’ll definitely return.
https://w-rabbit.com/
great put up, very informative. I’m wondering whhy
the opposite specialists of this sector do not
understand this. Youu must proceed your writing. I’m confident, you have a huge readers’ base already!
my homepage – จัดไม้งานศพ
I got this site from my buddy who told me about this web site
and now this time I am browsing this website and reading very
informative articles here.
Hi i am kavin, its my first occasion to commenting
anywhere, when i read this article i thought i could also make
comment due to this sensible article.
Wonderful beat ! I would like to apprentice while you amend your web site,
how can i subscribe for a blog website? The account helped me a acceptable deal.
I had been a little bit acquainted of this your broadcast
offered bright clear idea
“Thanks for breaking this down so clearly! I had no idea how much gut health impacts overall wellness.
Prime Biome sounds like a solid, natural option.”
Hi there friends, its enormous piece of
writing regarding teachingand entirely explained, keep
it up all the time.
I am not sure where you are getting your info, but great topic.
I needs to spend some time learning more or understanding more.
Thanks for fantastic info I was looking for this information for
my mission.
I absolutely love your blog and find nearly all
of your post’s to be just what I’m looking for.
Do you offer guest writers to write content for yourself?
I wouldn’t mind creating a post or elaborating on most
of the subjects you write regarding here. Again, awesome site!
We are a bunch of volunteers and starting a new scheme in our community.
Your web site offered us with useful information to work on. You have performed a formidable process and our entire
group can be grateful to you.
I am sure this piece of writing has touched all the internet people, its
really really fastidious post on building up new web site.
“This is seriously impressive tech! Producing up to 60 gallons
of clean water a day just from air? The Aqua Tower could be a total game-changer, especially
in areas with water shortages.”
Pretty element of content. I just stumbled upon your blog and in accession capital
to claim that I get actually enjoyed account your weblog posts.
Any way I’ll be subscribing to your feeds or even I achievement you get right of
entry to consistently fast.
https://pargirlmothers.com/
It’s enormous that you are getting ideas from this piece of writing as well as
from our discussion made at this time.
You said this well!
This post is genuinely a nice one it assists new web viewers, who are wishing in favor of blogging.
My web page; Bel-Air mansion photographer
Does your site have a contact page? I’m having problems locating it but, I’d like
to send you an e-mail. I’ve got some recommendations for your blog
you might be interested in hearing. Either way, great blog
and I look forward to seeing it develop over time.
Also visit my site – Recruitment Australia
obviously like your web-site however you need to test the spelling on several of your posts.
A number of them are rife with spelling problems and I in finding it very bothersome to inform the truth however I will certainly
come back again.
Feel free to surf to my page … Paramount Recruitment
Hi! I could have sworn I’ve been to your blog before but after
browsing through many of the posts I realized it’s new to me.
Regardless, I’m certainly happy I came across it and I’ll be
book-marking it and checking back frequently!
Thanks on your marvelous posting! I truly enjoyed reading it, you may be a
great author.I will be sure to bookmark your blog
and will often come back sometime soon. I want to encourage you to continue your great writing, have
a nice day!
Stop by my site; 강남호빠
hello!,I really like your writing so much!
percentage we keep up a correspondence extra approximately your article on AOL?
I require a specialist in this space to resolve my problem.
May be that’s you! Having a look forward to see you.
I do not know whether it’s just me or if perhaps everybody else experiencing issues with your website.
It appears like some of the text within your posts are running off
the screen. Can someone else please provide feedback
and let me know if this is happening to them too?
This may be a problem with my web browser because I’ve had this happen previously.
Appreciate it
Here is my webpage – taylor swift official video
This site was… how do I say it? Relevant!!
Finally I’ve found something that helped me. Cheers!
My site … 강남호빠
Hi there, just became alert to your blog through
Google, and found that it is really informative.
I am gonna watch out for brussels. I’ll appreciate if you continue this in future.
A lot of people will be benefited from your writing.
Cheers!
Take a look at my web site – country songs
That is a very good tip particularly to those fresh to the blogosphere.
Brief but very precise information… Appreciate your sharing this one.
A must read article!
Wonderful beat ! I would like to apprentice while you amend your web site, how can i subscribe
for a blog website? The account aided me a acceptable deal.
I had been a little bit acquainted of this your broadcast
offered bright clear concept
Review my web page … Workplace Training
I’m amazed, I must say. Rarely do I encounter a
blog that’s both equally educative and interesting, and without a doubt, you’ve hit
the nail on the head. The issue is something which too few men and
women are speaking intelligently about. I am very happy I came across this in my
search for something concerning this.
Here is my web site :: 카지노솔루션
Thanks for sharing your thoughts. I truly appreciate your efforts and
I am waiting for your next post thanks once again.
My homepage … iplwin latest version
Nice post. I learn something totally new and challenging on sites I stumbleupon on a daily basis.
It’s always useful to read through articles from other writers and use a little something from their websites.
Feel free to surf to my web site vipertoto
Hmm is anyone else experiencing problems with the images on this
blog loading? I’m trying to figure out if its a problem on my end or
if it’s the blog. Any feed-back would be greatly appreciated.
Greetings! Very useful advice within this post!
It’s the little changes that will make the most important changes.
Thanks for sharing!
Here is my web-site Paramount Recruitment Services
Everything is very open with a precise explanation of the issues.
It was truly informative. Your website is useful.
Many thanks for sharing!
Paragraph writing is also a excitement, if you
be familiar with after that you can write if not it is difficult to write.
Here is my web site – youtube alternative app without ads
Hi there to all, for the reason that I am really eager of reading this webpage’s
post to be updated daily. It consists of nice data.
Also visit my website :: iplwin latest version
Howdy! Someone iplwin in my Myspace group shared this website with us so
I came to take a look. I’m definitely enjoying the information. I’m bookmarking and will
be tweeting this to my followers! Fantastic blog and great style and design.
hi!,I love your writing so much! percentage we communicate extra about your post on AOL?
I require an expert in this house to resolve my problem.
May be that’s you! Taking a look ahead to
look you.
Feel free to visit my blog post iplwin app
If you desire to get a good deal from this article
then you have to apply these techniques to your won web site.
Your style is very unique compared to other folks I have read stuff
from. I appreciate you for posting when you have
the opportunity, Guess I’ll just bookmark this blog.
Nicely put, Cheers!
Here is my webpage; https://classfollow.com/read-blog/3313_uncovering-the-truth-behind-baccarat-sites-discover-the-inavegas-scam-verificati.html
Having read this I believed it was rather enlightening.
I appreciate you finding the time and energy to put this short article together.
I once again find myself spending a lot of time both reading and leaving comments.
But so what, it was still worthwhile!
It’s very straightforward to find out any topic on net as compared to
books, as I found this paragraph at this website.
my blog post :: HR and Recruitment Australia
Attractive part of content. I simply stumbled upon your web
site and in accession capital to say that I acquire actually enjoyed account your weblog
posts. Anyway I will be subscribing on your feeds
and even I achievement you access constantly rapidly.
Hello there! I know this is kind of off topic but I was wondering if you knew where I could find a captcha plugin for my comment form?
I’m using the same blog platform as yours and I’m having
trouble finding one? Thanks a lot!
Having read this I believed it was really enlightening.
I appreciate you finding the time and effort to put this article together.
I once again find myself spending a lot of time both reading and posting comments.
But so what, it was still worth it!
This is such a game-changer! I’ve been looking for a reliable water purifier that doesn’t rely on electricity.
The Aqua Tower looks perfect for both home use and
camping trips. Thanks for breaking it down so clearly!
Hello, i believe that i noticed you visited my web site thus i came to go back the desire?.I am attempting to find things to improve my web site!I suppose its adequate to use
a few of your ideas!!
As the admin of this web page is working, no question very quickly
it will be well-known, due to its feature contents.
Here is my website eharmony special coupon code 2025
Keep on working, great job!
my website; https://www.nigeriauniforms.com
Keast, Jackie (eight December 2023). “‘The brand new Boy’, ‘Speak to Me’, ‘The Newsreader’, ‘The Misplaced Flowers of Alice Hart’ lead AACTA nominees”.
That is a list of tv packages and motion pictures that have been formerly broadcast by the Australian pay tv channel SF, which closed 31
December 2013 and was changed by Syfy. Jonas Quinn is a fictional character within the Canadian-American television series
Stargate SG-1, a science fiction show a few military workforce exploring the galaxy by way of a network of alien transportation devices.
Phrase is that Gary Busey got so into the character he was enjoying that he really advert-libs a superb portion of his dialogue in the movie.
All: is now not useful, and tends to provide unexpected outcomes (e.g.
no matches, or those containing the word all). Written by Stephen King and Joe Hill, “In the Tall Grass” is a surreal tale
of a gaggle of people trapped in a grassy subject during which time and area not make lots of sense.
The influence on the river and the individuals who
depended on it for his or her livelihoods was severe.
I go to see each day a few websites and information sites to
read articles, but this blog gives feature based content.
Very nice article. I definitely appreciate this site.
Thanks!
My family all the time say that I am wasting my time
here at web, but I know I am getting familiarity daily by reading thes nice articles.
Hi, everything is going well here and ofcourse every one is sharing data,
that’s actually good, keep up writing.
Very nice blog post. I certainly appreciate this site.
Keep writing!
my page :: Slot Game
I’ve always been fascinated by the idea of the pineal gland
being our “third eye.” Love that Pineal XT focuses on detoxifying it
naturally—definitely something I’m interested in trying!
It’s remarkable designed for me to have a website, which is helpful
in favor of my know-how. thanks admin
I got this web site from my pal who informed me about this site and now
this time I am browsing this web site and reading
very informative articles at this time.
https://reinventingthebible.com/
Čau lidi, jestli hledáte fakt dobré kasinovou platformu s bohatou nabídkou her, výhodné bonusy a fajnovým prostředím, nejlepší volba je https://dgb.225kz.cc/space-uid-73914.html. Bonusy jsou tam fakt peckový, přihlášení je rychlé přes spinmama casino login a k tomu pohodlnou appku, kde můžete hrát kdykoliv a kdekoliv. Mají často promo kódy, které nabízí free spiny a super bonusy. Mám z toho fakt radost – všechno je plynulé, férové a bez zbytečných průtahů. Kdo chce pohodovou a zábavnou hru bez stresu, tohle kasino stojí za to. Díky!
ชอบแนวคิดที่แชร์ไว้ในบทความนี้ครับ
ถ้าใครกำลังมองหาร้านจัดดอกไม้งานศพ
ผมแนะนำลองดูร้านที่มีผลงานจริงและรีวิวดี ๆ ครับ
My brother suggested I might like this website. He was once totally right.
This submit actually made my day. You can not consider simply how much
time I had spent for this info! Thanks!
บทความนี้ให้ข้อมูลมีประโยชน์มากครับ ถ้าใครกำลังมองหาบริการจัดดอกไม้งานศพ
ผมแนะนำลองดูร้านที่มีผลงานจริงและรีวิวดี ๆ
ครับ
Finally, a testosterone booster that focuses on natural ingredients!
PhaloBoost sounds like a solid option for guys looking to feel more energized and improve overall performance without harsh side effects.
ขอบคุณสำหรับบทความดี ๆ ครับ ถ้าใครกำลังมองหาร้านจัดดอกไม้งานศพ ผมแนะนำลองดูร้านที่มีผลงานจริงและรีวิวดี ๆ
ครับ
Moin,
hat jemand von euch schon mal was von http://zespol-teatralny.eu/2024/05/11/the-joy-of-giving-serving-others-with-a-generous-heart/ gehört?
Ich bin neulich drüber gestolpert, wegen dem Angebot mit Free Spins ohne Einzahlung.
Dachte erst, das ist wieder so ein 0815-Ding, und wurde positiv überrascht. Nach dem Login gab’s direkt Freispiele, ohne dass ich etwas einzahlen musste.
Die Seite läuft stabil und übersichtlich. Was mir besonders gefällt:
Selbst wenn man länger dabei ist, gibt’s immer wieder Codes. Gibt’s nicht überall.
Auch die Umsatzbedingungen sind klar. Ich bleib mal dran.
Würd mich interessieren, wie ihr das seht.
If you would like to take a great deal from this piece of writing then you have to apply these methods
to your won web site.
Estuve buscando sitios para jugar online y me topé con http://toycarland.com/blog.php?aidx=216099, y la verdad que me dejó buena impresión. El acceso es súper fácil, sin tener que dar mil datos. La versión para el móvil me anda fluida, incluso en un Android que ya tiene sus años. Se nota que no es un copia-pega de la web, no como otras que te sacan de la partida cada rato. El tema del bono de bienvenida también suma. No es una de esas promos que te piden cumplir mil requisitos raros, acá te lo dan sin complicaciones y es útil para empezar. Y lo mejor: después siguen tirando beneficios cada tanto, no es solo una vez y ya. Además, algo que me gustó es que el soporte está en español, y cuando me trabé con una promo, me resolvieron el tema sin drama. En resumen, si alguien anda buscando algo que valga la pena, yo diría que Spinmama está muy bien. No digo que sea perfecto, pero por ahora todo me va de 10.
Great goods from you, man. I’ve understand your
stuff previous to and you are just extremely fantastic.
I actually like what you have acquired here, really like
what you are stating and the way in which you say it.
You make it enjoyable and you still care for to keep
it wise. I can’t wait to read far more from you.
This is actually a tremendous site.
Oi, gente! Quero compartilhar uma parada sobre o https://valetinowiki.racing/wiki/User:ReganSouthwick8, que tá bombando no mundo dos jogos online. O tigrinho dourado é carismático e o jogo é acessível, atraindo novatos e jogadores experientes. Essa questão dos horários que rendem mais prêmios deixa o jogo ainda mais intrigante pra quem joga. Claro que não existe garantia, mas isso aumenta a expectativa e a adrenalina a cada giro. E o mais importante: a plataforma realmente paga, dando aquela segurança que todo mundo quer na hora de apostar. Se emoção, estratégia e mistério são sua praia, o Fortune Tiger não pode faltar na sua lista. Mas sempre joga com consciência, o importante é curtir a experiência.
Thanks a bunch for sharing this with all of us you really recognize what you are talking about!
Bookmarked. Please additionally talk over with my website =).
We can have a link alternate arrangement
between us
It’s an awesome paragraph in support of all the web people; they will get advantage from it I am
sure.
Servus Leute,
hat jemand von euch schon mal was von http://www.icecap.co.kr/bbs/board.php?bo_table=sub0403_en&wr_id=236670 gehört?
Ich hab’s mir letztens mal angeschaut, wegen dem Bonus ohne Risiko.
War zuerst skeptisch, aber das hat sich echt gelohnt. Der Bonus war sofort nach Anmeldung aktiv, ganz ohne eigenes Guthaben.
Die Seite läuft stabil und übersichtlich. Was mir besonders gefällt:
Treue wird belohnt – das ist eher unüblich. Gibt’s nicht überall.
Auch die Umsatzbedingungen sind klar. Ich spiele jetzt öfter dort.
Falls jemand von euch auch da ist – wie sind eure Erfahrungen?.
Plinko macht einfach Laune, Leute! Ich bin mit http://www.annunciogratis.net/author/imaoden518 gestartet und war direkt gehooked – richtig chillig zum Üben und Testen. Die Plinko App läuft sauber, macht Spaß und hat coole Extras. Das Feeling, wenn die Kugel ganz unten in der hohen Auszahlung landet – unbeschreiblich. Einfach mal reinziehen – ist geiler als man denkt. Und für die Pros unter euch: Casino-Version bringt den Kick auf ein neues Level. Wer kennt gute Varianten oder Apps für Plinko?
Good information. Lucky me I discovered your blog by chance (stumbleupon).
I have saved as a favorite for later!
I’d like to find out more? I’d want to find out some additional information.
Zdravím všechny, když sháníte spolehlivé internetové kasino s širokou herním portfoliem, výhodné bonusy a fajnovým prostředím, doporučuju mrknout na https://bravepatrie.com/spip.php?article1943. Spinmama casino bonus je bomba, přihlásíte se bez problémů přes spinmama casino login a k tomu spinmama app, kde můžete hrát kdykoliv a kdekoliv. Mají často promo kódy, které vám přidají free spiny a další výhody. Líbí se mi, jak to tam všechno funguje – všechno je plynulé, férové a bez zbytečných průtahů. Kdo chce pohodovou a zábavnou hru bez stresu, Spinmama je jasná volba. Díky!
hello there and thank you for your information – I have certainly picked up something
new from right here. I did however expertise a few technical points using this site,
since I experienced to reload the website many times previous to I could get it
to load properly. I had been wondering if your web host is OK?
Not that I’m complaining, but slow loading instances times will
often affect your placement in google and could damage your
quality score if advertising and marketing with Adwords. Anyway I am adding this RSS to
my email and can look out for a lot more
of your respective intriguing content. Make sure you update this
again very soon.
It’s wonderful that you are getting ideas from this paragraph as
well as from our discussion made at this place.
Feel free to visit my web-site :: Youtu.be/cZXBn6FEMRs?si=N-tzI-RNA8ptd9am
Amazing! This blog looks just like my old one! It’s on a totally different topic but
it has pretty much the same layout and design. Great choice of colors!
Feel free to visit my web-site :: internet voor Nederlanders in Hongarije
Hurrah, that’s what I was looking for, what a data!
present here at this website, thanks admin of this web site.
Also visit my blog post :: PetCareShed dog harness
Hey! Would you mind if I share your blog with my
twitter group? There’s a lot of folks that I think
would really appreciate your content. Please let me know.
Thanks
My blog: Hungary broadband for foreigners
wonderful points altogether, you simply gained a emblem new reader.
What would you recommend in regards to your publish that you just made some days ago?
Any positive?
Feel free to visit my homepage; PetCareShed Australia dog harness
Nice post. I learn something totally new and challenging on sites I stumbleupon every day.
It’s always useful to read through content from
other authors and practice something from other
sites.
Here is my website – Hungary home WiFi easy setup
Moin,
hat jemand von euch schon mal was von http://www.career4.co.kr/bbs/board.php?bo_table=ci_consulting&wr_id=27364 gehört?
Ich hab’s mir letztens mal angeschaut, weil der No-Deposit-Bonus ganz gut aussah.
Hab’s nicht sofort ernst genommen, aber war dann echt überrascht. Direkt nach dem Einloggen kamen ein paar Free Spins, ohne dass ich etwas einzahlen musste.
Auch die Spinmama App ist ganz solide. Was mich richtig überrascht hat:
Es gibt nicht nur für neue Spieler was, sondern auch für Bestandskunden regelmäßig Bonus Codes. Das ist selten.
Ziemlich fair auf den ersten Blick. Ich bin jedenfalls positiv überrascht.
Spielt noch jemand hier bei Spinmama?.
Παιδιά, το https://oke.zone/viewtopic.php?pid=1633784 με έχει εντυπωσιάσει ως μια αξιόπιστη και καινοτόμα πλατφόρμα online καζίνο, το login είναι απίστευτα γρήγορο και εύκολο, κάτι που κάνει όλη τη διαφορά , πραγματικά υπάρχει επιλογή για όλα τα γούστα, από slots μέχρι live casino. Αυτό που μου αρέσει επίσης πολύ είναι η ασφάλεια και η διαφάνεια που προσφέρουν, κάτι που είναι κρίσιμο ειδικά για την ελληνική αγορά . Τα μπόνους τους είναι επίσης δελεαστικά και αυξάνουν πολύ την απόλαυση του παιχνιδιού . η mobile έκδοση δουλεύει άψογα και αυτό κάνει το spin mama casino ακόμη πιο πρακτικό. Το προτείνω ανεπιφύλακτα γιατί συνδυάζει όλα όσα θέλει ένας παίκτης σήμερα .
Superb site you have here but I was wanting to know if you knew of any forums that cover the same topics talked about here?
I’d really like to be a part of online community where I can get
suggestions from other knowledgeable individuals that share
the same interest. If you have any suggestions, please let me know.
Many thanks!
my blog post … PetCareShed Australia dog harness
Hello to all, since I am actually eager of reading this web site’s
post to be updated on a regular basis. It contains good data.
Here is my page; abonnement smart iptv
There’s definately a lot to know about this subject. I love all the points you made.
Παιδιά, το https://sciencewiki.science/wiki/User:BrittanyCastles με έχει εντυπωσιάσει ως μια αξιόπιστη και καινοτόμα πλατφόρμα online καζίνο, η διαδικασία σύνδεσης είναι απλή και χωρίς προβλήματα, πολύ βολική , έχει μεγάλη γκάμα παιχνιδιών, κάτι που δεν το βλέπεις εύκολα σε άλλα καζίνο . Αυτό που μου αρέσει επίσης πολύ είναι η ασφάλεια και η διαφάνεια που προσφέρουν, κάτι που είναι κρίσιμο ειδικά για την ελληνική αγορά . έχουν πολύ καλές προσφορές που σε κρατάνε ενεργό και ενθουσιασμένο. η mobile έκδοση δουλεύει άψογα και αυτό κάνει το spin mama casino ακόμη πιο πρακτικό. Το προτείνω ανεπιφύλακτα γιατί συνδυάζει όλα όσα θέλει ένας παίκτης σήμερα .
Great website. A lot of useful information here. I
am sending it to several buddies ans additionally sharing in delicious.
And certainly, thank you on your effort!
My web page; art prompt engineering
Hello! I’ve been reading your site for a while now and finally
got the courage to go ahead and give you a shout out from Dallas Tx!
Just wanted to say keep up the fantastic work!
Good post! We will be linking to this great article on our website.
Keep up the good writing.
Here is my page PetCareShed dog harness
Thank you for any other informative site. Where else may just I get that type of information written in such an ideal approach?
I’ve a mission that I am just now working on, and
I’ve been at the glance out for such information.
Hi, i think that i saw you visited my weblog thus i came to “return the favor”.I’m trying to find things to
enhance my site!I suppose its ok to use some of your ideas!!
https://jlrppatterns.com/
Hej! Ktoś już grał na https://groeberhuette.com/it/2024/04/12/eventi/? Sam trafiłem tam trochę z ciekawości i nie żałuję. Proces zakładania konta to kwestia chwili, wszystko po polsku, więc mega wygodnie. Dostałem darmowy bonus na wejściu – super sprawa, bo nie trzeba nic wpłacać. Kasyno działa szybko i stabilnie, nawet na mobilce. No i mają całkiem sporo promocji – warto sprawdzać, bo często wpadają kody bonusowe. Jak ktoś szuka czegoś nowego, a nie chce od razu inwestować kasy, to według mnie warto dać Spinmama szansę. Jakie sloty polecacie na tej platformie?
Hi, Neat post. There is a problem together with your site in internet voor Nederlanders in Hongarije explorer, could check this?
IE nonetheless is the marketplace leader and a big section of folks will miss
your wonderful writing due to this problem.
Very good site you have here but I was wanting to know if
you knew of any forums that cover the same topics discussed in this article?
I’d really love to be a part of group where I can get responses from other experienced people that share the same interest.
If you have any suggestions, please let me know.
Bless you!
wonderful post, very informative. I ponder why the opposite specialists of this sector don’t understand this.
You should proceed your writing. I’m sure, you have a huge readers’
base already!
Feel free to visit my web site: iptv premium
Παιδιά, το https://theterritorian.com.au/index.php?page=user&action=pub_profile&id=2254675 με έχει εντυπωσιάσει ως μια αξιόπιστη και καινοτόμα πλατφόρμα online καζίνο, το login είναι απίστευτα γρήγορο και εύκολο, κάτι που κάνει όλη τη διαφορά , πραγματικά υπάρχει επιλογή για όλα τα γούστα, από slots μέχρι live casino. Αυτό που μου αρέσει επίσης πολύ είναι η ασφάλεια και η διαφάνεια που προσφέρουν, κάτι που είναι κρίσιμο ειδικά για την ελληνική αγορά . Τα μπόνους και οι προσφορές κάνουν το παιχνίδι πιο διασκεδαστικό και αξίζουν . η mobile έκδοση δουλεύει άψογα και αυτό κάνει το spin mama casino ακόμη πιο πρακτικό. Είναι μια από τις καλύτερες πλατφόρμες αυτή τη στιγμή και αξίζει να τη δοκιμάσετε.
Everything is very open with a very clear description of the issues.
It was truly informative. Your site is very helpful.
Thank you for sharing!
My web blog – iptv playlist
hello!,I love your writing very much! share we keep in touch more approximately your post on AOL?
I require an expert on this area to unravel my problem.
Maybe that is you! Taking a look ahead to see you.
Feel free to surf to my blog post :: internet Hongarije maandcontract
An intriguing discussion is worth comment. I do think
that you should write more on this issue, it may not be a taboo matter but usually people do not discuss
these issues. To the next! Many thanks!!
Feel free to visit my webpage abonnement iptv 12 mois smart tv
My brother suggested I would possibly like this blog. He used to be totally right.
This publish actually made my day. You cann’t believe just how much time I had spent for this info!
Thanks!
Check out my blog post internet voor emigranten zonder gedoe
Good web site you’ve got here.. It’s hard to find quality writing like yours these
days. I seriously appreciate people like you!
Take care!!
Check out my page: internetdiensten in Hongarije
Thanks for the auspicious writeup. It in reality was once a leisure account it.
Glance complex to far delivered agreeable from you! By the way,
how could we keep in touch?
Here is my blog post :: no contract internet Hungary
이건 극도로 좋은 포스트였어요. 실제 노력으로 좋은 기사를 만드는
데 시간과 실제 노력을 들였지만, 뭐라고 해야
할까… 저는 늦추고 많이 아무것도 하지 못하는 것 같아요.
I’m more than happy to find this great site. I wanted to thank you for ones time due to this wonderful read!!
I definitely liked every little bit of it and i also have
you saved as a favorite to see new information on your web site.
Wow, marvelous blog structure! How lengthy
have you ever been blogging for? you make running a blog glance easy.
The full look of your website is wonderful, as neatly as
the content material!
https://forexfactory.my.id/
I’m not sure where you are getting your information, but great
topic. I needs to spend some time learning more
or understanding more. Thanks for great info I was looking for this info for
my mission.
my web page: no contract internet Hungary
I’m not sure where you’re getting your info, but great
topic. I needs to spend some time learning more or understanding more.
Thanks for wonderful information I was looking for this information for my mission.
Feel free to surf to my web blog: internet Hongarije maandcontract
Thank you for sharing your info. I truly appreciate your efforts and I will be waiting easiest internet for foreigners Hungary your further write ups
thanks once again.
Paragraph writing is also a excitement, if you be acquainted with then you can write or else it is difficult to write.
Feel free to visit my web-site; Hungary internet providers
An outstanding share! I have just forwarded this onto a colleague who has been doing a little research on this.
And he in fact ordered me dinner simply because I found it for him…
lol. So allow me to reword this…. Thank YOU for the meal!!
But yeah, thanx for spending the time to discuss this issue here
on your blog.
my page; order internet Hungary
This is a topic that’s near to my heart… Take care!
Where are your contact details though?
Feel free to visit my page :: internet zoals in Nederland in Hongarije
I think everything typed was actually very logical.
However, consider this, what if you wrote a catchier post
title? I mean, I don’t wish to tell you how to run your blog,
however what if you added something that makes people want more?
I mean SMI diamond grinding wheels is kinda boring.
You might peek at Yahoo’s home page and note how they create news headlines to get viewers to click.
You might add a related video or a picture or two to get readers excited about what you’ve written. In my opinion, it would
make your blog a little livelier.
Stop by my web site expat internetaanbieder Hongarije
Write more, thats all I have to say. Literally, it seems
as though you relied on the video to make your point. You clearly know what youre talking about, why waste your
intelligence on just posting videos to your weblog
when you could be giving us something enlightening to read?
Feel free to surf to my web-site – internet zoals in Nederland in Hongarije
Well spoken certainly. .
Great post. I used to be checking continuously this blog and I’m inspired!
Extremely useful information specially the final
phase 🙂 I take care of such information a lot. I was looking for this certain information for a very
long time. Thanks and good luck.
Also visit my web site internet installatie Hongarije
Hello it’s me, I am also visiting this web site regularly,
this website is actually good and the users are actually sharing pleasant thoughts.
Check out my web page – internet voor emigranten zonder gedoe
I’ve been surfing online more than three hours today, yet I never found any interesting article
like yours. It is pretty worth enough for me. beste provider voor Nederlanders in Hongarije my opinion, if
all website owners and bloggers made good content as you
did, the web will be a lot more useful than ever before.
What’s up everyone, it’s my first pay a quick visit at this web site, and post is genuinely fruitful for
me, keep up posting these articles or reviews.
My web site wifi in Hongarije
Hi there, I found your site via Google while searching for a related topic, your website came up, it looks great.
I have bookmarked it in my google bookmarks.
Hello there, simply changed into alert to your weblog thru Google, and found that it is
really informative. I’m gonna watch out for brussels. I’ll be grateful if
you happen to proceed this in future. A lot of other folks might be
benefited out of your writing. Cheers!
Hi there to every , as I am truly eager of reading this web site’s post
to be updated daily. It includes fastidious material.
Feel free to visit my web site … goedkoop internet Hongarije
Moin,
hat jemand von euch schon mal was von https://pediascape.science/wiki/User:ErnestinaConnal gehört?
Ich hab’s testweise ausprobiert, weil der Bonus ohne Einzahlung ziemlich interessant klang.
Hab erst gedacht, das ist wieder so eine Falle, und wurde positiv überrascht. Gleich nach dem Spinmama Login waren die Freispiele da, komplett ohne Einzahlung.
Die Seite läuft stabil und übersichtlich. Einer der Pluspunkte:
Auch als Stammspieler bekommst du regelmäßig Aktionen. Ist bei vielen Anbietern nicht so.
Keine miesen Tricks wie bei anderen Casinos. Ich bin jedenfalls positiv überrascht.
Spielt noch jemand hier bei Spinmama?.
Everything is very open with a clear explanation of the
issues. It was definitely informative. Your website is extremely
helpful. Thanks for sharing!
Here is my web-site :: Hungary broadband deals
Thanks for every other informative website. Where else could
I am getting that kind of information written in such a perfect means?
I’ve a venture that I’m just now running on, and I have
been on the glance out for such info.
Here is my homepage – monthly internet Hungary
Hi there, just became alert to your blog through Google, and found
that it’s really informative. I’m gonna watch out for
brussels. I will appreciate if you continue this in future.
Numerous people will be benefited from your writing. Cheers!
my web-site; fiber internet Hungary
I have been surfing online greater than three hours lately, yet I by no means discovered any interesting
article like yours. It is beautiful price sufficient for me.
Personally, if all website owners and bloggers made excellent content as you did,
the net will be much more helpful than ever before.
Hi, I do think this is an excellent blog. I stumbledupon it 😉 I may return yet again since i have book marked it.
Money and freedom is the greatest way to change, may you be rich and continue to guide
other people.
Here is my web page; สมัครแทงหวยออนไลน์
Heya i’m for the first time here. I came across this board and I find It truly useful
& it helped me out much. I hope to give something back and help others like you
aided me.
My blog … fast internet in Hungary
What’s up, yeah this post is genuinely good and I have learned lot of things from it regarding blogging.
thanks.
Pretty! This was an extremely wonderful article. Thanks for supplying these details.
You’re so cool! I don’t think I’ve read through anything
like that before. So nice to find someone with some unique
thoughts on this issue. Really.. many thanks for starting this
up. This site is something that is required on the web, someone with a bit of originality!
Good information. Lucky me I found your site by chance (stumbleupon).
I have book-marked it for later!
Feel free to surf to my web page … best internet in Hungary
Its like you read my mind! You appear to know so much
about this, like you wrote the book fast internet in Hungary it or something.
I think that you can do with a few pics to drive the message home
a bit, but other than that, this is excellent blog. A fantastic
read. I’ll definitely be back.
hey there and thank you for your info – I have definitely picked up anything new from right
here. I did however expertise several technical issues using this website,
as I experienced to reload the site a lot of times previous to I could get it to load properly.
I had been wondering if your web host is OK? Not that I’m
complaining, but slow loading instances times will sometimes affect your placement
beste internet in Hongarije google and could damage your high-quality score if advertising and marketing with Adwords.
Anyway I’m adding this RSS to my email and could look out for much more of your respective intriguing content.
Make sure you update this again soon.
I am actually delighted to glance at this webpage posts which carries lots of valuable
data, thanks for providing such data.
Also visit my blog; glasvezel internet Hongarije
I’ve been browsing on-line greater than three hours lately, yet I never discovered any fascinating article like
yours. It’s beautiful value enough for me. In my opinion, if all website
owners and bloggers made excellent content as you did, the net
can be a lot more useful than ever before.
Here is my webpage; internet installatie Hongarije
Hi, yes this piece of writing is truly good and I have learned lot
of things from it regarding blogging. thanks.
Feel free to surf to my web site: internet voor emigranten zonder gedoe
Hey there! I understand this is somewhat off-topic but
I needed to ask. Does building a well-established blog like yours require a lot of work?
I’m completely new to operating a blog but I do
write in my diary on a daily basis. I’d like to start a blog so I can easily share my personal experience and views online.
Please let me know if you have any suggestions or tips Hungary ISP for expats new aspiring bloggers.
Thankyou!
I’m extremely impressed together with your writing
skills as neatly as with the structure for your blog.
Is this a paid topic or did you modify it your self?
Either way stay up the excellent high quality writing, it’s rare to peer a nice blog like this
one these days..
Also visit my web blog – internet in Hongarije
Hi! Quick question that’s entirely off topic.
Do you know how to make your site mobile friendly?
My weblog looks weird when viewing from my iphone.
I’m trying to find a template or plugin that might be able to correct this issue.
If you have any suggestions, please share. With thanks!
my webpage – internet for expats Hungary
When I originally commented I clicked the “Notify me when new comments are added” checkbox and now
each time a comment is added I get three e-mails with the
same comment. Is there any way you can remove me from that service?
Thanks!
Feel free to surf to my site … internet plans in Hungary
Howdy! This is my first visit to your blog! We are a collection of volunteers and starting a
new initiative in a community in the same niche. Your
blog provided us beneficial information to work on. You have done a
extraordinary job!
Definitely believe that which you stated. Your favorite justification seemed to be on the internet the
simplest thing to be aware of. I say to you, I certainly get annoyed while people think about worries that
they plainly do not know about. You managed to hit the
nail upon the top as well as defined out the whole thing without having
side-effects , people can take a signal. Will probably be back to
get more. Thanks
https://youzhieducation.com/
Keep on writing, great job!
Look into my page; high speed internet Hungary
I’m now not certain where you are getting your info, but great topic.
I must spend a while learning much more or
figuring out more. Thanks for wonderful info I was searching for this info for my mission.
My partner and I stumbled over here coming from a different page
and thought I should check things out. I like what I see so i am just following you.
Look forward to looking into your web page for a second
time.
It’s very straightforward to find out any matter on web as compared to textbooks, as I
found this paragraph at this website.
Just want to say your article is as astounding. The clarity in your post is just spectacular and i could assume you’re an expert on this subject.
Well with your permission allow me to grab your RSS feed to keep updated with forthcoming
post. Thanks a million and please keep up the gratifying work.
my page: Hungary internet packages
I love reading through a post that can make men and women think.
Also, thanks for allowing for me to comment!
Feel free to surf to my web site: fast internet in Hungary
Hey! Someone in my Myspace group shared this website with us so I came to check it out.
I’m definitely enjoying the information. I’m book-marking and will be tweeting
this to my followers! Fantastic blog and amazing style and design.
While traditional casinos could take days to handle withdrawals, crypto casino transactions usually finish in a few minutes.
Fala, pessoal! Quero compartilhar uma parada sobre o https://datagems.econtentsys.gr/the-importance-of-building-a-strong-brand-identity/, que tá bombando no mundo dos jogos online. Esse jogo do tigrinho dourado não é só visualmente top, com aquele design que chama sorte, mas também é super fácil de jogar, tanto pra quem tá começando quanto pra quem já manja. Essa questão dos horários que rendem mais prêmios deixa o jogo ainda mais intrigante pra quem joga. Embora não tenha comprovação, a expectativa dos horários pagantes deixa o jogo mais empolgante. O melhor é que o Fortune Tiger é uma plataforma confiável que paga de verdade, o que é fundamental. Se você curte um jogo que mistura emoção, estratégia e mistério, vale muito a pena experimentar o Fortune Tiger. Mas joga na boa, porque o principal é aproveitar o jogo.
Hi, Neat post. There is a problem with your website in web explorer, would check this?
IE still is the market leader and a big element
of other folks will pass over your wonderful writing due to this problem.
Hi there this is somewhat of off topic but I was wanting to know if blogs use WYSIWYG
editors or if you have to manually code with HTML. I’m starting a
blog soon but have no coding know-how so I wanted to get advice
from someone with experience. Any help would be enormously appreciated!
My webpage – dispensary for sale Oregon
Awesome write ups. Kudos.
Nice answer back in return of this issue with real arguments and telling the whole
thing on the topic of that.
Feel free to visit my website :: หนังโป๊
Hi there, I check your blogs daily. Your writing style is witty, keep up the good work!
Here is my web blog หนังโป๊
Hi there, after reading this amazing piece of writing i am also
glad to share my familiarity here with mates.
my web blog – revo999
Hey there would you mind letting me know which webhost you’re
using? I’ve loaded your blog in 3 completely different internet browsers and I must
say this blog loads a lot quicker then most. Can you recommend a good hosting provider at a honest price?
Thanks a lot, I appreciate it!
If you are going for best contents like I do, simply pay a quick visit this web page all the time since
it presents quality contents, thanks
Also visit my page … Paramount Recruitment Melbourne
I’m really impressed together with your writing talents as smartly as
with the layout on your blog. Is this a paid theme or did
you customize it your self? Either way stay up the nice quality writing, it is uncommon to look a
great weblog like this one nowadays..
Feel free to surf to my web site :: Oregon cannabis land
Hi to all, the contents existing at this web page are genuinely remarkable Oregon Cannabis business for sale people experience, well, keep
up the good work fellows.
Wow! In the end I got a website from where I know how to genuinely obtain useful data concerning my study and knowledge.
My web-site หนังโป๊
Hello, I enjoy reading all of your article post.
I like to write a little comment to support you.
Stop by my web blog – Witchcraft books shop
Servus Leute,
hat jemand von euch schon mal was von https://www.jiebbs.net/home.php?mod=space&uid=277250&do=profile&from=space gehört?
Ich hab’s testweise ausprobiert, weil der Bonus ohne Einzahlung ziemlich interessant klang.
War nicht sicher, ob das wirklich seriös ist, aber es war besser als gedacht. Der Bonus war sofort nach Anmeldung aktiv, ganz ohne eigenes Guthaben.
Auch die Spinmama App ist ganz solide. Was mich richtig überrascht hat:
Es gibt nicht nur für neue Spieler was, sondern auch für Bestandskunden regelmäßig Bonus Codes. Das ist selten.
Ziemlich fair auf den ersten Blick. Ich spiele jetzt öfter dort.
Würd mich interessieren, wie ihr das seht.
Pretty! This has been an extremely wonderful post.
Thanks for providing these details.
Look at my web site; how to become a Turkish citizen
For newest news you have to pay a visit web and on internet I found this site as a most excellent web site for latest updates.
Feel free to surf to my blog; Paramount Recruitment Australia
Hmm is anyone else experiencing problems with the pictures on this blog loading?
I’m trying to figure out if its a problem on my end or
if it’s the blog. Any suggestions would be greatly appreciated.
Definitely imagine that which you said. Your favorite reason appeared to be
on the web the easiest factor to keep in mind of.
I say to you, I definitely get irked while people think about worries that they just do not recognise about.
You controlled to hit the nail upon the highest and also outlined out
the whole thing with no need side effect , other folks
can take a signal. Will likely be back to get more.
Thanks
Also visit my blog – mpo808
I like the valuable info you provide in your articles.
I will bookmark your blog and check again here regularly.
I am quite sure I’ll learn many new stuff right here!
Good luck Oregon Cannabis business for sale the next!
Very nice post. I simply stumbled upon your weblog and wanted to say that I have really enjoyed surfing around your weblog
posts. In any case I will be subscribing for your feed and
I am hoping you write again very soon!
my blog … Oregon Cannabis Properties
Hey There. I found your weblog the use of msn. That is an extremely well written article.
I’ll make sure to bookmark it and return to read more of your helpful info.
Thanks for the post. I will certainly return.
My web site: JAV
Excellent blog here! Also your site loads up fast! What web host are you using?
Can I get your affiliate link to your host? I wish my site loaded up as
quickly as yours lol
my homepage: Oregon Cannabis business for sale
My developer is trying to persuade me to move to
.net from PHP. I have always disliked the idea
because of the costs. But he’s tryiong none the less. I’ve been using WordPress on various websites for about a year and am nervous about switching to another
platform. I have heard fantastic things about blogengine.net.
Is there a way I can transfer all my wordpress content
into it? Any kind of help would be greatly appreciated!
My page: Witchcraft starter kit
Very good write-up. I certainly love this site. Thanks!
I visited several sites however the audio quality dispensary for sale Oregon audio songs current at this web site is
in fact fabulous.
Fantastic website you have here but I was curious about if you knew of any message boards that cover the
same topics discussed here? I’d really love to be
a part of community where I can get opinions from other knowledgeable people that share the same interest.
If you have any recommendations, please let me know.
Kudos!
my homepage; olcc processer license for sale
I used to be recommended this blog by means of my cousin. I am not positive whether or not this put
up is written via him as nobody else understand such detailed about my trouble.
You are incredible! Thanks!
Feel free to visit my homepage :: olcc producer license for sale
Hello there, You have done an excellent job. I’ll certainly digg it and personally recommend to my friends. I am sure they will be benefited from this web site.
I’m not sure why but this blog is loading incredibly slow for me.
Is anyone else having this problem or is it a issue on my end?
I’ll check back later and see if the problem still exists.
https://ihrm2016.com/
Hello, after reading this awesome piece of writing i am as well delighted
to share my knowledge here with mates.
We are a group of volunteers and opening a new scheme in our community.
Your web site provided us with valuable info to work on. You have done an impressive job and our entire community will be thankful to you.
Thanks for the auspicious writeup. It in reality was a entertainment account it. Look advanced to far delivered agreeable from you! By the way, how could we keep in touch?
Here is my webpage: https://WWW.Schooluniforms.ae/school-socks.html
Fine way of telling, and fastidious post to obtain facts on the
topic of my presentation subject, which i am going to present in school.
Feel free to surf to my web page :: OnebetAsia Rumus Togel
I have read so many articles or reviews regarding the blogger lovers but this piece of writing is truly a good paragraph, keep it up.
This website truly has all of the information I wanted about this subject and didn’t know
who to ask.
I have to thank you for the efforts you’ve put in penning this blog.
I really hope to see the same high-grade content
by you later on as well. In truth, your creative writing abilities has inspired me to
get my own website now 😉
Post writing is also a fun, if you know afterward you can write otherwise it is difficult to write.
Here is my homepage – goedkoopste internet Hongarije expats
Wonderful, what a blog it is! This webpage gives valuable facts
to us, keep it up.
We stumbled over here from a different website and thought I might as well check things
out. I like what I see so now i am following you.
Look forward to looking at your web page for a second time.
Here is my blog – Hungary internet without paperwork
I do not even understand how I ended up here, but I thought this post
was once good. I don’t recognise who you are but certainly you are going to a famous blogger should you aren’t already.
Cheers!
my page: monthly internet Hungary
I will immediately grab your rss feed as I can not in finding your e-mail subscription hyperlink or e-newsletter service.
Do you have any? Please allow me know in order that I could
subscribe. Thanks.
Stop by my webpage … easy internet setup Hungary
Hello There. I found your blog using msn. This is
an extremely well written article. I will be sure to bookmark it and return to read more of your useful information.
Thanks for the post. I will certainly comeback.
My web site :: best internet in Hungary
Very well voiced certainly! .
You are so interesting! I do not think I’ve read through anything like that before.
So nice to find someone with a few unique thoughts on this subject.
Seriously.. thank you for starting this up.
This web site is one thing that is required
on the web, someone with some originality!
I’m no longer sure the place you are getting your information, but good topic.
I needs to spend a while learning more or understanding more.
Thank you for great info I was in search of this information for my mission.
Have a look at my website; easy internet setup Hungary
It’s really a cool and helpful piece of info.
I’m glad that you simply shared this useful information with us.
Please keep us up to date like this. Thanks for sharing.
my website :: Hungary internet providers
Hi there, You’ve done an excellent job. I’ll certainly digg
it and personally suggest to my friends. I’m
sure they’ll be benefited from this website.
We are a group of volunteers and starting a brand new scheme in our community.
Your website offered us with useful information to work on. You’ve done a
formidable job and our entire neighborhood will likely be thankful to you.
Great article. I am going through many of these issues as well..
https://forhelpyou.com/
MIOTOTO merupakan situs toto togel 4D terbaik dan terpercaya di Indonesia yang dikenal luas di kalangan pecinta togel online.
Dengan menyediakan berbagai pilihan pasaran resmi, prediksi togel yang
akurat dan selalu diperbarui, serta layanan profesional, MIOTOTO menjadi pilihan utama bagi
pemain togel yang ingin bermain secara aman dan nyaman.
Hurrah! After all I got a webpage from where I be able to really take valuable facts regarding my study and knowledge.
my webpage; https://www.uniform-factory.net/medical-lab-coats.html
I was suggested this website by my cousin. I am not sure whether this post is written by him as nobody else know such
detailed about my problem. You are wonderful! Thanks!
Does your blog have a contact page? I’m having problems locating it but, I’d like to send you an e-mail.
I’ve got some suggestions for your blog you might be interested in hearing.
Either way, great website and I look forward to seeing
it improve over time.
Hello, always i used to check website posts here early
in the daylight, since i like to find out more and more.
I’ve been struggling with sugar cravings
and unstable blood sugar for a while, so learning about Gluco6 really caught my attention. Love
that it combines science with natural ingredients — definitely going to
look more into this. Thanks for breaking it down so clearly!
Whoa plenty of valuable info!
Feel free to visit my site: Korean Sports Betting (https://www.thebigme.cc:3000/arnulforedmond)
Thanks. A lot of forum posts!
It’s really a cool and useful piece of information. I’m satisfied that you simply shared this helpful information with us.
Please stay us up to date like this. Thanks for sharing.
I think this is one of the most vital info for me. And
i am glad reading your article. But should remark on few general things, The web site style is ideal, the articles is really great : D.
Good job, cheers
This article will assist the internet people for creating
new blog or even a blog from start to end.
Hey I know this is off topic but I was wondering if you knew of any
widgets I could add to my blog that automatically tweet my
newest twitter updates. I’ve been looking for a plug-in like this for quite some time and was hoping maybe you would have
some experience with something like this.
Please let me know if you run into anything. I truly enjoy reading your
blog and I look forward to your new updates.
Also visit my blog … Training Courseware
It’s the best time to make a few plans for the longer term and it’s time to be happy.
I have read this post and if I may I desire
to suggest you some interesting things or suggestions.
Perhaps you can write subsequent articles regarding
this article. I desire to read even more issues about it!
Visit my page halifax roofing
Remarkable! Its really amazing post, I have got much clear
idea on the topic of from this paragraph.
My website … dune couch
An impressive share! I have just forwarded this onto a coworker who
had been conducting a little homework on this. And he in fact bought me lunch
simply because I found it for him… lol. So
allow me to reword this…. Thanks for the meal!!
But yeah, thanks for spending time to talk about this matter here
on your blog.
my site: free
Way cool! Some very valid points! I appreciate you
writing this article and the rest of the website is really good.
Have a look at my page: business
You need to take part in a contest for one of the best sites on the
web. I most certainly will highly recommend this blog!
Look into my site; metal roofing
I would like to thank you for the efforts you’ve put in penning this site.
I’m hoping to see the same high-grade blog posts by
you in the future as well. In truth, your creative writing
abilities has motivated me to get my own, personal site now 😉
I am really impressed with your writing skills and also with the layout on your blog.
Is this a paid theme or did you customize it yourself?
Either way keep up the excellent quality writing, it’s rare to see a nice blog
like this one today.
Visit my web site … roofing contractors near me
hey there and thank you for your info – I have certainly picked up anything new from right
here. I did however expertise several technical points using
this site, since I experienced to reload the site a lot of
times previous to I could get it to load properly.
I had been wondering if your web host is OK? Not that I’m complaining,
but sluggish loading instances times will sometimes affect your placement in google and could damage your high quality score
if advertising and marketing with Adwords. Well I am adding this RSS to my e-mail
and can look out for a lot more of your respective exciting content.
Ensure that you update this again soon.
Also visit my web-site halifax roofing
We absolutely love your blog and find a lot of your post’s to be what precisely I’m looking for.
Would you offer guest writers to write content for you personally?
I wouldn’t mind creating a post or elaborating on a lot of the subjects you write in relation to here.
Again, awesome web site!
With havin so much content and articles do you ever run into any problems of plagorism or copyright infringement?
My website has a lot of exclusive content I’ve either authored myself or outsourced but it seems a lot of it is popping
it up all over the web without my permission. Do you know any techniques to
help protect against content from being
stolen? I’d really appreciate it.
my web blog … Training Courseware
What’s Taking place i am new to this, I stumbled upon this I
have discovered It absolutely useful and it has helped me out loads.
I hope to give a contribution & assist different users like its helped me.
Good job.
My web page template
That is a good tip particularly to those fresh to the blogosphere.
Short but very accurate information… Appreciate your sharing this one.
A must read article!
What’s up colleagues, fastidious piece of writing and
pleasant arguments commented at this place, I am really enjoying by these.
My page; halifax roofing
I really love your site.. Pleasant colors & theme.
Did you create this web site yourself? Please reply back as I’m hoping to create my own website
and would like to learn where you got this from or just what the theme is named.
Kudos!
IPTV kaufen – Einfach, schnell und zuverlässig zum eigenen Fernseherlebnis
Entdecke die Welt des IPTV und genieße eine große Auswahl an Kanälen, hochwertige Streams und flexible Nutzungsmöglichkeiten.
Mit einem zuverlässigen IPTV Anbieter kannst du bequem von zu Hause
aus live TV, Serien und Filme in bester Qualität streamen. Jetzt unkompliziert dein IPTV-Abonnement sichern und das Fernseherlebnis auf ein neues Level heben!
London Nightlife: A Guide To Thhe Town’s Best Bars And Clubs Sixes Cricket Blog bkog (Freda)
Its not my first time to visit this web page, i am browsing this website dailly and obtain pleasant
data from here daily.
You ought to be a part of a contest for one of the most useful sites on the internet.
I will highly recommend this website!
Do you mind if I quote a few of your articles as long as I provide credit and sources back to
your site? My blog site is in the very same niche as
yours and my users would certainly benefit from a lot of the information you
present here. Please let me know if this ok with you. Cheers!
Great tips With thanks.
Pretty section of content. I just stumbled upon your site and in accession capital to assert that I get in fact enjoyed account your blog posts.
Any way I’ll be subscribing to your augment and even I achievement you access consistently quickly.
Do you have any video of that? I’d love to find out some additional information.
I was suggested this blog by my cousin. I am not sure whether this post is written by him as no one else know such detailed about my problem. You are incredible! Thanks!
How To Get Indexed On The Net Search Fast Without Submitting To Google submit (Enriqueta)
It’s actually a great and helpful piece of info. I am
glad that you just shared this helpful info with
us. Please stay us informed like this. Thanks for sharing.
Wow that was strange. I just wrote an really long
comment but after I clicked submit my comment didn’t appear.
Grrrr… well I’m not writing all that over again. Anyhow, just wanted
to say fantastic blog!
Greetings from Idaho! I’m bored to death at work so
I decided to check out your blog on my iphone during lunch break.
I really like the information you provide here and can’t wait
to take a look when I get home. I’m surprised at how quick your blog loaded on my phone ..
I’m not even using WIFI, just 3G .. Anyhow, amazing
site!
Wow, marvelous blog layout! How long have you been blogging for?
you made blogging look easy. The overall look of your web site is fantastic, let alone the content!
Hi there i am kavin, its my first time to commenting anyplace, when i
read this article i thought i could also make comment due to this brilliant piece of writing.
This was super informative! I’ve been feeling low on energy
lately and looking for something more natural
to help. Red Boost sounds promising, especially with the focus
on circulation and vitality. Appreciate the honest breakdown!
Hey There. I found your blog using msn. This is a really well written article.
I will make sure to bookmark it and come back to read more of your useful
information. Thanks for the post. I’ll definitely return.
Fine knowledge, Thanks!
Quality articles is the main to be a focus for the visitors to pay a visit the web site,that’s what this website is providing.
Hi! I just wanted to ask if you ever have any trouble
with hackers? My last blog (wordpress) was hacked and I ended up losing months of hard work due to no data backup.
Do you have any methods to protect against hackers?
Here is my homepage; vpn
Hello, this weekend is nice for me, since this point in time i
am reading this fantastic informative paragraph here at my home.
My site increase trading consistency
I’m no longer certain the place you are getting your information, but good
topic. I must spend a while learning much more or understanding more.
Thanks for excellent information I was on the lookout for this info for my mission.
It’s the best time to make some plans for the future and it’s time to be happy.
I’ve read this post and if I could I desire to suggest you few
interesting things or suggestions. Maybe you could write next articles
referring to this article. I want to read more things about
it!
Also visit my webpage; Aniwatch
I loved as much as you will receive carried out right here.
The sketch is tasteful, your authored subject matter stylish.
nonetheless, you command get got an nervousness over that you wish
be delivering the following. unwell unquestionably
come more formerly again since exactly the same nearly very often inside case you shield this hike.
Also visit my web site – قیمت هود آشپزخانه
Hello, i read your blog from time to time and i own a similar one
and i was just curious if you get a lot of spam remarks?
If so how do you reduce it, any plugin or anything you can advise?
I get so much lately it’s driving me crazy so any help is very much
appreciated.
Look at my homepage trading indicator
Moin,
hat jemand von euch schon mal was von https://elearnportal.science/wiki/Tauche_Ein_Ins_Spinmama_Casino_:_Profitiere_Vom_Bonus_Ohne_Einzahlung_Schnapp_Dir_Einzigartige_Promo_Codes_Und_Erlebe_Sicheres_Spannendes_Spielen_Online. gehört?
Ich hab’s kürzlich entdeckt, wegen dem angeblichen Startguthaben ohne Einzahlung.
Dachte erst, das ist wieder so ein 0815-Ding, aber das hat sich echt gelohnt. Der Bonus war sofort nach Anmeldung aktiv, ohne Risiko.
Auch die Spinmama App ist ganz solide. Was mich richtig überrascht hat:
Selbst wenn man länger dabei ist, gibt’s immer wieder Codes. Mag ich.
Auch die Umsatzbedingungen sind klar. Ich schau mal, wie sich das entwickelt.
Habt ihr den Bonus auch schon mitgenommen?.
This review gave me hope! I’ve been struggling with stubborn nail fungus for years, and it’s so frustrating when nothing works.
Glad to hear ProNail Complex might actually deliver results without all the hype.
I really like what you guys are usually up too.
This type of clever work and exposure! Keep up the great works guys I’ve incorporated
you guys to my blogroll.
I’ve been browsing on-line more than 3 hours today, but I never found any attention-grabbing article like
yours. It is beautiful worth enough for me. In my opinion, if all webmasters and bloggers made good content
as you probably did, the net will be a lot
more useful than ever before.
I am really loving the theme/design of your site. Do you ever run into any browser compatibility problems?
A small number of my blog readers have complained about
my blog not operating correctly in Explorer but looks great in Chrome.
Do you have any solutions to help fix this issue?
I think the admin of this web site is really working hard for his site, for the reason that here every material is quality based material.
https://texasnativeamericanlawsection.com/
I was suggested this blog by means of my cousin. I am not sure whether or not this
submit is written through him as nobody else recognise such specified about my trouble.
You are incredible! Thanks!
Heya i am for the first time here. I came across this board and I to
find It really helpful & it helped me out much.
I’m hoping to give one thing back and help others like you aided me.
Hey! I’m at work browsing your blog from my new iphone! Just wanted to say
I love reading your blog and look forward to all your posts!
Carry on the fantastic work!
Nice post. I was checking constantly this blog and I am impressed!
Very helpful info specially the remaining section 🙂
I handle such info a lot. I used to be seeking this certain information for a very lengthy time.
Thank you and best of luck.
hello there and thank you for your info – I have definitely picked up something new from right here.
I did however expertise a few technical issues using this website, since I experienced
to reload the site many times previous to I could get
it to load properly. I had been wondering
if your web hosting is OK? Not that I am complaining, but sluggish loading
instances times will very frequently affect your placement in google and can damage your
quality score if advertising and marketing with Adwords.
Well I am adding this RSS to my e-mail and can look out for much more of your respective
fascinating content. Make sure you update this again very soon.
I always spent my half an hour to read this webpage’s articles or reviews everyday
along with a mug of coffee.
Here is my page – headshot photographer in Chicago
Hi my family member! I want to say that this article is awesome, great written and
come with approximately all significant infos. I would like to see extra posts like this .
Because the admin of this site is working, no question very shortly it
will be well-known, due to its feature contents.
Feel free to surf to my blog post … Iraq
Hej! Ktoś już grał na https://localbusinessblogs.co.uk/wiki/index.php?title=User:Tommy62E215349? Wszedłem z nudów i… zostałem, bo naprawdę warto. Proces zakładania konta to kwestia chwili, platforma jest w pełni po polsku, co ułatwia sprawę. Bonus bez wpłaty na dzień dobry – od razu kilka spinów na próbę. Serwis działa elegancko, także na smartfonie – żadnych lagów. Promocje pojawiają się regularnie, a kody bonusowe to miły dodatek. Jak ktoś szuka czegoś nowego, a nie chce od razu inwestować kasy, to według mnie warto dać Spinmama szansę. Graliście już coś ciekawego na Spinmama?
It’s a pity you don’t have a donate button! I’d without a doubt donate to this superb blog!
I guess for now i’ll settle for bookmarking and adding your RSS feed to my
Google account. I look forward to fresh updates and will share
this blog with my Facebook group. Chat soon!
What’s Going down i am new to this, I stumbled upon this I’ve
discovered It positively useful and it has helped me out loads.
I’m hoping to contribute & aid other customers like its aided me.
Great job.
my web page: UhOh7 @Tik ToK Shop
I’m gone to convey my little brother, that he should also go to see this
website on regular basis to get updated from hottest gossip.
Stop by my website: headshot photographer in Chicago
I really like your blog.. very nice colors & theme.
Did you create this website yourself or did you hire someone to
do it for you? Plz answer back as I’m looking
to create my own blog and would like to find out where u got this from.
thanks a lot
my web blog … headshot photographer in Chicago
I every time spent my half an hour to read this website’s posts every day along with a mug of coffee.
https://cirugiadehernias.com/
토닥이를 처음 이용하시는 분들도
걱정하지 않으셔도 됩니다. 아래와 같은 간단한 절차로 쉽게 예약하고 이용할
수 있습니다.
Wonderful blog! I found it while surfing
around on Yahoo News. Do you have any suggestions on how to get
listed in Yahoo News? I’ve been trying for a while but I never seem to get there!
Appreciate it
Canada After Dark: Your Go-to Information Forr Nightlife & Entertainment Article (https://Doodleordie.Com)
Fantastic beat ! I would like to apprentice even as you
amend your web site, how can i subscribe for a weblog site?
The account helped me a acceptable deal. I had been a
little bit familiar of this your broadcast provided brilliant transparent idea
It’s a shame you don’t have a donate button! I’d without a doubt donate to this fantastic blog!
I guess for now i’ll settle for bookmarking and adding
your RSS feed to my Google account. I look forward to brand new
updates and will share this blog with my Facebook group.
Talk soon!
Write more, thats all I have to say. Literally, it seems as though you
relied on the video to make your point. You obviously know what youre talking about, why waste your
intelligence on just posting videos to your weblog when you could be giving us something enlightening to read?
The Ultimate Guide To Nightliffe In Japan: Toop Spots And Ideas link – Graig,
I’ve been exploring for a little for any high quality articles or blog posts
on this sort of area . Exploring in Yahoo I at last
stumbled upon this website. Studying this information So i am happy to convey that I’ve a very good
uncanny feeling I found out just what I needed. I most without a doubt will make sure to do not disregard
this web site and give it a glance regularly.
Wow, marvelous blog layout! How long have you been blogging for?
you make blogging look easy. The overall look of your web site is great, as well as the content!
What’s up, just wanted to mention, I loved thiis blog post.
It was helpful. Keep on posting!
my page: ดอกไม้งานศพ
Currently it sounds like Drupal is the best blogging platform out there right now.
(from what I’ve read) Is that what you’re using on your blog?
Hi there, I enjoy reading through your article.
I wanted to wite a little commment to support you.
Herre is mmy web page; ดอกไม้งานศพ
I’m not sure why but this sife iis loading very slow for me.
Is anyone else having this issue or is it a issue on my end?
I’ll ceck back later annd see if the problem still exists.
my webpage: จัดไม้งานศพ
The site is operated by the same company that owns Betcoin Casino and Betcoin Poker and is one of the most trusted and reliable Bitcoin sportsbooks.
Genuinely when someone doesn’t know then its up
to other users that they will help, so here it occurs.
This design is steller! You most certainly know how to
keep a reader amused. Between your wit and your videos, I was
almost moved to start my own blog (well, almost…HaHa!) Great
job. I really enjoyed what you had to say, and more than that, how you presented
it. Too cool!
I’m not that much of a internet reader to be honest but your sites really nice, keep it up!
I’ll go ahead and bookmark your site to come back later on. Many thanks
A motivating discussion is definitely worth comment.
I do believe that you need to publish more on this topic, it may not be a taboo matter
but usually people do not discuss these subjects. To the next!
Best wishes!!
Review my homepage … Laser & Aesthetic Clinic
I know this if off topic but I’m looking into starting
my own weblog and was curious what all is required to get set up?
I’m assuming having a blog like yours would cost a pretty penny?
I’m not very internet savvy so I’m not 100% certain. Any recommendations
or advice would be greatly appreciated. Thanks
My web-site; Cocktail
You have made some really good points there. I looked
on the net for more info about the issue and found
most individuals will go along with your views on this web
site.
Simply wish to say your article is as amazing.
The clearness in your submit is just great and i can think you
are a professional on this subject. Well along
with your permission allow me to snatch your RSS
feed to stay up to date with approaching post.
Thank you 1,000,000 and please keep up the gratifying
work.
Also visit my web page :: 미국로또 불법
Magnificent beat ! I wish to apprentice
at the same time as you amend your web site, how can i subscribe for a blog web site?
The account aided me a appropriate deal. I had been a little bit familiar of this your broadcast provided bright
transparent idea
My page … 파로코
Good blog you have got here.. It’s difficult
to find high-quality writing like yours nowadays.
I truly appreciate people like you! Take care!!
Feel free to surf to my web page alcohol rehab Chester New Jersey
บทความนี้ให้ข้อมูลมีประโยชน์มากครับ ถ้าใครกำลังมองหาร้านจัดดอกไม้งานศพ ผมแนะนำลองดูร้านที่มีผลงานจริงและรีวิวดี ๆ ครับ
Greetings! Very helpful advice in this particular post! It is the little
changes which will make the most important changes.
Thanks a lot for sharing!
Feel free to surf to my blog post: mesotherapy treatment
Normally I do not read post on blogs, but I would like to say that this write-up very
forced me to try and do so! Your writing taste has been amazed me.
Thanks, quite great article.
Here is my web blog; Homemade cocktails
It’s an remarkable article for all the internet users; they will obtain advantage from it I am sure.
Also visit my site; GOLD TELEGRAM SIGNALS
I was able to find good information from your blog articles.
Have a look at my website … music therapy for addiction treatment
Wow, marvelous blog layout! How long have you ever been running
a blog for? you make running a blog glance easy.
The total look of your site What is music therapy for addiction?
wonderful, as smartly as the content material!
Greetings from Idaho! I’m bored to death at work so I decided to browse your blog on my iphone during lunch break.
I love the info you present here and can’t wait to take
a look when I get home. I’m shocked at how quick your blog
loaded on my mobile .. I’m not even using WIFI, just 3G ..
Anyways, fantastic site!
Check out my webpage :: 미국복권 온라인구매
Howdy! Do you know if they make any plugins to help with Search Engine Optimization? I’m trying to get my blog to rank for some targeted keywords but I’m
not seeing very good gains. If you know of any please share.
Many thanks!
Also visit my web-site: Cocktail
I used to be able to find good information from your blog articles.
Here is my blog post – Cocktails
I seriously love your site.. Very nice colors & theme.
Did you make this website yourself? Please reply back as I’m trying to create my very
own website and want to know where you got this from or just what the
theme is named. Kudos!
Here is my page: 미국복권불법
I am in fact pleased to read this weblog posts
which consists of lots of valuable information, thanks
Training courses for Customer Service providing these
kinds of data.
Unquestionably believe that which you said. Your favourite reason seemed to
be on the internet the easiest thing to bear in mind of.
I say to you, I definitely get irked even as other people consider issues that
they plainly don’t know about. You controlled to hit the nail upon the top and also defined out
the entire thing with no need side effect , other people
could take a signal. Will probably be back to get more.
Thanks
Look at my web-site :: Drug rehab Chester New Jersey
It’s going to be finish of mine day, but before
finish I am reading this enormous piece of writing to increase my
knowledge.
Here is my web page: super clone watches USA
bookmarked!!, I like your website!
my web-site :: How much does Alcohol detox cost?
My brother recommended I might like this blog. He was
totally right. This post truly made my day. You cann’t imagine
simply how much time I had spent for this info! Thanks!
If some one wants expert view on the topic of running a blog after that i propose him/her to visit this blog, Keep up the
pleasant work.
Also visit my web page: 미국복권 온라인구매
Howdy! I could have sworn I’ve been to this blog before
but after reading through some of the post I realized it’s new to me.
Nonetheless, I’m definitely delighted I found it and I’ll be bookmarking and checking back often!
Here is my blog: Cocktail recipe
Amazing! Its actually awesome article, I have got How much does Alcohol detox cost?
clear idea regarding from this paragraph.
Good post! We will be linking to this great article on our site.
Keep up the good writing.
Here is my blog :: addiction treatment Chester NJ
What a stuff of un-ambiguity and preserveness of precious familiarity regarding unpredicted emotions.
Also visit my page :: Homemade cocktails
Woah! I’m really enjoying the template/theme of this website.
It’s simple, yet effective. A lot of times it’s very difficult to get that “perfect balance” between usability and visual appearance.
I must say you’ve done a amazing job with this.
In addition, the blog loads super quick for me on Internet explorer.
Exceptional Blog!
My web page – alcohol rehab Chester New Jersey
Ahaa, its fastidious conversation concerning this article here at
this weblog, I have read all that, so now me also commenting here.
Excellent blog here! Also your site loads up
very fast! What web host are you using? Can I get your affiliate link to your host?
I wish my website loaded up as quickly as yours lol
I loved as much as you’ll receive carried out right here.
The sketch is tasteful, your authored subject matter stylish.
nonetheless, you command get bought an edginess over that you wish be delivering the
following. unwell unquestionably come further formerly again as exactly the
same nearly a lot often inside case you shield this increase.
https://programmerg.com/tren-teknologi-yang-akan-membentuk-industri-software-di-masa-depan/
Hey there would you mind letting me know which webhost you’re utilizing?
I’ve loaded your blog in 3 different browsers and I must say this blog loads a lot quicker then most.
Can you recommend a good web hosting provider at a honest price?
Thanks a lot, I appreciate it!
My partner and I stumbled over here different web page
and thought I might as well check things out.
I like what I see so i am just following you. Look
forward to checking out your web page again.
Heya i’m for the primary time here. I found this
board and I find It truly helpful & it helped me out much.
I hope to provide one thing back and aid others like you helped me.
https://kibuyut.net/
Singapore: Nightlife And Clubs website (glose.com)
Its such as you read my thoughts! You seem to understand so much about this,
such as you wrote the book in it or something. I think that you just could do with a few % to force
the message home a little bit, however instead of that, this
is magnificent blog. A great read. I will definitely be back.
รับซื้อตลับหมึกเก่า ราคาดี รับทั่วประเทศ!
♻️
หากคุณมีตลับหมึกที่ไม่ใช้แล้ว เราพร้อมรับซื้อในราคายุติธรรม
สนใจติดต่อสอบถามได้ตลอดเวลา รวดเร็วทันใจ มั่นใจได้ว่าปลอดภัย
รับซื้อตลับหมึกเก่า
ราคาดี รับทั่วประเทศ!
♻️
หากคุณมีตลับหมึกที่ไม่ใช้แล้ว เราพร้อมซื้อคืนในราคายุติธรรม
สนใจติดต่อสอบถามได้ตลอดเวลา บริการเร็ว มั่นใจได้ว่าปลอดภัย
fantastic publish, very informative. I’m wondering why the
other specialists of this sector don’t notice this.
You should continue your writing. I am confident, you have a huge readers’ base already!
I’m gone to convey my little brother, that he
should also pay a quick visit this blog on regular basis to take updated from most recent
news update.
Hmm is anyone else having problems with the pictures on this blog loading?
I’m trying to figure out if its a problem on my end or if it’s the blog.
Any feed-back would be greatly appreciated.
Greetings! I know this is kinda off topic but I was wondering if you knew where I could locate a
captcha plugin for my comment form? I’m using the same blog platform as yours and
I’m having problems finding one? Thanks a lot!
Good day I am so happy I found your weblog, I really found you by error, while I was searching on Bing for something else, Regardless I am here now and would
just like to say cheers for a tremendous post and a all round thrilling blog (I also love the
theme/design), I don’t have time to go through it all at the minute but I have saved it and also added your RSS feeds, so when I
have time I will be back to read a great deal more, Please
do keep up the fantastic jo.
This is my first time pay a quick visit at here and i
am actually impressed to read all at alone place.
ซื้อตลับหมึกมือสอง ราคาดี รับทั่วประเทศ!
♻️
หากคุณมีตลับหมึกที่ไม่ใช้แล้ว เราพร้อมรับซื้อในราคายุติธรรม
สนใจติดต่อสอบถามได้ตลอดเวลา บริการเร็ว มั่นใจได้ว่าปลอดภัย
Feel free to surf to my blog :: รับซื้อตลับหมึกเก่า
Hey
Just wanted to say how nice your website is!
I also have a website about 놀쟈초대장
come visit and give me some comments!
Thank!
Great article.
Thank you for the good writeup. It in truth was once a enjoyment account it. Look advanced to more added agreeable from you! By the way, how could we be in contact?
Look into my web blog: https://www.schooluniforms.ae/school-hoodies.html
Hey! Do you know if they make any plugins to protect against hackers?
I’m kinda paranoid about losing everything I’ve worked hard
on. Any recommendations?
รับซื้อตลับหมึกเก่า ราคาดี รับทั่วประเทศ!
♻️
หากคุณมีตลับหมึกที่ไม่ใช้แล้ว เราพร้อมซื้อคืนในราคายุติธรรม
สนใจติดต่อสอบถามได้ตลอดเวลา
บริการเร็ว มั่นใจได้ว่าปลอดภัย
First of all I want to say awesome blog! I had a quick question that I’d like to ask if you don’t
mind. I was interested to find out how you center yourself and
clear your mind prior to writing. I have had a difficult time clearing my mind in getting my ideas out.
I truly do enjoy writing but it just seems like the first 10 to 15 minutes tend to be wasted simply just trying to figure out how to begin. Any recommendations or tips?
Many thanks!
Hey I know this is off topic but I was wondering if you knew of any widgets I could add to my blog that automatically tweet my newest twitter updates.
I’ve been looking for a plug-in like this for quite some time and was hoping
maybe you would have some experience with something
like this. Please let me know if you run into
anything. I truly enjoy reading your blog and I look forward to your new updates.
It’s remarkable to pay a quick Visit now this website and reading the views of
all colleagues about this piece of writing, while I am also eager of getting know-how.
Hi there would you mind stating which blog platform you’re using?
I’m going to start my own blog in the near future but I’m having a difficult time choosing between BlogEngine/Wordpress/B2evolution and Drupal.
The reason I ask is because your layout seems different then most blogs and
I’m looking for something unique. P.S Apologies for getting off-topic but I had
to ask!
Also visit my homepage: Melbourne Training
My partner and I stumbled over here from a different web
page and thought I may as well check things out.
I like what I see so i am just following you. Look forward to going over your web
page again.
Feel free to visit my website: Our products
What a stuff of un-ambiguity and preserveness of precious familiarity on the topic of unpredicted emotions.
My homepage :: Download now
Asking questions are genuinely good thing if you are not understanding something entirely,
however this article provides pleasant understanding
yet.
รับซื้อตลับหมึกใช้แล้ว ราคาดี รับทั่วประเทศ!
♻️
หากคุณมีตลับหมึกที่ไม่ใช้แล้ว เราพร้อมซื้อคืนในราคายุติธรรม
สนใจติดต่อสอบถามได้ตลอดเวลา บริการเร็ว
มั่นใจได้ว่าปลอดภัย
Look into my web blog – รับซื้อตลับหมึกเก่า
No matter if some one searches for his necessary thing, so he/she needs to be available that in detail, thus that thing is maintained over here.
Have a look at my web-site; Service overview
Hi there terrific blog! Does running a blog similar to this take a large amount of work?
I’ve absolutely no knowledge of programming however I was hoping
to start my own blog soon. Anyway, should you have any suggestions or tips
for new blog owners please share. I understand this is off topic however I simply needed to ask.
Thanks a lot!
Check out my homepage – Brisbane Training
With a massive welcome bonus worth up to 10 Ethereum, and a variety of other valuable promotions, TG Casino makes for one of the best options of all no ID verification casinos out there.
ซื้อตลับหมึกมือสอง ราคาดี รับทั่วประเทศ!
♻️
หากคุณมีตลับหมึกที่ไม่ใช้แล้ว
เราพร้อมซื้อคืนในราคายุติธรรม
สนใจติดต่อสอบถามได้ตลอดเวลา บริการเร็ว มั่นใจได้ว่าปลอดภัย
Review my page … รับซื้อตลับหมึกเก่า
รับซื้อตลับหมึกเก่า ราคาดี รับทั่วประเทศ!
♻️
หากคุณมีตลับหมึกที่ไม่ใช้แล้ว เราพร้อมซื้อคืนในราคายุติธรรม
สนใจติดต่อสอบถามได้ตลอดเวลา บริการเร็ว มั่นใจได้ว่าปลอดภัย
ซื้อตลับหมึกมือสอง ราคาดี รับทั่วประเทศ!
♻️
หากคุณมีตลับหมึกที่ไม่ใช้แล้ว เราพร้อมซื้อคืนในราคายุติธรรม
สนใจติดต่อสอบถามได้ตลอดเวลา บริการเร็ว มั่นใจได้ว่าปลอดภัย
my web blog – รับซื้อตลับหมึกเก่า
รับซื้อตลับหมึกใช้แล้ว ราคาดี รับทั่วประเทศ!
♻️
หากคุณมีตลับหมึกที่ไม่ใช้แล้ว เราพร้อมรับซื้อในราคายุติธรรม
สนใจติดต่อสอบถามได้ตลอดเวลา รวดเร็วทันใจ มั่นใจได้ว่าปลอดภัย
Have a look at my webpage :: รับซื้อตลับหมึกเก่า
Hello
Stoped by to say how nice your blog is!
I have a blog about 놀쟈
feel free to visit and give me some likes
Thank you!
You need to be a part of a contest for one of the most useful blogs online.
I’m going to highly recommend this site!
Superb post but I was wanting to know if you could write a litte more on this topic?
I’d be very thankful if you could elaborate a little bit further.
Thanks!
سامانه استعلام جو یک پلتفرم یکپارچه
برای انواع خدمات استعلامی ضروری از جمله {خلافی خودرو، سوابق بیمه، خدمات بانکی،
وضعیت گذرنامه و پلاک} میباشد.
Howdy! I understand this is sort of off-topic however I needed to ask.
Does operating a well-established website such as yours take a massive amount work?
I’m brand new to running a blog however I do write in my journal every
day. I’d like to start a blog so I can easily share my own experience and
feelings online. Please let me know if you have any kind of ideas or tips for brand new aspiring bloggers.
Thankyou!
It is in point of fact a great and helpful piece of info.
I’m happy that you just shared this useful information with us.
Please keep us up to date like this. Thanks for sharing.
At this time I am going away to do my breakfast, later than having my breakfast coming again to read
other news.
https://bswproject.com/
When I originally left a comment I seem to have clicked on the -Notify me when new
comments are added- checkbox and from now on every time a comment is added I
recieve four emails with the exact same comment.
Is there an easy method you can remove me from that service?
Thanks!
Helpful information. Fortunate me I found your web site by chance, and I’m shocked why this twist of
fate did not came about in advance! I bookmarked it.
https://brookehofsess.com/
An intriguing discussion is definitely worth comment. I think that you ought to write more about this subject, it may not be a taboo matter but generally people don’t discuss these subjects.
To the next! Best wishes!!
https://forexcalendar.my.id/
What’s up to all, the contents present at this website are genuinely awesome for people knowledge, well, keep up the nice work fellows.
รับซื้อตลับหมึกเก่า ราคาดี รับทั่วประเทศ!
♻️
หากคุณมีตลับหมึกที่ไม่ใช้แล้ว เราพร้อมรับซื้อในราคายุติธรรม
สนใจติดต่อสอบถามได้ตลอดเวลา รวดเร็วทันใจ มั่นใจได้ว่าปลอดภัย
Hello
Stoped by to say how fantastic your blog is!
I myself have an post about 한국야동
feel free to visit and give me some feedback
Thank!
With thanks! Excellent stuff!
my blog; https://git.hichinatravel.com/king1894734227
Wow, this Secret Scope Camera looks like a game-changer for home security!
Love how compact it is, yet it still offers 360° coverage and
HD clarity. The smart alerts feature is such a smart
touch—peace of mind without the constant
monitoring. Definitely adding this to my safety setup!
First of all I would like to say excellent blog!
I had a quick question which I’d like to ask if you don’t mind.
I was interested to find out how you center yourself and clear your thoughts prior to writing.
I have had a tough time clearing my mind in getting my thoughts out there.
I truly do take pleasure in writing but it just seems like the first 10 to 15 minutes are
usually wasted just trying to figure out how to begin. Any recommendations or tips?
Thanks!
I’m not sure where you are getting your info, but good topic.
I needs to spend some time learning much more or understanding
more. Thanks for wonderful information I was looking for this information for my
mission.
https://mollyjuneroquet.com/
This design is spectacular! You definitely know how to
keep a reader amused. Between your wit and your videos, I was almost moved to start my own blog (well, almost…HaHa!) Excellent job.
I really enjoyed what you had to say, and more than that, how you presented it.
Too cool!
https://heyimalivemag.com/
I would like to thank you for the efforts you have put in writing this blog.
I’m hoping to check out the same high-grade blog posts from you later
on as well. In truth, your creative writing abilities has encouraged me to get
my very own site now 😉
Have you ever thought about including a little bit
more than just your articles? I mean, what you say is important
and everything. But imagine if you added some great photos or videos to give your posts more, “pop”!
Your content is excellent but with pics and clips, this blog could certainly be one
of the best in its niche. Very good blog!
I am actually glad to read this blog posts which consists of tons of valuable
information, thanks for providing these kinds of information.
Please let me know if you’re looking for a article author for your site.
You have some really good articles and I believe I would be a good asset.
If you ever want to take some of the load off, I’d love to
write some content for your blog in exchange for a link back to mine.
Please blast me an e-mail if interested. Many thanks!
Also visit my homepage; best real estate agent in Grass Valley CA
What i do not realize is in fact how you’re no longer actually much more smartly-liked than you may be now.
You are so intelligent. You already know therefore considerably when it comes to this subject, produced me in my opinion imagine
it from a lot of numerous angles. Its like men and women aren’t fascinated until it’s something to accomplish with Lady gaga!
Your individual stuffs nice. Always deal with it up!
16 Greatest Evening Time Actions In Singapore 2024 website [Clayton]
If you desire to get a good deal from this article then you
have to apply such methods to your won weblog.
my webpage … best realtor in Fort Lauderdale FL
Good respond in return of this difficulty with firm arguments and telling the whole thing on the
topic of that.
my web-site … realtor in Carbondale CO
It’s hard to come by experienced people on this subject, however, you seem like you
know what you’re talking about! Thanks
Feel free to visit my web blog: realtor in Galion OH
I know this if off topic but I’m looking into starting my own weblog and
was wondering what all is needed to get set up? I’m assuming
having a blog like yours would cost a pretty penny?
I’m not very web smart so I’m not 100% sure. Any suggestions or advice
would be greatly appreciated. Kudos
Stop by my blog: real estate agent Fort Lauderdale FL
My partner and I stumbled over here different page and thought I
might check things out. I like what I see so now i am following
you. Look forward to finding out about your web page again.
my web page :: real estate agent Bartlett TN
Great post. I was checking continuously this blog and I am impressed!
Extremely helpful information specially the last part :
) I care for such info much. I was looking for this particular info for a long time.
Thank you and best of luck.
My page – best realtor in Galion OH
Amazing! This blog looks exactly like my old one! It’s on a totally different topic but it has pretty much the
same page layout and design. Great choice of colors!
my blog post; realtor in Dallas TX
Heya are using WordPress for your blog platform?
I’m new to the blog world but I’m trying to get started and create my own. Do you require
any coding knowledge to make your own blog? Any help would be greatly appreciated!
Also visit my web blog best real estate agent in Galion OH
Normally I don’t learn post on blogs, however I wish to
say that this write-up very forced me to take a look
at and do it! Your writing style has been surprised me.
Thank you, very great post.
Feel free to surf to my homepage – real estate agent Fairfax VA
Hello everyone, it’s my first pay a quick visit at this site, and article is
really fruitful in support of me, keep up posting such posts.
Visit my web page – best real estate agent in Inwood WV
You could definitely see your skills in the article you write.
The arena hopes for more passionate writers like you who aren’t afraid
to say how they believe. At all times go after your heart.
Also visit my web page: best real estate agent in Sarasota FL
What’s up, just wanted to say, I liked this article.
It was inspiring. Keep on posting!
My blog – real estate agent Fairfax VA
I get pleasure from, cause I discovered just what I used to be taking a look for.
You have ended my four day lengthy hunt! God Bless you man. Have a nice day.
Bye
Also visit my website – real estate agent Bartlett TN
I’m not sure where you’re getting your info, however good topic.
I needs to spend some time finding out more or figuring out more.
Thanks for wonderful information I was looking
for this info for my mission.
my site – best realtor in Fairfax VA
Ahaa, its good discussion about this post at this place at
this weblog, I have read all that, so at this time me also commenting here.
Look into my web site … realtor in Sarasota FL
Hi there! I’m at work surfing around your blog from my new iphone 4!
Just wanted to say I love reading your blog and look forward to all your posts!
Keep up the fantastic work!
Feel free to visit my web site :: real estate agent Bartlett TN
It is perfect time to make a few plans for the long run and it is time to be happy.
I’ve learn this publish and if I could I desire to suggest you few interesting issues or tips.
Maybe you can write next articles regarding this article. I wish to learn more issues approximately it!
my web site: best realtor in Carbondale CO
Wonderful work! This is the type of information that
are supposed to be shared around the net. Disgrace on Google for not positioning this put up upper!
Come on over and consult with my web site . Thank you =)
I blog often and I truly appreciate your content. The article has really peaked my interest.
I will book mark your blog and keep checking for new details about once a week.
I opted in for your RSS feed as well.
my web blog: realtor in Fort Lauderdale FL
These are in fact enormous ideas in about blogging.
You have touched some nice things here. Any way keep
up wrinting.
Feel free to surf to my page best realtor in Carbondale CO
This is nicely said. !
Also visit my webpage … https://www.youtube7.com/
Great weblog here! Additionally your web site loads up fast!
What web host are you using? Can I am getting your affiliate hyperlink in your
host? I want my site loaded up as fast as yours lol
Feel free to visit my web page :: best real estate agent in Grass Valley CA
I could not refrain from commenting. Well written!
Also visit my web blog: best realtor in Sarasota FL
I am extremely inspired along with your writing skills and also with the format
in your blog. Is this a paid theme or did you modify it your self?
Anyway stay up the excellent quality writing, it is rare to look a nice blog like
this one these days..
Also visit my website :: best realtor in San Jose CA
I savour, result in I found exactly what I was looking for.
You have ended my 4 day long hunt! God Bless you man. Have
a nice day. Bye
My web page … best real estate agent in Galion OH
What i do not understood is in reality how you are now
not actually much more neatly-appreciated than you might
be right now. You’re very intelligent. You know therefore considerably on the subject
of this matter, produced me in my view consider it from a lot of varied angles.
Its like women and men don’t seem to be involved except it’s one thing to accomplish with
Woman gaga! Your individual stuffs great. At all
times take care of it up!
My blog … real estate agent Cape Cod MA
Hi there! Do you know if they make any plugins to assist with Search Engine Optimization?
I’m trying to get my blog to rank for some targeted keywords but I’m
not seeing very good success. If you know of any please share.
Thanks!
Here is my page :: best real estate agent in Thornton CO
Why users still make use of to read news papers when in this technological
globe the whole thing is existing on web?
Feel free to visit my web site – realtor in San Jose CA
Thank you for some other informative blog. Where else may I am getting
that kind of info written in such a perfect method?
I have a challenge that I’m simply now running on, and I’ve
been at the look out for such info.
My website real estate agent Heber Springs AR
I really like what you guys are up too. Such clever work and exposure!
Keep up the terrific works guys I’ve incorporated you
guys to my blogroll.
You’re so awesome! I do not think I have read a single thing like that before.
So good to find another person with some original thoughts on this subject
matter. Seriously.. thanks for starting this
up. This web site is something that’s needed on the internet, someone with some originality!
I’ve been surfing online more than three hours today, yet I never found any interesting article like yours.
It is pretty worth enough for me. In my opinion, if all
webmasters and bloggers made good content as you
did, the net will be much more useful than ever before.
Also visit my homepage – best real estate agent in Thornton CO
of course like your web-site but you have to check the spelling on several of your posts.
Many of them are rife with spelling problems and I to
find it very troublesome to tell the reality on the other hand I will definitely come back again.
Have a look at my page: best real estate agent in Thornton CO
Wow, that’s what I was exploring for, what a stuff!
existing here at this blog, thanks admin of this site.
Also visit my web site – best real estate agent in Carbondale CO
Современные стиральные
машины – это надежные и удобные
устройства, которые значительно облегчают повседневные заботы хозяйки.
Однако, как и любая другая техника, стиральные машины
подвержены износу и могут выходить из строя.
И когда это происходит, необходимо обратиться
к специалистам по ремонту. Ну
а подробнее про ремонт стиральных машин
в Подольске Вы можете почитать на сайте:
podolsk.ctc-service.ru
Heya! I just wanted to ask if you ever have any problems with hackers?
My last blog (wordpress) was hacked and I ended up losing several
weeks of hard work due to no back up. Do you have any solutions
to protect against hackers?
Take a look at my webpage – best realtor in Thornton CO
Write more, thats all I have to say. Literally, it seems as though you relied on the video to make your point. You obviously know what youre talking about, why waste your intelligence on just posting videos to your weblog when you could be giving us something enlightening to read?
Here is my blog post; https://Dubaiuniform.ae/towels-supplier.html
continuously i used to read smaller content that as
well clear their motive, and that is also happening with this
post which I am reading at this place.
my page best real estate agent in Inwood WV
I think the admin of this site is really working hard in favor of his web site, as here every data is quality based data.
https://klikhammerofthor.com/
You really make it seem so easy with your presentation but I find this
topic to be actually something that I think I would never
understand. It seems too complicated and extremely broad for
me. I’m looking forward for your next post, I’ll try to get the
hang of it!
Feel free to visit my web page … best real estate agent in Fairfax VA
Hey would you mind sharing which blog platform you’re
using? I’m planning to start my own blog in the near future but I’m having a
difficult time making a decision between BlogEngine/Wordpress/B2evolution and
Drupal. The reason I ask is because your design seems different then most blogs
and I’m looking for something completely unique.
P.S Sorry for being off-topic but I had to ask!
my site: realtor in Dallas TX
Hello, i think that i saw you visited my web site so i came to “return the favor”.I am trying to find things to improve my site!I suppose
its ok to use some of your ideas!!
Incredible tons of terrific tips.
I have to thank you for the efforts you’ve put in writing this
blog. I really hope to see the same high-grade blog posts by you in the future as well.
In truth, your creative writing abilities has motivated me to get my own blog now ;
)
Here is my homepage :: best realtor in Sarasota FL
Appreciation to my father who informed me on the topic of this webpage, this web site is in fact amazing.
Visit my site realtor in Inwood WV
I think the admin of this site is genuinely working hard in support of his site, because here every information is quality based material.
Here is my site … best real estate agent in Fairfax VA
Cheers. A lot of content.
Also visit my web page – Online Gambling Sites (http://baoxianzhanggui.com:8090/joseharlan2046)
Wow, incredible weblog format! How lengthy have you been blogging for?
you make running a blog glance easy. The total look
of your web site is wonderful, let alone the content!
Feel free to visit my webpage: best realtor in Grass Valley CA
Hey there! I just wish to give you a big thumbs up for your great info you have
got right here on this post. I will be returning
to your website for more soon.
Here is my web site; best real estate agent in Sarasota FL
It’s very straightforward to find out any matter on net as compared
to textbooks, as I found this article at this website.
Also visit my webpage: real estate agent Cape Cod MA
Hi there it’s me, I am also visiting this web page daily, this web site is genuinely nice and the
visitors are truly sharing nice thoughts.
Here is my blog post … best real estate agent in Heber Springs AR
ซื้อตลับหมึกมือสอง ราคาดี รับทั่วประเทศ!
♻️
หากคุณมีตลับหมึกที่ไม่ใช้แล้ว เราพร้อมรับซื้อในราคายุติธรรม
สนใจติดต่อสอบถามได้ตลอดเวลา
บริการเร็ว มั่นใจได้ว่าปลอดภัย
Here is my web-site :: รับซื้อตลับหมึกเก่า
รับซื้อตลับหมึกเก่า ราคาดี รับทั่วประเทศ!
♻️
หากคุณมีตลับหมึกที่ไม่ใช้แล้ว เราพร้อมซื้อคืนในราคายุติธรรม
สนใจติดต่อสอบถามได้ตลอดเวลา รวดเร็วทันใจ มั่นใจได้ว่าปลอดภัย
ซื้อตลับหมึกมือสอง ราคาดี รับทั่วประเทศ!
♻️
หากคุณมีตลับหมึกที่ไม่ใช้แล้ว เราพร้อมรับซื้อในราคายุติธรรม
สนใจติดต่อสอบถามได้ตลอดเวลา บริการเร็ว
มั่นใจได้ว่าปลอดภัย
Feel free to visit my site … รับซื้อตลับหมึกเก่า
Excellent blog you’ve got here.. It’s difficult to find high-quality
writing like yours nowadays. I really appreciate people like you!
Take care!!
Excellent article. Keep writing such kind of information on your blog.
Im really impressed by it.
Hello there, You’ve done a fantastic job. I will certainly digg it and individually recommend to my friends.
I am sure they’ll be benefited from this website.
Also visit my site; best real estate agent in San Jose CA
Nice post. I learn something new and challenging on sites I
stumbleupon every day. It’s always useful to read content from other authors and practice something from their web sites.
Here is my website best realtor in Galion OH
What’s up colleagues, pleasant paragraph and fastidious arguments commented at this place, I am in fact
enjoying by these.
Review my website; best real estate agent in Thornton CO
It’s hard to find well-informed people about this
subject, however, you seem like you know what you’re talking about!
Thanks
Feel free to visit my page – real estate agent Grass Valley CA
Wow, amazing blog layout! How long have you been blogging for?
you make blogging look easy. The overall look of your web site is fantastic, let alone
the content!
Also visit my site: best realtor in Fort Lauderdale FL
Thanks for finally writing about > SMI diamond grinding wheels best
realtor in Inwood WV
Thanks for any other informative site. Where else could
I am getting that type of information written in such an ideal method?
I’ve a mission that I am just now operating on, and I’ve been on the look
out for such information.
Just desire to say your article is as surprising.
The clearness in your post is simply spectacular and i
can think you are knowledgeable on this subject. Fine with your permission let me to grab your feed to stay updated with impending post.
Thank you a million and please carry on the rewarding work.
my blog – real estate agent Grass Valley CA
Touche. Solid arguments. Keep up the great work.
Look into my web blog best real estate agent in Bartlett TN
Thank you for the good writeup. It if truth be told was
a enjoyment account it. Look advanced to far introduced agreeable from you!
However, how can we communicate?
รับซื้อตลับหมึกเก่า ราคาดี รับทั่วประเทศ!
♻️
หากคุณมีตลับหมึกที่ไม่ใช้แล้ว เราพร้อมซื้อคืนในราคายุติธรรม
สนใจติดต่อสอบถามได้ตลอดเวลา
รวดเร็วทันใจ มั่นใจได้ว่าปลอดภัย
I am regular reader, how are you everybody? This piece of writing
posted at this web page is in fact fastidious.
Here is my site; best real estate agent in Heber Springs AR
รับซื้อตลับหมึกเก่า ราคาดี
รับทั่วประเทศ! ♻️
หากคุณมีตลับหมึกที่ไม่ใช้แล้ว เราพร้อมรับซื้อในราคายุติธรรม
สนใจติดต่อสอบถามได้ตลอดเวลา
บริการเร็ว มั่นใจได้ว่าปลอดภัย
Seu site tem uma página de contato? Estou com problemas
para localizá-lo, mas gostaria de enviar um e-mail para você.
Tenho algumas ideias criativas para seu blog que você
pode estar interessado em ouvir. De qualquer forma, ótimo site e estou
ansioso para vê-lo desenvolver com o tempo.
Selir 77 login I’m really impressed together with your writing abilities and also with the structure for your weblog. Is that this a paid subject or did you customize it your self? Either way stay up the nice quality writing, it’s uncommon to look a nice blog like this one these days.
Hurrah! In the end I got a weblog from where I can truly take useful facts concerning my study and knowledge.
My web-site: real estate agent Carbondale CO
รับซื้อตลับหมึกใช้แล้ว ราคาดี รับทั่วประเทศ!
♻️
หากคุณมีตลับหมึกที่ไม่ใช้แล้ว เราพร้อมซื้อคืนในราคายุติธรรม
สนใจติดต่อสอบถามได้ตลอดเวลา บริการเร็ว มั่นใจได้ว่าปลอดภัย
Here is my web page; รับซื้อตลับหมึกเก่า
I am really loving the theme/design of your blog.
Do you ever run into any internet browser compatibility problems?
A small number of my blog visitors have complained about my site not working correctly in Explorer but looks great in Safari.
Do you have any tips to help fix this problem?
Also visit my blog post realtor in Bartlett TN
Hello there! I could have sworn I’ve been to your blog before but
after looking at some of the posts I realized it’s new to me.
Regardless, I’m certainly happy I found it and I’ll be book-marking it and checking back often!
My programmer is trying to convince me to move to .net
from PHP. I have always disliked the idea because
of the expenses. But he’s tryiong none the less.
I’ve been using Movable-type on a number of websites for
about a year and am concerned about switching to another platform.
I have heard excellent things about blogengine.net. Is there a way
I can transfer all my wordpress posts into it? Any
help would be really appreciated!
Selir77 Login Awsome info and straight to the point. I am not sure if this is in fact the best place to ask but do you guys have any ideea where to employ some professional writers? Thx 🙂
What’s up, I read your blogs regularly. Your writing style
is awesome, keep up the good work!
Look into my website best realtor in Heber Springs AR
รับซื้อตลับหมึกใช้แล้ว ราคาดี
รับทั่วประเทศ! ♻️
หากคุณมีตลับหมึกที่ไม่ใช้แล้ว เราพร้อมซื้อคืนในราคายุติธรรม
สนใจติดต่อสอบถามได้ตลอดเวลา บริการเร็ว มั่นใจได้ว่าปลอดภัย
my web site; รับซื้อตลับหมึกเก่า
Great post. I will be facing some of these issues as well..
my blog real estate agent Cape Cod MA
ซื้อตลับหมึกมือสอง ราคาดี รับทั่วประเทศ!
♻️
หากคุณมีตลับหมึกที่ไม่ใช้แล้ว เราพร้อมซื้อคืนในราคายุติธรรม
สนใจติดต่อสอบถามได้ตลอดเวลา รวดเร็วทันใจ มั่นใจได้ว่าปลอดภัย
my page; รับซื้อตลับหมึกเก่า
รับซื้อตลับหมึกเก่า ราคาดี รับทั่วประเทศ!
♻️
หากคุณมีตลับหมึกที่ไม่ใช้แล้ว เราพร้อมรับซื้อในราคายุติธรรม
สนใจติดต่อสอบถามได้ตลอดเวลา รวดเร็วทันใจ มั่นใจได้ว่าปลอดภัย
Hi there colleagues, its impressive piece of writing regarding educationand fully
explained, keep it up all the time.
Way cool! Some extremely valid points! I appreciate you
writing this post plus the rest of the website is extremely good.
Feel free to surf to my web-site … real estate agent Cape Cod MA
Really interesting review! I’ve been looking for something natural to support my hearing, especially with all the
ringing and occasional fogginess. Audifort sounds like it covers
both ear health and mental clarity—definitely worth checking out.
I really like your blog.. very nice colors Smart Tech & Sustainability theme.
Did you design this website yourself or did you hire someone to
do it for you? Plz respond as I’m looking to construct my own blog and would like to
know where u got this from. appreciate it
Hello! I understand this is somewhat off-topic but
I had to ask. Does managing a well-established website such as yours require a
lot of work? I am completely new to operating a blog however I do write in my journal on a daily basis.
I’d like to start a blog so I can share my experience and thoughts online.
Please let me know if you have any kind of recommendations or
tips for new aspiring bloggers. Thankyou!
Take a look at my web-site: best real estate agent in Carbondale CO
Hi, I do believe this is an excellent website. I stumbledupon it 😉
I am going to come back yet again since I bookmarked
it. Money and freedom is the greatest way to change,
may you be rich and continue to guide others.
Also visit my web blog: Biotech & Health Tech
An outstanding share! I have just forwarded this onto a coworker who was doing a little research on this.
And he in fact ordered me dinner simply because I discovered it
for him… lol. So allow me to reword this…. Thanks for
the meal!! But yeah, thanks for spending the time to discuss this issue here on your web page.
My webpage best real estate agent in Grass Valley CA
If you desire to get a great deal from this paragraph then you have
to apply such strategies to your won weblog.
Usually I do not learn article on blogs, however I wish to say
that this write-up very forced me to check out and do it! Your writing style has been surprised me.
Thanks, quite great article.
Woah! I’m really enjoying the template/theme of this
site. It’s simple, yet effective. A lot of times it’s tough to get that “perfect balance” between usability and appearance.
I must say you’ve done a amazing job with this. Additionally, the
blog loads extremely quick for me on Opera.
Excellent Blog!
Feel free to surf to my web page – Smart Tech & Sustainability
Does your website have a contact page? I’m having trouble locating
it but, I’d like to send you an e-mail. I’ve got some recommendations
for your blog you might be interested in hearing.
Either way, great site and I look forward to seeing
it improve over time.
My site realtor in Fort Lauderdale FL
hey there and thank you for your information – I have certainly picked up anything new from right here.
I did however expertise a few technical points using this web
site, as I experienced to reload the web site a lot of times previous to I could get it to load properly.
I had been wondering if your hosting is OK? Not that I am complaining, but sluggish loading
instances times will sometimes affect your placement in google and could damage
your high quality score if ads and marketing with Adwords.
Well I’m adding this RSS to my email and could look out for
a lot more of your respective exciting content. Make sure you update this again very soon.
Look at my site – best real estate agent in Bartlett TN
I got this web page from my buddy who told me regarding this site and at the moment this time
I am visiting this web site and reading very informative
posts here.
Stop by my web blog best real estate agent in Cape Cod MA
If you are going for best contents like I do, only go to see
this web site every day because it presents feature contents,
thanks
Also visit my web-site :: best real estate agent in Dallas TX
I know this if off topic but I’m looking into starting my own weblog and was curious what all is required to get set up?
I’m assuming having a blog like yours would cost a pretty penny?
I’m not very web smart so I’m not 100% positive. Any suggestions or advice would be
greatly appreciated. Thanks
Also visit my web page … African hunting
It’s an remarkable article for all the online viewers; they will take
advantage from it I am sure.
Wow, amazing blog layout! How long have you been blogging for?
you made blogging look easy. The overall look of your website is
fantastic, let alone the content!
My family all the time say that I am killing my time here at net, but I know I am getting know-how daily by reading thes good articles.
My web-site … eames lounge chair replica
Definitely believe that which you stated. Your favorite reason appeared
to be on the web the easiest thing to be aware of.
I say to you, I certainly get irked while people consider
worries that they just don’t know about. You managed to hit the nail upon the top and defined out the whole thing without
having side-effects , people can take a signal. Will probably be back to get more.
Thanks
Take a look at my website – real estate agent Dallas TX
Simply want to say your article is as surprising.
The clarity in your post is just great and i can assume you are an expert on this subject.
Fine with your permission let me to grab
your RSS feed to keep up to date with forthcoming post.
Thanks a million and please carry on the enjoyable work.
Wow, wonderful weblog format! How lengthy have you ever been running a blog for?
you make blogging glance easy. The overall glance of your web
site is magnificent, let alone the content material!
my web blog; emlak
Hi! I simply wish to offer you a big thumbs up for your excellent info you’ve got here on this post.
I am coming back to your blog for more soon.
My web site … realtor in Fairfax VA
Everything is very open with a clear clarification of
the challenges. It was definitely informative. Your website is very
helpful. Thanks for sharing!
Here is my page – emploi togo
This information is priceless. How can I find out more?
My blog real estate agent Cape Cod MA
Hi, Neat post. There is a problem along with your website
in internet explorer, would check this? IE nonetheless is the marketplace leader and
a big component to other people will omit your excellent writing because of this problem.
Take a look at my site … AI Proverb Canvas Art
Good day! This is my 1st comment here so I just wanted
to give a quick shout out and say I truly enjoy reading
through your blog posts. Can you recommend any other blogs/websites/forums
that deal with the same subjects? Thanks a lot!
Also visit my webpage :: queens urgent care
I am sure this paragraph has touched all the internet viewers,
its really really pleasant piece of writing on building up new webpage.
Here is my site :: best realtor in Grass Valley CA
Hello, I think your blog might be having browser compatibility issues.
When I look at your website in Ie, it looks
fine but when opening in Internet Explorer, it has some overlapping.
I just wanted to give you a quick heads up! Other then that, amazing blog!
I’ve read some excellent stuff here. Definitely
price bookmarking for revisiting. I wonder how a lot attempt
you place to create any such magnificent informative web site.
I pay a visit everyday a few sites and websites to read articles or reviews, however this website offers feature based posts.
Have a look at my web page … designer furniture sales online
An outstanding share! I’ve just forwarded this
onto a colleague who has been doing a little research on this.
And he in fact ordered me breakfast simply because I found it for him…
lol. So let me reword this…. Thank YOU for the meal!!
But yeah, thanx for spending some time to talk about this issue here on your internet site.
Have a look at my web site … best realtor in Galion OH
Very good website you have here but I was curious about
if you knew of any discussion boards that cover the same topics
talked about here? I’d really like to be a part of online community where I can get advice from other experienced people that share the same
interest. If you have any recommendations, please let me know.
Bless you!
Fastidious answers in return of this difficulty with real arguments and telling the whole thing about that.
My web page :: best realtor in Thornton CO
You should take part in a contest for one of the most useful blogs
on the net. I’m going to highly recommend this blog!
Here is my web-site realtor in Fairfax VA
Hi there, You’ve done a great job. I’ll certainly digg it and personally suggest to my friends.
I’m sure they will be benefited from this site.
https://forexdana.my.id/
Hi, Neat post. There is a problem together with your website in internet explorer, would test this?
IE still is the market chief and a good component to people will miss
your fantastic writing because of this problem.
Feel free to surf to my web page – Old Money Art
It’s the best time to make some plans for the future and it is time
to be happy. I’ve read this post and if I could I want to suggest you few interesting things or tips.
Perhaps you could write next articles referring to this article.
I desire to read more things about it!
Feel free to visit my site; realtor in Bartlett TN
I don’t even know how I ended up here, but I thought this post was
good. I do not know who you are but definitely you’re going
to a famous blogger if you aren’t already 😉 Cheers!
Feel free to visit my web blog: realtor in Dallas TX
Hey there, You have done a great job. I will certainly digg it and personally recommend to my friends.
I am confident they will be benefited from
this web site.
My blog post :: Video Editing
Howdy! Do you use Twitter? I’d like to follow you if that would be okay.
I’m undoubtedly enjoying your blog and look forward to
new updates.
Look at my blog post; Old Money Art
Hello, i believe that i saw you visited my web site thus i
got here to go back the prefer?.I am trying to in finding issues to
improve my site!I guess its adequate to make use of a few of your concepts!!
You could definitely see your expertise in the work you write.
The arena hopes for more passionate writers such as you who aren’t afraid to
say how they believe. All the time go after your heart.
https://nagasaonpaito.net/
What’s up to every body, it’s my first visit of this blog; this blog contains awesome and genuinely
fine data for visitors.
Feel free to visit my web page: realtor in Angeles CA
Do you mind if I quote a couple of your posts as long as
I provide credit and sources back to your site? My blog is in the exact same niche as yours and my visitors would genuinely benefit from some of the information you present here.
Please let me know if this ok with you. Cheers!
Here is my site … best real estate agent in Angeles CA
Thanks for some other great post. The place else may anyone get that kind of information in such a
perfect means of writing? I’ve a presentation subsequent week,
and I am on the look for such info.
I’m gone to convey my little brother, that he should also pay a
quick visit this webpage on regular basis to take updated from most recent reports.
Here is my homepage; best realtor in Heber Springs AR
Does your website have a contact page? I’m having problems locating it
but, I’d like to send you an e-mail. I’ve got some ideas for
your blog you might be interested in hearing.
Either way, great site and I look forward to seeing it grow over time.
Oh my goodness! Awesome article dude! Many thanks, However I am going
through problems with your RSS. I don’t know the reason why I cannot
join it. Is there anybody getting identical RSS problems?
Anyone that knows the solution can you kindly respond?
Thanx!!
my blog post best real estate agent in Bartlett TN
Having read this I believed it was extremely informative.
I appreciate you finding the time and effort to put this information together.
I once again find myself spending a lot of time both reading and commenting.
But so what, it was still worthwhile!
Feel free to surf to my page – best realtor in Thornton CO
I do not even know how I ended up here, but I thought this post was good.
I don’t know who you are but certainly you are going to a famous blogger if you are not already 😉 Cheers!
Stop by my web site … queens urgent care
You could definitely see your skills within the work you write. The world hopes for even more passionate writers such as you who aren’t afraid to say how they believe. At all times go after your heart.
Feel free to visit my site; https://Emiratesflag.ae/
Thanks for the auspicious writeup. It in fact used to be a leisure account it.
Look complicated to far delivered agreeable from you!
By the way, how can we be in contact?
My web blog; realtor in Heber Springs AR
Hi my family member! I wish to say that this post
is amazing, great written and include almost all important infos.
I’d like to look more posts like this .
Look into my web blog; best real estate agent in San Jose CA
Outstanding story there. What happened after? Take care!
May I simply just say what a relief to discover
someone that actually understands what they are discussing on the net.
You certainly know how to bring a problem to light and make it important.
A lot more people should check this out and understand this side
of the story. I can’t believe you aren’t more popular
since you most certainly have the gift.
my blog – best real estate agent in Heber Springs AR
I’m really enjoying the design and layout of your website.
It’s a very easy on the eyes which makes it much more pleasant for me to come here and visit more
often. Did you hire out a designer to create your theme?
Fantastic work!
Visit my web blog real estate agent Sarasota FL
Heya i am for the first time here. I found this board and I find It truly useful & it helped me out much.
I hope to give something back and help others like you aided
me.
my webpage Art Deco Prints
First of all I would like to say fantastic blog! I had a quick question which I’d like to ask if you do not mind.
I was interested to find out how you center yourself and clear your mind
prior to writing. I’ve had a tough time clearing my mind in getting my
thoughts out. I truly do take pleasure in writing but it just seems
like the first 10 to 15 minutes are lost simply just trying
to figure out how to begin. Any recommendations or hints?
Kudos!
An intriguing discussion is worth comment.
There’s no doubt that that you should publish more about this
subject matter, it might not be a taboo subject but usually
people do not speak about these issues. To the next!
Many thanks!!
Feel free to surf to my web site :: real estate agent Angeles CA
Wow, superb weblog structure! How long have you been blogging for?
you made blogging glance easy. The whole glance of your website is wonderful,
as neatly as the content!
Stop by my web page … best real estate agent in Bartlett TN
Hello, for all time i used to check web
site posts here early in the break of day, since i love to learn more and more.
my web site: best realtor in Sarasota FL
I’m impressed, I must say. Seldom do I come across a blog
that’s equally educative and engaging, and without a doubt,
you’ve hit the nail on the head. The problem is something that not enough people are speaking intelligently about.
I am very happy that I found this during my hunt for something concerning this.
my web-site – real estate agent Galion OH
Servus Leute,
hat jemand von euch schon mal was von https://hk.tiancaisq.com/home.php?mod=space&uid=8065773&do=profile&from=space gehört?
Ich hab’s testweise ausprobiert, wegen dem angeblichen Startguthaben ohne Einzahlung.
Dachte erst, das ist wieder so ein 0815-Ding, aber war dann echt überrascht. Gleich nach dem Spinmama Login waren die Freispiele da, vollkommen kostenlos.
Läuft auch mobil echt gut – hab’s über die App probiert. Was mich richtig überrascht hat:
Auch als Stammspieler bekommst du regelmäßig Aktionen. Das ist selten.
Keine miesen Tricks wie bei anderen Casinos. Ich behalte es mal im Auge.
Falls jemand von euch auch da ist – wie sind eure Erfahrungen?.
Share your unique link and earn up to 40% commission! https://shorturl.fm/TrDeG
Excellent beat ! I wish to apprentice whilst you amend your web site, how can i subscribe for a blog web site?
The account helped me a applicable deal. I had been a little bit acquainted of this your broadcast
offered vibrant transparent concept
My web site – realtor in Fairfax VA
Nice weblog here! Also your site so much up very fast!
What host are you the usage of? Can I am getting your affiliate link
for your host? I desire my site loaded up as fast as yours
lol
Look into my blog – best real estate agent in Heber Springs AR
Wonderful blog! Do you have any tips for aspiring writers? I’m hoping to start my
own blog soon but I’m a little lost on everything.
Would you advise starting with a free platform like WordPress or go for a paid option? There are so
many options out there that I’m totally overwhelmed ..
Any tips? Cheers!
Look at my web blog: best real estate agent in Fort Lauderdale FL
Thanks to my father who shared with me on the topic of this webpage, this website is
genuinely awesome.
Look at my blog post – best real estate agent in San Jose CA
If you desire to obtain a great deal from this paragraph then you have to apply such techniques to your won website.
Also visit my webpage: best realtor in Angeles CA
I could not refrain from commenting. Exceptionally well written!
Hi there, I enjoy reading through your article post. I like to write a little comment to support you.
Hi there this is kind of of off topic but I was
wondering if blogs use WYSIWYG editors or if you have to manually code with HTML.
I’m starting a blog soon but have no coding experience so
I wanted to get advice from someone with experience.
Any help would be greatly appreciated!
Also visit my web page … best real estate agent in Inwood WV
Your audience, your profits—become an affiliate today! https://shorturl.fm/wmJg4
Wonderful article! We will be linking to this great post on our site.
Keep Get up to 72% off NordVPN + an Amazon.co.uk Gift Card the great writing.
It’s amazing for me to have a web site, which is useful designed for my know-how.
thanks admin
Also visit my site :: realtor in Fort Lauderdale FL
It’s very easy to find out any topic on net as compared to textbooks, as I found
this paragraph at this web page.
my web page – best real estate agent in San Jose CA
Good post. I learn something totally new and challenging on sites I stumbleupon everyday.
It’s always useful to read through content from other authors and use something from their websites.
My blog post :: premium South African streetwear
Thanks a bunch for sharing this with all folks you really recognize what
you are speaking approximately! Bookmarked.
Kindly additionally visit my site =). We could have a hyperlink alternate agreement among us
my blog post … realtor in Angeles CA
Greetings! I’ve been reading your weblog for a
while now and finally got the courage to
go ahead and give you a shout out from New Caney Texas!
Just wanted to say keep up the great work!
Here is my site real estate agent Sarasota FL
This is really interesting, You’re a very skilled
blogger. I have joined your feed and look forward to seeking more of your wonderful post.
Also, I’ve shared your website in my social networks!
Here is my homepage: best real estate agent in Galion OH
Magnificent site. Plenty of helpful info here. I am sending it to some pals ans additionally sharing in delicious.
And naturally, thank you to your sweat!
Feel free to visit my webpage – best real estate agent in Grass Valley CA
What’s Taking place i am new to this, I stumbled upon this I’ve discovered
It positively helpful and it has aided me out loads.
I’m hoping to give a contribution & aid different customers like its aided me.
Good job.
my page … real estate agent Cape Cod MA
Hi there to every one, for the reason that I
am really eager of reading this website’s post to be updated
on a regular basis. It contains good material.
My website … Deurbeslag kopen
Fantastic goods from you, man. I have be aware your
stuff prior to and you are just extremely great. I really like what you have received right here, certainly
like what you are saying and the way by which you say it.
You are making it entertaining and you continue to take care of
to stay it wise. I can’t wait to read far more from
you. That is actually a great website.
Just wish to say your article is as astounding.
The clarity to your put up is just spectacular and that i could suppose you’re a professional in this subject.
Well with your permission let me to grasp your RSS feed to keep updated
with imminent post. Thank you one million and please keep up the enjoyable
work.
my page … best real estate agent in Cape Cod MA
Great web site. A lot of helpful information here. I am sending it to
a few friends ans additionally sharing in delicious.
And naturally, thank you to your sweat!
my web blog – best realtor in Thornton CO
Hey! I’m at work browsing your blog from my new
iphone 3gs! Just wanted to say I love reading your blog and look forward to
all your posts! Carry on the outstanding work!
my blog realtor in San Jose CA
Hello! I know this is kinda off topic but I was wondering if you knew where I could locate a
captcha plugin for my comment form? I’m using the same
blog platform as yours and I’m having problems finding one?
Thanks a lot!
my web page; Deurbeslag kopen
hello!,I love your writing so so much! proportion we keep
up a correspondence extra about your post on AOL?
I require a specialist in this area to solve my problem.
May be that is you! Looking forward to see you.
Have a look at my web site – realtor in Sarasota FL
naturally like your website but you need to take a look at the spelling on quite a few of your
posts. Many of them are rife with spelling problems
and I to find it very troublesome to tell the truth then again I will surely
come again again.
Here is my homepage: Physiotherapy Dubai
Earn recurring commissions with each referral—enroll today! https://shorturl.fm/My1Sn
I could not refrain from commenting. Perfectly written!
Feel free to visit my page eames lounge chair replica
There is definately a lot to know about this subject. I like
all the points you’ve made.
Have you ever considered about including a little bit more than just your articles?
I mean, what you say is valuable and all.
But think of if you added some great visuals or video clips to give
your posts more, “pop”! Your content is excellent but with images and video clips,
this website could certainly be one of the most beneficial
in its field. Very good blog!
my web blog – queens urgent care
You actually make it seem so easy with your presentation but I
find this topic to be actually something which I think I would never understand.
It seems too complicated and very broad for me.
I’m looking forward for your next post, I’ll try to get
the hang of it!
My site: designer furniture sales online
Excellent way of describing, and fastidious piece of writing
to get facts about my presentation subject, which i am going to present in academy.
Wonderful beat ! I wish to apprentice while you amend your website,
how can i subscribe for a blog web site? The account aided best ophthalmologist near me a acceptable deal.
I had been tiny bit acquainted of this your broadcast provided bright clear idea
I don’t even know how I finished up right here, however I assumed this publish used to be great. I do not recognise who you might be but certainly you are going to a well-known blogger for those who aren’t already. Cheers!
Wow, that’s what I was searching for, what a information! existing here at this weblog, thanks admin of this
website.
Excellent post. I was checking continuously this blog and I’m impressed!
Extremely useful info specially the last part 🙂 I queens urgent care for such information much.
I was looking for this particular info for a long time.
Thank you and good luck.
70918248
References:
anabolic Steroid street names – https://www.kentturktv.com/ali-camli-kayserispora-istifasini-resmen-sundu/ –
Hey very nice blog!
my website … best ophthalmologist near me
This blog was… how do you say it? Relevant!!
Finally I’ve found something that helped me. Many thanks!
Also visit my blog post :: emlak
Thanks a lot! I enjoy it.
Greetings I am so happy I found your webpage, I really found you by mistake,
while I was browsing on Google for something else, Anyhow
I am here now and would just like to say many thanks for a
remarkable post and a all round enjoyable blog (I also love the theme/design), I don’t have time to read through it all
at the minute but I have book-marked it and also included your RSS feeds, so
when I have time I will be back to read a lot more, Please do keep up the excellent
job.
Stop by my web blog: designer furniture sales online
Hello friends, how is all, and what you desire to
say on the topic of this article, in my view its
in fact amazing in support of me.
Here is my webpage – designer furniture sales online
It’s actually a nice and helpful piece of info.
I’m satisfied that you shared this helpful info with us.
Please stay us up to date like this. Thanks for sharing.
Thanks for the auspicious writeup. It in fact was a amusement account it.
Look advanced to far introduced agreeable from you!
By the way, how can we communicate?
I am genuinely pleased to glance at this web site posts which includes lots
of helpful facts, thanks for providing these kinds
of statistics.
my web page … AB DAO
Hi, Neat post. There is an issue with your website in web explorer, could check this?
IE still is the market chief and a huge portion of other folks will
pass over your excellent writing because of this problem.
Here is my webpage; empowering ambitious women
Thanks for your marvelous posting! I definitely enjoyed reading it, you may be a great author.I will make
sure to bookmark your blog and definitely
will come back very soon. I want to encourage one to continue your great
work, have a nice evening!
my web-site: کانکس
This is really interesting, You are a very skilled blogger.
I’ve joined your rss feed and look forward to seeking more of your magnificent post.
Also, I have shared your website in my social
networks!
Also visit my homepage – AI
Hey there! I know this is kinda off topic but I’d figured I’d
ask. Would you be interested in trading links or maybe guest writing a blog
post or vice-versa? My blog discusses a lot of the same
topics as yours and I think we could greatly benefit from each other.
If you happen to be interested feel free to send me an email.
I look forward to hearing from you! Terrific blog by the way!
Look at my site Screen Recording
We stumbled over here different website and thought I should check things out.
I like what I see so now i’m following you. Look forward to finding out about your web page for a second
time.
Feel free to surf to my blog Buyplaya real estate
Hi, I do think this is an excellent web site. I stumbledupon it 😉 I may return yet again since I book marked
it. Money and freedom is the greatest way to change, may you be rich and continue to guide other people.
my page: Screen Recording
This is my first time go to see at here and i am genuinely
pleassant to read all at one place.
my web site; African Big 5 Hunting Packages
Can I simply say what a relief to find somebody who actually knows what they’re talking about
on the net. You definitely realize how to
bring an issue to light and make it important. More
people really need to check this out and understand this
side of your story. I was surprised that you’re not
more popular since you certainly possess the gift.
My homepage; AB DAO
Your mode of telling all in this article is really nice, every one be capable of simply understand
it, Thanks a lot.
my blog post … women’s empowerment
Appreciate this post. Let me try it out.
Feel free to surf to my website African Big 5 Hunting Packages
Thank you for any other magnificent post. Where else may
just anyone get that type of info in such a perfect way of writing?
I have a presentation next week, and I am at the search for such
info.
Touche. Great arguments. Keep up the amazing work.
I love it whenever people come together and share opinions.
Great website, stick with it!
Also visit my web page :: 半套
Thanks for one’s marvelous posting! I definitely enjoyed reading it, you might be a great author.
I will make certain to bookmark your blog and will eventually
come back at some point. I want to encourage you to definitely
continue your great job, have a nice day!
Look into my blog post X Tweets
I do accept as true with all of the ideas
you have introduced on your post. They are very convincing and can certainly work.
Still, the posts are very short for novices. May you please
prolong them a bit from subsequent time? Thank you for the post.
Also visit my page :: Deurbeslag kopen
No matter if some one searches for his necessary thing, thus he/she wants to be available that in detail, so that thing is maintained over here.
My blog: emploi togo
My spouse and I stumbled over here from a different website and thought I might as well check things out.
I like what I see so i am just following you. Look forward to finding out about your web page for
a second time.
Admiring the persistence you put into your website and in depth information you present.
It’s good to come across a blog every once in a while that
isn’t the same unwanted rehashed information. Great read!
I’ve saved your site and I’m adding your RSS feeds to my
Google account.
Take a look at my page … Physio
Howdy! I know this is kinda off topic but I was wondering
if you knew where I could get a captcha plugin for my comment
form? I’m using the same blog platform as yours and I’m having problems finding one?
Thanks a lot!
Feel free to surf to my web page Anthony Milewski
Fantastic post but I was wanting to know if you could write a
litte more on this topic? I’d be very grateful if
you could elaborate a little bit more. Kudos!
This is my first time pay a visit at here and i am truly impressed to read everthing at alone place.
my site; Anthony Milewski
Very shortly this website will be famous amid all blogging and site-building users,
due to it’s pleasant articles
My web site – coaching for ambitious women
Good day! I simply wish to give you a huge thumbs up coaching for ambitious women your
great info you’ve got right here on this post. I am coming back to your website for
more soon.
Les énigmes varient selon le niveau de difficulté, mais elles sont accessibles dès le niveau 20, ce qui permet à tous les joueurs, y compris ceux en mode monocompte, de se lancer dans cette activité.
Unlock top-tier commissions—become our affiliate partner now! https://shorturl.fm/HGXrC
Spot on with this write-up, I actually feel this website needs far more attention. I’ll probably be back again to
read more, thanks for the info!
Excellent article. Keep writing such kind of info on your page.
Im really impressed by it.
Hey there, You have performed a great job. I’ll certainly
digg it and for my part recommend to my friends.
I am confident they will be benefited from this web site.
My page: Buyplaya real estate
I would like to thank you luxury capsule wardrobe for men the efforts you
have put in penning this website. I’m hoping to
check out the same high-grade blog posts from you in the future as well.
In fact, your creative writing abilities has encouraged me to get my own, personal website
now 😉
Hi there, this weekend is pleasant designed for me, since this occasion i am reading this impressive educational post here at
my home.
Here is my webpage CBD lotion
It’s an awesome article designed for all the online visitors; they will get advantage from it I
am sure.
Feel free to surf to my website: Buyplaya real estate
Hello, Neat post. There’s a problem together with your web site in internet explorer, may test this?
IE nonetheless is the marketplace leader and Testosterone in Canada a huge component to other people will pass
over your wonderful writing because of this problem.
Quality posts is the key to invite the visitors to visit the web
site, that’s what this website is providing.
Here is my web site standby diesel generators
Hello there I am so happy I found your web site, I really found
you by mistake, while I was browsing on Yahoo for something else, Anyhow
I am here now and would just like to say cheers
for a remarkable post and a all round enjoyable blog
(I also love the theme/design), I don’t have time to go through it all at the minute but I have saved it and also included your RSS feeds, so when I have time I will be back to read a great deal more, Please do keep up the fantastic
jo.
My blog: Buyplaya Advisors
Hello there, You’ve done an excellent job. I will definitely digg it and personally suggest to my
friends. I’m confident they will be benefited from this website.
Feel free to visit my page دانلود آهنگ بی کلام
Unlock top-tier commissions—become our affiliate partner now! https://shorturl.fm/HGXrC
Greetings from Ohio! I’m bored to death at work so I decided to
browse your website on my iphone during lunch break.
I enjoy the info you present here and can’t wait to take a
look when I get home. I’m surprised at how fast your blog loaded on my phone ..
I’m not even using WIFI, just 3G .. Anyhow, very
good blog!
Hello there, There’s no doubt that your blog may be having internet browser compatibility problems.
When I take a look at your site in Safari, it looks fine however, if opening in I.E., it’s got
some overlapping issues. I just wanted to give you a quick heads
up! Other than that, fantastic site!
My web site – diesel generator installation
Thanks a bunch for sharing this with all people you actually recognise what you’re talking about!
Bookmarked. Please additionally seek advice from my site =).
We could have a hyperlink trade arrangement among us
Check out my web site – diesel generator south Africa
We’re a group of volunteers and opening a new scheme in our community.
Your site offered us with valuable info to work on. You have done a formidable job
and our entire community will be thankful to you.
my web site; exclusive men’s fashion South Africa
Pretty! This was an extremely wonderful post. Thank you for supplying these details.
My website – Equipment supplier South Africa
We stumbled over here from a different web page
and thought I may as well check things out. I like
what I see so now i’m following you. Look forward
to going over your web page again.
my web site ambitious women’s empowerment
Excellent post. I used to be checking continuously this weblog and I am inspired!
Very helpful information specifically the remaining part 🙂 I maintain such info a lot.
I used to be seeking this particular information for
a long time. Thank you and good luck.
My web blog: Ai
Hi there to every , because I am truly keen of reading this blog’s
post to be updated daily. It contains fastidious material.
Also visit my web-site – Physiotherapy near me
Hi, just wanted to tell you, I loved this article.
It was practical. Keep on posting!
Feel free to surf to my web site; Physiotherapy near me
Its like you read my thoughts! You appear to grasp so much about this, like you wrote the ebook in it
or something. I feel that you could do with some % to power
the message house a bit, however other than that, that is magnificent blog.
A great read. I will definitely be back.
Here is my web-site … Buyplaya Advisors
It’s actually a nice and useful piece of information. I’m happy that you shared this helpful information with us.
Please stay us up to date like this. Thank you for sharing.
Also visit my web blog – قیمت پنل خورشیدی 1404
Hi there! This blog post could not be written much better!
Going through this post reminds me of my previous roommate!
He continually kept preaching about this. I most certainly
will send this article to him. Pretty sure he’s going to have
a very good read. Thank you for sharing!
My blog post … Buyplaya real estate
Having read this I believed it was really enlightening.
I appreciate you taking the time and effort
to put this informative article together.
I once again find myself personally spending a lot of time both reading and
commenting. But so what, it was still worth it!
Here is my website: قیمت کانکس
wonderful issues altogether, you just gained a new reader.
What would you recommend about your submit that you made some days ago?
Any positive?
Have a look at my blog post :: Buyplaya real estate
If you would like to get a good deal from this article
then you have to apply these strategies to your won blog.
Feel free to surf to my page – PET plastic containers for products
semiconductormaterials.com
Excellent, what a website it is! This weblog presents helpful data to us, keep it up.
Have a look at my homepage ambitious women’s empowerment
Une fois dans la pièce centrale, cliquez sur le coffre central (distributeur de missions) à côté du PNJ Dhain.
Touche. Solid arguments. Keep up the great effort.
My web-site … Anthony Milewski
I always spent my half an hour to read this blog’s content every day along with a
cup of coffee.
Here is my web-site کانکس ویلایی
Hi, i think that i saw you visited my blog so i came to “return the favor”.I am
attempting to find things to enhance my site!I suppose
its ok to use a few of your ideas!!
Look into my website 半套
This is a topic that is close to my heart…
Best wishes! Where are your contact details though?
Here is my website :: THC gummies
This is my first time visit at here and i am truly happy to read all at alone place.
Feel free to surf to my web-site: دانلود آهنگ بی کلام
I got this web page from my pal who informed me about this website and now this time I am visiting this web page and reading very informative articles at this time.
My web page: CBD lotion
Write more, thats all I have to say. Literally, it seems
as though you relied on the video to make your point. You
clearly know what youre talking about, why waste your intelligence on just posting videos to
your blog when you could be giving us something informative to read?
Feel free to surf to my web blog – Deurbeslag kopen
Hello! I understand this is kind of off-topic however I needed to ask.
Does operating a well-established website like yours take
a massive amount work? I’m brand new to writing a blog however I do write
in my diary everyday. I’d like to start a blog so I can easily share my personal experience and feelings online.
Please let me know if you have any kind of ideas or tips for new aspiring bloggers.
Appreciate it!
my blog :: قیمت پنل خورشیدی
Hello, i feel that i saw you visited my web site so i came to go back the want?.I’m
trying to in finding issues to improve my web site!I
guess its good enough to use some of your
ideas!!
Visit my web-site: life coaching for ambitious women
What i do not realize is in truth how you are not actually
much more neatly-favored than you may be now.
You’re so intelligent. You recognize thus significantly
in relation to this topic, made me individually
consider it from so many various angles. Its like men and women don’t
seem to be fascinated until it’s something to do with Lady
gaga! Your personal stuffs excellent. Always handle it up!
my web-site Anthony Milewski
Fabulous, what a webpage it is! This webpage presents valuable information to us, keep
it up.
Here is my website ambitious women’s empowerment
Hello! I know this is kind of off topic but I was wondering which blog platform are you using for this site?
I’m getting tired of WordPress because I’ve had problems with hackers and
I’m looking at options for another platform.
I would be awesome if you could point me in the direction of a
good platform.
My site: poles rising
We are a bunch of volunteers and starting a brand new
scheme in our community. Your website offered us
with helpful information to work on. You’ve performed an impressive
job and our whole community will probably be grateful to you.
My webpage – Buyplaya Advisors
Simply wish to say your article is as surprising.
The clarity on your post is just great and that
i can assume you are a professional on this subject.
Well together with your permission allow me to grasp your RSS feed to keep up to date with imminent post.
Thanks a million and please carry on the enjoyable work.
my blog post VigorMuse Coaching
Hello
Stoped by to say how wonderful your site is!
I have a page about 놀쟈초대장
come visit and give me some comments!
Thank you!
Hey! Do you know if they make any plugins to help with Search Engine Optimization? I’m trying to get my blog
to rank for some targeted keywords but I’m not seeing very
good success. If you know of any please share. Thank you!
Ciatoto adalah platform judi online terpercaya yang
menyediakan permainan togel dan slot dengan sistem fair play serta peluang
menang tinggi. Dengan layanan 24 jam, metode deposit yang lengkap, dan berbagai
promo menarik, Ciatoto menjadi pilihan utama para pecinta togel
dan slot online di Indonesia.
Promote our brand and get paid—enroll in our affiliate program! https://shorturl.fm/frr2S
It’s hard to find educated people in this particular topic, but
you sound like you know what you’re talking about!
Thanks
Review my webpage – plastic packaging containers
Hi there, I check your new stuff on a regular basis.
Your story-telling style is witty, keep it up!
my web page – Avatars
I think this is among the most important information for me.
bulk plastic jars and bottles i am glad reading your article.
But wanna remark on some general things, The site style is perfect, the articles is really great :
D. Good job, cheers
I blog frequently and I truly thank you for your information. The article has really peaked
my interest. I’m going to bookmark your site and keep checking for new information about once a week.
I opted in for your Feed as well.
Hi there very nice site!! Guy .. Beautiful .. Amazing ..
I’ll bookmark your website and take the feeds additionally?
I am happy to find numerous helpful info right here within the
post, we’d like work out extra techniques in this regard,
thank you for sharing. . . . . .
Look into my blog … Anthony Milewski
Hello mates, its enormous piece of writing concerning cultureand fully
defined, keep it up all the time.
my site empty plastic containers for business
You should take part in a contest for one of the most useful sites on the internet.
I will highly recommend this web site!
Also visit my webpage; Industrial tools and equipment
Thank you for sharing your info. I truly appreciate your efforts and I will be waiting for your next
post thank you once again.
Also visit my web site: Creative
Very nice post. I certainly appreciate this site.
Stick with it!
My webpage AI & Machine Learning
Its not my first time to pay a quick visit this web
page, i am visiting this site dailly and obtain fastidious data from here
every day.
Also visit my blog :: Anthony Milewski
Hi, this weekend is good designed for me, for the reason that this occasion i am reading this enormous informative article here at my residence.
Also visit my web site; Videos
I love looking through an article that can make people think.
Also, thanks for allowing me to comment!
my website … Creative
I have been surfing online more than 3 hours
these days, but I never discovered any fascinating article like yours.
It’s pretty price enough for me. In my opinion, if all web owners and
bloggers made good content as you did, the net will be a lot more helpful than ever before.
Great site you have here.. It’s difficult to find quality writing
like yours these days. I really appreciate individuals like you!
Take care!!
my web blog Ai
I savor, result in I found exactly what I
used to be having a look for. You have ended my four day lengthy hunt!
God Bless you man. Have a nice day. Bye
Feel free to surf to my web page :: Material handling equipment supplier
Every weekend i used to pay a visit this site, for the reason that i wish for enjoyment, for the reason that this
this site conations really good funny information too.
It’s the best time to make some plans for the future and
it is time to be happy. I have learn this submit and if I may I wish to recommend you few fascinating things or advice.
Perhaps you could write next articles regarding this article.
I wish to learn even more issues approximately it!
After looking into a few of the articles on your site, I honestly appreciate
your technique of blogging. I saved it to my bookmark
site list and will be checking back in the near future.
Please check out my web site as well and let me know what you
think.
Feel free to surf to my homepage … realtor in Carbondale CO
Every weekend i used to go to see this web page, as i wish for
enjoyment, since this this website conations in fact good funny material too.
I have been surfing online greater than three hours nowadays,
but I never found any interesting article like
yours. It is lovely value enough for me. In my opinion, if all web owners and bloggers made just right content
material as you did, the web will probably be a lot more useful than ever before.
Feel free to surf to my web blog; best realtor in Dallas TX
Useful information. Lucky me I found your site accidentally, and I’m surprised why this twist of fate didn’t happened in advance!
I bookmarked it.
Here is my web blog; best realtor in San Jose CA
When someone writes an paragraph he/she maintains the image of a user in his/her brain that how a user can be aware of it.
So that’s why this article is outstdanding. Thanks!
my blog post; best realtor in Heber Springs AR
Hello! I could have sworn I’ve been to this site before but
after reading through some of the post I realized it’s new to me.
Anyhow, I’m definitely delighted I found it and I’ll be bookmarking and checking
back frequently!
Does your blog have a contact page? I’m having a tough time locating it but,
I’d like to shoot you an email. I’ve got some suggestions for your blog you
might be interested in hearing. Either way, great site
and I look forward to seeing it develop over time.
my blog post :: Smart Tech & Sustainability
Hello! Would you mind if I share your blog with my twitter group?
There’s a lot of folks that I think would really enjoy your content.
Please let me know. Thanks
Also visit my web page … best real estate agent in Carbondale CO
A fascinating discussion is definitely worth comment.
I think that you need to publish more about this subject, it might not
be a taboo subject but usually people don’t discuss these subjects.
To the next! Best wishes!!
Feel free to surf to my web site :: realtor in Fairfax VA
What’s up all, here every person is sharing these kinds of knowledge, therefore
it’s pleasant to read this website, and I used to go
to see this weblog every day.
Here is my page: real estate agent Angeles CA
Hi to every one, the contents present at this web site are genuinely amazing for people
experience, well, keep up the good work fellows.
My website: Blockchain & Web3
I am in fact grateful to the owner of this site who has shared this wonderful article at here.
Also visit my homepage … real estate agent Bartlett TN
Hi to every body, it’s my first pay a quick visit of this weblog; this web site contains
amazing and genuinely fine stuff for readers.
Also visit my blog; Blockchain & Web3
Sign up for our affiliate program and watch your earnings grow! https://shorturl.fm/pa77L
These are really impressive ideas in about blogging.
You have touched some nice points here. Any way keep up wrinting.
Look at my web-site :: Laser & Aesthetic Clinic
Since the admin of this site is working, no uncertainty very soon it will be renowned, due to its feature contents.
My page: realtor in Angeles CA
I visited multiple web pages however the audio feature for audio songs current at this web
page is really marvelous.
Here is my site … Biotech & Health Tech
It’s hard to find well-informed people on this topic, but you sound like you know what you’re
talking about! Thanks
Here is my site – real estate agent Sarasota FL
First of all I would like to say fantastic blog!
I had a quick question which I’d like to ask if you
do not mind. I was interested to find out how you center yourself
and clear your mind prior to writing. I’ve had a tough time
clearing my thoughts in getting my ideas out.
I truly do take pleasure in writing however it just seems like the first 10 to 15 minutes are
usually lost simply just trying to figure out how to begin. Any ideas or tips?
Appreciate it!
Stop by my homepage: Space & Robotics
Remarkable! Its actually awesome piece of writing,
I have got much clear idea on the topic of from this
paragraph.
My web blog … best real estate agent in Fairfax VA
Great post.
My page … 3 days Marrakech Desert Tour
Spot on with this write-up, I truly believe that
this site needs a great deal more attention. I’ll probably be returning
to read through more, thanks for the info!
Admiring the commitment you put into your site and
in depth information you offer. It’s nice to come across a blog every
once in a while that isn’t the same out of date rehashed information. Excellent read!
I’ve bookmarked your site and I’m adding your RSS
feeds to my Google account.
Look into my blog post: real estate agent Thornton CO
Magnificent beat ! I wish to apprentice while you amend your website, how can i subscribe for a blog site?
The account aided me a acceptable deal. I had been tiny bit acquainted of
this your broadcast offered bright clear idea
I got this web site from my buddy who told me about this web site and at the moment this time I am visiting this website
and reading very informative articles at this place.
Feel free to visit my web-site: best real estate agent in Bartlett TN
You’re so interesting! I don’t think I’ve truly read through anything like that before.
So nice to discover somebody with a few original thoughts
on this topic. Seriously.. thanks for starting this up.
This website is one thing that is needed on the internet, someone with
a little originality!
Also visit my website – Dog Leash
Hi there everybody, here every one is sharing these kinds of
knowledge, therefore it’s pleasant to read this web site, and I used to pay a visit this webpage everyday.
Look into my blog – Dog Leash
Hi there, You’ve done a great job. I’ll definitely digg it and personally suggest to my friends.
I amm confident they will be benefited from this wweb
site.
my web page – จัดไม้งานศพ
I feel this is one of the most significant information for me.
And i am happy studying your article. But wanna commentary on some normal issues, The website taste is ideal, the articles is truly great : D.
Just right task, cheers
Here is my webpage: mesotherapy treatment
What’s up, everything is going perfectly here and ofcourse every one is sharing facts, that’s in fact excellent, keep up writing.
Hey there would you mind stating which blog platform you’re working with?
I’m going to start my own blog in the near future but I’m having a difficult time making a decision between BlogEngine/Wordpress/B2evolution and Drupal.
The reason I ask is because your design seems different then most blogs and I’m looking for something unique.
P.S Sorry for being off-topic but I had to ask!
My blog; Smart Tech & Sustainability
Join our affiliate program and watch your earnings skyrocket—sign up now! https://shorturl.fm/Lu9po
Howdy! I could have sworn I’ve been to this site before but after reading through some of the post I realized
it’s new to me. Anyways, I’m definitely delighted I found it and I’ll be bookmarking and checking back often!
My web blog … Dog Leash
whoah this blog is excellent i like studying your articles.
Stay up the great work! You realize, lots of people are looking
round for this information, you can help them greatly.
Terrific article! This is the kind of information that should be shared across the web. Disgrace on Google for not positioning this post upper! Come on over and seek advice from my site . Thanks =)
I know this if off topic but I’m looking into starting my
own weblog and was curious what all is required to get setup?
I’m assuming having a blog like yours would cost a pretty
penny? I’m not very internet smart so I’m not 100% positive.
Any suggestions or advice would be greatly appreciated. Many thanks
Here is my site – Dog Leash
Turn your audience into earnings—become an affiliate partner today! https://shorturl.fm/KafGr
Your means of explaining everything in this paragraph is
really good, all can easily understand it, Thanks a lot.
Also visit my page best real estate agent in Galion OH
First of all I would like to say excellent blog!
I had a quick question that I’d like to ask if you do not mind.
I was interested to find out how you center yourself and
clear your thoughts before writing. I’ve had a hard time clearing my
mind in getting my thoughts out there. I truly do take pleasure in writing
however it just seems like the first 10 to 15 minutes are generally lost
simply just trying to figure out how to begin. Any recommendations or hints?
Many thanks!
Also visit my blog; skin tag removal treatment
Thank you, I’ve recently been searching for info about this subject for a
while and yours is the best I have found out till now.
But, what concerning the bottom line? Are you sure about the supply?
my blog: real estate agent Grass Valley CA
I have been exploring for a little bit for any
high-quality articles or weblog posts in this kind of house .
Exploring in Yahoo I ultimately stumbled upon this site.
Reading this information So i’m glad to express that I’ve a very just right uncanny
feeling I came upon just what I needed. I so much undoubtedly will make certain to don?t overlook this site and give it a look on a continuing basis.